
Test-Bank-for-Heizer-Operations-Management-9e
.pdf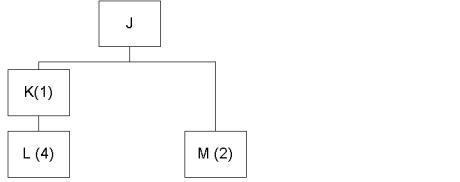
149.The MPS calls for 50 units of Product A and 60 of B. There are currently 35 of Product B on hand. Each A requires 2 of Part C; each B requires 5 of C. There are 160 units of C available.
a.Calculate the net requirements for B.
b.Calculate the gross requirements for C.
c.Calculate the net requirements for C.
(a) 60 - 35 = 25; (b) 50 x 2 + 25 x 5 = 225; (c) 225 - 160 = 65 (MRP structure, easy) {AACSB: Analytic Skills}
150.Consider the bill of material for Product J and the data given in the following table. The gross requirements for J are 200 units in week 6 and 250 units in week 8. Develop the MRP tables for each item for an 8-week planning period. Use the lot-for-lot lot-sizing rule.
Item |
Lead Time |
Quantity on Hand |
Scheduled receipts |
J |
1 |
0 |
|
K |
2 |
20 |
30 in week 2 |
L |
2 |
0 |
|
M |
1 |
20 |
10 in week 1 |
SEE NEXT PAGE FOR SOLUTION.
401
|
|
Number |
|
|
|
|
|
|
|
|
|
per |
Indented |
|
|
|
|
|
|
Item name |
Level |
parent |
BOM |
|
|
|
|
|
|
J |
0 |
1 |
J |
|
|
|
|
|
|
K |
1 |
1 |
K |
|
|
|
|
|
|
L |
2 |
4 |
L |
|
|
|
|
|
|
M |
1 |
2 |
M |
|
|
|
|
|
|
|
|
|
|
|
|
|
|
|
|
|
|
Lead |
|
Safety |
|
|
|
Minimum |
|
J |
|
time |
1 |
Stock |
0 |
Lot size |
1 |
quantity |
0 |
|
Period 0 |
Period 1 |
Period 2 |
Period 3 Period 4 |
Period 5 |
Period 6 |
Period 7 |
Period 8 |
|
Gross requirements |
|
0 |
0 |
0 |
0 |
0 |
200 |
0 |
250 |
Scheduled receipts |
|
|
|
|
|
|
|
|
|
On Hand Inventory |
|
0 |
0 |
0 |
0 |
0 |
0 |
0 |
0 |
NET POQ Req |
|
0 |
0 |
0 |
0 |
0 |
200 |
0 |
250 |
Planned receipts |
|
0 |
0 |
0 |
0 |
0 |
200 |
0 |
250 |
Planned orders |
|
0 |
0 |
0 |
0 |
200 |
0 |
250 |
0 |
|
|
|
|
|
|
|
|
|
|
|
|
Lead |
|
Safety |
|
|
|
Minimum |
|
K |
|
time |
2 |
Stock |
0 |
Lot size |
1 |
quantity |
0 |
|
Period 0 |
Period 1 |
Period 2 |
Period 3 Period 4 |
Period 5 |
Period 6 |
Period 7 |
Period 8 |
|
Gross requirements |
|
0 |
0 |
0 |
0 |
200 |
0 |
250 |
0 |
Scheduled receipts |
|
|
30 |
|
|
|
|
|
|
On Hand Inventory |
20 |
20 |
20 |
50 |
50 |
50 |
0 |
0 |
0 |
NET POQ Req |
|
0 |
0 |
0 |
0 |
150 |
0 |
250 |
0 |
Planned receipts |
|
0 |
0 |
0 |
0 |
150 |
0 |
250 |
0 |
Planned orders |
|
0 |
0 |
150 |
0 |
250 |
0 |
0 |
0 |
|
|
|
|
|
|
|
|
|
|
|
|
Lead |
|
Safety |
|
|
|
Minimum |
|
M |
|
time |
1 |
Stock |
0 |
Lot size |
1 |
quantity |
0 |
|
Period 0 |
Period 1 |
Period 2 |
Period 3 Period 4 |
Period 5 |
Period 6 |
Period 7 |
Period 8 |
|
Gross requirements |
|
0 |
0 |
0 |
0 |
400 |
0 |
500 |
0 |
Scheduled receipts |
|
10 |
|
|
|
|
|
|
|
On Hand Inventory |
20 |
20 |
30 |
30 |
30 |
30 |
0 |
0 |
0 |
NET POQ Req |
|
0 |
0 |
0 |
0 |
370 |
0 |
500 |
0 |
Planned receipts |
|
0 |
0 |
0 |
0 |
370 |
0 |
500 |
0 |
Planned orders |
|
0 |
0 |
0 |
370 |
0 |
500 |
0 |
0 |
|
|
|
|
|
|
|
|
|
|
|
|
Lead |
|
Safety |
|
|
|
Minimum |
|
L |
|
time |
2 |
Stock |
0 |
Lot size |
1 |
quantity |
0 |
|
Period 0 |
Period 1 |
Period 2 |
Period 3 Period 4 |
Period 5 |
Period 6 |
Period 7 |
Period 8 |
|
Gross requirements |
|
0 |
0 |
600 |
0 |
1000 |
0 |
0 |
0 |
Scheduled receipts |
|
|
|
|
|
|
|
|
|
On Hand Inventory |
|
0 |
0 |
0 |
0 |
0 |
0 |
0 |
0 |
NET POQ Req |
|
0 |
0 |
600 |
0 |
1000 |
0 |
0 |
0 |
Planned receipts |
|
0 |
0 |
600 |
0 |
1000 |
0 |
0 |
0 |
Planned orders |
|
600 |
0 |
1000 |
0 |
0 |
0 |
0 |
0 |
(MRP structure, moderate) {AACSB: Analytic Skills}
402
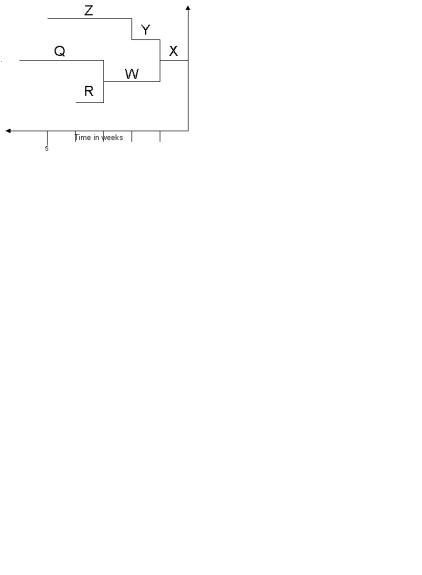
151.Each R requires 3 of component S and 3 of material A; each S requires 3 of part T. The lead time for assembly of R is 1 week. The lead time for the manufacture of S is 2 weeks. The lead time for material A is 1 week. The lead time for the procurement of T is 4 weeks.
a.Construct the time-phased product structure.
b.Construct the bill of material.
Solution:
|
Bill of Material |
|
||
Item |
Quantity |
|||
R |
|
|
|
1 |
|
S(3) |
|
|
3 |
|
|
T(3) |
|
9 |
|
A(3) |
|
|
3 |
(MRP structure, moderate) {AACSB: Analytic Skills}
152.Each X requires 2 of component Y and 1 of part W. Each Y requires 10 of Z. Each W requires 3 of Q and 2 of R. Lead times are X = 1 week, Y = 1 week, W = 2 weeks, R = 1 week, Z = 3 weeks, and Q = 3 weeks.
a.Construct the time-phased product structure.
b.Construct the bill of material.
Solution:
|
Bill of Material |
|
||
Item |
Quantity |
|||
X |
|
|
|
1 |
|
Y(2) |
|
|
2 |
|
|
Z(10) |
|
20 |
|
W(1) |
|
|
1 |
|
|
Q(3) |
|
3 |
|
|
R(2) |
|
2 |
(MRP structure, moderate) {AACSB: Analytic Skills}
403
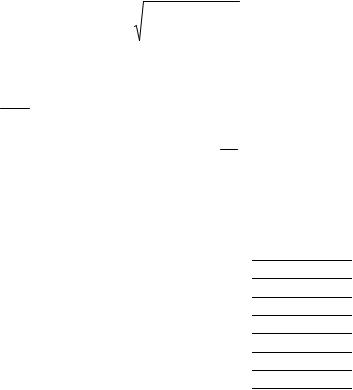
153. A product has the following gross requirements. Which is cheaper—lot-for-lot, part period balance, or EOQ lot sizing?
Week |
1 |
2 |
3 |
4 |
5 |
6 |
Requirements |
50 |
80 |
90 |
50 |
30 |
60 |
Other data for this scenario include: setup cost = $250, inventory holding cost $2 per unit per week. There is no beginning inventory; there are no scheduled receipts. The usage pattern is expected to continue for the remainder of the year.
Lot-for-lot will cost $250 x 6 = $1,500 for the six periods.
EOQ is based on 60 units per week demand: |
2 60 52 250 |
= 122 |
||
|
60 52 |
|
2 52 |
|
Annual setup costs = |
250 = $6,393; |
|
|
|
122 |
|
|
||
|
|
|
|
Annual holding costs = 1222 2 52 = $6,344
Total annual costs = $12,737; Cost for six weeks = 12,737 526 = $1,469
For part-period balancing, the EPP=250/2 = 125. Total cost for PPB over the six periods is $1,210.
Period |
Order size |
# of Units |
CumPP |
Setup cost |
Holding cost |
1 |
70 |
0 |
0 |
|
160 |
1, 2 |
150 |
80 |
80* |
250 |
|
1, 2, 3 |
240 |
90 * 2 |
260 |
|
|
3 |
90 |
0 |
0 |
|
|
3, 4 |
160 |
70 |
70 |
|
300 |
3, 4, 5 |
200 |
40 * 2 |
150* |
250 |
|
3, 4, 5, 6 |
270 |
70 * 3 |
360 |
|
0 |
6 |
70 |
0 |
0 |
250 |
|
|
|
|
Total |
750 |
460 |
Summary of costs: LFL = $1,500; EOQ = $1,469; PPB = $1,210. PPB is cheapest lot-sizing model for this problem. (Lot-sizing techniques, moderate) {AACSB: Analytic Skills}
404
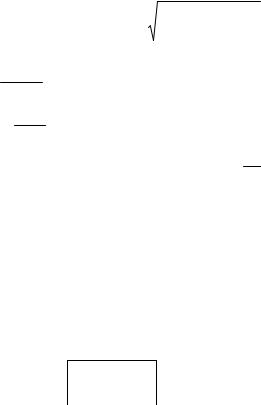
154. A product has the following gross requirements. Which is cheaper—lot-for-lot or EOQ lot-sizing?
Week |
1 |
2 |
3 |
4 |
Requirements |
50 |
30 |
40 |
80 |
Other data for this scenario include: setup cost = $1000, inventory holding cost $1 per unit per week. There is no beginning inventory; there are no scheduled receipts. The usage pattern is expected to continue for the remainder of the year.
Lot-for-lot will cost $1000 x 4 = $4,000 for the four periods.
EOQ is based on 50 units per week demand: |
2 50 52 1000 |
= 316 |
|
1 52 |
|
Annual setup costs = 5031652 1000 = $8,228;
Annual holding costs = 3162 1 52 = $8,216
Total annual costs = $16,444; Cost for four weeks = 16,444 524 = $1,265
Summary of costs: LFL = $4,000; EOQ = $1,265. EOQ is cheaper lot-sizing model for this problem. (Lot-sizing techniques, moderate) {AACSB: Analytic Skills}
155. Construct a product structure tree for a movie purchased in DVD format. Assume that it contains a single DVD disk. Don't be concerned with artwork—you may use labeled boxes for your parts and assemblies.
Not all DVDs are alike in their construction, so student answers will vary. Here is a fairly generic version. Note that the primary container is a one-piece molded plastic "clamshell." There are three layers, 0, 1, and 2.
Movie, DVD
format
|
|
|
|
|
|
|
|
|
|
|
|
|
|
|
|
|
|
|
|
|
|
|
|
|
|
|
|
|
|
|
|
|
|
|
|
|
|
|
|
|
|
|
|
|
|
|
|
|
|
|
|
|
|
|
|
|
|
|
|
|
|
|
Case Assembly |
|
|
|
|
|
|
Contents |
|
|
|
|
|
Packaging |
|
|
|
||||||||||
|
|
|
|
|
|
|
|
|
assembly |
|
|
|
|
|
|
assembly |
|
|
|
||||||||||
|
|
|
|
|
|
|
|
|
|
|
|
|
|
|
|
|
|
|
|
|
|
||||||||
|
|
|
|
|
|
|
|
|
|
|
|
|
|
|
|
|
|
|
|
|
|
|
|
|
|
|
|
|
|
|
|
|
|
|
|
|
|
|
|
|
|
|
|
|
|
|
|
|
|
|
|
|
|
|
|
|
|
||
|
|
|
|
|
|
|
|
|
|
|
|
|
|
|
|
|
|
|
|
|
|
|
|
|
|
|
|
|
|
One-piece |
|
Clear |
|
Electronic |
|
|
DVD |
|
|
Chapter |
|
Outside |
|
Shrink |
|
Security |
|||||||||||||
molded |
|
view |
|
|
security |
|
|
|
|
|
|
|
|||||||||||||||||
|
|
|
|
|
disk |
|
|
list |
|
label |
|
wrap |
|
tape (3) |
|||||||||||||||
clamshell |
|
layer |
|
|
tag |
|
|
|
|
|
|
|
|||||||||||||||||
|
|
|
|
|
|
|
|
|
|
|
|
|
|
|
|
|
|
|
|
|
|
|
|||||||
|
|
|
|
|
|
|
|
|
|
|
|
|
|
|
|
|
|
|
|
|
|
|
|
|
|
|
|
|
|
(Dependent inventory model requirements, moderate) {AACSB: Analytic Skills}
405
156. Construct an indented bill of material for a common 3-ring view binder (the kind that lets you slip your own cover sheet into the front panel). Assume the rings to be 1 inch diameter. Don't worry about other dimensions—pay attention to accounting for all of the parts.
Not all such binders are identical, and student answers will vary, but here is a fairly generic version. The main components are the cover assembly and the ring assembly. Students will need to include some form of locking mechanism and/or spring.
Indented bill of material, Three-ring binder
Cover assembly
Front cover
Chipboard interior
Vinyl exterior, inside and outside of front cover
Clear "view" layer, outside
Vinyl pocket, inside
Spine
Chipboard interior
Vinyl exterior, inside and outside of front cover
Clear "view" layer, outside
Back cover
Chipboard interior
Vinyl exterior, inside and outside of front cover
Clear "view" layer, outside
Vinyl pocket, inside
Ring Assembly
Spine
Main spine (holds the three sets of rings and the tabs)
Spring (runs the length of the spine)
Rings (3)
Left ring half
Right ring half
Spacer and tensioner (2)
Clasps (2) (holds the locking tabs in)
Rivets (2)
Locking tabs (2)
Paperwork
Front insert
Spine insert
UPC tag
(Dependent inventory model requirements, moderate) {AACSB: Analytic Skills}
157.Jacquie Welkener, operations manager for ABC Technologies, must schedule work for the next five days. Each unit takes 30 minutes to process. Available capacity is 8 hours per day. The production order quantities are 12, 18, 20, 13, and 17 for Monday through Friday, respectively. What should be the production plan?
Sixteen units should be produced each day. Thus, 4 units should be moved from Tuesday to Monday, 2 units should be moved from Wednesday to Tuesday, 2 units should be moved from Wednesday to Thursday, and 1 unit should be moved from Friday to Thursday. (Extensions of MRP, easy) {AACSB: Analytic Skills}
406
CHAPTER 15: SHORT-TERM SCHEDULING
TRUE/FALSE
1.Delta uses mathematical short-term scheduling techniques and a high-tech nerve center to manage the rapid rescheduling necessary to cope with weather delays and similar disruptions.
True (Global company profile, moderate)
2.Short-term scheduling is important to efficiency and to cost reduction, but its impact is not of strategic importance.
False (The strategic importance of short-term scheduling, moderate)
3.The benefits of effective scheduling include lower cost, faster delivery, and dependable delivery.
True (The strategic importance of short-term scheduling, moderate)
4.In forward scheduling, jobs are scheduled as late as possible within the time allowed by the customer due dates.
False (Scheduling issues, moderate)
5.One criterion for developing effective schedules is minimizing completion time.
True (Scheduling issues, easy)
6.Scheduling optimization systems used in retail stores typically track customer traffic in 4-hour time increments.
False (Scheduling services, difficult) {AACSB: Use of IT}
7.Process-focused facilities and repetitive facilities generate forward-looking schedules, but processfocused facilities do this with JIT and kanban while repetitive facilities generally use MRP.
False (Scheduling issues, moderate)
8.The work center master file contains data such as capacity and efficiency.
True (Scheduling process-focused facilities, moderate)
9.The constant work-in-process (ConWIP) card aids input-output control by limiting the amount of work in a work center.
True (Loading jobs, easy)
10.A Gantt load chart shows the loading and idle time of several departments, machines, or facilities.
True (Loading jobs, moderate)
11.Gantt charts are useful for scheduling jobs, but not for loading them.
False (Loading jobs, easy)
12.The assignment method provides an optimum, one-to-one assignment of jobs to resources.
True (Loading jobs, easy)
13.Earliest due date is a shop floor dispatching (sequencing) rule that relates the time available to complete a job to the amount of work left to be completed.
False (Sequencing jobs, moderate)
407
14.The critical ratio sequencing rule prioritizes the jobs based on the importance or value of the customers who have placed the orders.
False (Sequencing jobs, moderate)
15.Dispatching rules are typically judged by four effectiveness criteria: average completion time, utilization, average number of jobs in the system, and average job lateness.
True (Sequencing jobs, moderate)
16.Johnson's rule (and its extensions) sequences a set of jobs through a set of operations where the operations must be performed in a specific order.
True (Sequencing jobs, moderate)
17.Finite capacity scheduling allows virtually instantaneous changes by operators, which is the technique's primary advantage over rule-based scheduling.
True (Finite capacity scheduling, moderate)
18.The word "finite" in finite capacity scheduling refers to the use of finite or limited capacity rather than unlimited capacity.
True (Finite capacity scheduling, moderate)
19.The theory of constraints is fundamental to proper use of the assignment method of loading jobs.
False (Theory of constraints, moderate)
20.The theory of constraints is a body of knowledge that deals with anything that limits an organization's ability to meet its goals.
True (Theory of constraints, easy)
21.Substantial research has proved that the only successful method of dealing with bottlenecks is to increase the bottleneck's capacity.
False (Theory of constraints, moderate)
22.The first step in level material use is to combine orders into a few large batches in order to utilize economies of scale.
False (Scheduling repetitive facilities, easy)
23.In services, the scheduling emphasis is usually on staffing levels, not materials.
True (Scheduling services, easy)
24.Because of the significance of labor in the scheduling of services, behavioral and social issues, wage and hour law, and union contracts all complicate the scheduling process.
True (Scheduling services, moderate)
25.In manufacturing scheduling, physical inventories of goods can buffer variations in demand, but service scheduling normally lacks that buffer because services are generally consumed at the same time they are delivered.
True (Scheduling services, moderate)
408
26.Some firms have developed arrangements to literally “swap” employees with each other during their respective peak demand times.
True (Scheduling services, moderate)
MULTIPLE CHOICE
27.Which of the following statements regarding scheduling at Delta Airlines is false?
a.About one flight in twenty is disrupted by weather events.
b.Schedule changes at one airport have a ripple effect that may have impacts in many others.
c.Delta's high-tech computer and communications system is located in Atlanta.
d.Delta's rapid rescheduling uses mathematical scheduling models.
e.Delta's rapid rescheduling promotes air safety and limits traveler inconvenience, but has not resulted in money savings for Delta.
e (Global company profile, moderate)
28.Which of the following best describes the strategic importance of short-term scheduling?
a.Effective scheduling, through lower costs, faster delivery, and more dependable schedules, can provide a competitive advantage.
b.Effective scheduling is a tactical tool for increasing demand to meet production.
c.Forward scheduling looks to future demand levels in order to increase customer satisfaction.
d.Aggregate planning is a tactical action, but short-term scheduling is strategic because of its immense impact on costs.
e.Short-term scheduling matches capacity to demand during the short term, three to eighteen months into the future.
a (The strategic importance of short-term scheduling, moderate)
29.The three components that can lead to competitive advantage through effective scheduling are
a.aggregate planning, intermediate scheduling, and medium-term planning
b.forward scheduling, real-time scheduling, and backward scheduling
c.the item master file, the routing file, and the work-center master file
d.lower costs, faster delivery, and more dependable schedules
e.Gantt charts, Johnson's rule and the Pareto principle
d (The strategic importance of short-term scheduling, moderate)
30.The sequence of decisions that affect scheduling is
a.short termÆintermediate termÆlong term
b.capacity planningÆaggregate planningÆmaster scheduleÆshort-term schedules
c.strategic decisionsÆtactical decisionsÆoperational decisions
d.forward decisionsÆcurrent decisionsÆbackward decisions
e.none of the above
b (Scheduling issues, moderate)
31.Forward scheduling is the scheduling of
a.the end items or finished products
b.jobs as soon as the requirements are known
c.the start items or component parts
d.the final operation first beginning with the due date
e.jobs according to their profit contributions
b (Scheduling issues, moderate)
409
32.Short-term schedules are prepared
a.directly from the aggregate plans
b.directly from the capacity plans
c.from inventory records for items that have been used up
d.from master schedules which are derived from aggregate plans
e.from the purchasing plans
d (Scheduling issues, moderate)
33.Which scheduling technique should be employed when due dates are important for a job order?
a.forward scheduling
b.loading
c.dispatching
d.backward scheduling
e.master scheduling
d (Scheduling issues, moderate)
34.Which of the following is not an effectiveness criterion for scheduling?
a.minimizing customer waiting time
b.minimizing completion time
c.minimizing WIP inventory
d.maximizing utilization
e.maximizing flow time
e (Scheduling issues, moderate)
35.The scheduling criterion minimize work-in-process inventory
a.results in the smallest flowtime of all scheduling criteria
b.is especially useful in problems solved with Johnson's rule
c.uses the average number of jobs in the system as the indicator of the level of inventory
d.is identical to the maximize utilization criterion
e.All of the above are true.
c (Scheduling issues, moderate)
36.The four criteria for short-term scheduling
a.are of equal importance
b.include maximize completion time and minimize utilization
c.are applied simultaneously
d.may have different levels of importance, depending on circumstances
e.All of the above are true.
d (Scheduling issues, moderate)
37.Scheduling is rather straightforward in product-focused facilities because
a.kanban automates the scheduling of the assembly line
b.demand is reasonably stable, and capacities, set-up times, and run times are generally known
c.assembly line balancing assures the highest possible production efficiency
d.finite capacity scheduling has made MRP much more realistic
e.All of the above are true.
b (Scheduling issues, moderate)
410