
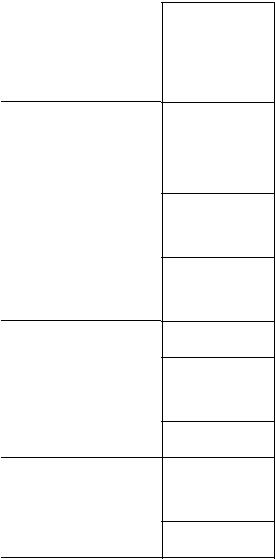
© И.В. Кривцун, 2001 (ИЭС им. Е.О. Патона НАНУ, Украина, 03680, г. Киев, ул. Боженко 11,
Тел. (044) 261-5349, Факс: (044) 268-0486, krivtsun@i.com.ua, http://www.plasma.kiev.ua/people/krivtsun.html
Tаблица 1.1
Основные схемы практической реализации лазерно-дуговых процессов
Тип комбинированного |
Расположение ла- |
|
процесса (используемые |
зерного пучка и |
|
источники тепла) |
дуги |
|
|
|
|
Л+ДНЭ |
с одной стороны |
|
изделия |
||
|
||
|
|
|
Л+ДНЭ |
с разных сторон |
|
изделия |
||
|
||
|
|
|
Л+ДПЭ |
с одной стороны |
|
|
|
|
Л+ДПЭ |
с разных сторон |
|
|
|
|
Л+ПД |
с одной стороны |
|
|
|
|
Л+ПД |
с разных сторон |
|
|
|
|
Л+ПС |
с одной стороны |
|
|
|
|
Л+ПС |
с разных сторон |
|
|
|
Области применения процесса
сварка, резка,
сверление, закалка
сварка, резка
сварка
сварка
сварка, резка,
наплавка
сварка
сварка, резка, закалка, напыление
резка
Литература
[5, 12, 17, 27-
29, 39, 44, 45]
[10, 12, 23]
[24, 39, 4446]
[34]
[31, 36, 38-
43, 45]
[32]
[33, 46]
[35]
В заключение данного раздела следует отметить, что известные способы лазерно-дуговой сварки, резки, обработки поверхности (Л+ДНЭ, Л+ДПЭ, Л+ПД, Л+ПС) и большинство устройств для их практической реализации были предложены до начала 1990-х годов. В дальнейшем (судя по содержанию работ последнего десятилетия) ученые сосредоточили свои усилия в большей мере на изучении технологических возможностей лазерно-дуговых процессов металлообработки, а также на исследовании физических явлений, протекающих
30
© И.В. Кривцун, 2001 (ИЭС им. Е.О. Патона НАНУ, Украина, 03680, г. Киев, ул. Боженко 11,
Тел. (044) 261-5349, Факс: (044) 268-0486, krivtsun@i.com.ua, http://www.plasma.kiev.ua/people/krivtsun.html
при взаимодействии сфокусированного лазерного излучения с дуговой плазмой
и их комбинированном воздействии на металлы.
•Энергетические характеристики и технологические возможности лазерно-дугового источника тепла
Параллельно с разработкой различных лазерно-дуговых процессов и устройств для их реализации происходило интенсивное накопление экспериментальных данных об энергетических характеристиках и технологических возможностях нового, комбинированного источника тепла. Исследовались параметры проплавления металла, производительность и качество лазерно-дуговой обработки в зависимости от соотношения мощностей лазерного пучка и электрической дуги, их взаимного расположения, условий фокусировки лазерного излучения и т.д. Эти исследования преследовали цель оценить перспективы промышленного применения того или иного комбинированного процесса и установить диапазон оптимальных режимов его реализации.
Как уже отмечалось выше, Стин был первым, кто начал изучать технологические возможности своего изобретения. Он исследовал эффективность совместного использования излучения СO2-лазера мощностью до 2 кВт и дуги с неплавящимся электродом при сварке и резке низкоуглеродистой стали малых толщин (0,2…3,0 мм), при сварке титана толщиной 0,8 мм и жести различного состава, а также при наплавке толстолистовой (12 мм) малоуглеродистой стали. Им было установлено, что комбинированное воздействие этих источников тепла на изделие позволяет значительно увеличить глубину проплавления и производительность процесса, почти не снижая качества обработки по сравнению с лазерными способами.
Эффективность совместного нагрева обрабатываемого металла излучением СO2-лазера небольшой мощности и аргоновой дугой с вольфрамовым электродом (при расположении обоих источников тепла с одной стороны изделия) была доказана и в работах [47, 48]. Эксперименты по комбинированной сварке углеродистых и нержавеющих сталей, никелевых
31
© И.В. Кривцун, 2001 (ИЭС им. Е.О. Патона НАНУ, Украина, 03680, г. Киев, ул. Боженко 11,
Тел. (044) 261-5349, Факс: (044) 268-0486, krivtsun@i.com.ua, http://www.plasma.kiev.ua/people/krivtsun.html
сплавов, латуни и меди показали существенное увеличение глубины проплавления по сравнению с лазерной сваркой в случае совпадения положения дугового кратера и фокуса лазерного пучка. Например, при лазернодуговой сварке труб из аустенитной стали диаметром 150 мм с толщиной стенки 4 мм полное проплавление было достигнуто при мощности лазера 450 Вт и токе дуги 25 А (Qa ≈ 190 Вт) [47], в то время как без дуги лазерный пучок той же мощности проплавлял металл лишь на несколько процентов его толщины, а для получения сквозного проплавления требовалось поднять мощность лазерного излучения до 1 кВт. Увеличение глубины проплавления в 3 и более раз наблюдалось и при комбинированной сварке пластин из нержавеющей стали толщиной 4 мм, о чем свидетельствуют приведенные в работе [48] зависимости геометрических параметров сварного шва от мощности лазерного пучка при различных значениях тока дуги и одной и той же скорости сварки. Авторами было замечено, что влияние дополнительного дугового нагрева на глубину проплавления металла уменьшается с ростом мощности лазерного излучения. При мощности излучения более 400 Вт изменение мощности дугового источника тепла от 180 до 600 Вт уже практически не сказывалось на глубине проплавления, а приводило лишь к расширению шва. Более того, если в комбинированном процессе использовалась дуга мощностью выше 600 Вт, шов расширялся настолько, что становился малоотличимым от шва, выполненного в отсутствие лазерного пучка. Таким образом, можно предположить, что для каждого фиксированного значения мощности лазерного излучения существует предел мощности электрической дуги, за которым форма шва, а значит, и характер теплового воздействия на обрабатываемый металл определяются преимущественно дуговым источником энергии, а роль лазерного пучка как одной из составляющих комбинированного источника тепла становится незначительной. Иными словами, существует оптимальное соотношение мощностей лазерного пучка и дуги, объединяемых в комбинированном процессе. В работе [48], например, было найдено, что в
32
© И.В. Кривцун, 2001 (ИЭС им. Е.О. Патона НАНУ, Украина, 03680, г. Киев, ул. Боженко 11,
Тел. (044) 261-5349, Факс: (044) 268-0486, krivtsun@i.com.ua, http://www.plasma.kiev.ua/people/krivtsun.html
случае лазерно-дуговой сварки труб из никелевого сплава с толщиной стенки 2,6 мм наилучшие результаты при мощности излучения 400 Вт дает использование дуги мощностью 120 Вт. Такое соотношение мощностей позволяло удвоить скорость сварки при сохранении формы шва, характерной для лазерной сварки, и, по-видимому, являлось оптимальным для данного технологического процесса.
Исследованию технологических особенностей и преимуществ комбинированной сварки толстолистовых (до 15 мм) низкоуглеродистых сталей посвящены работы [49-53] Хамазаки и других японских ученых. Наиболее полно результаты этих исследований изложены в обобщающей статье [52], которой следует уделить основное внимание.
Изучались два способа лазерно-дуговой сварки - с использованием неплавящегося и плавящегося электрода (в классификации комбинированных процессов, предложенной в предыдущем подразделе, они могут быть отнесены соответственно к Л+ДНЭ и Л+ДПЭ процессам). В первом случае использовалась схема процесса с расположением вольфрамового электрода - катода (диаметр 2,4 мм, угол наклона к поверхности изделия 45о, межэлектродный промежуток 1,0 мм) впереди лазерного пучка по ходу сварки, как показано на рис. 1.19. При этом дуга расплавляла верхний слой металла, а лазерный пучок осуществлял «кинжальное» проплавление. В экспериментах по Л+ДПЭ сварке дуговая горелка с плавящимся электродом - анодом (сварочная проволока диаметром 1,2 мм из малоуглеродистой стали, максимальный угол наклона к поверхности изделия 75о) устанавливалась позади лазерного пучка, как показано на рис. 1.20. Сварка осуществлялась на пластинах с различной формой разделки кромок, причем здесь, в отличие от Л+ДНЭ процесса, лазерное излучение оплавляло соприкасающиеся кромки свариваемого соединения, а заполнение разделки осуществляла дуга с расходуемым электродом.
33
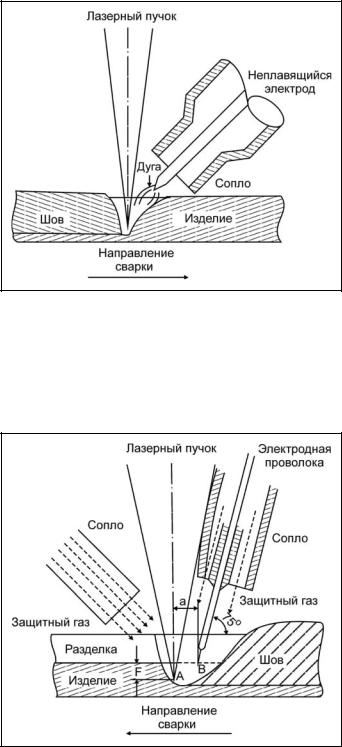
© И.В. Кривцун, 2001 (ИЭС им. Е.О. Патона НАНУ, Украина, 03680, г. Киев, ул. Боженко 11,
Тел. (044) 261-5349, Факс: (044) 268-0486, krivtsun@i.com.ua, http://www.plasma.kiev.ua/people/krivtsun.html
Рис. 1.19. Схема процесса лазерно-дуговой сварки при использовании дуги с неплавящимся электродом [52]
Рис. 1.20. Схема процесса лазерно-дуговой сварки при использовании дуги с
плавящимся электродом [52]
34
© И.В. Кривцун, 2001 (ИЭС им. Е.О. Патона НАНУ, Украина, 03680, г. Киев, ул. Боженко 11,
Тел. (044) 261-5349, Факс: (044) 268-0486, krivtsun@i.com.ua, http://www.plasma.kiev.ua/people/krivtsun.html
Результаты экспериментов по определению глубины проплавления при Л+ДНЭ сварке иллюстрируются рис. 1.21 - 1.27. В частности, на рис. 1.21 графически представлены зависимости глубины проплавления от скорости сварки при различной мощности лазерного излучения и постоянном токе дуги (штриховой кривой на этом же рисунке показана аналогичная зависимость для чисто лазерной сварки при мощности лазерного пучка 5 кВт). Сравнивая соответствующие зависимости для лазерно-дуговой и лазерной сварки, можно убедиться, что глубина проплавления в комбинированном процессе в 1,3…2,0 раза (в зависимости от скорости) превышает глубину проплавления в случае лазерной сварки пучком той же мощности. По оценке авторов работы [52], полученный ими эффект совместного воздействия лазерного излучения большой мощности (5 кВт) и дуги с неплавящимся электродом выше, чем в экспериментах Стина, [9, 10, 12, 13], который использовал лазер меньшей мощности (2 кВт).
Зависимости глубины проплавления от скорости сварки были измерены и для различных токов дуги при постоянной мощности лазерного излучения (рис. 1.22). На основе экспериментальных данных, приведенных на рис. 1.21, 1.22, построены кривые, иллюстрирующие зависимость глубины проплавления от тока дуги (рис. 1.23, а) и мощности лазерного излучения (рис. 1.23, б) при скорости сварки 1 м/мин. Эти рисунки наглядно доказывают, что использование дополнительного дугового нагрева позволяет получить ту же глубину проплавления, что и в случае лазерной сварки, при значительно меньшей мощности лазерного излучения.
Представляют интерес исследования авторов, направленные на определение оптимального расстояния между неплавящимся электродом и осью лазерного пучка (рис. 1.24) и оптимального интервала расположения фокальной плоскости пучка относительно поверхности образца (рис. 1.25 - 1.27) при Л+ДНЭ сварке. По данным работы [52], для получения максимального проплавления расстояние от рабочего конца неплавящегося
35
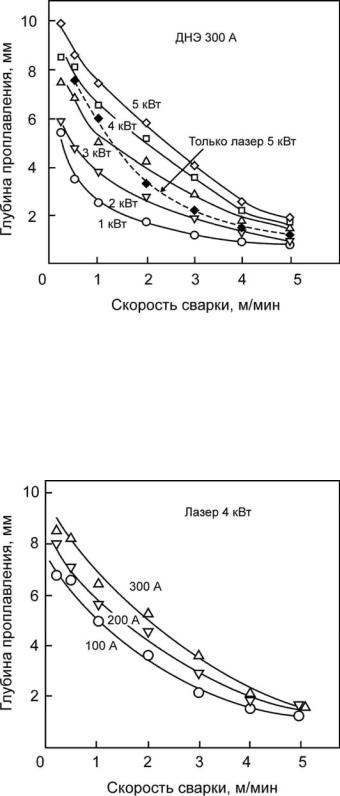
© И.В. Кривцун, 2001 (ИЭС им. Е.О. Патона НАНУ, Украина, 03680, г. Киев, ул. Боженко 11,
Тел. (044) 261-5349, Факс: (044) 268-0486, krivtsun@i.com.ua, http://www.plasma.kiev.ua/people/krivtsun.html
Рис. 1.21. Зависимости глубины проплавления от скорости Л+ДНЭ сварки стали при токе дуги 300 А и различных значениях мощности лазерного излучения [52]
Рис. 1.22. Зависимости глубины проплавления от скорости Л+ДНЭ сварки стали
при мощности лазерного излучения 4 кВт и различных значениях тока дуги [52]
36
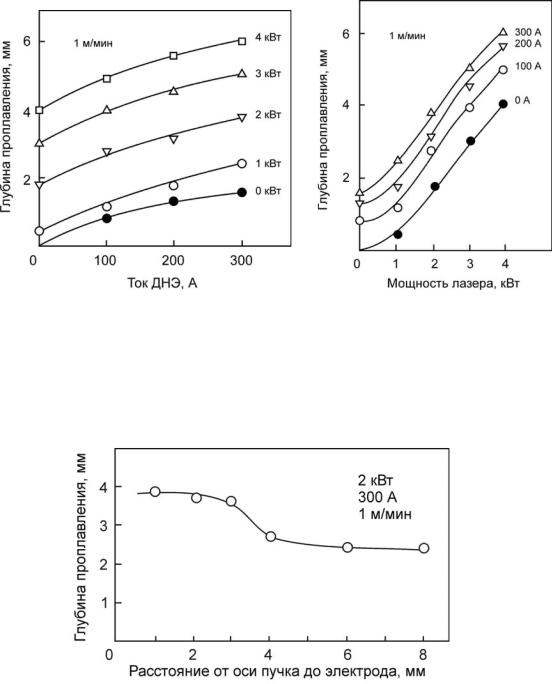
© И.В. Кривцун, 2001 (ИЭС им. Е.О. Патона НАНУ, Украина, 03680, г. Киев, ул. Боженко 11,
Тел. (044) 261-5349, Факс: (044) 268-0486, krivtsun@i.com.ua, http://www.plasma.kiev.ua/people/krivtsun.html
а б
Рис. 1.23. Зависимости глубины проплавления от тока дуги (а) и мощности лазер-
ного пучка (б) при постоянной скорости Л+ДНЭ сварки [52]
Рис. 1.24. Влияние расстояния неплавящегося электрода от оси лазерного пучка
на глубину проплавления при лазерно-дуговой сварке [52]
37
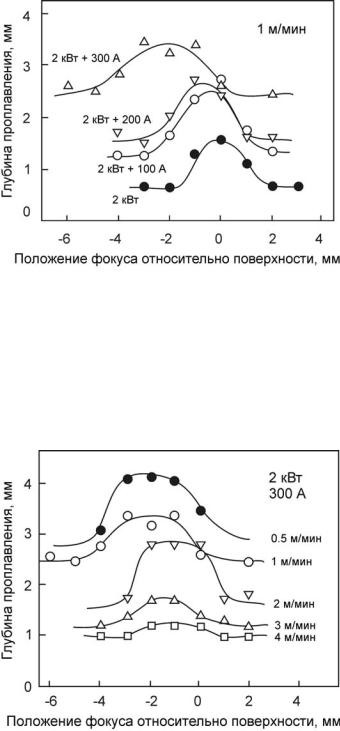
© И.В. Кривцун, 2001 (ИЭС им. Е.О. Патона НАНУ, Украина, 03680, г. Киев, ул. Боженко 11,
Тел. (044) 261-5349, Факс: (044) 268-0486, krivtsun@i.com.ua, http://www.plasma.kiev.ua/people/krivtsun.html
Рис. 1.25. Зависимости глубины проплавления от положения фокальной плоскости лазерного пучка относительно поверхности образца при различных значениях тока дуги (мощность лазерного излучения и скорость сварки постоянны) [52]
Рис. 1.26. Зависимости глубины проплавления от положения фокальной плоскости лазерного пучка при различных значениях скорости сварки
(мощность лазерного излучения и ток дуги постоянны) [52]
38
© И.В. Кривцун, 2001 (ИЭС им. Е.О. Патона НАНУ, Украина, 03680, г. Киев, ул. Боженко 11,
Тел. (044) 261-5349, Факс: (044) 268-0486, krivtsun@i.com.ua, http://www.plasma.kiev.ua/people/krivtsun.html
электрода до оси лазерного пучка должно лежать в интервале 2…3 мм. При меньших расстояниях существует опасность разрушения электрода под влиянием лазерного излучения, а при больших наблюдается уменьшение глубины проплавления (см. рис. 1.24), причиной которого, очевидно, является исчезновение эффекта «привязки» анодной области дуги к пятну лазерного нагрева. Оптимальный интервал расположения фокуса пучка относительно поверхности изделия (обеспечивающий глубину проплавления не менее 90 % ее максимального значения) может быть выбран по рис. 1.27. Как следует из этого рисунка, оптимальное положение фокальной плоскости по мере увеличения тока дуги смещается вниз от поверхности образца (рис. 1.27, а), и, наоборот, приближается к ней из глубины металла по мере увеличения скорости сварки (рис. 1.27, б). Этот эффект понятен, если иметь в виду, что фокус лазерного пучка должен отслеживать положение поверхности сварочной ванны, которое соответственно меняется с ростом тока дуги и скорости сварки.
Переходя к изложению результатов исследований авторов работы [52] по Л+ДПЭ сварке, отметим, что целью совместного использования лазера и дуги с плавящимся электродом было проверить возможность соединения этим методом пластин из малоуглеродистой стали толщиной 12 мм за один проход со скоростью 0,5 м/мин, чего не удавалось сделать ни с помощью сварки плавящимся электродом вплоть до тока 400 А, ни с помощью Л+ДНЭ сварки при мощности излучения 5 кВт и токе дуги 300 А. Л+ДПЭ сварка производилась в атмосфере гелия при мощности лазерного излучения до 5 кВт, токе дуги 400 А и различной форме разделки кромок.
Рисунки 1.28, 1.29 иллюстрируют зависимости глубины проплавления соответственно от расположения плавящегося электрода относительно лазерного пучка (т.е. параметра a на рис. 1.20) и положения фокуса пучка относительно дна разделки при различной форме последней. Как следует из рис. 1.28, максимальная глубина проплавления достигается при пересечении осей электрода и лазерного пучка на уровне дна разделки. Оптимальное же
39
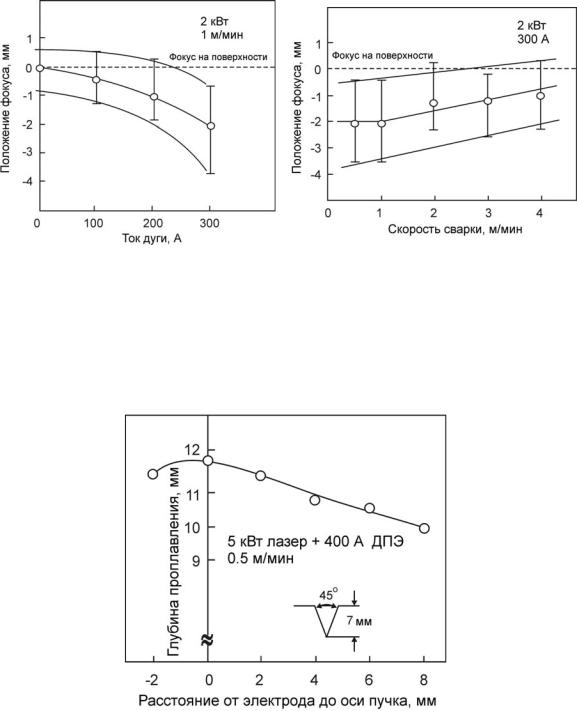
© И.В. Кривцун, 2001 (ИЭС им. Е.О. Патона НАНУ, Украина, 03680, г. Киев, ул. Боженко 11,
Тел. (044) 261-5349, Факс: (044) 268-0486, krivtsun@i.com.ua, http://www.plasma.kiev.ua/people/krivtsun.html
а |
б |
Рис. 1.27. Зависимость оптимального (обеспечивающего максимальную глубину проплавления) положения фокальной плоскости пучка относительно
поверхности изделия от тока дуги (а) и скорости Л+ДНЭ сварки (б) [52]
Рис. 1.28. Влияние расстояния плавящегося электрода от оси лазерного пучка на
глубину проплавления при Л+ДПЭ сварке [52]
40
© И.В. Кривцун, 2001 (ИЭС им. Е.О. Патона НАНУ, Украина, 03680, г. Киев, ул. Боженко 11,
Тел. (044) 261-5349, Факс: (044) 268-0486, krivtsun@i.com.ua, http://www.plasma.kiev.ua/people/krivtsun.html
положение фокуса находится ниже указанного уровня (см. рис. 1.29), что связано с прогибом поверхности сварочной ванны в результате силового воздействия дуги. Наконец, представленная на рис. 1.30 зависимость глубины проплавления от мощности лазерного излучения при Л+ДНЭ сварке позволяет сделать вывод, что лазерным пучком мощностью 4 кВт в комбинации с дугой, горящей в атмосфере гелия при токе 400 А, можно сваривать пластины толщиной 12 мм со скоростью 0,5 м/мин, применив V-образную разделку кромок на глубину 7 мм с углом их раскрытия 45о. Авторы работы [52] отмечают, что, повысив мощность излучения до 5 кВт, можно осуществить сварку более толстых пластин при той же скорости либо увеличить скорость сварки пластин толщиной 12 мм до 0,8 м/мин.
Кроме описанных выше экспериментальных данных, в рассматриваемой работе приводятся фотографии макрошлифов поперечных сечений швов, выполненных Л+ДНЭ сваркой (при различных значениях скорости, тока дуги и мощности лазерного пучка), а также Л+ДПЭ сваркой в сравнении с лазерной сваркой и сваркой плавящимся электродом. Относительно качества сварных соединений сообщается, что как при Л+ДНЭ, так и при Л+ДПЭ сварке наблюдалось хорошее формирование швов, отсутствовали подрезы и неравномерные усиления, присущие швам, выполненным, например, сваркой неплавящимся электродом на аналогичных режимах, а также поры и раковины. В результате обеспечивались высокие механические свойства получаемых соединений.
Заканчивая обзор работ [49-53], следует отметить, что авторы, высоко оценивая технологические возможности исследованных способов лазернодуговой сварки, делают вывод о перспективности их применения в промышленном производстве, поскольку комбинированные технологии не требуют лазерных установок большой мощности и в то же время позволяют реализовать преимущества лазерной сварки в отношении как формы и качества сварного шва, так и производительности процесса.
41
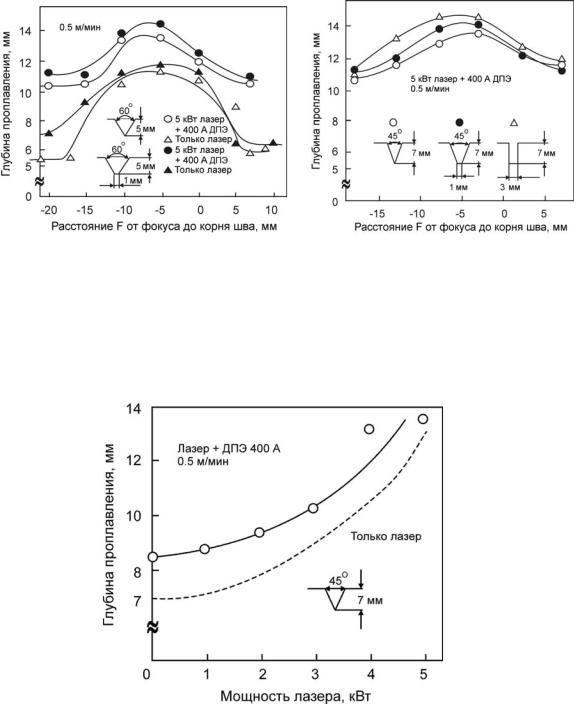
© И.В. Кривцун, 2001 (ИЭС им. Е.О. Патона НАНУ, Украина, 03680, г. Киев, ул. Боженко 11,
Тел. (044) 261-5349, Факс: (044) 268-0486, krivtsun@i.com.ua, http://www.plasma.kiev.ua/people/krivtsun.html
а б
Рис. 1.29. Влияние положения фокальной плоскости пучка на глубину проплав-
ления при лазерной (а) и Л+ДПЭ (а), (б) сварке стальных пластин с
различной формой разделки кромок [52]
Рис. 1.30. Глубина проплавления в зависимости от мощности лазерного излучения при постоянной скорости сварки: сплошная кривая - Л+ДПЭ
сварка при токе дуги 400 А; штриховая кривая - лазерная сварка [52]
42
© И.В. Кривцун, 2001 (ИЭС им. Е.О. Патона НАНУ, Украина, 03680, г. Киев, ул. Боженко 11,
Тел. (044) 261-5349, Факс: (044) 268-0486, krivtsun@i.com.ua, http://www.plasma.kiev.ua/people/krivtsun.html
Опубликованная американскими учеными в 1984 г. статья [54] является первой работой, посвященной изучению технологических особенностей лазерно-дуговой сварки алюминия и его сплавов. Авторы поставили перед собой задачу не только исследовать влияние различных параметров комбинированного процесса на глубину проплавления и устойчивость горения дуги при сварке алюминиевого сплава, но и дать трактовку полученных результатов на основе физических представлений о механизме взаимодействия дуги и лазерного пучка.
В экспериментах использовался СO2-лазер непрерывного действия мощностью 600 Вт и дуговая горелка с вольфрамовым электродом (катодом) диаметром 2,4 мм, установленная впереди лазерного пучка по ходу сварки так, что угол между поверхностью изделия и электродом составлял 45о, а расстояние от рабочего конца электрода до оси лазерного пучка не превышало 3,2 мм. Проводилась Л+ДНЭ сварка с неполным проплавлением стыковых соединений пластин из алюминиевого сплава 5052 толщиной 3,2 мм. Полученные результаты сравнивались с результатами не лазерной (как в большинстве рассмотренных выше работ), а дуговой сварки таких же образцов, т.к. при лазерной сварке не удавалось получить заметного проплавления из-за недостаточной мощности лазера.
Экспериментальные данные, приведенные на рис. 1.31 - 1.33, свидетельствуют об увеличении глубины проплавления и улучшении стабильности дуги в комбинированном процессе по сравнению с дуговой сваркой неплавящимся электродом. В частности, относительное увеличение глубины проплавления в диапазоне используемых режимов сварки составило 20-50 % (ср. рис. 1.31, 1.32). По мнению авторов работы [54], это меньше, чем эффект дополнительного лазерного воздействия при сварке углеродистых сталей, и объясняется известными трудностями сварки алюминиевых сплавов лазерным излучением малой мощности. Заметим, однако, что если привлечь данные работы [52] (см., например, рис. 1.23, а), то эффекты увеличения глубины
43
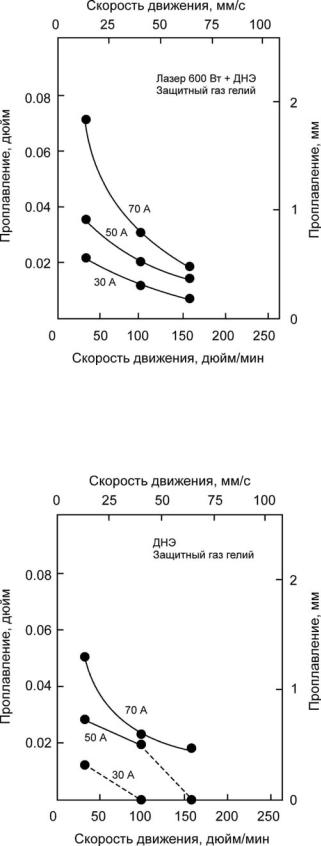
© И.В. Кривцун, 2001 (ИЭС им. Е.О. Патона НАНУ, Украина, 03680, г. Киев, ул. Боженко 11,
Тел. (044) 261-5349, Факс: (044) 268-0486, krivtsun@i.com.ua, http://www.plasma.kiev.ua/people/krivtsun.html
Рис. 1.31. Зависимости глубины проплавления от скорости лазерно-дуговой
(Л+ДНЭ) сварки алюминия при различных значениях тока дуги [54]
Рис. 1.32. Зависимости глубины проплавления от скорости дуговой (ДНЭ) сварки алюминия при различных значениях тока (штриховые участки кривых соответствуют нестабильному горению дуги) [54]
44
© И.В. Кривцун, 2001 (ИЭС им. Е.О. Патона НАНУ, Украина, 03680, г. Киев, ул. Боженко 11,
Тел. (044) 261-5349, Факс: (044) 268-0486, krivtsun@i.com.ua, http://www.plasma.kiev.ua/people/krivtsun.html
проплавления для стали и алюминия при прочих равных условиях можно оценить как соизмеримые. В работе [54] отмечается также, что, несмотря на увеличение глубины проплавления в комбинированном процессе, форма шва остается при всех используемых токах дуги типичной для дуговой сварки. Это позволяет предположить, что при лазерно-дуговой сварке алюминиевых сплавов эффект контрагирования дуги проявляется менее отчетливо, чем, например, при комбинированной сварке сталей [10, 12]. Причина такого различия в поведении дуги может заключаться в увеличении с ростом теплопроводности металла поперечных размеров зоны его лазерного испарения, определяющих степень контрагирования анодной области дуги.
При исследовании стабильности процесса лазерно-дуговой сварки алюминиевого сплава в сравнении со сваркой неплавящимся электродом было установлено, что дуга в присутствии лазерного излучения стабилизируется, в результате чего появляется возможность увеличить скорость сварки, причем этот эффект наиболее заметен на малых токах. С помощью комбинированного процесса авторам удалось получить гладкие, однородные швы при скорости сварки вплоть до 30,5 м/мин и токе дуги 70 А, в то время как дуговая сварка на этом токе позволяла достичь скорости не более 20,3 м/мин.
В работе [54] предлагаются три возможных механизма для объяснения наблюдаемых явлений. Это стабилизация анодного пятна дуги в присутствии лазерного пучка, увеличение поглощения энергии пучка поверхностью изделия вследствие нагрева обрабатываемого металла дугой и, наконец, непосредственное взаимодействие лазерного излучения с дуговой плазмой. Авторы работы [54] считают, что при мощности лазерного пучка 600 Вт два последних механизма не вносят существенного вклада в повышение стабильности процесса и увеличение глубины проплавления, а определяющую роль играет стабилизация анодного пятна дуги в зоне лазерного нагрева. С таким утверждением можно, вообще говоря, согласиться, однако нужно заметить, что физический механизм, лежащий в основе наблюдаемого авторами
45
© И.В. Кривцун, 2001 (ИЭС им. Е.О. Патона НАНУ, Украина, 03680, г. Киев, ул. Боженко 11,
Тел. (044) 261-5349, Факс: (044) 268-0486, krivtsun@i.com.ua, http://www.plasma.kiev.ua/people/krivtsun.html
эффекта стабилизации (также как и явления контрагирования анодной области дуги), - это появление в приповерхностной плазме в результате лазерного испарения металла паров алюминия, имеющих более низкий потенциал ионизации, чем гелий. Этим же можно объяснить и отмеченный в работе [54] эффект облегчения возбуждения дуги в присутствии лазерного пучка.
Сведения о реализации Л+ДНЭ сварки алюминия и его сплавов малых толщин, также как и других тонколистовых металлов, находим и в более поздних публикациях [55-58]. Авторы этих работ отмечают так называемый синергетический эффект совместного использования лазерного излучения и электрической дуги (эффект нарушения аддитивности теплового воздействия на изделие лазерного пучка и дуговой плазмы, о котором упоминалось выше). В работе [55], например, указывается, что в экспериментах по лазерно-дуговой сварке алюминия СО2-лазером мощностью 1,2 кВт и дугой с неплавящимся электродом при токе 60 А и скорости сварки 0,25 м/мин объем расплавленного металла на 77 % превышал простую сумму объемов расплавов, полученных в случае использования каждого из источников тепла в отдельности. В вышеупомянутых публикациях подчеркивается, что комбинированным способом удается получить качественные швы на алюминии при относительно малых мощностях лазерного пучка и дуги, а также высокой скорости сварки, чего не удавалось достичь лазерной сваркой при гораздо более высокой мощности лазерного излучения. Этим преимуществом комбинированного процесса воспользовались авторы работы [57], применив для сварки алюминиевого сплава толщиной ≥ 3 мм твердотельный ИАГ-лазер мощностью всего 360 Вт совместно с горелкой для сварки дугой с неплавящимся электродом на токе 50 А. Достигнутые ими параметры проплавления и производительность процесса оказались сравнимыми с получаемыми при сварке ИАГ-лазером мощностью 2 кВт.
Достоинства лазерно-дуговой сварки тонколистового алюминия и нержавеющей стали демонстрируются в работах [56, 58], где сравниваются
46
© И.В. Кривцун, 2001 (ИЭС им. Е.О. Патона НАНУ, Украина, 03680, г. Киев, ул. Боженко 11,
Тел. (044) 261-5349, Факс: (044) 268-0486, krivtsun@i.com.ua, http://www.plasma.kiev.ua/people/krivtsun.html
основные параметры режимов для трех способов сварки: ДНЭ, комбинированной (Л+ДНЭ) и лазерной. Так, при мощности лазерного излучения в интервале от 0,1 до 1,5 кВт (для двух последних способов), длине дуги 6 мм и 10 мм (соответственно для двух первых способов), типичная скорость сварки составляла 0,5; 2,0 и 1,0 м/мин, отношение глубины проплавления к ширине шва - 0,5; 2,0 и 1,0, а погонная энергия – 320; 50 и 160 Дж/мм соответственно. Отмечается улучшение стабильности горения дуги в комбинированном процессе и облегчение ее зажигания. Подчеркивается, что комбинированным способом удается сваривать листы очень малой толщины и соединять разнотолщинные элементы, не обеспечивая высокой точности сборки стыков, как это необходимо для лазерной сварки.
Положительные результаты по комбинированной сварке тонколистовых (0,5…1,0 мм) металлов, в том числе алюминия, но уже способом Л+ПД получены в упомянутой ранее работе [36], опубликованной английскими учеными из университета в Ковентри. Сварка осуществлялась с использованием СО2-лазера непрерывного действия мощностью 400 Вт и стандартной плазменной горелки, расположенной под углом к оси лазерного пучка впереди по ходу сварки (см. рис. 1.10). Обосновывая целесообразность замены в комбинированном процессе свободногорящей (открытой) дуги на плазменную (сжатую) дугу, авторы [36] указывают на целый ряд существенных недостатков Л+ДНЭ процесса, из-за которых он, несмотря на отмечаемые всеми исследователями потенциальные возможности, до сих пор не нашел широкого промышленного применения. Ограничения Л+ДНЭ способа сварки обусловлены главным образом особенностями поведения открытой дуги, которые проявляются даже в присутствии лазерного пучка, отрицательно влияя на характер комбинированного процесса в целом. Это общеизвестные трудности, связанные с зажиганием дуги и пространственной неустойчивостью ее столба при малых токах и больших скоростях перемещения дуговой горелки относительно изделия.
47
© И.В. Кривцун, 2001 (ИЭС им. Е.О. Патона НАНУ, Украина, 03680, г. Киев, ул. Боженко 11,
Тел. (044) 261-5349, Факс: (044) 268-0486, krivtsun@i.com.ua, http://www.plasma.kiev.ua/people/krivtsun.html
Как и ожидалось, применение в комбинированном процессе вместо свободногорящей дуги плазменной (сжатой) дуги позволило реализовать преимущества последней и такой комбинации в целом. Были получены следующие результаты: обеспечено надежное возбуждение дуги (за счет использования дежурной дуги) и увеличен срок службы вольфрамового электрода. Что касается положительных эффектов достигнутым способом Л+ПД по сравнению с лазерной или плазменной сваркой, то они аналогичны тем, которые наблюдались при реализации других типов комбинированных процессов и рассматривались выше. В частности, имел место явно выраженный синергетический эффект, в результате которого объем расплавленного металла при Л+ПД сварке оказывался больше суммы соответствующих объемов при лазерной и плазменной сварке по отдельности. Благодаря этому авторам работы [36] удалось увеличить скорость сварки тонколистовых металлов в 2…3 раза по сравнению с лазерной сваркой. Так стыковой шов с полным проплавлением на нержавеющей стали толщиной 0,6 мм был выполнен при мощности лазера 400 Вт и токе дуги 50 А на скорости 2,5 м/мин, которая в 2,5 раза превышает скорость достигаемую при использовании одного лишь лазера той же мощности. Взаимосвязь между током плазменной дуги и скоростью комбинированной сварки нержавеющей стали указанной толщины может быть проиллюстрирована с помощью рис. 1.34. Швы с полным проплавлением при тех же значениях параметров режима сварки были успешно выполнены и на титановом сплаве Ti-6Al-4V толщиной 0,75 мм.
Метод Л+ПД сварки особенно отчетливо проявил свои достоинства при сварке алюминия. Авторами [36] получены качественные стыковые швы с полным проплавлением на неочищенном алюминии толщиной 0,6 мм при скорости сварки 0,5 м/мин и малых токах дуги (скорость сварки ограничивалась лишь мощностью имеющегося лазера). При этом анодное пятно дуги, сформировавшись в пределах зоны нагрева металла, создаваемой лазерным пучком, перемещалось вместе с ней, что обеспечивало непрерывность швов и
48
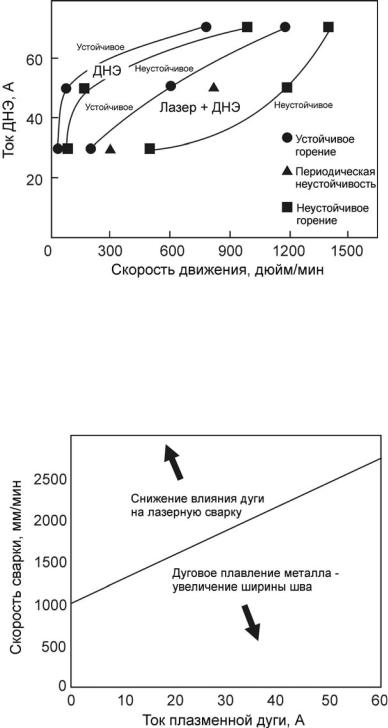
© И.В. Кривцун, 2001 (ИЭС им. Е.О. Патона НАНУ, Украина, 03680, г. Киев, ул. Боженко 11,
Тел. (044) 261-5349, Факс: (044) 268-0486, krivtsun@i.com.ua, http://www.plasma.kiev.ua/people/krivtsun.html
Рис. 1.33. Области устойчивого и неустойчивого горения дуги при дуговой (ДНЭ)
и лазерно-дуговой (Л+ДНЭ) сварке алюминия (мощность лазерного излучения 600 Вт, защитный газ - гелий) [54]
Рис. 1.34. Оптимальное соотношение между скоростью сварки и током плазменной дуги при лазерно-плазменной сварке нержавеющей стали толщиной 0,6 мм (мощность CO2-лазера 400 Вт) [36]
49
© И.В. Кривцун, 2001 (ИЭС им. Е.О. Патона НАНУ, Украина, 03680, г. Киев, ул. Боженко 11,
Тел. (044) 261-5349, Факс: (044) 268-0486, krivtsun@i.com.ua, http://www.plasma.kiev.ua/people/krivtsun.html
полное проплавление образца. Отметим, что попытки авторов рассматриваемой работы выполнить швы на алюминии с помощью плазменной либо лазерной сварки оказались безуспешными, в первом случае из-за блуждания анодного пятна дуги, во втором - из-за недостаточной мощности лазера.
Как преимущества Л+ПД сварки по сравнению с лазерной в работе [36] отмечаются более благоприятная с точки зрения прочности сварного соединения форма поперечного сечения швов и значительно более мягкие требования к точности сборки стыков и величине допустимого отклонения лазерного пучка от линии сплавления. Так, в отличие от лазерной сварки, где зазоры между стыкуемыми элементами не должны превышать 5…10 % толщины металла, при комбинированной сварке допустимы зазоры вплоть до
25…30 %.
Завершая обзор основных результатов работы [36], отметим, что проведенные исследования позволили ее авторам сделать вывод о более широких возможностях применения в промышленности Л+ПД сварки по сравнению с Л+ДНЭ сваркой и о необходимости дальнейшего изучения лазерно-плазменных процессов, в том числе реализуемых с помощью СО2- лазеров большей мощности или твердотельных ИАГ-лазеров. Отметим также актуальность поставленной авторами [36] задачи создания специализированных устройств для промышленной реализации Л+ПД процесса - интегрированных лазерных головок (лазерно-дуговых плазмотронов).
В более поздней работе [59] сотрудника того же университета, представлены результаты дальнейших исследований процесса Л+ПД сварки тонколистовых сталей и алюминиевых сплавов с использованием как СО2-, так и ИАГлазеров мощностью от 400 Вт до 6 кВт. В ходе этих исследований были получены хорошие результаты по комбинированной сварке стыковых соединений из разнотолщинных металлов, отмечено существенное снижение растрескивания шва вблизи основного металла по сравнению с лазерной сваркой алюминиевого сплава 6000 толщиной 2 мм, достигнуты скорости
50
© И.В. Кривцун, 2001 (ИЭС им. Е.О. Патона НАНУ, Украина, 03680, г. Киев, ул. Боженко 11,
Тел. (044) 261-5349, Факс: (044) 268-0486, krivtsun@i.com.ua, http://www.plasma.kiev.ua/people/krivtsun.html
сварки на 40 % превышающие соответствующие значения при лазерной сварке. Так, например, при Л+ПД сварке тонколистовых сталей непрерывные швы с полным проплавлением были получены на скоростях до 60 м/мин, причем стабильность процесса сварки сохранялась вплоть до скоростей порядка 90 м/мин. На основании полученных данных автор работы [59] делает вывод о том, что комбинированные лазерно-плазменные процессы позволяют преодолеть многие проблемы традиционной лазерной сварки и могут в ближайшем будущем существенно потеснить промышленные лазерные технологии.
Вопрос о расширении промышленного применения новых лазернодуговых технологий, в частности, об использовании их при производстве автомобилей, впервые обсуждался на международной конференции IBEC-94 в Детройте [60]. В ходе представления гибридного лазерно-дугового способа сварки листовых сталей и алюминия, осуществляемого путем комбинированного воздействия на изделие излучения ИАГ-лазера и дуги с неплавящимся электродом, было подчеркнуто, что этот способ имеет ряд достоинств, особенно важных для автомобильной промышленности, а именно: 50 % уменьшение стоимости сварки; такое же (50 %) увеличение производительности; снижение затрат на подготовку кромок; возможность контроля ширины шва и, наконец, сохранение первоначальной гибкости конструкции после сварки.
Анализируя в целом публикации последнего десятилетия, посвященные комбинированным лазерно-дуговым процессам, можно сделать вывод о том, что интерес к этим процессам не только не исчезает, но постепенно перемещается из сферы экспериментальных исследований в сферу промышленного производства. Вопрос о перспективах дальнейшего развития лазерно-дуговых технологий звучит и в названии уже упомянутой статьи [39], которое сформулировано автором следующим образом: «Синергетический эффект совместного использования сварочной дуги и лазерного пучка - для
51
© И.В. Кривцун, 2001 (ИЭС им. Е.О. Патона НАНУ, Украина, 03680, г. Киев, ул. Боженко 11,
Тел. (044) 261-5349, Факс: (044) 268-0486, krivtsun@i.com.ua, http://www.plasma.kiev.ua/people/krivtsun.html
практического применения или только для научных исследований?» Эта работа является по существу обзорной, обобщающей и анализирующей достижения ученых разных стран в области лазерно-дуговых процессов.
Автор [39] делает краткий экскурс в историю развития лазерно-дуговой сварки, описывает преимущества комбинированных процессов, которые неоднократно обсуждались выше, особо подчеркивает синергетический эффект совместного использования лазерного излучения и электрической дуги. Отметив недостатки Л+ДНЭ сварки автор переходит к анализу работ по Л+ДПЭ, а также Л+ПД сварке и делает вывод, что последние способы являются более перспективными для практического применения с точки зрения диапазона толщин и типа свариваемых металлов. Что касается Л+ДНЭ процесса, то он, несмотря на определенные недостатки, также должен найти в будущем более широкое применение, в чем убеждает имеющийся положительный опыт его использования (в частности, с присадкой) для сварки сложных тонкостенных конструкций и в ряде других случаев.
Автор [39] считает, что лазерно-дуговые процессы представляют интерес и с точки зрения теоретических и экспериментальных исследований, поскольку существует еще много нерешенных вопросов, например, касающихся влияния длины волны и мощности лазерного излучения на степень ионизации дуговой плазмы при разных токах дуги. Тем самым он не противопоставляет вынесенные в заголовок статьи направления развития комбинированных процессов или не выбирает лишь одно из них, а видит перспективы и того и другого.
В более поздней обзорной работе немецких ученых [45], также посвященной перспективам развития лазерно-дуговой сварки, авторы отдельно рассматривают технологические возможности комбинирования лазерной и дуговой сварки (когда дуга и лазерный пучок воздействуют на изделие на некотором расстоянии друг от друга) и их объединения (когда оба источника тепла воздействуют на изделие в пределах общей сварочной ванны), называя
52
© И.В. Кривцун, 2001 (ИЭС им. Е.О. Патона НАНУ, Украина, 03680, г. Киев, ул. Боженко 11,
Тел. (044) 261-5349, Факс: (044) 268-0486, krivtsun@i.com.ua, http://www.plasma.kiev.ua/people/krivtsun.html
последние способы гибридными процессами сварки. Как пример комбинации лазерного и дугового процессов рассматривается сварка стыковых соединений из низколегированной стали толщиной 20 мм с Y-образной разделкой кромок, при этом лазерное излучение (СО2-лазер, мощность 6,3 кВт) используется для сварки корня шва (скорость сварки 0,6 м/мин), а следующая на определенном расстоянии за лазерным пучком ДПЭ (напряжение 35 В, ток дуги 530 А, скорость подачи проволоки 27,5 м/мин) используется для заполнения разделки. Данная комбинация позволяет существенно снизить твердость металла корневого шва по сравнению с лазерной сваркой, причем наиболее однородное распределение твердости между основным металлом и металлом шва достигается при расстоянии между лазерным пучком и дугой равном 30 мм.
Переходя к рассмотрению известных способов объединения лазерного и дугового источников тепла в пределах общей сварочной ванны, таких как Л+ДНЭ, Л+ПД, Л+ДПЭ процессы, авторы [45] подробно описывают технологические возможности каждого из указанных способов применительно к сварке сталей и алюминиевых сплавов. Особое внимание уделяется Л+ДПЭ сварке, в том числе новому процессу, объединяющему лазерный пучок и две ДПЭ. По данным авторов такой процесс позволяет повысить скорость сварки на 33 % по сравнению с однодуговой Л+ДПЭ сваркой и на 800 % по сравнению со сваркой погруженной дугой. Как одно из достоинств процесса гибридной сварки с использованием двух дуг отмечается также существенное снижение погонной энергии, которое составляет 25 % по отношению к обычному Л+ДПЭ процессу и 83 % по отношению к процессу сварки погруженной дугой.
Подробный анализ преимуществ гибридной сварки (Л+ДПЭ) по сравнению с лазерной и дуговой сваркой плавящимся электродом, а также некоторые примеры практического использования указанного способа при сварке алюминиевых сплавов различного состава приведены в работах [61, 62]. Кроме того, авторами [62] проведен сравнительный анализ геометрии сварных швов, полученных лазерной (ИАГ-лазер), дуговой (ДПЭ) и гибридной сваркой
53
© И.В. Кривцун, 2001 (ИЭС им. Е.О. Патона НАНУ, Украина, 03680, г. Киев, ул. Боженко 11,
Тел. (044) 261-5349, Факс: (044) 268-0486, krivtsun@i.com.ua, http://www.plasma.kiev.ua/people/krivtsun.html
алюминия (параметры режимов выбирались таким образом, чтобы обеспечить одинаковую глубину проплавления металла при одной и той же скорости сварки). В частности, при лазерной сварке без присадочной проволоки поверхность шва несколько провисает (рис. 1.35, а), тогда как в случае дуговой сварки плавящимся электродом шов характеризуется значительным усилением
иимеет существенно большую ширину при той же глубине проплавления (рис. 1.35, б). В аналогичных условиях гибридный процесс позволяет получить более узкий профиль проплавления при вдвое меньшем расходе электродной проволоки, уменьшив тем самым излишнее усиление шва (рис. 1.35, в).
Вкачестве основных преимуществ гибридного процесса по сравнению с лазерной сваркой авторы [61, 62] отмечают улучшение сплавляемости и снижение требований к сборке стыков; увеличение глубины проплавления и скорости сварки; повышение пластичности швов после сварки; снижение капиталовложений. Что касается преимуществ Л+ДПЭ процесса по сравнению
сдуговой сваркой плавящимся электродом, то здесь отмечается существенное повышение скорости сварки и глубины проплавления; уменьшение ширины швов и снижение погонной энергии; повышение прочности швов на растяжение
идр.
Несмотря на то, что в рассмотренных выше публикациях мы не находим ссылок на работы ученых из стран СНГ, это не означает, что исследования лазерно-дуговых процессов там не проводились (первое упоминание об исследованиях, проведенных в бывшем СССР в области лазерно-дуговых способов металлообработки, относится к 1984 г. [63]). Обзор этих работ, посвященных изучению технологических возможностей комбинированных процессов металлообработки, следует начать с работы [64]. В ней, в частности, освещается опыт использования Л+ДНЭ сварки в трубосварочном производстве. Авторы сваривали прямошовные трубы диаметром 38 мм из стали 08Х18Н10Т толщиной 1,5 мм на скоростях от 2,5 до 3,5 м/мин. Излучение СO2-лазера (мощность 2,5 кВт) фокусировали в хвостовую часть сварочной
54
© И.В. Кривцун, 2001 (ИЭС им. Е.О. Патона НАНУ, Украина, 03680, г. Киев, ул. Боженко 11,
Тел. (044) 261-5349, Факс: (044) 268-0486, krivtsun@i.com.ua, http://www.plasma.kiev.ua/people/krivtsun.html
ванны, создаваемой дугой с неплавящимся электродом, горящей в аргоне на постоянном токе (50…250 А). При лазерно-дуговой сварке отмечено улучшение формирования шва, особенно в его верхней части, по сравнению с лазерной сваркой, что позволяет снизить требования к подготовке кромок и сборке стыка.
Упомянутая ранее статья [35] посвящена комбинированной резке пластин из нержавеющей стали толщиной до 2 мм и примечательна тем, что в качестве составляющих источника тепла были применены сфокусированное излучение твердотельного лазера и дуга косвенного действия (Л+ПС процесс). Авторы использовали ИАГ-лазер непрерывного действия мощностью около 200 Вт, работающий на длине волны излучения 1,06 мкм, и плазмотрон мощностью до 1 кВт со сменным соплом - анодом дуги, горящей с вольфрамового электрода в потоке аргона. Лазерная головка, в сопло которой подавался воздух, устанавливалась над пластиной под углом 60о к ее поверхности, а плазмотрон - вертикально под пластиной.
В рассматриваемой работе приводятся результаты экспериментальных исследований влияния основных параметров режима Л+ПС резки на ее производительность. Эксперименты показали, что лазерно-плазменная резка позволяет значительно повысить скорость обработки по сравнению с лазерной резкой, не снижая качества реза. Так, при электрической мощности плазменной дуги 880 Вт (по оценке авторов это соответствует мощности, вкладываемой в изделие, 440 Вт) и мощности лазерного излучения 150 Вт скорость увеличивалась приблизительно вдвое (рис. 1.36), при этом ширина реза и размер зоны термического влияния оставались близкими к соответствующим значениям, характерным для лазерного процесса (ср. рис. 1.37, 1.38). Отмечая, что с увеличением мощности плазменной дуги выше указанного значения скорость комбинированной резки не возрастала, а параметры и качество реза становились типичными для плазменного процесса, авторы делают вывод о существовании некоторого оптимального соотношения мощностей, вкладываемых
55
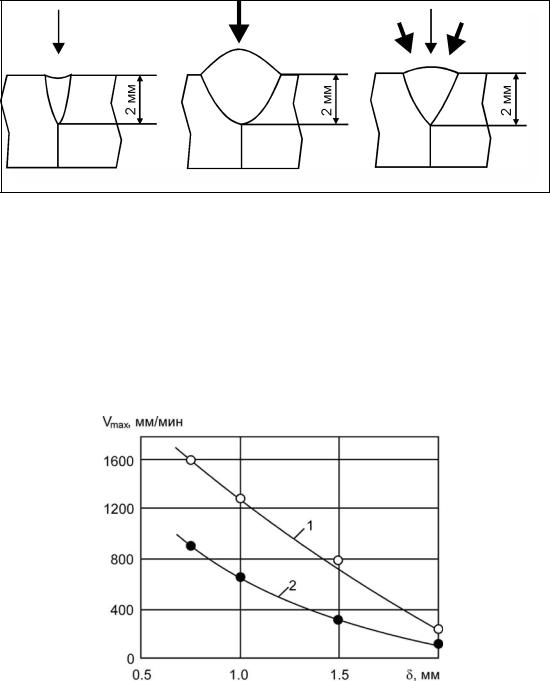
© И.В. Кривцун, 2001 (ИЭС им. Е.О. Патона НАНУ, Украина, 03680, г. Киев, ул. Боженко 11,
Тел. (044) 261-5349, Факс: (044) 268-0486, krivtsun@i.com.ua, http://www.plasma.kiev.ua/people/krivtsun.html
а б в
Рис. 1.35. Геометрия швов, полученных различными способами при одинаковой
глубине проплавления и скорости сварки 1 м/мин: (а) - лазерная сварка (мощность лазера 2 кВт); (б) - дуговая сварка плавящимся электродом (ток дуги 95 А, напряжение 20 В, скорость подачи проволоки 11 м/мин);
(в) – гибридная (Л+ДПЭ) сварка (мощность лазера 1,5 кВт, скорость подачи проволоки 5,5 м/мин) [62]
Рис. 1.36. Максимальная скорость резки пластин из нержавеющей стали в зависимости от их толщины: 1 - Л+ПС резка (мощность лазера 150 Вт, диаметр сопла плазмотрона 1,5 мм, мощность, вводимая плазменной
струей, 440 Вт); 2 - лазерная резка (мощность лазера 150 Вт, размер пятна фокусировки 0,5 мм) [35]
56
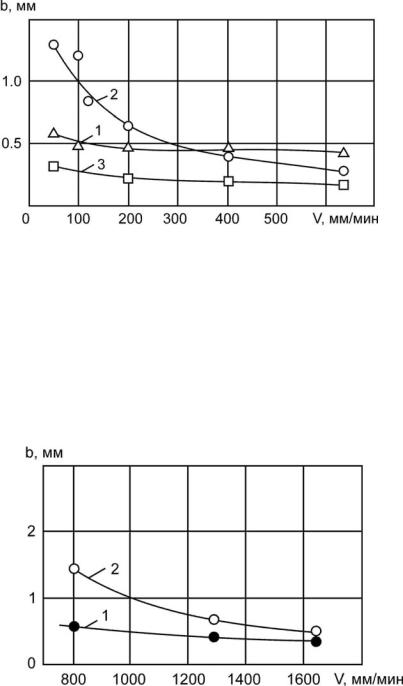
© И.В. Кривцун, 2001 (ИЭС им. Е.О. Патона НАНУ, Украина, 03680, г. Киев, ул. Боженко 11,
Тел. (044) 261-5349, Факс: (044) 268-0486, krivtsun@i.com.ua, http://www.plasma.kiev.ua/people/krivtsun.html
Рис. 1.37. Зависимости ширины реза и размера зоны термического влияния от
скорости лазерной резки нержавеющей стали толщиной 1,5 мм
(расстояние лазерной головки от поверхности образца 1 мм, остальные параметры те же, что и на рис. 1.34): 1 и 3 - ширина реза со стороны лазерного пучка и с противоположной стороны; 2 - размер зоны термического влияния [35]
Рис. 1.38. Размер зоны термического влияния и ширина реза в зависимости от скорости Л+ПС резки нержавеющей стали толщиной 1,5 мм (параметры те же, что и на рис. 1.34, 1.35): 1 - ширина зоны термического влияния; 2 – ширина реза [35]
57
© И.В. Кривцун, 2001 (ИЭС им. Е.О. Патона НАНУ, Украина, 03680, г. Киев, ул. Боженко 11,
Тел. (044) 261-5349, Факс: (044) 268-0486, krivtsun@i.com.ua, http://www.plasma.kiev.ua/people/krivtsun.html
плазменной струей и лазерным пучком в обрабатываемый металл, и оценивают его как не превышающее 3:1. Однако при определении теплового вклада плазменной струи в изделие авторы учитывают лишь КПД нагрева металла плазмой, забывая, например, о потерях энергии на аноде плазмотрона. С учетом этих потерь мощность, вкладываемая в изделие плазменной струей, будет существенно меньше 440 Вт. Поэтому более точным будет следующий вывод: для получения наилучшего эффекта при лазерно-плазменной резке мощности, вносимые в обрабатываемый металл плазменной струей и лазерным излучением, должны быть приблизительно равными. Это утверждение аналогично сделанному в работе [12] для комбинированной резки с использованием дуги прямого действия.
В работах [65-68] предпринята попытка оценить эффективность использования лазерно-дугового нагрева при осуществлении различных видов термообработки материалов, в том числе поверхностного упрочнения, наплавки, легирования и т.п. С этой целью вводится ряд количественных характеристик комбинированного процесса, в частности, коэффициент энерговклада Kla = Qa/Ql, где Qa, Ql - мощности дуги и лазерного пучка соответственно, и эффективность лазерно-дугового воздействия ηla = (ηlQl + ηaQa)/(Ql + Qa), где ηl - коэффициент поглощения лазерного излучения обрабатываемым металлом, ηa - коэффициент использования энергии дугового разряда. Для оценки эффективности процессов лазерно-дуговой металлообработки и их оптимизации авторы указанных работ предлагают исследовать зависимости величины ηla от коэффициента энерговклада Kla при различных, но фиксированных значениях коэффициентов ηl и ηa. Последнее допущение, однако, резко снижает достоверность результатов, получаемых в рамках такого подхода, т.к. не учитывает основной особенности лазернодугового воздействия на изделие, а именно взаимовлияния лазерного пучка и электрической дуги, объединяемых в комбинированном процессе. Как указывалось выше, коэффициент использования энергии дугового разряда
58
© И.В. Кривцун, 2001 (ИЭС им. Е.О. Патона НАНУ, Украина, 03680, г. Киев, ул. Боженко 11,
Тел. (044) 261-5349, Факс: (044) 268-0486, krivtsun@i.com.ua, http://www.plasma.kiev.ua/people/krivtsun.html
увеличивается под влиянием лазерного излучения [10, 12], а дополнительный дуговой нагрев обрабатываемого металла повышает эффективность поглощения лазерного пучка [54]. Степень этого взаимовлияния зависит не только от соотношения, но и от абсолютных значений мощностей лазерного излучения и дуги, поэтому при количественной оценке эффективности лазернодугового процесса металлообработки коэффициенты ηl и ηa нельзя считать постоянными при изменении величин Kla, а также Ql и Qa.
Завершая рассмотрение работ, посвященных энергетическим характеристикам и технологическим особенностям лазерно-дугового источника тепла, следует упомянуть книгу Дьюли (W. W. Duley) [69], в которой отражены достижения лазерной технологии за четверть века со времени появления первого лазера. Давая краткий анализ новых, лазерно-дуговых процессов сварки и резки, автор подчеркивает два главных момента: во-первых, то, что тепловой эффект комбинированного лазерно-дугового воздействия превышает сумму эффектов от каждого отдельно взятого источника тепла и, во-вторых, то, что максимальное увеличение производительности процесса достигается при соизмеримых значениях мощностей дуги и лазерного пучка, объединяемых в комбинированном источнике тепла. Отмечая высокую эффективность лазернодуговых способов металлообработки, автор связывает с ними перспективы дальнейшего развития лазерных технологий.
• Взаимное влияние лазерного пучка и электрической дуги в
комбинированных процессах металлообработки
Из обзора работ начального периода развития лазерно-дуговых способов соединения и обработки материалов видно, что наряду с проведением экспериментальных исследований эффектов комбинированного воздействия на изделие, ученые, начиная со Стина, предпринимали попытки объяснить наблюдаемые явления с точки зрения физики протекающих процессов. Смещение акцента исследований в сторону развития физических представлений о механизме лазерно-дуговых процессов произошло во второй
59
© И.В. Кривцун, 2001 (ИЭС им. Е.О. Патона НАНУ, Украина, 03680, г. Киев, ул. Боженко 11,
Тел. (044) 261-5349, Факс: (044) 268-0486, krivtsun@i.com.ua, http://www.plasma.kiev.ua/people/krivtsun.html
половине 1980-х годов. В этом отношении показательны работы советских ученых, публикации которых начали появляться в печати, когда основные эффекты лазерно-дугового воздействия на обрабатываемое изделие были уже описаны в литературе. Очевидно, именно поэтому мы не находим в них подробных исследований характеристик плавления металла и технологических возможностей комбинированных способов обработки. В большей степени эти работы посвящены изучению взаимовлияния лазерного излучения и электродуговой плазмы с целью определения оптимальных условий их совместного воздействия на материалы.
Вработах [70-72], например, основное внимание уделено вопросу о влиянии лазерного пучка на электрическую дугу, горящую с неплавящегося электрода в инертном газе. Так, в статье [70] представлены результаты экспериментальных исследований характеристик дуги постоянного тока прямой полярности при Л+ДНЭ сварке образцов из коррозионно-стойкой стали 08Х18Н10Т в атмосфере аргона. Эксперименты проводились с использованием СO2-лазера непрерывного действия мощностью 1 кВт и установки для аргонодуговой сварки вольфрамовым электродом, при этом дуговая горелка располагалась впереди луча под углом 45о к поверхности изделия. По осциллограммам тока и напряжения на дуговом промежутке строились зависимости напряжения дуги от мощности лазерного излучения при различных значениях сварочного тока, а также ее вольт-амперные характеристики при дуговой и комбинированной сварке. Эксперименты показали, что во всем исследованном диапазоне токов напряжение на дуге при лазерно-дуговой сварке ниже, чем при дуговой (рис. 1. 39), причем эта разница становится наиболее существенной если мощность лазерного пучка превышает
500 Вт (рис. 1.40).
Вдальнейшем авторы работы [70] расширили свои исследования влияния лазерного излучения на электрические параметры сварочной дуги, применив образцы из различных материалов [72]. Зависимости, подобные изображенным
60
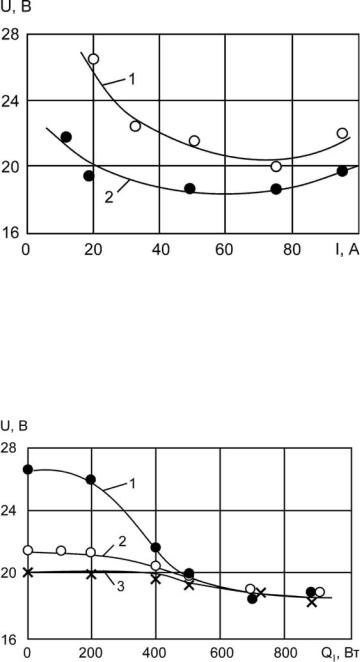
© И.В. Кривцун, 2001 (ИЭС им. Е.О. Патона НАНУ, Украина, 03680, г. Киев, ул. Боженко 11,
Тел. (044) 261-5349, Факс: (044) 268-0486, krivtsun@i.com.ua, http://www.plasma.kiev.ua/people/krivtsun.html
Рис. 1.39. Вольт-амперные характеристики дуги с неплавящимся электродом при сварке коррозионно-стойкой стали: 1 - аргонодуговая сварка; 2 - Л+ДНЭ сварка (мощность лазерного излучения 900 Вт) [70]
Рис. 1.40. Зависимости напряжения на дуге от мощности лазерного излучения при Л+ДНЭ сварке коррозионно-стойкой стали : 1 - ток дуги 20 А; 2 - 50
А; 3 - 75 А [70]
61