
Поъемно-транспортные машины
.pdf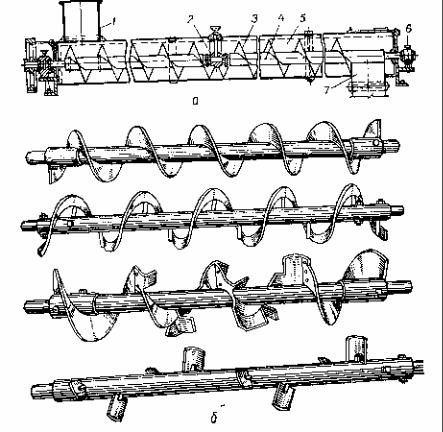
Привод аналогичен приводам цепного транспортера кроме всего снабжается электротормозом и остановом (роликовым или храповым).
ЛЕКЦИЯ 15
ТРАНСПОРТИРУЮЩИЕ МАШИНЫ БЕЗ ТЯГОВОГО ОРГАНА
1.Винтовые конвейеры (шпеки) применяются для транспортирования сыпучих, мелкокусковых материалов, вязких и тестообразных (мокрой глины, бетонной смеси и т.п.) в горизонтальном и наклонном положении до 20 на расстояние до 40 метров.
Производительность винтовых транспортеров в среднем 20 ÷40м3 / час, но при
больших размерах винта может быть доведена до 100 м3 /час.
Достоинства - компактность, герметичность, возможность транспортировать мокрые и тестообразные материалы.
Недостатки - сильный износ поверхности винта и желоба; повышенный удельный расход электроэнергии; измельчение материала при транспортировании.
Рис. 29 Винтовой конвейер: а – схема конвейера; б – винты (сверху вниз): сплошной, ленточный, фасонный и лопастный
Винтовой конвейер состоит из корпуса 5 с загрузочной воронкой 1 и загрузочным патрубком 7. Внутри корпуса размещается винт 3, вращающийся в подшипнике 2 и подпятнике 6.
80
Винты транспортеров
Основные параметры винтовых транспортеров общего назначения стандартизованы.
Диаметр винтов - 150; 200; 250; 300; 400; 500; 600 по ГОСТ 2037-43, мм.
Число заходов спирали - одно- и многозаходные (обычно двухзаходные).
Конструкция винта
К достоинствам винтовых конвейеров относятся простота конструкции и несложность ухода за ними, небольшие размеры в поперечном сечении, удобство промежуточной разгрузки и возможность полной герметизации, что особенно важно для пылящих грузов. Однако значительное трение материала о винт и желоб приводит к сильному износу конвейера, а также к измельчению транспортируемого материала и высокому удельному расходу энергии.
а) Сплошной винт - хорошо сыпучие материалы (цемент, песок, мел, гипс и др. гранулированные материалы).
ϕ = 0,25 ÷0,45 - коэффициент наполнения желоба и
w = 50 ÷120 - угловая скорость винта.
б) Ленточный винт - перемещение кусковых материалов - крупный гравий, песчаник, известняк и т.п., при ϕ = 0,25 ÷0,40 и n = 40 ÷100 об/мин.
в) Фасонный винт - перемещение тестообразных, слеживающихся и мокрых материалов (мокрая глина, бетон, цементный раствор), при ϕ = 0,15 ÷0,3; n = 30 ÷60 об/мин.
г) Лопастной винт |
- перемещение |
кусковых материалов и тестообразных, |
|
соответственно при ϕ = 0,25 ÷0,40 |
с n = 40 ÷100 об/мин |
||
ϕ = 0,15 |
÷0,30 |
с n = 30 ÷60 |
об/мин. |
Винты наибольшего диаметра, работающие с абразивным материалом изготавливаются либо литые чугунные с отбеленной поверхностью либо как и большие винты - из трубы, с приваренной к ней профильной заготовкой или лопастями из 3 ÷6 мм листового металла.
Шаг винта
tB =πDB tgα =ξDB
Здесь: α -угол наклона винтовой линии (угол подъема); ξ - коэффициент, учитывающий угол подъема винтовой линии;
Например: При α =14 ÷18o ; ξ = 0.8 ÷1.0 ;
обычно tB = (0.5 ÷1.0)DB ; причем чем легче материал тем tB больше.
Опоры винта
Вал винта через каждые 2,5 ÷3,0 м поддерживаются подшипниками, укрепленными в верхней части желоба и состоит из отдельных участков аналогичной длины соединенных муфтами.
Вал для восприятия осевого усилия имеет подшипник. Привод конвейера обычного
типа.
Расчет винтовых конвейеров.
1. Площадь заполнения желоба транспортера.
S=ϕ πD4 2 см2
2.Производительность транспортера:
Q = 3600Sγv т/час
81
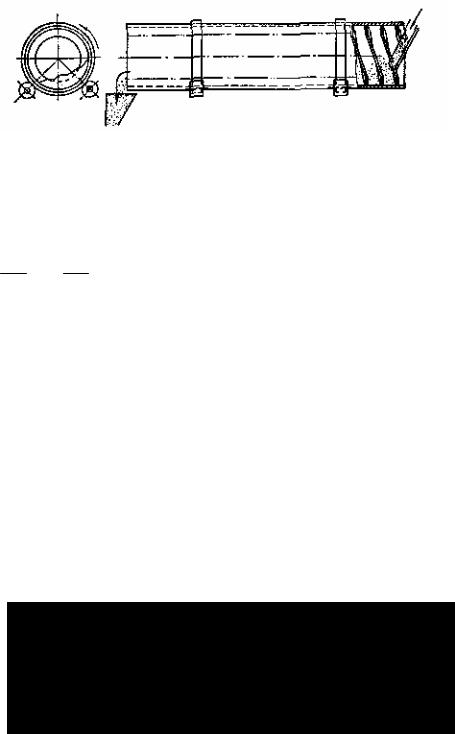
при: v = 60tn м\сек.
Q = 3600ϕ πD4 2 γ 60tn = 47ϕγtnD2
4. Потребная мощность на валу винта: а) для горизонтального транспортера
N Г = Сo 367QL квт;
Co - коэффициент сопротивления материала о желоб зависит от кусковатости,
абразивности, текучести и т.п. свойств материала;
Например: Для антрацита, каменной соли, орешкового угля и т.п. Co =2,5; Для извести, песка, цемента и т.п. Co = 4.
5) для наклонного транспортера
N H = QH367 +Co 367QL
Все остальное определяется обычным путем.
Транспортирующие трубы
Разновидность винтовых транспортеров. Внутренняя поверхность гладкая со спиралью из полосовой стали. Устанавливаются трубы на опорных роликах горизонтально
или под углом не более 3 ÷5o .
Загрузка и разгрузка производится с концов трубы. Число оборотов трубы должно быть настолько малым, чтобы материал не вращался вместе с трубой.
Высота гребня спирали
ϕ = 0.2 ÷0.3;
b = (0.2 ÷0.3)Dтр ;
Вращающиеся транспортирующие трубы (рис. 30) имеют на внутренней поверхности винтовые лопасти и применяются обычно в качестве технологического оборудования для сушки и охлаждения различных материалов, а также для других операций. Материал загружается у одного конца трубы и, постепенно
Рис. 30. Схема транспортирующей трубы с винтовой полкой
перемещаясь по ней, выгружается — у другого.
Скорость вращения трубы ограничена условием: материал не должен вращаться вместе с трубой. Для этого центробежные силы должны быть меньше сил тяжести:
mw2 r < mg,
(273)
w2 r < g, w = π30n - угловая скорость;
82

r = D2 - радиус трубы;
g = 9.81 м/сек2 - ускорение силы тяжести.
Из условия (273) находим:
n = 42D
Приближенно принимают
n ≈ (20 ÷30)D1
Диаметр трубы находится в пределах от 400 до 1000 мм. Высота винта лопасти - около 0,ЗD , а шаг лопастей S ≈ 0.5D .
Роликовые транспортеры
Различают неприводные роликовые транспортеры и приводные. Неприводные роликовые транспортеры:
Относятся к гравитационным устройствам, в которых наклонная плоскость образована рядом роликов установленных в раме.
Рис. 31
Обычно рольганги собираются из отдельных секций с L =2 ÷3 метра. Предназначены для перемещения штучных грузов.
При этом:
1. Шаг установки роликов: t p ≤ lгр
2. Полная сила сопротивления движению груза, весомQ :
F = F1 + F2 + F3 ;
Здесь:
а) сопротивление от сил трения в цапфах роликов, приведенное к наружному диаметру роликов:
F1 = (Q cos β +Gi)f Dd , кг;
Здесь: G - собственный вес ролика;
i - число роликов, на которых лежит груз;
f - коэффициент трения в подшипнике ролика;
d - диаметр цапфы ролика; D - диаметр ролика.
б) сопротивление качению груза по роликам:
F2 = Q cos β 2Dµ , Н;
Здесь: µ - коэффициент трения качения в см;
в) сопротивление, возникающее вследствие скольжения груза по роликам, и кинетическую энергию, сообщаемую роликам:
83

V 2 i
F3 =ψG gLH cos β , Н;
Здесь: ψ = 0,8 ÷0,9 - коэффициент, учитывающий что не вся масса ролика расположена на окружности диаметра;
VH - номинальная окружная скорость вращения ролика;
L - длина рольганга. Полная сила сопротивления:
F = F |
+ F |
+ F |
= |
Q cos β |
(fd + 2µ)+ψ |
GVH2 i |
cos β +Gif |
d |
, Н |
|
|
|
|||||||
1 |
2 |
3 |
|
D |
|
gL |
|
D |
|
|
|
|
|
|
|
При установившемся движении момент движущей силы = моменту сопротивления,
т.е.
|
|
|
|
|
Q cos β |
D |
|
= F |
D |
; |
|
|
|
|
|
|
|
||
|
|
|
|
|
2 |
|
|
|
|
|
|
|
|
||||||
|
отсюда: |
|
|
|
|
|
2 |
|
|
|
|
|
|
|
|
|
|||
|
|
|
|
|
|
|
|
|
|
|
|
|
|
|
|
|
|
||
|
F |
|
|
|
|
|
|
|
|
|
|
|
|
2 |
|
|
|
||
|
|
|
|
|
|
1 |
|
|
|
|
Gi |
|
d |
|
|||||
tgβ = |
, т.к. β = 2 |
÷7 |
o |
; а cos β ≈1; то: tgβ = |
(fd |
+ 2µ)+ |
QH |
+ f |
; |
||||||||||
|
|
|
|
|
ψ |
|
|
|
|||||||||||
|
Q cos β |
|
|
|
|
|
|
D |
|
|
|
|
Q |
gL |
|
D |
|
Но, если грузы на рольгангу следуют один за другим к ролики вращаются с n = const , работа груза, затрачиваемая на преодоление сопротивления скольжения груза по роликам и придание кинетической энергии роликам становится равной нулю, то:
|
1 |
|
|
G |
i |
|
|
tgβ = |
|
|
|
+ |
|
|
|
|
|
|
|
||||
|
2µ + fd 1 |
|
|
; |
|||
|
D |
|
|
Q |
т.к. F3 = 0;
Т.о. определяют угол наклона рольганга.
Приводные роликовые транспортеры
Широко применяются в ряде отраслей промышленности, особенно в металлургической (прокатные цехи).
Привод роликов может быть индивидуальным и групповым. Расчет ведется аналогично расчету неприводных рольгангов. При этом β = 0.
Затем по F определяют необходимую мощность двигателя и других агрегатов.
ЛЕКЦИЯ 16
ИНЕРЦИОННЫЕ ТРАНСПОРТЕРЫ
К группе инерционных транспортеров относятся качающиеся транспортеры и вибрационные транспортеры.
Качающиеся транспортеры
1 тип: Качающиеся транспортеры с возвратно поступательным движением желоба и постоянным давлением материала на желоб.
84
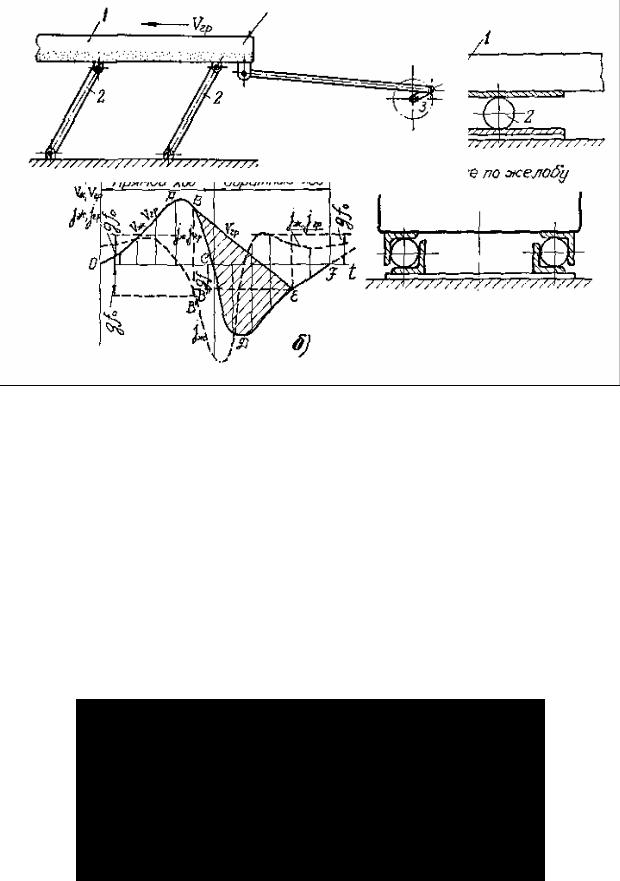
Рис. 32. схема – а и диаграмма - б движения желоба и материала на качающемся конвейере с шариковыми опорами и постоянным давлением груза на желоб
Число колебаний таких конвейеров находится в пределах 50 ÷100 кол/мин. и амплитуде колебаний 100 ÷300 см.
Прямолинейное движение желоба получаем при установке его на направляющих скольжения и качения от кривошипно-шатунного механизма. За счет постепенного изменения скорости, свойственного этим механизмам, материал увлекается вперед за счет сил трения материала о желоб и приобретает некоторое ускорение.
При ходе назад, желоб проскальзывает под материалом, продолжающим за счет сил инерции движение вперед.
При этом, если считать толщину слоя материала в желобе постоянной, давление на желоб на протяжении всего цикла остается постоянным.
Износ желоба при этом довольно значителен.
Ширина желоба принимается в пределах В = 200 ÷1200 мм; h = 8 ÷200 мм – высота. Качающиеся конвейера с возвратно-замкнутым криволинейным движением желоба и
переменным давлением материала на желоб:
Рис. 33. Схема качающегося конвейера с переменным давлением груза на желоб
Число колебаний таких конвейеров находится в пределах 800 ÷500 кол/мин, при амплитуде колебаний =10 ÷40мм.,
85

Криволинейное движение желоба возможно при установке его на упругих, наклонных
под углом r = 20 ÷30o к вертикальным стойкам, соединенных со стационарной или подвесной рамой, а так же при вертикальной подвеске желоба.
При одновременном ходе желоба вперед и вверх с ускорением, нормальная составляющая силы инерции повышает давление материала нижнюю стенку желоба.
При обратном ходе желоб отрывается от материала, вследствие чего, давление на желоб уменьшается. Материал за цикл совершает микрополет на величину амплитуды колебаний желоба.
Длина качающихся конвейеров
L ≤ 50 м; Q ≤ 400 т/час.
Вибрационные конвейера
Имеют высокую частоту колебаний при малой амплитуде w ≤ 3000 кол/мин. (частота круговых колебаний) r = 0.5 ÷1.5 мм.
Колебания создаются с помощью электромагнитных, эксцентриковых или грузовых вибраторов.
Желобом вибрационных конвейеров обыкновенно являются трубы.
Электровибраторы - крепятся к трубам снизу под углом 20 ÷30o к оси желоба через каждые 2 ÷2,5м. Корпус вибратора подвешивают на пружинных опорах.
Dтр = 350 ÷750 мм; Q = 50 ÷150 т\час.
Механические эксцентриновые вибраторы
Применяют в основном на опорных конвейерах с =150 ÷100 м, с = 400 т/час.
При этом радиус кривошипа выбирается весьма малым по сравнению с длиной шатуна и длиной опорных стержней, поэтому закон изменения скорости весьма близок к синусоидальному, а само движение желоба можно рассматривать как прямолинейное.
Вследствие синусоидального изменения скорости желоба ускорение, сообщаемое материалу изменяется по косинусоидальному закону.
При достаточно большом числе оборотов вертикальная составляющая ускорения оказывается больше ускорения силы тяжести материала и он совершает микрополет по параболе.
При этом груз не крошится, не пылит и практически не изнашивает желоба.
Грузовые вибраторы
При вращении грузов продольные составляющие центробежных сил придают трубе колебательное движение. Сечения труб могут быть самыми различными по форме
Производительность качающихся и вибрационных конвейеров.
Q = 3600FVψγ т/час
V - скорость движения материала;
для качающихся V = 0.1 ÷0.2 м/сек
для вибрационных V = 0.2 ÷0.3 м/сек.
ψ- коэффициент заполнения желоба;
ψ= 0.5 ÷0.6 - для качающихся и вибрационных с трубами круглого сечения;
ψ= 0.6 ÷0.8 - для вибрационных с открытыми желобами и прямоугольными трубами. Максимальное число оборотов кривошипа качающегося конвейера
nmax = 30 rкрtg1 α об\мин.
86

Здесь: rкр - радиус кривошипа;
α = 20 ÷30о - угол наклона стоек.
Скорость движения груза по качающемуся конвейеру:
V = 0.23nrfдtgα м\сек.
fд -коэффициент трения материала о стенку желоба в движении:
fд = 0,7 f ;
Мощность электропривода:
= QL(w +sin β)
N k3 367η квт;
Здесь: k3 =1.2 ÷1.25 - коэффициент запаса мощности;
w - коэффициент сопротивлений = 6 ÷10 ; β - угол наклона конвейера;
η = 0.8 ÷0.9 - КПД привода.
Пневматические и гидравлические транспортные устройства
Пневматические устройства. Работа этих устройств основана на способности перемещения сыпучих и штучных грузов (I) в потоке воздуха или (II) под давлением воздуха за счет создания разности давлений на концах трубопровода.
Достоинства ПТУ - герметичность, исключение потерь и выделений пыли, возможность перемещения грузов по сложным трассам, высокая производительность, большие расстояния перемещения, возможность полной автоматизации транспортных операций.
Производительность действующих установок I типа достигает до Q ≤ 300 т/час при
L= 1800 м и H ≤ 50 м
По способу создания разности давлений ПТУ I типа делятся на:
1.Всасывающие - разрежение в системе создается вакуум-насосом. Воздух вместе с материалом всасывается через сопла и по трубопроводу поступает в циклон – разгрузитель. Воздух после очистки, поступает в атмосферу.
2.Нагнетательные - давление в системе создается компрессором до 10 атм. В движущуюся струю воздуха через питатели подаются материалы. Разгрузка аналогичная.
3.Смешанна - забор материала по всасывающей системе, движение по нагнетательной, разгрузка обычная.
Недостатки - высокий расход энергии 1 ÷4 квтчас/т, что в 10 ÷15 раз превышает расход анергии на трансп. механ. путем.
Аэрация - насыщение воздухом сухих пылевидных материалов, вследствие чего они приобретают свойство текучести. Аэрацию производят в специальных желобах.
Желоб имеет весьма малый уклон = 0,04 ÷0,05. Позволяет создать простые и дешевые транспортирующие устройства. Расход воздуха 100 ÷100 м3/час на 1 м2 пористой перегородки.
Недостаток - невозможность транспортирования по уклону вверх.
Гидравлическое транспортирование материалов
Применяется в горнодобывающей промышленности для перемещения полезных ископаемых и породы, на обогатительных фабриках (подача сырья, удаление хвостов), в грануляционных, установках.
Достоинства - простота устройства, возможность непрерывного перемещения материала с одновременной его промывкой и охлаждением, высокая производительность, герметичность системы и отсутствие потерь.
87
Недостатки - большой расход воды, высокая энергоемкость, сложное обезвоживающее хозяйство, износ трубопроводов и насосов.
Применяются следующие схемы транспортирования:
1.Самотечные (низконапорные) - пульпа перемещается по желобу с уклоном 0,02 ÷0,06. На поворотах трассы, для увеличения скорости движения крупных кусков, устанавливаются сопла из которых вода подается под давлением 10 атм. Рабочие участки желобов футеруются износостойкими плитками (чугун, базальт).
2.Высоконапорные- 1 вариант - пульпа образуется в приемном устройстве и по трубам, всасывающая землесосом подается к месту назначения. Давление - 25 ÷60 атм.
2 вариант – в струю воды при помощи питателей подается сухой материал. Далее схема аналогичная.
3.Смешанная схема - в пределах цеха пульпа перемещается по желобу и попадает в приемник гидроэлеватора (эжекторного типа). В напорное сопло гидроэлеватора насосом высокого давления подается вода, которая вместе с пульпой проходит через диффузор в трубу.
Основные элементы устройств пневмотранспорта:
1)нагнетательный вентилятор, воздуходувки, компрессор или всасывающий экгаустер;
2)транспортные трубопроводы и их элементы (отводы, тройники, колена и пр.);
3)загрузочные устройства: питатели, шлюзовые затворы, всасывающие сопла, инжекционные воронки;
4)отделители (разгружатели): циклоны, осадочные камеры и пр.;
5)фильтры: центробежные, рукавные матерчатые, мокрые, электрические и др.;
6)аппаратура для дистанционного управления. Трубопроводы бывают круглые диаметром 25—100 мм и эллиптические с наибольшим сечением 250X400 мм.
88
ЛИТЕРАТУРА
Основная
1.Александров М.П. Подъемно-транспортные машины. – М.:Высшая школа, 1972г.
2.Парницкий А.Б., Шабашов А.П. Мостовые краны общего назначения. – М.: Машгиз, 1963 г.
3.Курсовое проэктирование грузоподъемных машин /Руденко Н.Ф., Александров М.П., Лысяков А.Г./ - М.: Машгиз, 1963 г.
Дополнительная
1.Расчеты грузоподъемных машин и транспортирующих машин /Иванченко Ф.К., Бондарев В.С., Колесник Н.П., Барабанов В.Я./ - Киев.: Вища школа, 1975г.
2.Иванченко Ф.К. Конструкция и расчет подъемно–транспортных машин. – Киев.: Вища школа, 1983 г.
89