
Пластмассы & etc
.pdf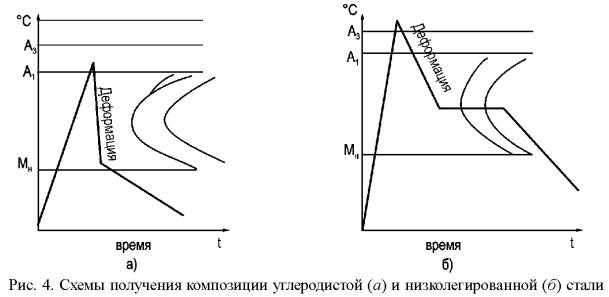
Исследованные нами доэвтектоидные углеродистые(стали 20, 50, 60 и У8) и низколегированные (17Г1С, 17Г2СФ, 35ГС) стали имели объемную долю карбидной фазы, близкую к критической, или больше ее(Vkp ). В большинстве сталей существует достаточно прочная естественная связь карбида с ферритной матрицей, поэтому при создании такой композиции в стали не возни проблема обеспечения прочной связи матрицы с упрочняющим волокном.
Прочность микрокристаллов карбида на порядок больше прочности
феррита. Это свидетельствует о том, что для получения естественных композиций
в сталях |
необходимо только направленно расположить |
частицы |
армирующей |
|
фазы и |
создать соответствующее размерное соотношение(L/h) |
карбидов, |
||
превышающее также определенную критическую величину. |
|
|
||
Электронно-микроскопическим |
исследованием |
на |
просвет , |
|
обработанных по предложенной |
технологии, установлено, |
что 80...90% всех |
карбидных частиц расположено под углом±15° (проволочные образцы) и под углом ±25° (ленточные образцы) к оси деформации.
Дополнительная холодная пластическая деформация (прокатка или волочение) со степенью обжатия20...40% полностью ориентирует в одном направлении
карбидную составляющую композиции. |
|
|
|
|
Деформация |
ферритно-карбидных |
структур |
протекает |
различн |
зависимости от дисперсности и ориентировки сорбитных колоний по отношению к оси деформации. На первых стадиях деформации течение происходит главным образом в благоприятно ориентированных колониях путем скольжения в феррите
параллельно пластинам карбида. Поперечное скольжение начинается при достаточно высоких напряжениях, когда затруднены пути легкого скольжения. Поперечное скольжение сопровождается изгибом и срезом карбидных пластин, т.
е. их разрушением. Локальное напряжение решетки α-фазы при этом приводит к появлению большого количества микротрещин, служащих очагами последующего
разрушения металла. Начало процесса дробления |
частиц определяет |
запа |
||
пластических свойств материала, а |
следовательно, и |
величину |
возможного |
|
упрочнения. |
|
|
|
|
Электронно-микроскопическое |
исследование |
показало, что |
в |
стали, |
прошедшей обычное патентирование, после 50% обжатия при волочении имеются
значительные |
участки |
измельченной |
структуры, состоящей |
из |
обломков |
|||
карбидов. |
|
|
|
|
|
|
|
|
При |
ориентированном |
расположении |
карбидных |
пластин |
в |
про |
деформации происходит лишь небольшое их доориентиров, аниетакже пластическая деформация, сопровождающаяся их утонением и удлинением. Отношение длины к толщине карбидных пластин в процессе50 %-ного обжатия образцов увеличивается в 3...5 раз.
В процессе деформации плотность дислокаций в ферритных промежутка увеличивается и образуется дислокационная ячеистая субструктура.
После больших степеней обжатия(ε=50...60%) в структуре с исходным хаотичным расположением карбидных пластин стенки ячеек состоят из сложных дислокационных образований и раздробленных карбидных частиц.
При деформации направленных структур образуется ячеистая структур, стенки которой представляют собой тонкие, вытянутые вдоль оси деформации
карбидные |
частицы, сплетенные с дислокациями. Размер ячеек |
по мере |
увеличения деформации уменьшается. |
|
|
При |
плоской прокатке всестороннее сжатие не достигается, |
поэтому |
возможности пластической деформации карбидных пластин меньше, чем при волочении. Кроме того, значительная часть карбидных пластин, располагаясь вдоль оси деформации, может занимать положение, перпендикулярное плоскости прокатки, что будет способствовать их разрушению при холодной пластической деформации. Это снижает возможность упрочнения без потери пластичности композиционной стали.
Так, например, холодная пластическая деформация (до 80 %) волочением сталей с направленной структурой, при сохранении высокой пластичности,
позволяет |
на 80... |
100 кгс/мм2 повысить |
их |
прочность по |
сравнению |
|||||
холоднотянутой |
проволокой, прошедшей |
обычное |
патентирование. При |
|||||||
холодной |
прокатке (ε>30%) тех |
же |
сталей |
повышение |
прочнос |
|||||
сопровождается резким ухудшением пластичности(удлинения и сужения), |
||||||||||
вызванного |
массовым |
дроблением |
карбидных |
пластин |
и |
образовани |
||||
большого |
количества микротрещин, поэтому прочность композиционных |
|||||||||
сталей, полученных |
комбинированной |
обработкой, включающей |
плоскую |
|||||||
прокатку, выше, чем у горячекатаной стали, на 35...50 %. |
|
|
|
|||||||
Следует |
отметить, |
что |
прочность, полученная |
экспериментально, |
выше |
расчетной по уравнению аддитивности, которое не учитывает субструктурного механизма упрочнения (табл. 27).
Цементитные частицы малоподвижны, от них зависит расстояние между
стенками ячеек. В связи с этим для стали наблюдается |
прямолинейн |
||||||
зависимость, которая графически показана на рис. 5. |
|
|
|
||||
Ориентированные цементитные частицы служат более эффективными |
|||||||
барьерами на пути движения дислокаций, чем хаотично |
расположенные, |
|
|||||
поэтому |
стали |
с |
ориентированной |
структурой |
имеют |
более |
в |
коэффициент упрочнения при деформации. На рис. 5 и |
6 представлена |
|
зависимость предела прочности стали от объемной доли цементита. |
|
|
|||||
Свободные члены |
в уравнениях прямых, полученных экспериментально и |
||||||
расчетным |
путем, различаются |
с |
вероятностьюР>0,999. |
Это |
еще |
раз |
|
подтверждает |
вывод |
о том, что |
при |
расчете прочности |
композиционных |
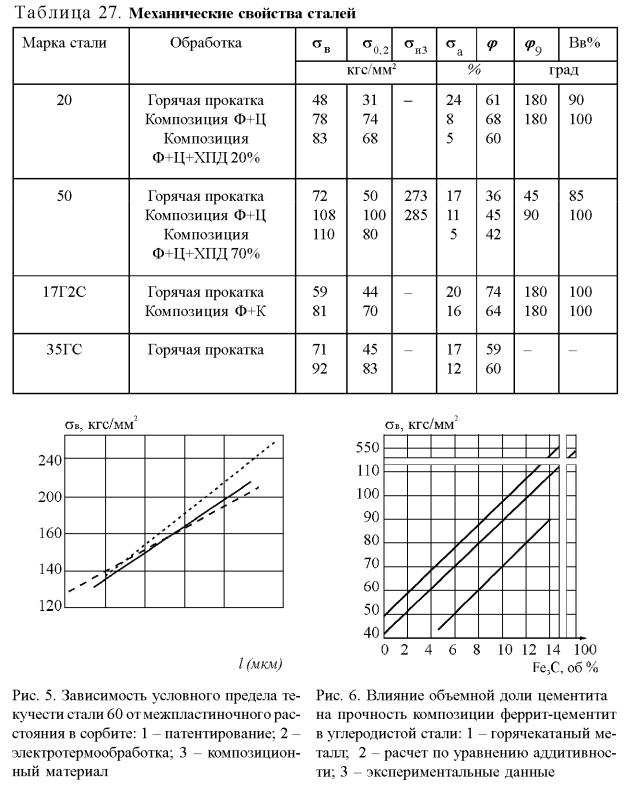
материалов с расстояниями между армирующими волокнами (пластинами) менее |
|
|||||
10 мкм |
следует |
учитывать |
субструктурный |
механизм |
упрочнения. В |
|
исследованных |
композиционных |
сталях |
межпластиночное |
расст |
||
составляло менее 0,15 мкм. |
|
|
|
|
Таким образом, имеется реальная возможность перераб доэвтектоидных углеродистых и низколегированных сталей в естественный композиционный материал. Применение этих сталей для изготовлени различного профиля, арматуры, проволоки и других деталей строительных конструкций может дать большой экономический эффект.
ОСНОВЫ МЕТАЛЛОВЕДЕНИЯ ПОРОШКОВЫХ СПЛАВОВ
Законы металловедения, которые в свою очередь базируются на законах физики, химии, термодинамики и других фундаментальных наук, полностью применимы к порошковым сплавам с учетом, разумеется, особенностей их строения, обусловленных технологией изготовления объекта исследования. Существует два принципиально различных способа получения металлического порошка:
-первый - восстановлением из оксидов(например, получение железного порошка из окалины);
-второй - распылением жидкого расплава.
Первый способ - это обычная традиционная порошковая металлургия, второй - относительно новый для сплавов на основе железа; раньше его применяли лишь для легкоплавких металлов (производство свинцовой дроби).
Порошковую металлургию |
распространяют |
на |
оба |
,способано |
есть |
обоснованная точка зрения к |
порошковым методам относить только первы |
||||
способ (восстановление), а |
второй (распыление) |
именовать |
гранульной |
||
металлургией. |
|
|
|
|
|
В данном пособии рассматриваются металловедческие аспекты только второго способа.
Посредством холодного прессования порошка можно получить изделие почти окончательной формы, которое не требует, как правило, последующей механической обработки (при этом сохраняется необходимость доводки шлифования). Пористость после холодного прессования составляет примерно 10%. Последующее спекание должно сохранить исходную пористость, иначе, например, при повышении температуры спекания произойдет заполнение пор и исказится форма изделия. Свойства такого спеченного изделия очень низкие.
Высокие стоимость порошка(углеродистая и низколегированная стали, полученные из порошков, в 3-4 раза дороже аналогичных сталей в прутке обычного металлургического производства) и энергоемкость процесса спекания делают этот
процесс |
для |
большинства |
машиностроительных |
деталей |
эконом |
|
невыгодным, |
если |
сравнивать |
порошковые |
изделия |
с |
изготовлен |
современным способом на автоматических линиях или по разным мето безотходной технологии (литье в кокиль, корковые формы, под давлением; объемная штамповка и др.). Спеченную деталь подвергают горячей доштамповке.
Вэтом случае пористость снижается 2...до3% и механические свойства
приближаются |
к |
свойствам |
литого |
металла(из |
заготовки). Однако |
||
технологический |
|
процесс |
производства |
деталей |
из |
порошка[холодное |
прессование - спекание - горячее прессование - механическая обработка (доводка, шлифование)] значительно сложнее обычной технологии, а получаемая стружка является ценным сырьем для металлургии. Тем не менее полностью отрицать возможность и даже целесообразность применения«классической» порошковой технологии изготовления деталей было бы неправомерно. Есть некоторые детали специфической и особо сложной формы(может быть одна на100 или на 1000), которые более удобно изготовлять методом порошковой металлургии.
Таким образом, «классическая» технология порошковой (восстановительной) металлургии полностью не отрицается применительно к машиностроительным
деталям, но при этом необходимо учитывать ее весьма узкое применение. Это и определяет объем производства стального порошка в развитых , ст составляющий десятые доли процента от объема стали обычного производства.
Для второго способа изготовления порошка (распыление) возможны два пути: или применение «классической» порошковой технологии (холодное прессование - спекание) или отказ от этого варианта технологии, но тогда возможно получение уникальных свойств готовых изделий(горячая экструзия определенных марок сплавов).
Впервом случае необходимо получать после распыления формуемый
холодном состоянии порошок, форма которого определяется ,средо распыляющей жидкий расплав.
При распылении водой образуются порошинки разветвленной формы, которые прессуются в холодном состоянии. При этом прочность составляет примерно 10Н/мм2 (пластичность - нулевая), что достаточно для того, чтобы изделие не рассыпалось под собственной массой и было транспортабельным.
После холодного прессования пористость достигает 10... 15% (насыпная масса
примерно 65% от |
теоретической 100%-ной |
плотности). Если |
холодное |
прессование придает |
изделию практически |
окончательную |
форму, то при |
последующем спекании пористость не должна измениться, иначе произойдет коробление изделия. В этом случае спекание осуществляется при относительно невысокой температуре, пористость сохраняется на уровне10... 15%), прочность
возрастает более чем на порядок(практически |
до 500 |
Н/мм2 и даже более), |
||||
пластичность не нулевая, но |
очень низкая. Применяя горячую подпрессовку |
|||||
(разными |
методами), можно |
снизить |
пористость |
до2...3% и |
достигнуть |
|
повышения |
прочности |
до1000 Н/мм2 |
и |
одновременного |
увеличени |
пластичности, но при этом(в той или иной степени) возникает необходимость механической обработки.
При распылении инертным газом (азотом, аргоном) полученный металл более чистый по содержанию кислорода, но порошинки (гранулы) имеют форму шара. Такие шарообразные порошинки (гранулы) в холодном состоянии не прессуются.
Из них можно лишь в горячем состоянии отпрессовать детали или сде металлургический полуфабрикат (пруток).
Схема разных технологических вариантов изготовления |
деталей из- |
р |
пыленных порошков (гранул) показана на рис. 7. |
|
|
Механические свойства порошковых материалов в значительной степени |
|
|
определяются их химическим составом, термической обработкой. Следует |
|
|
отметить, что кроме этих широко известных факторов |
для порошковы |
материалов определяющим являются все же содержание в них кислорода и пористость металла.
Влияние этих специфических для порошковых материалов факторо рассмотрим подробнее.
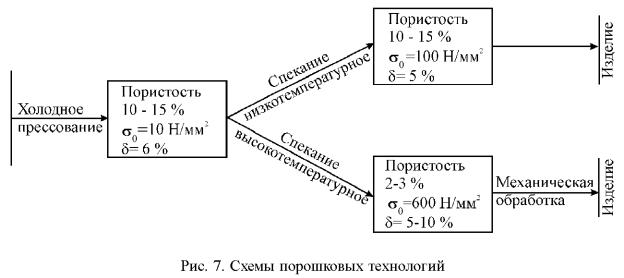
Представлены результаты испытания стали 40НЗМ (0,38 % С, 3 % Ni, 0,5 % Mo, 0,12 % О). Разную пористость получали применением деформации (горячего прессования) с различными степенями.
Повышение пористости металла приводит к снижению всех механических
свойств (рис. 8), |
однако их резкое снижение наблюдается |
при |
разно |
||||
пористости. Так, например, твердость (НRС) начинает быстро снижаться при |
|||||||
увеличении пористости более5 %, прочность - при пористости более3 %, |
|
||||||
пластические свойства - при |
пористости более2 %. При |
пористости 1 % |
|
||||
ударная вязкость снижается на 20 %, а температура полухрупкости повышается |
|
||||||
на 20 °С. Отсюда |
следует, что для удовлетворительной |
работоспособности |
|||||
изделий, изготовленных из |
порошков, при |
превалирующих напряжениях |
|||||
сжатия допускается пористость до3 %, статических напряжениях - до 2 %, а |
|
||||||
при |
воздействии |
динамических(ударных) |
нагрузок |
материал |
даже |
с |
незначительной пористостью непригоден.
Таким образом, области применения пористых стальных изделий примерно те же, что и изготовленных из серого чугуна.
Следует |
отметить, |
что даже |
при |
незначительной пористости(до 1 %) |
||||
порошковых материалов легирование их такими элементами, как никель и |
||||||||
марганец, |
а |
также |
термическое |
улучшение |
для повышения |
механических |
||
свойств не очень эффективно. |
|
|
|
|
||||
Распыление нейтральным газом (N, Аг) не гарантирует получения исходного |
||||||||
материала |
(порошка) |
с |
таким |
же |
низким |
содержанием |
кислорода, какое |
наблюдается у литого металла обычной выплавки.
Порошковый металл считается чистым по кислороду, если в нем содержится 0,01...0,02% О (общее содержание). Такое содержание кислорода характерно для бессемеровского металла, для мартеновского и конверторного(спокойного) - 0,005%, для электростали - 0,003%, для вакуумиро-ванного металла- 0,0015%. Главная причина повышенного содержания кислорода в порошковых изделияхокисление поверхности порошка при распылении, хранении и т. п.
Для порошкового материала характерно, что форма присутствующего в нем кислорода различна.
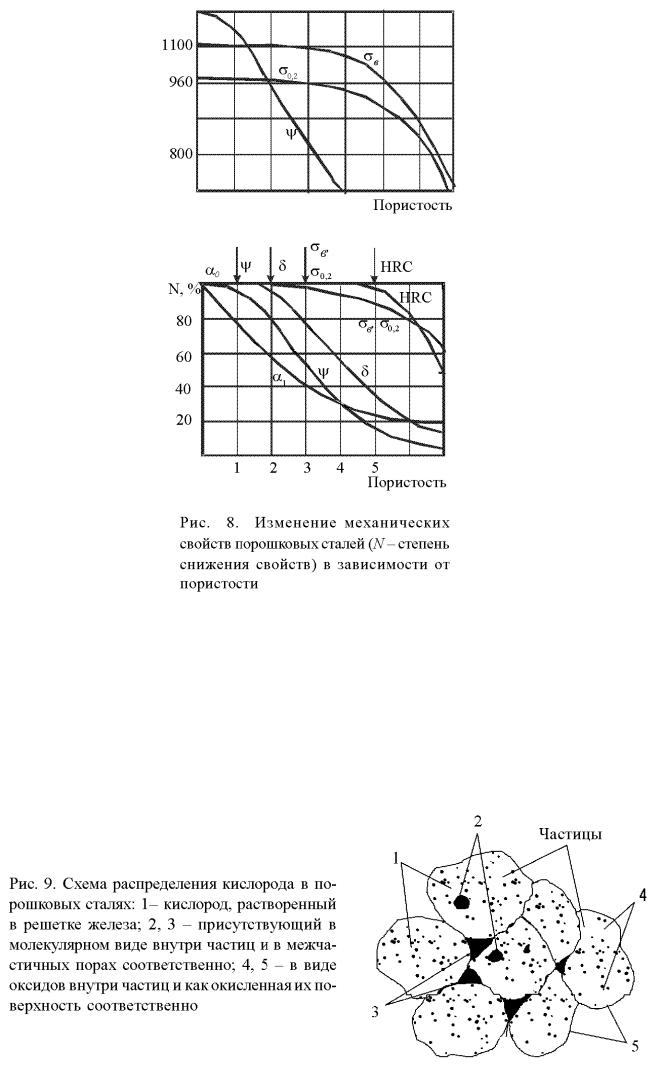
Во-первых, кислород может в молекулярном виде присутствовать в порах (межчастичных и внутричастичных). Такой кислород входит в общее содержание кислорода в металле, но на свойства его влияние наименее значительно(влияет наличие пор, а не содержание в них кислорода).
Во-вторых, кислород присутствует в виде оксидов на поверхности частиц. Влияние такого кислорода очень значительно, так как при этом уменьшается взаимодействие между частицами и, следовательно, легче происходит отделение частиц друг от друга при механическом воздействии.
Внутри частиц кислород может быть в виде оксидов и твердого раствора
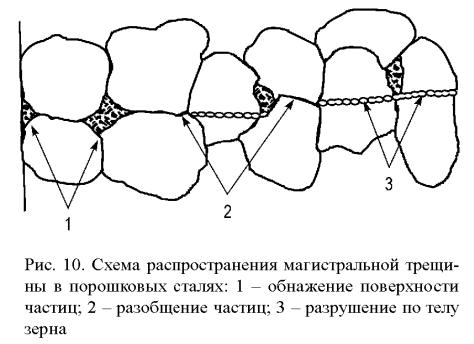
(рис. 9). Методика количественного определения каждого вида кислорода в достаточной степени еще не разработана.
Исследовано влияние кислорода в количестве 0,004%от в металле, полученным обычным металлургическим способом, до 0,045% в порошковом металле. Исследовали сталь 40НЗМ в термоулучшенном состоянии, пористость не превышала 0,5%.
Оказалось, что обычные механические свойства практически не зависят от содержания кислорода (в пределах 0,004...0,045%). Ударная вязкость литой стали (0,004% О) была значительно выше; хотя большого различия в положении
порога хладноломкости стали |
0,004с |
и |
0,012% О |
не обнаружено, при |
||
увеличении |
содержания |
кислорода |
0,045%до |
температура |
порога |
хладноломкости повышалась. Были исследованы две плавки с одинаковым
содержанием |
кислорода (0,012%): одна из |
порошка, распыленного |
азотом, |
|
||||||||||||
другая - |
из |
порошка, распыленного |
водой. |
Более |
низкое |
положение |
порога |
|||||||||
хладноломкости первой плавки свидетельствует о ,томчто важно не только |
||||||||||||||||
количество кислорода в металле, определяемое химическим анализом, но и его |
|
|||||||||||||||
форма. |
|
|
|
|
|
|
|
|
|
|
|
|
|
|
|
|
Низкие |
свойства |
пористой |
стали |
можно |
объяснить |
|
на |
осно |
||||||||
результатов исследования изломов металла с разным объемом трещин. |
|
Путь |
|
|||||||||||||
|
|
|
|
|
|
|
|
|
|
|
|
|
|
|
|
|
|
|
|
|
|
|
|
|
|
|
|
|
магистральной |
|
|||
|
|
|
|
|
|
|
|
|
трещины |
может |
быть |
|||||
|
|
|
|
|
|
|
|
|
различным (рис. 10): |
|
||||||
|
|
|
|
|
|
|
|
|
1 |
-трещина |
обнажает |
|
||||
|
|
|
|
|
|
|
|
|
поверхность частиц, 2 |
|
||||||
|
|
|
|
|
|
|
|
|
- |
разделяет |
частицы |
|||||
|
|
|
|
|
|
|
|
|
друг от друга, 3 - |
|
||||||
|
|
|
|
|
|
|
|
|
проходит |
|
по |
телу |
||||
|
|
|
|
|
|
|
|
|
зерна |
(выше |
|
порога |
||||
|
|
|
|
|
|
|
|
|
хладноломкости |
|
по |
|||||
|
|
|
|
|
|
|
|
|
вязкому |
механизму). |
|
|||||
|
|
|
|
|
|
|
|
|
При |
|
|
|
|
больш |
||
|
|
|
|
|
|
|
|
|
количестве |
пор (в |
|
|||||
|
|
|
|
|
|
|
|
|
данном |
случае 7 % и |
|
|||||
|
|
|
|
|
|
|
|
|
|
|
|
|
|
более) |
|
|
внутризеренного разрушения не наблюдали, трещина разделяет частицы либо |
|
|||||||||||||||
обнажает их поверхность. При отсутствии пор, т. е. в хорошо деформированном |
|
|||||||||||||||
металле, |
трещина |
проходит |
только |
по |
телу , |
зернаразделения |
|
частиц |
||||||||
практически |
не наблюдается. При пористости 5% (промежуточный случай) в |
|
||||||||||||||
излом входят все три вида поверхности. |
|
|
|
|
|
|
|
|
|
|
||||||
В |
порошковых |
|
изделиях |
при |
|
повышенном |
|
|
содержании |
ки |
||||||
уменьшается |
прокаливаемость, |
увеличивается |
количество |
|
неметаллических |
|||||||||||
включений (оксидов |
и |
др.), а |
также |
повышается |
порог |
хладноломкости, .е. |
увеличивается склонность к охрупчиванию. Однако в литых сталях отрицательное влияние кислорода более значительно.
Общий вывод, который можно сделать, следующий: порошковая технология не обеспечивает получения изделий, механические свойства которых были бы хотя бы
на уровне свойств сталей обычного производства. Это исключает применение порошковой технологии для высоконагруженных деталей. Если учесть высокую стоимость порошка и повышенную энергоемкость процесса(распыления или восстановления, спекания), то этот процесс ограничивается изготовление неответственных изделий специфической формы, для которых порошковый метод может оказаться конкурентоспособным по сравнению с обычным мето изготовления изделий.
Таким образом, нецелесообразность массового производства изделий из обычных сталей порошковым методом очевидна.
Свойства порошковых изделий уступают, в лучшем случае приближаются к свойствам изделий, изготовленных обычным способом. Следовательно, при более
низких |
свойствах |
и |
более |
высоких |
стоимости |
исходногоматери |
энергоемкости процесса |
спекания |
в целом |
этот процесс в подавля |
большинстве случаев невыгоден потребителю. Лишь в отдельных случаях целесообразно использование порошковой технологии(особенно для изделий сложной конфигурации).
Однако возможен подход к проблеме использования метода порошково металлургии с другой стороны. Необходимо изыскать возможность применения метода порошковой металлургии с использованием ее специфических особенностей для получения изделий более высокого качества, чем полученных по обычной технологии. Такие примеры известны уже много -летэто высокотвердые инструментальные сплавы, высококоэрцитивные магнитные сплавы. Основой этих сплавов являются высокотвердые химические соединения и единственный способ получения из них изделийспекание их частиц с использованием связки. Этот метод известен, он весьма эффективен для получения высокотвердых материалов
под |
названием «металлокерамика» или |
в |
более |
общем |
«минералокерамика». |
|
|
|
|
|
Обратимся к классическому приему улучшения |
свойств- к |
термической |
обработке, в частности к закалке. В современном понимании закалка может быть трех видов: 1 - закалка с использованием переменной растворимости - получение закалкой перенасыщенного твердого раствора; последующий процесс старения вызывает его распад и окончательно формирует свойства; 2 - закалка с использованием полиморфного превращения; возможно много вариаций структурных состояний, особенно при использовании отпуска(вторичный после закалки нагрев металла, претерпевшего полиморфное превращение); 3 - закалка из жидкого состояния - получение еще более пересыщенного твердого раствора, чем в случаях 1 и 2, с увеличением скорости охлаждения (большой набор разных структурных состояний).
Современная техника позволяет использовать широкий диапазон скоростей охлаждения при кристаллизации - 10 порядков.
Высокие скорости процесса кристаллизации достигаются при распыле жидкого расплава. При этом газ - не самый энергичный охладитель. Практически наиболее часто применяемые энергоносители - азот и вода - позволяют получить средние скорости охлаждения. При увеличении размера частицы от10 до 1000 мкм скорость охлаждения уменьшается на 2...3 порядка.
Таким образом, используя разные энергоносители (условия кристаллизации) и подбирая соответствующий размер частиц, можно получить сплав, охлажденный
со скоростями от 102 до 107 °С/с, т. е. для системы типа Fe-C (свыше 2...3 % С) - от обычных структур эвтектичного типа до аморфизированного металла.
Структура литого металла, полученного обычным способом, состоит из твердого раствора и эвтектики (ледебурита). При быстром охлаждении структура состоит из дендритов твердого раствора и избыточных частиц . карб Поскольку эти карбиды выделились при высокой температуре из пересыщенного выше равновесной концентрации твердого раствора, они должны рассматриваться как первичные карбиды, окончательный их размер определяется условиями первичной кристаллизации, при последующих нагревах рост их невозможен. Карбидная фаза быстрорежущей стали, как известно, состоит из карбидов трех типов - первичных, вторичных и эвтектоидных. Форма и размеры эвтек-тоидных карбидов изменяются в результате термической обработ(таки как они растворимы в аустените). Размер первичных карбидов определяется условиями первичной кристаллизации, в обычной быстрорежущей стали они присутствуют в виде крупных включений(остатки ледебуритной эвтектики, раздробленной ковкой или прокаткой), а в порошковой стали- в виде мелких(менее 1 мкм) включений, практически не отличимых от вторичных карбидов.
Наличие крупных первичных карбидов, с одной стороны, необходимо, так как без них нагрев под закалку при высоких температурах вызвал бы рост зерна и вследствие этого ухудшение механических свойств, но, с другой стороны, крупные частицы карбидов, являющиеся концентраторами напряжений, снижают механические свойства. Степень снижения механических свойств определяется размером этих карбидов. Отсюда следует главное преимущество порошковых быстрорежущих сталей - более высокие механические свойства.
Быстрое охлаждение жидкого расплава со скоростями105... 107°С/с характерно и для лазерной обработки с оплавлением поверхности. В связи с этим сведения об особенностях кристаллизации применимы и к лазерной обработке с
оплавлением, но при этом скорость охлаждения |
определяется не |
диаметро |
|
частиц, а толщиной оплавленного слоя. |
|
|
|
Структура быстроохлажденной быстрорежущей стали(аустенит, дисперсные |
|||
карбиды) типична |
для безвольфрамовых(низковольфрамовых) сталей. |
Для |
|
высоковольфрамовых |
(высокомолибденовых) сталей |
характерно |
наличие |
остаточной фазы, образование которой неизбежно даже при очень больших скоростях охлаждения.
Механические свойства инструментальных сталейочень важная -ха рактеристика, не менее важная, чем красностойкость (теплостойкость). Для обычных быстрорежущих сталей 18,Р Р6М5 и др. красностойкость составляет
458...620 °С.
Классический способ повышения красностойкостилегирование стали кобальтом, но это не всегда целесообразно, особенно для тонколезвийного инструмента, так как при этом снижается прочность.
Природа избыточных первичных карбидов определяется легированностью стали. В высоколегированных вольфрамом и молибденом сталях, в том числе наиболее распространенных сталях Р18, Р6М5, первичные карбиды представляют собой двойной карбид вольфрама или молибдена. В низколегированных вольфрамом и молибденом сталяхРМ2ФЗ, ЭК41, ЭК42 и др. - роль первичных играют карбиды ванадияVC. При твердости обычного шлифовального круга