
13_Nizkotemperaturnye_poverkhnosti
.pdf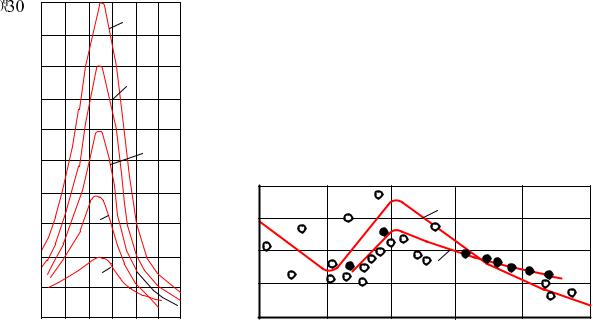
387
возрастает с уменьшением tст ). В то же время интенсивность коррозии зависит от процентного содержания H2SO4 в конденсирующейся пленке на по-
верхности металла. При более низкой температуре (ниже 110 °С) в пленке растет масса влаги и снижается доля серной кислоты.
Скорость коррозии металла в наиболее опасной зоне температур 100– 110 °С существенно снижается при уменьшении избытка воздуха в продуктах сгорания (рис. 13.22, а, кривая 2), что связано с резким уменьшением образования SO3 в потоке газов. В том же направлении изменяется скорость корро-
зии, если уменьшить содержание серы в топливе.
K, |
а) |
K, |
tст , °С |
б) |
tст , °С |
Рис. 13.22. Скорость коррозии металла от температуры стенки при разных видах сжигания топлива: а – при сжигании мазута и разных избытках воздуха для РВП; 1 – при aт £1,02 ;
2–4 – при aт =1,03 -1,05 ; 5 – при aт ³1,1; б – при сжигании твердого топлива; 1 – для трубчатого воздухоподогревателя; 2 – для РВП
Для исключения низкотемпературной коррозии необходимо иметь tст ³ tps + (10 -15) °С, однако это экономически оправдано лишь при сжигании
малосернистых мазутов и сернистых твердых топлив, у которых tст не превышает 110 °С. В других случаях при высоком значении tст температура ухо-
дящих газов будет чрезмерно велика, значительно возрастут потери с уходящими газами. Для исключения заметного роста потерь q2 допускают в возду-
хоподогревателе невысокую скорость коррозии (не более 0,2 мм/год), обеспечив за счет предварительного подогрева воздуха на входе в воздухоподогреватель соответствующую температуру стенки. Taк при сжигании сернистых мазутов допускается tст =120 °С, что увеличивает рабочую кампанию холод-
ного слоя РВП до четырех лет. Однако при этом несколько повышается тем-
388
пература уходящих газов и снижается КПД котла. Изменение температуры уходящих газов DJух при повышении температуры поступающего воздуха
Dtвп′ связано следующей зависимостью:
′ |
(13.7) |
DJух = 0,7Dtвп . |
Так, при подогреве воздуха на входе РВП с 50 °С до 90 °С температура уходящих газов повысится на DJух = 0,7 × 40 = 28 °С, что снизит экономич-
ность котла примерно на Dhк =1,1% .
Для уменьшения низкотемпературной коррозии воздухоподогревателей (при конденсации паров серной кислоты) стараются повысить температуру холодного воздуха перед воздухоподогревателем. Для чего организуется рециркуляция части горячего воздуха в холодный пакет или предварительный подогрев воздуха в калориферах отборным паром турбины. Выходную холодную часть воздухоподогревателя часто выделяют в самостоятельные кубы, удобные для замены при ремонте. В трубчатых воздухоподогревателях такие кубы имеют самостоятельное крепление на каркасе. В регенеративных воздухоподогревателях холодные пакеты выполняют из утолщенных листов набивки.
Подогрев воздуха в таких холодных кубах должен обеспечить в горячих пакетах температуру стенок (или листов) выше точки росы, которая может достигать 100–150 °С в зависимости от содержания серы в топливе (большая цифра соответствует повышенному серосодержанию).
На рис. 13.23 представлены несколько способов предвключенного подогрева холодного воздуха в воздухоподогревателях. На рис. 13.23, а – частичная рециркуляция горячего воздуха на всас дутьевого вентилятора; на рис. 13.23, б – подогрев холодного воздуха в калорифере отборным из турбины паром низкого давления с температурой около 120 °С; на рис. 13.23, в – подогрев в калорифере горячей водой с температурой несколько выше tр , которую по-
лучают из замкнутой системы особого экономайзера низкого давления 4. Следует отметить, что при частичной рециркуляции воздуха через дуть-
евой вентилятор (см. рис. 13.23, а) проходит увеличенный расход воздуха, что повышает расход электроэнергии на дутье. В этой связи предельная температура подогрева воздуха составляет 50 °С.
Использование пара из отбора турбин для подогрева воздуха (рис. 13.23, б) оказывается более экономичным, чем рециркуляция газов, если при проектировании турбины этот отбор предусмотрен. Однако при значительном подогреве воздуха сильно повышается температура уходящих газов, что делает экономически не целесообразным подогрев воздуха свыше 60–70 °C. Применение «отборного» пара для подогрева холодного воздуха позволяет

389
снизить расходы на собственные нужды и одновременно повысить КПД станции.
В последние годы находит распространение каскадный трубчатый воз- духоподогреватель (рис. 13.23, г), в котором температура металла tм поддер-
живается выше tр при всех режимах эксплуатации без применения громозд-
ких устройств. Для этого холодный поток воздуха перед калорифером разделяется на два потока. Каскадная часть 9 работает на полном расходе дымовых газов, но при неполном расходе воздуха (30–40 %), второй поток (70–60%) байпасируется и смешивается с каскадным потоком в смесителе 11. На графике дано изменение температур газов ϑг , воздуха tв . Из графика видно, что
в калорифере и каскадном кубе 9 температура воздуха растет быстрее из-за малого расхода воздуха; продукты сгорания в каскадной части охлаждаются меньше, а поэтому их температура выше.
|
|
6 |
|
2 |
Пар |
3 |
7 |
|
|
|
|
|
3 |
8 |
|
|
|
|
|
|
|
6 |
|
1 |
1 |
4 |
|
|
|
||
|
|
5 |
|
|
|
tг.в |
|
|
|
|
|
|
10 |
|
|
|
tсм |
11 |
1 |
|
|
|
|
3 |
9 |
|
|
|
|
|
|
||
|
|
|
|
|
tх.в. |
|
|
|
|
|
|
ϑух |
|
12 |
|
|
tг.в |
|
|
tв |
|
ϑг |
|
|
|
|
tх.в. |
tсм |
ϑух |
tг.в |
Рис. 13.23. Схемы устройств повышения температуры холодного воздуха в воздухоподогревателе: 1 – дутьевой вентилятор; 2 – шибер, регулирующий рециркуляцию; 3 – калорифер; 4 – экономайзер низкого давления; 5 – циркуляционный насос; 6 – экономайзер; 7 – воздух; 8 – воздухоподогреватель; 9 – каскадная часть; 10 – основная часть; 11 – смеситель; 12 – линия байпаса
390
В настоящее время проводятся работы по усовершенствованию конструкций как рекуперативных, так и регенеративных воздухоподогревателей. Исследуется работа трубчатых подогревателей со стеклянными и эмалированными трубками; проверяются новые оптимальные конструктивные решения по стальным трубчатым подогревателям; проверяются по РВП новые уплотнения и набивки, в частности, с жидкими промежуточными теплоносителями, с плотным зернистым слоем и др.
13.4.2. Загрязнение и абразивный износ поверхностей
Поступающие вместе с топливом в зону горения минеральные примеси подвергаются высокотемпературным физическим преобразованиям: часть из них плавится и даже испаряется, другие в этих условиях образуют новые эвтектические сплавы и соединяются в более крупные расплавленные частицы, которые выпадают в нижнюю часть топки (холодную воронку) в виде шлака. Основная масса мелких золовых частиц уносится из топки с продуктами сгорания в виде летучей золы.
Характеристики плавления частиц золы. В составе летучей золы име-
ются три группы частиц, отличающиеся химическим ставом и физическим состоянием в зоне высоких температур.
Легкоплавкие соединения имеют температуру плавления 700–850 °С. Это в основном хлориды и сульфаты щелочных металлов ( NaCl , CaCl2 ,
Na2SO4 , MgCl2 , Al2 (SO4 )3 ). В зоне высоких температур ядра факела они ис-
паряются, а затем конденсируются на поверхности труб, так как температура чистой стенки всегда менее 700 °С. Их количество в составе летуче золы невелико (менее 1%).
Среднеплавкие компоненты золы с температурой плавления 900– 1100 °С ( FeS, FeO , Na2SiO3 , K2SO4 и др) находятся в топке в расплавленном
состоянии, при контакте с поверхностью нагрева налипают на нее и по мере снижения температуры застывают и цементируют другие твердые частицы.
Тугоплавкими компонентами золы являются, как правило, оксиды металлов типа MeO, (CaO , MgO, Fe2O3 ), а также SiO2 , Al2O3 и др. Температу-
ра их плавления (1600–2800 °С) превышает температуру газов в ядре факела, поэтому они проходят зону горения без изменения своего состояния, оставаясь твердыми. Ввиду малых размеров они уносятся потоком газов и составляют основную массу летучей золы
Плавкостные характеристики золы в топочной камере зависят от соотношения основных и кислых (по химическим свойствам) компонентов, входящих в расплав. Количественно это соотношение характеризуют показателем кислотности расплава
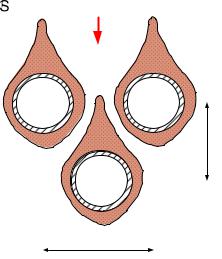
391
K = |
Fe2O3 +CaO+MgO+Na2O+K2O . |
(13.8) |
|
SiO2 + Al2O3 + TiO2 |
|
При значении K >1 шлаки являются основными по химическим свойствам, а при K <1 – кислыми. Последние относятся к так называемым «длинным» шлакам с более медленным изменением вязкости при снижении температуры, они более предпочтительны при организации жидкого шлаудаления. В то же время при твердом шлакоудалении эти шлаки более склонны к шлакованию экранов топки.
Летучая зола представляет собой эвтектические смеси компонентов различной плавкости. В таких смесях тугоплавкие компоненты типа MeO при их малом содержании в золе (5–20%) приводят к снижению температуры расплавления эвтектической смеси (особенно это относится к окислам Fe2O3
и CaO при наличии в потоке SO2 ), что создает опасность шлакования кон-
вективных поверхностей в горизонтальном газоходе. При содержании MeO в золе более 25%, а также при повышенном содержании Al2O3 и SiO2 (более
65% по массе) температура плавления золовых частиц повышается и шлакование не имеет места даже при повышенной температуре потока газов.
Виды отложений на поверхностях нагрева. По степени механической прочности образующихся на поверхности металла отложений они разделяются на сыпучие, связанные рыхлые, прочные и сплавленные (шлаковые). Шлаковые отложения развиваются в зоне температур газов 700–900 °С (рис. 13.24) и могут привести к перекрытию (зашлакованию) части газохода, что вызовет необходимость снижения нагрузки на котле ввиду ограничения тяги
в результате резкого роста аэродинамического сопротивления газового тракта котла.
В образовании связанных рыхлых и плотных отложений участвуют щелочные соединения ( K2O, Na2O ), а также сульфатные
S2
Рис. 13.24. Характер золового заноса поперечно обтекаемого низкотемпературного пучка с шахматным расположением труб при сжигании угля
типа Na2SO4 и золовые фракции с повышен-
ным содержанием оксидов железа. Характер плотных отложений близок к показанному на рис. 13.24, только в меньших масштабах, они развиваются на поверхностях воздухоподогревателя при сжигании мазута и температуре стенки ниже 200 °С, где начинается конденсация на поверхности нагрева паров серной кислоты совместно с влагой. При наличии силикатов натрия образуются твердые, прочные, стеклоподобные направления на трубах.
На твердых топливах в этой зоне обра-
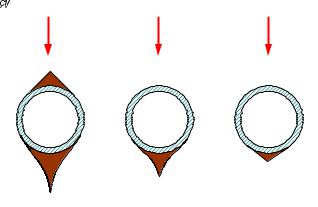
392
зуется слой рыхлых влажных отложений, содержащих золовые частицы различного состава.
В зоне относительно низких температур газового потока – менее 600– 700 °C и до температур «холодной части» воздухоподогревателя – наиболее распространены при сжигании твердых топлив сыпучие отложения. Они имеют слабую механическую связь с поверхностью и между собой и легко удаляются при встряхивании или прямом ударе по участку отложений. Кроме аэродинамических факторов, приводящих к набрасыванию частиц золы на поверхности труб, в переносе мелких фракций золы участвуют электростатические силы (за счет разного электростатического заряда поверхности трубы и частички золы), а также силы термофореза (движение частиц из горячего потока к более холодной поверхности трубы).
Сыпучие отложения преимущественно образуются на тыльной стороне трубы по отношению к направлению движения газового потока, в зоне вихрей в следе за трубой (рис. 13.25) и сильно зависят от скорости потока. На лобовой стороне заметные сыпучие отложения появляются лишь при малых скоростях набегающего потока (менее 5–6 м/с) или при наличии в потоке
очень тонкой летучей золы (при жидком шлакоудалении в топке). |
|
||
|
Интенсивность |
образова- |
|
|
ния сыпучих отложений сильно |
||
|
зависит от фракционного состава |
||
|
золы. Крупные фракции золы |
||
|
размером свыше 30 мкм облада- |
||
|
ют достаточно большой кинети- |
||
|
ческой энергией |
при движении |
|
|
около трубы и разрушают нарас- |
||
|
тающие отложения. В таких слу- |
||
Рис. 13.25. Загрязнение труб сыпучими отложе- |
чаях отложения оказываются не- |
||
значительными. |
В |
длительной |
|
ниями при разных скоростях движения газов |
эксплуатации при |
постоянном |
|
|
контакте отложений с газовым потоком может происходить связывание (спекание) частиц между собой за счет сульфатных соединений Na и K , поэтому желательно систематическое удаление таких отложений.
Сыпучие и другие виды загрязнений поверхности труб ухудшают теплообмен с газовым потоком и снижают эффективность ее работы. Оценку тепловой эффективности поверхности нагрева производят через приведенный
коэффициент загрязнения, ξз , (м2 × К) |
/Вт: |
|
||
xз |
= |
dз |
, |
(13.9) |
|
||||
|
|
lз |
|
где δз , λз – средняя условная толщина слоя отложений по периметру трубы,

393
м, и теплопроводность золового слоя, Вт/(м × К) .
Изменение коэффициента загрязнения ξз в разных условиях эксплуата-
ции позволяет оценить изменение размера отложений, т. е. установить влияние режимных факторов на характер отложений. Значение коэффициента ξз
получают при испытаниях путем сравнения реального тепловосприятия поверхности с теоретическим при совершенно чистых трубах.
Как следует из результатов испытаний (рис. 13.26), загрязнение труб отложениями летучей золы мало зависит от концентрации ее в потоке дымовых газов. Разница в загрязнениях наблюдается только в первые часы работы до установления динамического равновесия. Более интенсивное загрязнение труб (более высокое значение коэффициента ξз имеет место в случае присут-
ствия в потоке тонких фракций золы. Во всех случаях с увеличением скорости потока загрязнения труб сыпучими отложениями уменьшаются, что связано с ростом кинетической энергии частиц и разрушением образующихся отложений более крупными частицами.
ε,103 |
17,5 |
ε,103 |
|
Коридорный пучок |
|
|
14,0 |
|
2 |
|
|
|
(м К)/Вт |
|
Шахматный пучок |
||
|
|
|
|
|
|
|
10,5 |
|
3 |
|
|
|
|
|
|
|
|
|
7,0 |
|
|
|
4 |
|
|
|
|
|
|
|
3,5 |
|
|
|
|
τ |
0 4 |
6 |
8 |
10 12 14 ω , м/с 18 |
а) |
б) |
Рис. 13.26. Изменение коэффициента загрязнении труб ξ в зависимости от концентрации золы в потоке и ее крупности (трубы d = 38 мм, S1 / d = S2 / = 2 : а – в зависимости от вре-
мени работы; б – в зависимости от скорости потока; 1 – концентрация золы 21 г/м3; 2 – то же при концентрации 7 г/м3; 3 – мелкая зола; 4 – крупная зола
Большое влияние на степень загрязнения поверхности оказывают тип пучка труб (шахматный или коридорный) и продольный шаг труб S2 в шах-
матном пучке. При равных прочих условиях (скорость газов, диаметр труб) коэффициент загрязнения коридорного пучка в 1,7–3,5 раза больше, чем шахматного (рис. 13.27). С уменьшением продольного шага труб S2 (уплотнение
пучка труб) загрязнение существенно уменьшается. Загрязнение труб существенно возрастает при низких скоростях газового потока, поэтому скорости газов в поверхностях менее 3–4 м/с не допускаются, а с учетом рабочего диапазона нагрузок котла (до 0,5Dном ) скорости газов при номинальной нагрузке
принимаются не ниже 6 м/с для поперечно омываемых пучков труб и не менее 8 м/с – для продольного тока газов в поверхностях воздухоподогревателей.

394
Абразивный износ поверхностей нагрева. Сущность абразивного износа заключается в том, что крупные частицы золы, обладающие достаточной твердостью и остротой граней, при ударах о стенку трубы непрерывно срезают с поверхности микроскопически малые слои оксида металла, постепенно уменьшая в этом месте толщину стенки трубы) (рис. 13.28). Частицы несгоревшего топлива (чаще у антрацитов и полуантрацитов) также вызывают истирание поверхности.
10
9
8
7
6
5
4
3
2
1
ε,103
(м2К)/Вт
S2 d = 3,0
2,0 1,5
1,2
1,0
|
|
|
К |
о |
|
|
|
|
|
||
|
|
|
|
|
|
р |
|
|
|
|
|
|
|
|
|
|
|
и |
|
|
|
|
|
|
|
|
|
|
|
д |
|
|
|
|
|
|
|
|
|
|
|
о |
|
|
|
|
|
|
|
|
|
|
|
р |
|
|
|
|
|
|
|
|
|
|
|
н |
|
|
|
|
|
|
|
|
|
|
|
ы |
|
|
|
||
|
|
|
|
|
|
|
|
й |
|
|
|
|
|
|
|
|
|
|
|
|
п |
|
|
|
|
|
|
|
|
|
|
|
у |
|
|
|
|
|
|
|
|
|
|
|
ч |
|
|
Ш |
|
|
|
|
|
|
|
|
о |
|
|
а |
|
|
|
|
|
|
|
|
к |
||
|
|
|
|
|
|
|
|
|
|
т |
|
|
х |
|
|
|
|
|
|
|
|
|
|
|
|
м |
|
|
|
|
|
|
|
|
р |
|
|
а |
|
|
|
|
|
|
|
||
|
|
|
|
|
|
|
|
|
у |
||
|
|
|
т |
|
|
|
|
|
|
б |
|
|
|
|
|
н |
ый п |
|
|
|
|||
|
|
|
|
|
|
у |
|
|
|
|
|
|
|
|
|
|
|
ч |
|
|
|
|
|
|
|
|
|
|
|
|
о |
|
|
|
|
|
|
|
|
|
|
|
|
кт |
|
||
|
|
|
|
|
|
|
|
|
р |
|
|
|
|
|
|
|
|
|
|
|
у |
|
|
|
|
|
|
|
|
|
|
|
|
б |
|
|
|
|
|
|
|
|
|
|
|
|
|
0 |
5 |
6 |
7 |
8 |
9 10 11 12 13 ω, м/с15 |
Рис. 13.27. Сравнение коэффициентов загрязнения различных пучков труб
Таким образом, золовой износ прежде всего определяется абразивностью частиц золы. Последняя прежде всего зависит от содержания SiO2 в зо-
ле и заметно увеличивается, когда SiO2 > 60% . Так, например, сильно абра-
зивными свойствами обладает зола экибастузского каменного угля, так как в ее составе содержание
SiO2 > 80% .
а) |
б) |
Рис. 13.28. Места и характер абразивного износа труб: а
– места абразивного износа трубы поперечным набегающим потоком газов: б – упрошенная схема срезания частицами золы металла с поверхности трубы; 1 – место износа металла трубы
Интенсивность абразивного износа поверхности нагрева неравномерна как по сечению газохода, в котором размещена поверхность, так и по периметру труб. Существенное влияние на неравномерность износа оказывает поворот газов на 90° при входе в конвективную шахту, при этом наиболее грубые фракции золы от-
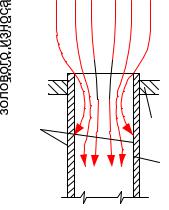
395
брасываются к задней стене шахты и создают в этой зоне поверхности нагрева повышенную опасность износа труб.
|
При поперечном обтекании шахматного |
|
пучка труб наибольшему абразивному износу |
|
подвержены участки трубы при угле атаки га- |
|
зов 30–50°. Коридорные пучки подвергаются |
|
существенно меньшему износу, так как по- |
|
следующие трубы находятся в аэродинамиче- |
|
ской тени впередистоящих. При продольном |
|
движении газов внутри труб (воздухоподогре- |
|
ватель) абразивный износ происходит на |
|
входном участке трубы длиной 150–200 мм за |
Рис. 13.29. Абразивный износ |
счет удара крупных частиц о стенку после су- |
жения струи на входе (рис. 13.29). В после- |
|
трубы при продольном обтека- |
дующем поток стабилизируется, и крупные |
нии: 1 – труба воздухоподогрева- |
частицы будут двигаться параллельно стенке |
теля; 2 – верхняя трубная доска |
на некотором ее удалении. |
|
Интенсивность износа также зависит от общего количества золы в топливе, т.е. от Ap , и определяется концентрацией частиц золы в газовом потоке, г/м3:
mзл |
= |
10Араун |
× |
273 |
|
(13.10) |
|||
|
Vг |
273 + Jг |
|
||||||
|
|
|
|
|
|||||
или в безразмерном виде |
|
|
|
|
|
|
|
|
|
|
|
|
|
Араун |
|
||||
|
mзл = |
|
. |
(13.11) |
|||||
|
(100G ) |
||||||||
|
|
|
|
|
|
г |
|
||
Здесь Vг – объем газов при сжигании 1 кг топлива, м /кг; аун |
– доля золы, |
||||||||
уносимая из топки с газовым потоком; Gг |
– масса дымовых газов, кг/кг топ- |
||||||||
лива: |
|
|
|
|
|
|
|
|
|
G =1- 0,01Ар |
+1,306aV 0 . |
(13.12) |
|||||||
г |
|
|
|
|
|
|
|
в |
|
Абразивный износ более сильно проявляется в зоне температур газов ниже 600 °C, когда частицы теряют поверхностную пластичность и становятся твердыми, т.е. в верхней части конвективной шахты. Интенсивность износа неравномерна как по сечению газохода, так и по периметру труб. При входе в конвективную шахту из горизонтального газохода газы имеют разворот на 90 °С, в результате чего наиболее грубые фракции золы отбрасываются к задней стене шахты и имеют там повышенную концентрацию.
При поперечном обтекании трубы наибольшему износу подвергаются боковые ее стенки под углом 30–40 °С, где обтекающий трубу поток прохо-
396
дит по касательной к поверхности (рис. 13.28). Коридорные пучки подвергаются существенно меньшему износу, так как по ходу газов трубы находятся в аэродинамической тени первой (лобовой) трубы, на которую к тому же поток газов набегает с более низкой скоростью (из свободного газохода), чем скорость газов в межтрубном пространстве пучка.
Интенсивность износа определяется:
1)кинетической энергией отдельных частиц золы, которая зависит квадрата скорости газов – wг2 ;
2)количеством частиц, проходящих у поверхности в единицу времени, которое зависит от концентрации частиц в потоке газов μзл и является возрас-
тающей функцией от скорости wг ;
3)неравномерностью концентраций золы в потоке kμ и скоростей газов
всечении kω ;
4)плотностью расположения труб в поперечноомываемом пучке, что
определяет торможение частиц при контакте с поверхностью и уменьшение их скорости в следующем ряду труб, по сравнению со скоростью газов.
В итоге интенсивность износа, Iиз мм/год, зависит в третьей степени от скорости газов:
I |
|
= 0,028amk |
|
m |
|
(k |
w |
) |
3 |
æ S |
- d ö1,8 |
t |
|
× R0,6 |
, |
(13.13) |
||
|
|
|
|
|
1 |
|
|
|
||||||||||
из |
μ |
зл |
|
ç |
|
÷ |
p |
|||||||||||
|
|
|
|
ω г |
|
|
|
|
90 |
|
|
|||||||
|
|
|
|
|
|
|
|
|
|
è |
|
S1 ø |
|
|
|
|
|
|
где a – коэффициент абразивности золы, |
|
мм × с3/(г × ч); |
m – относительный |
показатель износоустойчивости труб, зависящий от химического состава стали; τp – время эксплуатации поверхности, ч/год. На входе в конвективную
шахту при П-образной компоновке котла коэффициенты неравномерности концентраций золы и скоростей газов имеют следующие значения kμ =1,2 ÷1,25 и kω =1,25 ÷1,3. Допустимым считается износ стенки труб
Iиз = 0,2 мм/год из расчета нормальной работы трубы не менее 10 лет ( τp = 60 − 70 тыс. час). Максимально допустимая по условиям износа скорость газов в первом ряду конвективного пакета верхней части шахты, ωиз ,
м/с, определяется из (13.13) и для шахматного пучка труб при относительном шаге труб S1 / d = 2,5 составляет:
Топливо |
ωиз , м/с |
Топливо |
ωиз , м/с |
Экибастузский уголь |
7,0 |
Кизеловский уголь |
10,5 |
Подмосковный уголь |
9,0 |
Антрацит марки АШ |
11,5 |
Челябинский уголь |
10,0 |
Донецкий уголь марки Т |
12,0 |