
SAMPLE DMLC Part II
.pdf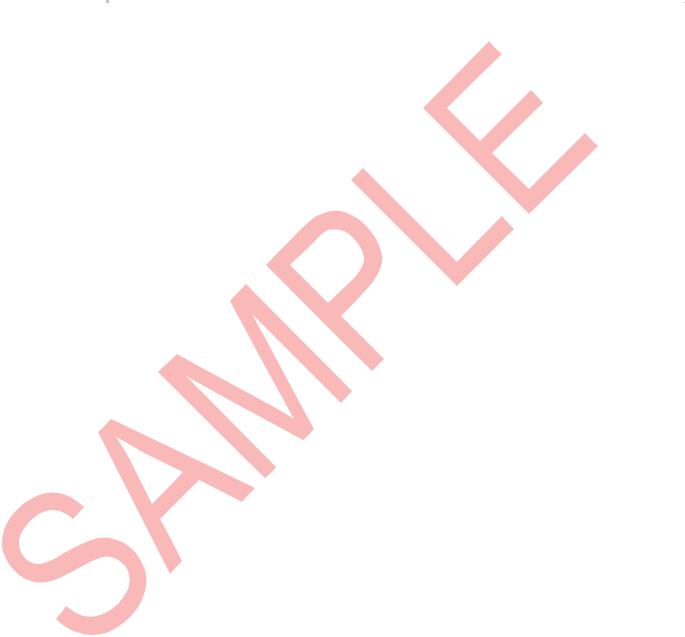
|
MLC-MANUAL |
Revision: 0 |
|
|
|
||
Page 11/26 |
|||
|
TITLE 2 – CONDITION OF EMPLOYMENT |
||
|
|
|
|
|
|
07.02.2013 |
|
|
|
|
2.6. Inspection and Certification
No certified item
2.7 Manning levels
MLC Owner |
provides the Safe Manning Certificate to the Crewing Manager |
|
|
|
instructing the Crewing Manager to man the ship with a sufficient number of seafarers by |
|
taking into account the provision for the minimum hours of rest and the danger posed by fatigue |
|
in order to ensure that ships are operated safely, efficiently and with due regard to security |
|
under all conditions |
|
|
Crewing |
manning the ship as ordered by the MLC Owner |
Manager |
|
|
|

|
MLC-MANUAL |
Revision: 0 |
|
|
|
||
Page 12/26 |
|||
|
TITLE 3 – ACCOMMODATION, |
||
|
RECREATIONAL FACILITIES, FOOD AND |
|
|
|
|||
|
CATERING |
07.02.2013 |
|
|
|
||
|
|
|
3.1 Accommodation and recreational facilities
MLC Owner /
Master
Chief Officer
ensures that the ships are in compliance with the minimum standards established by MLC 2006, providing and maintaining decent accommodation and recreational facilities for seafarers working or living on the ships
ensures that the accommodations are safe and decent in compliance with MLC 2006
determines and provides recreational facilities (as per MLC Convention B 3.1.11) at least to the minimum requirement and as far as reasonable due to ship’s size and manning level
minimum standards include:
-a bookcase and facility for reading and writing
-TV in a common room (e.g. mess room)
ensures that separate sleeping rooms and sanitary facilities are provided for men and women, when applicable
ensures that on-board recreational facilities are offered to the seafarer at no costs
performs weekly inspections of seafarer accommodation areas and documents the results (with detected defects and their prompt rectification) on form “Maintenance on board Checklist”, which is kept for at least 3 years
3.2 Food and catering
MLC Owner |
ensures that food and drinking water are of appropriate quality, nutritional value and quantity, |
Master |
taking into account the requirements of the ship and the differing cultural and religious |
|
backgrounds of seafarers on the ship |
|
|
|
provides food to seafarers free of charge during the period of engagement |
|
|
|
ensures that drinking water analysis are carried out at least one time within a 12-month period |
Crewing
Manager
Chief Officer
Cook
checks the qualification of cooks to be employed and ensures the age (not less than 18 years old)
ensures that ships cooks are trained and qualified and hold a certificate or approved document/license, which confirms proper experience and/or the participation of a training course(s) (see e.g. “MN Attestation for existing ship’s cooks”)
performs weekly inspections of food, water and catering facilities and documents the results
(including identified deficiencies and their prompt rectification) on form “Maintenance on board Checklist”, which is kept for at least 3 years
ensures that the tanks for potable water are cleaned and disinfected onboard in intervals not exceeding one year
prepares weekly menu plans and displays the menu plans in the mess-room(s)
prepares adequate, varied and nutritious meals and serves these in hygienic conditions

|
|
|
|
|
MLC-MANUAL |
Revision: 0 |
|
|
|
|
|
|
|
|
|
|
|
Page 13/26 |
||
|
|
|
|
|
TITLE 4 – HEALTH AND SAFETY |
|
|
|
|
|
|
PROTECTION AND ACCIDENT PREVENTION |
|
|
|
|
|
07.02.2013 |
||
|
|
|
|
|
|
|
|
|
|
|
|
||
|
4.1 Medical care on board ship and ashore |
|
||||
|
|
|
|
|||
|
Crewing |
|
ensure that seafarers are covered for the protection of their health) and have access to |
|||
|
Manager |
and |
prompt, adequate and free medical care (including essential dental care) whilst working on |
|||
|
Master |
|
|
board (see also P&I-Entry Certificate of Crewing Manager) |
|
|
|
|
|
|
|
||
|
|
|
|
allow seafarers to visit a qualified medical doctor or dentist without delay in ports of call, |
||
|
|
|
|
where practicable |
|
|
|
|
|
|
|
|
|
|
Master |
or |
a |
holds a valid First Aid / Medical Care certificate |
|
|
|
qualified person |
|
||||
|
maintains the Medical Log Book/ uses the medical report form contained in the International |
|||||
|
(acc. to STCW) |
Medical Guide for Ships or the Ship`s Captains Medical Guide or a similar publication to facilitate |
||||
|
delegated |
by |
the medical treatment of seafarers ashore |
|
||
|
him |
|
|
|
|
|
|
|
|
maintains the records confidential |
|
||
|
|
|
|
|
||
|
|
|
|
|||
|
MLC |
Owner / |
ensures that a complete and up-to-date list of radio stations through which medical advice can be |
|||
|
Master |
|
obtained is available on board |
|
||
|
|
|
|
|
|
|
4.2 Shipowners liability
MLC Owner
bears the liability and risks (not covered by the Crewing Manager’ P&I Cover) required under the provision of the MLC 2006 (see item 2.5 repatriation)
Crewing |
ensures seafarers right to material assistance and support with respect to the financial |
Manager |
consequences of sickness, injury or death occurring during their employment |
|
|
|
defrays the expense of medical care, including material treatment and the supply of the |
|
necessary medicines and therapeutic appliances, on board and lodging away from home until the |
|
sick or injured seafarer has recovered or until the sickness or incapacity has been declared of a |
|
permanent character |
|
|
|
provides financial security to assure compensation in the event of death or long-term disability |
|
of seafarers due to an occupational injury, illness or hazard |
|
|
Master |
ensures that the property left on board by sick, injured or deceased seafarers are safeguarded |

|
MLC-MANUAL |
Revision: 0 |
|
|
|
||
Page 14/26 |
|||
|
TITLE 4 – HEALTH AND SAFETY |
||
|
PROTECTION AND ACCIDENT PREVENTION |
|
|
07.02.2013 |
|||
|
|
||
|
|
|
4.3 Health and safety protection and accident prevention
4.3.1 Occupational health and safety policy
The occupational healthand safety policy describes the companies system to ensure personal protection in all aspects of our work. Working safely is condition of employment. It is basis for all employees to put into action the following goals:
0. Right for safe working and living conditions
All our personnel have the right to a safe and secure workplace that complies with safety standards, the right to fair terms of employment, the right to decent working and living conditions on board ship and a right to health protection, medical care and other forms of social protection (as far as practicable).
1. Avoid accidents, injuries and diseases/ Do things right straight away
Our philosophy is focused on prevention of accidents and injuries straight away. We react immediately to any malfunction by analysing and overcoming their cause and commit ourselves to continual improvement.
2. Comply with laws, rules and regulations
We will at any time follow all applicable national and international Codes, guidelines, rules and regulations regarding health and safety and other requirements to which the organisation subscribes.
3. Guarantee competency and professional behaviour
We guarantee professionalism by continuously training our personnel in risk awareness and -protection. Therefore we provide required methods, resources and trainings to prove our competency and our professional behaviour every day.
4. Identify and assess risks
The company undertakes to protect personnel and assets against all identified risks and has therefore implemented a procedure for the permanent and continuous identification and assessment of risks with regards to health and safety protection and resulting control measures. Special attention is brought to the following subjects: structural features of the ship (e.g. asbestos), machinery, extreme surface temperature (high or low), effects of noise and vibration, effects of ambient factors (e.g. tobacco smoke), safety measures on and below deck, cargo equipment, mooring equipment, fire prevention and fire-fighting, anchors, chains and lines, dangerous cargo and ballast, personal protective equipment, working aloft and in enclosed spaces, fatigue, drug abuse, HIV/ AIDS protection and emergency and accident response.
5. Cleanliness equals safety
Seamen on board are obliged to live in hygienic and safe conditions on board of our vessels.
6. Protection of seafarers under the age of 18
We particularly aim at the safety and protection of the health of seafarers below the age of 18.
7. Personal protective equipment
Personal protective equipment is being used and maintained correctly.
In order to reach these objectives we ensure that our occupational health and safety management policy is understood, put into practice and maintained at all levels of our organisation (including the services of subcontractors and suppliers). All required resources necessary to implement the above are provided. Our policy is displayed on board in a public place.
………………………………………………………………………… |
|
Managing Director of XXXXXReederei GmbH & Co. KG |
XXXXX, 13.12.2012 |

|
MLC-MANUAL |
Revision: 0 |
|
|
|
||
Page 15/26 |
|||
|
TITLE 4 – HEALTH AND SAFETY |
||
|
PROTECTION AND ACCIDENT PREVENTION |
|
|
07.02.2013 |
|||
|
|
||
|
|
|
4.3.2 Healthand safety committee
The healthand safety committee consists of the Master, the Safety Officer and a representative elected by the Officers and ratings. All departments on board have to be represented in the safety committee. The Master is the chairman of the meeting. The Master records the appointment of a safety committee in the official logbook.
The safety committee meeting is held at no more than six weeks intervals.
It is the duty of the safety committee to use their best endeavours to ensure that the provisions of the Code of Safe Working Practices, MLC 2006, relevant legislation, and Shipping Notices are complied with, to improve the standard of safety consciousness among the crew, and to:
-make representations and recommendations on behalf of the crew to the MLC owner on matters affecting the occupational health and safety of the crew;
-ensure the observance of the employer's occupational health and safety policies and to make recommendations for their improvement;
-consider and take any appropriate action in respect of any occupational health and safety matters affecting the ship and its crew;
-input into risk identification and assessment and determination of adequate control measures
-reviewing incidents
-discussing changes and their relevance in the work places
-acting as community of interests regarding health and safety management, keep a record of their deliberations, conclusions and any representations made to the Master or to the health and safety committee, of the replies thereto and of any action resulting there from;
-ensure that any conclusions reached on matters of occupational health and safety are followed up.
The Safety Officers documents the safety committees meetings on ISM-form “Safety/ Security Drill, Exercise, Report and Meeting Form”. (ref. to SBM Forms and Checklists, Ch. 8, no. 3)
4.3.3 Risk evaluation
please see companies SBM Shipboard Manual Chapter 7.6 Safe Working Practice and Risk Assessment
4.3.4 Occupational health and accident prevention notices
Master |
displays relevant occupational healthand accident prevention notices and official instructions |
|
with respect to particular hazards on the ship in a public location |
|
|
4.3.5 Reporting of occupational accidents |
please see SBM Shipboard Manual Chapter 9.1 Reports of Incidents and related procedures required by the Flag State (ref. to the Antigua & Barbuda Directive 001-2012 “The Merchant Shipping (Reports of Accidents) Directive 2012”)

|
MLC-MANUAL |
Revision: 0 |
|
|
|
||
Page 16/26 |
|||
|
TITLE 4 – HEALTH AND SAFETY |
||
|
PROTECTION AND ACCIDENT PREVENTION |
|
|
07.02.2013 |
|||
|
|
||
|
|
|
4.3.6 Procedures to prevent identified risks
The MLC owner does not levy a charge for anything done in the below procedures.
Clothing and personal protective equipment
All employees |
only wear provided personal protective equipment |
|
correctly fasten their clothing |
|
remove clothing and shoes saturated with oil or other chemicals at once and wash the |
|
body with soap and plenty of water |
|
wear safety boots or shoes with non-slip soles and heavy steel toe-caps outside of |
|
living quarters |
|
clean their shoes if these are slippery |
|
wear hard hats at all times when outside the accommodation |
|
wear appropriate hand protection when handling corrosive materials, hot items and |
|
sharp materials |
|
remove jewellery from fingers, ears and wrist while working |
|
avoid nylon clothing to avoid the risk of injury through burns |
|
wear eye protection when chipping, scraping, spraying, using hammers or sledges on |
|
metal, welding, cutting or using grinders or drills, or when handling corrosive liquids |
|
wear eye protection with dark lenses in the immediate vicinity of burning, cutting, |
|
welding, etc. |
Working in cold weather conditions |
|
|
|
Department Head |
ensures warming up-periods |
|
ensures that adequate working clothes (e.g. winter overall, winter gloves) are worn |
|
familiarises the crew with skin-protective measures against frostbites (e.g. using |
|
vaseline) |
|
encourages the drinking of warm fluids, such as soup or hot chocolate |
|
introduces more frequent rest breaks, if possible |
|
educates the crew members about recognising the early symptoms of cold stress |
Working in hot weather conditions |
|
|
|
Department Head |
reschedules work to cooler times of the day, if possible |
|
ensures that adequate working clothes are worn |
|
provides more frequent rest breaks, if possible |
|
introduces shading to rest and work areas, if and where possible |
|
encourages the drinking of plenty of drinking water to avoid dehydration |
|
educates workers about recognising the early symptoms of heat stress |
|
encourages workers to protect skin against sun damages |
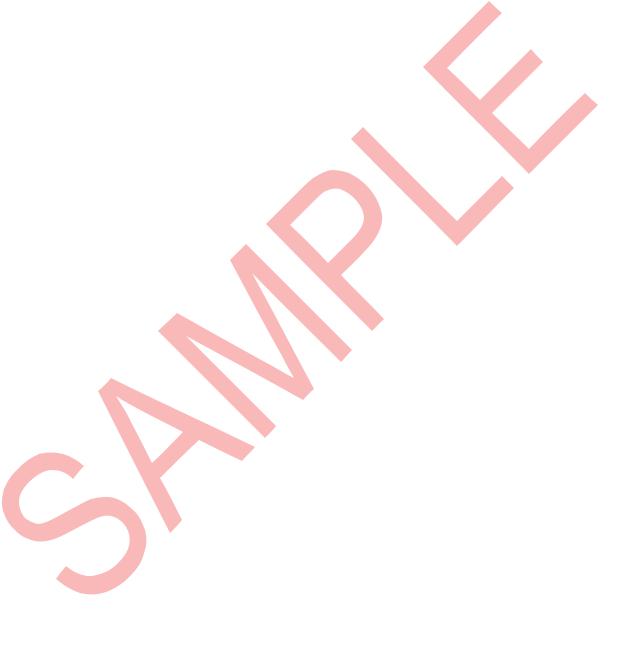
|
|
|
MLC-MANUAL |
Revision: 0 |
|
|
|
|
|
|
|
|
|
Page 17/26 |
|||
|
|
|
TITLE 4 – HEALTH AND SAFETY |
||
|
|
|
PROTECTION AND ACCIDENT PREVENTION |
|
|
|
|
07.02.2013 |
|||
|
|
|
|
||
|
|
|
|
|
|
|
Use of cranes and lifting gear |
|
|
||
|
|
|
|
||
|
Master |
ensures that cranes, which are not in use, are properly housed and secured |
|
||
|
|
ensures that nobody uses any cranes and lifting gear unless properly trained for this |
|
||
|
|
purpose (and are competent) |
|
|
|
|
|
determines the safe working load of the lifting equipment and the weight of the load to |
|
||
|
|
be lifted |
|
|
|
|
|
exercises care to ensure that all personnel are aware and clear of the load to be lifted |
|
||
|
|
prior to operating a hoist or winch |
|
|
|
|
|
ensures that only one person should be giving instructions to a crane or winch |
|
||
|
|
operator and he must be able to see what is happening to the load |
|
|
|
|
|
ensures that the equipment is within safe limits and that the wire is being reeled |
|
||
|
|
correctly |
|
|
|
|
|
ensures that the crane is marked with the SWL (Safe Working Load) |
|
|
|
|
|
ensures that steadying lines are used when lifting heavy equipment off or onto the |
|
||
|
|
deck |
|
|
Entering enclosed spaces
please see SBM Shipboard Manual Chapter 7.6.1 Entering enclosed space
Working with electricity
please see SBM Shipboard Manual Chapter 7.6.5 Working on electrical circuits
Working Aloft
please see SBM Shipboard Manual Chapter 7.6.4 Working Aloft
Diving Operations
Diver |
takes all necessary precautions according to form |
|
“Diving Permit” and documents the results on the form |
Helicopter operations |
|
please see SBM Shipboard Manual Chapter 8.4.17 Helicopter Operations
Working on deck
Every person working |
must wear proper personal protective equipment |
on deck |
never takes off eyes off heavy loads nearby which are being lifted |
|
never stands in the bight (loop) or rope or wire which is being paid out or |
|
recovered or inside the angle of a wire passing through a block |
|
keeps clear of ropes or wires under tension unless required to do something to |
|
them or to whatever they are attached to |
|
never stands between shifting loads and solid objects |
|
uses gloves when handling wires |
|
does not operate a winch unless knowing that it is safe to do so |
|
keeps an eye for damaged ropes, wires and loose shackles |
|
inspects a ladder before climbing |
|
observe the rules against smoking and open fire (in marked areas) |

|
|
|
MLC-MANUAL |
Revision: 0 |
|
|
|
|
|
|
|
Page 18/26 |
||
|
|
|
TITLE 4 – HEALTH AND SAFETY |
|
|
|
|
PROTECTION AND ACCIDENT PREVENTION |
|
|
|
07.02.2013 |
||
|
|
|
|
|
|
|
|
|
|
|
Working below deck |
|
||
|
|
|
||
|
Every person |
ensures proper ventilation (please observe below chapter regarding ventilation) |
||
|
working below |
|
|
|
|
ensures that emergency exits are freely accessible at any time |
|
||
|
deck |
|
||
|
|
|
|
|
|
arranges for proper lighting |
|
||
|
|
|
||
|
|
|
|
|
|
|
immediately closes cabin floor hatches to avoid anyone falling |
|
|
|
|
|
|
|
|
|
observes the rules against smoking and open fire |
|
|
|
|
|
|
|
|
Ventilation |
|
|
|
Death and serious health damage can result from inadequate ventilation on board.
Carbon dioxide asphyxiation can result from incomplete combustion of gas/ paraffin/ diesel heaters. Engine exhaust fumes are extremely toxic.
If you feel dizzy or awaken with headaches, check heaters, cookers and ventilation fans and ducts, report symptoms to the Master. If necessary evacuate cabins or wear a gas mask.
Chief Officer/ |
ensures that proper ventilation is maintained |
Engineer |
|
|
|
Ventilation and Air Conditioning System |
|
|
|
Chief Officer/ |
ensures that ventilation of the sleeping rooms, mess room(s) is maintained adequately based on |
Engineer |
the climatic condition |
|
|
|
ensures that the air con systems is maintaining the air temperature and humidity adequately |
|
based in the climate condition |
|
|
Hot Works
please see SBM Shipboard Manual Chapter 7.6.2 Hot Works
Structural features of the ship
MLC Owner
secures all safety-relevant structural features of the ship during the construction process and ensures that no life-endangering materials are used (e.g. asbestos)
All crew members
Safety Officer
safety helmets to be worn in order to avoid head injuries by touching web frames, stringers, brackets, top rails, etc.
marks slippery decks to protect people from falling/ drowning
during winter time ensures that slippery decks will be avoided by using salt, sand, or the like
Machinery
Engineers |
ensure that no floor plates are missing or damaged |
|
|
|
comply with all required protective measures before, during and after grinding and welding |
|
|
|
store batteries appropriately to avoid acid burns, explosions and suffocations |
|
|
|
observe deck head protrusions to avoid head injuries |
|
|
|
secure accesses to the engine-room to protect people from falling |
|
|
|
ensure that hot surfaces and pipes cannot be touched |
|
|
|
control the pressure levels of air bottles |
|
|

|
|
|
MLC-MANUAL |
Revision: 0 |
|
|
|
|
|
|
|
Page 19/26 |
||
|
|
|
TITLE 4 – HEALTH AND SAFETY |
|
|
|
|
PROTECTION AND ACCIDENT PREVENTION |
|
|
|
07.02.2013 |
||
|
|
|
|
|
|
|
|
|
|
|
Extreme surface temperature (high or low) |
|
||
|
|
|
||
|
Chief Officer/ |
familiarises the crew in order to ensure that nobody touches above equipment without adequate |
||
|
Engineer |
safety measures |
|
|
|
|
|
|
|
Effects of noise
Exposure to noise results in deafness, tinnitus (with buzzing, rumbling and/ or ringing). Loss of hearing is incurable.
|
|
Safety Officer |
informs all crew members on the dangers of noise on the ability to hear and health in general |
|
and on the correct use of ear protection |
|
|
Department |
provide approved ear protection for all crew members exposed to noise |
Heads |
|
|
|
Crewmember |
wears ear protection that fits properly, when applicable |
|
|
Effects of vibration
1.) Hand-/ arm vibration
Hand-arm vibration is vibration transmitted from work processes into crew members' hands and arms. It can be caused by operating hand-held power tools, like needle hammers, grinders. Regular and frequent exposure to handarm vibration can lead to permanent health effects. This is most likely when contact with a vibrating tool or work process is a regular part of a crew members job. Occasional exposure is unlikely to cause ill health. Hand-/ arm vibration can cause a range of conditions collectively known as hand-/ arm vibration syndrome (HAVS) as well as specific diseases such as carpal tunnel syndrome.
Department |
looks for alternative work methods which eliminate or reduce exposure to vibration |
|
Head |
|
|
limits the use of high-vibration tools wherever possible |
||
|
||
|
|
|
|
limits the time that crew members are exposed – several shorter periods are preferable |
|
|
|
|
|
rotate screw members to limit exposure times |
|
|
|
2.) Whole body vibration
Whole-body vibration is transmitted through the seat or feet of employees .Large shocks and jolts may cause health risks including back-pain.
The owner undertakes to limit the vessels vibration during the vessels design and construction process.
Safety Officer |
inform screw members on the hazards associated with vibration |
|
|
Mooring equipment
please see SBM Shipboard Manual Chapter 7.6.8 Safe Mooring
Effects of ambient factors (e.g. tobacco smoke)
Exposure to tobacco smoke – even occasional smoking or secondhand smoke – causes immediate damage to your body that can lead to serious illness or death.
Therefore smoking in marked public areas on board is prohibited.
During port stays outside smoking is only allowed if in compliance with the port regulations.
Fire prevention and fire-fighting
please see SBM Shipboard Manual Chapter 8.4.1

|
MLC-MANUAL |
Revision: 0 |
|
|
|
||
Page 20/26 |
|||
|
TITLE 4 – HEALTH AND SAFETY |
||
|
PROTECTION AND ACCIDENT PREVENTION |
|
|
07.02.2013 |
|||
|
|
||
|
|
|
Anchors, chains and lines
please see SBM Standing Orders Deck/ Bridge Chapter 5.3 Anchors, chains and lines preparedness
Dangerous cargo and ballast
For the handling of dangerous cargo please observe SBM Shipboard Manual Chapter 8.9
Chief Officer |
informs Chief Engineer on need for ballasting/ deballasting |
|
|
|
|
Chief |
Engineer |
performs ballasting/ deballasting operations |
and/or |
person |
|
maintains controlled condition if overflowed |
||
delegated by him |
|
|
or master |
|
|
|
|
|
Chief Officer |
supervises the process |
|
|
|
|
Fatigue
Fatigue can be defined as temporary loss of strength and energy resulting from hard physical or mental work. There are several factors that effect navigation officer’s fatigue. Fatigue is associated with poor quality sleep, negative environmental factors, high job demands and high stress.
Occupational risks increase dramatically with fatigue.
Prolonged periods without sleep impairs judgement, concentration and the ability to communicate.
Fatigue minimization procedure
Tired crew |
notify your reliever, if you find it difficult to remain alert (e.g. on watch) |
|
|
Master |
increase team awareness and contribution |
|
|
|
increase communication facilities to decrease psychological fatigue |
|
|
|
encourage regular and sufficient nutrition |
|
|
|
ensure that required hours of rest are complied with |
|
|
Drug and alcohol abuse
please see SBM Shipboard Manual Chapter 2.2
HIV/ AIDS protection
Master |
encourages crew to use condoms |
|
|
Protection in mosquito infested ports / plague of insects (in special trading areas)
Master |
ensures that mosquito nets are provided on board and that they are used |
|
|
|
encourages the crew to wear skin protection, e.g. clothes or salves |
|
|
Emergency and accident response
see SBM Shipboard Manual Chapter 8