
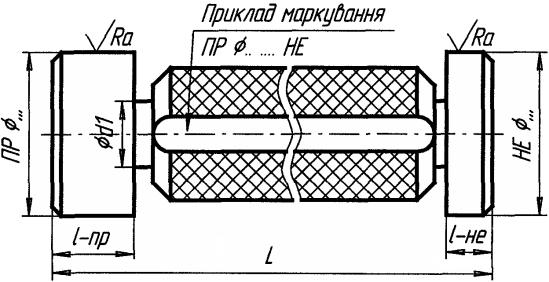
|
|
|
|
Таблиця 4.2 |
|
|
|
|
|
|
|
Квалітет контрольованих поверхонь |
Параметр шорсткості, мкм, |
||||
Ra* номінальних розмірів, мм |
|||||
|
|
|
|||
|
|
|
|
|
|
Калібр-пробка |
Калібр- |
Контрольний |
0,1 … 100 |
Понад 100 до 360 |
|
скоба |
калібр |
||||
|
|
|
|||
|
|
|
|
|
|
6 |
- |
6-9 |
0,04 (0,025) |
0,08 (0,06) |
|
7-9 |
6-9 |
10 і більш грубий |
0,08 (0,06) |
0,16 (0,10) |
|
10-12 |
|
7 |
0,16 (0,10) |
0,16 (0,10) |
|
13 і більш грубий |
|
|
0,32 (0,20) |
0,32 (0,20) |
|
|
|
|
|
|
|
|
|
*У дужках вказані переважні значення. |
ПРОБКИ ДВОСТОРОННІ ПОВНОГО ПРОФІЛЮ
Таблиця 4.3
Номінальні |
Довжина пробок L, мм |
Ручки |
|
||||
діаметри, мм |
двосторонніх |
прохідних |
непрохідних |
Номер |
|
d1 |
|
> 1 |
≤ 3 |
63 |
55 |
53 |
1 |
|
6 |
> 3 |
≤ 6 |
66 |
57 |
54 |
1 |
|
6 |
> 6 |
≤ 10 |
75 |
65 |
62 |
2 |
|
8 |
> 10 |
≤ 14 |
86 |
75 |
71 |
3 |
|
10 |
> 14 |
≤ 18 |
102 |
89 |
84 |
4 |
|
13 |
> 18 |
≤ 24 |
116 |
101 |
95 |
5 |
|
16 |
> 24 |
≤ 50 |
131 |
114 |
107 |
6 |
|
20 |
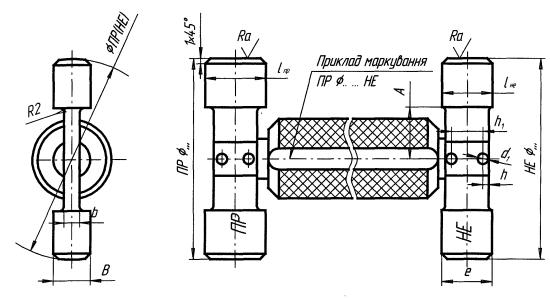
ПРОБКИ ДВОСТОРОННІ НЕПОВНОГО ПРОФІЛЮ
Таблиця 4.4
Номінальні |
|
l |
B |
b |
l1 |
A |
h |
h1 |
d |
m1 |
d1 |
||
діаметри, мм |
Пр |
|
Не |
||||||||||
Понад 50 ≤ 60 |
28 |
|
23 |
14 |
6 |
18 |
18 |
5 |
13 |
- |
- |
4,2 |
|
Понад 60 |
≤ 70 |
28 |
|
23 |
14 |
6 |
18 |
23 |
5 |
13 |
- |
- |
4,2 |
Понад 70 |
≤ 80 |
28 |
|
23 |
14 |
6 |
18 |
28 |
5 |
13 |
- |
- |
4,2 |
Понад 80 |
≤ 90 |
32 |
|
28 |
14 |
8 |
22 |
32 |
6 |
16 |
12 |
9 |
4,2 |
Понад 90 |
≤ 100 |
32 |
|
28 |
14 |
8 |
22 |
37 |
6 |
16 |
12 |
12 |
4,2 |
Понад 100 ≤ 110 |
38 |
|
28 |
14 |
8 |
22 |
40 |
6 |
16 |
12 |
14 |
4,2 |
|
Понад 110 ≤ 120 |
38 |
|
28 |
14 |
8 |
22 |
45 |
6 |
16 |
12 |
15 |
4,2 |
|
Понад 120 ≤ 135 |
42 |
|
32 |
18 |
10 |
26 |
50 |
7 |
19 |
15 |
18 |
5,2 |
|
Понад 135 ≤ 150 |
42 |
|
32 |
18 |
10 |
26 |
56 |
7 |
19 |
15 |
21 |
6,5 |
|
|
|
|
|
|
|
|
|
|
|
|
|
|
|
СКОБИ ЛИСТОВІ ОДНОСТОРОННІ
Таблиця 4.5
Номінальні |
|
|
|
Розміри скоби, мм |
|
|
|
|
||||
діаметри, мм |
d |
H |
C |
e |
r |
k |
n |
f |
d1 |
m |
|
|
Понад 6 ≤ 10 |
40 |
32 |
4 |
5 |
8,5 |
14 |
22 |
9 |
8 |
2 |
|
|
Понад 10 ≤ 20 |
50 |
40 |
5 |
8 |
12,5 |
19 |
28 |
13 |
10 |
2 |
|
|
Понад 20 ≤ 30 |
65 |
54 |
6 |
9 |
17,5 |
22 |
35 |
21 |
12 |
3 |
|
|
Понад 30 ≤ 40 |
82 |
70 |
7 |
11 |
22 |
25 |
43 |
31 |
12 |
4 |
|
|
Понад 40 |
≤ 50 |
94 |
80 |
8 |
12 |
27 |
27 |
50 |
41 |
12 |
4 |
|
Понад 50 |
≤ 65 |
116 |
100 |
8 |
13 |
35,5 |
33 |
62 |
51 |
18 |
6 |
|
Понад 65 |
≤ 80 |
136 |
117 |
9 |
15 |
42,5 |
36 |
73 |
60 |
18 |
6 |
|
Понад 80 |
≤ 100 |
164 |
139 |
9 |
17 |
52,5 |
39 |
86 |
86 |
18 |
7 |
|
Понад 100 ≤ 120 |
186 |
156 |
10 |
18 |
62 |
42 |
104 |
104 |
20 |
8 |
|
|
Понад 120 ≤ 140 |
208 |
170 |
10 |
19 |
72 |
45 |
124 |
124 |
20 |
10 |
|
|
Понад 140 ≤ 160 |
230 |
185 |
10 |
20 |
82 |
48 |
144 |
144 |
20 |
10 |
|
|
Понад 160 ≤ 180 |
250 |
199 |
10 |
23 |
92 |
51 |
164 |
164 |
20 |
10 |
|
|
|
|
|
|
|
|
|
|
|
|
|
|
|
5. РОЗРАХУНОК РОЗМІРНИХ ЛАНЦЮГІВ
За індивідуальним кресленням потрібно скласти розмірний ланцюг, для якого визначити допуски всіх складових ланок. З цією метою на складальному кресленні вузла або виробу в цілому виявляємо ланки, які утворюють замкнений контур розмірів, на основі якого складаємо схему ланцюга. На основі розмірної схеми визначаємо величину замикальної ланки і допуски на
їївиготовлення, одним з нижче наведених методів.
5.1.Метод максимуму – мініміму
Узагальному випадку при n збільшувальних і р зменшувальних ланках номінальний розмір замикальної ланки лінійного розмірного ланцюга визначають за формулою:
n |
n+p |
(5.1) |
A∆ = ∑Aj − |
∑Aj ; . |
|
j=1 |
j=n+p |
|
Складові розміри можуть змінюватись в межах допуску. У разі сполучення найбільших збільшувальних і найменших зменшувальних розмірів замикальний розмір має найбільше значення, у разі сполучення найменших збільшувальних і найбільших зменшувальних розмірів – найменше значення, яке визначається за формулами:
n |
|
|
n+ p |
(5.2) |
A∆max = ∑Amaxj |
− |
∑Aminj ; |
||
j=1 |
|
j=n+ p |
|
|
A∆min = ∑n |
|
|
n+ p |
|
Aminj |
− |
∑Amaxj ;. |
(5.3) |
|
j=1 |
|
|
j=n+1 |
|
Оскільки різниця між найбільшим та найменшим розміром є допуск, віднімемо почленно рівняння (5.3) від рівняння (5.2):
n |
n+ p |
|
TA∆ = ∑TAj + |
∑TAj . |
(5.4) |
j=1 |
j=n+1 |
|
Якщо прийняти загальну кількість ланок в ланцюгу як m, а загальну кількість складових m – 1 = n + p, то можна записати:
m−1 |
|
TA∆ = ∑TAj , |
(5.5) |
j=1

тобто допуск замикальної ланки дорівнює сумі допусків складових розмірів.
5.2. Метод одного квалітету (більш точний)
Метод використовують, коли всі складові розміри можуть бути виконані з допуском одного квалітету. Необхідний квалітет визначають таким чином. Відомо, що допуск розміру Таj = aj i, де і – одиниця допуску. Для розмірів від
1 до 500 мм
|
i = 0,453 |
D |
+ 0,001D , |
(5.6) |
|||||||||
де D – середній геометричний розмір вибраного інтервалу розмірів. |
|
||||||||||||
Тоді з формул (5.5) і (5.6) можна записати: |
|
|
|||||||||||
|
n+p |
|
|
|
|
|
|
|
|
|
n+p |
(5.7) |
|
|
TA∆ = ∑a j( 0,453 |
|
|
|
+0,001D j ) = |
∑a jij ; |
|||||||
|
D j |
||||||||||||
|
j |
|
|
|
|
|
|
|
|
|
j |
|
|
де аj - число одиниць квалітету, яке визначає допуск j – розміру. |
|
||||||||||||
За умовою задачі а1 = а2 =. . . =аm-1=aср, тоді |
|
||||||||||||
|
n+ p |
|
|
|
|
|
|
|
|
|
|
n+ p |
(5.8) |
|
TA∆ = acp ∑( 0,453 |
D |
j +0,001D j ) = acp ∑ij , |
||||||||||
|
j=1 |
|
|
|
|
|
|
|
|
|
|
j=1 |
|
звідки |
a |
cp |
= |
TA∆ |
, |
|
(5.9) |
||||||
|
|
||||||||||||
|
|
|
n+ p |
|
|
∑i j j=1
де ТА∆ – мм в мкм, D – в мм.
Для розмірів до 500 мм можна вибирати приблизні значення одиниці допуску і з табл. 5.1 для кожного інтервалу розмірів.
Таблиця 5.1
інтервал |
іmid |
|
розмірів,мм |
||
≤3 |
0,55 |
|
>3 |
≤6 |
0,73 |
>6 ≤10 |
0,90 |
|
>10 |
≤18 |
1,08 |
>18 |
≤30 |
1,31 |
>30 |
≤50 |
1,56 |
>50 |
≤80 |
1,86 |
інтервал |
іmid |
розмірів,мм |
|
>80 ≤120 |
2,19 |
>120 ≤180 |
2,53 |
>180 ≤250 |
2,91 |
>250 ≤315 |
3,23 |
>315 ≤400 |
3,54 |
>400 ≤500 |
3,89 |
|
|
|
|
|
Таблиця 5.2 |
||
|
|
|
|
|
|
Квалітет |
a |
Квалітет |
a |
||
5 |
7 |
|
11 |
100 |
|
6 |
10 |
|
12 |
160 |
|
7 |
16 |
|
13 |
250 |
|
8 |
25 |
|
14 |
400 |
|
9 |
40 |
|
15 |
640 |
|
10 |
64 |
|
16 |
1000 |
|
|
|
|
17 |
1600 |
|
За значенням аср з табл. 5.2 вибираємо найближчий квалітет. Визначивши допуски номінальних складових розмірів, їх значення коригуємо, враховуючи конструктивні і експлуатаційні вимоги, можливості процесу виготовлення. Допуски охоплюючих розмірів рекомендується визначати як для основного отвору, а для охоплених розмірів – як до основного валу. При цьому слід дотримуватись умови
n+ p |
|
TA∆ ≥ ∑TAj . |
(5.10) |
j=1
Винайшовши допуски ТА1, ТА2,, . . ., Таm-1 за заданим відхиленням ES (A∆) і EI (A∆) визначаємо значення і знаки верхніх і нижніх відхилень складових розмірів такими, щоб вони задовольняли рівняння (5.7) і (5.10).
6.РЕКОМЕНДАЦІЇ ДО ПРОСТАВЛЕННЯ ДОПУСКІВ ФОРМИ
ІРОЗТАШУВАННЯ НА КРЕСЛЕННЯХ ДЕТАЛЕЙ
6.1.Вали
На рис. 6.1 наведено приклад розташування необхідних умовних позначень технічних вимог до деталей типу валів, валів-шестерен і черв’яків. Для цих деталей робочою віссю вала є загальна вісь посадочних поверхонь для підшипників кочення, тому вимірювальною базою для контролю поверхонь деталі є вісь обертання.
Похибки форми посадочних поверхонь підшипників кочення спотворюють геометрію доріжок, якими рухаються тіла кочення, тому допуск
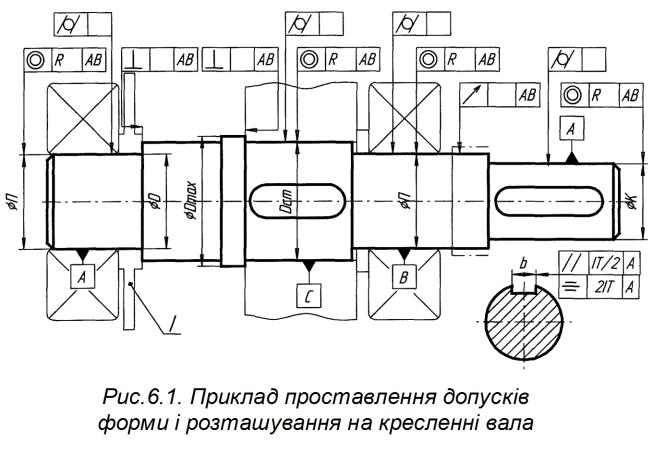
циліндричності зазначених поверхонь обмежуємо і приймаємо приблизно 0,3Td (де Тd – допуск розміру посадочної поверхні вала). Аналогічне призначення має обмеження допуску перпендикулярності, який задають на діаметрі d0 залежно від типу підшипника: IT7 – для кулькового радіального і радіально-упорного; IТ6 – для радіального з короткими циліндричними роликами; IТ5 – для конічного роликового.
На кресленні кільця 1 задають допуск паралельності базових торців на один квалитет точніше.
Допуск співвісності задають на діаметри посадочних поверхонь підшипників відносно їх загальної вісі за наступним даними: IT5 – для кулькового радіального і радіально-упорного; IT4 – для радіального з короткими циліндричними роликами; IT3 – для конічного роликового.
Для посадочних поверхонь зубчастих і черв'ячних коліс допуск циліндричності приймають таким, що приблизно дорівнює 0,3Тd, з метою обмеження концентрації контактного тиску по поверхні посадки, щоб отримати оптимальну пляму контакту зубів спряжених коліс, яку в свою
чергу визначає норма точності напрямку зуба. Допуск співвісності встановлюється для забезпечення кінематичної точності передачі. При L/d ≥ 0,8 визначаємо відхилення посадочної поверхні вала під колесо для зубчастих і черв'ячних коліс і задаємо допуск на діаметрі посадочної поверхні. При відношенні L/d < 0,8 задаємо відхилення від перпендикулярності торця заплечика вала до загальної вісі. У разі довгої маточини вимоги точності до торця заплечика вала не ставляться.
Допуск циліндричності для посадочних поверхонь муфт, шківів і зірочок приймають такими, що приблизно дорівнюють 0,4 Тd.
Для обмеження можливого дисбалансу як самого вала, так і в зборі з деталлю, встановленою на його кінці, задається допуск співвісності посадочних поверхонь муфт, шківів, зірочок, який задають за такими даними:
Частота обертання вала, хв-1 |
600 |
1000 |
1500 |
3000 |
Допуск співвісності, мм |
0,030 |
0,018 |
0,012 |
0,008 |
Для недопущення значної амплітуди коливань робочої кромки манжети, що призводить до руйнування гуми внаслідок втомлюваності, встановлюємо допуск радіального биття поверхні вала під манжетні ущільнення за такими даними:
Частота обертання вала, хв-1 до |
1000 |
понад 1000 |
до 1500 |
|
|
|
|
|
понад 1500 до 3000 |
Допуск биття, мм |
0,040 |
|
0,03 |
0,02 |
Для забезпечення рівномірного контакту робочих поверхонь шпонки і паза вала допуск паралельності шпонкових пазів приймають, таким, що дорівнює 0,5 Tшп, допуск симетричності таким, що дорівнює 2,0 Tшп (де Tшп – допуск розміру ширини шпонкового паза).
6.2. Зубчасті і черв’ячні колеса
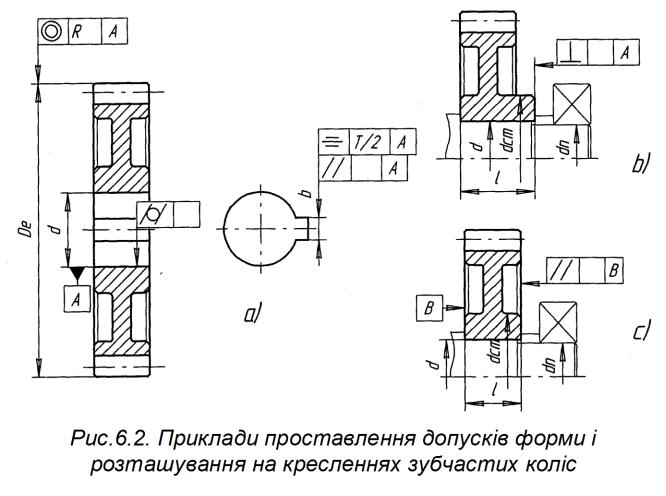
На кресленнях зубчастих і черв'ячних коліс зовнішній циліндр і торці зубчастого вінця часто використовують як технологічні бази: торці вінця – як установчу базу для виготовлення зубів, а поверхня зовнішнього циліндра – під час вивіряння заготовки на верстаті і контролю деяких параметрів зубів. Допуск розміру зовнішнього діаметра колеса приймають залежно від модуля: при m до 2,5 мм – h 12, понад 2,5 до 6,3 – h 13, понад 6,3 – h 14.
Допуск циліндричності базового отвору приймають таким, що приблизно дорівнює 0,3 TD, де TD – допуск діаметра отвору.
Кінематична точність передачі забезпечується обмеженням допуску співвісності зубчастого вінця відносно посадочного отвору (для валівшестерень до загальної осі посадочних поверхонь для підшипників кочення). Допуск співвісності зовнішнього циліндра задають на діаметрі посадочного отвору.
Биття внаслідок похибки форми позначається практично тільки на висоті зуба і є відносно малою величиною. Радіальне биття, зумовлене
похибкою розташування, визначає зміщення центра мас відносно осі обертання внаслідок чого виникає неврівноваженість. В зв'язку з цим можна обмежитися допуском співвісності зовнішнього циліндра відносно посадочного отвору, а для валів-шестерень – відносно загальної вісі поверхні. Для посадочних поверхонь підшипників кочення слід проставляти допуск на радіальне биття зовнішнього діаметра, що дорівнює приблизно
0,1Td.
Допуск співвісності задають для насадних коліс на діаметрі посадочного отвору, для валів-шестерень – на ділильному діаметрі.
Допуск перпендикулярності (рис. 6.2, б) до осі посадочного отвору торця маточини для коліс з відношенням (L/d ≥ 0,8) приймають на діаметрі отвору підшипника dп за такими даними: IT7 для кулькового радіального і радіально-упорного; IT6 – для радіального з короткими циліндричними роликами; IT5 – для конічного роликового.
На кресленні колеса допуск перпендикулярності задаємо на діаметрі маточини dст , перемножуючи вказаний допуск на відношення dст/dn.
На кресленні кільця розпірної втулки між колесом і підшипником задаємо допуск паралельності торців.
Для забезпечення норм контакту зубів передачі потрібно на діаметрі dст задавати допуск перпендикулярності базового торця зубчатого вінця до осі посадочного отвору. Для вузьких коліс (рис. 6.2, в) з відношенням L/d < 0,8 допуск паралельності торців маточини приймають на діаметрі dп отвору підшипника за наступним даними: IT6 – для кулькового радіального і радіально-упорного; IT5 – для радіального з короткими циліндричними роликами; IT4 – для конічного роликового.
6.3. Кришки підшипників
Допуски на розміри кришки задаємо такі: на висоту – h9; для закладної кришки на ширину – h11; на зв'язаний розмір D для глухих кришок, що привертаються –- d11, для кришок з отвором, що привертаються під манжету – h8, для всіх закладних кришок – h8; на діаметр отвору Dм під манжету – H8.

Допуск паралельності торців кришок на діаметрі D приймаємо за такими даними: IT6 – для кулькового радіального і радіально-упорного; IT5 – для радіального з короткими циліндричними роликами; IT4 – для конічного роликового підшипників. На кресленні кришки підшипника допуск паралельності базових торців задають на діаметрі Dф, тому вказаний допуск перемножують на відношення Dф/D (рис. 6.3).
Якщо торець кришки не виступає опорною базою підшипника, то вимогу точності до нього не ставлять.
Допуск паралельності для базування манжети за торцем центруючої поверхні кришки на діаметрі D задаємо за дев’ятим квалітетом.
Допуск співвісності посадочної поверхні для манжети на діаметрі Dм задаємо за шостим квалітетом.
Рис.6.3. Основні розміри кришки підшипника На діаметри отворів під кріпильні болти призначають залежний допуск
розташування. Діаметр розташування кріпильних отворів на кресленні беруть в рамку. Величину допуску приймають Тn = 0,2(d0 – d), де d0 діаметр отвору під гвинт; d — діаметр гвинта.
6.4. Стакани
На рис. 6.4 наведено вимоги до форми і точності розташування поверхонь стаканів для найпоширеніших схем. Стакани невеликої довжини базують за торцем фланця, тому характер технічних вимог визначається основною базою поверхні С фланця, внаслідок чого розташування базових торців стакану для упору підшипників забезпечується встановленням вимог паралельності цих торців базовому торцю С фланця.
Допуск циліндричності посадочного отвору стакану приймають таким, що приблизно дорівнює рівним 0,3 ТD, де ТD – допуск розміру посадочного отвору.
Допуск співвісності посадочних отворів для підшипників відносно їх загальної осі на діаметрі D задають таким, що приблизно дорівнює IТ4.
Допуск паралельності торців для упору кілець підшипників на діаметрі D щодо базового торця фланця задають за такими даними: IТ8 – для кулькового радіально-упорного; IТ6 – для конічного роликового підшипників.
Допуск перпендикулярності осі посадочного отвору базовому торцю фланця задають на діаметрі D за рекомендаціями, вказаними в підрозділі 6.1.
Допуск круглості центруючої поверхні задають таким, що приблизно дорівнює 0,4 Тd, де Тd – допуск розміру центруючого пояска діаметром d.
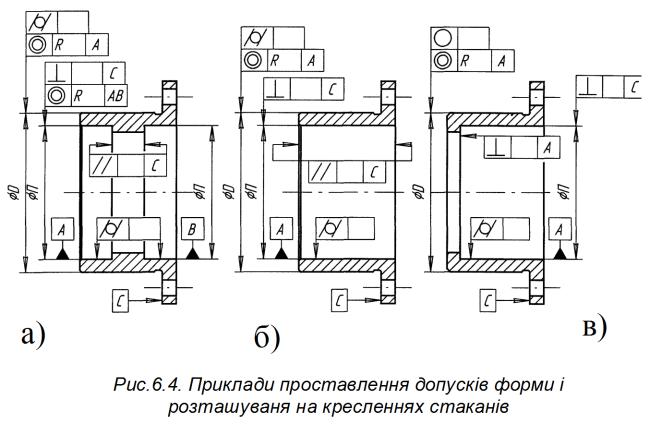
Допуск циліндричності зовнішнього циліндра задаємо таким, що приблизно дорівнює 0,4 Тd, де Тd – допуск розміру зовнішнього циліндра.
Наведені значення допусків співвісності, задані в радіусному виразі (літера R в рамці умовного позначення), можна задавати також у діаметральному виразі. Для цього у рамці умовного позначення замість R зображають знак ǿ, а значення допуску подвоюють.
6.5. Втулки, кільця
На кресленні втулок проставляємо габаритний осьовий розмір Г, допуск на який визначаємо за результатами обчислень відповідної розрахункової схеми.
Вимоги точності розташування поверхонь залежать від того, яка поверхня втулки є базовою. Якщо основна база втулки – торці, то обмежуємо відхилення від паралельності торців (рис. 6.5, а). Якщо основна база втулки –циліндрична поверхня, то задають відхилення від перпендикулярності торців осі посадочної поверхні (рис. 6.5, б).

ЛІТЕРАТУРА
1.ДСТУ 2500 – 94. Єдина система допусків і посадок. Терміни і визначення . Позначення і загальні норми. – Введ.
Навчальне видання
ВЗАЄМОЗАМІННІСТЬ, СТАНДАРТИЗАЦІЯ ТА ТЕХНІЧНІ ВИМІРЮВАННЯ
МЕТОДИЧНІ ВКАЗІВКИ до виконання курсової роботи
для студентів напряму 0902 “Інженерна механіка”
денної, заочної та скороченої форм навчання
У к л а д а ч : Кадомський Сергій Віталійович
РВЦ НУХТ. 01033 Київ-33, вул. Володимирська, 68