
Суберляк О.В. "Технологія переробки"
.pdf
111
Рис. 4.61. Схема кільцевої головки:
1 – трубна заготовка (екструдат); 2 – дорн; 3 – циліндр (мундштук)
Для виготовлення плівок екструзійним методом придатні поліолефіни (ПП, ПЕ), полістирол, пластифікований ПВХ, полівініліденхлорид, поліетилентерефталат, деякі марки поліамідів, кополімери етилену і вінілацетату, естери целюлози. Останнім часом для виготовлення плівок використовують піноматеріали.
Плівки використовують для електроізоляційних, радіотехнічних цілей, для побутових потреб як пакувальні засоби. Крім плівок з однорідних полімерів випускають також армовані, багатоколірні, багатошарові та комбіновані плівки.
4.4.3.1. Технологічний процес формування плівки екструзією з роздувом рукава (рукавний метод)
Технологічний процес формування плівки екструзією з роздуванням рукава складається з наступних стадій: підготовки сировини, стадії формування і завершальних стадій.
Підготовка сировини включає:
–сортування за партіями (для екструзії категорично заборонено змішування партій, бо для кожної партії сировини проводиться налагоджування технологічного режиму);
–контроль вмісту вологи і технологічних параметрів сировини;
–підсушування;
–транспортування – здійснюється транспортними засобами цеху, а подача сировини в
бункер екструдера проводиться індивідуальним пневмотранспортом.
Завершальні операції можуть бути такими: контроль якості плівки, радіаційна обробка, можливе нарізання на стрічки, намотування в рулони, пакування і складування. При контролі якості плівки контролюють товщину (безперервно), прозорість та зовнішній вигляд.
Рукавний метод одержання плівок – простий, високопродуктивний і економічний. Можливі три схеми одержання рукавних плівок екструзією з наступним роздувом: 1) з подачею рукава вгору; 2) з прийманням рукава вниз; 3) з горизонтальним відбором рукава.
Найпоширеніша перша схема. Вона економічна з невеликими технічними ускладненнями, агрегат займає мало площі. Схема екструзійної установки подана на рис. 4.62.
При формуванні плівки методом рукавної екструзії з подачею рукава вгору лінія включає такі стадії:
1.підготовка розтопу: завантаження сировини, топлення, гомогенізація і нагнітання розтопу полімеру;
2.перетискання розтопу через кільцеву головку;
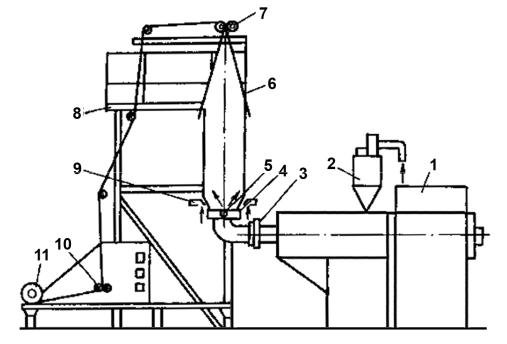
112
3.роздув рукава і його охолодження;
4.складання рукава;
5.намотування плівки на шпулі.
Рис. 4.62. Схема агрегату для одержання плівок рукавним методом з подачею рукава вгору:
1 – екструдер; 2 – бункер; 3 – фільтр; 4 – головка; 5 – трубопровід для подачі повітря; 6 – щоки для складання трубчастого рукава; 7 – тягові валки; 8 – естакада; 9 – охолоджувальне кільце;
10 – спрямовуючі валки; 11 – намотувальний пристрій
Агрегат з відведенням рукава вниз використовують для виробництва плівок невеликих розмірів, бо під дією власної ваги рукав може обірватися на ділянці, де полімер перебуває у високоеластичному стані. До переваг такої схеми можна віднести більш легке налагоджування технологічного процесу й краще охолодження плівки (рис. 4.63).
Недоліком перших двох схем є поворот течії розтопу при вході в кутову головку, що викликає небезпеку перегріву і термодеструкції полімеру.
Горизонтальну схему використовують в агрегатах і автоматизованих лініях для виробництва мішків, де ступінь роздуву невеликий, а товщина плівки перевищує 200 мкм. Цим методом одержують плівки з термонестабільних полімерів (наприклад, з полівінілхлориду) (рис. 4.64).
У процесі формування плівки можлива іонізаційна обробка (для зняття статичної електрики), радіаційна обробка (для підвищення міцності плівки). Проводиться періодичний, або постійний контроль товщини і якості плівки. Товщину міряють вручну мікрометричним методом (коли від рукава відтинається смужка плівки), або неперервно за допомогою фоточи радіаційних датчиків, які можуть бути підключені до регуляторів, що включені в загальну схему регулювання за допомогою ЕОМ, або виведені на щит керування. Другий метод більш прогресивний і потребує поширення в промисловості.
Якщо треба одержати плівку великого діаметру й товщини, використовують спарену екструзію, коли працюють три й більше екструдери, які нагнітають розтоп в одну головку
(рис. 4.65).
Аналогічну схему використовують при формуванні багатошарових плівок, різниця лише в кількості колекторних каналів в екструзійній головці. При формуванні багатошарових плівок на кожен полімер існує окремий колектор.

113
Рис. 4.63. Схема агрегату для одержання плівок екструзією з наступним роздувом рукава (приймання рукава вниз):
1 – екструдер; 2 – подача стисненого повітря; 3 – головка екструдера; 4 – охолоджуюче кільце; 5 – рукав; 6 – щоки для складання рукава; 7 – тягові валки; 8 – натяжний ролик; 9 – намотувальний пристрій
Рис. 4.64. Схема агрегату для одержання плівок рукавним методом
згоризонтальним відбором рукава:
1– екструдер; 2 – одержувана плівка; 3 – подача стисненого повітря; 4 – кільце повітряного охолодження; 5 – рукав після роздуву; 6 – щоки для складання рукава; 7 – тягові валки;
8 – натяжний ролик; 9 – намотувальний пристрій
а) Основні технологічні параметри екструзії плівки з роздуванням рукава
Режим екструзії рукавної плівки – це комплекс технологічних параметрів, які обчислюються для кожної партії матеріалу і при переході на іншу партію обов'язково уточнюються.
Технологічний режим визначають такі параметри:
1.температура по зонах циліндра екструдера, переходу і головки;
2.число обертів шнека;
3.тиск у головці;
4.температура і кількість повітря, яке йде на обдування (охолодження) рукава;

114
5.ступінь роздування рукава;
6.ступінь поздовжньої витяжки.
Рис. 4.65. Схема спареної екструзії (ко–екструзії): 1 – екструдер; 2 – екструзійна головка
Якщо перші три параметри визначають продуктивність екструдера і якість екструдованого розтопу (розділ 2), то наступні параметри – характеристику (властивості) отриманої плівки (її товщину, оптичні і фізико-механічні властивості).
Ступінь роздуву:
np |
|
Др |
, |
(4.79) |
|
||||
|
|
dсeр |
|
де: Др – діаметр рукава після роздування; dcеp – середній діаметр екструзійної щілини. Величина ступеня роздуву перебуває в межах 1,5 ÷4,5 і залежить від тиску і температури повітря, яке подається в рукав (прямо пропорційно), кількості повітря для обдування на охолодження (обернено пропорційно).
Ступінь поздовжньої витяжки залежить від співвідношення швидкості намотування (відведення плівки) і швидкості екструдування розтопу:
nв |
|
н |
, |
(4.80) |
|
|
|||||
|
|
|
е |
|
|
|
|
|
|
Швидкість екструдування можна виразити як об’ємну витрату:
е |
V |
, |
(4.81) |
F |
|||
|
щ |
|
|
де: V – об’єм екструдованого розтопу за одиницю часу; Fщ – площа щілини екструзійної головки. Або:
e |
|
G |
|
, |
(4.82) |
dсeр |
|
||||
|
|
|
|
де: G – маса розтопу, екструдована за одиницю часу; – густина розтопу; – товщина (ширина) кільцевої щілини головки; dсер – середній діаметр кільцевої щілини.
Слід також зауважити, що ступінь витяжки залежить від швидкості тверднення, тобто інтенсивності обдування, температури розтопу й теплофізичних характеристик полімеру. Ступінь витяжки визначає товщину плівки і її фізико-механічні властивості.
На якість плівки суттєво впливає температура розтопу й швидкість його екструдування, а також коефіцієнт (ступінь) роздування. При збільшенні температури розтопу підвищується

115
прозорість плівки, особливо товстої. Це можна пояснити зниженням напружень зсуву в розтопі й підвищенням ступеня аморфізації кристалічного полімеру. Швидкість екструдування на прозорість впливає обернено пропорційно, однак ця залежність значно згладжується при збільшенні ступеня роздуву.
У таблиці 4.15 подані орієнтовні режими екструзії плівок з роздувом рукава для поліолефінів.
|
|
|
|
|
|
|
|
Таблиця 4.15 |
|
|
Режими екструзії з роздувом рукавних плівок із поліолефінів |
||||||||
|
|
|
|
|
|
|
|
|
|
|
|
Температура циліндра за |
Температура го- |
Тиск у |
|
||||
Термопласт |
|
зонами, ºС |
|
ловки за зонами, ºС |
|
||||
|
|
головці , МПа |
|
||||||
|
|
1 |
2 |
3 |
4 |
1 |
2 |
||
|
|
|
|
||||||
ПЕНГ |
|
125 |
135 |
135 |
145 |
140 |
140 |
10 ÷ 15 |
|
ПЕВГ |
|
140 |
160 |
175 |
180 |
180 |
185 |
13 ÷ 19 |
|
ПП |
|
185 |
215 |
235 |
245 |
250 |
250 |
15 ÷ 20 |
|
б) Вплив ступеня роздуву і швидкості охолодження на фізико-механічні властивості плівки
Фізико-механічні властивості змінюються неоднозначно при зміні одного з параметрів, тобто на них справляє вплив сумісна дія всіх параметрів – це й температура розтопу, швидкість екструзії і швидкість охолодження, ступінь витяжки і роздуву.
Співвідношення швидкості охолодження розтопу і ступеня роздуву значною мірою визначає форму рукава в нижній частині (на виході з головки) і в кінцевому підсумку впливає на фізико-механічні властивості плівки вздовж і поперек напрямку екструзії. Можливі форми рукава зображені на рис. 4.66.
Рис. 4.66. Вплив інтенсивності обдування на форму рукава
Форма рукава залежить, у першу чергу, від інтенсивності охолодження. На рисунку 4.66 зображені крайні випадки та оптимальний випадок охолодження. Тут 1 – максимально швидке охолодження. Внаслідок швидкого при такому охолоджені наростання в'язкості відбувається швидка фіксація випрямлення макромолекул у напрямку дії внутрішнього тиску роздуву (в горизонтальному напрямку). Орієнтація в горизонтальному напрямку є значною, бо через велику в’язкість виникають великі орієнтаційні напруження зсуву в радіальному напрямку, які не можуть релаксувати. Через це міцність у поперечному напрямку плівки значно перевищує міцність у поздовжньому напрямку: ||.
116
У випадку повільного (недостатнього) охолодження маємо випадок 2 – мінімальна швидкість охолодження. При витягуванні плівки спостерігається в основному орієнтація полімеру у вертикальному (поздовжньому або тангенціальному) напрямку через повільне наростання в’язкості. У зв’язку із цим міцність плівки в напрямку витяжки значно перевищує міцність плівки в радіальному (горизонтальному) напрямі: ||. Це варіант 2.
Варіант 3 – оптимальний варіант охолодження забезпечує рівномірну витяжку й однакову орієнтацію вздовж і перпендикулярно до напрямку витяжки, тому міцність в обох напрямках близька за значеннями: ||.
в) Технологічні особливості екструзії рукавної плівки і проблеми, які виникають при її реалізації
Тепловий режим екструзії впливає на властивості плівок. При низьких температурах розтопу відбувається значне витягування плівки, що супроводжується орієнтацією макромолекул і підвищенням її міцності, а також появою поверхневих дефектів. При високій температурі розтопу швидше проходить релаксація напружень, які виникають у полімері при роздуванні і при витяжці. Підвищена температура екструзії забезпечує плівці кращу прозорість і блиск.
Як видно, температура переробки при цьому методі є нижчою, ніж при литті під тиском, що обумовлене необхідністю запобігання обриву рукава.
Товщина і фізико-механічні властивості плівки, як уже зазначалося, залежать від: а) поздовжньої витяжки, яка задається швидкістю екструдування;
б) від ступеня роздуву, що залежить від надлишкового тиску повітря всередині рукава і визначається здатністю розтопу до деформування. При надто великому ступені витяжки чи роздування плівка, як це було зазначено вище, набуває явно вираженої анізотропії міцності.
Шлях, на якому здійснюється витяжка, залежить від швидкості тверднення (кристалізації) розтопу (переходу із в’язкотекучого стану у високоеластичний чи склоподібний).
У свою чергу довжина зони витяжки залежить від природи полімеру (його теплофізичних характеристик) і швидкості (інтенсивності) охолодження.
При оформленні технологічної схеми важливо також знати загальну довжину рукава до складання, яка повинна узгоджуватися з температурою злипання полімеру (температурою липкості). Так, для ПЕ ця температура повинна бути нижчою, ніж 40°С.
Для отримання прозорої плівки з добрими фізико-механічними властивостями довжина зони в'язкотекучого стану повинна бути невеликою, бо зі зменшенням швидкості охолодження зростає імовірність кристалізації та зростання концентрації напружень зсуву, які викликають помутніння плівки і анізотропію її властивостей.
Для інтенсифікації охолодження і вирівнювання умов тверднення плівки із зовнішньої і внутрішньої сторін рекомендується двостороннє охолодження (рис 4.67, а).
Однак, при охолодженні повітрям внаслідок порівняно невеликих значень коефіцієнта тепловіддачі виникає відчутний температурний градієнт між поверхнею плівки та повітрям, тому теплообмін є малоефективним. Щоб прискорити охолодження з рівномірним тепловим потоком, використовують рідинне (водяне) охолодження (рис. 4.67, б). Внаслідок значно вищої, порівняно з повітрям, теплопровідності води, ефективність рідинного охолодження може бути підвищена в 1000 разів відносно повітряного. Рідинне охолодження, як правило, використовують при витяжці плівки вниз. Недоліком такого методу є проблема відокремлення води від плівки (її висушування).

117
Рис. 4.67. Різновидності охолодження плівки:
а) повітряне – з подачею охолодженого стисненого повітря; б) водяне
Досить ефективним є аерозольне охолодження – у цьому випадку використовують зволожене повітря.
Крім викладених вище загальних технологічних проблем при здійсненні технології одержання рукавної плівки потрібно комплексно розв’язувати завдання, які виникають при:
1.роботі екструдера – необхідність рівномірної подачі розтопу з якомога більш однорідними (однаковими), точно встановленими характеристиками;
2.забезпеченні рівномірного (без пульсацій) виходу однорідного, однаково нагрітого розтопу з головки (утворення якісної трубної заготовки);
3.охолодженні рукава – забезпечення рівномірності охолодження;
4.складанні рукава;
5.узгодженості швидкості намотування й екструзії плівки.
Розглянемо стисло реалізацію кожного завдання.
1. Для одержання якісного розтопу з рівномірною його подачею на профільний (формувальний) елемент, як ми вже знаємо, необхідне чітке узгодження роботи трьох зон екструдера, яке встановлюється за допомогою математичного моделювання процесу. Для узгодження роботи всіх зон застосовують:
–добір матеріалу з потрібними (і обов’язково однаковими) реологічними властивостями;
–використання шнека відповідної конструкції для кожного матеріалу, а то й кожної партії;
–встановлення технологічних параметрів екструдування залежно від теплофізичних і реологічних характеристик матеріалу;
–дроселювання та фільтрація розтопу на виході з екструдера.
Слід зауважити, що якість труби істотно залежить від гомогенності розтопу, який надходить на головку. Для зміни ступеня гомогенності розтопу на виході з екструдера ставлять дросельний пристрій. При зменшенні перетину каналу в дроселі підвищується тиск у циліндрі (зростає опір), і, відповідно, зростає ступінь гомогенізації (див. розділ 4.4.2.3).
Якість заготовки також значно залежить від характеристики фільтруючого пакета (до речі, це може бути додатковий дросель). Має вплив розмір комірок фільтруючих сіток і кількість останніх. Число сіток визначається залежно від перепаду тиску, який не повинен перевищувати 3 ÷ 5 МПа. Розмір комірок бажано брати якомога менший. Найчастіше в практиці використовують сітки з розміром комірок 75 ÷ 560 мкм. Кількість комірок тоді становить 6400 ÷ 144 шт/см2.

118
2. Для отримання якісного рукава встановлюється оптимальний режим, який повинен забезпечити: рівномірну подачу строго каліброваної заготовки (труби). Адже цілком зрозуміло, що в звичайній, кутовій головці перепад тиску (відповідно напруження зсуву й реологічні характеристики, включаючи саморозігрів) буде різний по кільцю внаслідок відповідних втрат при обтіканні дорна в каналі. Напрями розв’язання цієї проблеми полягають заходах, що передбачають конструювання головок з вирівнюванням потоку, а саме:
а) змінний перетин каналу між мундштуком (циліндром) і дорном;
б) s-подібний шлях на вході в головці для вирівнювання потоку розтопу; в) виконання на дорні радіальних розподільчих каналів (рис. 4.68);
г) виконання гвинтових нарізок на дорні і мундштуці, причому гвинтові канали виконані змінного перетину, зрозуміло, з більшим розміром на віддаленому краї кільця від входу розтопу;
д) головки, у яких дорн або/та мундштук, обертаються назустріч.
е) використання прямоточних головок – на вертикальних екструдерах, встановлених у напрямку відтягування рукава, чи при горизонтальній схемі екструзії;
ж) використовують дію вібрації (ультразвуку) на головку. Це сприяє зменшенню дисипативних втрат при течії в каналах головки.
У випадку кутової екструзії внаслідок кутового переходу виникають великі напруження зсуву, і через додатковий опір течії спостерігається більша дисипація енергії, що зумовлює зменшення в’язкості розтопу, зростання швидкості течії, але одночасно можливі деструктивні процеси. Ці явища суттєво зменшуються при обертанні поверхонь, по яких тече розтоп.
Рис. 4.68. Схема головки з гвинтовими каналами на дорні:
а – загальний вид головки; б – повздовжний розріз каналів головки в радіальному напрямку; 1 – центральний канал; 2 – радіальні канали; 3 – дорн; 4 – кільцевий канал; 4а – початкова дільниця
кільцевого каналу; 5 – корпус головки; 6 – колектор
Довжина формувальної щілини головки впливає, передусім, на мутність плівки. Зі зменшенням довжини каналу напруження зсуву, які виникають на вході в канал при кутовому переході, не встигають релаксувати, що зумовлює так зване періодичне зривання
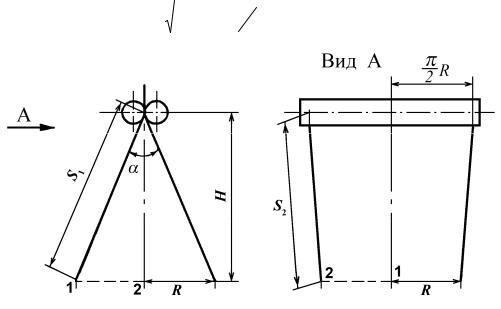
119
розтопу на поверхні при виході заготовки (явище еластичної турбулентності) і утворення шорсткої поверхні.
Після виходу заготовки з головки розтоп одночасно піддають роздуванню, витяжці й охолодженню. Швидкість витяжки, рівнотовщинність плівки, її прозорість і фізико-механічні властивості значною мірою залежать від швидкості й рівномірності охолодження. Чим більша швидкість охолодження, тим більша прозорість плівки, бо менша ступінь кристалічності та орієнтаційних напружень.
Суттєвий вплив на якість плівки та її різнотовщинність має рівномірність охолодження рукава – товщина тим більша, чим вища інтенсивність охолодження.
3. Проблеми рівномірності охолодження. Найпоширеніший метод охолодження – обдув повітрям, яке виходить з кільця через отвори. Недолік такого обдування – нерівномірність повітряних потоків з кожного отвору. Для поліпшення обдування використовують:
а) кільця з декількома вихідними щілинами замість отворів; б) охолоджуючі муфти з металу, які мають внутрішню поверхню, виконану за профілем, що
відповідає профілю рукава. Усередині муфта охолоджується водою, і при контакті з рукавом, внаслідок високої теплопровідності, інтенсифікується процес охолодження разом з поліпшенням рівномірності його через контакт по всій поверхні;
в) використання для обдування повітряно-водяної суміші; г) застосування системи водяного охолодження. Особливості цих технічних рішень описані
раніше.
4. Проблема складання рукава.
Як видно з рис. 4.69, точки 1 і 2 проходять не однаковий шлях, який можна розрахувати з наступних залежностей:
|
Lз 1,15 LB , |
|
|
(4.83) |
|
|
|
|
|
|
|
S2 |
|
H2 R |
1 2 |
, |
(4.84) |
|
2 |
|
|
|
Рис. 4.69. Схема складання рукава
Таке явище викликає утворення складок, які запресовуються і фіксуються на шпулі. Поява складок суттєво залежить від кута розкладу щік. Зі збільшенням кута співвідношення S2/S1 зростає, також зростає імовірність утворення складок. Отже, для запобігання цьому або зменшують , або щоки роблять випуклими до середини, щоб збільшити S1.
5. Утворення складок ще більш імовірне при намотуванні плівки за рахунок:
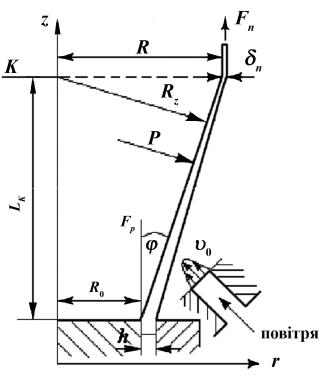
120
а) зміни лінійної швидкості на рулоні через постійне зростання його діаметру, коли окружна швидкість (швидкість обертання рулону) залишається постійною; тому потрібне узгодження е і н, або імовірність утворення складок зменшується при наявності натягувального пристрою перед намотуванням;
б) внаслідок термозбігу плівки – зусилля, які виникають при цьому, зморщують плівку; в) вигинання від статичної електрики – внаслідок тертя полімеру об щоки, валки і руху в
повітрі спостерігається електризація плівки, яка викликає електростатичне відштовхування на рулоні. У такому випадку статичний заряд можна зменшити, зволожуючи повітря, використовуючи нейтралізатори, які іонізують повітря в області естакади, а також, додаючи до сировини антистатики. Часто використовують іонізуюче опромінення УФ-променями, або коронним розрядом;
г) наявність повітряних конвективних потоків, що зумовлює нерівномірність охолодження рукава і нерівномірність усадки.
При здійсненні технології треба підтримувати умови, які б виключали гойдання рукава (вітер, протяг, теплові конвективні потоки), особливо до лінії кристалізації, бо це призводить до утворення хвилястої поверхні плівки через нерівномірність охолодження і кристалізації. Інколи (крім герметизації ділянки вікон і дверей) добрий ефект дає „капсулювання” рукава (його ховають під прозорий ковпак).
г) Обчислення температурних параметрів рукавної екструзії
Висоту рукава до складання визначають експериментально (за значенням температури липкості), або аналітично. Як ми вже зазначали раніше, формування рукава здійснюється до лінії тверднення (кристалізації) – LК, упродовж якої спостерігається роздування (np), витяжка nB н е плівки і утворення необхідної надмолекулярної структури в полімері.
Рис. 4.70. Геометрія рукавної заготовки
Виходячи з того, що висота лінії кристалізації залежить від теплофізичних характеристик розтопу й режиму охолодження, обчислення зводиться до визначення кількості тепла, яке потрібно забрати від розтопу для повного тверднення. Охолодження