
- •1. ЦЕЛЬ РАБОТЫ
- •2. ОСНОВНЫЕ СВЕДЕНИЯ
- •2.1. Оборудование для плазменного напыления
- •2.2. Напыляемые материалы
- •2.2.1. Металлы и сплавы
- •2.2.2. Оксиды
- •2.3. Технология нанесения покрытий
- •2.3.1. Подготовка напыляемых материалов
- •2.3.2. Механическая обработка поверхностей
- •2.3.3. Напыление подслоя
- •2.3.4. Получение покрытий напылением
- •2.3.5. Оплавление покрытий
- •2.3.6. Механическая обработка покрытий
- •2.4. Требования к покрытию
- •3. ЗАДАЧИ РАБОТЫ
- •4. ОТЧЕТ ПО РАБОТЕ
- •5. ОХРАНА ТРУДА
- •6. КОНТРОЛЬНЫЕ ВОПРОСЫ
- •БИБЛИОГРАФИЧЕСКИЙ СПИСОК
- •Основной
- •Дополнительный
МИНИСТЕРСТВО ОБРАЗОВАНИЯ И НАУКИ РОССИЙСКОЙ ФЕДЕРАЦИИ
СЫКТЫВКАРСКИЙ ЛЕСНОЙ ИНСТИТУТ – ФИЛИАЛ ГОСУДАРСТВЕННОГО ОБРАЗОВАТЕЛЬНОГО УЧРЕЖДЕНИЯ
ВЫСШЕГО ПРОФЕССИОНАЛЬНОГО ОБРАЗОВАНИЯ «САНКТ-ПЕТЕРБУРГСКАЯ ГОСУДАРСТВЕННАЯ ЛЕСОТЕХНИЧЕСКАЯ АКАДЕМИЯ ИМЕНИ С. М. КИРОВА»
КАФЕДРА ОБЩЕТЕХНИЧЕСКИХ ДИСЦИПЛИН
И. В. Боровушкин
ПЛАЗМЕННАЯ ОБРАБОТКА МАТЕРИАЛОВ
Методическое руководство к лабораторным и практическим занятиям по дисциплине
«Технология конструкционных материалов и материаловедение» для студентов специальностей 170400, 150200, 230100, 311300, 311400
всех форм обучения
Самостоятельное учебное электронное издание
СЫКТЫВКАР 2010
УДК 621.7 ББК 30.3
Б83
Утверждено к опубликованию в электронном виде советом лесотранспортного факультета Сыктывкарского лесного института 15 сентября 2010 г. (протокол № 1).
Рецензент:
Л. В. Шильников, начальник техбюро главного механика (ОАО «Монди Сыктывкарский ЛПК»)
Ответственный редактор:
А. Ф. Кульминский, кандидат технических наук, доцент
Боровушкин И. В.
Б83 ПЛАЗМЕННАЯ ОБРАБОТКА МАТЕРИАЛОВ [Электронный ресурс] : методическое руководство к лабораторным и практическим занятиям по дисциплине «Технология конструкционных материалов и материаловедение» для студентов специальностей 170400, 150200, 230100, 311300, 311400 всех форм обучения: самост. учеб. электрон. изд. / СЛИ ; И. В. Боровушкин. – Электрон. дан. (1 файл в формате pdf: 1,2 Мб). – Сыктывкар : СЛИ, 2010. – Ре-
жим доступа: http://lib.sfi.komi.com. – Загл. с экрана.
УДК 621.7 ББК 30.3
Методическое руководство предназначено для студентов специальностей 170400, 150200, 230100, 311300, 311400 всех форм обучения, изучающих дисциплину «Технология конструкционных материалов и материаловедение». Приведена теоретическая часть по теме, определен порядок работы. Для самоподготовки даны контрольные вопросы и рекомендована литература.
Темплан 2009/10 учеб. г. Изд. № 157.
* * *
Самостоятельное учебное электронное издание
БОРОВУШКИН Игорь Владимирович, профессор, кандидат технических наук, доцент
ПЛАЗМЕННАЯ ОБРАБОТКА МАТЕРИАЛОВ
Методическое руководство к лабораторным и практическим занятиям по дисциплине «Технология конструкционных материалов и материаловедение» для студентов специальностей 170400, 150200, 230100, 311300, 311400 всех форм обучения
Электронный формат – pdf
Разрешено к публикации 30.09.10. Объем 2,4 уч.-изд. л.; 1,2 Мб
_______________________________________________________________________________________
Сыктывкарский лесной институт – филиал государственного образовательного учреждения высшего профессионального образования «Санкт-Петербургская государственная лесотехническая академия имени С. М. Кирова» (СЛИ). 167982, г. Сыктывкар, ул. Ленина, 39
institut@sfi.komi.com, www.sli.komi.com
_______________________________________________________________________________________
Редакционно-издательский отдел СЛИ. Заказ № 82.
© СЛИ, 2010 © И. В. Боровушкин, 2010
2
|
ОГЛАВЛЕНИЕ |
|
1. |
ЦЕЛЬ РАБОТЫ........................................................................................................................................ |
4 |
2. |
ОСНОВНЫЕ СВЕДЕНИЯ...................................................................................................................... |
4 |
|
2.1. Оборудование для плазменного напыления.................................................................................. |
6 |
|
2.2. Напыляемые материалы................................................................................................................ |
15 |
|
2.2.1. Металлы и сплавы.................................................................................................................. |
15 |
|
2.2.2. Оксиды..................................................................................................................................... |
16 |
|
2.3. Технология нанесения покрытий ................................................................................................. |
17 |
|
2.3.1. Подготовка напыляемых материалов................................................................................. |
18 |
|
2.3.2. Механическая обработка поверхностей ............................................................................. |
18 |
|
2.3.3. Напыление подслоя................................................................................................................. |
20 |
|
2.3.4. Получение покрытий напылением........................................................................................ |
21 |
|
2.3.5. Оплавление покрытий............................................................................................................ |
24 |
|
2.3.6. Механическая обработка покрытий.................................................................................... |
25 |
|
2.4. Требования к покрытию................................................................................................................ |
27 |
3. |
ЗАДАЧИ РАБОТЫ................................................................................................................................ |
28 |
4. |
ОТЧЕТ ПО РАБОТЕ.............................................................................................................................. |
29 |
5. |
ОХРАНА ТРУДА................................................................................................................................... |
30 |
6. |
КОНТРОЛЬНЫЕ ВОПРОСЫ............................................................................................................... |
31 |
БИБЛИОГРАФИЧЕСКИЙ СПИСОК...................................................................................................... |
32 |
|
|
Основной................................................................................................................................................ |
32 |
|
Дополнительный................................................................................................................................... |
32 |
3
1. ЦЕЛЬ РАБОТЫ
Целью работы является знакомство с технологиями плазменной обработки материалов, с оборудованием и материалами плазменной резки, сварки, напыления, использованием концентрированных высокоэнергетических источников в различных областях техники, в том числе при проектировании, производстве и ремонте оборудования лесного комплекса.
2. ОСНОВНЫЕ СВЕДЕНИЯ
Во многих изделиях их поверхность определяет работоспособность изделия в целом и в частности такие характеристики, как сопротивление износу, жаростойкость, коррозионную стойкость и др. В парах трения (валы, оси, пальцы) износ в десятые и сотые доли миллиметра (посадочные места подшипников) приводит к необходимости разборки механизма и замене изношенных деталей. Восстановление деталей выполняется различными способами: гальванически путем нанесения слоев хрома или железа; наплавкой нелегированными или легированными материалами; напылением различных металлов, сплавов и неметаллических соединений (карбиды, оксиды, интерметаллиды). Все эти способы применяются в промышленности, имея свои достоинства и недостатки.
Широкое применение напыления для восстановления и упрочнения поверхностей объясняется тем, что при напылении температура напыляемого изделия не превышает, как правило, 150–200 ºС, что позволяет избежать напряжений, деформаций и структурных изменений в поверхностных слоях, так характерных для сварки и наплавки. При этом отсутствует проплавление напыляемой поверхности и, как следствие, проникновение металла подложки в напыляемый, обычно легированный, слой, чего трудно избежать при наплавке и что вызывает необходимость выполнять много слоев, затрачивая материал, энергию, время и увеличивая вероятность трещин и деформаций в наплавляемых изделиях.
При гальваническом восстановлении изделий очень велики затраты электрической энергии, затруднительно восстановление локальных участков, дорого и небезопасно утилизировать отходы гальванических процессов.
Плазменное напыление – процесс нанесения покрытия на поверхность детали (изделия) с помощью плазменной струи. Плазменная струя – это частично или полностью ионизированный газ, обладающий электропроводностью и имеющий высокую температуру.
Различают высоко- и низкотемпературную плазму. Первая, так называемая физическая плазма, ионизирована практически полностью, и ее электронная температура оценивается в сотни тысяч и более градусов. Низкотемпературная – технологическая – плазма, с температурой в несколько тысяч или десятков тысяч градусов, ионизирована частично и содержит значительную долю нейтральных частиц.
Низкотемпературная плазма – многокомпонентная система, состоящая из атомов или молекул в основном состоянии; молекул, атомов, радикалов в различных возбужденных квантовых состояниях; ионов, электронов. Для напыления плазменных покрытий применяется низкотемпературная плазма.
4
Сущность плазменного напыления заключается в том, что в высокотемпературную плазменную струю подается распыляемый материал, который нагревается, плавится и в виде двухфазного потока направляется на подложку. При ударе и деформации происходит взаимодействие напыляемых частиц с поверхностью основы или с уже напыленным материалом и в результате формирование покрытия.
Плазменный процесс состоит из трех основных стадий:
1)генерация плазменной струи;
2)ввод распыляемого материала в плазменную струю, его нагрев и ускорение;
3)взаимодействие плазменной струи и расплавленных частиц с основой. Плазменным напылением наносятся износостойкие, антифрикционные, корро-
зионностойкие и другие покрытия.
Напыление с помощью низкотемпературной плазмы позволяет:
−избежать участия в напыленном слое химических элементов подложки;
−использовать различные материалы: металлы, сплавы, оксиды, карбиды, нитриды, бориды, пластмассы и различные их комбинации;
−наносить несколько разнородных слоев, получая покрытия со специальными характеристиками;
−наносить покрытия на листовые материалы, на конструкции больших размеров и поверхности сложной формы;
−практически избежать деформации основы, на которую производится напы-
ление;
−покрывать изделия из самых разнообразных материалов, включая материалы, не терпящие термообработки в печи (стекло, фарфор, дерево, ткань);
−значительно увеличить размеры детали (восстановление и ремонт изношенных деталей). Этим методом можно наносить слои толщиной несколько миллиметров;
−обеспечить равномерное напыление как большой площади, так и ограниченных участков больших изделий;
−легко механизировать и автоматизировать процесс напыления;
−обеспечить высокую производительность нанесения покрытия при относительно небольшой трудоемкости;
−улучшить качество покрытий. Они получаются более равномерными и стабильными, высокой плотности и с хорошим сцеплением с поверхностью.
К основным недостаткам метода нанесения покрытий напылением можно отне-
сти:
−неэкономичность процесса напыления при нанесении покрытий на небольшие детали из-за больших потерь напыляемого материала, пролетающего в струе мимо изделия. В таких случаях покрытие лучше наносить другими способами;
−сильный шум, ультрафиолетовое излучение, образование вредных для здоровья работающих соединений напыляемого материала с воздухом, которое сопровождает процесс напыления.
5
2.1. Оборудование для плазменного напыления
Для получения плазмы используются различные генераторы низкотемпературной плазмы – плазмотроны, которые должны обеспечить выполнение следующих требований:
− температура плазмы на выходе должна быть достаточно высокой (от
10 000 К);
−плазма должна быть достаточно чистой, т. е. свободна от загрязнения частицами, которые не входят в состав рабочего слоя;
−высокая эффективность преобразования электрической энергии в тепловую, что обеспечивает возможность получения максимального КПД технологического процесса;
−параметры низкотемпературной плазмы должны быть стабильными, управляемыми и обеспечивать оптимальные условия процесса;
−генерация плазмы должна обеспечиваться в течение длительного промежутка времени;
−возможность использования различных плазмообразующих сред;
−простота эксплуатации, легкость возбуждения электрического разряда, желательно без ввода дополнительных устройств (поджигающих электродных проволочек) в область разрядного канала;
−легкость ввода исходного материала в плазменный поток.
Для организации промышленных технологических плазменных процессов наиболее перспективными в настоящее время считаются электродуговые генераторы низкотемпературной плазмы, поскольку именно они наиболее полно удовлетворяют перечисленным выше требованиям. Наиболее простой нагреватель газа представляет собой дуговой электрический разряд, горящий между двумя торцовыми электродами, обдуваемый плазмообразующим газом в осевом или перпендикулярном направлении. В дуге газ ионизируется и за разрядом образуется плазменная струя с высокой температурой, что позволяет использовать его для резки металлических и неметаллических материалов, для сварки металлов и сплавов, для напыления металлов и неметаллических соединений – карбидов, оксидов, интерметаллидов на различные подложки. В качестве плазмообразующих газов используются аргон, азот, водород, их смеси, а также воздух.
Электродуговые плазмотроны позволяют получить следующие параметры плазменных струй:
−скорость нагретого газа на выходе из дуговых плазмотронов – от 10 до 100 М (в зависимости от расхода плазмообразующего газа, диаметра сопла плазмотрона, мощности в дуге);
−максимальная температура на оси струи – от 10 000 до 50 000 К;
−среднемассовая температура нагретого газа 10 000 К при работе на одноатомных газах и 4 000–5 000 К при работе на двухатомных плазмообразующих газах (азот, водород, их смеси).
Особенность работы электродуговых плазменных установок состоит в высокой эффективности преобразования электрической энергии в тепловую; в стабильности горения электрической дуги; возможной эрозии электродов, что приводит к загрязненности плазменной струи.
6
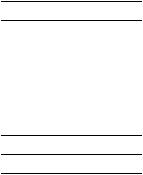
Плазменные покрытия наносят обычно на воздухе в специальном помещении с вытяжной вентиляцией или в герметичной камере с контролируемой атмосферой чаще всего с нейтральной. Для нанесения плазменных покрытий применяются такие установки, как УПУ-ЗД, УМП-6, «Киев-7» и др. (табл. 1). Эти установки предназначены для получения плазменным напылением теплозащитных, жаростойких, электроизоляционных, износостойких и антикоррозионных покрытий из металлических порошков и керамики на внутренние и наружные поверхности вращения, а также на поверхности плоских изделий.
Таблица 1 Технические характеристики плазменных электродуговых установок
Параметры |
УПУ-3Д |
УМП-6 |
«Киев-7» |
Потребляемая мощность, кВт |
35 |
30 |
40 |
Максимальный ток дуги, А |
400 |
– |
– |
Расход газов, м3/ч |
0,9–6,0 |
3,0–5,0 |
3,2–5 |
Рабочее давление газов, МПа |
0,3–0,4 |
0,4–0,5 |
0,124 |
Расход воды, м3/ч |
0,48–0,60 |
– |
0,6 |
Производительность распыления, кг/ч |
До 2 |
До 7 |
До 7 |
Размеры, мм |
1650 × 700 × 450 |
1640 × 1100 × 400 |
1600 × 600 × 450 |
Масса, кг |
200 |
265 |
300 |
Установка для плазменного напыления включает: плазмотрон, источник питания, газораспределительную систему, механизм подачи материала, систему охлаждения, пульт управления и различные элементы оснастки.
На рис. 1 представлена принципиальная схема универсальной плазменной установки УМП-6, на рис. 2 – пульт управления ее.
В качестве источника питания установки УМП-6 применяется полупроводниковый выпрямитель ИПН-160/600-Ш, состоящий из трехфазного силового трансформатора с плавным регулированием рабочего тока (до 600 А), выпрямительного блока, пускорегулирующей аппаратуры. В источнике предусмотрен переключатель для получения напряжения холостого хода: 80, 120, 160 В. Вместе с тем, вместо выпрямителя ИПН-160/600-Ш могут использоваться и обычные сварочные генераторы, соединенные последовательно для увеличения напряжения холостого хода, а также сварочные выпрямители, применяемые для сварки. Источники питания плазменной дуги должны иметь крутопадающую внешнюю вольтамперную характеристику.
Плазмотрон – газоразрядное устройство, служащее для нанесения плазменных покрытий. Наиболее важным элементом плазмотрона является сопло, от конструкции которого зависит длина дуги, стабильность ее горения, а также скорость и характер истечения струи. Сопловой (анодный) узел через электроизоляционный блок стыкуется с катодным узлом, представляющим собой стержневой электрод, изготовленный из вольфрама с добавкой иттрия или лантана. Отрицательный вывод источника постоянного тока присоединяется к вольфрамовому стержню-катоду, а положительный к соплу-аноду. Плазмообразующий газ подается во внутреннюю межэлектродную камеру, образованную медным соплом-анодом и вольфрамовым электродом. Принципиальная схема электродугового плазмотрона для напыления покрытий дана на рис. 3.
7
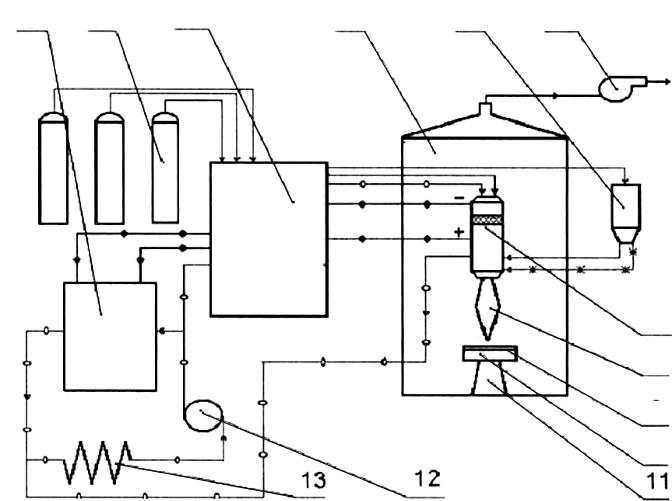
1 |
2 |
3 |
4 |
5 |
6 |
7
8
9
10
|
|
12 |
|
|
13 |
|
|
|
|
|
11 |
|||
|
|
|
|
|
–––♦–––♦–––♦––– электрический ток; –––o–––o–––o––– вода;
–––◊–––◊–––◊––– газ; –––*–––*–––*––– порошок
Рис. 1. Принципиальная схема плазменной установки УМП-6:
1 – источник питания; 2 – баллоны с газом; 3 – пульт управления; 4 – камера напыления; 5 – порошковый дозатор; 6 – вытяжной вентилятор; 7 – плазмотрон; 8 – плазменная струя; 9 – напыленное покрытие; 10 – изделие; 11 – устройство для перемещения изделия;
12 – водяной насос; 13 – холодильник
8
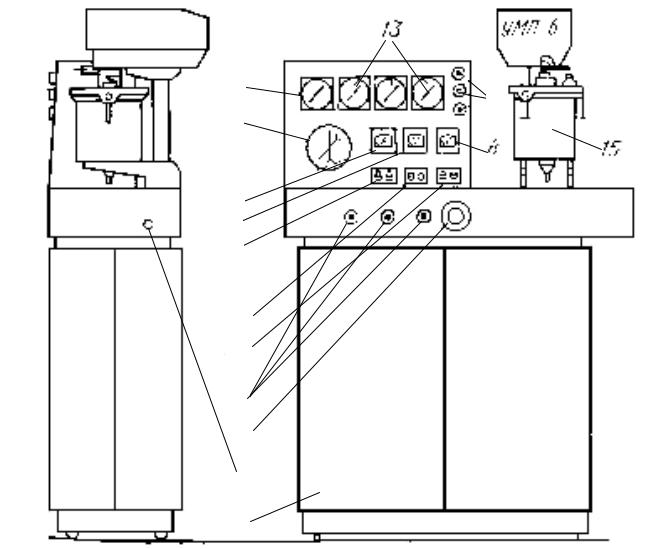
13 |
|
УМП-6 |
12
14
11
8 |
|
15 |
|
|
|
10
9
7
6
5
4
3
2
1
Рис. 2. Пульт управления установкой УМП-6:
1 – пульт управления; 2 – механизм подъема порошкового дозатора; 3 – регулятор подачи порошка; 4 – вентили; 5, 6 – кнопки «пуск»-«стоп»; 7 – тумблеры;
8 и 9 – вольтметры; 10 – амперметр; 11 – термометр манометрический; 12 – манометр водяной; 13 – манометры газовые; 14 – лампы сигнальные; 15 – дозатор порошка
9
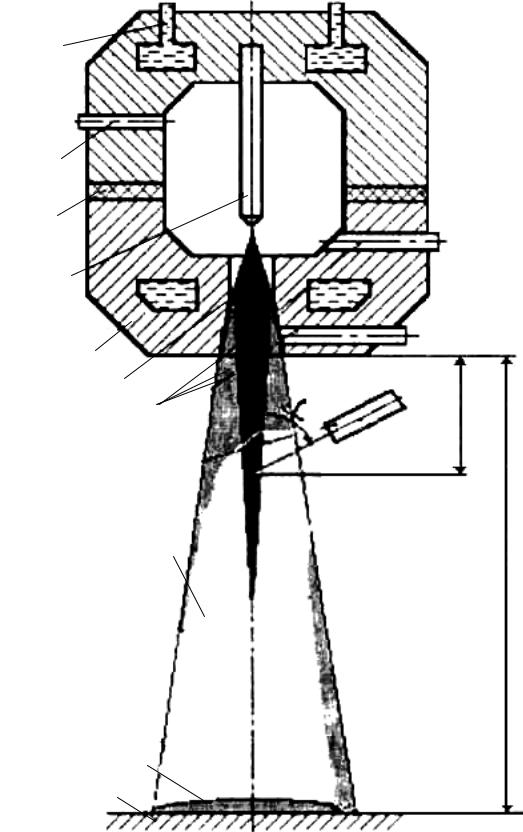
1
2
3
4
5
6
7
K
8
L
9
10
Рис. 3. Электродуговой плазмотрон для напыления:
K – дистанция ввода порошка в плазменную струю; L – дистанция напыления; α – угол ввода порошка в плазменную струю; 1 – водяное охлаждение;
2 – вход плазмообразующего газа; 3 – электроизоляционный блок; 4 – катод плазмотрона; 5 – сопло – анод плазмотрона; 6 – плазменная струя; 7 – ввод напыляемого порошка;
8 – плазменная струя с нагретым порошком; 9 – напыленное покрытие; 10 – напыляемое изделие
10
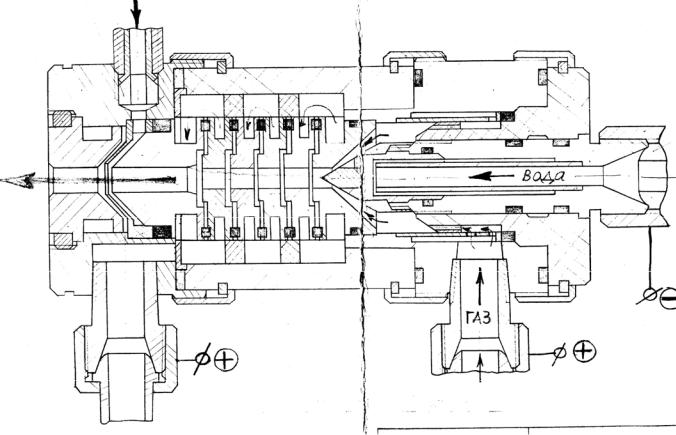
При использовании в качестве плазмообразующего газа аргона или азота, их смесей применяется вольфрамовый или медный водоохлаждаемый электрод. Если же используется воздух, то применяется гафниевый или (реже) циркониевый электрод, запрессованный в медную обойму. Необходимость использования гафния или циркония связана с тем, что вольфрам при высокой температуре интенсивно окисляется в среде воздуха.
Для увеличения мощности плазмы за счет поднятия напряжения расстояние между катодом и анодом увеличивают за счет промежуточных вставок, изолированных как от катода, так и от анода. На рис. 4 показан воздушно-плазменный плазмотрон с промежуточными медными вставками.
Для возбуждения дуговой плазмы напряжения, прикладываемого к электродам, недостаточно. Поэтому для возбуждения дуги прибегают к дополнительным мероприятиям, обеспечивающим появление ионизированных частиц в межэлектродном пространстве. Для возбуждения плазменной струи обычно используют высокочастотную искру, которую получают от осциллятора, встроенного в источник питания. Генератор высокой частоты дает первоначальный импульс, от которого атомы газа возбуждаются и ионизируются. Между полюсами загорается дуга, поддерживающая уровень ионизации.
Рис. 4. Плазмотрон с промежуточными вставками
Плазменная струя оформляется медным соплом. Благодаря охлаждающему действию стенок сопла наружные слои столба деионизируются и объем ионизированной части столба уменьшается. Это приводит к повышению напряжения дуги и значительному увеличению плотности тока в столбе. Плазменная струя обжимается
11
еще и магнитным полем, создаваемым потоком заряженных частиц в плазме. Обжатие плазменной струи способствует росту ее температуры. Нагретый ионизированный поток газа выносится с высокой скоростью из сопла в виде яркосветящейся плазменной струи высокой температуры (5 000–15 000 ºС).
Как уже отмечалось, мощность плазмотрона зависит от размеров межэлектродного пространства. Коэффициент полезного действия плазмотрона 60–80 %, примерно 0,8 всей мощности плазмотрона расходуется на нагрев плазмообразующего газа. Наибольшему разрушению подвергается сопло плазмотрона, поэтому оно изготавливается из меди и делается сменным. Срок службы сопла зависит от режима работы плазмотрона, вида плазмообразующего газа, его чистоты по содержанию кислорода и влаги, системы охлаждения и составляет от 15 до 1000 ч.
Важной конструктивной особенностью плазмотрона является место ввода напыляемого порошка. Напыляемый материал может вводиться в столб плазмы через анодный сопловой узел и за срез плазмотрона (рис. 3). Выбор места зависит от теплофизических свойств материала, его сыпучести, склоннности к комкованию.
Дистанционный пульт управления позволяет плавно и достаточно точно регулировать основные энергетические параметры плазменной обработки (электрические параметры, расход плазмообразующего и транспортирующего газов).
Независимо от типа плазмотрона, надежная работа установок для плазменного напыления зависит от ряда факторов, одним из которых является эффективность системы охлаждения. Наиболее эффективное охлаждение можно обеспечить, используя системы замкнутого типа с применением специальных устройств, улучшающих отвод тепла. Надежная работа плазменных установок может быть достигнута предварительным снижением температуры охлаждающей среды холодильного агрегата до +2 ºС, электромагнитной обработкой охлаждающей воды, использованием дистиллированной воды в контуре хладагента.
Вкачестве плазмообразующих газов при нанесении покрытий применяют аргон, азот, смеси аргона с азотом или водородом или, при определенных условиях, воздух. Все эти газы поставляются в баллонах. Баллоны с редукторами устанавливаются вне помещения, в специально оборудованных шкафах. Аргоновая плазма (ионизированный газ) имеет высокую температуру 15 000–30 000 К. Температура азотной плазмы ниже (10 000–15 000 К), но имеет высокое теплосодержание за счет поглощенной энергии диссоциации и ионизации, выделяемой при рекомбинации (при охлаждении газа в свободной плазменной струе). Аргон значительно дороже азота. Исходя из вышеизложенного, наиболее широко в качестве плазмообразующего газа применяется азот или воздух. При использовании воздуха он подается от воздушного компрессора через осушители.
При плазменном нанесении покрытий в качестве исходного материала может использоваться проволока или порошок. Порошковое плазменное напыление более экономично, чем проволочное, позволяя получать покрытия более высокого качества.
При порошковом напылении используются питатели (дозаторы) различных конструкций.
Встандартной установке УМП-6 применяется порошковый питатель, конструкция которого дана на рис. 5.
Дозатор состоит из следующих основных узлов: бачка, механизма перемещения порошка, системы транспортирующего газа, привода с кулачковой муфтой. Количе-
12
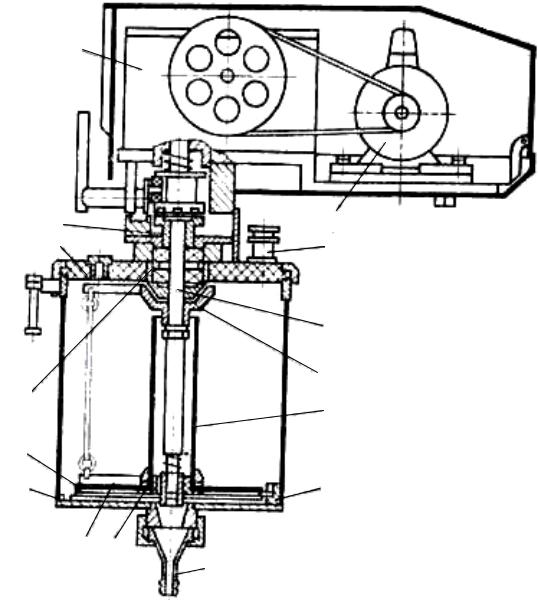
ство порошка, подаваемого в плазмотрон несущим газом, определяется скоростью вращения ротора с лопатками.
Широко распространены и роторные дозаторы, где подача порошка из бункера осуществляется колесом-крыльчаткой, частота вращения которого определяет количество расходуемого порошка и регулируется электрической схемой. Именно такой дозатор (рис. 6) установлен на установке УМП-6 в лаборатории «Технология конструкционных материалов» кафедры ОТД.
6
5
4
3
2
1
15 14
13
7
8
9
10
11
12
Рис. 5. Порошковый дозатор установки УМП-6:
1 – бачок дозатора; 2 – днище съемное; 3 – лопатки верхние; 4 – крышка; 5 – муфта; 6 – редуктор; 7 – электродвигатель; 8 – клапан предохранительный; 9 – валик ротора; 10 – подвеска;
11 – труба центральная; 12 – упор; 13 – воронка с ниппелем; 14 – шнек; 15 – лопатки нижние
13
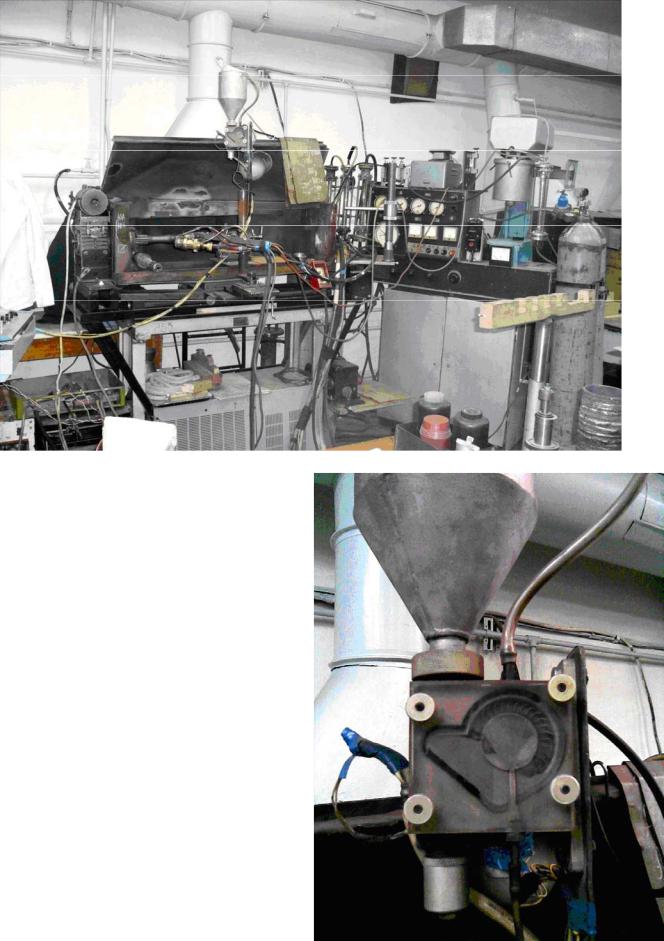
а)
б)
Рис. 6. Плазменный пост для напыления (а); роторный дозатор (б) 14