
SML / Лекция_3
.pdf
59
Таблица 3.2 – Температура нагрева кокилей перед заливкой
|
|
Толщина стен- |
Температура на- |
Сплавы |
Характер отливок |
ки отливок, мм |
грева кокиля Тф, |
|
|
|
оС |
Алюминиевые |
Тонкостенные, |
2,2 – 4,0 |
400 – 420 |
|
ребристые; |
5 –10 |
350 – 400 |
|
ребристые корпусные; |
Менее 8 |
250 – 350 |
|
простые без ребер |
Более 8 |
200 – 250 |
|
|
|
|
Магниевые |
Тонкостенные, |
3 – 4 |
350 – 400 |
|
сложные |
|
|
|
Толстостенные |
– |
250 –350 |
|
|
|
|
Медные |
Средней сложности |
5 – 10 |
120 – 200 |
|
|
|
|
Серый чугун |
Разная сложность |
Менее 5 |
400 – 450 |
|
отливок |
5 –10 |
300 – 400 |
|
|
10 – 20 |
250 – 400 |
|
|
20 – 40 |
150 – 250 |
Сталь |
Тонкостенные |
– |
300 |
|
Толстостенные |
– |
150 |
|
|
|
|
вых и неметаллических включений в отливке, если при затвердевании в отлив-
ке не образовались усадочные дефекты (раковины, пористость, трещины), а ее структура и механические свойства соответствуют заданным.
Из теории формирования отливки известно, что эти условия во многом зависят от того, насколько данный технологический процесс обеспечивает вы-
полнение одного из общих принципов получения качественной отливки – ее направленное затвердевание и питание. Направленное затвердевание и питание отливки обеспечивают комплексом мероприятий: конструкцией отливки, ра-
циональным ее расположением в форме, конструкцией литниково-питающей системы, технологическими режимами литья, конструкцией и свойствами ма-
териала формы и т.д.
При литье в кокиль главная из этих особенностей – высокая интенсив-
ность охлаждения расплава и отливки – вызывает затруднения при заполнении
60
формы расплавом и не всегда благоприятно влияет на качество отливок, осо-
бенно чугунных.
Интенсивность теплового взаимодействия между кокилем и расплавом или отливкой можно регулировать. Обычно это достигается созданием опреде-
ленного термического сопротивления на границе контакта отливки (расплава) и
рабочей поверхности полости кокиля. Для этого на поверхность внутренней полости кокиля наносят слой огнеупорной облицовки и краски. Благодаря меньшей по сравнению с металлом кокиля теплопроводности огнеупорного покрытия, между отливкой и кокилем возникает термическое сопротивление,
препятствующее переносу теплоты. Изменяя величину теплопроводности и толщину слоя покрытия, можно регулировать скорость охлаждения отливки, ее структуру, плотность и механические свойства.
Покрытие должно хорошо наноситься и удерживаться на поверхности формы, противостоять резким колебаниям температуры, при нагреве не выде-
лять газов, способных растворяться в металле отливки или создавать на ее по-
верхности газовые раковины.
В состав покрытия входят огнеупорные материалы, связующие, активи-
заторы и стабилизаторы (см. примеры составов в таблице 3.3).
В качестве огнеупорных материалов применяют пылевидный кварц, ша-
мотный порошок, оксиды и карбиды металлов, тальк, графит, асбест.
Связующими для покрытий являются жидкое стекло, огнеупорная глина,
сульфитный щелок.
Активизаторы применяют для улучшения схватывания покрытия с по-
верхностью кокиля. В качестве активизаторов используют для шамотных и ас-
бестовых покрытий тетраборат натрия Na2B4O7·10Н2О (буру) и гидроксид бора В(ОН)3 (борную кислоту H3BO3), для маршаллитовых – кремнефторитый на-
трий Na2SiF6, для тальковых – тетраборат натрия, гидроксид бора или марган-
цевокислый калий.
Стабилизаторы применяют для того, чтобы уменьшить седиментацию
61
Таблица 3.3 – Характеристика отдельных составов, применяемых в качестве
огнеупорных покрытий (красок) кокилей
Матери- |
|
Содержание |
Коэффициент |
|
ал отли- |
Компоненты составов |
компонента, |
теплопроводности, |
|
вок |
масс. % |
Вт/(м·К) |
||
|
||||
|
|
|
|
|
Алюминиевые |
1. Оксид цинка |
15 |
0,41 |
|
сплавы |
Асбест прокаленный |
5 |
|
|
|
(пудра) |
|
|
|
|
Жидкое стекло |
3 |
|
|
|
Вода |
77 |
|
|
|
2*. Асбест прокаленный |
8,7 |
0,27 |
|
|
Мел молотый |
17,5 |
|
|
|
Жидкое стекло |
3,5 |
|
|
|
Вода |
70,3 |
|
|
|
|
|
|
|
Магниевые |
3. Тальк |
18 |
0,39 |
|
сплавы |
Гидроксид бора |
2,5 |
|
|
|
Жидкое стекло |
2,5 |
|
|
|
Вода |
77 |
|
|
Чугун |
4. Пылевидный кварц |
10 – 15 |
0,58 |
|
|
Жидкое стекло |
3 – 5 |
|
|
|
Вода |
87 – 80 |
|
|
|
5*. Молотый шамот |
40 |
0,25 |
|
|
Жидкое стекло |
6 |
|
|
|
Вода |
54 |
|
|
|
Марганцовокислый ка- |
0,05 |
|
|
|
лий (сверх 100%) |
|
|
|
|
|
|
|
|
Сталь |
6. Огнеупорная состав- |
30 – 40 |
0,3 |
|
|
ляющая (циркон, карбо- |
|
|
|
|
рунд, оксид хрома) |
|
|
|
|
Жидкое стекло |
5 – 9 |
|
|
|
Гидроксид бора |
0,7 –0,8 |
|
|
|
Вода |
Остальное (до |
|
|
|
|
плотности |
|
|
|
|
1,1 – 1,22 г/см3) |
|
|
|
|
|
|
* Состав применяют для покрытия поверхности литниковых каналов и вы- поров.
62
(оседание) огнеупорных составляющих покрытия. С этой целью обычно ис-
пользуются поверхностно-активные вещества ОП5, ОП7.
Рассмотрим технологические особенности изготовления отливок из раз-
ных сплавов.
3.3.1 Отливки из цветных сплавов
Отливки из алюминиевых сплавов. Согласно ГОСТ 1583 – 73 литей-
ные алюминиевые сплавы разделены на пять групп (I – V). Наилучшими литей-
ными свойствами обладают сплавы группы I – силумины. Для них характерны хорошая жидкотекучесть, небольшая линейная усадка (0,9 – I %), стойкость к образованию трещин, достаточная герметичность. Силумины марок АЛ2, АЛ4,
АЛ9, АК7, АК9, АК12 широко используют в производстве, однако они склонны к образованию грубой крупнозернистой эвтектики в структуре отливки и рас-
творению газов.
Сплавы группы II (так называемые «медистые силумины») также нередко отливают в кокиль. Эти сплавы, обладающие хорошими литейными свойствами и большей прочностью, чем силумины группы I, менее склонны к образованию газовой пористости в отливках.
Сплавы групп III – V имеют более низкие литейные свойства по сравне-
нию со сплавами групп I и II – пониженную жидкотекучесть, повышенную усадку (до 13%), склонны к образованию трещин, рыхлот и пористости в от-
ливках. Получение отливок из сплавов III—V групп сопряжено со строгим со-
блюдением технологических режимов для обеспечения хорошего заполнения формы и питания отливок при затвердевании.
Все литейные алюминиевые сплавы в жидком состоянии интенсивно рас-
творяют газы и окисляются. При их затвердевании газы выделяются из раство-
ра и образуют газовую и газоусадочную пористость, которая снижает механи-
ческие свойства и герметичность отливок. Образующаяся на поверхности рас-
плава пленка оксидов при заполнении формы может разрушаться и попадать в
63
тело отливки, снижая ее механические свойства и герметичность. При высоких скоростях движения расплава в литниковой системе пленка оксидов, переме-
шиваясь с воздухом, образует пену, которая попадает в полость формы, приво-
дя к образованию дефектов в теле отливки.
Температуру заливки расплава в кокиль назначают в зависимости от хи-
мического состава и свойств сплава, толщины стенки отливки и ее размеров.
Для силуминов типа АЛ2, AJI4, АЛ9 ее принимают о пределах 700 – 750оС, для сплавов с широким интервалом затвердевания, в частности для сплавов типа АЛ19, обладающих пониженной жидкотекучестью, – в пределах 720 – 770оС.
Продолжительность выдержки отливки в кокиле назначают с учетом ее размеров и массы. Обычно отливки охлаждают в форме до температуры около
400оС.
Отливки из магниевых сплавов. Магниевые литейные сплавы по срав-
нению с алюминиевыми обладают худшими литейными свойствами. Они обла-
дают пониженной жидкотекучестью, большой усадкой (3,2 – 1,5%), склонно-
стью к образованию горячих трещин, пониженной герметичностью, высокой склонностью к окислению в жидком и твердом состояниях, способностью вос-
пламеняться в жидком состоянии. Магниевые сплавы имеют большой интервал кристаллизации, склонны к растворению газов и поэтому в отливках часто об-
разуются микрорыхлоты. Отливки из магниевых сплавов склонны к коробле-
нию при затвердевании и термической обработке.
Наибольшее применение для литья в кокиль нашли сплавы марок МЛ5 и
МЛ6 (системы Mg – Al – Zn), сплав МЛ12 (системы Mg – Zn – Zr) и МЛ10 (сис-
темы Mg – Nd – Zr).
Температура заливки магниевых сплавов зависит от их химического со-
става и обычно на 100 – 150оС превышает температуру ликвидуса, что вызвано пониженной жидкотекучестью этих сплавов. Обычно температура заливки со-
ставляет 700 – 750оС для тонкостенных отливок и 650 – 700оС для массивных и толстостенных отливок.
Отливки из медных сплавов. Литьем в кокиль изготовляют отливки из
64
латуней, бронз, а также из чистой меди.
Латуни обычно имеют небольшой интервал кристаллизации, хорошую жидкотекучесть, но большую усадку (1,5 – 2,5%). Латуни мало склонны к обра-
зованию усадочной пористости, но интенсивно растворяют водород. Эта осо-
бенность всех медных сплавов наиболее сильно проявляется у кремнистых ла-
туней, отливки из которых часто поражаются газовой пористостью.
Бронзы оловянные имеют хорошую жидкотекучесть, повышенную усадку
(1,4 – 1,6%), большой интервал кристаллизации, а потому и повышенную склонность к образованию усадочной пористости в отливках. Алюминиевые бронзы имеют небольшой интервал кристаллизации, большую усадку (1,7 – 2,5 %). Отливки из них получаются плотными, но эти сплавы склонны к образова-
нию оксидных плен из-за повышенной окисляемости содержащегося в них алюминия. Плены, попадающие в тело отливки, снижают механические свой-
ства и герметичность изделий из алюминиевых бронз. Кремнистые бронзы,
аналогично кремнистым латуням, склонны к образованию газовой пористости.
Свинцовые бронзы склонны к ликвации, ухудшающей свойства отливок.
Отливки из медных сплавов при литье в кокиль часто поражены трещи-
нами. Это затрудняет получение в кокилях сложных тонкостенных отливок.
Главный способ предупреждения этих дефектов – хорошее раскисление и ра-
финирование сплавов от шлаковых включений, увеличивающих склонность сплавов к образованию трещин.
Температура заливки медных сплавов выбирается в зависимости от их химического состава и конфигурации отливки. Для отдельных сплавов темпе-
ратура заливки составляет, оС: оловянные бронзы – 1150 – 1200; алюминиевые бронзы – 1100 – 1150; кремнистые латуни – 1000 – 1050; свинцовые латуни –
1000 – 1100. При этом массивные отливки заливают при температурах близких к нижнему пределу, а тонкостенные – к верхнему.
Дефекты отливок из цветных сплавов и методы их предупреждения.
Общими характерными дефектами отливок при литье в кокиль являются:
1) недоливы и неслитины при низкой температуре расплава и кокиля пе-
65
ред заливкой, недостаточной скорости заливки, большой газотворности стерж-
ней и красок, плохой вентиляции кокиля; 2) усадочные дефекты (раковины, утяжины, пористость, трещины) из-за
недостаточного питания массивных узлов отливки, чрезмерно высокой темпе-
ратуры расплава и кокиля, местного перегрева кокиля, нерациональной конст-
рукции литниковой системы; 3) трещины вследствие несвоевременного подрыва металлического
стержня или вставки, высокой температуры заливки, нетехнологичной конст-
рукции отливки; 4) шлаковые включения при использовании загрязненных шихтовых ма-
териалов, недостаточном рафинировании сплава перед заливкой, неправильной работе литниковой системы;
5) газовая пористость при нарушении хода плавки (использовании за-
грязненных влагой и маслом шихт, чрезмерно высокого перегрева, недостаточ-
ного рафинирования или раскисления сплава).
Специфические дефекты отливок из магниевых сплавов – это дефекты усадочного происхождения (пористость, трещины, рыхлоты), обусловленные широким температурным интервалом их затвердевания. Для устранения этих дефектов требуется доводка и точное соблюдение технологических режимов – температуры расплава и кокиля, применение краски и др. Часто отливки из магниевых сплавов из-за плохой работы литниковой системы поражены шла-
ковыми включениями, что приводит к коррозии отливки при ее эксплуатации и хранении. Такие дефекты устраняют тщательной доводкой литниковой систе-
мы.
Специфическими дефектами отливок из медных сплавов являются: газо-
вая пористость при плохом рафинировании и очистке сплава от шлаковых час-
тиц, вторичные оксидные плены при литье алюминиевых бронз вследствие разделения потока расплава на струи и окисления его в форме, трещины из-за плохого раскисления сплавов при плавке.
66
3.3.2 Отливки из чугуна
Серые чугуны обладают хорошими литейными свойствами: высокой жидкотекучестью, небольшой усадкой (до 1 %), незначительным влиянием га-
зосодержания на механические свойства, достаточно высоким сопротивлением образованию горячих трещин, малой склонностью к образованию усадочных раковин и пористости. Литейные свойства чугуна существенно зависят от его химического состава. С увеличением содержания углерода жидкотекучесть до-
эвтектических чугунов повышается, а заэтектических уменьшается. При увели-
чении содержания кремния и фосфора жидкотекучесть чугуна повышается,
влияние марганца и серы на жидкотекучесть металла несущественно.
Линейная усадка чугунов зависит от химического состава и скорости ох-
лаждения: перлито-ферритные чугуны со структурой (П+Ф+Гр) имеют усадку
0,7 – 0,9, перлитные – 1,1 – 1,15, белые – 1,65 –1,75%.
Трещиноустойчивость чугунов возрастает с повышением содержания уг-
лерода и кремния; увеличение содержания серы снижает трещиноустойчивость чугунов; увеличение содержания марганца до 0,9% повышает трещиноустой-
чивость, а при дальнейшем увеличении его содержания вероятность появления трещин возрастает. Опасность появления трещин резко возрастает при наличии в чугуне более 0,2% фосфора.
Чугунные отливки, полученные в кокилях, меньше поражены газовыми раковинами, чем отливки, полученные в песчаных формах, так как вследствие высокой скорости охлаждения металла в кокилях газы не успевают выделяться из расплава. Однако неправильная конструкция вентиляционной и литниковой систем, нарушения при окраске кокилей и подготовке расплава повышают ве-
роятность образования газовых дефектов в отливке.
Чугун в большей степени, чем другие сплавы, способен изменять струк-
туру в зависимости от скорости охлаждения и затвердевания отливки. Поэтому,
управляя скоростью охлаждения чугуна, можно получать отливки с любой структурой. Большое влияние на структуру чугуна оказывает также его хими-
67
ческий состав. В свою очередь, от структуры чугуна зависят механические свойства, износостойкость, герметичность, обрабатываемость отливки. Повы-
шение скорости охлаждения отливки при литье в кокиль приводит к уменьше-
нию количества и размеров графитных включений, к увеличению содержания перлита и уменьшению его зерна, что повышает механические и другие слу-
жебные свойства отливок.
Однако высокая скорость охлаждения может привести к образованию от-
беленного поверхностного слоя в отливке. В этом слое углерод почти полно-
стью находится в виде цементита (Fe3C), определяющего высокую твердость структуры. В результате отливки с отбеленной поверхностью трудно обраба-
тываются, но обладают высокой износостойкостью. Обычно их применяют без механической обработки или после шлифования. Примером могут служить ме-
лющие тела для дробильно-размольного оборудования, валки для прокатки ме-
таллов и др. Чугунные отливки с отбеленным поверхностный слоем, которые необходимо подвергать обработке резанием, предварительно термически обра-
батывают – подвергают графитизирующему отжигу для устранения отбела.
Для отжига отливок требуется дополнительное оборудование. Он сопря-
жен с энергетическими затратами, а также увеличивает длительность техноло-
гического цикла. По этой причине получение в кокилях отливок из чугуна с за-
данной структурой является одной из важнейших проблем данного способа ли-
тья.
Исследования и производственный опыт показывают, что основными на-
правлениями решения этой проблемы являются: правильный выбор химическо-
го состава чугуна и способов его модифицирования; снижение скорости охла-
ждения чугуна путем повышения начальной температуры кокиля, нанесения на его поверхность облицовок и красок, создающих термические сопротивления переносу теплоты от отливки к кокилю.
Для предотвращения отбела повышают содержание углерода и кремния в чугуне. Однако содержание кремния не должно быть выше 2,5%, так как иначе снижается жидкотекучесть чугуна и в структуре отливок появляются силико-
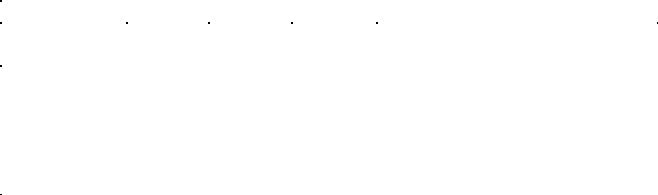
68
карбиды. Уменьшение глубины отбела может быть достигнуто модифицирова-
нием чугуна ферросилицием, силикокальцием. Наилучшими являются ком-
плексные модификаторы, вводимые в состав чугуна в количестве 0,2 – 0,3 мас. %, например, модификатор марки ФЦМ5. Составы чугунов, рекомендуемых для литья в кокиль, и режимы модифицирования приведены в таблице 3.4.
Таблица 3.4 – Химический состав серого чугуна, мас. % (остальное – Fe), реко-
мендуемый для кокильного литья
Характери- |
|
|
|
S |
|
Р |
|
стика отли- |
С |
Si |
Mn |
не более |
Модификатор |
||
вок |
|
|
|
|
|
|
|
Тонкостен- |
|
|
|
|
|
|
До 0,05 |
ные ребри- |
|
|
|
|
|
|
ФЦМ5 |
стые, отжи- |
3,6 – 3,7 |
2,1 – 2,3 |
0,4 – 0,5 |
0,1 |
|
0,05 |
|
гаемые на |
|
|
|||||
|
|
|
|
|
|
|
|
феррит |
|
|
|
|
|
|
|
|
|
|
|
|
|
|
|
Машино- |
|
|
|
|
|
|
0,2 AI |
строитель- |
|
|
|
|
|
|
(0,2 Аl и 0,3 |
ные (без от- |
3,5 – 3,7 |
2,0 – 2,2 |
0,5 – 0,9 |
0,06 |
|
0,12 |
ФС75) |
бела) |
|
|
|
|
|
|
|
|
|
|
|
|
|
|
|
Температура заливки чугуна в кокиль обычно составляет 1300 – 1350оС.
При более высоких температурах заливки снижается стойкость кокиля. Темпе-
ратуры заливки назначают в зависимости от толщины стенки отливки.
Температура выбивки отливки из кокиля обычно находится в пределах
600 – 1000оС.
Отжиг для устранения отбела обычно состоит в нагреве отливок до 850 – 950оС, выдержке 2 – 4 часа и охлаждении на воздухе. Для уменьшения внут-
ренних напряжений отливки нагревают до 500 – 600оС и после выдержки при температуре нагрева в течение 2 – 8 часов (в зависимости от толщины стенки и массы отливки) их охлаждают с печью со скоростью 20 – 50оС/ч до 250оС.
Дефекты отливок и меры их предупреждения. Наиболее характерными