
- •1. INTEGRATED AND AUTOMATED MANUFACTURING
- •1.1 INTRODUCTION
- •1.1.1 Why Integrate?
- •1.1.2 Why Automate?
- •1.2 THE BIG PICTURE
- •1.2.2 The Architecture of Integration
- •1.2.3 General Concepts
- •1.3 PRACTICE PROBLEMS
- •2. AN INTRODUCTION TO LINUX/UNIX
- •2.1 OVERVIEW
- •2.1.1 What is it?
- •2.1.2 A (Brief) History
- •2.1.3 Hardware required and supported
- •2.1.4 Applications and uses
- •2.1.5 Advantages and Disadvantages
- •2.1.6 Getting It
- •2.1.7 Distributions
- •2.1.8 Installing
- •2.2 USING LINUX
- •2.2.1 Some Terminology
- •2.2.2 File and directories
- •2.2.3 User accounts and root
- •2.2.4 Processes
- •2.3 NETWORKING
- •2.3.1 Security
- •2.4 INTERMEDIATE CONCEPTS
- •2.4.1 Shells
- •2.4.2 X-Windows
- •2.4.3 Configuring
- •2.4.4 Desktop Tools
- •2.5 LABORATORY - A LINUX SERVER
- •2.6 TUTORIAL - INSTALLING LINUX
- •2.7 TUTORIAL - USING LINUX
- •2.8 REFERENCES
- •3. AN INTRODUCTION TO C/C++ PROGRAMMING
- •3.1 INTRODUCTION
- •3.2 PROGRAM PARTS
- •3.3 CLASSES AND OVERLOADING
- •3.4 HOW A ‘C’ COMPILER WORKS
- •3.5 STRUCTURED ‘C’ CODE
- •3.6 COMPILING C PROGRAMS IN LINUX
- •3.6.1 Makefiles
- •3.7 ARCHITECTURE OF ‘C’ PROGRAMS (TOP-DOWN)
- •3.8 CREATING TOP DOWN PROGRAMS
- •3.9 CASE STUDY - THE BEAMCAD PROGRAM
- •3.9.1 Objectives:
- •3.9.2 Problem Definition:
- •3.9.3 User Interface:
- •3.9.3.1 - Screen Layout (also see figure):
- •3.9.3.2 - Input:
- •3.9.3.3 - Output:
- •3.9.3.4 - Help:
- •3.9.3.5 - Error Checking:
- •3.9.3.6 - Miscellaneous:
- •3.9.4 Flow Program:
- •3.9.5 Expand Program:
- •3.9.6 Testing and Debugging:
- •3.9.7 Documentation
- •3.9.7.1 - Users Manual:
- •3.9.7.2 - Programmers Manual:
- •3.9.8 Listing of BeamCAD Program.
- •3.10 PRACTICE PROBLEMS
- •3.11 LABORATORY - C PROGRAMMING
- •4. NETWORK COMMUNICATION
- •4.1 INTRODUCTION
- •4.2 NETWORKS
- •4.2.1 Topology
- •4.2.2 OSI Network Model
- •4.2.3 Networking Hardware
- •4.2.4 Control Network Issues
- •4.2.5 Ethernet
- •4.2.6 SLIP and PPP
- •4.3 INTERNET
- •4.3.1 Computer Addresses
- •4.3.2 Computer Ports
- •4.3.2.1 - Mail Transfer Protocols
- •4.3.2.2 - FTP - File Transfer Protocol
- •4.3.2.3 - HTTP - Hypertext Transfer Protocol
- •4.3.3 Security
- •4.3.3.1 - Firewalls and IP Masquerading
- •4.4 FORMATS
- •4.4.1 HTML
- •4.4.2 URLs
- •4.4.3 Encryption
- •4.4.4 Clients and Servers
- •4.4.5 Java
- •4.4.6 Javascript
- •4.5 NETWORKING IN LINUX
- •4.5.1 Network Programming in Linux
- •4.6 DESIGN CASES
- •4.7 SUMMARY
- •4.8 PRACTICE PROBLEMS
- •4.9 LABORATORY - NETWORKING
- •4.9.1 Prelab
- •4.9.2 Laboratory
- •5. DATABASES
- •5.1 SQL AND RELATIONAL DATABASES
- •5.2 DATABASE ISSUES
- •5.3 LABORATORY - SQL FOR DATABASE INTEGRATION
- •5.4 LABORATORY - USING C FOR DATABASE CALLS
- •6. COMMUNICATIONS
- •6.1 SERIAL COMMUNICATIONS
- •6.2 SERIAL COMMUNICATIONS UNDER LINUX
- •6.3 PARALLEL COMMUNICATIONS
- •6.4 LABORATORY - SERIAL INTERFACING AND PROGRAMMING
- •6.5 LABORATORY - STEPPER MOTOR CONTROLLER
- •7. PROGRAMMABLE LOGIC CONTROLLERS (PLCs)
- •7.1 BASIC LADDER LOGIC
- •7.2 WHAT DOES LADDER LOGIC DO?
- •7.2.1 Connecting A PLC To A Process
- •7.2.2 PLC Operation
- •7.3 LADDER LOGIC
- •7.3.1 Relay Terminology
- •7.3.2 Ladder Logic Inputs
- •7.3.3 Ladder Logic Outputs
- •7.4 LADDER DIAGRAMS
- •7.4.1 Ladder Logic Design
- •7.4.2 A More Complicated Example of Design
- •7.5 TIMERS/COUNTERS/LATCHES
- •7.6 LATCHES
- •7.7 TIMERS
- •7.8 COUNTERS
- •7.9 DESIGN AND SAFETY
- •7.9.1 FLOW CHARTS
- •7.10 SAFETY
- •7.10.1 Grounding
- •7.10.2 Programming/Wiring
- •7.10.3 PLC Safety Rules
- •7.10.4 Troubleshooting
- •7.11 DESIGN CASES
- •7.11.1 DEADMAN SWITCH
- •7.11.2 CONVEYOR
- •7.11.3 ACCEPT/REJECT SORTING
- •7.11.4 SHEAR PRESS
- •7.12 ADDRESSING
- •7.12.1 Data Files
- •7.12.1.1 - Inputs and Outputs
- •7.12.1.2 - User Numerical Memory
- •7.12.1.3 - Timer Counter Memory
- •7.12.1.4 - PLC Status Bits (for PLC-5s)
- •7.12.1.5 - User Function Memory
- •7.13 INSTRUCTION TYPES
- •7.13.1 Program Control Structures
- •7.13.2 Branching and Looping
- •7.13.2.1 - Immediate I/O Instructions
- •7.13.2.2 - Fault Detection and Interrupts
- •7.13.3 Basic Data Handling
- •7.13.3.1 - Move Functions
- •7.14 MATH FUNCTIONS
- •7.15 LOGICAL FUNCTIONS
- •7.15.1 Comparison of Values
- •7.16 BINARY FUNCTIONS
- •7.17 ADVANCED DATA HANDLING
- •7.17.1 Multiple Data Value Functions
- •7.17.2 Block Transfer Functions
- •7.18 COMPLEX FUNCTIONS
- •7.18.1 Shift Registers
- •7.18.2 Stacks
- •7.18.3 Sequencers
- •7.19 ASCII FUNCTIONS
- •7.20 DESIGN TECHNIQUES
- •7.20.1 State Diagrams
- •7.21 DESIGN CASES
- •7.21.1 If-Then
- •7.21.2 For-Next
- •7.21.3 Conveyor
- •7.22 IMPLEMENTATION
- •7.23 PLC WIRING
- •7.23.1 SWITCHED INPUTS AND OUTPUTS
- •7.23.1.1 - Input Modules
- •7.23.1.2 - Actuators
- •7.23.1.3 - Output Modules
- •7.24 THE PLC ENVIRONMENT
- •7.24.1 Electrical Wiring Diagrams
- •7.24.2 Wiring
- •7.24.3 Shielding and Grounding
- •7.24.4 PLC Environment
- •7.24.5 SPECIAL I/O MODULES
- •7.25 PRACTICE PROBLEMS
- •7.26 REFERENCES
- •7.27 LABORATORY - SERIAL INTERFACING TO A PLC
- •8. PLCS AND NETWORKING
- •8.1 OPEN NETWORK TYPES
- •8.1.1 Devicenet
- •8.1.2 CANbus
- •8.1.3 Controlnet
- •8.1.4 Profibus
- •8.2 PROPRIETARY NETWORKS
- •8.2.0.1 - Data Highway
- •8.3 PRACTICE PROBLEMS
- •8.4 LABORATORY - DEVICENET
- •8.5 TUTORIAL - SOFTPLC AND DEVICENET
- •9. INDUSTRIAL ROBOTICS
- •9.1 INTRODUCTION
- •9.1.1 Basic Terms
- •9.1.2 Positioning Concepts
- •9.1.2.1 - Accuracy and Repeatability
- •9.1.2.2 - Control Resolution
- •9.1.2.3 - Payload
- •9.2 ROBOT TYPES
- •9.2.1 Basic Robotic Systems
- •9.2.2 Types of Robots
- •9.2.2.1 - Robotic Arms
- •9.2.2.2 - Autonomous/Mobile Robots
- •9.2.2.2.1 - Automatic Guided Vehicles (AGVs)
- •9.3 MECHANISMS
- •9.4 ACTUATORS
- •9.5 A COMMERCIAL ROBOT
- •9.5.1 Mitsubishi RV-M1 Manipulator
- •9.5.2 Movemaster Programs
- •9.5.2.0.1 - Language Examples
- •9.5.3 Command Summary
- •9.6 PRACTICE PROBLEMS
- •9.7 LABORATORY - MITSUBISHI RV-M1 ROBOT
- •9.8 TUTORIAL - MITSUBISHI RV-M1
- •10. OTHER INDUSTRIAL ROBOTS
- •10.1 SEIKO RT 3000 MANIPULATOR
- •10.1.1 DARL Programs
- •10.1.1.1 - Language Examples
- •10.1.1.2 - Commands Summary
- •10.2 IBM 7535 MANIPULATOR
- •10.2.1 AML Programs
- •10.3 ASEA IRB-1000
- •10.4 UNIMATION PUMA (360, 550, 560 SERIES)
- •10.5 PRACTICE PROBLEMS
- •10.6 LABORATORY - SEIKO RT-3000 ROBOT
- •10.7 TUTORIAL - SEIKO RT-3000 ROBOT
- •10.8 LABORATORY - ASEA IRB-1000 ROBOT
- •10.9 TUTORIAL - ASEA IRB-1000 ROBOT
- •11. ROBOT APPLICATIONS
- •11.0.1 Overview
- •11.0.2 Spray Painting and Finishing
- •11.0.3 Welding
- •11.0.4 Assembly
- •11.0.5 Belt Based Material Transfer
- •11.1 END OF ARM TOOLING (EOAT)
- •11.1.1 EOAT Design
- •11.1.2 Gripper Mechanisms
- •11.1.2.1 - Vacuum grippers
- •11.1.3 Magnetic Grippers
- •11.1.3.1 - Adhesive Grippers
- •11.1.4 Expanding Grippers
- •11.1.5 Other Types Of Grippers
- •11.2 ADVANCED TOPICS
- •11.2.1 Simulation/Off-line Programming
- •11.3 INTERFACING
- •11.4 PRACTICE PROBLEMS
- •11.5 LABORATORY - ROBOT INTERFACING
- •11.6 LABORATORY - ROBOT WORKCELL INTEGRATION
- •12. SPATIAL KINEMATICS
- •12.1 BASICS
- •12.1.1 Degrees of Freedom
- •12.2 HOMOGENEOUS MATRICES
- •12.2.1 Denavit-Hartenberg Transformation (D-H)
- •12.2.2 Orientation
- •12.2.3 Inverse Kinematics
- •12.2.4 The Jacobian
- •12.3 SPATIAL DYNAMICS
- •12.3.1 Moments of Inertia About Arbitrary Axes
- •12.3.2 Euler’s Equations of Motion
- •12.3.3 Impulses and Momentum
- •12.3.3.1 - Linear Momentum
- •12.3.3.2 - Angular Momentum
- •12.4 DYNAMICS FOR KINEMATICS CHAINS
- •12.4.1 Euler-Lagrange
- •12.4.2 Newton-Euler
- •12.5 REFERENCES
- •12.6 PRACTICE PROBLEMS
- •13. MOTION CONTROL
- •13.1 KINEMATICS
- •13.1.1 Basic Terms
- •13.1.2 Kinematics
- •13.1.2.1 - Geometry Methods for Forward Kinematics
- •13.1.2.2 - Geometry Methods for Inverse Kinematics
- •13.1.3 Modeling the Robot
- •13.2 PATH PLANNING
- •13.2.1 Slew Motion
- •13.2.1.1 - Joint Interpolated Motion
- •13.2.1.2 - Straight-line motion
- •13.2.2 Computer Control of Robot Paths (Incremental Interpolation)
- •13.3 PRACTICE PROBLEMS
- •13.4 LABORATORY - AXIS AND MOTION CONTROL
- •14. CNC MACHINES
- •14.1 MACHINE AXES
- •14.2 NUMERICAL CONTROL (NC)
- •14.2.1 NC Tapes
- •14.2.2 Computer Numerical Control (CNC)
- •14.2.3 Direct/Distributed Numerical Control (DNC)
- •14.3 EXAMPLES OF EQUIPMENT
- •14.3.1 EMCO PC Turn 50
- •14.3.2 Light Machines Corp. proLIGHT Mill
- •14.4 PRACTICE PROBLEMS
- •14.5 TUTORIAL - EMCO MAIER PCTURN 50 LATHE (OLD)
- •14.6.1 LABORATORY - CNC MACHINING
- •15. CNC PROGRAMMING
- •15.1 G-CODES
- •15.3 PROPRIETARY NC CODES
- •15.4 GRAPHICAL PART PROGRAMMING
- •15.5 NC CUTTER PATHS
- •15.6 NC CONTROLLERS
- •15.7 PRACTICE PROBLEMS
- •15.8 LABORATORY - CNC INTEGRATION
- •16. DATA AQUISITION
- •16.1 INTRODUCTION
- •16.2 ANALOG INPUTS
- •16.3 ANALOG OUTPUTS
- •16.4 REAL-TIME PROCESSING
- •16.5 DISCRETE IO
- •16.6 COUNTERS AND TIMERS
- •16.7 ACCESSING DAQ CARDS FROM LINUX
- •16.8 SUMMARY
- •16.9 PRACTICE PROBLEMS
- •16.10 LABORATORY - INTERFACING TO A DAQ CARD
- •17. VISIONS SYSTEMS
- •17.1 OVERVIEW
- •17.2 APPLICATIONS
- •17.3 LIGHTING AND SCENE
- •17.4 CAMERAS
- •17.5 FRAME GRABBER
- •17.6 IMAGE PREPROCESSING
- •17.7 FILTERING
- •17.7.1 Thresholding
- •17.8 EDGE DETECTION
- •17.9 SEGMENTATION
- •17.9.1 Segment Mass Properties
- •17.10 RECOGNITION
- •17.10.1 Form Fitting
- •17.10.2 Decision Trees
- •17.11 PRACTICE PROBLEMS
- •17.12 TUTORIAL - LABVIEW BASED IMAQ VISION
- •17.13 LABORATORY - VISION SYSTEMS FOR INSPECTION
- •18. INTEGRATION ISSUES
- •18.1 CORPORATE STRUCTURES
- •18.2 CORPORATE COMMUNICATIONS
- •18.3 COMPUTER CONTROLLED BATCH PROCESSES
- •18.4 PRACTICE PROBLEMS
- •18.5 LABORATORY - WORKCELL INTEGRATION
- •19. MATERIAL HANDLING
- •19.1 INTRODUCTION
- •19.2 VIBRATORY FEEDERS
- •19.3 PRACTICE QUESTIONS
- •19.4 LABORATORY - MATERIAL HANDLING SYSTEM
- •19.4.1 System Assembly and Simple Controls
- •19.5 AN EXAMPLE OF AN FMS CELL
- •19.5.1 Overview
- •19.5.2 Workcell Specifications
- •19.5.3 Operation of The Cell
- •19.6 THE NEED FOR CONCURRENT PROCESSING
- •19.7 PRACTICE PROBLEMS
- •20. PETRI NETS
- •20.1 INTRODUCTION
- •20.2 A BRIEF OUTLINE OF PETRI NET THEORY
- •20.3 MORE REVIEW
- •20.4 USING THE SUBROUTINES
- •20.4.1 Basic Petri Net Simulation
- •20.4.2 Transitions With Inhibiting Inputs
- •20.4.3 An Exclusive OR Transition:
- •20.4.4 Colored Tokens
- •20.4.5 RELATIONAL NETS
- •20.5 C++ SOFTWARE
- •20.6 IMPLEMENTATION FOR A PLC
- •20.7 PRACTICE PROBLEMS
- •20.8 REFERENCES
- •21. PRODUCTION PLANNING AND CONTROL
- •21.1 OVERVIEW
- •21.2 SCHEDULING
- •21.2.1 Material Requirements Planning (MRP)
- •21.2.2 Capacity Planning
- •21.3 SHOP FLOOR CONTROL
- •21.3.1 Shop Floor Scheduling - Priority Scheduling
- •21.3.2 Shop Floor Monitoring
- •22. SIMULATION
- •22.1 MODEL BUILDING
- •22.2 ANALYSIS
- •22.3 DESIGN OF EXPERIMENTS
- •22.4 RUNNING THE SIMULATION
- •22.5 DECISION MAKING STRATEGY
- •23. PLANNING AND ANALYSIS
- •23.1 FACTORS TO CONSIDER
- •23.2 PROJECT COST ACCOUNTING
- •24. REFERENCES
- •25. APPENDIX A - PROJECTS
- •25.1 TOPIC SELECTION
- •25.1.1 Previous Project Topics
- •25.2 CURRENT PROJECT DESCRIPTIONS
- •26. APPENDIX B - COMMON REFERENCES
- •26.1 JIC ELECTRICAL SYMBOLS
- •26.2 NEMA ENCLOSURES
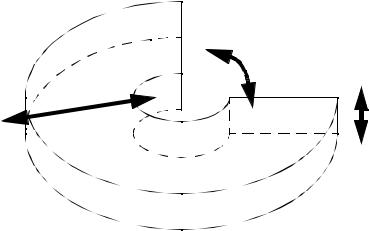
|
page 300 |
max. force |
40 lbs |
• T-axis |
|
motion |
revolute |
Range |
290 degrees |
Resolution |
0.003 deg. |
Speed |
|
max. speed |
90 deg/sec |
max. torque |
358. in.lbs |
• The workspace is pictured below, |
|
A-axis (290 deg)
R-axis (300mm)
Z-axis (120mm)
10.1.1 DARL Programs
•All DARL comments follow ’ at any position on a line.
•Statements are ended with a colon, and as long as colons are used, more than one statement can be used on a line.
•Line numbering is required for DARL programs.
page 301
•Dimensions are given in millimeters in the programs.
•Commas and spaces are treated as equivalent.
•A sample program is given below with comments for explanation,
10 SPEED 250 ‘set the speed of the robot 20 T1 = 0. -350. -50. 0. ‘ first point 30 T2 = 0. -50. -350. 0. ‘second point 40 T3 = 30. -50. -350. 30. ‘third point
50 MOVE T1:MOVE T2:MOVE T3 ‘move the gripper to different points in space 60 OUTPUT +OG0 200 ‘open gripper
70 MOVE T1 + T2 ‘add two positions and move there 70 OUTPUT +OG1 200 ‘close gripper
80 STOP
10.1.1.1 - Language Examples
•First, points can be defined in programs, they can also be defined by moving the robot to the location and storing the value. This allows the robot to accurately find points without measuring. It also means that points location values don’t need to appear in programs, they are stored in memory.
•A example that uses for-next, if-then, goto and gosub-return commands is shown below. These commands are very standard in their use.
page 302
10 |
FOR A |
= 2 TO 10 ‘ start a loop that will count from 2 to 10 |
||
40 |
IF A = 4 |
THEN GOTO 100 ‘when a has a value of 4 jump to |
line 100 |
|
50 |
IF A = 6 |
THEN GOSUB 200 ‘ when a has a value of 6 go to |
subroutine |
|
60 |
NEXT A ‘ |
go back to line 10 and increase the value of a |
until it reaches 10 |
|
70 |
END ‘end |
the program |
|
|
100 MOVE |
T1 |
‘ go to point 1 |
|
|
110 NEXT |
A ‘ go back to line 10 |
|
||
200 MOVE |
T2 |
‘ go to point 2 |
|
210 RETURN ‘ go back to where we left line 50
• A example that uses motion is shown below. The ‘move’ command causes a motion to another point by only turning the needed joints. ‘moves’ causes a more complex motion resulting in a straight line tool motion between points. ‘movec’ allows a circular interpolation dictated by three points (the start, and the two given). The shave command forces the robot to fully complete a motion and stop before going to the next point. The sync command will move the robot, but keep the gripper in the original position relative to the real world.
10 |
T1 |
= |
30. |
10. 10. 40. |
|
20 |
T2 |
= |
15. |
5. 5. 10. |
|
30 |
T3 |
= |
0. |
0. 0. |
0. |
40 |
MOVE |
T1 |
‘ move to a start point |
||
50 |
SHAVE ‘ |
allow |
motions to “only get close” before moving to the next point |
||
60 |
MOVE |
T2: |
MOVE |
T3 ’ slows down at t2 before going to t3 |
|
70 |
NOSHAVE |
‘ make motion stop fully before going to the next point |
|||
80 |
MOVE |
T1 |
‘ return to the start |
||
90 |
MOVE |
T2: |
MOVE |
T3’ stops at t2 before going to t3 |
|
100 MOVE T1 |
‘ return to the start |
110 MOVES T2: MOVES T3 ’ moves in a straight line from t1 to t2 and from t2 to t3 120 MOVE T1 ‘ back to the start again
130 MOVEC T2 T3 ‘ follows a smooth path, not slowing down at t2 140 MOVE T1 ‘ back to the start again
150 SYNC ‘ make gripper stay stationary relative to ground 160 MOVEC T2 T3 ‘ the arm moves, but the gripper stays at 0 170 NOSYNC ‘ make gripper follow robot
page 303
• A example that defines tool location offsets is shown below. This is particularly useful for a robot that has more than one tool attached. The normal tool location is on the end of the arm. With multiple tools attached we will have multiple tool center points. We can have a tool definition for each one of these. Note that the x-axis is the normal forward for the tool. The tool axis can only be changed in the x-y plane (or the plane perpendicular to the gripper rotation).
30 |
|
A = |
0.1 |
’ the tool center |
point x offset |
from the gripper |
|
40 |
|
B = |
0.2 |
’ the tool center |
point y offset |
from the gripper |
|
50 |
|
C = |
0.3 |
’ the tool center |
point z offset |
from the gripper |
|
60 |
|
D = |
1 |
’ |
define an offset for an axis |
|
|
70 |
|
E = |
0 |
’ |
define a zero offset for an axis |
|
|
80 |
|
DEF |
TL2 |
D E A B C ’ tool 2 at (0.1, 0.2, |
0.3) with the x-axis pointing forward (1,0) |
||
90 |
DEF TL3 E D C B A ’ tool 3 |
at (0.3, 0.2, 0.1) with the x-axis pointing to the left (0,1) |
|||||
100 |
TOOL |
1 |
’ indicate that you are using tool 1 |
||||
110 |
MOVE |
T1 ’ move to position 1 with the tool pointing in the normal direction |
|||||
111 |
remark |
note that the robot gripper will |
be positioned (-0.1, -0.2, -0.3) from normal |
||||
120 |
TOOL |
2 |
’ choose the tool |
on the gripper |
pointing to the left |
||
130 |
MOVE |
T1 ’ this will move |
the robot to (-0.3, -0.2, -0.1) |
||||
140 |
remark |
the robot will also move so that |
the tool is pointing to the left. |
• A example that uses pallet commands is shown below. Basically a pallet allows us to create an array of points (it does the calculations). We can then give a location on a pallet and move to that point. The basic pallet definition requires that we indicate the number of rows and columns. We also need to define the physical locations of the rows and columns.We do this by giving an origin point, and then defining where the first row and column end. To use the pallet location we can simply refer to the pallet location index.
page 304
110 R = 3 ’ define the number of rows on the pallet 120 C = 4 ’ define the number of columns
130 DEF PA2 (R,C) T1 T2 T3 ’ pallet with first row from t1 to t2, the first column from t1 to t3
140 FOR I = 0 TO R-1 ’ loop for the rows 150 FOR J = 0 TO C-1 ’ loop for the columns 160 MOVE T4’ move the pickup point
170 OUTPUT +OG3 ’ close the gripper
180 MOVE PA2(J,I) ’ move to the location on the pallet 190 OUTPUT -OG3 ’ open the gripper
200 NEXT J: NEXT I ’ continue the loop to the next parts
• A example that defines and uses new frames is shown below. We define a new frame of reference by using points. The first point becomes the new origin. The second point determines where the new x-axis points. The z-axis remains vertical, and the y-axis is shifted appropriately.
20 T1 = 2. 1. 0. 0. ’ define a point 30 T2 = 1. 1. 0. 0.
40 T3 = 2. 2. 0. 0.
50 DEF FR1 T2 T1 ’ defines frame with origin at (1,1,0), but x-y axis in original direction
60 DEF FR3 T1 T2 ’ defines origin at T1 and x-axis pointing T2-T1=(-1,0,0)
70 DEF FR2 T2 T3 ’ defines origin at T2 and x-axis pointing T3-T2 = (.71,.71,0) 80 MOVE T2 ’ THIS WILL MOVE TO (1 1 0 0)
90 FRAME 1 ’ USE REFERENCE FRAME #1
100 MOVE T2 ’ THIS WILL MOVE TO FR1+T2 = (2, 2, 0, 0) 110 FRAME 2 ’ USE REFERENCE FRAME #2
120 MOVE T2 ’ THIS WILL MOVE TO FR2+T2 = ( 1, 0, 0, 0) 130 FRAME 3 ’ USE REFERENCE FRAME #3
140 MOVE T2 ’ THIS WILL MOVE TO FR3+T2 = (1.71, 1.71, 0, 0) 150 FRAME 0’ GO BACK TO THE MAIN COORDINATES
80 MOVE T2 ’ THIS WILL MOVE TO (1 1 0 0)
• A example that uses simple inputs and outputs is shown below. Note that there are two connectors for I/O. The main or ‘E’xternal connector is on the main controller box. The other I/O