
Лабы
.pdfд) Перерасчет бетона на заданную марку
Перерасчет состава бетона на заданную марку производится следующим образом.
Определяют истинную активность цемента в бетоне по формуле
Rц = R28 / (А· ( Ц/В± 0,5 )) = ____________________________= кгс/см²,
где коэффициент А изнак(+) или(-) берутсявсоответствиистойформулой, по которой определялось Ц/В при расчете состава бетона; R28 – прочность бетонапробногозамеса, приведенная к стандартной в возрасте 28 суток; Ц/В – цементноводное
отношение полученного состава бетонной смеси; Rц - искомая активность цемента.
Определяют цементноводное отношение по формуле
Ц/ В = Rб / (А· Rц ± 0,5) = __________________________=,
где Rб - заданная марка бетона; Rц - активность цемента, найденная из предыдущего определения.
Определяют расход цемента путем умножения вычисленного значения Ц/В на величину расхода воды в литрах, полученную при опытном подборе состава бетона.
Ц= Ц/В·В= ____________________=_______ кг.
Врезультате произведенного перерасчета назначается состав бетона, в котором изменяется расход цемента, а расходы остальных материалов ( воды, песка, крупногозаполнителя) принимаютсятакими, каквподобранномсоставе бетона(табл. 7).
Таблица 7
Цемент, кг |
Песок, кг |
Крупный заполнитель, кг |
Вода, л |
|
|
|
|
|
|
|
|
51
Контрольные вопросы
1.Чтотакоебетон, иизкакихматериаловегоизготовляют?
2. Какиетребования предъявляютсяк качеству мелкогоикрупного заполнителейдлябетона?
3. Укажите факторы, влияющие на твердениеисвойства бетона. 4 .Как влияет температура на твердение и свойства бетона?
5.Как изменится подвижность бетонной смеси и свойства бетона с повышением водоцементногоотношения?
6.Какопределитьподвижностьиудобоукладываемостьбетоннойсмеси? Какие факторывлияютнаэтисвойства?
7.Как ускоряют твердение бетонной смеси?
8.Как изменится прочность бетона при увеличении марки цемента?
9.Как изменятся свойства бетона при увеличении расхода цемента?
10.Как влияет содержание воды в бетонной смеси на прочность бетона? 11.Как влияет ( при прочих равных условиях ) содержание песка на прочность бетона?
12.Воспроизведитесхемурасчетаоптимальногосоставатяжелогобетона.
52
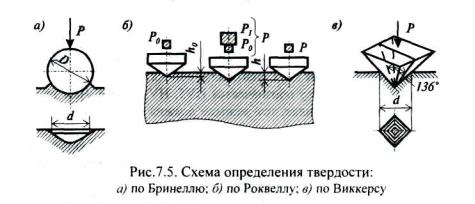
Лабораторная работа 9
ОПРЕДЕЛЕНИЕ ТВЕРДОСТИ МЕТАЛЛОВ
Цель работы: освоениеметодовопределениятвердостиметаллов. Оборудование и материалы: металлические образцы; стальной шарик;
штангенцир- куль; испытательнаямашина.
Твердость материала – сопротивление проникновению в поверхность стандартного тела – наконечника (индентора). Например, шарика, конуса, не деформирующихся при испытании.
Прямые испытания на твердость состоят в том, что в образец вдавливаютспециальныйтвердыйнаконечник(иззакаленнойстали, алмазаили сплава) различной формы (шарик, конус, пирамида). После снятия нагрузки остается отпечаток, величина которого характеризует твердость образца. При косвенных методах оцениваются свойства металла, пропорциональные его твердости. Общим для всех методов является создание местных контактных напряжений при воздействии стандартного наконечника на испытуемую поверхность. Они получили широкое распространение благодаря быстроте и простоте, портативности оборудования, а также возможности проводить испытания на готовых деталях (изделиях) без их разрушения. Испытание на твердость – основной метод оценки качества термической обработки изделия. Наибольшее распространение на практике получили методы Бринелля, Роквелла, Виккерса.
53
Твердость по Бринеллю определяют статическим вдавливанием в испытуемую поверхность под нагрузкой (Р) стального закаленного шарика диаметром (D). Число твердости НВ определяют отношением нагрузки Р к сферической поверхности отпечатка – лунки (шарового сегмента) F диаметром d поформуле
НВ= Р/F = 2·P/{3.14· D· [D – √(D²– d ²)]}.
Диаметр шарика D = 10; 5; 2,5 мм выбирают в зависимости от толщины изделия. Для небольших изделий учитывают также размеры поверхности для измерения, т. к. расстояние от центра отпечатка до края изделия должно составлять не менее 2,5 мм.
Нагрузку Р выбирают в зависимости от диаметра шарика и измеряемой твердости, которую приближенно оценивают с учетом природы сплава и способаегообработки. Длятермическиобработаннойсталиичугуна Р= 30D², для литой бронзы, меди и латуни Р= 10D², для алюминия Р= 2,5D².
Продолжительность выдержки под нагрузкой для стали и чугуна составляет 10 с, для латуни, меди и бронзы 30 с.
Так как значения D и Р заранее известны, то для определения числа
твердости необходимо лишь измерить диаметр |
отпечатка |
d и найти |
соответствующую твердость по таблицам. |
|
|
В ГОСТах и справочниках число твердости по Бринеллю при испытании |
||
шариком с D = 10 мм, Р = 30000 Н, τ = 10 с обозначается цифрами, |
||
характеризующими значение твердости (кгс/мм²), |
и буквами |
НВ. Например, |
185НВ или при других условиях после букв НВ |
указываются эти условия в |
следующемпорядке: диаметршарика(мм), нагрузка(кгс) ипродолжительность выдержки под нагрузкой (с), например, 175 НВ 5/750/20. По методу Бринелля нельзяиспытыватьметаллысчисломтвердостивыше 450НВ, т. к. шарикбудет деформироваться и результат получится неправильным.
Для многих материалов, определив число твердости НВ, можно найти предел прочности (σ), т. к. твердость и прочность связаны простым отношением: σ= k·НВ, где k - величина, зависящаяотматериала(например, для мягкой стали k = 0,34, литой стали k = 0,3 – 0,4, меди и ее сплавов k = 0,55, алюминиевых сплавов k = 0,35 – 0,36 и т. д.).
По методу Роквелла твердость определяют вдавливанием в изделие стальногошарикадиаметром 1,59 ммпритвердостиопределяемогометаллане более 2200 МПа (нагрузка 1000 Н) или алмазного конуса с углом 120º при испытании более твердых материалов (нагрузка 1500 Н) и при испытании сверхтвердых сплавов (нагрузка 6000 Н). Вдавливание в образец шарика или
54
конуса на приборе происходит под действием двух нагрузок: предварительной Ро, равнойвсегда 100 Н, иосновной Р1 при вдавливаниишарикасилой 900 Н (шкала В), силой 1400 Н (шкала С) и 5000 Н (шкала А). Общая нагрузка Р равна сумме этих нагрузок: Р= Ро+ Р1.
Взависимостиоттого, применяютсястальнойшарикилиалмазныйконус,
атакжеотнагрузок, прикоторыхпроводятиспытание(тоестьпокакойшкале- В, С или А), число твердости обозначают НRВ, НRС, НRА. Определение твердости проводят на приборе Роквелла. По показаниям большой стрелки циферблата определяют твердость, которая является условной величиной, характеризующей разность глубин отпечатков. Для перевода параметров твердости по Роквеллу в параметры твердости по Бринеллю пользуются переводной таблицей.
Преимуществом способа Роквелла является быстрота измерения. Применение алмазного конуса позволяет измерить твердость закаленной стали и других очень твердых материалов, тонких изделий или поверхностного слоя толщинойдо 0,4 мм (шкалаА) и до 0,7 мм (шкалаВиС).
Недостаток измерения твердости по методу Роквелла заключается в том, что необходима тщательная подготовка поверхности – шлифование. На приборе Роквелла, где глубина отпечатка мала и ее измеряют с точностью до 0,002 мм (цена деления – условная единица твердости), могут оказать влияние загрязненность, вибрация и другие условия производства.
Метод испытания вдавливанием алмазной пирамиды (метод Виккерса) используют для определения твердости деталей малой толщины и тонких поверхностных слоев, имеющих высокую твердость. При испытании в металл вдавливают четырехгранную пирамиду (с углом при вершине α = 136º ) под нагрузкой от 50 Н до 1000 Н.
Диагональ отпечатка измеряют с помощью микроскопа, укрепленного на приборе, и по полученным показаниям определяют число твердости, обозначаемоеНV, какудельноедавлениенаединицуповерхностиотпечатка:
НV = 2·Рsin(α/2)/d²= 1,8544· P/d²,МПа,
где Р – |
нагрузка на пирамиду, Н; |
d – среднее |
арифметическое двух |
диагональныхотпечат- ков, замеренных после снятия нагрузки, м. |
|||
Преимущество метода Виккерса – |
возможность |
измерения твердости |
|
мягких, |
а также особо твердых материалов. |
|
55
Задание1. Определение твердости металлов по методу Бринелля
1. Получить металлический образец и подготовить его к испытанию. Общие требования к проведению испытаний:
а) прилагаемая нагрузка должна действовать перпендикулярно поверхности
образца; |
|
|
|
|
||
б) нагрузка должна |
прилагаться и возрастать плавно. |
|||||
2. |
В зависимости |
от толщины испытываемого образца выбрать нагрузку |
||||
|
индентора |
|
|
|
|
|
( табл. 1.). |
|
|
|
|
||
|
|
|
|
|
|
Таблица 1 |
|
|
|
|
|
|
|
№ |
|
Индентор |
|
Диаметр, |
Нагрузка, |
Толщинаобраз- |
п/п |
|
|
|
мм |
кН |
ца, мм(сплав) |
|
|
|
|
|
|
|
1. |
|
Стальнойшарик |
10 |
30 |
10 (сталь, чугун) |
|
2. |
|
Стальнойшарик |
5 |
10 |
5 (бронза, латунь) |
|
3. |
|
Стальнойшарик |
2,5 |
2,5 |
2,5 (алюминий) |
|
|
|
|
|
|
|
|
Контрольные вопросы
1.Что такое твердость?
2.Какиеметодыизмерениятвердостисуществуютнапрактике?
3.Покакомупринципуосуществляютсяметодыизмерениятвердости?
4.КаквыбираетсянагрузкаприиспытаниинатвердостьпоБринеллю?
5.Какова размерность и как обозначается твердость, замеренная по Бринеллю?
6.Вчемзаключаетсяпринципиальноеотличиеспособовзамератвердости
по Бринеллю, Роквеллу, Виккерсу?
7. В каких случаях применяются алмазный конус или пирамида, а в каких – стальной шарик?
8э. Какиепреимуществаметодаопределениятвердости поВиккерсу?
56
Лабораторная работа 10
ИЗУЧЕНИЕ ДИАГРАММЫ СОСТОЯНИЯ ЖЕЛЕЗО – ЦЕМЕНТИТ
Цель работы: освоениедиаграммысостоянияжелезо- цементит
Сплавы железа с углеродом (стали и чугуны) являются наиболее
распространенными металлическими материалами. |
|
Для технически чистогожелеза температура плавления равна |
1539 ± 5ºС, |
плотность 7,85 кг/м³. Железо обладает невысокой твердостью |
НВ 50-70, |
хорошей пластичностью, до температуры 768 ºС обладает |
магнитными |
свойствами, апри 768 ºС(точкаКюри) теряетих. Имеетдвеаллотропические
модификации |
α-железо и γ-железо. Альфа-модификация существует при |
температуре ниже |
911ºС и выше 1401ºС, а от 911ºС до 1401ºС – гамма- |
модификация. Железо в чистом виде не имеет широкого применения, поэтому имеютместосплавыжелезасуглеродом.
В зависимости от содержании углерода железоуглеродистые сплавы подразделяются на стали и чугуны. Сталями называются железоуглеродистые сплавы, содержание углерода в которых не превышает 2,14%; содержание углерода до 0,8% - доэвтектоидные, 0,8% - эвтек- тоидные и более 0,8% - заэвтектоидные. Чугунами называют сплавы железа с углеродом, содержащие углерода более 2,14%; содержание углерода более 2,14% -доэвтектические, 4,3% - эвтектические, более 4,3% - заэвтектические.
Кривая охлаждения или нагревания жидких расплавов металла не является плавной и имеет ряд остановок и перегибов, что связано с соответствующими превращениями, протекающими в них. Такие места на температурнойкривойназываются критическими.
Металлы преимущественно кристаллизуются в виде объемно- центрированных, гране-центрированных кубических, гексагональных и орторомбическихрешеток.
Для изучения структурных составляющих рассмотрим диаграмму состояния железо- цементит. Фазовые составляющие представлены в табл. 1
57
|
|
|
|
|
|
|
Таблица1 |
|
|
|
|
|
|
|
|
|
|
Железо- |
|
|
|
|
|
|
|
|
углеродистый |
Составляющие |
Условия образования и физ- |
Твердость, |
|
||||
сплав |
|
сплава |
|
зические свойства |
НВ |
|
||
|
|
|
|
|
||||
Аустинит |
Твердый раствор |
При затвердевании жидкого |
170 - 220 |
|
||||
|
углерода в γ- же- |
раствора с содержанием угле- |
|
|
||||
|
лезе. Содержит до |
рода не более 4,3%. Мягок, |
|
|
||||
|
2% углерода |
не обладает магнитными |
|
|
||||
|
|
|
|
|
свойствами, тягуч, мало упруг. |
|
|
|
|
|
|
|
|
||||
|
Твердый раствор |
При медленном охлаждении |
|
|
||||
Феррит |
углерода и дру- |
доэвтектоидной стали выде- |
60 – 100 |
|
||||
|
гих элементов |
ляется из аустенита. Мягок, |
|
|
||||
|
в α-железе.Содер- |
очень тягуч, при температу- |
|
|
||||
|
жит до 0,006% |
ре ниже точки Кюри обладает |
|
|
||||
|
углерода |
|
|
магнитными свойствами |
|
|
||
|
|
|
|
|
|
|||
|
Химическое сое- |
Первичный – |
из жидкого рас- |
|
|
|||
Цементит |
динение железа с |
твора при содержании углеро- |
820 |
|
||||
|
углеродом – |
кар- |
да свыше 4,3%; вторичный - |
|
|
|||
|
бит железа Fe3С. |
из аустенита при медленном |
|
|
||||
|
Содержание угле- |
охлаждении. |
|
|
|
|||
|
рода 6,67% |
|
Твердый, хрупок. До темпера- |
|
|
|||
|
|
|
|
|
туры 210 ºС обладает магнит- |
|
|
|
|
|
|
|
|
ными свойствами. При темпе- |
|
|
|
|
|
|
|
|
ратуре 210 ºС теряет их |
|
|
|
|
|
|
|
|
||||
|
Эвтектоидная |
При медленном охлаждении |
|
|
||||
Перлит |
смесь цементита с |
аустенита в результате диф- |
160 – 230 |
|
||||
|
ферритом |
|
|
фузии углерода. |
|
|
||
|
|
|
|
|
Более тверд и прочен, чем фер- |
|
|
|
|
|
|
|
|
рит, но менее пластичен. Обла- |
|
|
|
|
|
|
|
|
дает магнитными свойствами |
|
|
|
|
|
|
|
|
|
|||
|
Эвтектическая |
Образуется |
при затвердева- |
|
|
|||
Ледебурит |
смесь аустенита и |
нии жидкого сплава с содер- |
600 |
|
||||
|
цементита |
при |
жанием углерода свыше 2%. |
|
|
|||
|
температуре |
вы- |
Хрупок |
|
|
|
||
|
ше |
723º С и пер- |
|
|
|
|
||
|
лита |
с |
цементи- |
|
|
|
|
|
|
том |
при |
темпера- |
|
|
|
|
|
|
туре ниже 723º С. |
|
|
|
|
|||
|
Содержание |
угле- |
|
|
|
|
||
|
рода 4,3% |
|
|
|
|
|
Надиаграммеданыфазовыйсоставиихструктуравинтервалепосоставу от чистого железа до цементита (6,67% С). на оси абсцисс показано содержание углерода (С) в процентах по массе, а на параллельной ей линии – содержаниецементита, наосиординат– температура.
58
Точка А на диаграмме отмечает температуру плавления чистого железа, а точка D – цементита. В сплавах цементит является метастабильной фазой. Его температураплавленияравнапримерно 1500ºС.
Первичная кристаллизация сплавов системы железо-углерод начинается подостижениитемператур, соответствующихлинииАВСД(линияликвидус), и заканчиваетсяпритемпературах, образующихлиниюАНJEGF (линиясолидус). Процесс первичной кристаллизации сталей заканчивается по линии АНJE, а если по линии АВ, то из жидкого раствора выделяются кристаллы твердого растворауглеродавα- железе. Процесскристаллизациисплавовссодержанием углерода до 0,1% заканчивается по линии АН с образованием α-твердого раствора. Налинии НJВпротекаетперитектическоепревращение, врезультате которого образуется твердый раствор углерода в γ-железо, т.е. аустенит. Процесс первичной кристаллизации сталей заканчивается по линииАНJE.
При температурах, соответствующих линии ВС, из жидкого раствора кристаллизуется аустенит. В сплавах, содержащих от 4,3% до 6,67% углерода, при температурах, соответ- ствующих линии СД, начинают выделяться кристаллы цементита первичного. Цементит, кристаллизующийся из жидкой фазы, называется первичным. В точке С при температуре 1147ºС и концентрации углерода в жидком растворе 4,3% образуется эвтектика, которая называется ледебуритом. Эвтектическое превращение с образованием ледебурита можно записать формулой ЖР4,3 – ( А2,14 + Ц6,67). Процесс первичной кристаллизации чугунов заканчивается по линии ЕСF образованием ледебурита. Структура чугунов ниже 1147ºС такова: доэвтектический – аустенит + ледебурит, эвтектических – ледебурит и заэвтекти- ческих – цементит (первичный) + ледебурит.
Превращения, происходящиевтвердомсостоянии, называютсявторичной кристаллизацией. Они связаны с переходом при охлаждении γ-железа в α- железо ираспадом аустенита.
Линия GS соответствует температурам начала превращения аустенита в феррит. НижелинииGS сплавысостоятизферритаиаустенита.
Линия ES показывает температуры начала выделения цементита из аустенита. Цементит, выделяющийся из аустенита, называется вторичным цементитом.
В точке S при температуре 727º С и концентрации углерода в аустените 0,8% образуется эвтектоидная смесь, состоящая из феррита и цементита, которая называется перлитом. Про- цесс превращения аустенита в перлит можнозаписать формулой А-0,8П(Ф0,03 + Ц6,67).
59
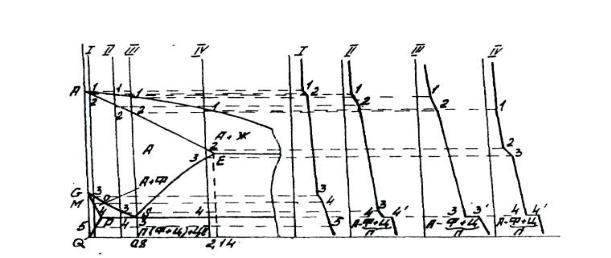
Линия РQ показывает на уменьшение растворимости углерода в феррите при охлаж- дении и выделении цементита, который называется третичным цементитом.
Следовательно, сплавы, содержащие менее 0,008% углерода (точка Q), являются однофазными и имеют структуру чистого феррита, а сплавы, содержащие от 0,008 до 0,03% углерода, структуру феррит + цементит третичныйиназываются техническим железом.
Доэвтектоидные стали при температуре ниже 727ºС имеют структуру феррит + перлит, эвтектоидные – перлит и заэвтектоидные перлит + цементит вторичный.
В доэвтектических чугунах в интервале температур 1140 – 727º С при охлаждении из аустенита, вследствие уменьшения растворимости углерода (линия ЕS), выделяется цементит вторичный. По достижении температуры 727ºС (линия РSК) аустенит, обедненный углеродом до 0,8% (точка S), превращается в перлит. Таким образом, после окончательного охлождения структура доэвтектических чугунов состоит из перлита, цементита вторичного иледебуритапревращенного(перлит+ цементит).
Структураэвтектическихчугуновпритемпературениже727º Ссостоитиз ледебуритапревращенного. Заэвтектическийчугунпритемпературахниже727º С состоит изледебу- рита превращенного и цементита первичного.
Превращения, протекающие при охлаждении сплавов с различным содержанием углерод
Рис2. Частьдиаграммысостояния«железо-углерод» (до2,14 % С)
60