
ТКМ (Сварочное производство)
.pdf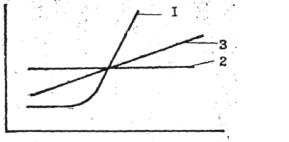
пологопадающей характеристике источника питания. Видно, что I1 < I2, следовательно, дуга более устойчива при крутопадающей ВАХ источника питания. Чем больше крутизна падения характеристики в рабочей части, тем меньше колебания тока при изменении длины дуги.
Источники питания с пологопадающей ВАХ применяются для автоматической и полуавтоматической сварки под флюсом.
Источники питания с жесткой ВАХ применяются для сварки в защитных газах с возрастающей ВАХ дуги.
На рисунке 7 представлены комбинации жесткой и возрастающей ВАХ источника питания с возрастающей ВАХ дуги.
U, В
I, А
Рисунок 7 – Жесткая (2) и возрастающая (3) ВАХ источника питания при возрастающей (1) ВАХ дуги.
ТРЕБОВАНИЯ К ИСТОЧНИКАМ СВАРОЧНОГО ТОКА
Для обеспечения устойчивого процесса сварки источники питания сварочной дуги должны удовлетворять следующим, требованиям.
1. Напряжение холостого хода должно быть достаточным для легкого возбуждения дуги, в то же время не должно превышать нормы безопасности. Максимально допустимое напряжение холостого хода для источников постоянного тока – 90 В, переменного – 80 В. Для возбуждения дуги в первом случае требуется 40÷60 В, во втором - 50÷70 В.
2. Рабочее напряжение горения дуги должно быстро устанавливаться и изменяться в зависимости от длины дуги, обеспечивая ее устойчивое горение. С увеличением, длины дуги напряжение должно быстро возрастать, а с уменьшением – быстро падать. Время восстановления рабочего напряжения от 0 до 30 В
11
после каждого короткого замыкания (при капельном переносе металла от электрода к свариваемой детали) должно быть менее 0,05 сек.
3. Ток короткого замыкания не должен превышать сварочный ток более чем на 40÷50%. При этом источник тока должен выдерживать продолжительные короткие замыкания сварочной цепи. Это условие
необходимо для предохранения обмоток источника тока от перегрева и повреждения.
Источник питания сварочной дуги должен обеспечивать возможность настройки различных режимов сварки, то есть
установление оптимальной величины силы тока при заданном напряжении дуги. Для этой цели источник питания должен
обеспечивать получение в определенном диапазоне регулирования несколько внешних характеристик, обеспечивающие устойчивое горение дуги.
Каждый источник питания рассчитывают на определенную нагрузку, при которой он работает, не перегреваясь выше допустимых норм. Силу тока и напряжение источника питания в этом случае называют номинальными. Номинальная величина силы тока различна при различных режимах работы.
РЕЖИМ РАБОТЫ ИСТОЧНИКА ПИТАНИЯ
Обычно работа источника питания сварочной дуги происходит с периодическими включениями и выключениями нагрузки. Для
характеристики режима работы источника питания применяют следующие показатели:
1) продолжительность работы
ПР = |
tСВ |
|
×100% , |
(4) |
||
|
|
|||||
|
|
tСВ + tXX |
|
|||
2) продолжительность включения |
|
|||||
|
|
tСВ |
|
|
(5) |
|
ПВ = tСВ + tП |
×100% |
|||||
|
где tСВ – время (продолжительность) сварки, tХХ – время холостого хода,
tП – время паузы.
Различие между ПР и ПВ заключается в том, что в первом случае
12
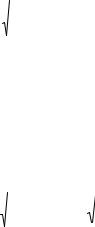
во время паузы источник питания не отключается от сети и работает на холостом ходу, а во втором случае источник питания полностью отключается от сети.
В паспорте любого источника питания указываются номинальные значения сварочного тока IН и продолжительности работ ПРН (или же ПВН). Например, запись в паспорте ПРН = 40% означает, что при
сварке на номинальном токе продолжительность непрерывной сварки не должна превышать 4-х из 10 мин.
При изменении продолжительности работы максимально допустимая величина тока определяется по формуле:
I Д |
= I Н |
× |
ПР Н |
, |
(6) |
ПР Д |
|
||||
|
|
|
|
где ПРД – допустимое значение ПР.
Пример: Рассчитать максимально допустимый сварочный ток для источника питания, в паспорте которого приведены: IН = 500 А и ПРН = 60%, при непрерывном режиме работы в течении 10 мин (т.е. при ПРД =100%).
Пользуясь формулой (6), находим:
|
ПР Н |
|
|
|
|
|
I Д = I Н × |
= 500 × |
60 |
|
= 387 A |
||
100 |
||||||
|
ПР Д |
|
|
|
РЕЖИМ РУЧНОЙ ДУГОВОЙ СВАРКИ
Прежде чем проводить сварочные работы, определяют режим сварки, обеспечивающий хорошее качество сварного шва,
установленные размеры форму при минимальных затратах материалов, электроэнергии и труда.
Режимом сварки называется совокупность параметров, определяющих процесс сварки: вид тока, диаметр электрода, напряжение и величина сварочного тока, длина дуги, скорость перемещения электрода вдоль шва и др. Основные параметры – диаметр электроды и величина сварочного тока.
Диаметр электрода устанавливается в зависимости от толщины свариваемых кромок, вида сварного соединения, размеров шва и
13
положения его в пространстве. Для стыковых соединений приняты следующие практические рекомендации:
При сварке листового материала толщиной до 4 мм в нижнем
положении диаметр электрода выбирают равным толщине свариваемой стали.
При сварке листов большей толщины используют электроды диаметром 4÷6 мм.
При выполнении угловых и тавровых соединений принимают во внимание величину катета шва.
При катете 3÷5 мм сварку проводят электродом, диаметром 3÷4 мм, а при катете 6÷8 мм применяют электроды диаметром 4÷5мм.
По выбранному диаметру электрода устанавливают величину сварочного тока, которая должна соответствовать данным в паспорте или сертификате на электроды.
Ориентировочно величину сварочного тока, для электродов 4÷6
мм можно установить по формуле: |
|
Iсв =(40÷50)× dЭ, А |
(7) |
При использовании формул должны учитываться. поправки:
1.Если толщина, металла меньше 1,5×dЭ при сварке в нижнем положении, то сварочный ток уменьшают на 10÷15%.
2.Если толщина металла более 3×dЭ, то сварочный ток увеличивают на 10÷15%
3.При ведении сварки вертикального или горизонтального шва сварочный ток уменьшают на 10÷15%.
4.При выполнении потолочного шва сварочный ток уменьшают на 10÷20%.
СПОСОБЫ ЗАЖИГАНИЯ ДУГИ
Зажечь дугу можно двумя способами – «впритык» и «чирканьем».
По способу впритык торцом электрода кратковременно касаются свариваемого металла и при возникновении искры отводят электрод от поверхности изделия на 3÷4 мм, поддерживая горение образовавшейся дуги. При таком способе зажигания возможно «примерзание» электрода, когда он, не будучи отведен от поверхности, приваривается к ней и дуга гаснет. Отрывать
14
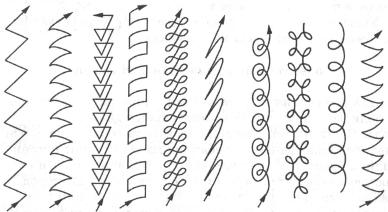
примерзший электрод следует резким поворачиванием его влево и вправо, как бы отламывая, а, не отрывая от поверхности.
Способ зажигания дуги чирканьем уменьшает вероятность примерзания электрода. Боковым движением электродом проводят (чиркают) по свариваемой поверхности и отводят как в первом способе. Однако этот прием неудобен при сварке в труднодоступных и стесненных местах.
ДВИЖЕНИЯ ЭЛЕКТРОДА
Сварка может вестись в четырех направлениях: слева направо, справа налево, от себя и к себе. Вне зависимости от направления сварки электрод наклоняется в сторону движения на 15°, чтобы обеспечить максимальную глубину проплавления основного металла. При наплавке поверхностного слоя, электрод наклоняется в обратную сторону на эту же величину, для того чтобы уменьшить проплавление основного металла и перемешивание его с наплавляемым.
При прямолинейном движении электрода вдоль шва, ширина наплавляемого валика будет равна 0,8÷1,5 диаметра электрода, в зависимости от силы тока и скорости движения. Швы шириной 1,5÷4
диаметра электрода получают с помощью колебательных движений электрода, некоторые из которых приведены на рисунке 8, а виды сварных соединений на рисунке 9.
Рисунок 8 - Траектория движения конца электрода при сварке
15
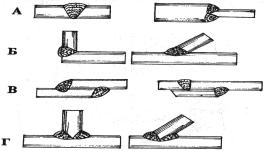
Рисунок 9 – Виды сварных соединений:
А- стыковое, Б- угловое, В- нахлесточное, Г – тавровое.
ПОРЯДОК ВЫПОЛНЕНИЯ РАБОТЫ
1.Ознакомиться с физическими и электрическими свойствами сварочной дуги
2.Уяснить условия устойчивого горения дуги и требования к источникам сварочного тока.
3.В соответствии с размерами свариваемых образцов установить режим сварки.
4.С целью установления влияния длины дуги на форму шва провести процесс сварки при 2-х значениях длины дуги (короткой и длинной).
5.Полученные данные занести в таблицу результатов:
№ |
Длин |
Толщи |
Профи |
Диаметр |
Тип, |
Форма |
Сила |
п/ |
а |
на |
ль |
электрод |
марка |
сварног |
сварочно |
п |
дуги, |
свариваемого |
а, мм |
электро |
о шва |
го тока, |
|
|
мм |
металла, мм |
|
да |
|
А |
|
1 |
|
|
|
|
|
|
|
2 |
|
|
|
|
|
|
|
СОДЕРЖАНИЕ ОТЧЕТА
Отчет должен содержать название работы, перечень оборудования, определения основных положений по теме, графическое изображение характеристик дуги и источников питания, таблицу результатов.
16
КОНТРОЛЬНЫЕ ВОПРОСЫ
1.Что собой представляет сварочная дуга, каковы условия её возникновения?
2.Каково распределение теплоты по различным областям сварочной дуги?
3.Какое влияние и на что оказывает длина дуги при сварке?
4.Какие условия необходимы для устойчивого горения дуги при ручной электродуговой сварке?
5.Сущность требований, предъявляемых к источникам питания при сварке? Виды источников питания.
6.Как выбирается режим при ручной электродуговой сварке?
17
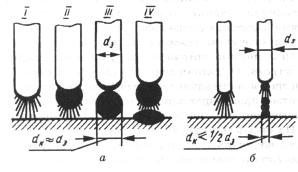
Лабораторная работа №2
Определение коэффициентов расплавления, наплавки, потерь на угар и разбрызгивание при ручной дуговой сварке
Цель работы: определить величину коэффициентов расплавления,
наплавки и потерь на угар и разбрызгивание при ручной дуговой сварке.
Оборудование и инструменты: сварочный пост, электроды, щиток, металлическая пластина, весы, штангенциркуль.
1.ТЕОРЕТИЧЕСКАЯ ЧАСТЬ
Впроцессе ручной дуговой сварки происходят процессы расплавления электродного металла, перенос и наплавка его на поверхность свариваемой или наплавляемой детали. Перенос металла может происходить либо дискретно каплями, либо непрерывной струей, как показано на рисунке 1. Капельный перенос металла наблюдается при малой плотности тока, струйный – при больших значениях сварочного тока и малом диаметре электродной проволоки.
Рисунок 1 – Этапы наплавка капельным (а) и струйным переносом электродного металла:
I – горящая дуга начинает плавить металл; II –образование капли расплавленного металла; III – капля стекает на металл, замыкая дуговой промежуток; IV – восстановление дуги и образование следующей капли; dЭ, dК – диаметры электрода капли.
Основными величинами, характеризующими процесс сварки и наплавки, являются:
18
·коэффициент расплавления металла αР,
·коэффициент наплавки αН,
·производительность расплавления электродов ПР,
·производительность наплавки ПН,
·коэффициент потерь ψ.
Коэффициент расплавления металла αР показывает, какое
количество электродного металла расплавляется в единицу времени на один ампер сварочного тока, и определяется формулой
α Р = |
GР |
, г/(А×ч) |
(1) |
|
I × t |
||||
|
|
|
где GР – масса расплавленного за время t электродного металла, г; I – величина сварочного тока, А;
t – время горения дуги, ч.
Коэффициент расплавления зависит от материала электрода, состава его покрытия, рода, полярности и плотности тока. Кроме того, в процессе сварки электрод нагревается, что тоже сказывается на интенсивности расплавления электродного метала. До начала сварки электрод имеет комнатную температуру, к концу сварки он может нагреться до 500¸600° С, если в его покрытии нет органических веществ и не выше 250° С, если есть. Для стальных электродов коэффициент расплавления обычно равен от 7 до 22 г/(А×ч).
Производительностью расплавления электродов называют массу расплавленного сварочной дугой электродного металла в единицу времени. Производительность расплавления электродов ПР зависит от количества тепла, сообщенному электроду и определяется по формуле
ПР=αР×I, г/ч |
(2) |
где αР коэффициент расплавления металла, г/(А×ч). I – величина сварочного тока, А;
Чем больше ток, тем выше производительность расплавления металла.
Для оценки процесса наплавки применяется коэффициент наплавки aН, определяемый по формуле
19
α Н = |
GН |
, г/(А×ч) |
(3) |
I ´ t
где GН – масса наплавленного электродного металла за время t, г;
I – величина сварочного тока, А; t – время горения дуги, ч.
Значение коэффициента наплавки αН меньше коэффициента
расплавления αР на 1..5 г/(А×ч) и обычно составляет 6..18 г/(А×ч).
Производительность процесса наплавки ПН численно равна массе наплавляемого металла в единицу времени на один ампер сварочного
тока: |
|
ПН=αН×I, г/ч |
(4) |
где αН коэффициент наплавки, г/(А×ч). I – величина сварочного тока, А;
Например, при ручной наплавке покрытыми электродами производительность достигает 0,8..3,0 кг/ч, при автоматической наплавке под флюсом – 2..15 кг/ч, при электрошлаковой – 20..60 кг/ч, при автоматической наплавке электродами большого сечения до 150 кг/ч.
Величина GН всегда меньше GР, так как имеются потери на разбрызгивание и угар.
Для оценки величины этих потерь введен, так называемый
коэффициент потерь ψ, показывающий какая доля расплавленного металла теряется. Определяется по одной из равнозначных формул:
ψ = GР − GН ×100% |
(5) |
||
и |
GР |
|
|
α Р −α Н |
|
|
|
ψ = |
×100% |
(6) |
|
α Р |
|
||
Здесь разность GН -GР |
есть |
количество металла, |
которое |
«теряется» вследствие разбрызгивания, окисления, испарения (угар) за время горения дуги.
Коэффициент потерь зависит от состава электрода и его покрытия,
20