
A_Compelling_Global_Resource
.pdf
McKinsey Sustainability & Resource Productivity |
|
Energy efficiency: A compelling global resource |
29 |
Exhibit 3
Variation in energy productivity
Variation in energy productivity among developing countries,1 2005, %
Type of contribution to variation in energy productivity,2 %
|
|
Fixed |
|
Climate |
|
13 |
|
|
|
|
|
|
|
|
|
||||
Unexplained 43 |
|
|
Industrial |
|
|
|
21 |
||
|
|
|
|
|
|
|
|||
|
|
|
|
structure |
|
|
|
||
57 Explained |
Flexible |
|
|
|
|
|
|
||
|
|
|
|
|
|
|
|||
|
|
|
Policies |
|
|
|
23 |
||
|
|
|
|
|
|
|
|
|
|
|
|
|
|
|
|
|
|
|
|
1Data covers 27 developing countries (defined as those with a 2007 average per capita income of less than $11,000, adjusted for purchasing-power parity).
2Climate is based on hot/cold days; industrial structure reflects the manufacturing and nonmanufacturing subsectors of the economy, combined with level of per capita income; policies include gas subsidies and gas taxes, as well as an index of corruption.
Source: Global Insight; International Energy Agency (IEA); national sources; McKinsey Global Institute analysis
Implementing and enforcing energy efficiency standards is a third area for action. Such standards boost production of more efficient appliances and equipment and reduce their cost. Indonesia has recently adopted the UN technical regulation on auto energy efficiency, for example, and Ghana has pioneered standards for household appliances in Africa.
A fourth priority is encouraging public–private partnerships, such as collaborations between governments, energy service companies, utilities, and mortgage companies, to finance higher energy efficiency in buildings. China, which manufactures 70 percent of the world’s lightbulbs, now has very large subsidies in place to promote the uptake of energy-efficient bulbs.
If developing countries and their businesses seize the initiative on energy productivity, they will cut their energy costs, insulate themselves from future energy shocks, and secure a more sustainable development path—benefits that are all the more desirable given the current global financial turmoil.

30
Capturing the lean energy-efficiency opportunity
in industrial and
manufacturing operations
By Nicole Roettmer, Erik Schaefer, and Ken Somers
Between 1990 and 2009, many industrial and manufacturing companies boosted corporate performance by adopting lean production methods to optimize material and labor productivity. Indeed, a multiyear study of how well thousands of manufacturing companies in North America, Europe, and Asia adopted management best practices (including lean), highlighted just how important these practices are to a company’s economic success (Exhibit 1). 1
Exhibit 1
An analysis of the development of energy productivity over time reveals substantial improvement potential
Current capabilities
•Optimizing lead and cycle times and preventing waste
•Managing organization using KPIs for quality and lead and cycle times
•Training and leading employees in shortening lead and cycle times and improving quality
Source: BMU 2007a, McKinsey
Factor input per unit of value added,
Historical productivity
improvements
350
300 |
|
|
|
250 |
|
|
|
200 |
|
|
|
150 |
|
|
|
100 |
|
|
|
indexed |
|
|
|
50 |
|
|
|
0 |
|
|
|
1960 |
1970 |
1980 |
1990 |
Labor productivity
Material productivity
Energy productivity
2000
New requirements to increase energy productivity
•Including energy efficiency in optimization levers
•Making energy consumption transparent
•Systematizing waste detection
•Developing methods to reduce waste
•Incorporating energy
key performance indicators (KPIs) in management/ governance systems
•Building capabilities for continual energy-efficiency improvement
1The study, conducted from 2005 to 2008 by McKinsey and the London School of Economics, looked closely at how well manufacturing companies adopted proven best practices, such as lean, and at the relationship between these efforts and financial results. An early view on the research, published in February 2006, is available
at mckinseyquarterly.com: Stephen J. Dorgan, John J. Dowdy, and Thomas M. Rippin, “The link between management and productivity.”
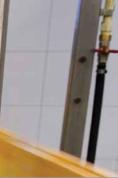
McKinsey Sustainability & Resource Productivity |
|
Energy efficiency: A compelling global resource |
31 |
But most companies that have adopted lean techniques have not incorporated, or only partly adopted, new tools for increasing energy efficiency. Until now, most companies did not pay much attention to cutting energy costs for three main reasons. First, the cost of oil, though rising since 2002, has been relatively inexpensive for years. Second, through 2008, companies focused the majority of their improvement efforts on growth and increasing capacity. And third, companies struggled to track their energy efficiency, which is often highly dependent upon production rates and product mix, in a meaningful way. As a consequence, for many years companies typically found it easier to focus their lean continuous improvement projects on cutting costs or increasing output, which yielded higher returns per project, than on efforts to increase energy efficiency.
With the rise in oil prices in 2007 and 2008, however, companies realized that reducing waste in energy use could have a significant impact on the bottom line. Currently the price of oil is still twice or more what it was during much of the 1990s, and though it has fallen from its highs of 2008, most analysts expect it to rise again as the global economy rebounds. Energy costs for European chemical companies on average rose from 4.8 percent of total costs in 2002 to 11.6 percent in 2006. Because of the run-up in energy costs, the return on efforts to optimize energy usage at many companies was generally three times greater in 2006 than in the 1990s, when oil traded for $25 per barrel on average (corrected for inflation).
In both our research and our experience working with a number of manufacturing companies across several sectors, we have found that most companies can reduce the overall energy efficiency of their operations by 10 percent or better with relatively small investments and by up to 35 percent when making substantially larger ones. Savings vary by sector, of course. Typical savings among integrated steel players in Europe or the United States can be 10 to 15 percent or more, and among chemical companies 10 to 20 percent. What’s more, all of these savings can be
achieved with limited investment and simple payback periods of less than two years. One European company, for instance, estimates that it can shave 6 percent off its energy costs without any capex investments and an additional 5 percent with capex expenses of less than $20 million.
This is not to say that companies have ignored energy inefficiencies. Most of them have taken a variety of steps to lower their energy intensity (the amount of energy consumed per unit produced)—from launching “green” awareness programs among employees to substituting variable for fixed drives in electric motors to reduce the energy consumed. Traditional lean programs also typically identify savings
gained by improving every aspect of a manufacturing step, frequently including energy savings. But in our experience, traditional lean programs enable companies to realize only about one-sixth of their potential energy savings—leaving the rest on the table. Why? Few companies are making systematic efforts to holistically map out energy consumption at each step in their operating processes or to identify specific energy waste in their production systems and then to focus on opportunities to reduce it. They have not been setting concrete goals for improvement—the way they have in other areas where they have applied lean tools and thinking. As a result, few are realizing anything near their energy-savings potential.
Companies can realize greater gains by incorporating energy-efficiency analyses and techniques into their existing lean approaches in three ways. First, they can focus specifically on energy consumption (rather than on energy as an input to a process), and systematically identify waste as they would in any other lean program. Teams focused on improving energy efficiency, for instance, might use such lean approaches as value-added identification to determine the energy required to make the product and the amount of energy wasted, which can be more than 40 percent in process industries (Exhibit 2).
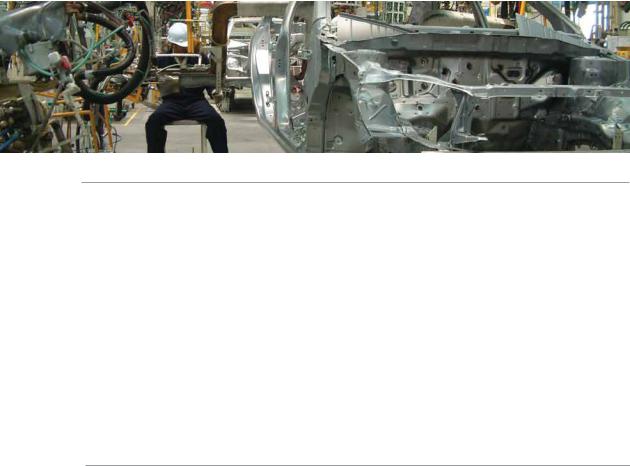
32
Exhibit 2
Energy efficiency is included in the lean methodology—the “8 kinds of waste” for energy
8 kinds of waste |
Definition |
Example |
|
|
|
|
|
1 |
Overproduction |
Producing excess energy (input energy that is unused) |
Venting excess steam |
|
|
|
|
2 |
Waiting |
Consuming energy while production is stopped |
Laser welding line on standby still consume |
|
|
|
40% of maximum energy |
|
|
|
|
3 |
Transportation |
Inefficient transportation of energy |
Leaks and heat radiation in steam network |
|
|
|
|
4 |
Overspecification |
Process energy consumption (deliberately) higher |
Blast furnace operating at 1,100° C |
|
|
than necessary |
instead of the required 1,000° C |
|
|
|
|
5 |
Inventory |
Stored goods use/lose energy |
Crude steel cools in storage, is then |
|
|
|
reheated for rolling |
|
|
|
|
6 |
Rework/scrap |
Insufficient reintegration in upstream process when |
Re-drying polymer lines that did not get |
|
|
quality is inadequate |
coagulated in drying process |
|
|
|
|
7 |
Motion (inefficient processes) |
Energy-inefficient processes |
Excess oxygen in steam boiler |
8 Employee potential/intellect |
Failure to use people’s potential to identify and |
|
prevent energy waste |
Employees not involved in developing energy saving initiatives
A European automaker, for example, over the years made many improvements in its paint-shop operations through lean processes. More recently, it focused specifically on reducing energy usage in the paint shop. In one process, a fixed amount of wax is stored and heated to 135 degrees centigrade for use in sealing auto body cavities before painting. The shop stored about 20 tons of wax on site, and heating the wax consumed about 1,400 kilowatts of electricity. Intent upon reducing energy, the automaker redesigned the process to keep only 8 tons of wax in inventory, lessening to 200 kilowatts the amount of energy needed for heating it. This represented an 85 percent reduction in energy use and annual savings of €260,000.
A second way companies can extend their lean programs to improve energy efficiency is by optimizing energy integration in heating and cooling operations. A chemical company changed its process to release heat more quickly during polymerization, allowing evaporation to start sooner and saving energy in the subsequent drying stage. The total savings for both steps amounted to ten percent and brought the production line close to the industry cost benchmark.
A third way companies can achieve greater gains is by adopting more energy-efficient technologies. A South American steel player, for instance, developed a boiler optimization model that allowed it to reduce the energy losses within its boilers to 3 percent below those of its competitors.
To ensure that the gains are sustainable, companies need to put into place a performance management system for energy efficiency that will provide an objective basis for discussion. One company, for instance, annually spent about $300 million on energy, but the chief operating officer’s team had not discussed key performance indicators (KPIs) for energy in two years because it had little sense of how KPIs would change in response to actual operating decisions. A performance management system for energy must correct for such factors as price fluctuations, product mix, and throughput that play a part in classical energy consumption.

McKinsey Sustainability & Resource Productivity |
|
Energy efficiency: A compelling global resource |
33 |
To capture these improvements companies will need to:
Lead visibly from the top. Companies must signal the importance of energy cost reduction to employees and communicate the opportunity to reduce energy costs in the existing language of lean. For instance, they should emphasize the importance of low-or-no-capex ideas generated through structured frontline engagement, cross-functional problem solving, and changes in mind-sets and behaviors.
Show teams how to win. Many of the leading players in energy efficiency have invested in developing coaches trained in the discovery of energy waste, which is often invisible and tends to be spread across an entire plant. Identifying that waste requires specific technical knowledge, such as steam production network economics or pinch analysis. A Chinese company, for instance, using the wrong valuation for its steam, decided to increase steam production to generate electricity—and destroyed $3 million in value. In addition to technical knowledge, coaches must possess the ability to tap into frontline knowledge in order to identify solutions and mobilize personnel to capture savings in a manner similar to typical lean programs.
Apply an opportunity-based mind-set to identifying energy opportunities. In our experience, the most successful companies have forced their managers to move from a benchmarking mind-set to one focused instead on opportunities and closing gaps to technical limits for energy savings. This stretches the organization’s aspirations on the energy savings that can be achieved with the existing asset configuration and product requirements. Given the extreme product mixand site-specificity of energy production, transport, and consumption, a benchmarking discussion will quickly devolve into an analysis of variance that leads only to incremental changes. Focusing instead on theoretically achievable energy efficiencies and on the identification of specific types of losses between actual and theoretical positions enables a far more fruitful discussion on potential improvement levers. Such a conversation will generate
strong insights in the type and size of losses, and forms a clearly quantified basis for a relentless focus on loss reduction.
Set up the right metrics. Frequently, the challenge for low-cost improvement starts with insufficient energy-consumption metering and energy-generation cost allocation. Improving these enables companies to identify operating changes that lower energy usage, such as reducing standby times. Better information about consumption and cost allocation also helps in developing meaningful KPIs. With a combination of energy-efficiency planning and employee training, low-cost, sustainable savings can be achieved. Relevant metrics would then include a clear correction for product mix, quality losses, and throughput variation.
Energyefficiencyintheautosector
Eveninrelativelylow-energy-consumingindustriessuchasautomotivemanufacturing,energy usageperproductishighenoughtobeworthaddressing.Forexample,energycostsforthe productionoftheaverageGermancarcurrentlystandatonlyabout€70.Evenonthesmall consumptionbaseinthissector,energy-efficiencyimprovementscanamountto5percentperyear withminorinvestment.
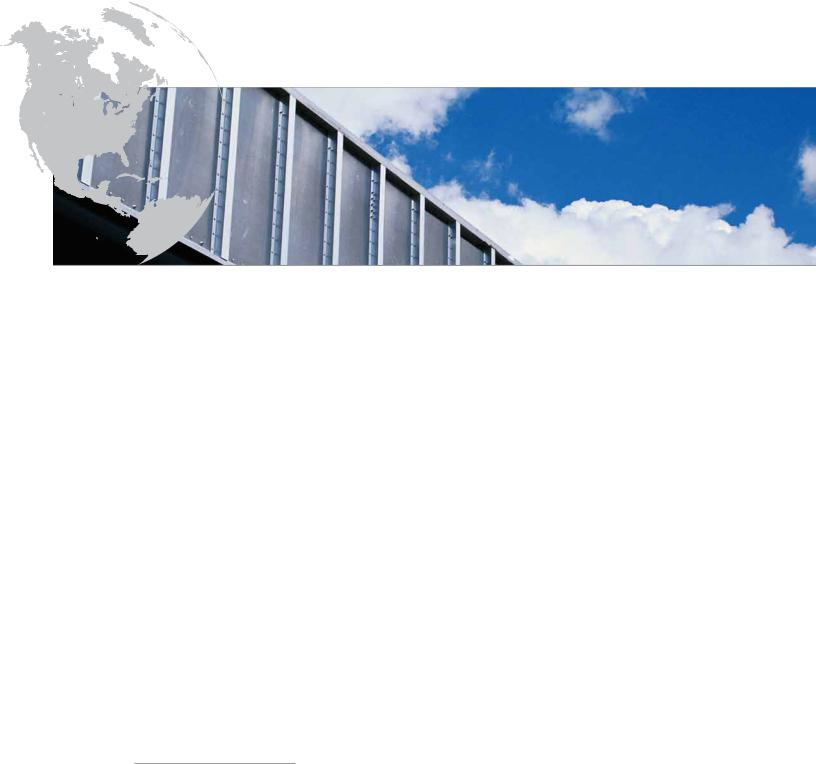
34
Making
supply chains
energy efficient
By Heiko Bette, Tobias Meyer, and Martin Stuchtey
Cheap oil helped to underwrite an ever-expanding globalization of production systems and procurement in many sectors over the last 30 years. Whole industries benefited by taking advantage of low regional factor costs and specialization—made possible by the low cost of fueling the movement of goods by land, sea, and air.
Circumstances have changed. The price of oil has risen steadily since 2002, hitting historic highs in 2007 and 2008. The price of crude oil at its peak—$146 per barrel in July 2008—was 13 times higher than at its trough, $11 per barrel in November 2001. In early 2009—in the midst of a global recession—oil was trading at around $50 per barrel, still about double the average price of $25 per barrel observed over the period of 1990–2005. As expected, the price of oil did rise again when the economy showed signs of a rebound and demand for energy was once again expected to grow.1 Some analysts see signs that the foundation for the next spike has already been laid.2 Many shippers expect that oil will trade in a range of $60 to $100 for at least the next ten years.
Today, transportation of goods consumes some 15 million barrels of oil each day, close to a fifth of total world production (Exhibit 1). For the trucks, cargo planes, and ships that account for most of this consumption in global trade, there are few, and in some cases no, alternative fuels available. At $50 per barrel of oil, the spend on fuel to keep modern supply chains humming is $750 million per day. The opportunities to reduce energy usage and related carbon emissions throughout a global industrial supply chain—from shippers to freight carriers—are significant. Our research shows that sectors as varied as high tech, fashion, and automotive can save as much as half the energy that globally dispersed supply chains consume without adding net cost.
Energy-saving activities include shifting production steps closer to end-user markets, reducing packing volume, switching to less energy-intensive3 modes of transporting select goods, managing ship speed at sea, and adopting traffic guidance systems on land.
1For more information, see the McKinsey Global Institute report, “Averting the next energy crisis: The demand challenge,” March 2009, available on mckinsey.com/mgi.
2See, for instance, Steve Gelsi, “Energy-spending cutbacks spark price-spike talk,” MarketWatch, April 8, 2009.
3Defined as the amount of oil consumed by the respective transportation asset per ton-kilometer of goods transported. A ton-kilometer is a generally recognized measure of road freight production, which takes into account both the weight of the shipment and the distance shipped per hour worked. Metric ton: 2,205 pounds.

McKinsey Sustainability & Resource Productivity
Energy efficiency: A compelling global resource |
35 |
Exhibit 1
Freight transportation drives a significant and growing share of world oil demand
Millions of barrels of oil per day1
|
|
Consumption split |
|
|
|
Passenger |
|
|
100% = 44.4 mio bbl daily2 |
|
|
|
Freight |
|
|
|
|
|
|
|
|
85.7 |
= 257.8 PJ daily3 |
|
2.3 |
0.8 |
|
|
|
|
||||
|
|
26.5 |
7.9 |
2.7 |
3.4 |
0.7 |
Transportation |
44.7 |
|
|
|
|
|
|
|
Passenger transport |
|
|
|
Supply chains: |
Industrial |
20.0 |
accounts for 66% of |
|
|
|
|
oil consumption, |
|
|
|
Freight transport |
||
Power |
10.5 |
mainly cars |
|
|
|
accounts for 34% of |
|
|
|
|
oil consumption |
||
Other |
10.5 |
|
|
|
|
|
|
|
|
|
|
||
Oil demand, |
|
|
|
|
|
|
2006 |
Private cars |
Trucks |
|
|
Inland waterways |
|
|
|
|
and buses |
|
||
|
|
|
|
Rail4 |
||
|
|
|
Aviation—international |
|
||
|
|
|
Maritime |
|||
|
|
|
Aviation—national |
1 1 barrel (bbl) = 159 liter.
2Excluding 0.3 mio bbl daily for pipeline transport and nonenergy use of oil (eg, lubricants).
3Based on specific Joule/liter for each fuel type; 1 PJ = 1 Peta Joule = 1015 Joule.
4Does not include electric rail.
Source: US International Energy Agency; McKinsey analysis
Achieving these savings will be challenging, however. It will require a concerted effort by all stakeholders involved in a supply chain, substantial investments in upgrading infrastructure and transportation assets, and major shifts in consumer mindsets and behavior. But it can be done. It starts with a clear understanding of the economics of the opportunity to unlock substantial value by improving energy productivity in supply chains.
The prize: Reducing energy intensity
In our study of energy usage in global supply chains, we analyzed six broad levers across the flow of goods to reduce energy intensity. We studied a variety of commodities, supply chains, and transportation assets across several sectors to see how each of the levers applies. Generally, shippers—by which we mean the manufacturers, wholesalers, and retailers that represent the lion’s share of transport demand—can influence three of these levers. They are:
Increasing the value density of shipped products (the value of the product relative to its physical or volumetric weight). This can, for instance, be achieved by reducing product weight, size, or packaging.
Reducing the average distance that products travel from source to end user.
Changing the mix of transport modes employed to move products—for example, shipping by sea rather than by air.

36
Companies in transportation businesses—including carriers, third-party logistics providers, equipment manufacturers, and infrastructure companies—chiefly influence three other levers affecting the energy efficiency of transport assets. Governments and transport regulators also can have an impact on these levers, as decisions they make about various kinds of transport infrastructure influence how effective transportation assets will be. The levers are:
Improving the energy efficiency of transportation assets (including ships, aircraft, and trucks) through advances in technology and improvements in design.
Achieving more efficient use of transportation capacity by individual players in a supply chain— for example, by increasing load factors and reducing average shipping speed.
Improving the collective use of transportation assets and infrastructure, for example by implementing smart traffic management systems to help trucks avoid traffic jams and unnecessary detours.
We calculated the impact of these levers on reducing energy consumption within the context of three different oil-price scenarios: $40, $100, and $250 per barrel. The conclusions were astounding. Without adding net cost, players can lower energy intensity by 38 percent in the $100-per-barrel price scenario, and by 51 percent in the $250-per-barrel scenario. This reduction assumes a transition period until 2020, which would be required to make the necessary investments and replace old assets with more energy-efficient equipment. Based on 2008 volumes, this could reduce global oil consumption by as much as eight million barrels a day—nearly 10 percent of total global oil demand. Remarkably, even with the oil price as low as $40 per barrel, nearly half of this global potential, four million barrels a day, can be realized cost effectively for consumers and companies (Exhibit 2).
These conclusions come from a comprehensive analysis of each of the six levers and a careful review of the full potential across the levers to avoid inconsistencies and double counting. To develop the analyses, we reviewed shipment data of transportation companies, comparing specified gross and net weight of products; studied options for redesigning product packaging to lower weight and volume while maintaining the functionality; modeled scenarios for optimizing both production and sourcing locations as well as the mix of transportation modes under realistic assumptions (such as taking into account lead-time restrictions, inventory cost, customs duties, and so on); and drew on analysis of the energy-efficiency potential of different technologies, and of traffic management systems and other technologies to reduce congestion and allow for more efficient vehicle and aircraft routing.4
4A more detailed presentation of our research findings is available in interactive form on mckinseyquarterly.com/ghost.aspx?ID=/Increasing_the_energy_efficiency_of_supply_chains_2414.
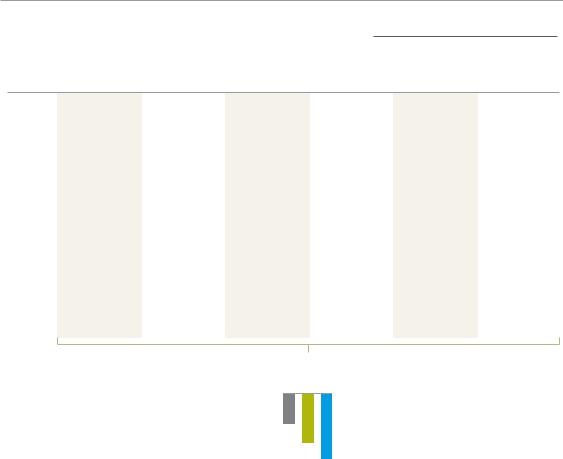
McKinsey Sustainability & Resource Productivity
Energy efficiency: A compelling global resource |
37 |
Exhibit 2
Energy-efficient supply chains—impact of levers
Scenarios
Reduction of energy intensity, % |
|
A ($40/bbl) |
|
B ($100/bbl) |
|
C ($250/bbl) |
|
|
|
Reduction in energy intensity assuming rationale and informed behavior of shippers, providers, investors, consumers, and government, 10-year horizon
|
1 Value density1 |
2 Average |
3 Modal mix1 |
4 Asset |
5 Individual |
6 Collective |
|||||||||||||||||||||||||||||||||||||
|
|
|
|
|
|
|
|
|
|
distance1 |
|
|
|
|
|
|
|
|
technology |
|
usage |
|
usage2 |
||||||||||||||||||||
Impact per |
|
|
–2 –3 –3 |
|
–1 –4 –15 |
|
–3 –4 –7 |
–10 –20 –22 |
|
–7 –12 –17 |
|
–1 –2 –3 |
|||||||||||||||||||||||||||||||
lever per |
|
|
|
|
|
|
|
|
|
|
|
|
|
|
|
|
|
|
|
|
|
|
|
|
|
|
|
|
|
|
|
|
|
|
|
|
|
|
|
|
|
|
|
|
|
|
|
|
|
|
|
|
|
|
|
|
|
|
|
|
|
|
|
|
|
|
|
|
|
|
|
|
|
|
|
|
|
|
|
|
|
|
|
|
|
|
|
|
|
|
|
|
|
|
|
|
|
|
|
|
|
|
|
|
|
|
|
|
|
|
|
|
|
|
|
|
|
|
|
|
|
|
|
|
|
|
|
|
|
|
|
scenario vs |
|
|
|
|
|
|
|
|
|
|
|
|
|
|
|
|
|
|
|
|
|
|
|
|
|
|
|
|
|
|
|
|
|
|
|
|
|
|
|
|
|
|
|
2007 base |
|
|
|
|
|
|
|
|
|
|
|
|
|
|
|
|
|
|
|
|
|
|
|
|
|
|
|
|
|
|
|
|
|
|
|
|
|
|
|
|
|
|
|
|
|
|
|
|
|
|
|
|
|
|
|
|
|
|
|
|
|
|
|
|
|
|
|
|
|
|
|
|
|
|
|
|
|
|
|
|
|
|
|
|
|
|
|
Lever |
•Reduce packing |
•Shift of production |
•Shift from air to |
•Significant |
•Reduction of |
•Traffic guidance |
|||||||||||||||||||||||||||||||||||||
description/ |
volume |
process steps |
ocean for lower |
windfall efficiency |
vessel speed esp. |
systems to avoid |
|||||||||||||||||||||||||||||||||||||
example |
•High potential |
closer to market, |
value parts, eg, |
gain (scale, |
for container |
jams, braking |
|||||||||||||||||||||||||||||||||||||
|
lever for modes |
eg, local |
power cables |
propulsion) even |
•Load factor |
•Reduction of |
|||||||||||||||||||||||||||||||||||||
|
that are ‘cubed |
packaging |
•Investment in |
at lower oil prices |
optimization |
turnaround times |
|||||||||||||||||||||||||||||||||||||
|
out,’ eg, trucks |
•In scenario C, shift |
rail to allow shift |
|
|
|
|
|
|
|
(all modes) |
(use of saved time |
|||||||||||||||||||||||||||||||
|
•Large lever for |
of raw material |
from road |
|
|
|
|
|
|
|
|
|
|
|
|
|
|
for reduction of |
|||||||||||||||||||||||||
|
FMCG and |
processing to |
|
|
|
|
|
|
|
|
|
|
|
|
|
|
|
|
|
|
|
|
|
speed) |
|||||||||||||||||||
|
electronics |
source, eg, steel |
|
|
|
|
|
|
|
|
|
|
|
|
|
|
|
|
|
|
|
|
|
|
|
|
|
|
|
|
|||||||||||||
|
companies |
making |
|
|
|
|
|
|
|
|
|
|
|
|
|
|
|
|
|
|
|
|
|
|
|
|
|
|
|
|
•Low relevance for bulk commodities
Total impact by scenario
–23 –38 –51 |
1 Based on fuel consumption after pulling levers 4, 5, and 6. 2Small impact, as mainly enabler for scale.
Let’s look in more detail at the opportunities for reducing energy intensity through each of these levers.
Actions for shippers
The levers shippers can influence could trigger an 11 percent reduction in energy consumption at zero net cost in a $100-per-barrel oil-price scenario. More than half of this potential would be economically viable even at an oil price of $40.
What, then, are the practical actions that shippers can take?
Increasing the value density of shipped products
Value density is a measure of a product’s economic value against its weight or volume. Increasing the value density reduces the amount of volume transported, depending on the product category. One action shippers can take, for instance, is redesigning product packaging. We estimate that
38
30 percent of the truck space used to transport finished goods is taken up by packaging material or empty space. One computer manufacturer recently eliminated nearly all throw-away primary packaging for its notebook PCs by developing a compact, stylish messenger bag, which now carries the notebook from factory to retail shelf and is part of the product acquired by the customer. This reduced consumer-facing packaging by 97 percent, and the optimization of the laptop packaging led to a quarter fewer trucks being required to deliver the laptops.
Shippers can also change the shape of a product to reduce value density. For example, a retailer and a wholesaler partnered to redesign milk containers to make them stackable, thus eliminating the need for shipping crates. They achieved substantial fuel savings.
Consumer goods companies can remove the filler material traditionally used to make products look bigger. One such company removed water from its detergents, reducing product sizes by a factor of two and cutting transport costs in half. Because mere size is one of the ways customers tend to judge the value of a product, this measure was supported by a marketing campaign emphasizing that the new smaller product was more powerful and could therefore deliver the same performance despite its smaller size.
Increasing value density can mean big savings for some companies. For consumer durables, for example, reductions in transport volume of 20 to 30 percent are typical. For other companies, however, the savings will be smaller or negligible. With bulk commodities, such as crude oil and grain, there are few opportunities to increase product value density. Looked at in total across sectors, however, the optimization of product value density and packaging could reduce energy use in distribution by 2 to 3 percent, without affecting product functionality.
Reducing the average distance that products travel
In many global supply chains today, there are ample opportunities to redesign geographical production and sourcing footprints so that products need not be shipped as far—thus making the chains less energy intensive. One way to squeeze transportation costs out of a final product is to move the production of noncore components—for example, primary packing, handbooks, and power cables in the case of electronic goods—to the region where the items will be sold. Local sourcing of such components reduces the total ton-kilometers required—and at oil prices above $100 per barrel, the higher costs of transport begin to outweigh the additional cost of near-shore production for many goods.
A holistic review of supply chains will reveal such breakpoints and will allow companies to optimize the design of their production process, location footprint, transportation, and inventory (Exhibit 3).
Changing the mix of transport modes
By changing the modal mix, shippers could potentially reduce the energy intensity of supply chains by some 5 percent. Moving goods by air or by truck is more energy intensive than doing so by ship or rail, and so a shift from the former to the latter modes can have a major impact on oil
consumption. In fact, container-based ocean freight has grown much faster than air freight over the past two decades, with the result that the energy intensity of transporting goods has already been reduced significantly (Exhibit 4).