
мальной высоты h, однако необходимо учитывать возможность её установки на выбранном станке. Например, на станке мод. 16К20 невозможно установить державку высотой более 25 мм.
ВЫБОР РЕЖИМОВ РЕЗАНИЯ. Для каждой СМП в каталогах Sandvik Coromant и Walter указывается диапазон глубин и подач, при которых обеспечивается удовлетворительное стружколомание. Если величина припуска превышает максимальную глубину резания для выбранной СМП, то его необходимо снимать за несколько рабочих ходов.
Определение скорости резания осуществляется двумя способами.
1.Выбор в соответствии с рекомендациями, представленными в [2, 3]. Табличные значения скорости резания соответствуют стойкости инструмента, равной 15 мин, и условной твёрдости той группы обрабатываемых материалов, в которую входит материал заготовки. Например, для нелегированных сталей с содержанием углерода C = 0,55 – 0,80% (группа Р, СМС 01.3) условная твердость равна НВ 170 (приложение 1). В случае задания иного периода стойкости выбранную скорость резания необходимо умножить на коэффициент коррекции (приложение 2). Если твёрдость материала заготовки отличается от условной, выбранную скорость резания также необходимо скорректировать (приложение 3).
2.Расчет с помощью специальных программ [6, 8]. На сайте [6] можно осуществить копирование чертёжа выбранного инструмента, а также его 3D модели.
2. ТИПОВОЙ АЛГОРИТМ ВЫБОРА СВЕРЛ
ОПРЕДЕЛЕНИЕ ГРУППЫ, К КОТОРОЙ ОТНОСИТСЯ ОБРАБАТЫВАЕМЫЙ МАТЕРИАЛ СОГЛАСНО СТАНДАРТУ ISO, И ПОДГРУППЫ СОГЛАСНО КЛАССИФИКАЦИИ SANDVIK COROMANT осуществляется так
же, как и при выборе токарного инструмента (приложение 1).
12
ОПРЕДЕЛЕНИЕ УСЛОВИЙ ОБРАБОТКИ осуществляется так же, как
и при выборе токарного инструмента (п. 1).
На этом этапе выбора инструмента для сверления необходимо решить, какое сверло целесообразнее использовать: цельное, составное (сверло с напаянными режущими пластинами) или сборное (сверло с СМП). При этом определяющими фак-
торами являются диаметр и длина обрабатываемого отверстия.
Цельные и составные сверла работают на низких скоростях резания с повышенными подачами, так как имеют две режущие кромки. Они превосходят сборные конструкции по производительности, однако инструментальные расходы выше.
Сборные сверла применяют при высоких скоростях резания с низкими подачами. Это означает, что они будут работать с большой производительностью только на высокоскоростном оборудовании. Сверла с СМП более универсальны и надежны. Кроме того, себестоимость отверстий, полученных ими, ниже, что особенно существенно для мелкосерийного производства.
Вдиапазоне отверстий средних диаметров (d = 10…30 мм) возможно применение как составных сверл, так и сборных. Составные сверла позволяют получить более качественные отверстия как в отношении точности, так и в отношение шероховатости поверхности.
Вслучаях когда поверхность заготовки не перпендикулярна оси сверла, а также при рассверливании отверстий или при сверлении перпендикулярных отверстий, рекомендуется выбирать сборные свёрла. Их применение снизит себестоимость изготовления одной детали за счет сокращения времени простоев, поскольку легче поменять пластину на сверле, чем перетачивать само сверло. Эта экономия особенно важна при массовом производстве.
ВЫБОР ТИПА ХВОСТОВИКА. Многие типы сверл выполняются с различными хвостовиками. Выберите тип хвостовика, соответствую-
13

щий оборудованию, на котором будет производиться сверление. Тип хвостовика указывается на страницах с таблицами размеров свёрл.
В таблицах размеров сборных свёрл указаны начальные символы кодов устанавливаемых пластин. В большинство сборных сверл устанавливают несколько пластин (2 – 4). Центральная и периферийная пластины в большинстве случаев не являются взаимозаменяемыми. Для каждой из них необходимо выбрать геометрию передней поверхности и инструментальный материал.
Геометрия СМП, как правило, определяет форму стружколома, наличие и размер отрицательной фаски на передней поверхности, величину заднего угла и др. Стружколомы фирмы Sandvik Coromant кодируются, как правило, двумя буквами. Примеры различных геомет-
рий СМП для сверл CoroDrill 880 (фирма Sandvik Coromant) приведе-
ны на рис. 2.1. Геометрия LM оптимизирована для обработки длинностружечных материалов (см. рис. 2.1, а); геометрия MS – для обработки материалов группы M (см. рис. 2.1, б); геометрия GM предназначена для работы в хороших условиях обработки (см. рис. 2.1, в); геометрия GR – для средних условий (см. рис. 2.1, г); геометрия GT – для тяжёлых условий (см. рис. 2.1, д).
а |
б |
в |
г |
д |
Р и с. 2.1. Стружколомы сверла CoroDrill 880 (фирма Sandvik Coromant)
Стружколомы фирмы Walter кодируются, как правило, одной буквой и двумя цифрами (рис. 2.2). Коды стружколомов СМП указываются в конце их обозначений.
14
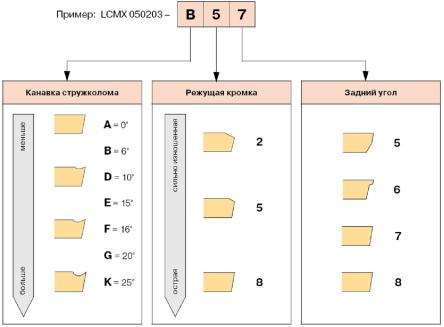
Р и с. 2.2. Примеры стружколомов сборных свёрл фирмы Walter
ВЫБОР ИНСТРУМЕНТАЛЬНОГО МАТЕРИАЛА. Основные марки ин-
струментальных материалов, из которых могут быть изготовлены цельные и составные свёрла, содержатся в соответствующих таблицах размеров. Для сборных свёрл основные марки инструментальных материалов представлены в таблицах с кодами и размерами пластин. Для выбора инструментального материала можно воспользоваться шкалами условной тяжести обработки, которые были описаны ранее (п. 1).
ОПРЕДЕЛЕНИЕ РЕЖИМОВ РЕЗАНИЯ осуществляется описанными
ранее способами для токарного инструмента (п. 1).
3. ТИПОВОЙ АЛГОРИТМ ВЫБОРА ФРЕЗ
ОПРЕДЕЛЕНИЕ ГРУППЫ, К КОТОРОЙ ОТНОСИТСЯ ОБРАБАТЫВАЕМЫЙ МАТЕРИАЛ СОГЛАСНО СТАНДАРТУ ISO, И ПОДГРУППЫ СОГЛАСНО КЛАССИФИКАЦИИ SANDVIK COROMANT осуществляется так
же, как и при выборе токарного инструмента (приложение 1).
ОПРЕДЕЛЕНИЕ УСЛОВИЙ ОБРАБОТКИ осуществляется так же, как
и при выборе токарного инструмента (п. 1).
15
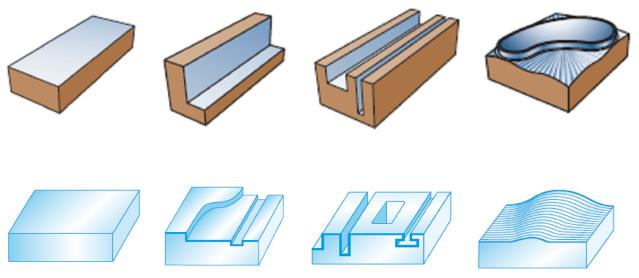
ВЫБОР ТИПА И РАЗМЕРОВ ФРЕЗЫ. Выбор фрезы по типу не все-
гда однозначен, поскольку области их применения пересекаются. Тип фрезы определятся формой и размерами обрабатываемых поверхностей (рис. 3.1). В каталогах [2, 3] выделяют следующие типы обрабатываемых поверхностей: плоскости, уступы, пазы, профильные поверхности.
а |
б |
в |
г |
д |
е |
ж |
з |
|
|
|
|
Ри с. 3.1. Типы фрезерных операций [2, 3]
а– г – условные обозначения [2]; д – з – условные обозначения [3]; а, д – фрезерование плоскостей; б, е – фрезерование уступов; в, ж - фрезерование пазов; г, з – профильное
(копировальное) фрезерование
Выбор диаметра фрезы производится исходя из мощности станка, возможности закрепления её на станке и ширины обрабатываемой поверхности. При торцовом фрезеровании диаметр фрезы D должен быть, по возможности, больше ширины фрезерования B. Согласно [7] (рис. 3.2):
D = (1,25…1,5) B. |
(3.1) |
Широкие поверхности фрезеруют за несколько рабочих ходов. Если для обработки необходима фреза диаметром менее 20 мм,
цельные концевые фрезы являются первым выбором для большинства материалов.
16
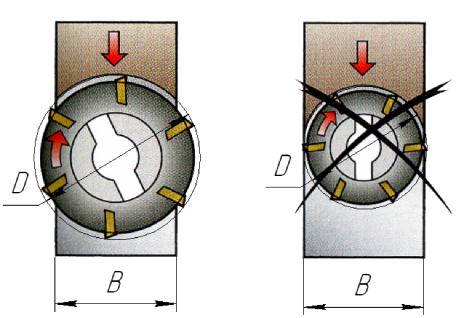
Р и с. 3.2. Рекомендации по выбору диаметра фрезы
Рекомендации по выбору главного угла в плане при торцо-
вом фрезеровании. На толщину срезаемого слоя при фрезеровании влияет главный угол в плане , который представляет собой угол между главной режущей кромкой пластины и направлением подачи (рис. 3.3). В названиях торцовых фрез фирмы Sandvik Coromant [3] угол в плане определяют последние две цифры. Например, фреза
CoroMill 245 имеет угол в плане = 45 .
Направление силы резания в значительной степени зависит от величины главного угла в плане. При угле в плане 90° (см. рис. 3.3, а) радиальная составляющая силы резания Fr превышает осевую составляющую Fx. Это означает, что обрабатываемая поверхность не подвергается большому давлению, что благоприятно для нежестких заготовок. Основная область применения таких фрез – обработка перпендикулярных уступов.
При обработке фрезой с углом в плане = 45° (см. рис. 3.3, б) осевые и радиальные силы резания приблизительно одинаковы и потребляемая мощность невысока. Это фрезы рекомендуются для обработки материалов, дающих стружку надлома, а также материалов, склонных к выкрашиваниям при значительных радиальных усилиях на выходе инструмента. При врезании меньше нагрузка на режущую
17
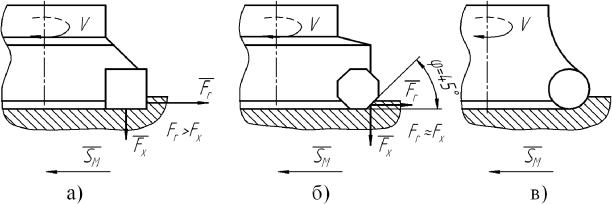
кромку в сравнении с фрезой с углом в плане = 90°. Меньше склонность к вибрациям при больших вылетах инструмента или при закреплении в приспособлении с небольшими усилиями зажима.
Р и с. 3.3. Торцовые фрезы, характеризуемые различным значением угла в плане:
а– угол в плане = 90 ; б – угол в плане = 45 ;
в– угол в плане зависит от глубины резания
Уфрез с круглыми пластинами (см. рис. 3.3,в) главный угол в плане меняется от 0 до 90° в зависимости от глубины резания. Эти фрезы имеют очень прочную режущую кромку, могут работать при больших подачах стола SM, поскольку образуют довольно тонкую стружку на большой длине режущей кромки. Направление сил резания меняется вдоль режущей кромки, поэтому направление результирующей нагрузки зависит от глубины резания.
Фрезы с круглыми режущими пластинами рекомендуется применять для обработки труднообрабатываемых материалов таких, как титан и титановые сплавы. Современная геометрия круглых пластин делает их более универсальными. В настоящее время фрезы с круглыми пластинами – это фрезы широкого применения, которые используются при снятии больших объемов металла.
Рекомендации по выбору шага зубьев фрезы при торцовом фрезеровании. Шаг зубьев фрезы представляет собой расстояние между соседними зубьями и для каждого диаметра фрезы зависит от числа зубьев.
18

В каталоге фирмы Sandvik Coromant [3] все фрезы по шагу зубьев могут быть разделены на 3 группы: фрезы с крупным (L), нормальным (М) и мелким (Н) шагом (рис. 3.4, а – в). Например, фреза диаметром 80 мм с крупным шагом имеет 4 пластины (зуба), с нормальным – 6 пластин, с мелким – 8. Шаг фрезы может быть неравномерным, что способствует уменьшению вибраций (см. рис. 3.4, г, д).
L M H
а |
|
б |
|
в |
|
|
|
|
|
г |
д |
Ри с. 3.4. Шаг зубьев фрезы [3]:
а– крупный (L), б – нормальный (M), в – мелкий (H), г – условное обозначение равномерного шага, д – условное обозначение неравномерного шага
Наиболее часто используются фрезы с нормальным шагом (М). Они рекомендуются в качестве первого выбора.
Фрезы с крупным шагом (L), т.е. с меньшим количеством пластин, предназначены для тяжелых условий обработки: недостаточная жёсткость технологической системы (ТС) мощность станков невелика, большие вылеты инструмента и др. Такие фрезы работают при малых подачах стола, снимая металл малым числом режущих зубьев. У них достаточно места между пластинами для размещения длинных стружек.
Фрезы с мелким шагом (Н) с большим количеством пластин следует применять на жестких и мощных станках при хороших условиях
19
обработки, когда есть условия для полной реализации режущих возможностей пластин при высоких подачах стола. Они пригодны также для обработки материалов, дающих элементную стружку надлома (графитный чугун – СМС 08 по классификации Sandvik Coromant), и некоторых жаропрочных материалов (СМС 20), когда необходимо ограничивать скорости резания. Такие фрезы имеют преимущества и при обработке узких поверхностей, поскольку обеспечивают достаточное число одновременно работающих пластин и, соответственно, более стабильное протекание процесса резания.
В таблицах с обозначениями и размерами корпусов фрез указан тип и размер устанавливаемых пластин. Размер пластины определяет максимальную глубину резания.
При выборе геометрии передней поверхности СМП необходимо учитывать материал обрабатываемой детали, глубину резания и подачу. В обозначении пластин Sandvik Coromant [3] геометрию передней поверхности, как правило, определяет последние две буквы. Первая из них, как правило, соответствует группе обрабатываемого материала согласно стандарту ISO (приложение 1). Вторая буква определяет диапазон глубин резания и подач, при которых обеспечивается удовлетворительное стружколомание (рис. 3.5), [3, 7].
Универсальная геометрия М пригодна для обработки заготовок как с наличием корки, так и без неё.
Геометрия L имеет более острую режущую кромку и предназначена для выполнения фрезерования с небольшими нагрузками. Применяется для обработки нежёстких заготовок. Возможна обработка вязких материалов: образуемые заусенцы минимальны.
Геометрия H имеет прочную режущую кромку и работает в тяжёлых условиях: при больших глубинах резания и подачах. При этом требуется достаточная жёсткость технологической системы (ТС).
20
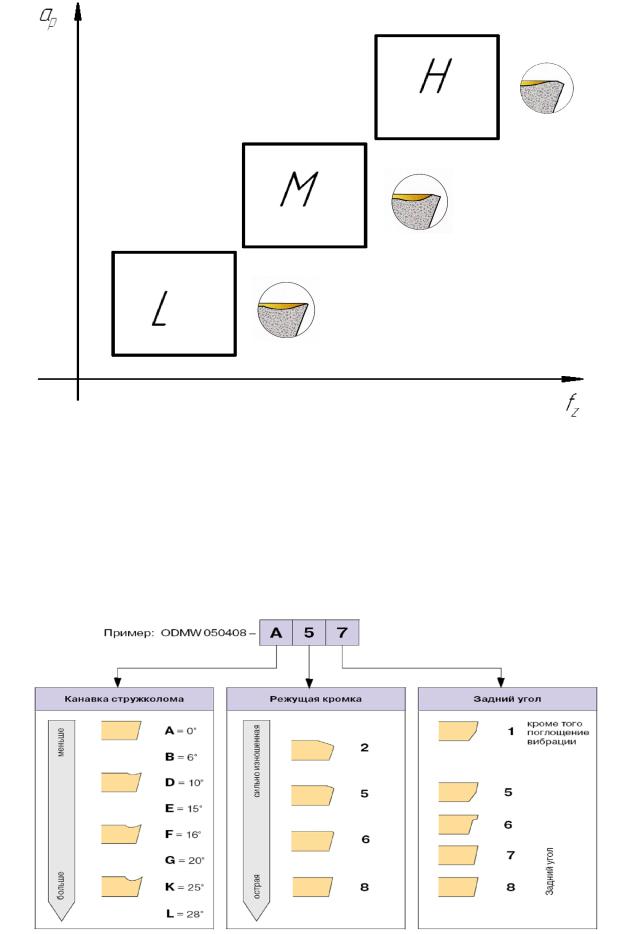
Р и с. 3.5. Основные геометрии передних поверхностей фрезерных пластин
Sandvik Coromant:
L – лёгкая; M – средняя; H - тяжёлая
Геометрии фрезерных пластин фирмы Walter кодируются, как правило, одной буквой и двумя цифрами (рис. 3.6). Коды стружколо-
мов СМП указываются в конце их обозначений.
Р и с. 3.6. Примеры стружколомов сборных фрез фирмы Walter
21
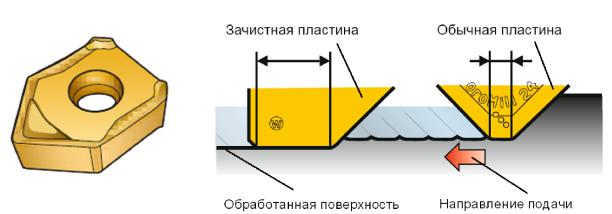
При окончательной обработке в фрезу можно установить зачистную пластину Wiper. Она располагается ниже остальных пластин и обеспечивает высокое качество обработанной поверхности. Пластина имеет длинную зачистную режущую кромку, что позволяет увеличить величину подачи до 4 раз и получить при этом высокое качество обработанной поверхности. Достаточно использовать одну зачистную пластину на фрезе.
а |
б |
Ри с. 3.7. СМП Wiper для торцовых фрез:
а– общий вид; б – формирование шероховатости обработанной поверхности
при торцовом фрезеровании
ВЫБОР ИНСТРУМЕНТАЛЬНОГО МАТЕРИАЛА осуществляется опи-
санными ранее способами для токарного инструмента (п. 1).
ОПРЕДЕЛЕНИЕ РЕЖИМОВ РЕЗАНИЯ осуществляется описанными ранее способами для токарного инструмента (п. 1). Исходными данными для назначения скорости являются марка обрабатываемого материала, марка инструментального материала (твёрдого сплава) и максимальная толщина стружки (среза) hex. Максимальная толщина стружки (среза) hex определяется по формулам, приведённым в приложении 4.
22