
Техпроцессы в машиностроении_лек
.pdf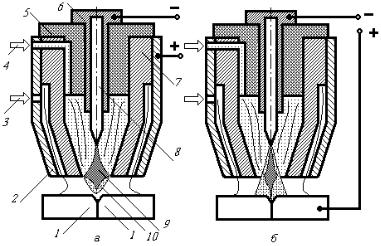
Плазменная сварка
Плазменная сварка - сварка плавлением, при которой нагрев произво-
дится сжатой дугой. Источником теплоты при плазменной сварке является
плазменная струя – направленный поток ионизированных частиц газа, с тем-
пературой до 20 000оС. Сжатая дуга - это столб дуги, помещенный в узкий канал, который ограничивает его расширение. Устройства для получения сжатой дуги называют плазматронами.
Плазму получают, пропуская поток плазмообразующего газа через столб сжатой электрической дуги 9 (рис. 6.15). Столб электрической дуги 9,
Рис. 6.15. Схемы плазма-
тронов:
а - косвенного действия; б –
прямого действия: 1 – сва-
риваемые заготовки; 2 – за-
щитное сопло; 3 – подача
защитного газа; 4 – подача плазмообразующего газа; 5 -изолятор; 6 – элек-
трододержатель; 7 – плазмообразующее сопло; 8 - электрод; 9 - электриче-
ская дуга; 10 - плазменная дуга.
горящий между электродом 8 и плазмообразующим соплом 7, помещают в узкий канал с охлаждаемыми стенками, и через него продувают плазмообра-
зующий газ. В качестве плазмообразующего газа обычно используют аргон.
Для получения более мощной дуги используют водород или азот.
Столб дуги сжимается, что приводит к повышению в нем плотности энергии и температуры. Частые столкновения частиц газа приводят к их высокой ио-
низации. Загорается плазменная дуга 10. Нагретый в дуге газ, сталкиваясь с
494
поверхностями свариваемых заготовок 1, нагревает и оплавляет их. Под дав-
лением газа расплавленный металл заготовок раздвигается, энергия дуги пе-
редается непосредственно твердому металлу дна сварочной ванны.
Меняя расход газа и диаметр канала сопла, можно изменять давление струи плазмы, а также плотность теплового потока, передаваемого от дуги к заготовкам. Это основное технологическое преимущество сжатой дуги, по-
зволяющее регулировать размеры и форму сварочной ванны. В сжатой дуге достигается высокая плотность теплового потока, особенно при малой мощ-
ности дуги. Это позволяет получать узкие швы с малой шириной зоны тер-
мического влияния и увеличивать скорость сварки. Так как плазмообразую-
щий газ передает детали значительную долю общей полезной мощности, а
нагрев газа сильно зависит от всех параметров режима, то эффективный КПД сжатой дуги можно изменять в пределах 30…80%. Другим преимуществом сжатой дуги является повышение ее пространственной устойчивости.
Уменьшается блуждание активного пятна по поверхности детали из-за ста-
билизирующего действия плазмообразующего газа. Это улучшает формиро-
вание шва.
Различают плазмотроны косвенного (рис. 6.15, а) и прямого (рис. 6.15,
б) действия. В плазматронах косвенного действия дуга горит между электро-
дом и соплом. Эти плазмотроны применяют при обработке неэлектропровод-
ных материалов и при пайке. Для сварки и резки чаще применяют плазмо-
троны прямого действия. В них дуга горит между электродом и свариваемы-
ми заготовками. В этих плазматронах сжатую дугу зажигают в две стадии.
После подачи в плазматрон газа зажигают вспомогательную (дежурную) дугу между электродом и соплом плазматрона искровым разрядом от осциллятора или, замыкая промежуток электрод - сопло графитовым стержнем. Дежур-
ную дугу питают от отдельного маломощного источника или от основного источника через ограничивающее сопротивление, чтобы ограничить ее ток и уменьшить износ сопла. Под действием газа дежурная дуга образует струю
495
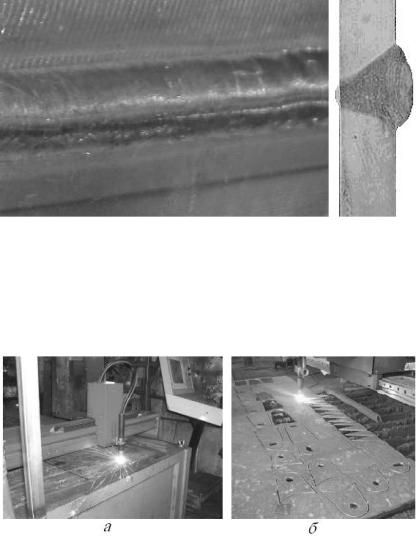
плазмы небольшой мощности. При ее соприкосновении с деталью зажигается рабочая дуга.
При плазменной сварке применяют сварочный ток силой 3...400 А, на-
пряжение дуги 25...35 В, средняя скорость сварки составляет 15...50 м/ч.
Сжатой дугой сваривают детали толщиной 0,01...16 мм, отношение глубины проплавления к ширине шва составляет от 1:3 до 3:1 при толщине сваривае-
мых кромок 3...12 мм.
Плазменную дугу используют для сварки металлов (высоколегирован-
ной стали, сплавов титана (рис. 6.16), никеля, молибдена, вольфрама) и неме-
таллов; резки всех материалов; пайки; наплавки; напыления.
Рис. 6.16. Сварной шов титановой пластины.
Плазменная резка производится высоко-
скоростной плазменной дугой. В отличие от плазменных сварочных головок, плазменный резак снабжен дополнительными каналами для подачи в зону резания защитного газа. Резка производится при величине тока 55…150А и напряжении
110…120 В. В современных установках для плазменной резки (рис. 6.17),
Рис. 6.17. Рабочая зона малогабаритной (а) и
портальной (б) устано-
вок для плазменной резки.
оснащенных числовым программным управлением, можно разрезать практи-
чески любые конструкционные материалы. В частности, можно разрезать
496
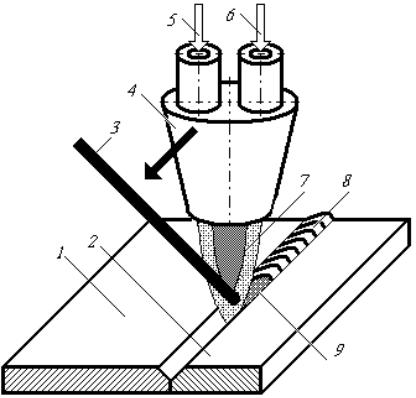
низколегированные стали толщиной до 20 мм с точностью до 0,25 мм и ско-
ростью реза до 1,12 м/мин.
6.3. ХИМИЧЕСКИЕ СПОСОБЫ СВАРКИ
Химические способы включают в себя термитную и газовую сварку.
Газовая сварка
Газовая сварка - сварка плавлением, при которой для нагрева исполь-
зуется тепло пламени смеси горючих газов с кислородом, сжигаемых с по-
мощью горелки.
Схема газовой сварки (ГС) показана на рис. 6.18. Кромки заготовок 1и 2 подвергаются местному нагреву до оплавления сосредоточенным пламенем
6.
Рис. 6.18. Схема газовой сварки:
1, 2 – свариваемые заго-
товки; 3 – присадочный пруток; 4 – газовая го-
релка; 5 – подача ки-
слорода; 6 – подача го-
рючего газа; газовое 7 –
пламя; 8 – сварной шов;
9 - ванна жидкого ме-
талла; стрелкой указано перемещение горелки.
Образовавшаяся ванна жидкого металла 9 контактирует с кромками обоих листов. При перемещении горелки 4 в направлении стрелки под пла-
менем металл будет расплавляться, а позади, в связи с охлаждением, – за-
твердевать, образуя, сварной шов 8. Для увеличения рабочего сечения шва и повышения прочности сварного соединения, кромки под сварку делают со
497
скосом (разделка кромок). Полученный объем заполняют дополнительным расплавленным металлом, используя присадочный пруток 3.
ГС не требует сложного и дорогого оборудования, а также источника электроэнергии. Изменяя тепловую мощность пламени, его положение отно-
сительно места сварки и скорость сварки, можно в широких пределах регу-
лировать скорость нагрева и охлаждения свариваемого металла. При помощи ГС можно сваривать почти все металлы, применяемые в технике. Такие ме-
таллы, как чугун, медь, латунь, свинец легче поддаются газовой сварке, чем дуговой.
В ГС используются горючие газы: ацетилен, водород, метан, пропан и пары керосина. Основным горючим газом является ацетилен. Ацетилен -
бесцветный газ, с резким запахом, ядовит, взрывоопасен. Ацетилен получают из природного газа термоокислительным пиролизом метана с кислородом
(используется для снаряжения ацетиленовых баллонов) или в специальных ацетиленовых генераторах при взаимодействии карбида кальция с водой:
CaC2+2H2O=C2H2+Ca(OH)+ Q. Наиболее безопасно использовать ацетилен,
поставляемый в баллонах. Ацетилен поставляется в баллонах белого цвета с красной надписью «ацетилен». Ацетиленовые баллоны, для уменьшения взрывоопасности, заполнены пористым наполнителем (гранулированный ак-
тивированный уголь размером зерна 1…3,5 мм) и ацетоном. При давлении
1,5 МПа в одном литре ацетона растворяется до 368 л ацетилена. Макси-
мальное давление в ацетиленовых баллонах – 1.9 МПа.
Кислород поставляется в баллонах голубого цвета с черной надписью
«кислород». При давлении 15 МПа, в баллоне помещается 600 л газообразно-
го кислорода. Так как масла и жиры в атмосфере сжатого кислорода способ-
ны самовоспламеняться, то вся кислородная аппаратура не должна контакти-
ровать с этими веществами. В противном случае возможен взрыв с воронкой глубиной до 5 метров.
Для уменьшения сетевого или баллонного давления газа и обеспечения постоянного рабочего давления в газовых магистралях применяются газовые
498
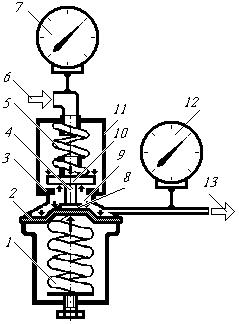
редукторы. Одноступенчатый (однокамерный) газовый редуктор показан на рис. 6.19. Запорный клапан 10 редуктора находится под давлением двух сил:
давления запорной пружины 5 и давления гибкой мембраны 2. При нормаль-
ном рабочем давлении редуцированного газа в камере низкого давления 9 ус-
танавливается равновесие, запорный клапан прижимается к седлу 3 запорной пружины и преграждает доступ газа из камеры высокого давления (из балло-
на). Гибкая мембрана, за счет регулировочной пружины 1,через нажимной диск 8 и толкач 4 воздействует на запорный клапан и стремится открыть его.
Изменяя натяжение регулировочной пружины можно менять рабочее давле-
ние. Корпуса редукторов для различных газов окрашиваются в тот же цвет,
что и газовые баллоны.
Рис. 6.19. Схема однокамерного газового ре-
дуктора:
1 – регулировочная пружина; 2 - гибкая мем-
брана; 3 - седло запорной пружины; 4 – тол-
кач; 5 - запорная пружина; 6 – магистраль вы-
сокого давления; 7 – манометр высокого дав-
ления; 8 - нажимной диск; 9 - камера низкого давления; 10 - запорный клапан; 11 - корпус;
12 – манометр низкого давления; 13 – магист-
раль низкого давления.
Горелка для газовой сварки – устройство для газовой сварки с регулируемым смешением газов и созданием направ-
ленного газового пламени. Для сварки чаще всего используются газосвароч-
ные горелки инжекторного типа (рис. 6.20, а), так как они наиболее безопас-
ны.
Под давлением 0,1…0,4 МПа, кислород поступает в горелку, через вен-
тиль 4 и подается в кольцевой инжектор 8. Выходя с большой скоростью из узкого канала инжектора, кислород подсасывает горючий газ, поступающий
499

через вентиль 7. В смесительной камере 3 получаем горючую смесь, которая,
через мундштук 2, подается к сменному наконечнику 1.
Рис. 6.20. Сварочные го-
релки:
а – инжекторная; б – без-
инжекторная; 1 - смен-
ный наконечник; 2 -
мундштук; 3 - смеситель-
ная камера; 4 - кислород-
ный вентиль; 5 – кисло-
родная магистраль; 6 –
ацетиленовая магистраль; 7 - вентиль горючего газа; 8 - кольцевой инжектор.
При работе газовой горелки возможен так называемый обратный удар
(проникновение пламени и взрывной волны в шланги и далее в источник го-
рючего газа), что приведет к взрыву газа. Для предотвращения попадания пламени в источник газа используются предохранительные затворы. Разли-
чают предохранительные затворы сухие и жидкостные (водяные затворы).
Наибольшее распространение получили водяные затворы. Для генераторов низкого давления применяют затворы открытого типа. В них взрывная волна и пламя, движущиеся навстречу горючему газу, выводятся в атмосферу. Наи-
более безопасны затворы закрытого типа. В них взрывная волна и пламя га-
сятся внутри затвора.
Все горючие газы, содержащие углеводороды, при сгорании образуют сварочное пламя, имеющее три отчетливо видимые зоны (рис. 6.21): ядро,
восстановительную зону и факел.
Ядро имеет форму закругленного ярко светящегося конуса. Оно состо-
ит из раскаленных частиц углерода сгорающих в наружной части ядра. Вос-
становительная зона в основном состоит из окиси углерода, получаемого за
500
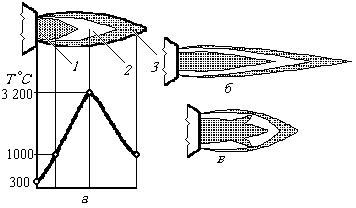
счет сгорания ацетилена: C2H2+O2=2CO2+2H2O. Эта зона имеет более темный цвет.
Рис. 6.21 Строение и распреде-
ление температур ацетилен -
кислородного пламени:
а – нормальное пламя; б –
окислительное пламя; в – вос-
становительное пламя; 1 – яд-
ро; 2 – восстановительная зона;
3 – факел; Т – температура.
Наибольшая температура сварочного пламени находится в этой зоне,
на расстоянии 2…4 мм от ядра. Факел имеет удлиненную конусообразную форму. Он состоит из углекислого газа и паров воды, которые получаются при сгорании окиси углерода и водорода, поступающих из восстановитель-
ной зоны и из окружающего атмосферного воздуха:
4CO+2H2+3O2=4CO2+2H2O.
Внешний вид и температура газового пламени зависит от соотношения объемов ацетилена и кислорода β=V1/V2, где V1 - объем подаваемого в горел-
ку кислорода; V2 - объем подаваемого в горелку ацетилена. В зависимости от величины β можно получить три вида сварочного пламени: нормальное,
окислительное и восстановительное.
Для нормального пламени (рис. 6.21, а) (β = 1…1,3) характерно отсут-
ствие в восстановительной зоне свободного кислорода и углерода. При свар-
ке нормальным пламенем сварочная ванна контактирует в основном с водо-
родом и окисью углерода, образующимися в восстановительной зоне свароч-
ного пламени. Обычно окись углерода не успевает вступить в химическую реакцию с легирующими элементами стали. При высоких температурах во-
дород растворяется в расплаве железа. При охлаждении сварочной ванны во-
дород выделяется из расплава, поступает в факел сварочного пламени и сго-
501
рает с образование паров воды. При сварке медных и алюминиевых сплавов,
высоколегированных сталей, выделяющийся водород приводит к растрески-
ванию и пористости сварного шва.
Окислительное пламя получается при избытке кислорода (β = 1,5…1,7).
Ядро окислительного пламени (рис. 6.21, б) имеет конусообразную форму бледной окраски. Все пламя приобретает синевато – фиолетовую окраску и горит с характерным шумом. Температура пламени несколько выше, чем у нормального. При сварке сталей наблюдается значительное окисление свар-
ного шва, поэтому пламя применяют для сварки латуни и для пайки тверды-
ми припоями. При использовании окислительного сварочного пламени про-
исходит интенсивное окисление железа: Fe+O=FeO. Образующаяся закись железа окисляет легирующие элементы и углерод: Si+2FeO=SiO2+2Fe; Mn+FeO=MnO+Fe; Fe3C+FeO = CO↑+4Fe (частичное восстановление железа).
Окислы марганца и кремния могут остаться в металле сварного шва или всплыть вверх и перейти в сварочный шлак. Если содержание марганца,
кремния и углерода в сварочной ванне недостаточно, то восстановление же-
леза не происходит, что приводит к ухудшению механических свойств свар-
ного шва.
Науглероживающее пламя (рис. 6.21, в) получается при избытке ацети-
лена (β = 0,95). Ядро пламени может иметь несколько зубчиков, теряет рез-
кость очертаний, а на его конце появляется зеленый венчик. Восстановитель-
ная зона почти сливается с ядром. При большом избытке ацетилена (β > 0,95)
пламя начинает коптить. Избыточный углерод легко поглощается расплав-
ленным металлом сварного шва.
При сварке науглероживающим пламенем окись углерода и свободный углерод реагируют с железом, образуя карбид железа: 3Fe+2CO=Fe3C+CO2; 3Fe+C= Fe3C. Следовательно, происходит науглероживание железа. Эти хи-
мические реакции позволяют применять науглероживающее пламя для свар-
ки чугуна.
502
ГС применяют при: изготовлении и ремонте изделий из тонколистовой стали (сварка сосудов и резервуаров небольшой емкости, заварка трещин,
вварка заплат и т.д.); сварке трубопроводов малых и средних диаметров (до
100мм) и фасонных частей к ним; ремонтной сварке литых изделий из чугу-
на, бронзы и силумина (заварка литейных дефектов); сварке изделий из алю-
миния и его сплавов, меди, латуни, свинца; наплавке латуни на стальные и чугунные детали; сварке кованого и высокопрочного чугуна с применением присадочных прутков из латуни и бронзы, низкотемпературной сварке чугу-
на.
Газокислородная резка металлов заключается в сжигании нагретого ме-
талла в струе чистого кислорода. Различают два вида резки: разделительная и поверхностная. При разделительной резке из металлического листа вырезает-
ся заготовка для дальнейшей обработки. Разделительная резка может осуще-
ствляться вручную по разметке. В серийном производстве применяется резка с использованием стационарных машин по шаблонам. При поверхностной резке удаляется лишний металл с поверхности изделий. Для осуществления процесса резки необходимы следующие условия: Температура плавления ме-
талла должна быть больше температуры его горения в атмосфере кислорода.
В противном случае, металл будет плавиться и переходит в жидкое состояние до резки. Температура плавления шлаков должна быть меньше температуры горения металла в атмосфере кислорода (выделение шлаков должно проис-
ходит в жидкотекучем состоянии). Количество тепла, выделяемого при резке должно быть достаточным для поддержания непрерывности процесса. Теп-
лопроводность металла не должна быть слишком высокой и должна способ-
ствовать сохранению тепла на поверхности кромки реза. Температура плав-
ления шлаков должна быть меньше температуры горения металла в кислоро-
де. Количество теплоты, выделяемой при резке должно поддерживать непре-
рывность процесса. Температура плавления металла должна быть больше температуры его горения в кислороде. Наиболее полно этому условию удов-
летворяют низкоуглеродистые и низколегированные стали. При содержании
503