
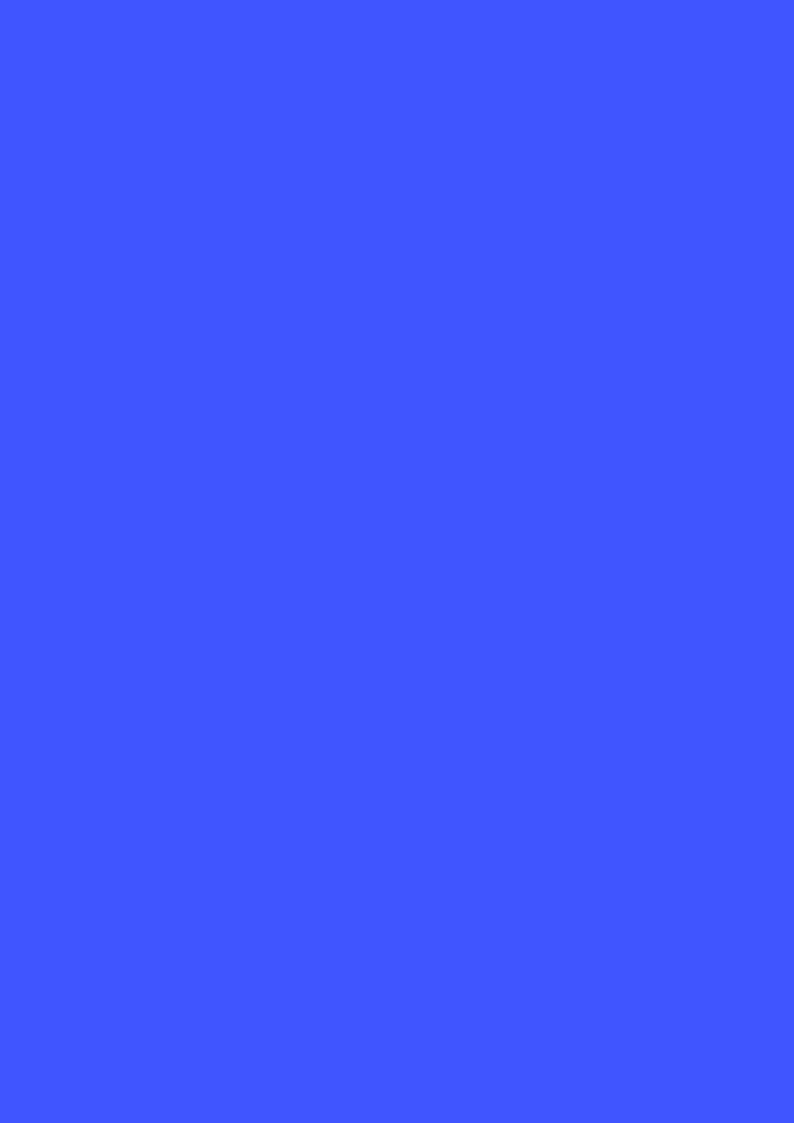
МІНІСТЕРСТВО ОСВІТИ І НАУКИ УКРАЇНИ НАЦІОНАЛЬНИЙ УНІВЕРСИТЕТ ХАРЧОВИХ ТЕХНОЛОГІЙ
Кафедра машинобудування, стандартизації та сертифікації обладнання
Кадомський С.В.
ВЗАЄМОЗАМІННІСТЬ, СТАНДАРТИЗАЦІЯ ТА ТЕХНІЧНІ ВИМІРЮВАННЯ
МЕТОДИЧНІ ВКАЗІВКИ до виконання курсової роботи
для студентів напряму 0902 “Інженерна механіка ”
денної, заочної та скороченої форм навчання
Київ 2012
З М І С Т
Загальні вимоги
1.Розрахунок і вибір посадок з зазором
2.Розрахунок і вибір посадок з натягом
3.Вибір посадок кілець підшипників кочення
4.Розрахунок гладких конічних калібрів
5.Розрахунок розмірних ланцюгів
6.Рекомендації до проставлення допусків форми і розташування на кресленнях деталей Література
Курсова робота з дисципліни “Взаємозамінність, стандартизація і технічні вимірювання ” зміцнює теоретичні знання, одержані студентами під час вивчення лекційного курсу, надає практичних навичок з їх використання, які в подальшому застосовуються при вивченні дисциплін та курсовому проектуванні з дисциплін “Деталі машин ”, “Технологічні основи машинобудування ”, “Обладнання харчових виробництв ”, дипломному проектуванні тощо.
Пояснювальна записка до курсової роботи з ВСіТВ складається з розрахункової та підсумкової графічної частин, в якій подаються результати отриманих розрахунків і креслення. До неї входять такі розділи.
1.Завдання для розрахунку посадки з зазором і натягом, складальне креслення вузла і його стисла характеристика (опис роботи), яке видається консультантом індивідуально кожному студенту.
2.Розрахунок і вибір посадки з зазором. Ескіз схеми полів допусків.
3.Розрахунок і вибір посадки з натягом. Ескіз схеми полів допусків.
4.Розрахунок гладких граничних калібрів для контролю заданого з’єднання. Ескіз схеми полів допусків калібру-пробки і калібру-скоби.
5.Вибір посадок кілець підшипників кочення.
6.Креслення вузла з проставленими на ньому вибраними посадками.
7.Креслення трьох різнотипних деталей з різноманітних матеріалів: вал, кришка, стакан, втулка тощо з проставленими на них розмірами з допусками, параметрами шорсткості, відхиленнями форми та розташування, технологічними вимогами, матеріалом. Креслення оформлюються відповідно до вимог стандартів.
8.Схема розмірного ланцюга з проставленими на ньому розмірами і його розрахунок одним з методів: “максимуму – мінімуму ”, імовірнісному та ін.
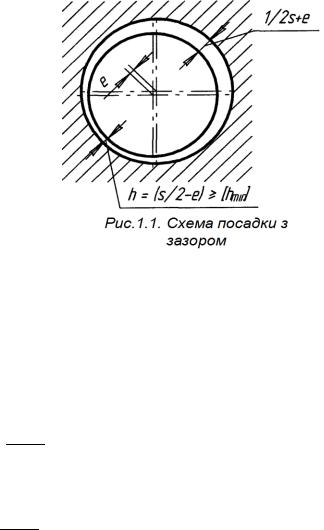
1. РОЗРАХУНОК І ВИБІР ПОСАДКИ З ЗАЗОРОМ
Розрахунок посадки з зазором здійснюється для підшипників ковзання, які працюють в умовах рідинного тертя, коли поверхні вала і втулки повністю відокремлені шаром мастила, внаслідок чого граничне тертя між ними замінюється внутрішнім тертям в рідкому середовищі.
Вихідні дані для розрахунку посадки з зазором: d – діаметр з’єднання, м;
L – довжина підшипника, м; R – радіальне навантаження, Н; n – частота обертання, об/хв; t – робоча температура, ºС.
Розрахунок здійснюється в такій послідовності.
1.Розраховуємо кутову швидкість вала, рад/с:
ϖ= π30n ,
2.Визначаємо середній тиск, Н/м2:
p = LRd
3. З табл. 1.1 вибираємо висоту мікронерівностей поверхонь тертя. Шорсткість отвору RaD i валу Rad може бути різною, якщо враховувати, що втулка оброблюється з меншою точністю.
|
|
|
Таблиця 1.1 |
|
|
Висота мікронерівностей посадочних |
RaD |
Rad |
|
|
0,2…1,6 |
0,1…1,6 |
||
|
поверхонь, мкм |
|||
|
|
|
|
|
4. Визначаємо допустиму мінімальну товщину масляного шару, мкм: |
||||
|
[hмін ] ≥ hpt = Kpt(4RaD+4Rad+γD), |
|
|
де hpt – товщина масляного шару, за якого забезпечується рідинне тертя, мкм; Kpt – коефіцієнт запасу надійності за товщиною масляного шару (Kpt≥2); γD – добавка на нерозривність масляного шару (γD = 2…3 мкм).

5. З табл. 1.2 вибираємо мастило для підшипника ковзання. З табл. 1.3 визначаємо його динамічну в’язкість при робочій температурі підшипника μ2. Для проектних розрахунків приймаємо в’язкість вибраного мастила при температурі на 10…20 ºС вище робочої – μ1.
|
|
|
|
|
|
|
|
|
Таблиця 1.2 |
||
|
|
|
|
|
|
|
|
|
|
|
|
|
Питоме навантаження |
|
Кутова швидкість |
Рекомендована марка |
|||||||
|
р×106, Н/м2 |
|
|
ω, рад/с |
|
|
мастила |
||||
|
до 0,5 |
|
|
до 15 |
|
Індустріальне 12 (І-12) |
|
||||
|
|
|
понад 15 |
|
|
Велосіт (І-5А) |
|||||
|
|
|
|
|
|
|
|||||
|
|
|
|
|
до 10 |
|
Індустріальне 45 (І-45) |
||||
|
0,5…6,5 |
|
|
10…25 |
|
|
– // – |
30 (І-30) |
|||
|
|
|
|
|
понад 25 |
|
|
– // – |
20 (І-20) |
||
|
|
|
|
|
до 10 |
|
Автотракторне АК-15 |
||||
|
6,5…15 |
|
|
10…25 |
|
|
– // – |
АК-10 |
|||
|
|
|
|
|
понад 25 |
|
|
І-45 або І-30 |
|||
|
|
|
|
|
|
|
|
|
Таблиця 1.3 |
||
|
|
|
|
|
|
|
|
|
|||
|
Марка мастила |
|
Динамічна вязкість μ×10-3 Н∙с/м2, при температурі |
||||||||
|
|
|
40 ºС |
|
50 ºС |
60 ºС |
70 ºС |
80 ºС |
|||
|
Велосіт (І-5А) |
|
5,8 |
|
3,6…4,5 |
3,5 |
2,8 |
- |
|
|
|
|
І-12 |
|
16,5 |
|
9…12,6 |
8,5 |
6,3 |
4,8 |
|
|
|
|
І-20 |
|
26,0 |
|
15,3…20,7 |
13,0 |
9,2 |
6,9 |
|
|
|
|
І-30 |
|
40,0 |
|
25,2…29,7 |
18,5 |
13,0 |
9,4 |
|
|
|
|
І-45 |
|
70,0 |
|
31,5…40,5 |
23,0 |
19,0 |
13,5 |
|
|
6. Визначаємо мінімальний допустимий зазор в підшипнику ковзання, мкм:
|
Kµϖd 2 |
− |
(Kµϖd 2 )2 |
−16 ph2 |
mµ ϖd 2 |
|
|
Smin F = |
1 |
|
1 |
pt |
2 |
|
, |
|
|
4 phpt |
|
|
|
||
|
|
|
|
|
|
|
де K i m – коефіцієнти, які визначають з табл.1.4 за співвідношенням L/d.
|
|
|
|
|
Таблиця 1.4 |
||
|
|
|
|
|
|
|
|
L/d |
K |
m |
L/d |
K |
m |
||
|
|
|
|
|
|
|
|
0,4 |
0,255 |
0,356 |
0,9 |
0,690 |
0,705 |
|
|
0,5 |
0,355 |
0,472 |
|
1,0 |
0,760 |
0,760 |
|
0,6 |
0,452 |
0,568 |
|
1,1 |
0,823 |
0,823 |
|
0,7 |
0,539 |
0,634 |
|
1,2 |
0,880 |
0,880 |
|
0,8 |
0,623 |
0,698 |
|
1,5 |
1 |
1 |
|
|
|
|
|
|
|
|
|
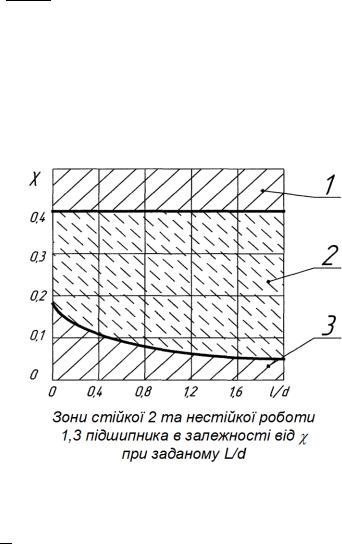
7. Враховуючи, що посадку з зазором здійснюють в системі основного отвору з табл. 1.5 верхнє граничне відхилення вала es визначаємо за величиною основного відхилення, значення якого для всіх квалітетів постійне і відповідає мінімальному зазору посадки, або більше за нього, тобто еs ≥ Smin F.
8. Перевіряємо можливість забезпечення рідинного тертя за умови
Smin = es ≈Smin F.
9. Визначаємо коефіцієнт навантаженності підшипника
CR = p ψ2 ,
µ1 ϖ
де ψ = S/d – відносний зазор.
10.З табл. 1.5 залежно від L/d та розрахованого в п.9 коефіцієнта навантаженості підшипника СR визначаємо відносний зазор χ. Якщо розраховане значення СR не збігається з табличним,
вибираємо найближче.
11.За рисунком залежно від L/d та χ
визначаємо умови роботи підшипника. Якщо вона нестабільна, змінюємо зазор заміною поля допуску валу. Наприклад, “g” на “f” або “f” на “e” (без зміни
квалітету) |
і повторюємо розрахунок з |
||
п. 8 – 10 з умовою Smin = es. |
|
||
12. |
При |
стабільній |
роботі |
підшипника розраховуємо мінімальну товщину масляного шару мкм, за формулою:
hmin = S2 (1−χ),
13. Перевіряємо запас надійності за товщиною масляного шару:
K pt |
= |
|
hmin |
|
|
. |
4R |
+4R |
+γ |
D |
|||
|
|
aD |
ad |
|
|

Якщо Крт ≥ 2, поле допуску вибрано правильно. Якщо рідинне тертя не забезпечується, вибираємо інше поле допуску валу і розрахунок з п.9 повторюємо.
14. Розраховуємо найбільший функціональний зазор підшипника, мкм:
|
|
|
|
|
|
|
|
|
Kµ ϖd 2 |
+ (Kµ ϖd 2 )2 |
−16 ph2 |
mµ ϖd 2 |
|
|
|
Smax F = |
2 |
2 |
pt |
2 |
|
, |
|
|
|
4 phpt |
|
|
|
||
|
|
|
|
|
|
|
де K i m – коефіцієнти, які визначають з табл.1.4 за співвідношенням L/d.
15. Приймаємо, що підшипник зношується до 50 мкм за рік. На основі цього визначаємо максимальний зазор посадки підшипника, мкм:
Smax = Smax F – 50.
16.На підставі виконаних розрахунків з табл. 1.6 визначаємо типову посадку з’єднання таким чином, щоб значення Smin відповідало табличному, вибраному в п.7, а Smax наближалося до Smax, розрахованому в п.15.
Звибраних посадок (ДСТУ 2500 – 94), остаточно вибираємо переважну.
17.Для вибраної посадки будуємо схему розташування полів допусків для отвору і валу, вказуємо мінімальний та максимальний зазори з’єднання.
Примітка: у разі , коли під знаком квадратного кореня в п.6 одержується від’ємна
величина, слід збільшити кількість обертів вала, довжину підшипника, замінити мастило
або зменшити навантаження. Всі зміни обов’язково треба узгодити з керівником курсової роботи.
Приклад розрахунку посадки наведено в Додатку 1.
2. РОЗРАХУНОК ПОСАДКИ З НАТЯГОМ
З'єднання з натягом використовують для утворення нерухомих нерозбірних з’єднань, які передають крутний момент.
Посадки цієї групи розраховують на максимальний натяг – з позиції міцності деталей, які утворюють з’єднання, а мінімальний натяг з позиції працездатності з’єднання з умовою передачі необхідного крутного моменту і осьових сил за рахунок сил тертя, які виникають на деформованих контактуючих поверхнях. Фактичний натяг визначають за номінальними розмірами валу і втулки без урахування шорсткості поверхонь,
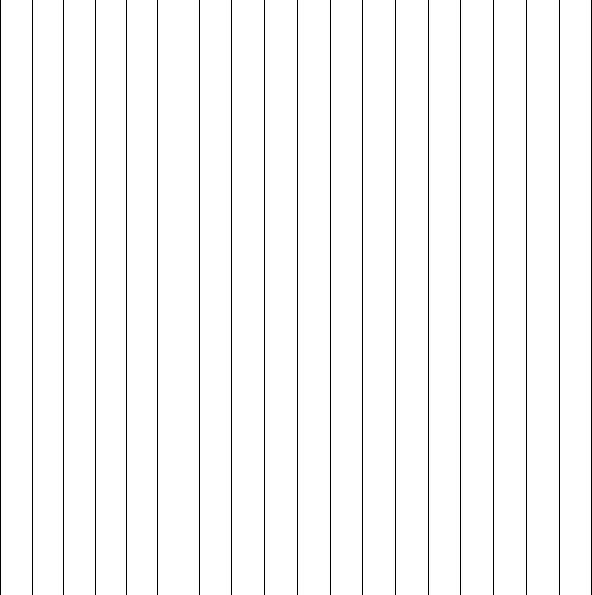
мікронерівності якої зминаються під дією тиску і зменшують величину натягу.
Таблиця 1.6
|
Граничні зазори [ |
Smax |
, мкм], в посадках з зазором в системі отвору |
|||||||||||||||||
|
Smin |
|||||||||||||||||||
|
|
|
|
|
|
|
|
|
|
|
|
|
|
|
|
|
|
|
|
|
|
|
|
|
|
за номінальних розмірів від 1 до 500 мм |
|
|
|
|
|||||||||||
Інтервал |
Н7 Н7 Н8 Н8 H9 Н10 |
Н7 H7 H8 H8 H9 Н6 |
Н7 Н8 Н8 Н9 H9 |
H6 |
Н7 |
|||||||||||||||
розмірів, мм |
c8 |
d8 |
d8 |
d9 |
d9 |
d10 |
e7 |
e8 |
e8 |
e9 |
e9 |
f6 |
f7 |
f7 |
f8 |
f8 |
f9 |
g5 |
g6 |
|
Понад 1 |
84 |
44 |
48 |
59 |
70 |
100 |
34 |
38 |
42 |
53 |
64 |
18 |
26 |
30 |
34 |
45 |
56 |
12 |
18 |
|
до 3 |
60 |
20 |
20 |
20 |
20 |
20 |
14 |
14 |
14 |
14 |
14 |
6 |
6 |
6 |
6 |
6 |
6 |
2 |
2 |
|
Понад 3 |
100 |
60 |
66 |
78 |
90 |
126 |
44 |
50 |
56 |
68 |
80 |
26 |
34 |
40 |
46 |
58 |
70 |
17 |
24 |
|
до 6 |
70 |
30 |
30 |
30 |
30 |
30 |
20 |
20 |
20 |
20 |
20 |
10 |
10 |
10 |
10 |
10 |
10 |
4 |
4 |
|
Понад 6 |
117 |
77 |
84 |
98 |
112 |
156 |
55 |
62 |
69 |
83 |
97 |
31 |
43 |
50 |
57 |
71 |
85 |
20 |
29 |
|
до 10 |
80 |
40 |
40 |
40 |
40 |
40 |
25 |
25 |
25 |
25 |
25 |
13 |
13 |
13 |
13 |
13 |
13 |
5 |
5 |
|
Понад10 |
140 |
95 |
104 120 136 |
190 |
68 |
77 |
86 |
102 118 |
38 |
52 |
61 |
70 |
86 |
102 |
25 |
35 |
||||
до 18 |
95 |
50 |
50 |
50 |
50 |
50 |
32 |
32 |
32 |
32 |
32 |
16 |
16 |
16 |
16 |
16 |
16 |
6 |
6 |
|
Понад18 |
164 119 131 150 169 |
233 |
82 |
94 |
106 125 144 |
46 |
62 |
74 |
86 |
105 124 |
29 |
41 |
||||||||
до 30 |
110 |
65 |
65 |
65 |
65 |
65 |
40 |
40 |
40 |
40 |
40 |
20 |
20 |
20 |
20 |
20 |
20 |
7 |
7 |
|
Понад30 |
184 144 158 181 204 |
280 |
100 114 128 151 174 |
57 |
75 |
89 |
103 126 149 |
36 |
50 |
|||||||||||
до 50 |
130 |
80 |
80 |
80 |
80 |
80 |
50 |
50 |
50 |
50 |
50 |
25 |
25 |
25 |
25 |
25 |
25 |
9 |
9 |
|
Понад50 |
216 176 192 220 248 |
340 |
120 136 152 180 208 |
68 |
90 |
106 122 150 178 |
42 |
59 |
||||||||||||
до 80 |
150 100 100 100 100 |
100 |
60 |
60 |
60 |
60 |
60 |
30 |
30 |
30 |
30 |
30 |
30 |
10 |
10 |
|||||
Понад80 |
259 209 228 261 294 |
400 |
142 161 180 213 246 |
80 |
106 125 144 177 210 |
49 |
69 |
|||||||||||||
до 120 |
180 120 120 120 120 |
120 |
72 |
72 |
72 |
72 |
72 |
36 |
36 |
36 |
36 |
36 |
36 |
12 |
12 |
|||||
Понад120 |
303 248 271 308 345 |
465 |
165 188 211 248 285 |
93 |
123 146 169 206 243 |
57 |
79 |
|||||||||||||
до 180 |
230 145 145 145 145 |
145 |
85 |
85 |
85 |
85 |
85 |
43 |
43 |
43 |
43 |
43 |
43 |
14 |
14 |
|||||
Понад180 |
358 288 314 357 400 |
540 |
192 218 244 287 330 108 142 168 194 237 280 |
64 |
90 |
|||||||||||||||
до 250 |
280 170 170 170 170 |
170 |
100 100 100 100 100 |
50 |
50 |
50 |
50 |
50 |
50 |
15 |
15 |
|||||||||
Понад250 |
433 323 352 401 450 |
610 |
214 243 272 321 370 120 160 189 218 267 316 |
72 |
101 |
|||||||||||||||
до 315 |
330 190 190 190 190 |
190 |
110 110 110 110 110 |
56 |
56 |
56 |
56 |
56 |
56 |
17 |
17 |
|||||||||
Понад315 |
506 356 388 439 490 |
670 |
239 271 303 354 405 134 176 208 240 291 342 |
79 |
111 |
|||||||||||||||
до 400 |
400 210 210 210 210 |
210 |
125 125 125 125 125 |
62 |
62 |
62 |
62 |
62 |
62 |
18 |
18 |
|||||||||
Понад400 |
600 390 424 482 540 |
730 |
261 295 329 387 435 146 194 228 262 320 478 |
87 |
123 |
|||||||||||||||
до 500 |
480 230 230 230 230 |
230 |
135 135 135 135 135 |
68 |
68 |
68 |
68 |
68 |
68 |
20 |
20 |
Переважні посадки, передбачені стандартом, виділено жирним шрифтом.
Вихідні дані для розрахунку посадки з натягом: діаметр валу – dном, м; внутрішній діаметр валу – d1, м; довжина з’єднання – L, м; зовнішній діаметр втулки – d2, м; крутний момент, який передає з’єднання – Мкр, Н∙м; діюча осьова сила – Rос, кН; матеріал охоплюваної (вал) і охоплюючої (втулка) деталей; робоча температура з’єднання – 20 ºС.
Розрахунок міцності посадок з натягом здійснюється в такій послідовності.
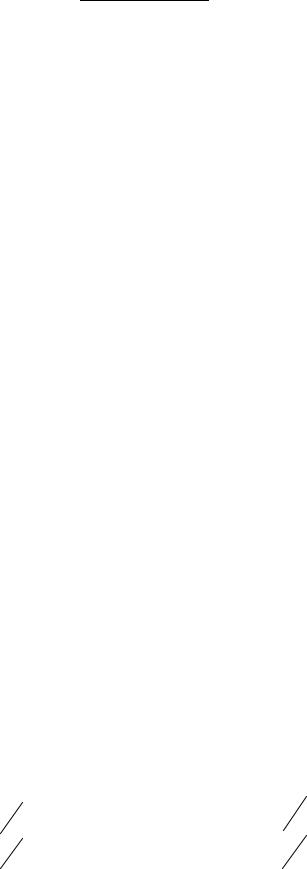
1. Знаходимо рівнодіючу осьової сили Roc і крутного моменту Mкр, Н:
T= Roc2 +(2Mкр / dном)2 .
2.Визначаємо мінімальний тиск на контактуючій поверхні, Н/м2:
[ pмін ] = |
|
T |
. |
|
π dном l f |
||||
|
|
|||
Вибираючи коефіцієнт тертя f, |
слід враховувати його залежність від |
матеріалу деталей (табл. 2.1), шорсткості поверхонь спряжених деталей, питомого тиску на контактній поверхні.
|
|
|
Таблиця 2.1 |
||
|
|
|
|
|
|
|
|
Коефіцієнти тертя |
|||
Матеріал деталей з’єднання |
|
|
f (використання |
|
|
f1 |
(запресування) |
температурних |
|||
|
|||||
|
|
|
деформацій) |
||
Сталь – сталь |
|
0,06…0,13 |
0,1…0,2 |
|
|
Сталь – чавун |
|
0,07…0,12 |
0,11…0,15 |
|
|
Сталь (чавун) – магнієві сплави |
|
0,03…0,05 |
0,05…0,08 |
|
|
Сталь (чавун) – бронза |
|
0,05…0,07 |
0,08…0,11 |
|
|
Сталь (чавун) – латунь |
|
0,05…0,10 |
0,08…0,15 |
|
3. Визначаємо найменший розрахунковий натяг Nмін, за якого з’єднання зберігає нерухомість:
|
|
|
|
Nмін |
=[ pмін ] d ( |
C1 −µ1 |
+ |
C2 +µ2 |
) , |
|
|
|
||||||||
|
|
|
|
E1 |
|
|
|
|
|
|||||||||||
|
|
|
|
|
|
|
|
|
|
|
|
E2 |
|
|
|
|
|
|
||
де Е1, Е2 і μ1, μ2 — відповідно модулі нормальної пружності і пуансонові |
||||||||||||||||||||
константи матеріалів |
(табл. 2.2) |
охоплюваної |
(індекс 1) і охоплюючої |
|||||||||||||||||
(індекс 2) деталей; С1 |
|
і |
С2 – |
коефіцієнти Ляме, які визначаємо за |
||||||||||||||||
формулами відповідно: |
|
|
|
|
|
|
|
|
|
|
|
|
|
|
|
|
|
|
||
|
1 + ( |
d1 |
d |
) |
2 |
|
|
|
|
|
1+(dном |
)2 |
|
|||||||
|
|
|
|
; |
|
|
C2 |
= |
|
|
|
|
d2 |
|
, |
|||||
C = |
|
|
|
|
|
ном |
|
|
|
|
|
|
|
|
|
|||||
|
|
|
|
|
|
|
|
|
|
|
dном |
|
|
|||||||
|
|
d |
|
|
|
|
|
|
|
|
|
|
||||||||
1 |
1 −( |
1 |
dном ) |
2 |
|
|
|
|
|
1 |
−( |
d2 ) |
2 |
|
||||||
|
|
|
|
|
|
|
||||||||||||||
|
|
|
|
|
|
|
|
|
|
|
де d1 i d2 — відповідно внутрішній діаметр охоплюваної і зовнішній діаметр охоплюючої деталей.
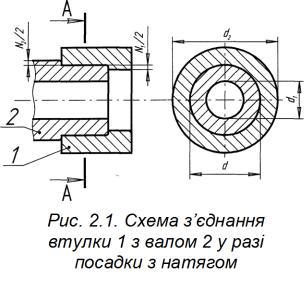
|
|
|
Таблиця 2.2 |
|
|
Матеріал |
Е,∙Н/м2 |
|
μ |
|
Сталь і сталеве литво |
(1,96…2)•1011 |
|
0,3 |
|
Чавунне литво |
(0,74…1,05)•1011 |
|
0,25 |
|
Бронза |
(0,84)•1011 |
|
0,35 |
|
Латунь |
(0,78)•1011 |
|
0,38 |
4. Визначаємо мінімально допустимий натяг з’єднання, мкм: |
||||
|
[Nмін] = Nмін р +γш + γт + γц+ γп, |
|
|
де γш – коефіцієнт, що враховує зминання нерівностей контактуючих поверхонь, під час утворення натягу, мкм, γш = 4,8(Rad + RaD); γт – коефіцієнт, що враховує різницю коефіцієнтів лінійного розширення матеріалів деталей з’єднання. Розраховуємо γт по формулі γт = (αа – αв)(tp – t0)d; γц – коефіцієнт, що враховує послаблення натягу під дією відцентрових сил. Приймаємо γц = 0; γп – коефіцієнт, який враховує зменшення натягу під час повторних запресувань. Він визначається по формуліγп = 2 (kaRza+ kbRb ). Де k визначається по табл. , а Rz по табл. 1.5.
5. Обчислюємо максимально допустимий тиск [pмax], за якого відсутня пластична деформація на контактуючих поверхнях з’єднання.
У разі запресування втулок (найзагальніший випадок) величина натягу, складається з деформацій стиску внутрішньої труби і розтягу зовнішньої труби (рис. 2.1).
Найбільший допустимий тиск визначаємо за умови, що найбільші напруги, які виникають в поверхневих шарах спряжених деталей, не перевищують границі текучості матеріалів σт.
Небезпечними можуть стати нормальні концентричні напруги на внутрішній поверхні порожнистого вала σdмax або внутрішній поверхні втулки σDмах .
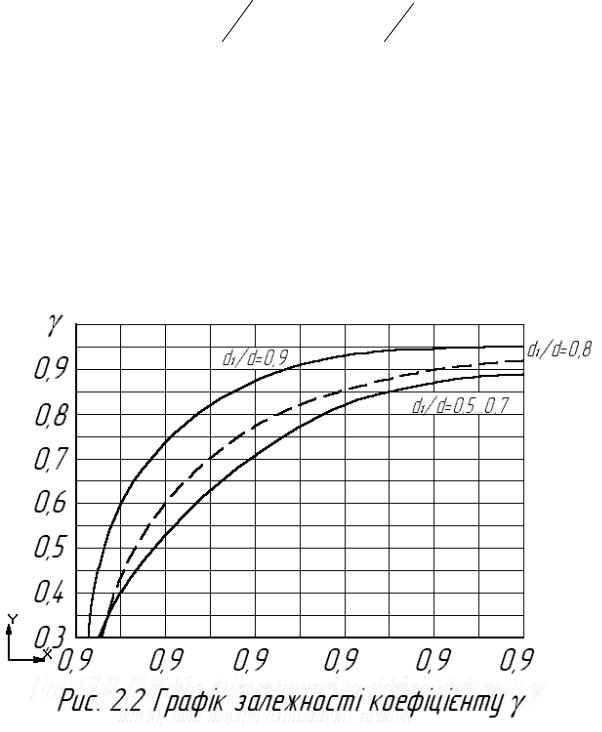
Визначаємо тиск відповідно для валу р1 і втулки р2:
pmax ≤ |
σt1 |
C |
; |
pmax ≤ |
σt 2 |
C |
. |
1 |
|
2 |
|
||||
|
|
1 |
|
|
|
|
2 |
З двох розрахованих значень вибираємо найменше, яке множимо на коефіцієнт 0,6 з метою створення коефіцієнта запасу міцності:
[pмax]=0,6 pмaxрозр.
6. Знаходимо найбільший розрахунковий натяг, мкм:
Nмax =[ pмax ] d ( |
C1 − µ1 |
+ |
C2 + µ2 |
) |
|
|
|||
|
E1 |
E2 |
7. Визначаємо максимально допустимий натяг
[Nмax] = Nмax p γ + γш
де γ – коефіцієнт, що враховує збільшення тиску біля торця охоплюючої деталі d залежності від співвідношення L/dном i dном/d2 (див. рис. 2.1)
8. З урахуванням розрахованих Nмax i Nмiн з таблиці 2.3 визначаємо посадку з натягом. Необхідну несучу здатність посадки забезпечуємо збільшенням довжини з'єднання, діаметра d2 або зменшенням d1.
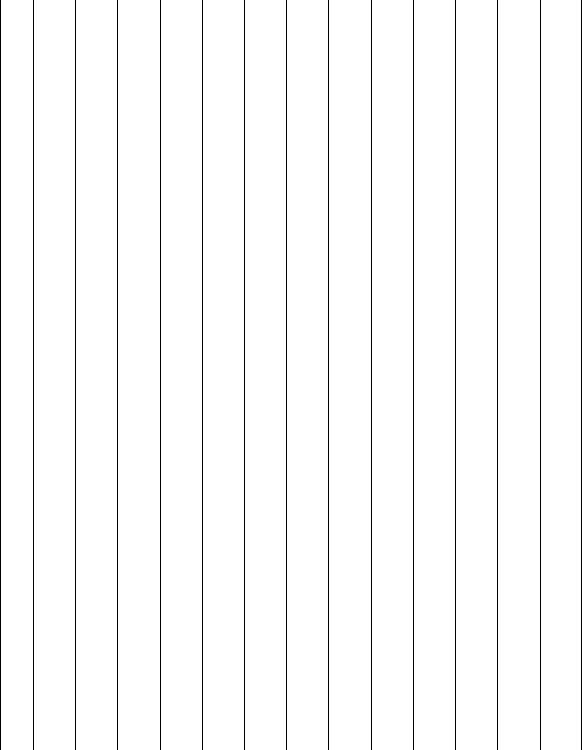
9. Для вибраної посадки будуємо схему розташування полів допусків для отвору і валу, вказуємо мінімальний і максимальний натяги з’єднання.
Таблиця 2.3
|
Граничні натяги [ |
Nmax |
, мкм], для посадок в системі отвору |
|
|
||||||||||
|
Nmin |
|
|
||||||||||||
|
|
|
|
|
|
|
|
|
|
|
|
|
|
|
|
Інтервал |
Н5 |
H6 |
Н7 |
Н6 |
H7 |
Н6 |
H7 |
Н7 |
H8 |
Н7 |
Н8 |
Н7 |
H8 |
H8 |
Н8 |
розмірів, мм |
n4 |
р5 |
р6 |
r5 |
r6 |
s5 |
s6 |
s7 |
s7 |
t6 |
t7 |
u7 |
u8 |
x8 |
z8 |
Понад 10 |
17 |
26 |
29 |
31 |
34 |
36 |
39 |
46 |
46 |
- |
- |
51 |
60 |
72 |
87 |
до 18 |
4 |
7 |
0 |
12 |
5 |
17 |
10 |
10 |
1 |
- |
- |
15 |
6 |
13 |
23 |
Понад 18 |
17 |
31 |
- |
37 |
- |
44 |
48 |
56 |
- |
- |
- |
69 |
81 |
97 |
121 |
до 24 |
4 |
9 |
- |
15 |
- |
22 |
14 |
14 |
- |
- |
- |
27 |
8 |
21 |
40 |
Понад 24 |
21 |
31 |
35 |
37 |
41 |
44 |
48 |
56 |
56 |
54 |
- |
69 |
81 |
97 |
121 |
до 30 |
6 |
9 |
1 |
15 |
7 |
22 |
14 |
14 |
2 |
20 |
- |
27 |
8 |
21 |
40 |
Понад 30 |
24 |
37 |
42 |
37 |
58 |
54 |
59 |
68 |
68 |
70 |
62 |
95 |
109 |
136 |
175 |
до 40 |
6 |
10 |
1 |
15 |
9 |
27 |
18 |
18 |
4 |
23 |
8 |
35 |
21 |
41 |
73 |
Понад 40 |
24 |
37 |
42 |
37 |
58 |
54 |
59 |
68 |
68 |
70 |
62 |
95 |
109 |
136 |
175 |
до 50 |
6 |
10 |
1 |
15 |
9 |
27 |
18 |
18 |
4 |
23 |
8 |
35 |
21 |
41 |
73 |
Понад 50 |
28 |
45 |
51 |
54 |
60 |
66 |
72 |
83 |
83 |
85 |
73 |
117 |
133 |
168 |
218 |
до 65 |
7 |
13 |
2 |
22 |
11 |
34 |
23 |
23 |
7 |
36 |
9 |
57 |
41 |
76 |
126 |
Понад 65 |
28 |
45 |
51 |
56 |
62 |
72 |
78 |
89 |
89 |
94 |
79 |
132 |
148 |
192 |
256 |
до 80 |
7 |
13 |
2 |
22 |
13 |
40 |
29 |
29 |
13 |
45 |
15 |
72 |
56 |
100 |
164 |
Понад 80 |
33 |
52 |
59 |
66 |
73 |
86 |
93 |
106 |
106 |
113 |
96 |
159 |
178 |
232 |
312 |
до 100 |
8 |
15 |
2 |
29 |
16 |
49 |
36 |
36 |
17 |
56 |
20 |
89 |
70 |
124 |
204 |
Понад 100 |
33 |
52 |
59 |
66 |
76 |
94 |
101 |
114 |
114 |
126 |
105 |
179 |
198 |
264 |
364 |
до 120 |
8 |
15 |
2 |
32 |
19 |
57 |
44 |
44 |
25 |
69 |
29 |
109 |
90 |
156 |
256 |
Понад 120 |
39 |
61 |
68 |
81 |
88 |
110 |
117 |
132 |
132 |
147 |
126 |
210 |
233 |
311 |
428 |
до 140 |
9 |
18 |
3 |
38 |
23 |
67 |
52 |
52 |
29 |
82 |
37 |
130 |
107 |
185 |
302 |
Понад 140 |
39 |
61 |
68 |
83 |
90 |
118 |
125 |
140 |
140 |
159 |
139 |
230 |
253 |
343 |
478 |
до 160 |
9 |
18 |
3 |
40 |
25 |
75 |
60 |
60 |
37 |
94 |
50 |
150 |
127 |
217 |
352 |
Понад 160 |
39 |
61 |
68 |
86 |
93 |
126 |
133 |
148 |
148 |
171 |
162 |
250 |
273 |
373 |
528 |
до 180 |
9 |
18 |
3 |
43 |
28 |
83 |
68 |
68 |
45 |
106 |
59 |
170 |
147 |
247 |
402 |
Понад 180 |
45 |
70 |
79 |
97 |
106 |
142 |
151 |
168 |
168 |
195 |
174 |
282 |
308 |
422 |
592 |
до 200 |
11 |
21 |
4 |
48 |
31 |
93 |
76 |
76 |
50 |
120 |
71 |
190 |
164 |
278 |
448 |
Понад 200 |
45 |
70 |
79 |
100 |
109 |
150 |
159 |
176 |
176 |
209 |
186 |
304 |
338 |
457 |
647 |
до 225 |
11 |
21 |
4 |
51 |
34 |
101 |
84 |
84 |
58 |
134 |
83 |
212 |
186 |
313 |
503 |
Понад225 |
45 |
70 |
79 |
104 |
113 |
160 |
169 |
186 |
186 |
225 |
212 |
330 |
356 |
497 |
712 |
до 250 |
11 |
21 |
4 |
55 |
38 |
111 |
94 |
94 |
68 |
150 |
94 |
238 |
212 |
353 |
568 |
Понад250 |
50 |
79 |
88 |
117 |
126 |
181 |
193 |
218 |
210 |
250 |
226 |
367 |
396 |
556 |
791 |
до 280 |
11 |
24 |
4 |
62 |
42 |
126 |
106 |
106 |
77 |
166 |
108 |
263 |
234 |
394 |
629 |
Понад280 |
50 |
79 |
88 |
121 |
130 |
193 |
202 |
222 |
222 |
272 |
242 |
402 |
431 |
606 |
871 |
до 315 |
11 |
24 |
4 |
66 |
46 |
138 |
118 |
118 |
89 |
188 |
124 |
298 |
269 |
444 |
709 |
Понад315 |
55 |
87 |
98 |
133 |
144 |
215 |
226 |
247 |
247 |
304 |
270 |
447 |
479 |
679 |
989 |
до 355 |
12 |
26 |
5 |
72 |
51 |
154 |
133 |
133 |
101 |
211 |
137 |
333 |
301 |
501 |
811 |
Понад355 |
55 |
87 |
98 |
139 |
150 |
- |
244 |
265 |
265 |
330 |
351 |
492 |
524 |
749 |
1089 |
до 400 |
12 |
26 |
5 |
78 |
57 |
- |
151 |
151 |
119 |
237 |
205 |
378 |
346 |
571 |
911 |
Переважні посадки виділено жирним шрифтом У разі відсутності стандартної посадки, яка задовольняє розрахованим
величинам граничних натягів передбачаємо додаткове кріплення деталей з’єднання.

3.ВИБІР ПОСАДОК КІЛЕЦЬ ПІДШИПНИКІВ КОЧЕННЯ
1.Аналізуємо роботу підшипникового вузла, визначаємо вид навантаження для кілець підшипника.
2.Посадку кілець підшипника визначаємо за рекомендаціями наведеними в таблицях 3.1 і 3.2.
Таблиця 3.1
|
Поля допусків посадочних місць під |
|
||
Номінальний |
підшипники кочення при місцевому |
Тип підшипника |
||
діаметр, мм |
навантаженні |
|||
|
||||
|
Валів (осей) |
Отворів в корпусах |
|
|
Спокійне |
навантаження, можливі помірні поштовхи, вібрація під час |
|||
≤ 80 |
перевантаження до 150% |
|
||
h5,h6, g5, g6, f6, is6 |
H6, H7 |
Всі типи, крім |
||
> 80 ≤ 260 |
h5,h6, g5, g6, f6, is6 |
G6,G7 (H6, H7, H8) |
||
штампованих, |
||||
> 260 ≤ 500 |
f6, is6 |
G6, G7 |
||
голчастих |
||||
> 500 ≤ 1600 |
f6, is6 |
F7, F8 |
||
|
Навантаження з ударами і вібрацією, можливе перевантаження
до 300%
≤80
>80 ≤ 260
>260 ≤ 1600
Всі розміри
Всі розміри
h5,h6 |
Js6, Js7 |
Всі типи, крім |
|
h5,h6 |
H6, H7 (Js6, Js7) |
штампованих, |
|
g5, g6 |
H6, H7 (Js6, Js7) |
роликових коніч- |
|
них дворядних |
|||
|
|
||
h5,h6, g5, g6 |
H6, H7(Js6, Js7) |
Роликові, конічні |
|
дворядні |
|||
|
|
||
Незалежно від характеру навантаження |
|||
k5, k6, js5, js6 |
K6, K7, Js6, Js7 |
Роликові, голчасті, |
|
(в стакан зі сталі) |
штамповані |
||
|
|
|
|
|
|
|
Таблиця 3.2 |
|||
|
|
|
|
|
|
|
|
|
|
Клас |
Шорсткість Ra, мкм, посадочних поверхонь під |
||||||||
підшипники кочення при номінальних розмірах в мм |
|
||||||||
точності |
|||||||||
валів |
отворів |
валів |
отворів |
валів |
отворів |
||||
підшипника |
|||||||||
<80 |
>80 |
<80 |
>80 |
<80 |
>80 |
|
|
||
|
|
|
|||||||
0 |
1,25 |
2,5 |
1,25 |
2,5 |
2,5 |
2,5 |
|
|
|
6,5 |
0,63 |
1,25 |
0,63 |
1,25 |
1,25 |
2,5 |
|
|
|
4 |
0,32 |
0,63 |
0,63 |
0,63 |
1,25 |
2,5 |
|
|
4. РОЗРАХУНОК ГЛАДКИХ ГРАНИЧНИХ КАЛІБРІВ
Приклад. Виконати повний розрахунок калібрів для посадки ǿ75 Н7/е8
(ES = 30 мкм, EI = 0 мкм, es = – 60 мкм, ei = – 106 мкм).
Умовні позначення, які використовуються у розрахунку полів допусків для калібрів:
ІТ – допуск виробу;
Н1 – поле допуску на виготовлення робочих калiбрiв (скоб) для валу;
Y1 – поле допуску на вихiд pозміpу зношеного пpохiдного калiбpу для валу за межу поля допуску виpобу;
Z1 – вiдхил сеpедини поля допуску на виготовлення пpохiдного калібру для валу вiдносно найменшого граничного pозмipу виpобу;
Hs – поле допуску тих самих калiбрiв, але зі сферичною вимiрювальною поверхнею;
Нр – поле допуску на виготовлення контрольних калiбрiв для скоб; D – номiнальний pозмip виpобу;
Н – поле допуску на виготовленння калiбpiв (пробок) для отвоpу;
Y– поле допуску на вихiд pозмipу зношеного пpохiдного калiбpу за межу поля допуску виpобу;
Z– вiдхил сеpедини поля допуску на виготовлення пpохiдного калiбpу для отвоpiв вiдносно найменшого гpаничного pозмipу виpобу;
d, d1 - величина для компенсації похибки контролю калiбpами отвоpiв з pозмipами бiльше 180 мм.
1. На основі побудованої схеми полів допусків для посадки обчислюємо найбільший та найменший граничні розміри отвору і валу, мм:
Dmax = D + ES = 75,000 + 0,030 = 75,030; Dmin = D + EI = 750,000 + 0 = 75,000; dmax = d + es = 75,000 + ( -0,060 ) = 74,940; dmin = d + ei = 75,000 + ( -0,106 ) = 74,894.
2. За табл. 4.1 знаходимо допуски і граничні відхилення робочих калібрів і контркалібрів:
для отвору: ǿ75Н7: Z = 4 мкм, Y = 3 мкм, Н = 5 мкм;
для валу: ǿ75е8: Z1 = 7 мкм, Y = 5 мкм, Н = 8 мкм, Нр = 3 мкм.
3. Визначаємо розміри калібрів і контркалібрів за такими формулами: калібри-пробки:
ПРmax = Dmin + Z + H/2 = 75,000 + 0,004 + 0,0025 = 75,0065; ПРmin = Dmin + Z – H/2 = 75,000 + 0,004 – 0,0025 = 75,0015; ПРзн = Dmin – Y = 75,000 – 0,003 = 74,997;
НЕmax = Dmax + H/2 = 75,030 + 0,0025 = 75,0325; НЕmin = Dmax – H/2 = 75,030 – 0,0025 = 75,0275;
виконавчі розміри робочих калібрів-пробок:
ПР = ПРmax-Н = 75,0065 -0,005; ПРзн = 74,997;
НЕ = НЕmax-Н = 75,0325 -0,005;
калібри-скоби:
ПРmax = dmax – Z1 + H1/2 = 74,940 – 0,007 + 0,004 = 74,937; ПРmin = dmax – Z1 – H1/2 = 74,940 – 0,007 – 0,004 = 74,929; ПРзн = dmax + Y1 = 74,940 + 0,005 = 74,945;
НЕmax = dmin + H1/2 = 74,894 + 0,004 = 74,898; НЕmin = dmin – H1/2 = 74,894 – 0,004 = 74,890;
виконавчі розміри робочих калібрів–скоб, мм:
ПР = ПРmax+Н1 = 74,929 +0,008; ПРзн = 74,945;
НЕ = НЕ min+Н1 =74,890 + 0,008.
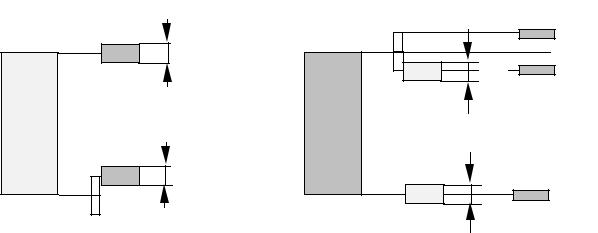
4. Контркалібри для контролю скоб розраховуємо за формулами:
К-ПРmax = dmax – Z1 + Hp/2 = 74,940 – 0,007 + 0,0015 = 74,9345; К-ПРmin = dmax – Z1 – Hp/2 = 74,940 – 0,007 – 0,0015 = 74,9315; К-Иmax = dmax + Y1 + Hp/2 = 74,940 +0,005 + 0,0015 = 74,9465; К-Иmin = dmax + Y1 – Hp/2 = 74,940 +0,005 – 0,0015 = 74,9435; К-НЕmax = dmin + Hp/2 = 74,894 + 0,0015 = 74,8955;
К-НЕmin = dmin – Hp/2 = 74,894 – 0,0015 = 74,8925;
виконавчі розміри контркалібрів, мм:
К-ПР = К-ПРmax-Нр = 79,9345 - 0,003; К-И = К-Иmax-Нр = 79,9465 - 0,003; К-НЕ = К-НЕmax-Нр = 79,8955 - 0,003.
5. Після розрахунку виконавчих розмірів калібрів для контролю отвору і валу визначаємо розташування полів допусків калібрів для контролю отвору та валу з необхідними числовими значеннями (табл. 4.1).
ES |
|
H |
es |
Y1 |
|
|
К-ЗнНр |
|
Z1 |
|
H1 |
Нр |
|||
|
|
Не |
|
|
|||
|
|
|
|
Пр |
|
К-Пр |
|
|
TD |
|
|
Td |
|
||
|
|
|
|
|
|
||
|
Z |
H |
|
|
Не |
H1 |
К-Не |
EI |
ei |
|
|
||||
Y |
|
|
|
|
Нр |
||
а) для контролю отвору |
|
в) для контролю валу |
|||||
6. Креслимо ескізи калібру-скоби і калібру-пробки відповідно до |
рекомендацій і розмірів, наведених у табл. 4.2 – 4.5.
Таблиця 4.1
Квалі |
Позна |
|
|
|
Номінальні розміри, мкм |
|
|
|
IT |
||||||
|
>3 |
>6 |
>10 |
>18 |
>30 |
>50 |
>80 |
>120 |
>180 |
>250 |
>315 |
>400 |
|||
тет |
чення |
до 3 |
до |
до |
до |
до |
до |
до |
на форму |
||||||
|
|
|
до 6 |
до10 |
до18 |
до30 |
до50 |
до80 |
120 |
180 |
250 |
315 |
400 |
500 |
|
|
Z |
1 |
1,5 |
1,5 |
2 |
2 |
|
|
|
|
|
|
|
|
|
6 |
Y |
1 |
1 |
1 |
1,5 |
1,5 |
|
|
|
|
|
|
|
|
|
α, α1 |
0 |
0 |
0 |
0 |
0 |
|
|
|
|
|
|
|
|
|
|
|
Z1 |
1,5 |
2 |
2 |
2,5 |
3 |
|
|
|
|
|
|
|
|
|
|
Y1 |
1,5 |
1,5 |
1,5 |
2 |
3 |
|
|
|
|
|
|
|
|
|
|
H |
1,2 |
1,5 |
1,5 |
2 |
2,5 |
|
|
|
|
|
|
|
|
IT2 |
|
H1 |
2 |
2,5 |
2,5 |
3 |
4 |
|
|
|
|
|
|
|
|
IT1 |
|
HP |
0,8 |
1 |
1 |
1,2 |
1,5 |
1,5 |
|
|
|
|
|
|
|
IT1 |
|
|
до 3 |
>3 |
>6 |
>10 |
>18 |
>30 |
>50 |
>80 |
>120 |
>180 |
>250 |
>315 |
>400 |
|
|
|
до |
до |
до |
до |
до |
до |
|
|||||||
|
|
|
до 6 |
до10 |
до18 |
до30 |
до50 |
до80 |
120 |
180 |
250 |
315 |
400 |
500 |
|
|
Z, Z1 |
1,5 |
2 |
2 |
2,5 |
3 |
3,5 |
4 |
5 |
6 |
7 |
8 |
10 |
11 |
|
7 |
Y, Y1 |
1,5 |
1,5 |
1,5 |
2 |
3 |
3 |
3 |
4 |
4 |
6 |
7 |
8 |
9 |
|
α, α1 |
0 |
0 |
0 |
0 |
0 |
0 |
0 |
0 |
0 |
3 |
4 |
6 |
7 |
|
|
|
H, H1 |
2 |
2,5 |
2,5 |
3 |
4 |
4 |
5 |
6 |
8 |
10 |
12 |
13 |
15 |
IT2 |
|
Hs |
- |
- |
1,5 |
2 |
2,5 |
2,5 |
3 |
4 |
5 |
7 |
8 |
9 |
10 |
IT1 |
|
Hp |
0,8 |
1 |
1 |
1,2 |
1,5 |
1,5 |
2 |
2,5 |
3,5 |
4,5 |
6 |
7 |
8 |
IT1 |
|
|
до 3 |
>3 |
>6 |
>10 |
>18 |
>30 |
>50 |
>80 |
>120 |
>180 |
>250 |
>315 |
>400 |
|
|
|
до |
до |
до |
до |
до |
до |
|
|||||||
|
|
|
до 6 |
до10 |
до18 |
до30 |
до50 |
до80 |
120 |
180 |
250 |
315 |
400 |
500 |
|
|
Z, Z1 |
2 |
3 |
3 |
4 |
5 |
6 |
7 |
8 |
9 |
12 |
14 |
16 |
18 |
|
8 |
Y, Y1 |
3 |
3 |
3 |
4 |
4 |
5 |
5 |
6 |
6 |
7 |
9 |
9 |
11 |
|
α, α1 |
0 |
0 |
0 |
0 |
0 |
0 |
0 |
0 |
0 |
4 |
6 |
7 |
9 |
|
|
|
H |
2 |
2,5 |
2,5 |
3 |
4 |
4 |
5 |
6 |
8 |
10 |
12 |
13 |
15 |
IT2 |
|
H1 |
3 |
4 |
4 |
5 |
6 |
7 |
8 |
10 |
12 |
14 |
16 |
18 |
20 |
IT3 |
|
Hs, |
1,2 |
1,5 |
1,5 |
2 |
2,5 |
2,5 |
3 |
4 |
5 |
7 |
8 |
9 |
10 |
IT1 |
|
Hp |
|
|
|
|
|
|
|
|
|
|
|
|
|
|
|
|
до 3 |
>3 |
>6 |
>10 |
>18 |
>30 |
>50 |
>80 |
>120 |
>180 |
>250 |
>315 |
>400 |
|
|
|
до |
до |
до |
до |
до |
до |
|
|||||||
|
|
|
до 6 |
до10 |
до18 |
до30 |
до50 |
до80 |
120 |
180 |
250 |
315 |
400 |
500 |
|
|
|
|
|
|
|
|
|
|
|
||||||
|
Z, Z1 |
5 |
6 |
7 |
8 |
9 |
11 |
13 |
15 |
18 |
21 |
24 |
28 |
32 |
|
9 |
Y, Y1 |
0 |
0 |
0 |
0 |
0 |
0 |
0 |
0 |
0 |
0 |
0 |
0 |
0 |
|
α, α1 |
0 |
0 |
0 |
0 |
0 |
0 |
0 |
0 |
0 |
4 |
6 |
7 |
9 |
|
|
|
H |
2 |
2,5 |
2,5 |
3 |
4 |
4 |
5 |
6 |
8 |
10 |
12 |
13 |
15 |
IT2 |
|
H1 |
3 |
4 |
4 |
5 |
6 |
7 |
8 |
10 |
12 |
14 |
16 |
18 |
20 |
IT3 |
|
Hs, |
1,2 |
1,5 |
1,5 |
2 |
2,5 |
2,5 |
3 |
4 |
5 |
7 |
8 |
9 |
10 |
IT1 |
|
Hp |
|
|
|
|
|
|
|
|
|
|
|
|
|
|
Закінчення табл. 4.1
Квалі |
Позна |
|
|
|
|
Номінальні розміри, мкм |
|
|
|
IT |
||||||
|
>3 |
>6 |
>10 |
>18 |
>30 |
>50 |
>80 |
>120 |
>180 |
>250 |
>315 |
>400 |
||||
тет |
чення |
до 3 |
до |
до |
до |
до |
до |
до |
на форму |
|||||||
|
|
|
до 6 |
до10 |
до18 |
до30 |
до50 |
до80 |
120 |
180 |
250 |
315 |
400 |
500 |
|
|
|
Z, Z1 |
5 |
6 |
7 |
8 |
|
9 |
11 |
13 |
15 |
18 |
24 |
27 |
32 |
37 |
|
10 |
Y, Y1 |
0 |
0 |
0 |
0 |
|
0 |
0 |
0 |
0 |
0 |
0 |
0 |
0 |
0 |
|
α, α1 |
0 |
0 |
0 |
0 |
|
0 |
0 |
0 |
0 |
0 |
7 |
9 |
11 |
14 |
|
|
|
H |
2 |
2,5 |
2,5 |
3 |
|
4 |
4 |
5 |
6 |
8 |
10 |
12 |
13 |
15 |
IT2 |
|
H1 |
3 |
4 |
4 |
5 |
|
6 |
7 |
8 |
10 |
12 |
14 |
16 |
18 |
20 |
IT3 |
|
Hs, |
1,2 |
1,5 |
1,5 |
2 |
|
2,5 |
2,5 |
3 |
4 |
5 |
7 |
8 |
9 |
10 |
IT2 |
|
HP |
|
|
|
|
|
|
|
|
|
|
|
|
|
|
|
|
|
до 3 |
>3 |
>6 |
>10 |
>18 |
>30 |
>50 |
>80 |
>120 |
>180 |
>250 |
>315 |
>400 |
|
|
|
|
до |
до |
до |
до |
до |
до |
|
||||||||
|
|
|
до 6 |
до10 |
до18 |
до30 |
до50 |
до80 |
120 |
180 |
250 |
315 |
400 |
500 |
|
|
|
Z, Z1 |
10 |
12 |
14 |
16 |
|
19 |
22 |
25 |
28 |
32 |
40 |
45 |
50 |
55 |
|
11 |
Y, Y1 |
0 |
0 |
0 |
0 |
|
0 |
0 |
0 |
0 |
0 |
0 |
0 |
0 |
0 |
|
α, α1 |
0 |
0 |
0 |
0 |
|
0 |
0 |
0 |
0 |
0 |
10 |
15 |
15 |
20 |
|
|
|
H, H1 |
4 |
5 |
6 |
8 |
|
9 |
11 |
13 |
15 |
18 |
20 |
23 |
25 |
27 |
IT4 |
|
Hs |
- |
- |
4 |
5 |
|
6 |
7 |
8 |
10 |
12 |
14 |
16 |
18 |
20 |
IT3 |
|
Hp |
1,2 |
1,5 |
1,5 |
2 |
|
2,5 |
2,5 |
3 |
4 |
5 |
7 |
8 |
9 |
10 |
IT1 |
|
|
до 3 |
>3 |
>6 |
>10 |
>18 |
>30 |
>50 |
>80 |
>120 |
>180 |
>250 |
>315 |
>400 |
|
|
|
|
до |
до |
до |
до |
до |
до |
|
||||||||
|
|
|
до 6 |
до10 |
до18 |
до30 |
до50 |
до80 |
120 |
180 |
250 |
315 |
400 |
500 |
|
|
|
Z, Z1 |
10 |
12 |
14 |
16 |
|
19 |
22 |
25 |
28 |
32 |
45 |
50 |
65 |
70 |
|
12 |
Y, Y1 |
0 |
0 |
0 |
0 |
|
0 |
0 |
0 |
0 |
0 |
0 |
0 |
0 |
0 |
|
α, α1 |
0 |
0 |
0 |
0 |
|
0 |
0 |
0 |
0 |
0 |
15 |
20 |
30 |
35 |
|
|
|
H, H1 |
4 |
5 |
6 |
8 |
|
9 |
11 |
13 |
15 |
18 |
20 |
23 |
25 |
27 |
IT4 |
|
Hs |
- |
- |
4 |
5 |
|
6 |
7 |
8 |
10 |
12 |
14 |
16 |
18 |
20 |
IT3 |
|
Hp |
1,2 |
1,5 |
1,5 |
2 |
|
2,5 |
2,5 |
3 |
4 |
5 |
7 |
8 |
9 |
10 |
IT1 |
|
|
до 3 |
>3 |
>6 |
>10 |
>18 |
>30 |
>50 |
>80 |
>120 |
>180 |
>250 |
>315 |
>400 |
|
|
|
|
до |
до |
до |
до |
до |
до |
|
||||||||
|
|
|
до 6 |
до10 |
до18 |
до30 |
до50 |
до80 |
120 |
180 |
250 |
315 |
400 |
500 |
|
|
|
Z, Z1 |
20 |
24 |
28 |
32 |
|
36 |
42 |
48 |
54 |
60 |
80 |
90 |
100 |
110 |
|
13 |
Y, Y1 |
0 |
0 |
0 |
0 |
|
0 |
0 |
0 |
0 |
0 |
0 |
0 |
0 |
0 |
|
α, α1 |
0 |
0 |
0 |
0 |
|
0 |
0 |
0 |
0 |
0 |
25 |
35 |
45 |
55 |
|
|
|
H, H1 |
10 |
12 |
15 |
18 |
|
21 |
25 |
30 |
35 |
40 |
46 |
52 |
57 |
63 |
IT5 |
|
Hs |
- |
- |
9 |
11 |
|
13 |
16 |
19 |
22 |
25 |
29 |
32 |
36 |
40 |
IT5 |
|
Hp |
2 |
2,5 |
2,5 |
3 |
|
4 |
4 |
5 |
6 |
8 |
10 |
12 |
13 |
15 |
IT2 |