
Лисиенко Ресурсы и факторы управления в енергосбережении 2011
.pdfпути роста коэффициента теплоотдачи встает и ограничение по равномерности нагрева металла. При равных коэффициентах теплоотдачи часто с точки зрения форсирования тепловой нагрузки предпочтительным оказывается способ отопления, обеспечивающий большую равномерность нагрева. Поиску такого способа отопления и посвящен ряд работ. В частности, при способе факельносводового отопления печей достигается наибольшая равномерность нагрева при примерно одинаковых коэффициентах теплоотдачи по сравнению с традиционным отоплением с помощью стержневых факелов (боковых, торцевых горелок). Максимальный температурный уровень факелов снижается за счет интенсивной теплоотдачи к кладке печи, а вынос вредных выбросов может дополнительно подавляться организацией циркуляционного (подковообразного) движения газов в рабочем пространстве печей. При этом теплоотдача от газов относительно уменьшается, а излучение кладки существенно возрастает, что не дает снижения теплового потока на металл, по сравнению с торцевым отоплением.
Максимальные температуры газов при этом способе отопления заметно ниже, чем при торцевом отоплении (по данным на стенде Научно-исследовательского института металлургической теплотехники (ВНИИМТ) – на 50–100 °С), что приводит к относительному уменьшению выбросов оксидов азота в атмосферу. Кроме того, при этом способе максимум температур смешается ближе к своду, уменьшается геометрический напор газов в рабочем пространстве печи и величина выбиваний дымовых газов непосредственно на рабочую площадку, что значительно улучшает условия труда вблизи печей и снижает концентрацию вредных веществ уровне рабочей площадки.
По данным измерений на печах с факельно-сводовым отоплением, концентрация оксидов азота NOx существенно оказалась меньше, чем на печи с торцевым отоплением, а на рабочей площадке выбросов NOx не было. Перевод на факельно-сводовое отопление методической печи Первоуральского новотрубного завода (ПНТЗ) привел к снижению удельного расхода топлива и улучшению условий работы обслуживающего персонала. Положительные результаты работы при переводе на факельно-сводовое ото-
91
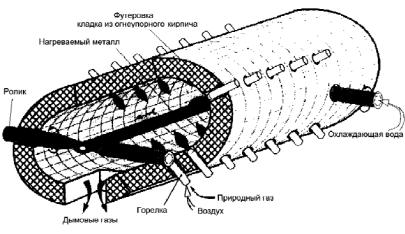
пление были достигнуты и на ряде других печей, в том числе и на других заводов.
2.Технология рециркуляции продуктов сгорания для снижения образования оксидов азота предназначена для снижения токсичных выбросов в атмосферу при сжигании газообразного или жидкого топлива в котельных установках.
Рециркуляция продуктов сгорания представляет собой наиболее
эффективный метод подавления образования оксидов азота (NOx) при сжигании как газа, так и мазута, позволяющий снизить содер-
жание NOx в уходящих газах на 60–70 %. Метод основан на отборе части продуктов сгорания за котлом и подаче их в зону горения.
Реализация предлагаемой технологии рециркуляции продуктов сгорания на котле не требует повышения производительности дымососов, необходимо только изготовление системы перепускных трубопроводов для продуктов сгорания.
3.Струйно-факельный нагрев (СФН). Скоростной нагрев металла в виде струйно-факельного отопления обеспечивает экономию топлива и снижение выбросов в атмосферу.
Печь представляет собой футерованную (выложенную огнеупорным кирпичом) камеру сгорания круглого сечения, разделенную на секции (рис. 5.13).
Рис. 5.13. Схема печи струйно-факельного нагрева трубной заготовки
92
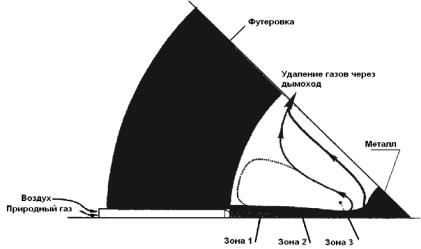
В футеровке печи размещается система металлических сопел, направленных на нагреваемый металл и служащих для подачи подготовленной горючей смеси в рабочее пространство. При струйнофакельном нагреве струя газовоздушной смеси сгорает до удара о металл, что позволяет получить исключительно высокую плотность теплового потока на металл. На практике такой режим удается реализовать, если температура продуктов сгорания, заполняющих печное пространство, близка к 1600 К.
На рис. 5.14 показана картина струйного течения для отдельного сопла. Газо-воздушная смесь с температурой 300–600 К вытекает из сопла со скоростью 100–400 м/с в раскаленное печное пространство. Эта смесь непосредственно за срезом сопла образует холодное конусообразное ядро факела протяженностью 5–6 диаметров сопла (зона 1).
Рис. 5.14. Струйное течение газов для отдельного сопла печи струйно-факельного нагрева
Благодаря большой скорости течения, на границе ядра факела происходит интенсивное турбулентное перемешивание газовоздушной смеси с горячими дымовыми газами, струи прогреваются и воспламеняются, так что температура струи перед ударом о металл достигает 1800–1900 К. Омыв поверхности металла и кладки (фу-
93
теровки), горячие продукты сгорания подсасываются в холодное ядро факела (см. рис. 5.14), интенсифицируют его прогрев, зажигание и организуют стабилизацию пламени. Среднее время пребывания смеси в ядре факела не превышает 10-4 с.
Интенсивное перемешивание печных газов обеспечивает практически полное выгорание топлива. Продукты сгорания (дым) удаляются через дымоходы, расположенные в торцах каждой секции. Температура внутри секции определяется расходом топлива (природного газа) и температурой металла на входе секции, изменяясь от 1600 К в начальных до 1950 К в конечных секциях.
Для подачи в печь используется смесь природного газа и воздуха. Благодаря снижению температуры в рабочем пространстве до 400 °С, в том числе и огнеупорной футеровки до 200–250 °С – за счет интенсивной теплоотдачи к металлу, применение струйнофакельных горелок скоростного нагрева сокращает на порядок эмиссию оксидов азота по сравнению с туннельными горелками (см. также рис. 5.6). В печах струйно-факельного нагрева оксиды азота в основном образуются по быстрому механизму, и их эмиссия близка к минимально возможной (см. также рис. 5.5 и 5.6). Отметим также, что при использовании струйно-факельного отопления существенно (в 1,5–2 раза) увеличивается производительность нагревательных и термических печей, уменьшается удельный расход топлива, сокращается расход огнеупорных материалов, улучшаются условия динамики разогрева и пуска печей.
4.Одним из эффективных способов подавления образования
NOx в высокотемпературных печах является также акустическое воздействие на факел. При этом рекомендуемые частоты акустиче-
ских колебаний составляют 1,5–2,0 кГц, требуемая мощность на 1 м3 объема газов – 0,25–0,3 Вт. Один из факторов этого явления связан со сглаживанием температурных пульсаций в факеле и со снижением пиков наиболее высоких температур пламени.
5.Интересным примером успешного и эффективного применения горелочных устройств, способов отопления и вентиляции промышленных цехов является прямое использование продуктов сгорания природного газа. Несмотря на подачу продуктов сгорания непосредственно в пространство цехов, содержание вредных вы-
94
бросов (NОх, СО) снижено до такой минимальной степени, что это не наносит никакого ущерба обслуживающему персоналу. Это обеспечивается тщательным перемешиванием природного газа и воздуха в специальных горелочных устройствах, точным регулированием коэффициента расхода воздуха за счет автоматизации соотношения «газ-воздух», снижением температуры горения при увеличении коэффициента расхода воздуха (см. формулу (3.11) и рис. 5.1).
5.4. Модельные представления и основные факторы, влияющие на эмиссию оксида углерода
Основные механизмы эмиссии оксида углерода. Реакция го-
рения оксида углерода (угарного газа)
CO+ |
1 |
O |
=CO |
|
(5.23) |
2 |
|
||||
|
2 |
|
2 |
|
отличается очень большими скоростями собственно химического взаимодействия, время реагирования порядка t = 10-8 c. Поэтому в основном появление в продуктах сгорания топлив химического недожога в виде СО обусловлено другими факторами, нежели кинетика процессов горения, т.е. скорости химического реагирования.
На выходе из рабочего пространства энерготехнологических агрегатов оксид углерода может появиться в результате действия трех основных механизмов.
1. Имеет место недостаток кислорода для горения, т.е. коэффициент расхода воздуха α < 1. В этом случае в продуктах сгорания при наличии СО либо отсутствует кислород, т.е. О2 = 0, либо имеет место соотношение
СО> |
1 |
О2 . |
(5.24) |
|
2 |
||||
|
|
|
2. Длина факела превышает длину рабочего пространства печи. Признаком этого механизма является одновременное присутствие в продуктах сгорания О2 и CO, причем в этом случае в соответствии с реакцией дожигания СО в СО2 (5.23) имеет место соотношение
СО ≤ |
1 |
О2 . |
(5.25) |
|
2 |
|
|
95
3. Третий механизм заключается в возможном появлении СО в результате условий термодинамического равновесия реакции (5.23) при высоких температурах. Реакция (5.23) обратима и при значительном повышении температуры горения существенно сдвигается влево, т.е. в сторону диссоциации двуоксида углерода и образования СО. Однако при температурах рабочего пространства многих печей (не выше 1800–2000 °С) химический недожог в результате диссоциации не превышает 2–3 %.
Успешная борьба с выделением оксида углерода на выходе из рабочего пространства печи не только обеспечивает улучшение процессов теплоотдачи, но и является надежным гарантом отсутствия вредных выбросов угарного газа в атмосферу. Основные пути при этом: сокращение длины факела и подача достаточного количества окислителя для полного сгорания топлива.
Рассмотрим более подробно основные мероприятия по сокращению эмиссии оксидов углерода.
Мероприятия по сокращению эмиссии оксида углерода. Со-
отношение газ–воздух. Для предотвращения образования СО вследствие недостатка окислителя (воздуха), необходимо обеспечивать требуемое соотношение подаваемого топлива и окислителя, т.е. поддержание необходимого коэффициента расхода воздуха α. Этот коэффициент должен быть больше единицы, но не превышать некоторого значения, при котором начинает снижаться температура горения. Условие управления при этом может быть выражено в виде критерия
α = opt α. |
(5.26) |
На практике соблюдение этого условия достигается применением автоматических регуляторов соотношения «газ–воздух», чаще всего с коррекцией этого соотношения по содержанию необходимого по условию (5.23) кислорода в продуктах сгорания с некоторым избытком кислорода (α = 1,05–1,08) обычно О2 = 0,5–1,5%.
В случае регулирования соотношения «газ–воздух» в качестве заданного устройства используется задатчик по коэффициенту расхода окислителя (воздуха) α. Корректирующий регулятор воздействует на заданное значение α – корректирует его (рис. 5.15). При этом необходимый расход окислителя (воздуха) определится по соотношению
96
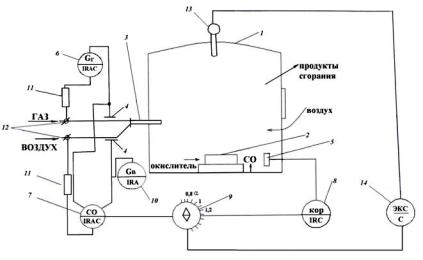
Vв = Vг Lα = Vг α L0, |
(5.27) |
где Vв – расход окислителя (например, воздуха); Vг – расход газа; Lα – теоретически необходимое количество воздуха при α ≠ 1; α – коэффициент расхода воздуха; L0 – теоретически необходимое количество воздуха при α = 1.
Рис. 5.15. Схема автоматизированного регулирования соотношения «газ-воздух»: 1 – рабочее пространство энерготехнологического агрегата (например, промышленной печи); 2 – нагреваемый материал; 3 – горелочное устройство; 4 – датчики расходов (измерительные диафрагмы); 5 – датчик на кислород; 6 – вторичный прибор и регулятор расхода газа; 7 – регулятор соотношения «газ-воздух»;
8 – корректирующий регулятор на содержание кислорода в продуктах сгорания; 9 – задатчик соотношения «газ-воздух» (коэффициент α расхода воздуха α); 10 – вторичный прибор расхода воздуха; 11 – усилительные механизмы; 12 – регулирующие органы (дроссельные заслонки); IRA – показывающий, записывающий и сигнализирующий вторичный прибор; С – регулятор; GГ и
СВ – расход газа и воздуха, соответственно; 13 – датчик температуры; 14 – экстремальный регулятор
Необходимость в корректировке величины α по сравнению с заданным в соответствии с измеряемыми расходами газа и воздуха определяется в условиях действующих энерготехнологических агрегатов возможными подсосами воздуха и выбиваниями продуктов сгорания через неплотности в конструкции агрегата (например, через рабочие окна печи), а также возможным использованием ки-
97
слорода на технологические процессы и возможным выделением оксида углерода в процессе плавания или нагрева (см. рис. 5.15).
В ряде исследований рекомендовано при управлении процессом горения применение экстремального регулятора для установления значения коэффициента расхода воздуха, соответствующего максимальной температуре рабочего пространства или самого факела (см. рис. 5.15). В этом случае критерий оптимизации формулирует-
ся по максимуму температуры печи Тпеч: |
|
Тпеч = max Tпеч. |
(5.28) |
Управление длиной факела. В общем случае длина факела оп-
ределяется приближенной формулой В.Г. Лисиенко: |
|
|||||
l |
= K |
Σ |
11,4Ξ |
C0 |
D , |
(5.29) |
|
||||||
ф |
|
0 |
|
|||
|
|
|
|
Ccx |
|
где lф – длина факела; D0 – диаметр выходного сечения сопла горелки; С0 и Ссх – начальная и стехиометрическая концентрация топлива в продуктах сгорания (в смеси с воздухом); Ξ – фактор неравноплотности горящей струи, учитывающий отличие плотности струи от плотности окружающей среды и подаваемого газа; KΣ – обобщенный коэффициент обстановки, учитывающий влияние различных факторов на длину факела.
При величине С0 = 1 (отсутствие предварительного перемешивания газа и воздуха) формула (5.29) может быть преобразована к виду
lф = Kz 11,4Ξ(L0θρ +1)D0 , |
(5.30) |
где θρ = ρ0в/ρ0г – фактор начальной неравноплотности, равный отношению плотности воздуха для горения ρ0в к плотности газа ρ0г (при нормальных условиях).
Величина обобщенного коэффициента обстановки приближенно может быть выражена в виде сомножителей ряда частных коэффициентов
KΣ = Kу Kα Kдв Kн Kин Kβ Kγ Kзак, |
(5.31) |
где Kу, Kα, Kдв, Kн, Kин, Kβ, Kγ,Kзак – коэффициенты, учитывающие: импульс облегающего потока; коэффициент расхода воздуха;
двухфазность струи; стесненность развития факела; подачу интен-
98
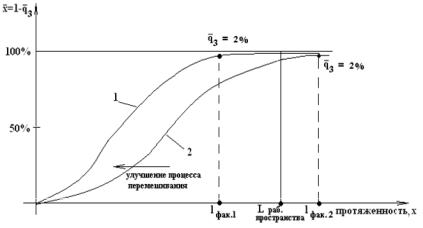
сификатора; угол встречи воздуха и газа; угол атаки факела на нагреваемую поверхность; закручивание потоков соответственно.
Таким образом, в распоряжении как конструктора, так и автоматчика оказывается достаточно много факторов, обеспечивающих выгорание топлива в пределах рабочего пространства агрегата. Такими факторами в случае автоматического управления может быть подача интенсификатора, закручивание струй, изменение диаметра выходного сопла газа, путем, например, распределения подачи газа по центру и по периферии корпуса горелки.
Характер изменения степени выгорания топлива по длине рабочего пространства в случае короткого и чрезмерно длинного факела показан на рис. 5.16. Как видим, в случае 1 – lф < Lраб.пр., в случае
2 – lф > Lраб.пр.
Рис. 5.16. Зависимость степени выгорания топлива по длине рабочего пространства печи при коротком (1) и чрезмерно длинном (2) факелах:
х − степень выгорания топлива; Qпот′′ − средний химический недожог топлива;
х – протяженность рабочего пространства; Lраб.пр. – конечная длина рабочего пространства
Величина степени выгорания х может быть оценена по формуле В.Г. Лисиенко и В.Б. Кутьина:
х |
= 1 − ехр(−mх2 ), |
(5.32) |
99
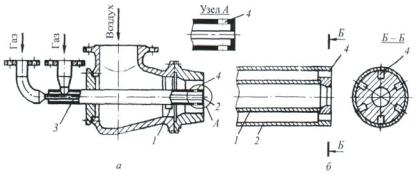
где m – эмпирический коэффициент, зависящий от длины факела. Так, если принять при х = lф величину степени выгорания топлива х = 0,98 (2 % химический недожог топлива), то при х = lф = 1 м;
m = − |
2,3lg(1− х) |
= − |
2,3lg(1−0,98) |
= 3,91. |
|
x |
|
1 |
|
На рис. 5.17 представлен пример конструкции газовой горелки ФСГ-Р УГТУ-УПИ средней тепловой мощности с регулируемой длиной факела, а на рис. 5.18 схемы регулирования длины факела в рабочем пространстве нагревательной печи. Это достигается переключением подачи газа через центральное сопло горелки (длинный факел) и через периферийный ввод, заканчивающийся рядом выпускных отверстий (короткий факел).
Рис. 5.17. Конструкция горелки ФСГ-Р:
а– общий вид горелки; б – вариант сопел периферийного подвода газа;
1– внутренняя газоподводящая труба; 2 – сопло центрального подвода газа; 3 – наружная газоподводящая труба; 4 – сопла периферийного подвода газа
На рис. 5.19 показана конструкция горелки большой тепловой мощности с регулируемой длиной факела для вращающихся барабанных обжиговых печей. Как видим, горелки снабжены соплами для дополнительной интенсификации процесса горения за счет подачи боковых струй кислорода или компрессорного воздуха (конструкции УГТУ-УПИ и Московского института стали и сплавов – МИСиС).
100