
Краткий курс лекций_2012 НИЯЗОВ
.pdfметре волокон 9 мкм. Торцы световодов полируют. Такой пучок передает изо-
бражение, сформированное линзами объектива, на окуляр (рис. 2.14).
При использовании световодов следует иметь в виду, что они могут силь-
но деполяризовать проходящий свет.
Разрешающая способность серийных световодов составляет в среднем
15…20 мм-1. Лучшие образцы могут иметь разрешающую способность до 50 мм-1.
В целом волоконные световоды, используемые в эндоскопах, пока усту-
пают по качеству изображения линзовым системам. Однако разрабатываются меры по устранению мозаичной структуры изображения в световодах и повы-
шению их разрешающей способности.
Волоконные световоды обладают преимуществами, делающими их неза-
менимыми при решении многих задач. Так, они позволяют передавать изобра-
жение без искажения при их изгибе по любому криволинейному профилю. Вы-
сокая световая эффективность световодов используется при создании освети-
тельных систем эндоскопов. При этом источник света располагается вне прибо-
ра, что позволяет исключить нагрев изделия.
Волоконные осветители «холодного» света могут иметь торцы любой формы, например, кольцевой, что обеспечивает высокую равномерность осве-
щения объекта.
Одна из оптических схем гибкого волоконно-оптического эндоскопа
(фиброскопа) показана на рис. 2.15.
Конструктивно такие эндоскопы выполняют в виде блока осветителя с естественным световодом длиной 1,5…2,5 м и собственно эндоскопа с эффек-
тивной длиной 0,5…6 м. Некоторые модели имеют механизм дистанционной фокусировки оптики адаптера 9 и изгиба передней части (длиной до 100 мм) 8
эндоскопа в пределах 120º при диаметре 0,5…14 мм.
31
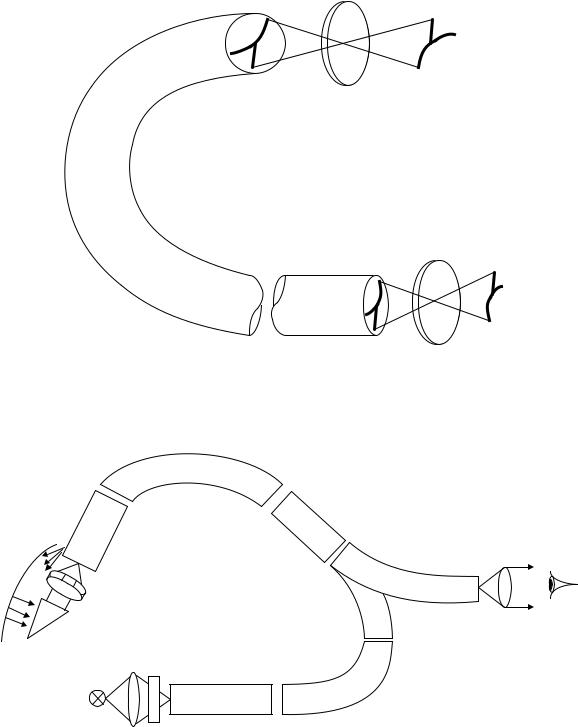
Рис. 2.14. Схема формирования и передачи изображения пучком воло-
конно-оптических элементов с упорядоченной структурой.
4'
5 |
6 |
7 |
|
8 |
|
|
|
9 |
|
|
10 |
2 |
3 |
4 |
1
Рис. 2.15. Оптическая система гибкого эндоскопа (фиброскопа):
1 – источник света; 2 – конденсор; 3 – тепловой фильтр; 4 – внешний ос-
ветительный световод; 5 – информационный световод для передачи изображе-
ний; 6 – окуляр; 7 – система регистрации и (или) анализа изображений (глаз,
фотокамера, передающая телевизионная трубка); 8 – дистальная часть эндоско-
па; 9 – оптический адаптер; 10 – поверхность объекта контроля.
32
Заменяя оптические адаптеры с одного типа на другой, можно подобрать угол поля зрения (в пределах 10…120º), направление визирования (прямой или боковой обзор) и глубину наблюдения (2 мм…∞).
Можно создать технические эндоскопы с параллельным соединением жгутов для одновременного наблюдения нескольких точек объекта.
Особенности оптических схем эндоскопов. Как видно из вышеизложен-
ного, эндоскопы – это оптические устройства, содержащие как ахроматические
(направлены сферические и хроматические аберрации для двух длин волн), так и простые элементы, которые формируют и передают информацию о качестве внутренних поверхностей ОК. Из наблюдательного прибора эндоскоп превра-
щается в прибор для точных измерений. Осветитель ОК обычно размещается со стороны объектива.
Технический прогресс в эндоскопии неразрывно связан с решением таких важных задач, как большое поле зрения, отсутствие искажений изображения,
точная передача цветов и необходимая яркость.
Самые яркие изображения получают эндоскопами малой длины и боль-
шого диаметра. При увеличении длины эндоскопа изображение становится ме-
нее ярким из-за потерь света в дополнительных оптических элементах, уста-
навливаемых для передачи изображения на достаточно большие расстояния.
Для минимизации таких потерь оптические элементы просветляют.
Тепловой метод контроля
Данный метод основан на регистрации инфракрасного излучения, исхо-
дящего от поверхности нагретого тела. Тепловым источником нагревают кон-
тролируемый объект. В зоне дефектов отвод теплоты происходит с иной интен-
сивностью по сравнению с участком однородной структуры. Возникающие температурные градиенты предопределяют различие в тепловом инфракрасном излучении, которое регистрируется соответствующим приемником и затем пре-
образуется в электрические сигналы. Этот метод позволяет выявлять как по-
верхностные, так и внутренние дефекты в виде пустот, трещин, расслоений и
33
пр. Методом предусматривается дистанционное излучение полей температур в инфракрасном диапазоне.
Различают активный метод контроля, когда источник нагревает иссле-
дуемый участок, и пассивный, который основан на использовании собственно-
го теплового излучения нагретого агрегата.
Для проведения тепловизионного контроля используются инфракрасные камеры для предупредительного и теплового контроля промышленных и энер-
гетических объектов (типа TH 5104, Thermo Tracer TH7105 фирмы NEC, Япо-
ния) и тепловизоры, которые применяются для измерения и наблюдения рас-
пределения температуры на поверхности объектов в целях обнаружения дефек-
тов и неисправностей оборудования (тип TVS-600, TVS-100 фирмы Nippon Avionics, Япония).
Для определения температурного состояния деталей в труднодоступных и опасных местах оборудования используются инфракрасные измерители темпе-
ратуры (пирометры) (типа M100, M7, M90 фирмы Mikron, США, бесконтакт-
ные пирометры ST 20/30/60/80 и контактные термометры TK-5.03, TK-5.05, TK- 5.07).
Метод акустико-эмиссионного контроля (МАЭ)
МАЭ основан на регистрации упругих импульсных колебаний, возни-
кающих в объекте в местах дефектов и распространяющихся от них при нагру-
жении объекта. Анализ результатов акустико-эмиссионного конроля произво-
дится по сопоставлению полученных сигналов со значениями, определенными в процессе калибровки на образцах, выполненных из аналогичного материала с искусственными дефектами.
В основу метода положено явление эмиссии упругих волн твердым телом при локальных динамических перестройках его структуры, деформировании и локальном разрушении. Предполагается, что возникновения акустической эмиссии связано микропроцессами необратимого деформирования и разруше-
ния материалов. Приложенная нагрузка приводит к возникновению в материале
объекта полей напряжений и деформаций, за счет энергии которых зарождают-
34
ся и развиваются дефекты, приводящие к снижению прочности материала. При этом происходит перераспределение энергии в материале, и, как следствие,
возникновение акустической эмиссии. В металлах возникновения акустической эмиссии связано с образованием и движением дислокаций, зарождением и раз-
витием трещин, с фазовыми превращениями и другими динамическими явле-
ниями.
Электрическим сигналом акустической эмиссии называется электриче-
ский сигнал на выходе приемного преобразователя. Сигналы акустической эмиссии характеризуются следующими параметрами:
общее число импульсов – количество зарегистрированных импульсов за данный промежуток времени;
суммарная акустическая эмиссия – число зарегистрированных превы-
шений сигналом акустической эмиссии установленного уровня за исследуемый
промежуток времени;
активность акустической эмиссии – общее число импульсов в единицу
времени;
уровень акустической эмиссии – среднее квадратическое значение сигнала в течение исследуемого интервала времени;
амплитуда акустической эмиссии – максимальное значение сигнала в течение исследуемого промежутка времени;
амплитудное распределение – это распределение пяти амплитуд аку-
стической эмиссии за исследуемый интервал времени;
энергия сигнала акустической эмиссии – это энергия, выделяемая в месте измерения в исследуемой полосе частот за выбранный интервал времени.
Характерной особенностью акустической эмиссии при повторном нагру-
жении является быстрое уменьшение числа импульсов и их амплитуд при по-
следующих нагружениях. Это явление называется эффектом Кайзера, который заключается в явлении невоспроизводимости акустической эмиссии при по-
35
вторном нагружении вплоть до максимальной нагрузки предшествующего на-
гружения.
Полное исчезновение акустической эмиссии при повторном нагружении свидетельствует о том, что материал не повреждается и усталостного разруше-
ния не ожидается. Если же при повторных нагружениях значения параметров акустической эмиссии уменьшаются в малой степени, то это значит, что идет быстрое накопление повреждений и возможно усталостное разрушение объек-
та.
Для обнаружения всех опасных источников сигналов в процессе акусти-
ко-эмиссионного контроля производят оперативное накопление и обработку данных. При наличии цифровых регистраторов используется запоминание сиг-
налов с целью последующего анализа процессов.
Методы акустической диагностики, использующие в качестве информа-
ции шум работающего агрегата и его элементов, позволяют при регистрации общего спектра определять вновь появившиеся в процессе эксплуатации (в ре-
зультате наличия каких-либо дефектов) новые источники шума, и по ним оце-
нивать изменение состояния объекта.
При испытании объекта или в процессе его эксплуатации приложение на-
грузки приводит к возникновению в зоне предразрушения акустического сиг-
нала. Информация о времени распространения сигнала, его амплитуде и пр.
воспринимается пьезоэлектрическими акустическими датчиками (преобразова-
телями акустической эмиссии), расположенными на поверхности контролируе-
мого объекта.
Основными задачами, решаемыми акустико-эмиссионным методом, яв-
ляются:
выявление разнообразных дефектов, в том числе развивающихся тре-
щин, коррозии, мест эрозионного износа;
контроль герметичности корпусных конструкций, с целью выявления сквозных дефектов, мест утечек, неплотностей соединений;
контроль качества сварных швов;
36

выявление мест повышенной напряженности и перегрузки конструк-
ции объекта.
Метод может использоваться как самостоятельный метод контроля, так и
вместе с другими методами (визуально-оптическим, магнитопорошковым,
Апиллярным, ультразвуковым и др.).
Реализация метода осуществляется применением специальных устройств,
а именно, с помощью акустико-эмиссионных систем, предназначенных для
многоканальной регистрации и измерений параметров сигнала акустической
эмиссии (типа A-line 320, AMS 44, фирмы Vallen Systeme GMBH, Германия).
Таблица 2.2 – Преимущества и недостатки физических методов контроля
Метод |
Преимущества |
Недостатки |
|
- возможность выявления |
- высокие трудозатраты при диаг- |
|
дефектов без удаления |
ностировании крупногабаритных |
|
защитных покрытий; |
объектов и изделий относительно |
|
- регистрация результа- |
большой толщины; |
|
тов контроля. |
- относительно низкая чувствитель- |
|
|
ность при выявлении трещиновид- |
|
|
ных дефектов. Обязательным усло- |
Радиационный |
|
вием является необходимость сов- |
|
падения направления просвечива- |
|
|
|
|
|
|
ния с плоскостью трещины; |
|
|
- необходимость устройств защиты |
|
|
от биологического воздействия на |
|
|
организм обслуживающего персо- |
|
|
нала от рентгеновского и других |
|
|
видов излучения при строгом со- |
|
|
блюдении техники безопасности. |
|
- простота технологии; |
- определенные затруднения в по- |
|
- достаточно высокая |
лучении результатов контроля при |
|
чувствительность к вы- |
сварке магнитных деталей немаг- |
|
явлению дефектов опре- |
нитным электродом; |
Магнитный |
деленных видов; |
- пропуск трещин при толщине за- |
|
- возможность точной |
щитного покрытия более 30 мкм; |
|
локализации дефектов, |
- редкое снижение производитель- |
|
их ориентации и протя- |
ности при обследовании крупнога- |
|
женности. |
баритных элементов изделий. |
37

|
|
|
|
|
|
|
|
|
Продолжение таблицы 2.2 |
1 |
|
|
|
2 |
|
|
|
|
3 |
|
- |
обеспечивает |
|
одновре- |
- не всегда позволяет точно опреде- |
||||
|
менное выявление внут- |
лить размеры дефектов; |
|||||||
|
ренних и поверхностных |
- затруднен контроль изделий из |
|||||||
|
дефектов различной ори- |
жаропрочных (крупнозернистых) |
|||||||
|
ентации практически |
во |
сталей; |
||||||
|
всех |
конструкционных |
- сложность использования специ- |
||||||
Ультразвуковой |
сталях и сплавах; |
|
альной аппаратуры, что требует вы- |
||||||
- |
позволяет |
выявление |
сокого уровня квалификации пер- |
||||||
|
дефектов |
при |
|
односто- |
сонала. |
||||
|
роннем доступе к изде- |
|
|||||||
|
лию; |
|
|
|
|
|
|
|
|
|
- |
возможность |
контроля |
|
|||||
|
без |
удаления |
защитных |
|
|||||
|
покрытий. |
|
|
|
|
|
|
||
|
- возможность выявления |
- трудности контроля сварных швов |
|||||||
|
поверхностных дефектов |
ввиду различной электропроводно- |
|||||||
|
без |
удаления |
защитных |
сти основного материала объекта и |
|||||
|
покрытий; |
|
|
|
|
|
материала сварного шва; |
||
|
- |
возможность |
точного |
- высокая трудоемкость ручного |
|||||
Вихревой |
определения |
|
|
границ |
контроля при значительной площа- |
||||
|
трещин; |
|
|
|
|
|
ди поверхности изделия. |
||
|
- малые габариты и вес |
|
|||||||
|
аппаратуры; |
|
|
|
|
|
|||
|
- |
высокая достоверность |
|
||||||
|
результатов контроля. |
|
|
||||||
|
- |
высокая |
чувствитель- |
- возможность пропуска дефекта из- |
|||||
|
ность; |
|
|
|
|
|
за наличия окислов в полостях тре- |
||
|
- |
наглядность |
результа- |
щин, наличия загрязнений и корро- |
|||||
|
тов; |
|
|
|
|
|
|
зии на поверхности объекта и нали- |
|
|
- |
возможность примене- |
чия «захлопнутых» трещин на по- |
||||||
|
ния при контроле изде- |
верхности. |
|||||||
|
лий, |
выполненных |
из |
|
|||||
Капиллярный |
магнитных |
и |
|
немагнит- |
|
||||
|
ных материалов; |
|
|
|
|||||
|
- |
возможность |
контроля |
|
|||||
|
больших площадей |
по- |
|
||||||
|
верхности |
изделия при |
|
||||||
|
неизвестной |
ориентации |
|
||||||
|
предполагаемых |
дефек- |
|
||||||
|
тов. |
|
|
|
|
|
|
|
|
|
|
|
|
|
|
|
|
|
38 |

|
|
|
|
|
|
|
Продолжение таблицы 2.2 |
1 |
|
|
|
2 |
|
|
3 |
|
- |
высокая |
наглядность |
- использование сложно аппаратуры |
|||
|
результатов при обнару- |
и необходимость высокого уровня |
|||||
|
жении наружных дефек- |
квалификации персонала; |
|||||
|
тов; |
|
|
|
|
- отсутствие возможности выявле- |
|
|
- |
возможность |
исследо- |
ния внутренних дефектов материа- |
|||
|
вания |
труднодоступных |
ла изделия. |
||||
Визуально- |
элементов |
оборудования |
|
||||
без разборки; |
|
|
|
||||
оптический |
|
|
|
||||
- |
возможность |
докумен- |
|
||||
|
|
||||||
|
тации |
результатов |
кон- |
|
|||
|
троля с целью дальней- |
|
|||||
|
шего анализа тенденции |
|
|||||
|
развития дефектов |
при |
|
||||
|
последующих |
исследо- |
|
||||
|
ваниях. |
|
|
|
|
|
|
|
- возможность выявления |
- наличие посторонних шумов мо- |
|||||
|
внутренних и поверхно- |
жет привести к появлению помех и |
|||||
|
стных дефектов при од- |
трудности выделения «нужных» |
|||||
|
носторонне доступе к аг- |
сигналов; |
|||||
|
регату; |
|
|
|
|
- зависимость энергии сигнала аку- |
|
Акустико- |
- |
возможность |
контроля |
стической эмиссии от ряда пара- |
|||
эмиссионного |
крупногабаритных |
объ- |
метров (структура материала, из ко- |
||||
контроля |
ектов; |
|
|
|
|
торого выполнен объект; расстоя- |
|
|
- |
относительно |
невысо- |
ние между датчиком и дефектом; |
|||
|
кие трудозатраты; |
|
наличие защитных покрытий по- |
||||
|
- |
возможность локально- |
верхности объекта); |
||||
|
го обследования элемен- |
- сложность расшифровки результа- |
|||||
|
тов объекта. |
|
|
тов контроля. |
2.2 Методы диагностики по изменению параметров динамических
процессов
К этим методам следует отнести не только собственно параметрическую диагностику, основанную на контроле параметров работающих агрегатов, но и вибрационную диагностику, т.к. параметрические методы включают несколько каналов контроля различных процессов, в т.ч. и вибрацию агрегатов и их от-
дельных узлов.
39
2.2.1. Вибрационная диагностика
Прежде, чем перейти к описанию физических основ вибродиагостики,
технологии и методики ее проведения, а также используемых средств, рассмот-
рим основные цели и задачи вибродиагностики.
Методы вибродиагностики направлены на обнаружение и идентифика-
цию таких неисправностей агрегата, которые оказывают влияние на его вибра-
цию: дефектов роторов, опорной системы и узлов статора, испытывающих либо генерирующих динамические нагрузки.
Целями вибродиагностики являются:
-предупреждение развития дефектов агрегата и сокращение затрат на его восстановление,
-определение оптимальной технологии восстановления работоспособно-
сти агрегата, если возникший дефект исключает возможность его нормальной эксплуатации.
Основной задачей вибродиагностики является разделение множества возможных технических состояний агрегата на два подмножества: исправных и неисправных.
Следующей задачей является постановка диагноза, состоящего в опреде-
лении характера и локализации одного или группы дефектов, соответствующих вибрационному состоянию агрегата.
Одной из задач вибродиагностики является возможное обнаружение де-
фекта на ранней стадии и прогнозирование его развития во времени.
На основании диагноза определяется оптимальный режим эксплуатации агрегата в условиях возникшей неисправности и технология устранения дефек-
та и восстановления работоспособности агрегата.
Чем надежней и конкретней диагноз, тем ниже затраты, связанные с вос-
становлением агрегата.
Основы вибрационной диагностики базируются на рассматриваемых ни-
же понятиях.
40