
Лекции_Конспект_Логистика
.pdf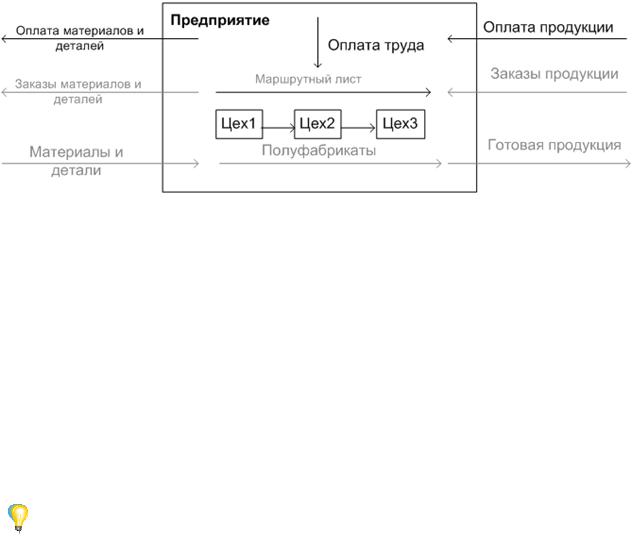
Оплата материалов и деталей рождает исходящий по отношению к предприятию финансовый поток.
Оплата продукции – входящий.
Оплата труда работникам предприятия – внутренний.
2. По назначению, финансовые потоки делятся на: а) ФП, обусловленные процессом закупки товаров; б) ФП, возникающие в процессе продажи товаров; в) инвестиционные;
г) ФП, связанные с формированием материальных затрат в процессе производственной деятельности предприятий;
Есть такое понятие как «Уровень неснижаемых остатков». Т.е. чтобы производство работало бесперебойно, необходимо, чтобы материалы, детали всегда были в определённом количестве – не ниже определённого уровня. Когда какая-то деталь подходит к этому уровню, - это уже звонок в Отдел закупок, чтобы они её докупили.
А если деталей значительно больше уровня неснижаемых остатков это плохо или хорошо?
Это плохо, т.к. большой запас – связывает значительные финансовые средства. Если весь все остатки в производстве перевести в денежную форму, то получатся миллионы рублей, которые постоянно лежат на складах и цехах.
Т.о. затраты на поддержание Уровня неснижаемых остатков – рождают ФП вида г). д) ФП по воспроизводству рабочей силы.
Воспроизводство рабочей силы - непрерывное возобновление социальных, культурных и профессиональных характеристик рабочей силы.
Z.B. «Текучесть» кадров работников цехов предприятий составляет в настоящее время около 25% в год. Т.е. четверть работников за год уходит, а значит получаем низкую квалификацию рабочих, что в конечном итого сказывается на качестве продукции.Поэтому предприятия вынуждены финансировать обучение, питание, медицинское обслуживание и отдых своих работников, для реализации воспроизводства.
3. В зависимости от применяемых форм расчётов, ФП делятся на:
11
а) денежные ФП, характеризующие движение наличных фин. средств;
б) информационно-финансовые потоки, обусловленные движением безналичных фин. средств.
4. По видам хозяйственных связей различают:
а) горизонтальные ФП, характеризующие движение денежных средств между равноправными субъектами предпринимательской деятельности (например, между двумя дочерними компаниями);
б) вертикальные ФП, характеризующие движение денежных средств между неравноправными субъектами (например, между материнской и дочерней компанией).
2.2. Понятие и отличительные признаки логистической системы
Вопрос 5. Понятие и отличительные признаки логистической системы
Одним из наиболее важных в логистике является понятие логистической системы.
В принципе, любая система (от греч. systema – целое, составленное из частей) представляет собой совокупность взаимосвязанных элементов (звеньев), образующих определённую целостность.
Логистическая система (ЛС) – сложная организационно завершённая (структурированная) экономическая система, которая состоит из элементовзвеньев, взаимосвязанных в едином процессе управления материальными и сопутствующими информационными и финансовыми потоками.
Прежде чем дать разъясняющий пример, дадим ещё несколько определений.
Любая ЛС состоит из совокупности элементов – звеньев, между которыми установлены определённые функциональные связи и отношения.
Звено логистической системы (ЗЛС) – экономически или (и) функционально обособленный объект, неделимый в рамках поставленной задачи анализа или построения ЛС, выполняющий свою локальную цель, связанную с определёнными логистическими операциями или функциями.
Любая система, в том числе логистическая, имеет 4-е отличительных признака:
1.Целостность и делимость. Система есть целостная совокупность элементов (звеньев), взаимодействующих друг с другом.
2.Связи. Между элементами системы имеются существенные связи, которые могут быть материальными, информационными, прямыми и обратными и т.д.
3.Организация. Связи и элементы системы должны быть упорядочены, т.е. иметь определённую структуру.
4.Интегративные качества. Это качества, присущие системе в целом, но не свойственные и одному элементу в отдельности.
Z.B. Шариковая ручка, как система.
Можно привезти множество примеров систем. Возьмём шариковую ручку и проверим, имеет ли она 4-е признака системы.
1. Ручка является единым целым и состоит из отдельных элементов: корпус, колпачок, стержень, пружина и т.д.
12
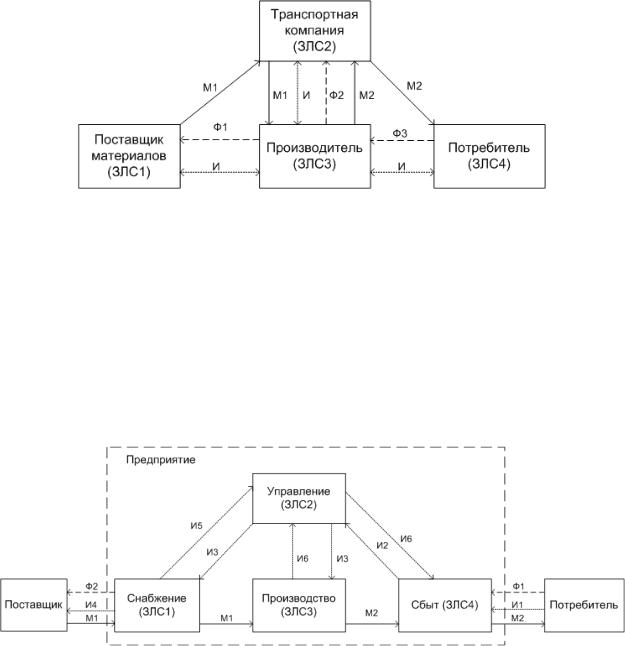
2.Между элементами есть связи – ручка не рассыпается, благодаря связям между элементами.
3.Элементы ручки связаны в определённом порядке, иначе бы она развалилась.
4.Ручкой удобно писать и носить, чем не обладает ни один из её элементов.
Точно также можно доказать, что такие объекты, как автомобиль, оптовая база, предприятие, совокупность взаимосвязанных предприятий являются системами.
Z.B. На макроуровне, при прохождении материального, информационного и финансового потока от одного предприятия к другому в качестве элементов (звеньев) системы могут рассматриваться сами предприятия, а также связывающий их транспорт.
М – материальный поток; Ф – финансовый поток;
И – информационный поток.
М1 – материалы, доставляемые транспортной компанией к производителю; М2 – готовая продукция, доставляемая транспортной компанией к потребителю; Ф1 – оплата материалов производителем; Ф2 – оплата услуг транспортной компании производителем;
Ф3 – оплата готовой продукции потребителем.
И – соответствующие информационные потоки между предприятиями.
На микроуровне, само предприятие является логистической системой, содержащей следующие основные подсистемы (звенья):
Звено «Снабжение» - обеспечивает поступление материального потока в ЛС. Звено «Сбыт» - обеспечивает выбытие материального потока из ЛС.
Звено «Производство» - принимает материальный поток из звена «Снабжение», преобразует его в ходе различных технологических операций, и передаёт в звено «Сбыт».
13
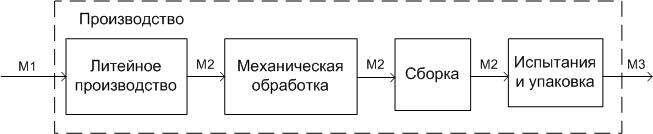
Звено «Управление» - с помощью информационных потоков обеспечивает согласованную работу всех звеньев ЛС.
Звенья «Поставщик» и «Потребитель» не входят в данную ЛС.
И1 – заказ продукции предприятия потребителем; Ф1 – оплата продукции предприятия потребителем; И2 – портфель заказов; И3 – план производства;
И4 – заказ материалов у поставщика; Ф2 – оплата материалов предприятием М1 – материалы;
И5 - информация о выполнении плана закупок; И6 – информация о выполнении плана производства; М2 – готовая продукция.
Потребитель делает заказ на продукцию предприятия (И1), которая обрабатывается в ЗЛС «Сбыт». На основании всех заказов, собранных от потребителей, формируется портфель заказов (И2), который поступает в ЗЛС «Управление». На основании портфеля заказов формируется План производства (И3), которым руководствуются ЗЛС «Производство» и ЗЛС «Снабжение». На основании Плана производства ЗЛС «Снабжение» готовит План закупок (нет на схеме), руководствуясь которым делает заказы на материалы у поставщика (И4). После поступления оплаты (Ф2), поставщик привозит материалы (М1), поступающие в ЗЛС «Снабжение», которое информирует об этом ЗЛС «Управление» (И5). Далее материалы поступают в ЗЛС «Производство», где из них получается готовая продукция (М2). ЗЛС «Производство» информирует ЗЛС «Управление» о выполнении плана производства (И6). Готовая продукция (М2) поступает в ЗЛС «Сбыт» и далее – потребителю.
При более подробном рассмотрении каждое из перечисленных звеньев само разворачивается в сложную систему или цепь:
М1 – материалы; М2 – полуфабрикаты;
М3 – готовая продукция.
Логистическая функция – обособленная совокупность логистических операций, направленных на реализацию поставленных перед ЛС или ЗЛС задач.
Логистическая операция – действие, не подлежащее дальнейшей декомпозиции в рамках поставленной задачи, связанное с возникновением, преобразованием или поглощением материального и сопутствующих информационных и финансовых потоков.
14
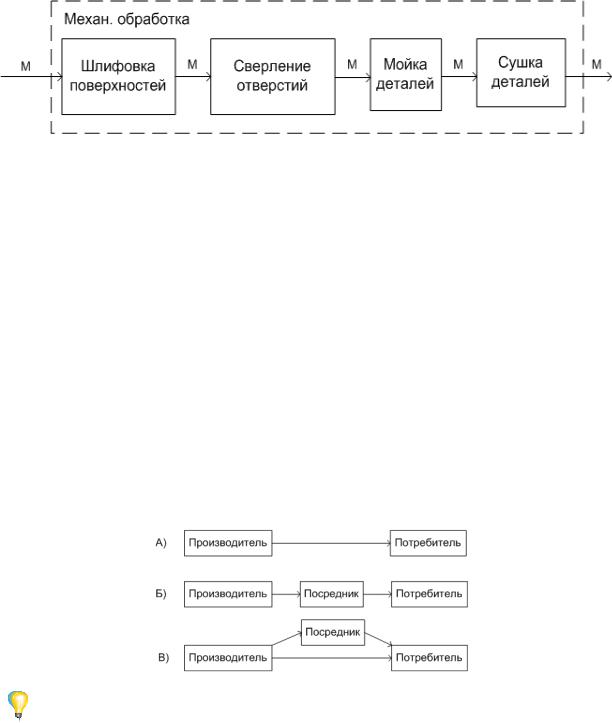
Z.B. Если рассмотреть технологический процесс механической обработки деталей, то он представляет собой набор действий, таких как шлифовка поверхностей, сверление отверстий, мойка деталей и сушка деталей.
В приведённом примере Механ. обработка – представляет собой Логистическую функцию, а шлифовка поверхностей, сверление отверстий, мойка деталей и сушка деталей –
Логистические операции.
2.3. Виды логистических систем
Вопрос 8. Виды логистических систем
Логистические системы делят на макро- и микрологистические.
Макрологистическая система – это крупная система управления материальными и сопутствующими им информационными и финансовыми потоками, охватывающая промышленные предприятия, посреднические, торговые и транспортные организации, расположенные в разных регионах страны или в разных странах. Подобная система представляет собой определённую инфраструктуру региона, страны или группы стран.
На уровне макрологистики выделяют три вида ЛС:
1.ЛС с прямыми связями. В них материальный поток проходит непосредственно от производителя продукции к её потребителю (рис.а)
2.Эшелонированные ЛС. В таких системах на пути материального потока есть хотя бы один посредник. (рис. б)
3.Гибкие ЛС. В таких системах движение материального потока от производителя к потребителю может осуществляться как напрямую, так и через посредников (рис. в).
Примером а) может послужить КМЗ, где горно-шахтное оборудование заказывается потребителем напрямую. Потребитель – различные угледобывающие компании. Примером б) служат предприятия пищевой промышленности, продукция которых сначала поступает в гипермаркеты, а затем – к конечному потребителю.
Примером в) – хлебопекарня, где хлеб продаётся напрямую потребителю, либо поступает к нему через посредников.
15
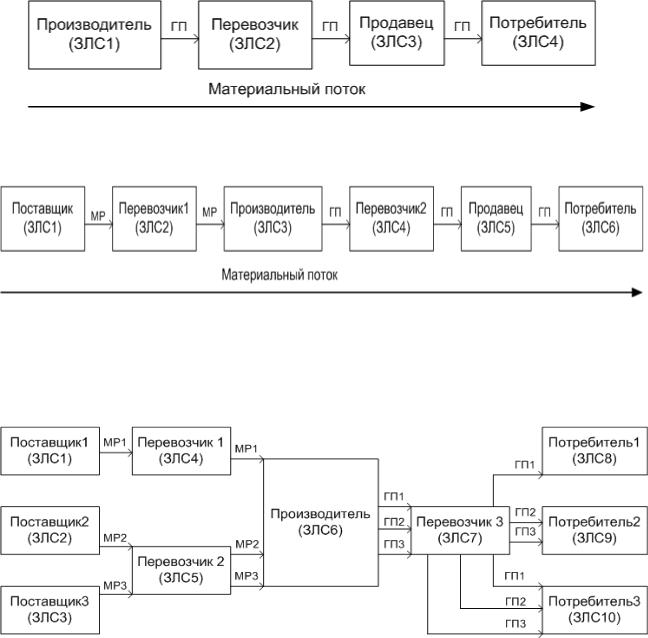
Микрологистические системы являются подсистемами, структурными составляющими макрологистических систем. К ним относят производственные и торговые предприятия, территориальнопроизводственные комплексы.
2.4. Логистические цепи и логистические каналы
Логистическая цепь – множество звеньев ЛС, линейно упорядоченное по материальному (информационному, финансовому) потоку с целью анализа или проектирования определённого набора логистических функций и издержек.
Полная логистическая цепь – линейно упорядоченное множество звеньев ЛС от поставщика материальных ресурсов, до конечного потребителя готовой продукции.
Логистический канал – упорядоченное множество звеньев ЛС, включающее в себя все логистические цепи или их участки, проводящие материальные потоки от поставщиков материальных ресурсов до конечного потребителя, и необходимые для изготовления конкретного вида продукции.
Производитель (ЗЛС6) изготавливает три вида продукции – ГП1, ГП2, ГП3, которая поступает к трём разным потребителям – ЗЛС8, ЗЛС9, ЗЛС10.
Для производства продукции использует три вида материалов – МР1, МР2, МР3, поставляемых от трёх разных поставщиков – ЗЛС1, ЗЛС2, ЗЛС3.
Для перевозки материалов и готовой продукции, производитель пользуется услугами трёх разных перевозчиков – ЗЛС4, ЗЛС5, ЗЛС7.
16
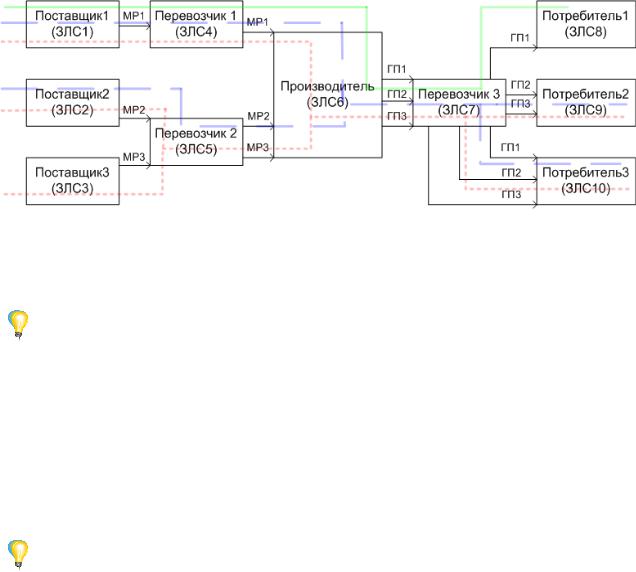
1.Если предположить, что материал МР1 используется для изготовления ГП1, то последовательность:
(ЗЛС1 - ЗЛС4 - ЗЛС6 - ЗЛС7 - ЗЛС8) – представляет собой полную логистическую цепь.
2.Если предположить, что материалы МР1 и МР2 используются для изготовления ГП2, то логистический канал для продукции ГП2 представляет собой множество:
(ЗЛС1; ЗЛС2; ЗЛС4; ЗЛС5; ЗЛС6; ЗЛС7; ЗЛС9; ЗЛС10)
3.Если предположить, что материалы МР1, МР2 и МР3 используются для изготовления ГП3, то логистический канал для продукции ГП3 представляет собой множество:
сами напишите… (ЗЛС1; ЗЛС2; ЗЛС3; ЗЛС4; ЗЛС5; ЗЛС6; ЗЛС7; ЗЛС9; ЗЛС10)
Тема 3. Основные логистические концепции и системы
3.1. Логистическая концепция “точно в срок”
Есть такое понятие как «Размер страховых запасов». Т.е. чтобы производство работало бесперебойно, необходимо, чтобы материалы, детали всегда были в определённом количестве – не ниже определённого уровня. Когда какая-то деталь подходит к этому уровню, - это уже звонок в Отдел закупок, чтобы они её докупили.
А если деталей значительно больше уровня неснижаемых остатков это плохо или хорошо?
Это плохо, т.к. большой запас – связывает значительные финансовые средства. Если весь все остатки в производстве перевести в денежную форму, то получатся миллионы рублей, которые постоянно лежат на складах и цехах.
Комментарий по поводу образования больших запасов ГП на складе. В Питере есть завод, производящий карбюраторы – ООО ТС (бывший Ленинградский карбюраторный завод). Производственная мощность завода составляет 10 тыс. карбюраторов в месяц (условно).
17
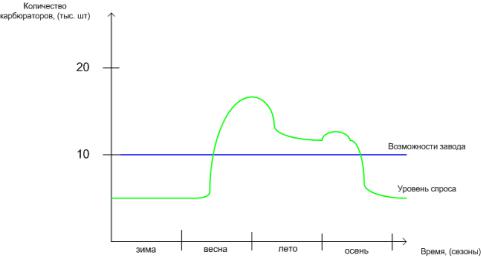
Спрос на карбюраторы сильно колеблется в зависимости от сезонного фактора: зимой и вначале весны - спрос значительно ниже производственных возможностей завода. Но к середине весны, он резко повышается, и держится на высоком уровне всё лето и часть осени. В эти сезоны предприятие уже не в состоянии удовлетворить высокий спрос – не хватает производственных мощностей. Для решения этой проблемы предприятие ввело так называемые Прогнозные заказы, и включает их в план производства вместе с заказами от потребителя. Т.е. завод зимой получает заказы на 5 тыс. карбюраторов в месяц, и добавляет к ним ещё прогнозные заказы на ещё 5 тыс. Произведя продукцию – 10 тыс. в мес., предприятие поставляет 5 тыс. поставщику, а оставшиеся 5 тыс. накапливает на складе ГП. Т.о. зимой накапливается значительный запас, расходуемый в весеннелетний сезон.
Страховой запас — запас материальных ресурсов, предназначенный для бесперебойного снабжения производства и потребления в случаях уменьшения поставок по сравнению с предусмотренными.
Т.о. чтобы производство работало бесперебойно, необходимо, чтобы материальные ресурсы (материалы, детали) всегда были в определённом количестве – не ниже уровня страхового запаса.
Если количество материальных ресурсов значительно выше уровня страхового запаса, то происходит связывание значительных финансовых средств.
В ответ на проблему высокого уровня страховых запасов, связывающего финансовые средства компании, появилась концепция “точно в срок” (“just-in-time”).
Концепция появилась в конце 50-ых годов в Японии, когда компания Toyota Motor, а затем и другие автомобилестроительные компании Японии и США начали внедрять микрологистическую систему KANBAN (“карточка”).
Первоначальным лозунгом концепции было потенциальное исключение запасов материалов, деталей и полуфабрикатов в производственном процессе сборки автомобилей и их основных агрегатов. Исходной постановкой было то, что если производственное расписание заданно, то можно так организовать движение материальных потоков, что все материалы, детали и полуфабрикаты будут поступать в необходимом количестве, в нужное место (на сборочной линии - конвейере) и к точно назначенному сроку для производства и сборки готовой продукции. При такой постановке страховые запасы, связывающие денежные средства компании, значительно уменьшились.
18

Например, запасы деталей в расчете на один выпускаемый автомобиль у фирмы Toyota составляет 77 долларов, в то время как на автомобильных фирмах США этот показатель равен примерно 500 дол, а у наших компаний – ещё в несколько раз выше.
Концепция “точно в срок” – концепция построения логистической системы в производстве, снабжении и распределении (ГП), основанная на синхронизации процессов доставки материальных ресурсов и готовой продукции в необходимых количествах к тому времени, когда ЗЛС в них нуждаются, с целью минимизации затрат, связанных с созданием запасов.
Основные черты компаний, работающих по концепции “точно в срок”:
1.минимальные (нулевые) запасы материальных ресурсов, незавершённого производства и готовой продукции.
2.взаимоотношения по закупкам материальных ресурсов с небольшим числом надёжных поставщиков и перевозчиков.
3.эффективная информационная поддержка. Это современная информационная система управления производством, которая рассчитывает потребность в материалах, производственные программы, и синхронизирует процессы снабжения, производства и распределения ГП. Примерами таких систем могут служить наши ИС “Парус” и “1С: Предприятие”. Хотя две последние служат лишь уменьшению страховых запасов.
4.короткий производственный цикл (период времени между началом и окончанием процесса производства определенного вида продукции на предприятии).
Например, время изготовления 1-го горнопроходческого комбайна на КМЗ = 3 мес. А карбюратора на ООО “ТС” = 3 дня.
5.небольшой объём производства ГП и пополнения запасов.
6.высокое качество ГП и сервиса.
3.2. Тянущие и толкающие системы управления материальными потоками
Управление материальными потоками в рамках микрологистической системы может осуществляться двумя основными способами, принципиально отличающимися друг от друга: тянущим и толкающим. Системы, осуществляющие управление материальными потоками называются соответственно тянущими и толкающими.
Идея тянущей системы появилась достаточно давно – в середине ХХ века – и не имела отношения к производству. Она возникла в американских супермаркетах. Теперь уже всем знакома ситуация – на полках выставляется товар, подходит покупатель, берет одну или две единицы товара. Постепенно полка опустошается. Для рабочего, который должен следить за наполнением полок, этот момент является сигналом о том, что надо подвезти товар. Естественно, если никто с полки товар не берет, то ставить его туда не будут. Японцы, которые активно посещали Америку в рамках программы восстановления японской промышленности (в том числе заводы Форда) и, конечно, посещали супермаркеты, сделали для себя интересные выводы, которые позже стали основой новой идеологии производства.
Тянущая система организует производство, в котором детали и полуфабрикаты подаются от предыдущего производственного звена к последующему по мере необходимости, возникающей у последующего звена. Система управления производством не вмешивается
19
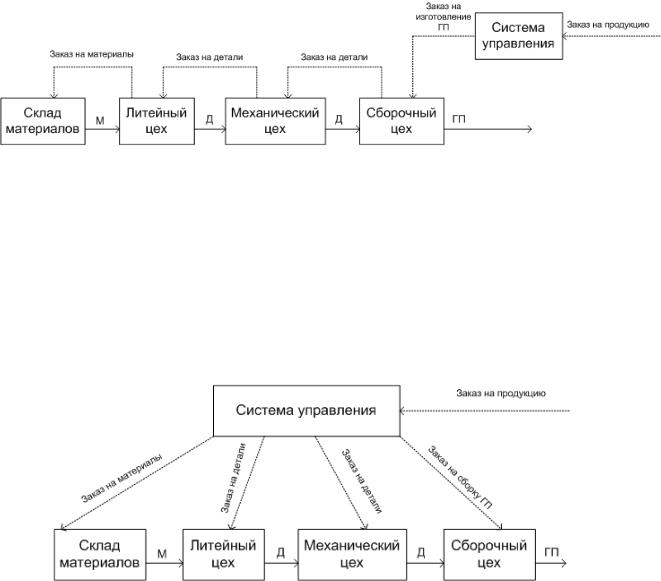
в обмен материальными потоками между подразделениями предприятия, а ставит задачу изготовления лишь перед конечным звеном производственной цепи.
Предприятие получило заказ на изготовление продукции. Система управления передаёт заказ в Сборочный цех. Для выполнения заказа, Сборочный цех запрашивает детали у механического цеха. Передав из своего запаса детали, Механический цех с целью восполнения запаса заказывает их у Литейного цеха. Литейный цех, в свою очередь, заказывает материалы у склада материалов. Таким образом, материальный поток “вытягивается” каждым последующим звеном у предыдущего.
Толкающая система организует производство, в котором предметы труда (материалы, детали, полуфабрикаты), поступающие в производственное звено, непосредственно этим звеном не заказываются у предыдущего звена. Материальный поток “выталкивается” последующему производственному звену по команде из системы управления.
3.3. Микрологистическая система KANBAN
Микрологистическая система KANBAN (в переводе с японского - карточка), впервые примененная корпорацией Toyota Motors в 1959 году, является одной из первых попыток практического внедрения концепции "точно в срок" и относится к “тянущим” системам.
Система KANBAN, представляет собой систему организации непрерывного производственного потока, способного к быстрой перестройке и практически не требующего страховых запасов. Сущность системы заключается в том, что все производственные подразделения завода снабжаются ресурсами в количестве и в сроки, которые необходимы для выполнения заказа, заданного подразделением-потребителем. Т.о. каждое структурное подразделениепроизводитель оптимизирует свою работу в пределах заказа подразделения, осуществляющего операции на последующей стадии производственнотехнологического цикла.
Z.B. Предприятие имеет 3-и производственных подразделения: литейный цех, механический цех и сборочный цех. Материалы и детали обрабатываются каждым
20