
Баценков / Баценков
.pdf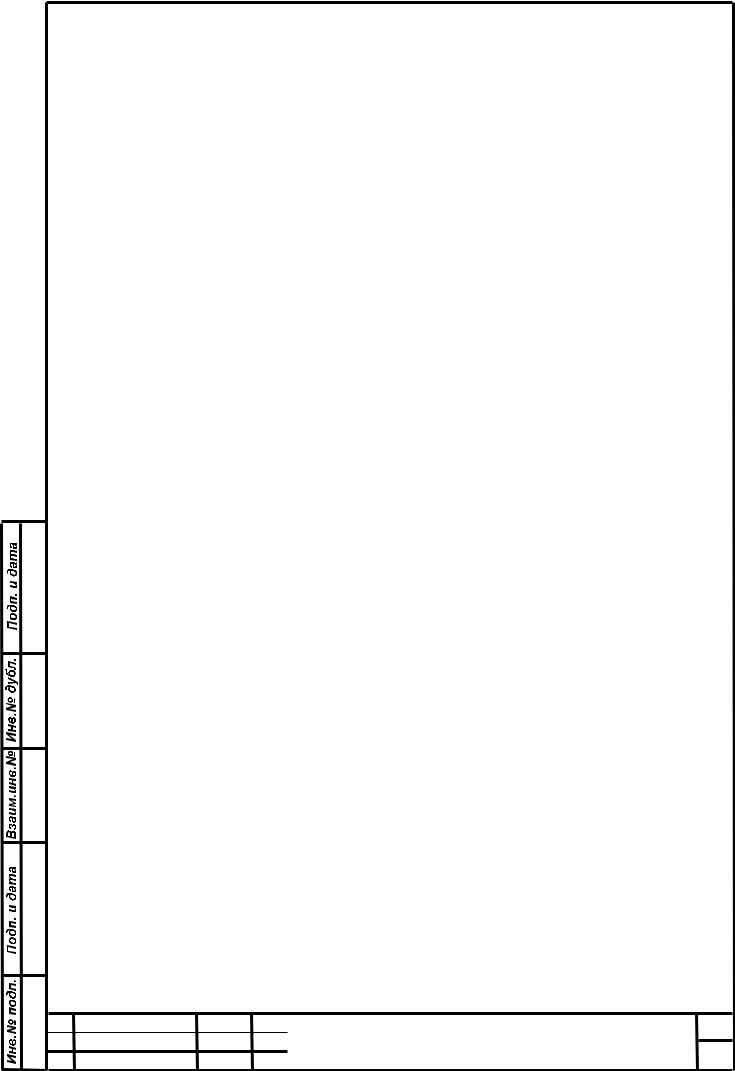
dP 150,003 2 0,135 150,273 мм; dP 150,273 2 0,273 150,819 мм; dP 150,819 2 3,480 157,779 мм;
Определяем значения допусков IT для каждого технологического пе-
рехода по ГОСТу 7505–89. |
|
|
Для заготовки по ГОСТ 7505–89 IT 5000 мкм; |
|
|
Для чернового точения IT 1000 мкм; |
|
|
Для чистового точения IT 160 мкм; |
|
|
Для шлифования IT 25 мкм. |
|
|
Определим наибольший предельный размер dmax |
прибавлением допус- |
|
ка IT к округленному наименьшему предельному размеру dmin |
||
dmax 3 150,003 0,025 150,028 мм; |
||
dmax 2 150,28 0,16 150,44 мм; |
||
dmax 2 151 1 152 мм; |
|
|
dmax Ç 158 5 163 мм. |
|
|
Определяем предельные значения |
припусков |
2Zmax как разность |
наибольших предельных размеров dmax и |
2Zmin как разность наименьших |
предельных размеров dmin предшествующего и выполняемого переходов:
2Zmaxпр |
3 150,44 150,028 0,412 мм 412 мкм; |
|
||
2Zmaxпр |
2 152 150,44 1,56 мм 1560 мкм; |
|
||
2Zmaxпр |
1 163 152 11 мм 11000 мкм; |
|
||
2Zminпр |
3 150,28 150,003 0,277 мм 277 мкм; |
|
||
2Zminпр 151 150,28 0,72 мм 720 мкм; |
|
|||
|
2Zminпр 158 151 7 мм 7000 мкм. |
|
||
Определяем номинальный припуск по формуле |
|
|||
|
|
|
Z0ном. Z0min HЗ Hд , |
(5.6) |
где Z0 min – минимальный предельный припуск, мм; |
|
|||
H З – нижнее отклонение размера заготовки, мкм; |
|
|||
H д – допуск на деталь, мкм. |
|
|||
По ГОСТ 7505-89 H З = 1700 мкм. |
|
|||
Z0ном. 7997 1700 25 9672 мкм |
|
|||
Определяем номинальный размер заготовки по формуле |
|
|||
|
|
|
dЗАГ .НОМ d Д .НОМ Z0НОМ . |
(5.7) |
|
|
|
dЗАГ .НОМ 150 9,7 159,7 мм |
|
Графическая схема расположения припусков и допусков на обработку поверхности Ø150k6( 0,0280,003) представлена на рисунке 5.1.
|
|
|
Лист |
|
|
КП.ПТП.40.15.012.00.00.ПЗ. |
13 |
Из Лист |
№ Докум. Подп Дата |
|
|
|
|
|
|
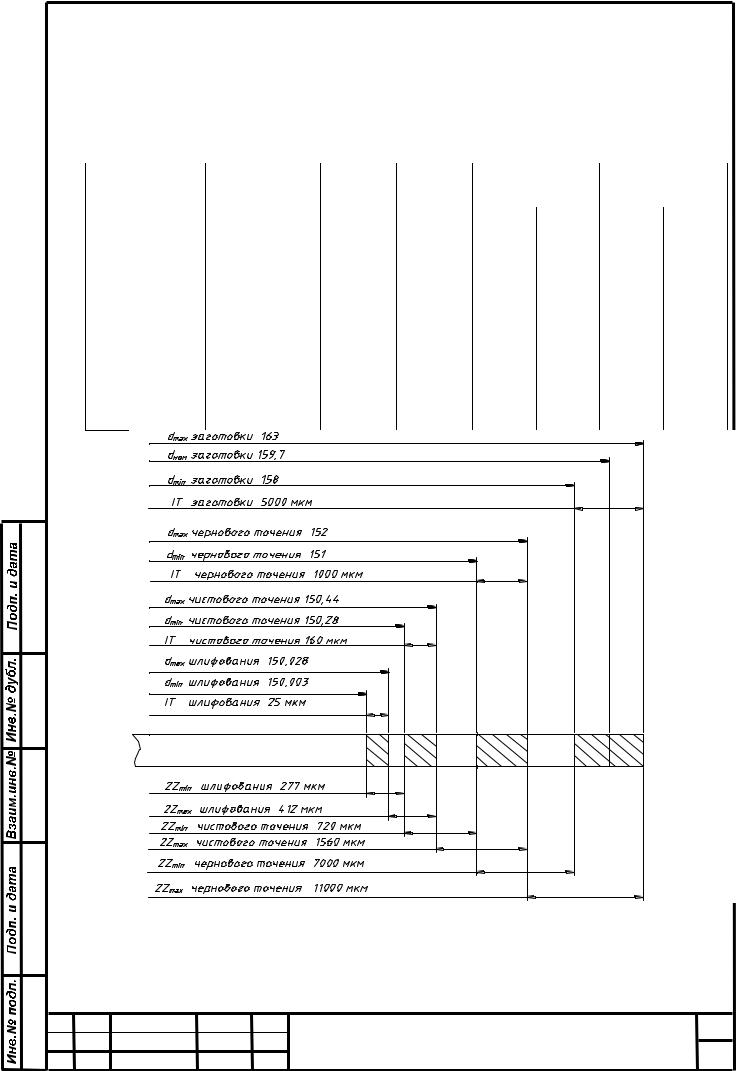
Технологический маршрут обработки поверхности Ø70k6( 00,,021002 ) со-
стоит из чернового точения, чистового точения и шлифования.
Таблица 5.2 – Расчѐт припусков и предельных размеров по технологическим |
||||||||
переходам на обработку поверхности Ø70k6( 0,021 ) |
|
|
|
|
||||
|
|
|
|
0,002 |
|
|
|
|
|
Технологиче- |
|
Расчѐт- |
|
Предельные |
Предельные |
||
|
ские переходы |
Табличный |
|
размеры, мм припуски, мкм |
||||
|
ный раз- |
Допуск |
||||||
|
обработки по- |
припуск |
|
|
|
|
||
|
мер d P , |
IT , мкм |
|
|
|
|
||
|
верхности |
2Zmin , мкм |
dmin |
dmax |
пр |
пр |
||
|
мм |
|
2Zmin |
2Z max |
||||
|
Ø70k6( 0,028 ) |
|
|
|
|
|
|
|
|
0,003 |
|
|
|
|
|
|
|
|
Заготовка |
– |
77,294 |
4500 |
77,3 |
81,8 |
– |
– |
|
|
|
|
|
|
|
|
|
|
Точение чер- |
2 3260 |
70,774 |
740 |
70,78 |
71,52 |
6520 |
10280 |
|
новое |
|||||||
|
|
|
|
|
|
|
|
|
|
Точение чи- |
2 260 |
70,254 |
120 |
70,26 |
70,38 |
520 |
1140 |
|
стовое |
|||||||
|
|
|
|
|
|
|
|
|
|
Шлифование |
2 126 |
70,002 |
19 |
70,002 |
70,021 |
258 |
359 |
Рисунок 5.1 – Схема графического расположения припусков и допусков |
|||
на обработку поверхности Ø150k6( |
0,028 ) |
|
|
|
|
0,003 |
|
|
|
|
Лист |
|
|
КП.ПТП.40.15.012.00.00.ПЗ. |
14 |
Из Лист № Докум. |
Подп Дата |
|
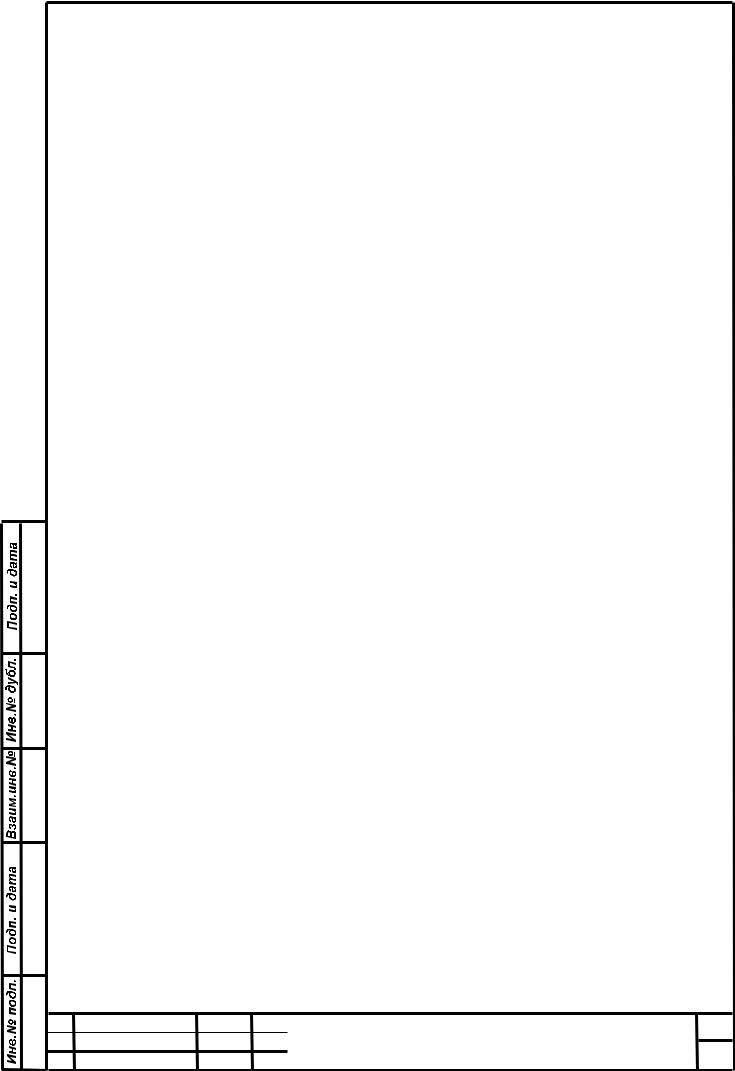
Определяем минимальные значения припусков. Минимальный припуск под черновое точение
2Z min 2 3260 мкм.
Минимальный припуск под чистовое растачивание
2Z min 2 260 мкм.
Минимальный припуск под шлифование
2Zmin 2 126 мкм.
Определим расчѐтные размеры d P , начиная с чертѐжного размера, путѐм последовательного прибавления расчетного минимального припуска 2Zmin каждого технологического перехода:
dP 70,002 2 0,126 70,254 мм;
|
|
|
|
dP 70,254 2 0,260 70,774 мм; |
|
|||||||
|
|
|
|
dP 70,774 2 3,260 77,294 мм. |
|
|||||||
|
Определяем значения допусков IT |
для каждого технологического пе- |
|
|||||||||
рехода по ГОСТу 7505–89. |
|
|
|
|
|
|
|
|
|
|
||
|
Для заготовки по ГОСТ 7505–89 IT 4500 мкм; |
|
|
|
||||||||
|
Для чернового точения IT 740 мкм; |
|
|
|
|
|||||||
|
Для чистового точения IT 120 мкм; |
|
|
|
|
|||||||
|
Для шлифования IT 19 мкм. |
|
|
|
|
|
||||||
|
Определим наибольший предельный размер dmax |
прибавлением допус- |
|
|||||||||
ка IT к округленному наименьшему предельному размеру dmin |
|
|||||||||||
|
|
|
|
dmax 3 70,002 0,019 70,021 мм; |
|
|||||||
|
|
|
|
|
|
dmax 2 |
70,26 0,12 70,38 мм; |
|
|
|
||
|
|
|
|
|
|
dmax 2 |
70,78 0,74 71,52 мм; |
|
|
|
||
|
|
|
|
|
|
dmax Ç 77,3 4,5 81,8 мм. |
|
|
|
|||
|
Определяем предельные |
значения припусков |
2Zmax как разность |
|
||||||||
наибольших предельных размеров dmax |
и |
2Zmin как разность наименьших |
|
|||||||||
предельных размеров dmin предшествующего и выполняемого переходов |
|
|||||||||||
|
2Zmaxпр |
3 70,38 70,021 0,359 мм 359 мкм; |
|
|||||||||
|
2Zmaxпр |
2 71,52 70,38 1,14 мм 1140 мкм; |
|
|||||||||
|
2Zmaxпр |
1 81,8 71,52 10,28 |
мм 10280 мкм; |
|
||||||||
|
2Zminпр |
3 70,26 70,002 0,258 мм 258 мкм; |
|
|||||||||
|
2Zminпр |
70,78 70,26 0,52 мм 520 мкм; |
|
|||||||||
|
2Zminпр |
77,3 70,78 6,52 |
мм 6520 мкм. |
|
||||||||
|
Определяем номинальный припуск. |
|
|
|
|
|||||||
|
По ГОСТ 7505-89 H З = 1500 мкм. |
|
|
|
|
|
||||||
|
Z0ном. 7298 1500 19 8779 мкм. |
|
|
|
||||||||
|
Определяем номинальный размер заготовки. |
|
|
|
||||||||
|
|
|
|
|
dЗАГ .НОМ 70 8,8 78,8 мм. |
|
|
|
||||
|
|
|
|
|
|
|
|
|
|
|
Лист |
|
|
|
|
|
|
|
|
|
|
|
|
||
|
|
|
|
|
|
|
КП.ПТП.40.15.012.00.00.ПЗ. |
|
15 |
|||
Из Лист |
№ Докум. Подп Дата |
|
|
|
|
|
|
|
|
|
|
|
|
|
|
|
|
|
|
|
|
|
|
|
|
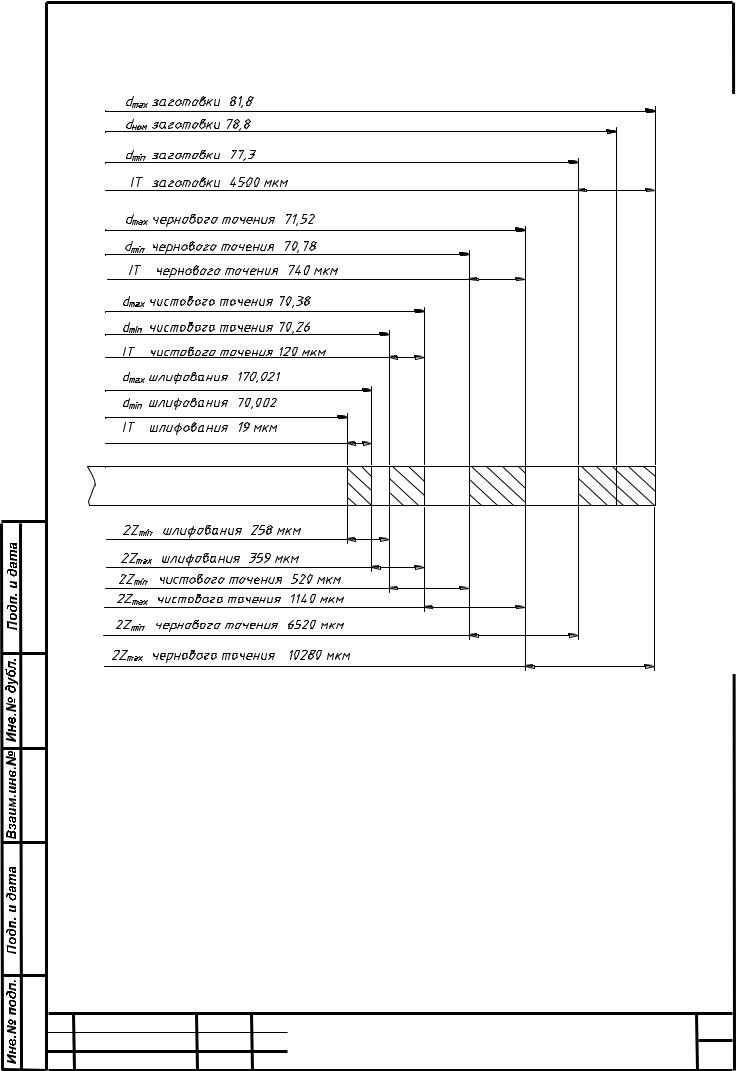
Графическая схема расположения припусков и допусков на обработку |
поверхности Ø70k6( 0,021 ) представлена на рисунке 3.2. |
0,002 |
Рисунок 5.2 – Схема графического расположения припусков и допусков |
на обработку поверхности Ø70k6( 0,021 ) |
0,002 |
На все остальные обрабатываемые поверхности назначаем припуски по |
ГОСТ 7505-89. Расчетные и табличные припуски заносим в таблицу 5.3. |
|
|
|
Лист |
|
|
КП.ПТП.40.15.012.00.00.ПЗ. |
16 |
Из Лист |
№ Докум. Подп Дата |
|
|
|
|
|
|
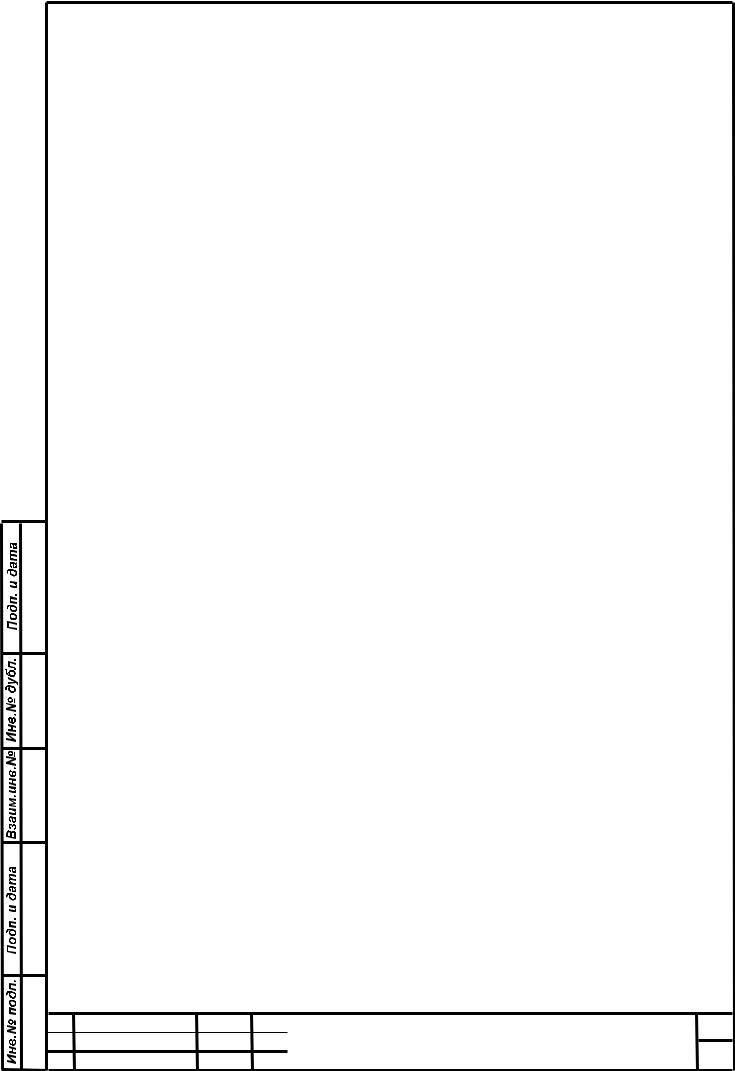
Таблица 5.3 – Припуски и предельные отклонения на обрабатываемые поверхности вала-шестерни
Размер детали |
Припуск |
|
Предельные откло- |
|
Табличный |
|
Расчѐтный |
нения |
|
|
|
|||
Ø150 0,0280,003 |
– |
|
2 4,8 |
+3,3 |
|
|
|
|
–1,7 |
Ø152 0,0280,003 |
2 4,5 |
|
– |
+3,3 |
|
|
|
|
–1,7 |
Ø 250,8 1,3 |
2 5,0 |
|
– |
+4,2 |
|
–2,1 |
|||
|
|
|
|
|
Ø165 1,0 |
2 4 |
|
– |
+3,7 |
|
–1,9 |
|||
|
|
|
|
|
Ø100 0,74 |
2 4 |
|
– |
+3,0 |
|
–1,5 |
|||
|
|
|
|
|
Ø 70 0,021 |
2 4,4 |
|
|
+3,0 |
0,002 |
|
|
|
–1,5 |
|
|
|
|
|
815 1,4 |
2 4,5 |
|
– |
+5,3 |
|
–2,7 |
|||
|
|
|
|
6 Расчет режимов резания и норм времени
6.1 Расчѐт режимов резания аналитическим методом
Используя аналитические формулы и справочные данные, приведенные в справочнике технолога-машиностроителя [5] производим расчѐт режимов резания на токарную и вертикально-фрезерную операции.
Расчѐт режимов резания на операцию №15–токарную с ЧПУ.
На токарном станке с ЧПУ мод. 16К20Т1 производится черновое то-
чение поверхностей Ø70,Ø100,Ø150,Ø165.
Инструменты – резец контурный, оснащѐнные пластинками из твѐрдого сплава Т15К6 ГОСТ 18882–73.
Глубина резания t 3,5 мм. Определяем величину подачи
S0 0,7 1,2 мм/об.
Учитывая жѐсткость системы станок–приспособление–инструмент– деталь принимаем S0 0,7 мм/об.
Принимаем по паспорту станка S0 0,7 мм/об. Определяем скорость резания
|
|
|
CV |
|
KV , |
(6.1) |
|
|
|
T m t x |
S y |
||||
|
|
|
|
|
|
||
|
|
|
|
0 |
|
|
|
где T – стойкость инструмента, мин; |
|
|
|
|
|||
|
|
|
|
|
|
|
Лист |
|
|
|
|
|
|
|
|
|
|
|
КП.ПТП.40.15.012.00.00.ПЗ. |
|
17 |
||
Из Лист |
№ Докум. Подп Дата |
|
|
|
|
|
|
|
|
|
|
|
|
|
|
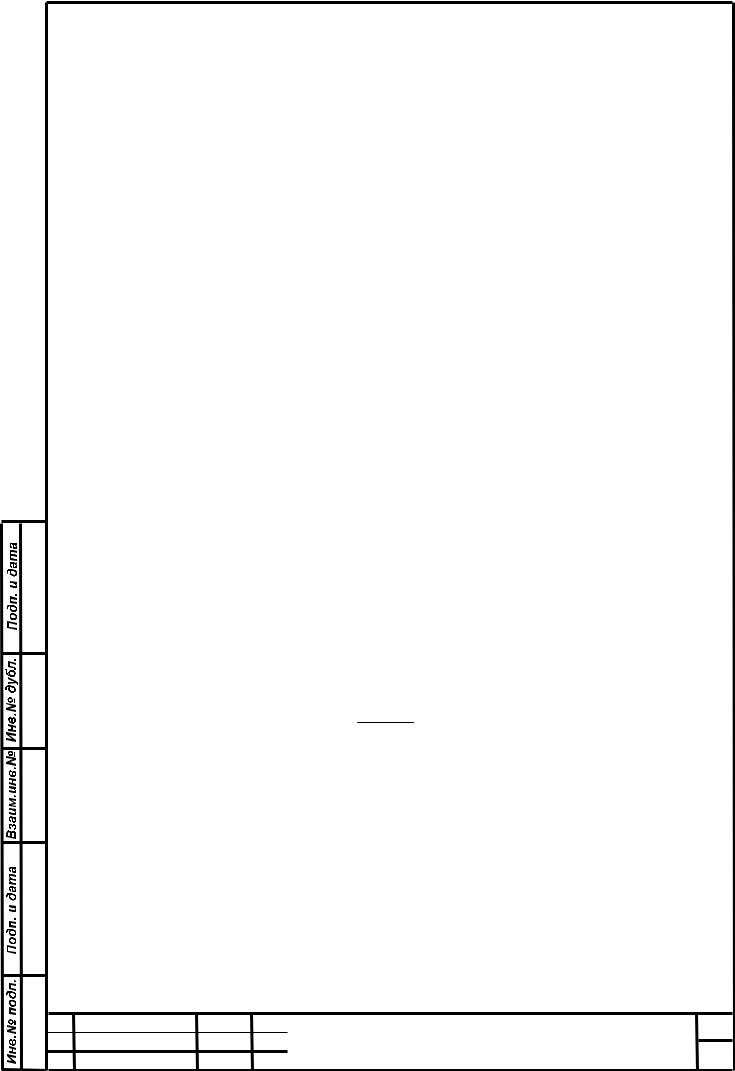
KV – общий поправочный коэффициент на скорость резания. |
|
|||||||||||
|
|
KV KMV K ПV KUV , |
|
|
(6.2) |
|||||||
где K MV – коэффициент, учитывающий обрабатываемый материал; |
|
|||||||||||
K ПV – коэффициент, учитывающий состояние поверхности заготовки; |
||||||||||||
KUV – коэффициент, учитывающий материал инструмента. |
|
|||||||||||
|
|
KV |
0,9 1 1 0,9 . |
|
|
|
||||||
340 |
|
|
|
|
|
|
|
|
|
|||
|
|
|
|
0,75 113,46 м/мин. |
|
|||||||
500,2 3,50,15 0,70,45 |
|
|||||||||||
Определяем частоту вращения шпинделя |
|
|
|
|||||||||
n |
1000 113,46 |
|
219 |
мин 1 . |
|
|
|
|||||
3,14 165 |
|
|
|
|||||||||
|
|
|
|
|
|
|
|
|
|
|||
Принимаем по паспорту станка |
nä 200 |
|
мин 1 ,тогда действительная |
|||||||||
скорость резания определяется по формуле |
|
|
|
|||||||||
|
|
|
д |
D n . |
|
|
(6.3) |
|||||
|
|
|
|
|
|
1000 |
|
|
|
|||
|
|
д |
3,14 165 200 |
103,62 |
мин 1 . |
|
||||||
|
|
1000 |
|
|
|
|
||||||
|
|
|
|
|
|
|
|
|
|
|||
Определяем минутную подачу по формуле |
|
|
||||||||||
|
|
|
SM S0 n . |
|
|
(6.4) |
||||||
|
|
SM 0,7 160 112 мм/мин. |
|
|||||||||
Определяем силу резания по формуле |
|
|
|
|||||||||
|
|
P |
10 C |
P |
t x S y n K |
p |
, |
(6.5) |
||||
|
|
Z |
|
|
|
|
|
0 |
|
|
где K p – поправочный коэффициент на силу резания.
Поправочный коэффициент на силу резания определяется по формуле
KP KMP K P K P K P KrP . |
(6.6) |
KP 1,24 0,89 1 1 0,93 1,13 .
P 10 300 3,51 |
0,70,75 103,62 0,15 1,13 4526 Н. |
Z |
|
Мощность рассчитываем по максимальной силе резания по формуле
N |
PZ |
|
1020 60 . |
(6.7) |
N |
4526 103,62 |
7,66 кВт. |
|
|
|||
|
1020 60 |
|
|
Проверяем достаточную мощность станка. |
|||
У станка модели 16К20Т1 Nшп Nдв . |
(6.8) |
||
Nшп 10 0,8 8 кВт. |
|
||
Обработка возможна при условии, что |
Nшп > N . Следовательно, обра- |
ботка на данном станке возможна, т.к. 8кВт > 7,66кВт.
Расчет режимов резания на операцию №40 – зубофрезерную.
|
|
|
Лист |
|
|
КП.ПТП.40.15.012.00.00.ПЗ. |
18 |
Из Лист |
№ Докум. Подп Дата |
|
|
|
|
|
|
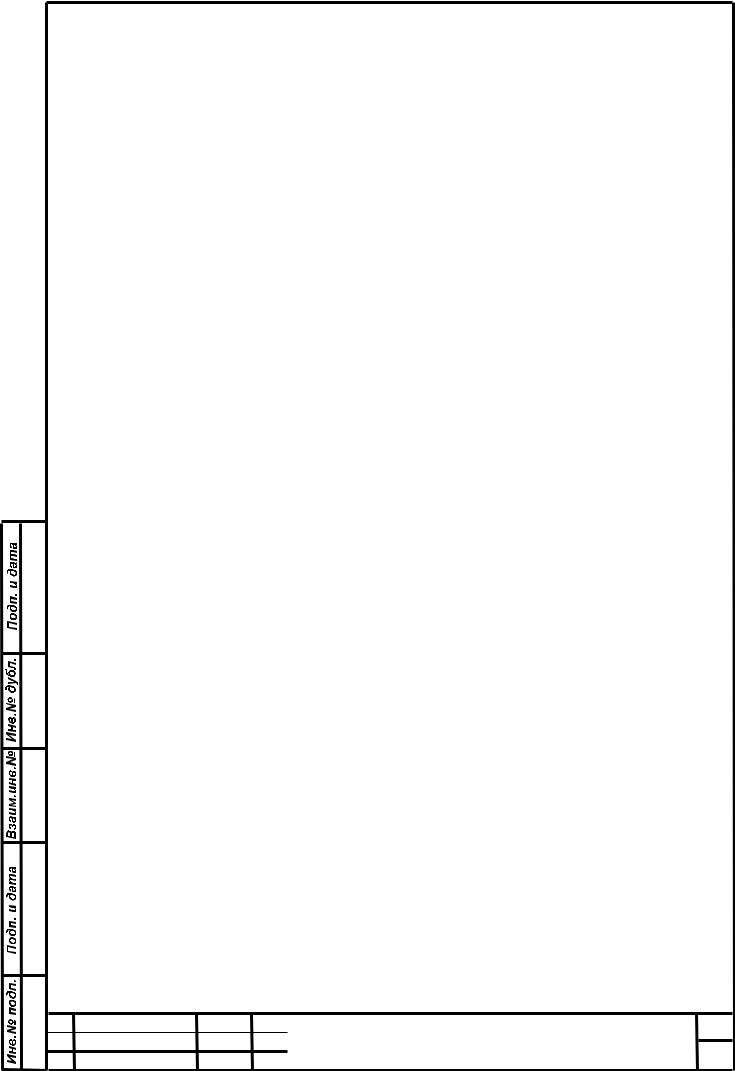
На станке модели 5К328А нарезаются зубья m=10 мм в количестве 22. Наружный диаметр зубчатого венца D=250,8 мм, ширина зубчатого венца b=265 мм. Обрабатываемый материал сталь 40Х ГОСТ4543–71.
Инструмент– червячная модульная фреза. Материал режущей части
быстрорежущая сталь Р6М5 ГОСТ 9324–80. |
|
|
Геометрические параметры: D=150 мм, d=50 мм, L=170 мм, z=9. |
|
|
Определяем глубину резания по формуле |
|
|
t 2,2 |
m . |
(6.9) |
t 2,2 10 |
22 мм. |
|
Определяем величину подачи на один оборот нарезаемого колеса
S0 2,16 2,55 мм/об.
Учитывая жѐсткость системы станок-приспособление-деталь (СПИД) принимаем S0 2,16 мм/об.
Принимаем по паспорту станка S0 2,0 мм/об. Определяем скорость резания
|
CV |
|
KV , |
(6.10) |
||
T S |
0 |
m X |
||||
|
|
|
||||
|
|
|
|
|
||
где – скорость резания, м/мин; |
|
|
||||
T – период стойкости фрезы, мин; |
|
|
||||
KV – общий поправочный коэффициент на скорость резания. |
|
|||||
KV KMV KЗV |
KWV KV K V KIV , |
(6.11) |
где K MV – коэффициент, учитывающий механические свойства обраба-
тываемого материала;
K ЗV – коэффициент, учитывающий число заходов фрезы;
KWV – коэффициент, учитывающий осевое перемещение фрезы; KV – коэффициент, учитывающий точность;
K V – коэффициент, учитывающий положение зубьев нарезаемого ко-
леса;
K IV – коэффициент, учитывающий число проходов.
|
KV 0,9 1 1 1 1 1 0,75 . |
||||||
|
350 |
|
|
0,9 31,9 м/мин. |
|||
|
|
|
|
|
|||
1800,33 2,00,5 100,1 |
|||||||
Определяем частоту вращения шпинделя по формуле |
|||||||
|
n |
1000 |
. |
(6.12) |
|||
|
|
||||||
|
|
|
D |
|
|||
|
n |
1000 31,9 |
67,7 |
мин 1 . |
|||
|
|
||||||
|
|
3,14 150 |
|
||||
Принимаем по паспорту станка nд 63 |
мин 1 ,тогда действительная |
скорость резания определяется по формуле
|
|
|
Лист |
|
|
КП.ПТП.40.15.012.00.00.ПЗ. |
19 |
Из Лист |
№ Докум. Подп Дата |
|
|
|
|
|
|
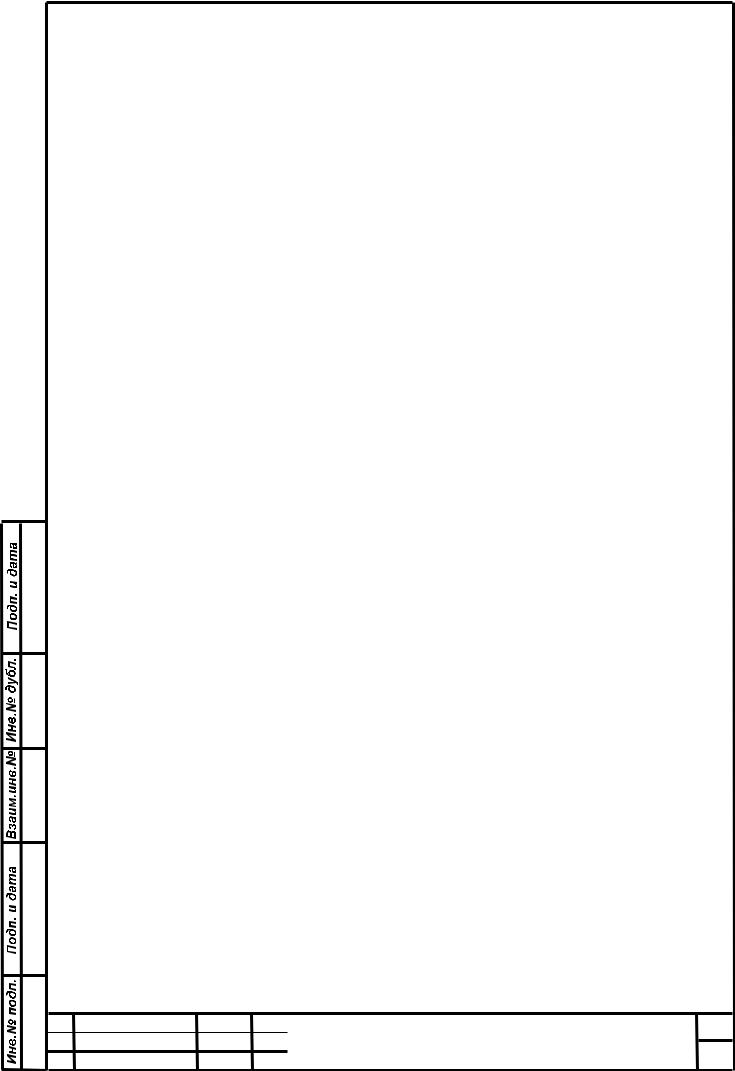
|
|
д D n . |
(6.13) |
||
|
1000 |
|
|
|
|
|
ä |
3,14 150 63 |
|
29,6 мин 1 . |
|
|
|
|
|||
|
1000 |
|
|
|
|
Определяем мощность резания |
|
|
|||
|
N 10 3 CN s y m X Du z q K N , |
(6.14) |
|||
где |
D – диаметр фрезы, мм; |
|
|
||
z – число зубьев нарезаемого колеса, шт.; |
|
||||
K N – поправочный коэффициент на мощность резания. |
|
||||
|
N 10 3 124 20,9 101,7 150 1 |
220 29,6 1 2,28 кВт |
|
||
Проверяем достаточность мощности привода станка. |
|
||||
У станка мод. 5К328А |
|
|
|||
|
Nшп Nдв , |
|
(6.15) |
||
где |
Nдв – мощность двигателя, кВт; |
|
|
– К.П.Д. станка.
Nшп 10 0,65 6,5 кВт
Обработка возможна при условии Nшп > N .Следовательно обработка на данном станке возможна, т.к. 6,5кВт>2,28кВт.
6.2 Расчѐт режимов резания по нормативам
Расчет режимов резания производим по справочнику [5].
Расчѐт режимов резания на операцию №20 – радиально-сверлильную. Переход 1. Сверление отверстия Ø17,35.
Определяем подачу на оборот сверла
S0 0,32 мм/об.
Принимаем по паспорту станка S0 0,3 мм/об. |
|
Определяем скорость резания |
|
табл K1 K2 K3 , |
(6.16) |
где табл – табличная скорость резания, м/мин; |
|
K1 – коэффициент, зависящий от обрабатываемого материала; K 2 – коэффициент, зависящий от стойкости инструмента;
K3 – коэффициент, зависящий от отношения длины резания к диаметру.
22 0,7 1,25 1,0 19,25 м/мин
Рассчитываем число оборотов шпинделя станка по формуле
|
|
|
Лист |
|
|
КП.ПТП.40.15.012.00.00.ПЗ. |
20 |
Из Лист |
№ Докум. Подп Дата |
|
|
|
|
|
|
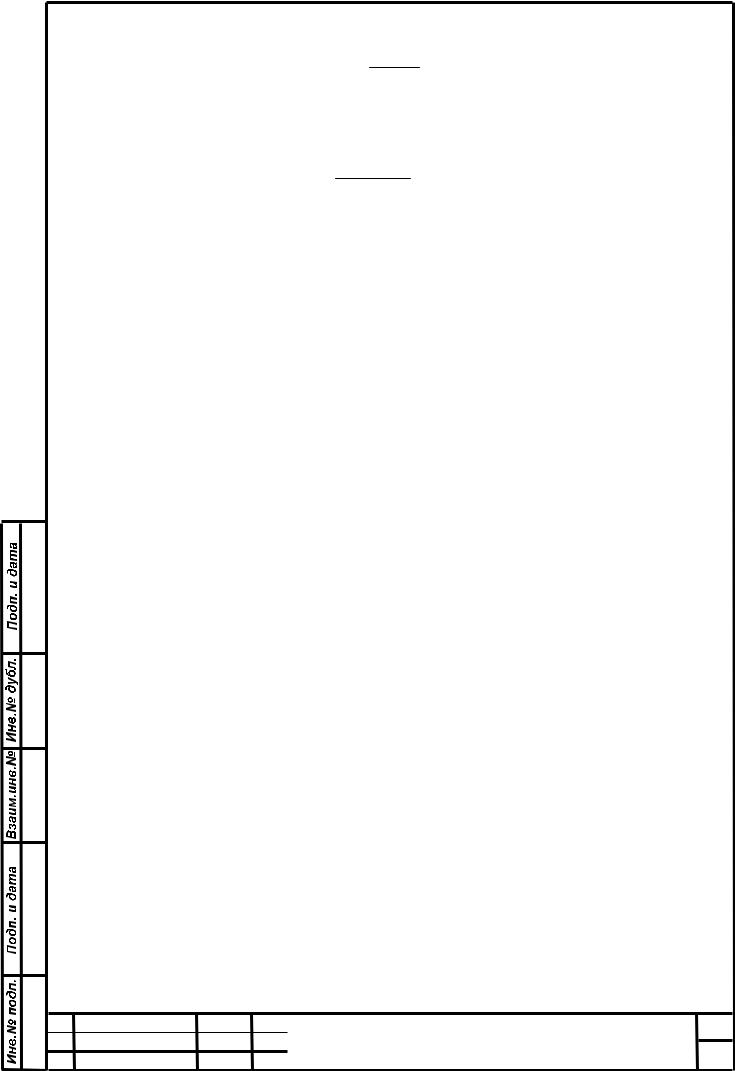
n 1000 ,
d
где d – диаметр сверла, мм.
n 1000 19,25 353,35 об/мин. 3,14 17,35
Принимаем по паспорту станка n 315 об/мин. Определяем минутную подачу по формуле
SM S0 n .
SM 0,3 315 94,5 мм/мин.
(6.17)
(6.18)
Уточняем скорость резания по принятому числу оборотов по формуле
|
|
д |
d n . |
(6.19) |
|
|
|
|
1000 |
|
|
д |
|
3,14 17,35 315 |
17,16 м/мин |
||
|
1000 |
|
|||
|
|
|
|
|
Переход 2. Рассверливание отверстия Ø17,35 в Ø21+0,4.
Определяем подачу на оборот сверла
S0 0,4 мм/об.
Принимаем по паспорту станка S0 0,3 мм/об.
Определяем скорость резания
24 0,7 1,25 1,0 21 м/мин.
Рассчитываем число оборотов шпинделя станка
|
n |
1000 21 |
|
318,47 об/мин. |
|
|
|
|
|||
|
|
3,14 21 |
|
|
|
|
Принимаем по паспорту станка n 315 об/мин. |
|
|||
|
Определяем минутную подачу |
|
|||
|
SM 0,3 315 94,5 мм/мин. |
|
|||
|
|
|
|
|
Лист |
|
|
|
|
|
|
|
|
|
|
КП.ПТП.40.15.012.00.00.ПЗ. |
21 |
Из Лист |
№ Докум. Подп Дата |
|
|
|
|
|
|
|
|
|
|
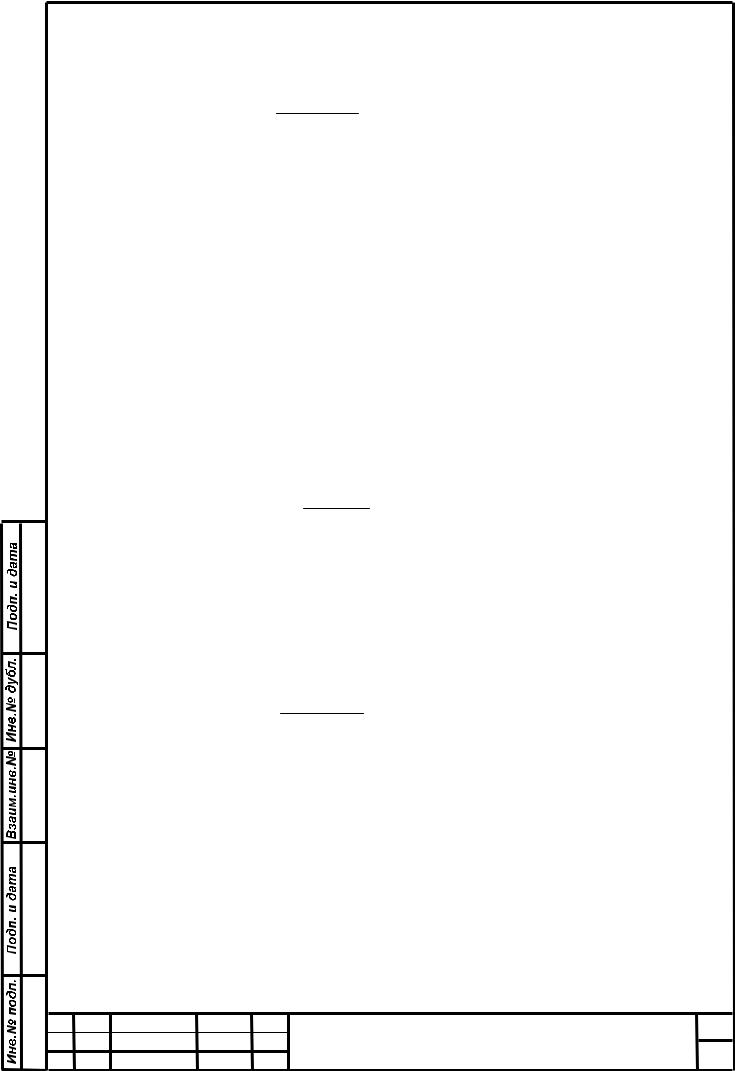
Уточняем скорость резания по принятому числу оборотов
д 3,14 21 315 20,77 м/мин. 1000
Переход 3. Зенкование конуса в размеры 6 0,1; Ø28+0,4.
Определяем подачу на оборот зенковки
S0 0,15 мм/об.
Принимаем по паспорту станка S0 0,15 мм/об
Определяем скорость резания
36 0,7 1,25 1,0 31,5 м/мин.
Рассчитываем число оборотов шпинделя станка
n 1000 31,5 358,28 об/мин. 3,14 28
Принимаем по паспорту станка n 315 об/мин. Определяем минутную подачу
мм/мин.
Уточняем скорость резания по принятому числу оборотов
д 3,14 28 315 27,7 м/мин. 1000
Переход 4. Нарезание резьбы М20.
Определяем подачу на оборот метчика
S0 2,5 мм/об
Принимаем по паспорту станка S0 2,5 мм/об
Определяем скорость резания по формуле
КП.ПТП.40.15.012.00.00.ПЗ.
Из Лист № Докум. Подп Дата
Лист
22