
© И.В. Кривцун, 2001 (ИЭС им. Е.О. Патона НАНУ, Украина, 03680, г. Киев, ул. Боженко 11,
Тел. (044) 261-5349, Факс: (044) 268-0486, krivtsun@i.com.ua, http://www.plasma.kiev.ua/people/krivtsun.html
ГИБРИДНЫЕ ЛАЗЕРНО-ДУГОВЫЕ ПРОЦЕССЫ СВАРКИ И ОБРАБОТКИ МАТЕРИАЛОВ (ОБЗОР)
•Эффекты совместного воздействия лазерного пучка и электрической дуги на обрабатываемое изделие
Развитие лазерно-дуговых процессов началось в конце 1970-х годов. Идея совместно использовать лазерный пучок и электрическую дугу для сварки и других видов обработки металлов таким образом, чтобы оба источника тепла воздействовали на изделие в пределах одной зоны нагрева, принадлежит английскому ученому Стину (W. M. Steen), который защитил свое изобретение рядом патентов [5-8]. Он предложил способы сварки, резки, сверления и обработки поверхности, при которых на обрабатываемое изделие направляют лазерный пучок и одновременно в зоне теплового воздействия лазерного излучения возбуждают дугу между электродом и изделием. Совместно с другими учеными он также выполнил первые экспериментальные исследования эффектов лазерно-дугового воздействия на обрабатываемый металл [9-14] и применил комбинированный способ сварки в конкретном производстве [15]. Практически все отличительные особенности новых лазерно-дуговых процессов по сравнению с дуговыми и лазерными способами металлообработки освещены в работах [9, 10, 12], поэтому остановимся на них более подробно.
Схема экспериментальной установки для реализации комбинированных процессов сварки и резки металлов приведена на рис. 1.1. В экспериментах использовался СO2-лазер непрерывного действия мощностью 2 кВт. С помощью поликристаллической KCl линзы с фокусным расстоянием 75 мм лазерный пучок диаметром 1 см фокусировался на поверхность образца в пятно размером 250…350 мкм. При этом он проходил через отверстие в медном сопле диаметром 3 мм в экспериментах по сварке или 1 мм в экспериментах по резке. Через сопло лазерной головки в зону обработки подавался гелий или кислород соответственно для сварки или резки. В качестве источника питания дуги
3
© И.В. Кривцун, 2001 (ИЭС им. Е.О. Патона НАНУ, Украина, 03680, г. Киев, ул. Боженко 11,
Тел. (044) 261-5349, Факс: (044) 268-0486, krivtsun@i.com.ua, http://www.plasma.kiev.ua/people/krivtsun.html
использовался аппарат для сварки неплавящимся электродом в инертном газе при токах до 250 А (либо сварочный генератор на ток до 400 А в комплекте с осциллятором). Дуговая горелка могла быть установлена как с той же стороны образца, на которую направлялся лазерный пучок, так и с противоположной (см. рис. 1.1). Вольфрамовый электрод горелки, защищаемый потоком аргона, во всех экспериментах был катодом, а изделие - анодом.
При осуществлении лазерно-дуговых процессов сварки и резки были отмечены следующие эффекты. Если оба источника тепла располагались с одной и той же стороны изделия, электрическое сопротивление дуги в режиме устойчивого горения (ток 100 А) под воздействием лазерного излучения уменьшалось, о чем свидетельствовало снижение напряжения на дуговом промежутке при одновременном росте тока (рис. 1.2, а). Кроме того, анодная область дуги «привязывалась» к плазменному факелу, создаваемому над поверхностью металла лазерным пучком. При меньших токах (70 А) неустойчивое горение дуги, связанное с блужданием анодного пятна, сменялось устойчивым (рис. 1.2, б) вследствие стабилизации ее анодной области в зоне воздействия на образец лазерного излучения. Последний эффект наблюдался и в том случае, когда источники тепла располагались по разные стороны изделия, при условии, что температура металла под пятном лазерного нагрева не менее чем на 400 К превышала температуру окружающей поверхности.
4
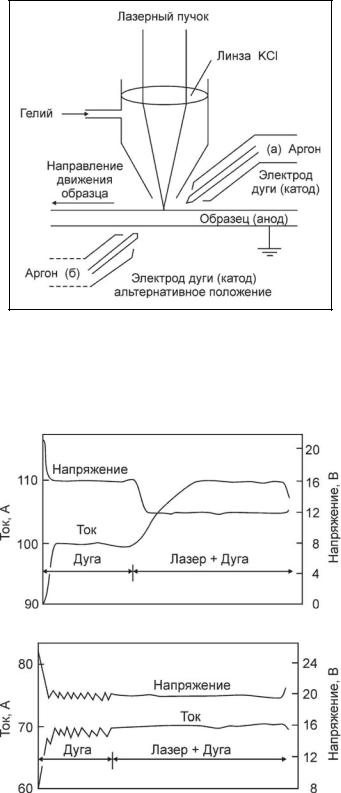
© И.В. Кривцун, 2001 (ИЭС им. Е.О. Патона НАНУ, Украина, 03680, г. Киев, ул. Боженко 11,
Тел. (044) 261-5349, Факс: (044) 268-0486, krivtsun@i.com.ua, http://www.plasma.kiev.ua/people/krivtsun.html
Рис. 1.1. Схемы реализации лазерно-дуговых процессов сварки и резки с распо-
ложением лазерного пучка и дуги с неплавящимся электродом с одной стороны изделия (а) и с разных сторон (б) [12]
а
б
Рис. 1.2. Осциллограммы тока и напряжения на дуге: (а) - снижение электрического сопротивления дуги при лазерно-дуговой сварке малоуглеродистой
стали толщиной 3 мм на скорости 22,5 мм/с; (б) - стабилизация
неустойчивого горения дуги под воздействием лазерного пучка при сварке той же стали толщиной 2 мм на скорости 45,0 мм/с [10]
5
© И.В. Кривцун, 2001 (ИЭС им. Е.О. Патона НАНУ, Украина, 03680, г. Киев, ул. Боженко 11,
Тел. (044) 261-5349, Факс: (044) 268-0486, krivtsun@i.com.ua, http://www.plasma.kiev.ua/people/krivtsun.html
Эффекты «привязки» анодного пятна дуги и стабилизации ее горения в комбинированном процессе даже при малых токах позволили значительно увеличить скорость сварки по сравнению не только с дуговой, но и с лазерной. На рис. 1.3 приведены зависимости скорости сварки от тока дуги при полном проплавлении образцов из различных металлов (значения мощности лазерного излучения указаны на рисунке). Наибольшее увеличение скорости (в 4 раза) наблюдалось при сварке малоуглеродистой стали толщиной 0,2 мм (кривая б) по схеме с расположением дуги и лазерного пучка с разных сторон изделия. Более скромные результаты (примерно двукратное увеличение скорости) получены для титана толщиной 0,8 мм (кривые а) и малоуглеродистой стали толщиной 2 мм при расположении дуги и лазерного пучка по одну сторону изделия. В последнем случае наблюдался еще один важный эффект, а именно отсутствие подрезов, характерных для высокоскоростной дуговой сварки.
Существенное увеличение скорости обработки по сравнению с лазерной было достигнуто и в опытах по лазерно-дуговой резке малоуглеродистой стали толщиной 3 мм с расположением лазерного пучка и дуги по разные стороны изделия. На рис. 1.4 представлены зависимости скорости резки от величины вводимой в металл тепловой энергии. До тех пор, пока прирост тепловложения в изделие за счет дуги не достигал величины, приблизительно равной тепловому вкладу от лазерного излучения (1870 Вт), наклон экспериментальной кривой не изменялся, а резка происходила так, как если бы просто увеличивалась мощность лазерного излучения. При этом качество реза сохранялось и оставалось сравнимым с качеством реза при лазерной обработке. Выше указанного предела вводимой мощности (≈ 3800 Вт) рост скорости резки замедлялся, а качество реза заметно ухудшалось - рез переставал быть параллельным и расширялся со стороны дуги из-за оплавления дугой его боковых сторон. При воздействии обоих источников тепла с одной стороны изделия также не удалось добиться качественной резки вследствие блуждания дуги по кромкам реза.
6
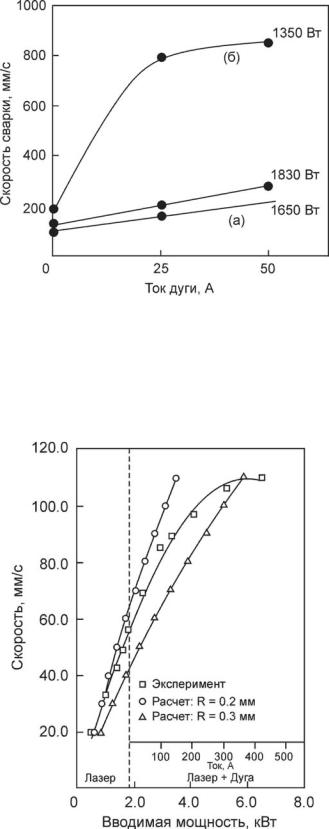
© И.В. Кривцун, 2001 (ИЭС им. Е.О. Патона НАНУ, Украина, 03680, г. Киев, ул. Боженко 11,
Тел. (044) 261-5349, Факс: (044) 268-0486, krivtsun@i.com.ua, http://www.plasma.kiev.ua/people/krivtsun.html
Рис. 1.3. Зависимость скорости лазерно-дуговой сварки от тока дуги: (а) - титан
толщиной 0,8 мм при расположении лазерного пучка и дуги с одной стороны образца; (б) - малоуглеродистая сталь толщиной 0,2 мм при расположении источников тепла с разных сторон [10]
Рис. 1.4. Зависимость скорости резки малоуглеродистой стали толщиной 3 мм от мощности, вводимой в изделие (вводимая мощность до 1870 Вт обеспечивается только лазерным пучком, а выше указанной величины – ла-
зерным пучком и электрической дугой) [12]
7
© И.В. Кривцун, 2001 (ИЭС им. Е.О. Патона НАНУ, Украина, 03680, г. Киев, ул. Боженко 11,
Тел. (044) 261-5349, Факс: (044) 268-0486, krivtsun@i.com.ua, http://www.plasma.kiev.ua/people/krivtsun.html
Авторы работ [9, 10, 12] пытаются дать трактовку описанных эффектов комбинированного воздействия на металлы при лазерно-дуговой сварке и резке на основе физических представлений. В работе [9] они, в частности, высказывают мнение, что причиной снижения напряжения на дуге под действием лазерного излучения (см. рис. 1.2, а) является уменьшение работы выхода анода в области пятна нагрева, создаваемого лазерным пучком, а, значит, и анодного падения потенциала, и связывают с этим эффект «привязки» анодной области дуги к зоне лазерного нагрева. С подобным мнением трудно согласиться, поскольку работа выхода анода, определяемая энергией Ферми (E. Fermi) электронов металла, с одной стороны, слабо зависит от его температуры, а с другой, практически не влияет на анодное падение потенциала в электрической дуге. В работах [10, 12] авторы больше не возвращаются к вышеуказанному предположению и объясняют явление «привязки» тем, что при одностороннем расположении источников тепла дуга ведет себя в соответствии с принципом минимума Штеенбека (M. Steenbeck), а именно: поскольку электропроводность лазерной плазмы, температура которой может достигать 20000 К, намного превышает электропроводность окружающего холодного газа, факел лазерной плазмы является предпочтительной, энергетически выгодной областью горения дуги. Соглашаясь с таким объяснением эффекта «привязки» анодной области дуги, следует отметить, что происходящее при этом взаимодействие излучения СO2-лазера с прианодной дуговой плазмой, приводит к повышению ее температуры, а, следовательно, и электропроводности. Именно это обстоятельство является причиной отмеченного в работах [10, 12] снижения напряжения на дуговом промежутке. Можно также предположить, что при расположении дуги и лазерного пучка с разных сторон изделия, стабилизация анодного пятна в зоне лазерного нагрева металла не приведет к снижению напряжения на дуге (см. рис. 1.2, б) из-за отсутствия непосредственного взаимодействия лазерного пучка с дуговой плазмой.
8
© И.В. Кривцун, 2001 (ИЭС им. Е.О. Патона НАНУ, Украина, 03680, г. Киев, ул. Боженко 11,
Тел. (044) 261-5349, Факс: (044) 268-0486, krivtsun@i.com.ua, http://www.plasma.kiev.ua/people/krivtsun.html
В работах [10, 12] констатируется, что эффект «привязки» анодной области дугового разряда к пятну лазерного нагрева проявляется при малых и средних токах дуги (менее 300 А). При больших токах может наблюдаться исчезновение указанного эффекта, что связано, по мнению авторов, с самостабилизацией дуги за счет мощной катодной струи, при наличии которой анодное пятно может перемещаться независимо от зоны нагрева, создаваемой лазерным пучком. Это рассматривается как одна из причин ухудшения качества комбинированной резки при увеличении тока дуги [12]. Высказывается также предположение, что увеличение тока дуги может привести к появлению нежелательного эффекта и в том случае, когда «привязка» анодной области дуги к факелу лазерной плазмы не исчезает (источники тепла расположены с одной стороны изделия). Это эффект отражения лазерного пучка плотной плазмой, который наблюдается при повышении плотности электронов в приповерхностной плазме выше критического значения (ne ≈ 1019 см-3 для полного отражения плазмой излучения СO2-лазера) и приводит к ограничению тепловложения в обрабатываемый металл. Авторы указанных работ считают этот эффект несущественным при токах дуги менее 300 А.
Явление «привязки» анодной области дуги к факелу лазерной плазмы не только обеспечивает улучшение стабильности горения дугового разряда в комбинированном процессе, но и приводит к такому важному эффекту, как контрагирование анодной области дуги. К этому заключению авторы работ [10, 12] приходят в результате сравнительного анализа профилей поперечных сечений сварных швов (рис. 1.5, 1.6), полученных в экспериментах по лазернодуговой сварке (заштрихованные кривые) и вычисленных на основе математической модели проплавления металла (незаштрихованные кривые). Локальный (в пределах общей зоны нагрева) вклад энергии лазерного и дугового источников тепла в изделие, наблюдающийся в условиях «привязки» анодного пятна дуги, дал основание авторам при построении математической модели рассматривать их как два коаксиально действующих цилиндрических
9
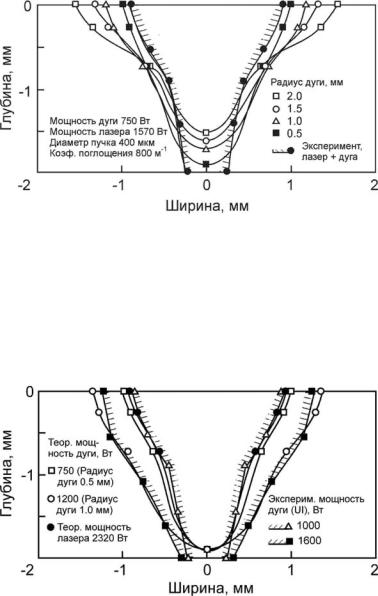
© И.В. Кривцун, 2001 (ИЭС им. Е.О. Патона НАНУ, Украина, 03680, г. Киев, ул. Боженко 11,
Тел. (044) 261-5349, Факс: (044) 268-0486, krivtsun@i.com.ua, http://www.plasma.kiev.ua/people/krivtsun.html
Рис. 1.5. Изменение расчетной формы проплавления металла при лазерно-дуго- вой сварке в зависимости от радиуса дугового источника тепла [10]
Рис. 1.6. Сравнение экспериментальных и расчетных профилей проплавления металла при комбинированной сварке с использованием лазерного пучка мощностью 1,57 кВт и дуги мощностью 1,0 и 1,6 кВт при коэффициенте использования мощности дуги 75 %, скорости сварки 33,5 мм/c и коэффициенте поглощения лазерного излучения плазмой 800 м-1
[10]
10
© И.В. Кривцун, 2001 (ИЭС им. Е.О. Патона НАНУ, Украина, 03680, г. Киев, ул. Боженко 11,
Тел. (044) 261-5349, Факс: (044) 268-0486, krivtsun@i.com.ua, http://www.plasma.kiev.ua/people/krivtsun.html
источника тепла, движущихся относительно образца. В модели предполагалось, что тепловая мощность, вводимая в изделие лазерным пучком, имеет гауссовское распределение по радиусу, а вводимая дугой - параболическое, и учитывались потери тепла поверхностью обрабатываемого металла за счет конвекции и излучения. Допускалось также, что в комбинированном процессе, как и при лазерной сварке, имеет место эффект проплавления в форме «замочной скважины». Чтобы учесть этот эффект в используемой математической модели проплавления образца часть расчетной области, лежащая выше изотермы кипения металла, считалась частично прозрачной для лазерного излучения. При этом предполагалось, что мощность лазерного пучка в полости «замочной скважины» уменьшается по мере удаления от поверхности изделия по экспоненциальному закону [12].
Сравнивая экспериментальный и расчетные профили расплава на рис. 1.5 (значения параметров указаны на рис. 1.5, 1.6 и в подписях к ним), можно убедиться, что расчет формы проплавления металла при радиусе дугового источника тепла 0,5 мм и мощности, вкладываемой им в изделие, 750 Вт, дает профиль шва, максимально близкий к наблюдаемому в экспериментах по лазерно-дуговой сварке с использованием дуги полной мощностью 1000 Вт. В то же время, ссылаясь на литературные данные, авторы работ [10, 12] отмечают, что свободногорящая дуга такой мощности имеет радиус теплового воздействия 1,5 мм. Аналогично дуга мощностью 1600 Вт (радиус теплового воздействия в отсутствие лазерного излучения 2,0 мм) в комбинированном процессе создает профиль расплава, соответствующий расчетному при радиусе источника тепла 1,0 мм и эффективной мощности 1200 Вт (см. рис. 1.6). Сопоставление этих данных позволило авторам сделать вывод о том, что анодная область дуги под влиянием лазерного излучения контрагирует, причем степень контрагирования уменьшается с ростом тока.
Предложенное в работе [12] объяснение указанного эффекта основывается на том, что контрагирование анодной области дуги может быть результатом
11
© И.В. Кривцун, 2001 (ИЭС им. Е.О. Патона НАНУ, Украина, 03680, г. Киев, ул. Боженко 11,
Тел. (044) 261-5349, Факс: (044) 268-0486, krivtsun@i.com.ua, http://www.plasma.kiev.ua/people/krivtsun.html
действия двух факторов. С одной стороны, это возникновение вблизи оси дуги под влиянием сфокусированного лазерного излучения высокотемпературной области плазмы с повышенной концентрацией заряженных частиц, а с другой стороны - появление истекающей из пятна лазерного нагрева струи паров металла, имеющих более низкий потенциал ионизации, чем окружающий газ. Локальное увеличение электропроводности плазмы под действием обоих факторов приводит к сосредоточению тока в приосевой зоне анодной области дуги, т.е. к ее контрагированию. Оба рассмотренных механизма могут вносить соизмеримый вклад в результирующий эффект контрагирования, если в комбинированных процессах используется излучение СO2-лазера, как, например, в работах [9, 10, 12]. Относительная значимость этих механизмов может однако измениться при изменении длины волны лазерного излучения. Такой вывод позволяют сделать результаты аналогичных исследований, выполненных автором данного обзора, по лазерно-дуговой сварке нержавеющей стали с использованием твердотельного ИАГ-лазера (мощность до 400 Вт) и аргоновой дуги с неплавящимся электродом (ток до 100 А) [16]. Основной причиной эффекта контрагирования анодной области дуги, наблюдающегося и в этом случае, можно считать только интенсивное испарение металла из зоны лазерного воздействия, т.к. образование вблизи оси дуги высокотемпературной области плазмы, поддерживаемой лазерным пучком, маловероятно из-за низкого коэффициента поглощения плазмой лазерного излучения с длиной волны 1,06 мкм (примерно на два порядка ниже, чем излучения СO2-лазера).
В работах [10, 12] показано, что профили швов при комбинированной сварке близки к расчетным профилям проплавления, если коэффициент использования энергии дуги выбирается равным 0,75 (см. рис. 1.5, 1.6), в то время как для обычного дугового источника тепла он составляет лишь 0,5. Это свидетельствует о более эффективной передаче энергии электрической дуги металлу под действием лазерного излучения, в результате чего тепловой
12
© И.В. Кривцун, 2001 (ИЭС им. Е.О. Патона НАНУ, Украина, 03680, г. Киев, ул. Боженко 11,
Тел. (044) 261-5349, Факс: (044) 268-0486, krivtsun@i.com.ua, http://www.plasma.kiev.ua/people/krivtsun.html
эффект комбинированного воздействия превосходит простую сумму тепловых эффектов лазерного и дугового источников тепла, взятых по отдельности. Кроме того, совпадение экспериментального профиля шва с расчетным (см. рис. 1.6) для случая, когда единственным источником тепла является лазерный пучок мощностью 2320 Вт, равной сумме мощностей лазерного источника (1570 Вт) и дугового при коэффициенте использования энергии дуги 0,75 (0,75×1000 Вт), дает основание утверждать, что дуга, контрагируя, действует в комбинированном процессе подобно сфокусированному лазерному пучку. Упомянутые эффекты связываются в работе [12] с проникновением анодной области дуги в полость «замочной скважины», создаваемой лазерным пучком. Не отрицая важной роли явления проникновения прианодной плазмы в «замочную скважину» при лазерно-дуговой сварке и резке, следует отметить, что повышение эффективности теплового воздействия дуги на изделие будет наблюдаться в комбинированных процессах и при отсутствии глубокого проплавления. Главной причиной повышения эффективности дугового нагрева является изменение под влиянием лазерного излучения характера протекания анодных процессов и, как следствие, увеличение энергии, вкладываемой дугой в анод. Именно поэтому этот эффект будет присутствовать не только при лазерно-дуговой сварке или резке, но и при термической обработке поверхности.
Завершая обзор работ [9, 10, 12], следует обратить внимание на важный вывод, к которому приходят авторы на основе анализа особенностей комбинированного воздействия на металлы при лазерно-дуговой сварке и резке. Это вывод о существовании взаимосвязи лазерного и дугового источников тепла, приводящей к нарушению аддитивности теплового воздействия лазерного пучка и электрической дуги на изделие. Последнее означает, что комбинированный лазерно-дуговой источник тепла может обеспечить более высокую скорость металлообработки, чем дуговой или лазерный источники в отдельности при эффективной мощности каждого из
13
© И.В. Кривцун, 2001 (ИЭС им. Е.О. Патона НАНУ, Украина, 03680, г. Киев, ул. Боженко 11,
Тел. (044) 261-5349, Факс: (044) 268-0486, krivtsun@i.com.ua, http://www.plasma.kiev.ua/people/krivtsun.html
них, эквивалентной суммарной мощности источников в условиях отсутствия взаимодействия между ними. Иными словами, совместное использование лазерного пучка и электрической дуги дает возможность при значительно меньшей мощности лазерного излучения достичь такой же производительности процесса, как и в случае обычной лазерной сварки или резки (мощность лазерного излучения, естественно, должна быть достаточна для обеспечения стабилизации анодной области дуги в пятне лазерного нагрева и ее контрагирования). Необходимо отметить и то немаловажное обстоятельство, что комбинированное использование лазерного пучка и дугового разряда позволяет повышать производительность процессов металлообработки не за счет дорогостоящей энергии лазерного излучения, а за счет гораздо более дешевой энергии электрической дуги. В этом состоит одно из основных преимуществ лазерно-дуговых способов соединения и обработки металлов.
•Схемы практической реализации лазерно-дуговых и лазерноплазменных способов сварки, резки и обработки поверхности
В конце 1970-х годов, вслед за английскими учеными, активную разработку различных способов лазерно-дуговой сварки, резки и обработки поверхности, а также устройств для их осуществления начали японские исследователи. Так, в 1977 г. Хамазаки (M. Hamasaki) предложил для увеличения глубины проплавления при сварке дугой с неплавящимся электродом (ДНЭ) в инертном газе направлять в сварочную ванну (несколько позади дуги по ходу сварки) сфокусированный лазерный пучок через специальное отверстие, выполненное в корпусе дуговой горелки [17]. Тем самым он запатентовал способ сварки, обеспечивающий комбинированное, в пределах общей сварочной ванны, воздействие на изделие лазерного излучения и электрической дуги с неплавящимся электродом (Л+ДНЭ).
В начале 1980-х годов, в течение буквально двух-трех лет, в Японии появляется целый ряд оригинальных технических решений, направленных на
14
© И.В. Кривцун, 2001 (ИЭС им. Е.О. Патона НАНУ, Украина, 03680, г. Киев, ул. Боженко 11,
Тел. (044) 261-5349, Факс: (044) 268-0486, krivtsun@i.com.ua, http://www.plasma.kiev.ua/people/krivtsun.html
практическое осуществление различных лазерно-дуговых процессов металлообработки. Если следовать хронологии развития новых методов обработки, в которых совместно используются лазерный пучок и дуговой разряд, то следует отметить, что уже в 1982 г. группа японских ученых высказала идею применить сфокусированное лазерное излучение в качестве дополнительного источника тепла при дуговой сварке плавящимся электродом в защитных газах [18]. Однако речь еще не шла о комбинированном воздействии на металл, а, значит, и о реализации лазерно-дугового процесса, поскольку ставилась цель использовать лазерный пучок всего лишь как вспомогательный инструмент для термообработки шва после сварки. Для этого предлагалось позади дуговой горелки на некотором удалении от нее установить лазерную головку и в процессе сварки осуществлять ее колебания поперек шва.
В это же время другая группа японских исследователей также вплотную подошла к изобретению комбинированного лазерно-дугового процесса применительно к сварке плавящимся электродом, предложив при лазерной сварке подавать присадочную проволоку в факел приповерхностной плазмы несколько впереди лазерного пучка [19] и осуществлять ее подогрев с помощью дополнительного источника тепла (вспомогательной дуги, пламени газовой горелки и т. п.) [20]. В следующем варианте лазерной сварки с присадкой, в котором авторы предусмотрели подогрев обратной стороны шва электрической дугой [21], по существу была предложена схема комбинированного лазернодугового процесса сварки с расположением источников тепла по разные стороны изделия, поскольку зоны теплового воздействия лазерного пучка и дуги объединялись в пределах единой сварочной ванны.
Придерживаясь и далее хронологической последовательности возникновения новых комбинированных способов соединения и обработки металлов с использованием лазерного излучения и электрической дуги, отметим заявку [22], в которой авторы предлагают в зазор стыкового соединения при лазерной сварке помещать присадочный металл и сначала
15
© И.В. Кривцун, 2001 (ИЭС им. Е.О. Патона НАНУ, Украина, 03680, г. Киев, ул. Боженко 11,
Тел. (044) 261-5349, Факс: (044) 268-0486, krivtsun@i.com.ua, http://www.plasma.kiev.ua/people/krivtsun.html
расплавлять его дуговой горелкой с неплавящимся электродом, а затем, переместив расплавленный участок шва под лазерную головку, не дожидаясь остывания ванны, производить лазерный переплав. Очевидно, что в данном случае, как и в заявке [18], нельзя говорить об осуществлении комбинированного лазерно-дугового процесса, поскольку отсутствует одновременное воздействие лазерного и дугового источников тепла на изделие. Упомянем здесь и заявку [23], также касающуюся совместного использования ДНЭ и излучения лазера при осуществлении комбинированного процесса сварки. В ней фактически предлагается применить схему лазерно-дуговой сварки, известную из работ Стина (см., например, [10]), с расположением лазерного пучка и дуги соответственно с лицевой и обратной стороны изделия для выполнения кольцевых швов на трубопроводах с целью исключения чрезмерного усиления шва и непроваров.
Наконец, Хамазаки, автор уже упомянутого ранее изобретения [17], в конце 1982 г. предложил способ сварки [24-26], при котором осуществляют одновременное проплавление обрабатываемого металла дугой с плавящимся электродом (ДПЭ), горящей в защитном газе, и лазерным излучением, причем лазерный пучок фокусируют вблизи дна кратера, образуемого дугой. При осуществлении этого способа лазерная головка и горелка для сварки плавящимся электродом располагаются над поверхностью металла таким образом, что лазерный пучок находится несколько впереди дуги по ходу сварки. Это изобретение положило начало развитию лазерно-дуговой сварки плавящимся электродом (Л+ДПЭ) в защитных газах.
Приблизительно год спустя в заявке [27] было предложено оригинальное устройство для осуществления комбинированной лазерно-дуговой сварки неплавящимся электродом, т.е. Л+ДНЭ процесса. В нем лазерный пучок направляется на изделие вдоль оси сопла дуговой горелки, через которое подается рабочий инертный газ (рис. 1.7). Коаксиально пучку на цилиндрическом изоляторе размещают четыре пары вольфрамовых электродов
16
© И.В. Кривцун, 2001 (ИЭС им. Е.О. Патона НАНУ, Украина, 03680, г. Киев, ул. Боженко 11,
Тел. (044) 261-5349, Факс: (044) 268-0486, krivtsun@i.com.ua, http://www.plasma.kiev.ua/people/krivtsun.html
(катодов). В сопло подается также защитный газ. Сварка осуществляется при одновременном горении двух дуг с диаметрально расположенных электродов (впереди и позади пучка). Другой вариант конструкции предусматривает установку вместо набора стержневых катодов специального сопла, выполняющего роль электрода дуги (рис. 1.8).
В заявке [28] и в патенте [29], опубликованных в середине 1980-х годов, также предлагается в качестве электрода дуги в устройстве для лазерно-дуговой сварки, резки и термообработки поверхности использовать кольцеобразный неплавящийся электрод, установленный на торце сопла фокусирующей лазерной головки. Как считают авторы этого изобретения, такая конструкция устройства повышает эффективность лазерного нагрева металла, т.к. плазма дуги, поглощая энергию лазерного излучения, передает ее затем изделию более эффективно, чем непосредственно лазерный пучок. Благодаря этому становится возможной сварка таких высокотеплопроводных металлов, как алюминий и медь. Отметим, что предложенное устройство, также как и описанное в заявке [27], позволяет реализовать особый тип разряда - комбинированный лазернодуговой разряд [30], характерной чертой которого является существенное взаимодействие сфокусированного лазерного излучения с плазмой столба электрической дуги.
Чтобы увеличить срок эксплуатации кольцевого электрода и уменьшить зону термического влияния при лазерно-дуговой обработке, те же авторы предложили усовершенствовать описанное устройство путем использования дополнительного наружного водоохлаждаемого сопла, через которое подается инертный газ [31]. Последний, кроме своей основной функции - защиты металла шва от окисления атмосферным кислородом, будет выполнять и другие важные функции, а именно: способствовать охлаждению электрода, увеличивая срок его службы, а также обжимать дуговую плазму, т.е. реализовать плазменную дугу (ПД). При этом зона термического влияния уменьшится
17
© И.В. Кривцун, 2001 (ИЭС им. Е.О. Патона НАНУ, Украина, 03680, г. Киев, ул. Боженко 11,
Тел. (044) 261-5349, Факс: (044) 268-0486, krivtsun@i.com.ua, http://www.plasma.kiev.ua/people/krivtsun.html
настолько, что становится возможным применение устройства и для резки
металлов. Это усовершенствование фактически привело авторов к созданию на
18
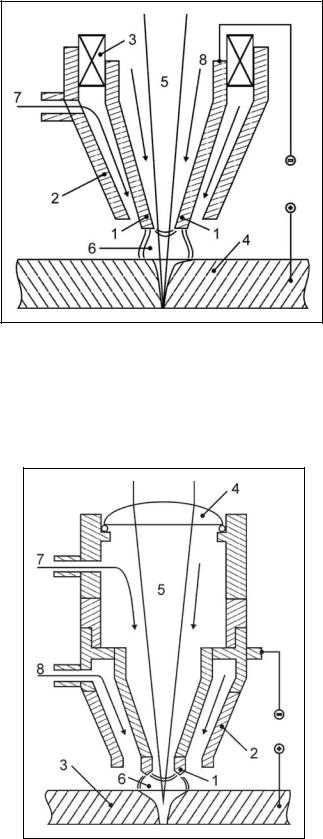
© И.В. Кривцун, 2001 (ИЭС им. Е.О. Патона НАНУ, Украина, 03680, г. Киев, ул. Боженко 11,
Тел. (044) 261-5349, Факс: (044) 268-0486, krivtsun@i.com.ua, http://www.plasma.kiev.ua/people/krivtsun.html
Рис. 1.7. Устройство для лазерно-дуговой (Л+ДНЭ) сварки: 1 - штыревые катоды
(расположенные по окружности); 2 - сопло для подачи защитного газа; 3 - цилиндрический изолятор; 4 - изделие; 5 - сфокусированный лазерный пучок; 6 - электрическая дуга; 7, 8 - защитный инертный газ [27]
Рис. 1.8. Устройство для Л+ДНЭ сварки: 1 - кольцевой электрод (катод); 2 - сопло для подачи защитного газа; 3 - изделие; 4 – фокусирующая линза; 5 – лазерный пучок; 6 - электрическая дуга; 7 - инертный газ; 8 - защитный инертный газ [27]
19
© И.В. Кривцун, 2001 (ИЭС им. Е.О. Патона НАНУ, Украина, 03680, г. Киев, ул. Боженко 11,
Тел. (044) 261-5349, Факс: (044) 268-0486, krivtsun@i.com.ua, http://www.plasma.kiev.ua/people/krivtsun.html
основе комбинированного разряда плазмотрона прямого действия для лазерноплазменной (Л+ПД) обработки металлов.
Скомбинировать лазерное излучение и сжатую плазменную дугу для получения двустороннего шва предложил и автор заявки [32] в способе сварки, согласно которому лазерный пучок и дуга располагаются по разные стороны изделия - соответственно с лицевой и обратной стороны шва. Естественно, что говорить здесь о непосредственном взаимодействии лазерного излучения с дуговой плазмой и возникновении комбинированного разряда можно только при условии сквозного проплавления образца.
В заявке [33], опубликованной в 1985 г., было предложено устройство для резки, сварки, закалки и напыления, в котором совместно используются лазерное излучение и плазменная струя. Плазменная струя (ПС) создается дугой, зажигаемой в кольцевом зазоре между двумя электродами, роль которых выполняют сопло лазерной головки и расположенное коаксиально с ним наружное водоохлаждаемое сопло (рис. 1.9). Плазмообразующий газ подается как в лазерную головку, так и в кольцевой зазор между двумя электродами (соплами) и формирует на выходе плазменную струю, соосную с лазерным пучком. Описанное устройство можно рассматривать как один из первых плазмотронов косвенного действия, предназначенных для реализации лазерноплазменных (Л+ПС) процессов металлообработки.
Известна еще одна схема реализации лазерно-дугового процесса с расположением источников тепла по разные стороны изделия, на которой основан способ комбинированной сварки лазером и дугой с плавящимся электродом в защитных газах, предназначенный для выполнения стыковых соединений с Y-образной разделкой кромок [34]. В этом способе дуговую горелку располагают со стороны разделки, т.е. с лицевой стороны шва, а лазерную головку - с обратной стороны шва. Сварку лазерным пучком производят со сквозным проплавлением, в результате чего значительный объем лазерной плазмы выдувается в разделку. Тем самым, во-первых, увеличивается
20
© И.В. Кривцун, 2001 (ИЭС им. Е.О. Патона НАНУ, Украина, 03680, г. Киев, ул. Боженко 11,
Тел. (044) 261-5349, Факс: (044) 268-0486, krivtsun@i.com.ua, http://www.plasma.kiev.ua/people/krivtsun.html
эффективность использования энергии лазерного излучения и, во-вторых, повышается стабильность горения дуги благодаря присутствию в разделке лазерной плазмы. Способ обеспечивает сварку толстолистовых металлов за один проход при использовании лазера небольшой мощности.
Работа по созданию новых схем и устройств для реализации лазернодуговых процессов соединения и обработки материалов не прекратилась и в последнее десятилетие. В частности, в научно-технической литературе этого периода находим сведения о способе Л+ПС резки с расположением источников тепла по разные стороны изделия [35], а также о способе Л+ПД сварки, реализованным по новой схеме [36-38]. В отличие от схемы, предложенной ранее [31], согласно которой лазерный пучок и плазменная дуга соосны, в работе [36] ось лазерного пучка и ось плазменной горелки направлены под углом друг к другу (рис. 1.10). Подобная схема практической реализации процесса Л+ПД сварки, предусматривающая подачу присадочной проволоки в зону сварки (рис. 1.11), приводится и в обзорной статье [39], в которой рассматриваются и другие известные способы реализации комбинированных процессов.
К соосному объединению плазменной дуги и лазерного пучка возвращаются авторы более поздних публикаций [40-43], в которых речь идет о создании специализированных устройств - интегрированных плазмотронов для реализации Л+ПД процессов сварки [40, 41] и порошковой наплавки [42, 43]. Основной особенностью таких устройств является конструкция катодного узла (тугоплавкий трубчатый катод или система штыревых катодов, расположенных по окружности) позволяющая подавать сфокусированное лазерное излучение в зону обработки вдоль оси плазмоформирующего канала плазмотрона (рис. 1.12). Интегрированные плазмотроны не только обеспечивают требуемую коаксиальность воздействия лазерного пучка и плазменной дуги на изделие в пределах общей зоны нагрева, но, в случае использования СО2-лазера (когда возможно возникновение лазерно-дугового разряда [30]), фактически являются
21
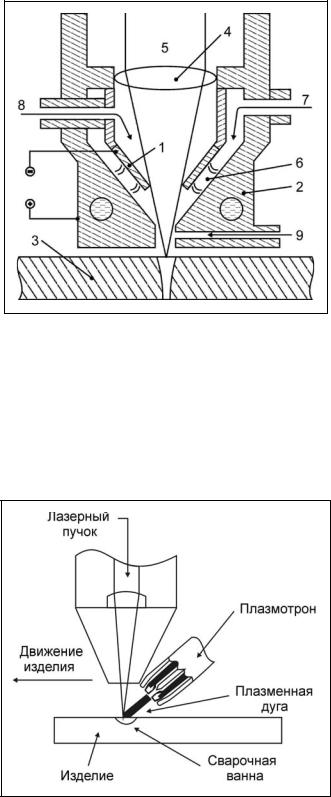
© И.В. Кривцун, 2001 (ИЭС им. Е.О. Патона НАНУ, Украина, 03680, г. Киев, ул. Боженко 11,
Тел. (044) 261-5349, Факс: (044) 268-0486, krivtsun@i.com.ua, http://www.plasma.kiev.ua/people/krivtsun.html
Рис. 1.9. Устройство для реализации лазерно-плазменных (Л+ПС) процессов: 1 - сопло лазерной головки; 2 - внешнее водоохлаждаемое сопло (анод); 3 - изделие; 4 - линза; 5 - лазерный пучок; 6 - электрическая дуга; 7, 8 - плазмообразующий газ; 9 - напыляемый материал (в случае лазерноплазменного напыления) [33]
Рис. 1.10. Схема процесса лазерно-плазменной (Л+ПД) сварки [36]
22
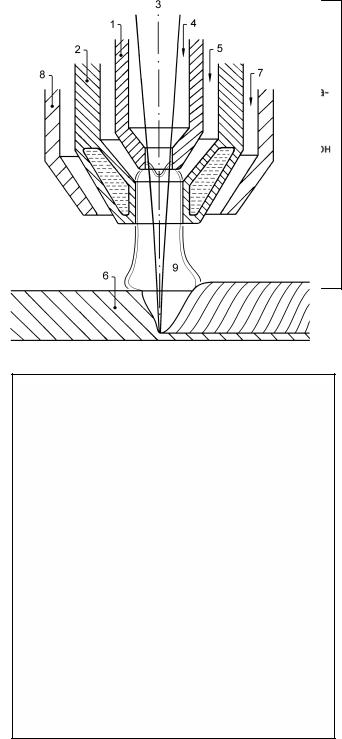
© И.В. Кривцун, 2001 (ИЭС им. Е.О. Патона НАНУ, Украина, 03680, г. Киев, ул. Боженко 11,
Тел. (044) 261-5349, Факс: (044) 268-0486, krivtsun@i.com.ua, http://www.plasma.kiev.ua/people/krivtsun.html
Рис. 1.11. Схема процесса Л+ПД сварки с присадочной проволокой [39]
Рис. 1.12. Интегрированный плазмотрон для реализации комбинированных
(Л+ПД) процессов сварки и обработки металлов: 1 - тугоплавкий труб-
чатый катод; 2 – водоохлаждаемое плазмоформирующее сопло; 3 - сфокусированный лазерный пучок; 4, 5 - плазмообразующий газ; 6 -
изделие (анод); 7 - защитный газ; 8 - сопло для подачи защитного газа; 9 – лазерно-дуговой разряд
23
© И.В. Кривцун, 2001 (ИЭС им. Е.О. Патона НАНУ, Украина, 03680, г. Киев, ул. Боженко 11,
Тел. (044) 261-5349, Факс: (044) 268-0486, krivtsun@i.com.ua, http://www.plasma.kiev.ua/people/krivtsun.html
плазменными генераторами нового типа, действующими на основе комбинированного разряда, как особого типа газового разряда. По аналогии с дуговыми плазмотронами они могут быть прямого действия (когда изделие является одним из электродов дуги) и косвенного действия, т.е. генерировать бестоковую плазменную струю. Как технические средства для реализации различных технологических процессов интегрированные лазерно-дуговые плазмотроны могут использоваться не только в процессах сварки и обработки материалов, связанных с воздействием на поверхность изделия, но и в технологических процессах, использующих весь объем плазмы, таких, например, как порошковая наплавка или напыление.
В качестве примера интегрированного плазмотрона коаксиальной схемы можно привести устройство для микроплазменной, лазерной и комбинированной (лазерно-микроплазменной) сварки нержавеющей стали, титановых и алюминиевых сплавов толщиной до 3 мм в автоматическом и ручном режимах (рис. 1.13, 1.14), которое разработано специалистами ИЭС им. Е.О. Патона и КБ «Южное» с перспективой использования для выполнения ремонтных работ в космических условиях. Данное устройство представляет собой двухэлектродный плазмотрон, имеющий вольфрамовый катод диаметром 1,5 мм для работы на прямой полярности и вольфрамовый электрод диаметром 2,5 мм для работы в режиме разнополярных импульсов тока, установленные внутри водоохлаждаемого корпуса. Электроды расположены диаметрально под углом 21о к оси плазмотрона и имеют возможность перемещения вдоль своих осей. Плазмотрон имеет сменное плазмоформирующее сопло, изготовленное из меди или молибдена, с диаметром выходного канала 2…3 мм и внешнее сопло для подачи защитного газа.
Предложенная конструкция интегрированного плазмотрона позволяет вводить сфокусированный лазерный пучок в зону сварки вдоль оси плазмоформирующего канала. Для этой цели в верхней части корпуса предусмотрен стыковочный узел (см. рис. 1.13) для подсоединения плазмотрона
24
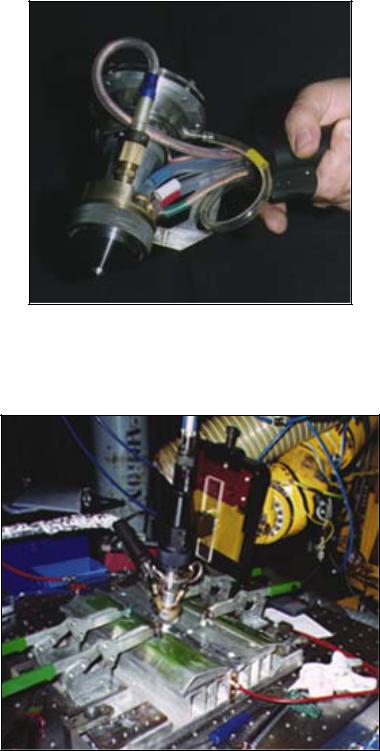
© И.В. Кривцун, 2001 (ИЭС им. Е.О. Патона НАНУ, Украина, 03680, г. Киев, ул. Боженко 11,
Тел. (044) 261-5349, Факс: (044) 268-0486, krivtsun@i.com.ua, http://www.plasma.kiev.ua/people/krivtsun.html
Рис. 1.13. Внешний вид интегрированного плазмотрона для автоматической и
ручной лазерно-микроплазменной сварки
Рис. 1.14. Лазерно-микроплазменная сварка в автоматическом режиме
25
© И.В. Кривцун, 2001 (ИЭС им. Е.О. Патона НАНУ, Украина, 03680, г. Киев, ул. Боженко 11,
Тел. (044) 261-5349, Факс: (044) 268-0486, krivtsun@i.com.ua, http://www.plasma.kiev.ua/people/krivtsun.html
к стандартной фокусирующей системе RSY-FM-D160Z HP/2 c регулируемым фокусным расстоянием 160 ± 6 мм, которая соединяется со световодом посредством коллиматора RSY-KM-B120 HPW/2. Плазмотрон предназначен для работы с пучком излучения твердотельного ИАГ-лазера мощностью до 2 кВт (размер пятна фокусировки 0,6…1,0 мм) при токах микроплазменной дуги прямой полярности до 50 А (в случае сварки сталей и титановых сплавов) или при использовании разнополярных импульсов тока амплитудой до 35 А (в случае сварки алюминя). Испытания плазмотрона продемонстрировали высокую стабильность его работы в широком диапазоне режимов сварки.
Принципиально новая схема реализации комбинированных процессов сварки с использованием ИАГ-лазера, которая также обеспечивает коаксиальность теплового и динамического воздействия лазерного пучка и электрической дуги на поверхность свариваемого металла, предложена в работе [44], опубликованной японскими учеными. Согласно этой схеме лазерный пучок после коллимирующей линзы с помощью системы зеркал разделяется на два пучка, как показано на рис. 1.15, которые затем фокусируются посредством двух собирающих линз в общий фокус, находящийся на поверхности изделия. Электрод дуги (плавящийся или неплавящийся) располагается в пространстве между указанными пучками несколько выше зоны их объединения и устанавливается нормально к поверхности металла. Внешний вид сварочных головок для реализации Л+ДНЭ и Л+ДПЭ сварки по описанной выше схеме показан на рис. 1.16. Кроме того в статье [44] приводится подробный анализ результатов исследования технологических возможностей применения разработанных устройств, включая фотографии поверхностей и макрошлифов поперечных сечений швов, выполненных Л+ДНЭ и Л+ДПЭ сваркой на стали и алюминии.
В работе [45], представляющей обзор результатов исследований по лазерно-дуговой сварке, выполненных немецкими учеными, кроме уже известных способов комбинированной сварки (Л+ДНЭ, Л+ПД, Л+ДПЭ), описан
26
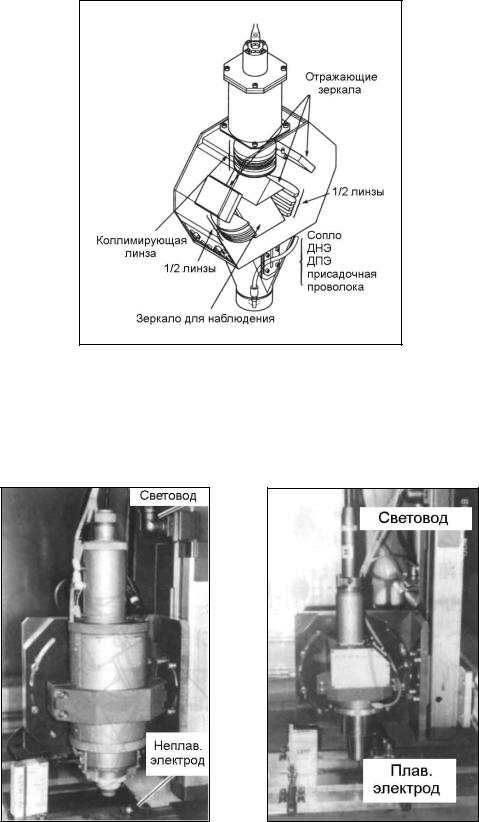
© И.В. Кривцун, 2001 (ИЭС им. Е.О. Патона НАНУ, Украина, 03680, г. Киев, ул. Боженко 11,
Тел. (044) 261-5349, Факс: (044) 268-0486, krivtsun@i.com.ua, http://www.plasma.kiev.ua/people/krivtsun.html
Рис. 1.15. Схема устройства для Л+ДНЭ и Л+ДПЭ сварки с разделением лазер-
ного пучка на две части и последующим их сведением в общий фокус
[44]
а |
б |
Рис. 1.16. Внешний вид сварочных головок для Л+ДНЭ (а) и Л+ДПЭ (б) сварки с
разделением лазерного пучка [44]
27
© И.В. Кривцун, 2001 (ИЭС им. Е.О. Патона НАНУ, Украина, 03680, г. Киев, ул. Боженко 11,
Тел. (044) 261-5349, Факс: (044) 268-0486, krivtsun@i.com.ua, http://www.plasma.kiev.ua/people/krivtsun.html
новый гибридный процесс, заключающийся в совместном использовании лазерного пучка и двух дуг с плавящимися электродами. Практическая реализация такого процесса потребовала создания специальной сварочной головки, внешний вид которой показан на рис. 1.17. Предложенная модульная конструкция головки предусматривает возможность изменения положения каждой из двух горелок для сварки плавящимся электродом относительно оси лазерного пучка и поверхности изделия. Наряду с возможностью раздельного регулирования режимов горения каждой ДПЭ, это позволяет использовать данное устройство для решения широкого круга сварочных задач.
Представляет интерес и более ранняя обзорная статья [46]. В ней, наряду со способами комбинированной лазерно-дуговой сварки, рассматриваются схемы и других гибридных процессов обработки материалов, в частности, плазменно-лазерного напыления. Отмечается, что применение лазерного излучения для оплавления напыленного с помощью плазменной струи слоя улучшает структуру, механические и функциональные свойства получаемого покрытия. В работе [46] приводятся четыре возможные схемы реализации процесса комбинированного напыления (рис. 1.18), обеспечивающие различные условия взаимодействия лазерного пучка и плазменной струи с напыляемым материалом. Сообщается, что при плазменно-лазерном нанесении покрытий достигается более высокая производительность, чем при физическом и химическом осаждении из паровой фазы. Очевидно, что наиболее перспективной является последняя из приведенных на рис. 1.18 схем, которая позволяет использовать лазерное излучение не только для нагрева напыляемого материала, но и для управления характеристиками ПС за счет взаимодействия лазерного пучка с плазмой.
Все рассмотренные выше схемы реализации лазерно-дуговых способов соединения и обработки материалов можно классифицировать по типу комбинированного процесса, а также по пространственному расположению источников тепла относительно изделия (табл. 1.1).
28
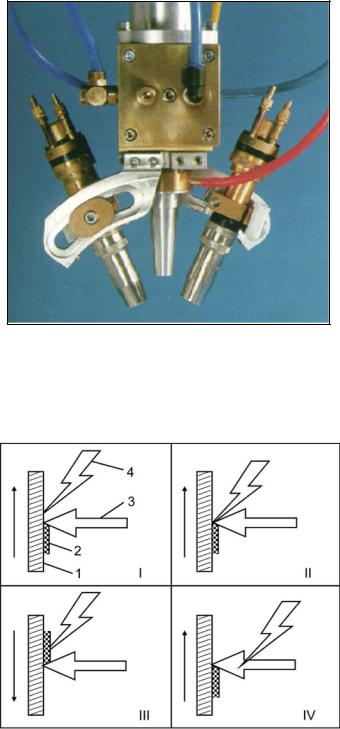
© И.В. Кривцун, 2001 (ИЭС им. Е.О. Патона НАНУ, Украина, 03680, г. Киев, ул. Боженко 11,
Тел. (044) 261-5349, Факс: (044) 268-0486, krivtsun@i.com.ua, http://www.plasma.kiev.ua/people/krivtsun.html
Рис. 1.17. Внешний вид сварочной головки для двухдуговой Л+ДПЭ сварки [45]
Рис. 1.18. Схема процесса плазменно-лазерного напыления: 1 - образец; 2 –
напыляемый материал; 3 - плазменная струя; 4 - лазерный пучок (вертикальные стрелки указывают направление движения образца)
[46]
29