
ГОСы ТХОм-51 2013 / ТМОХИ Жуйков
.pdf9. Перечислите рекомендации при разработке плана мех. обработки (последовательности выполнения операций).
В 1 очередь обрабатываются пов-ти, кот. будут служить базами для последующей обработки.
Во 2 очередь обрабатываются пов-ти с наибольшим припуском, чтобы сразу обнаружить дефекты (раковины, включения).
Точные пов-ти обрабатываются в последнюю очередь.
Черновые и чистовые проходы целесообразно выполнять на разных станках. Если данную операцию можно выполнить на разных станках, то выбирают тот станок, кот. дает большую производительность и более высокую точность и экономичность.
1.создание чертежей со всеми техническими требованиями (точность, шероховатость, допуски и посадки)
2.нужно определиться с типом производства (серийность)
3.нужно определиться с наличием имеющегося на предприятии оборудования, приспособлений, оснастки, инструментов, инструменталь-
ных материалов.
4. составление тех.процесса – последовательности материалов:
1)выбор заготовки (зависимость от типа производства и детали), марки материала
-чертеж
-припуски на обработку
2)составление порядка выполнения операций. На каждую операцию рассчитать припуск:
-на первой операции подготавливаются базовые поверхности, для закрепления заготовки при последующих операциях
-точная обработка производится на конечных операциях
3)рассчитать режимы резания на каждую операцию, переход, проход, нормы времени (важно для массового производства)
4)оформление документации (сводная ТК, операционные ТК,
контрольная ТК)
10. Какие факторы влияют на выбор марки инструментального материала?
Рабочая часть режущего инструмента должна обладать набором определенных физико-механических свойств (твердость, прочность, теплостойкость, теплопроводность, износостойкость, коэффициент трения).
Низкая термостойкость (~200 C) углеродистых (У10А, У12А) и низколегированных (В2, Ф, 9ХС, ХВГ) инструментальных сталей ограничивает их использование. Из угл. – напильники, надфили, ножовочные полотна. Из угл. и низ.лег. – только инструменты, работающие при низких скоростях резания – мелкоразмерные сверла, зенкеры, развертки, метчики и плашки.
Из высоколегированных (W, Mo, V, Co, C, Cr) быстрорежущих инструментальных сталей (Р9, Р6М5, Р9К5) изготавливают все виды и размеры инструментов, т.к. бр стали способны выдерживать большие кон-
тактные напряжения. Теплостойкость ~620-640 C, скорости резания в 2..2,5 раза больше, чем угл. и низ.лег. Обрабатываются конструкционные стали и цветные сплавы.
Твердые сплавы (ВК3, Т5К10 и др.). (WC, TiC, TaC, Co)
Твердыми, теплостойкими (>1000 C) и износостойкими твердосплавными пластинками оснащают все виды токарных резцов, большинство фрез, устанавливают на зенкерах, протяжках, развертках, зуборезных и резьбонарезных инструментах. Мелкие сверла, зенкеры, фрезы – целиком. Твердыми сплавами (ВК2-ВК8) обрабатываются хрупкие материалы (чугун), при обработке которых образуется стружка надлома. Двухкарбидными твердыми сплавами (ТК10, Т15К6) – стали (сливная стружка).
Минералокерамика (ЦМ332). Корунд (Al2O3) + стекло (связующее) – реж. пластинки. Теплостойкость порядка 1500 C позволяет обрабаты-
вать Ме со ск-ми до 600 м/мин. (-) низкий предел прочности только тонкая окончательная обработка.
Керметы (ВОК-60, ВОК-63, В3) = Минералокерамика + WC, TiC, МоC
выше прочность, но ниже теплостойкость (1300 C) – тонкая окончательная обработка.
Нитрид бора «Эльбор»– очень высокая прочность, сверхтвердость, те-
плостойкость 1800 C. Окончательная обработка чугуна, труднообрабатываемых материалов и термообработанных сталей.
Синтетические алмазы (АС). Оч. высок. тв-ть, теплостойкость 650 C, но высокая теплопроводность. Для прецизионной обработки Cu и Al сплавов, пластмасс, стеклопластиков, полупроводниковых материа-
лов. Скор. рез. 1000-1200 м/мин высокая производительность.

11. Обоснуйте последовательность назначения параметров режима резания. Какие факторы влияют на выбор глубины резания и подачи?
К параметрам режимов резания относятся: 1) скорость резания, v, м/мин.
v Dn
1000 м/мин
D – диаметр элемента, совершающего главное движение, n – частота вращения этого элемента.
2)глубина резания, t, мм. Это кратчайшее расстояние от обрабатываемой до обработанной поверхности.
3)подача S.
Существует 3 вида подач:
для многозубого инструмента, Sz, мм/зуб;
подача на один оборот заготовки или инструмента, S , мм/об
S = Sz * z,
где z – количество зубьев (для многозубого инструмента).
минутная подача, Sм, мм/мин
Sм = S * n,
Где n – частота вращения
Sм = Sz * z * n , - для фрезерования Глубина резания зависит от:
припуска на обработку: чем ближе к припуску, тем лучше. Слишком большой припуск (отливка, заготовка в подкладных штампах) в несколько проходов.
типа операции: черновая (от 2/3 до 3/4); чистовая (1/3 – 1/4); процесс уточнения – совсем чуть-чуть.
Ограничения: максимальная глубина рез. ограничивается возможностью оборудования, шириной пластины инструмента. При обработке (расточке) небольших отверстий – прочность и жесткость державки резца.
Подача определяется: предельно допустимой шероховатостью поверхности; прочностью слабого звена (предохранитель); прочность и жесткость инструмента.
Производительность зависит от объема снятого Ме, чем больше, тем
лучше. V=t·S·v,мм3/мин. Зависимость стойкости от t·S·v (см. график).
Самое низкое влияние на изменение стойкости резца оказывает гл.рез., затем подача, а потом скорость, поэтому в тех.процессе сначала выбирается гл.рез.(по максимуму), затем подача, а потом скорость.
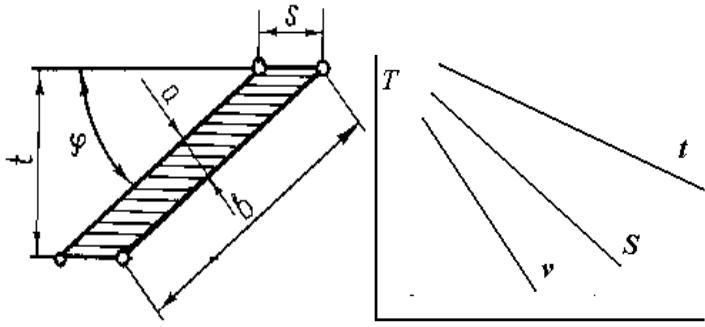
а=S·sinφ, b=t/ sinφ
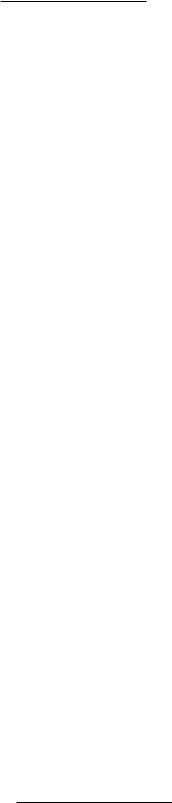
12.Приведите и расшифруйте эмпирическую формулу для расчета скорости резания и формулу для расчета частоты вращения шпинделя при точении как рассчитать фактическую скорость резания?
v CV K , м / мин
, где Cv |
T m t x S y |
- постоянный коэффициент зависящий от постоянных условий |
обработки (свойств обрабатываемого и инструментальных материалов, геометрии инструмента, наличия СОЖ);
K - суммарный поправочный коэффициент на изменённые условия обработки,
K KM K И K K
поправочные коэффициенты
KМ - на обрабатываемые материалы
KИ - на инструментальные материалы
K - на передний угол
K - на главный угол в плане
Т - период стойкости инструмента
m - показатель относительной стойкости
yv xv - характеризуют зависимость скорости от подачи и глубины
Первоначальная скорость резания и определяется по таблицам, с учетом глубины резания, подачи и стойкости инструмента.
По расчетной скорости находится расчетная частота вращения шпинделя.
n d v ,об / мин
1000
Далее поправочными коэффициентами корректируется значение частоты вращения шпинделя Выбранный режим резания корректируется по паспортным данным
станка, подбираются ближайшие значения n (округляют до ближайшего большего если разница между ними меньше 5%, если больше – в меньшую сторону) и sM. Отсюда после корректировки находим фактическую скорость резания:
d nфакт , м / мин
1000

13. Начертите схему операции сверления глухого отверстия и приведите формулу для расчета машинного времени
t0=(l1+l2)/(nS) – расчет машин времени, lр х =l1+l2 – длина рабоч хода.
где l1=R·ctgφ (R=1/2D) – вел-на врезания – расст от пов-ти заг-ки до вершины сверла, мм; зависит от диам сверла;
l2 – глубина отв-я, мм;
n – частота вращ-я заг-ки, об/мин; S–подача, мм/об,
φ – глав угол в плане.
Для расчета проходного отв-я добав-ся еще вел-на перебега.
14.Какие факторы влияют на точность механической обработки. Технологическая последовательность получения точных поверх-
ностей.
Под точностью обработки понимают степень соответствия обработанной детали техническим требованиям чертежа в отношении точности размеров, формы и расположения поверхностей. Если все параметры детали находятся в пределах указанных на чертеже допусков, деталь считается годной для сборки и дальнейшей работы.
Существует два метода обеспечения заданной точности обработки:
-Метод индивидуального получения размера точность обработки обеспечивается выверкой положения заготовки на станке и настройкой инструмента на заданный размер по нанесенным рискам на заготовке. Этот метод характерен для мелкосерийного и единичного производства.
- Метод автоматического получения размеров применяют, когда заготовки обрабатывают на станке и приспособлениях. При этом вся партия заготовок обрабатывается инструментом, предварительно настроенным на заданный размер. Этот метод характерен для серийного и массового производства.
На точность обработки влияет много факторов:
- Погрешность установки заготовки на станке при обработке в приспособлениях зависит от выбора установочных технологических баз (поверхностей, линий, точек), которые обеспечивают определенное положение заготовки на станке, сохраняемое в процессе обработки.
- Погрешности обусловленные упругим отжатиями технологической системы станок – приспособление – инструмент – заготовка под действием сил резания.
Тех система станок – приспособление – инструмент – заготовка не является жесткой. Сама заготовка имеет различную жесткость в разных сечениях. Все это приводит к тому, что под действием сил и моментов резания элементы технологической системы изменяют свое относительное пространственное положение. Для уменьшения погрешности этих погрешностей следует стабилизировать силу резания в процессе обработки, повышать жесткость тех системы и выравнивать жесткость заготовки.
- Погрешности, вызванные неточностью изготовления и износом режущего инструмента. Предопределяет погрешность обработки, а его износ сказывается на ее точности, причем необходимо учитывать только то износ инструмента, который влияет на размер обработки, - размерный износ. При обработке длинных валов – конусность; затупление инструмента повышает силу резания, что увеличивает упругие отжатия тех системы и тем самым еще больше снижать точность обработки. Уменьшить влияния разменного износа можно при помощи устройств активного контроля, которые измеряют заготовку в процессе обработки.
- Погрешности, вызываемые установкой инструмента на заданный размер, обусловлены тем, что при смене затупившегося инструмента новый инструмент невозможно установить в точности такое же положение из за погрешности измерения, регулировки.
- Погрешности станка. Неточность изготовления самого станка, которая регламентирована стандартом и указана в паспорте, и износ его элементов в процессе работы вызывают погрешности формы при обработке поверхности заготовки. Несоосность приводит к конусности.
15.Какие факторы процесса механической обработки определяют качество обработанной поверхности, его влияние на эксплуатационные характеристики изделия.
Качество поверхности является одним из важнейших факторов, обеспечивающих высокие эксплуатационные свойства и обусловливается свойствами металла и методами обработки. В процессе механической обработки (резание лезвийным инструментом, шлифование, полирование и др.) поверхностный слой деформируется под действием нагрузок и температуры, а также загрязняется примесями (частицы абразива, кислород) и другими инородными включениями.
Геометрические характеристики качества -отклонения формы - волнистость;
-шероховатость и глубина дефектного слоя -материал
-шероховатость-повышение класса точности шлифованием, но только на закаленных сталях -дефекты( напряжение для тонкостенных)
Качество поверхности оказывает существенное влияние на эксплуатационные свойства деталей машин: износостойкость, усталостную прочность, стабильность посадок, коррозионную стойкость и другие.
Формирование качества поверхности связано с влиянием следующих групп факторов:
1. Геометрии инструмента и особенностей процесса резания; Увеличение подачи, главного и вспомогательного угла в плане приводит к росту микронеровностей. Поэтому при чистовом точении не рекомендуются подрезные резцы.
Увеличение радиуса закругления резцов, их доводка по передней и задней поверхности - снижают шероховатость.
2.Соотношением между упругими и пластическими деформациями поверхности;
3.Возникающими вибрациями инструмента относительно заготовки.

16. Элементы и геометрические параметры резца
Резец – это режущий инструмент, предназначенный для обработки деталей различных размеров, форм, точности и материалов. Является основным инструментом, применяемым при токарных, строгальных и долбёжных работах.
Рабочая часть резца представляет собой клин, который под действием приложенного усилия деформирует слой металла, после чего сжатый элемент металла скалывается и сдвигается передней поверхностью резца. При дальнейшем продвижении резца процесс скалывания повторяется и из отдельных элементов образуется стружка.
Токарный проходной резец состоит из следующих основных элементов:
-Рабочая часть (головка); -Стержень (державка) — служит для закрепления резца на стан-
ке.
Рабочую часть резца образуют:
Передняя поверхность — поверхность, по которой сходит стружка в процессе резания.
Главная задняя поверхность — поверхность, обращенная к поверхности резания заготовки.
Вспомогательная задняя поверхность — поверхность, обращенная к обработанной поверхности заготовки.
Главная режущая кромка — линия пересечения передней и главной задней поверхностей.
Вспомогательная режущая кромка — линия пересечения передней и вспомогательной задней поверхностей.
Вершина резца — точка пересечения главной и вспомогательной режущих кромок.

Углы резца и их назначения:
На рисунке показана главная секущая плоскость. Передняя поверхность направлена вниз от главной режущей кромки, передний угол γ в этом случае считается положительным.
Для определения углов резца установлены следующие плоскости:
-Плоскость резания — плоскость, касательная к по-
верхности резания и проходящая через главную режущую кромку. -Основная плоскость — плоскость, параллельная направлениям
подач (продольной и поперечной).
-Главная секущая плоскость — плоскость, перпендикулярная проекции главной режущей кромки на основную плоскость.
-Вспомогательная секущая плоскость — плоскость, перпендикулярная проекции вспомогательной режущей кромки на основную плоскость.
Главные углы измеряются в главной секущей плоскости. Сумма уг-
лов α+β+γ=90°.
Главный задний угол α — угол между главной задней поверхностью резца и плоскостью резания. Служит для уменьшения трения между задней поверхностью резца и деталью. С увеличением заднего угла шероховатость обработанной поверхности уменьшается, но при большом заднем угле резец может сломаться. Следовательно чем мягче металл, тем больше должен быть угол.
Угол заострения β — угол между передней и главной задней поверхностью резца. Влияет на прочность резца, которая повышается с увеличением угла.
Главный передний угол γ — угол между передней поверхностью резца и плоскостью, перпендикулярной плоскости резания, проведённой через главную режущую кромку. Служит для уменьшения деформации срезаемого слоя. С увеличением переднего угла облегчается врезание резца в металл, уменьшается сила резания и расход мощности. Резцы с отрицательным γ применяют для обдирочных работ с ударной нагрузкой. Преимущество таких резцов на обдирочных работах заключается в том, что удары воспринимаются не режущей кромкой, а всей передней поверхностью.