
Дворецкий С.И. и др. - Комп. моделир. и оптимизация технологич. процессов и оборуд. [2003]
.pdf
n |
( pH ) |
|
|
|
−5,897+0,428pH, pH < 7 |
|
|
|
|
|
|
W2 = k2 ( pH ) cD2 |
|
|
|
|
|
19,86+4,428pH −0,286pH |
2 |
−4 |
pH |
3 |
, |
|
|
lgk2 |
= |
− |
|
−4,75 10 |
|
||||
|
|
|
|
|
7 ≤ pH ≤ 9,5 |
||||||
|
|
|
|
|
|
|
|
||||
|
|
|
|
|
|
|
|
|
|
|
|
|
|
|
|
|
5,504− pH, pH > 9,5 |
|
|
|
|
|
|
|
|
|
|
1, pH < 7 |
|
|
|
|
|
||
|
|
N2 |
|
|
|
−3,32 10−3 pH2 +2,21 10−3 pH3,7 ≤ pH ≤ 9,5 |
|||||
|
|
= 0,4 |
|||||||||
|
|
|
|
2, pH > 9,5 |
|
|
|
|
|
||
|
|
|
|
|
|
|
|
|
|
|
|
|
|
|
|
|
|
|
|
|
|
|
|
Обозначения: D − ArN2Cl , Az − (R −Y ) , cд, cAz - концентрации диазо- и азосоставляющих; cp , cп* - текущая и равновесная концентрации пигмента; [H + ] – концентрации ионов водорода; kW – ионное произ- ведение; ka ,kb , k p – константы кислотно-основных равновесий; I, ηд, ηк – скорости образования и роста кристаллов пигмента в диффузионной и кинетической областях; f (r) – плотность распределения по-
верхности кристаллов пигмента по их размерам; D – коэффициент диффузии (рассчитывается по уравнению Эйнштейна-Смолуховского.
Такие аппараты весьма эффективны как для проведения быстрых химических процессов, так и для интенсивного смешения с целью гомогенизации жидкости. Они успешно используются в качестве смесителей (для получения целевого продукта), предреакторов (для приготовления исходной реакционной смеси), малогабаритных реакторов (для проведения быстрых химических реакций), а также осуществления массообменных процессов [30 – 33].
Математическое описание процесса диазотирования, осуществляемого в турбулентных аппаратах трубчатого типа.
Основными элементами (модулями) турбулентных аппаратов трубчатого типа являются смеситель на входе в трубчатый аппарат, реактор цилиндрического типа, диффузор-конфузор и камеры смешения в аппарате комбинированного типа. Таким образом, для моделирования процесса диазотирования необходимо учесть процессы: 1) смешения дозируемых в аппарат компонентов в камере смешения, установленной на входе в аппарат; 2) химического взаимодействия в трубчатой части аппарата; 3) изменения условий протекания элементарных процессов химического взаимодействия при наличии в аппарате устройства турбулизации потока (диффузор-конфузора); 4) химического взаимодействияв камерах смешения ваппаратах комбинированного типа.
Рассмотрим основные этапы построения математической модели процесса диазотирования, осуществляемого в турбулентных аппаратах трубчатого типа в среде сильной минеральной кислоты (соляной, серной и др.). Исходное сырье – ароматический амин – непрерывно подается в реактор в виде солянокислой суспензии. Одновременно в реактор вводится водный раствор нитрита натрия, подача которого может распределяться по длине трубчатой части реактора или по секциям комбинированного реактора (рис. 3.24, 3.25).
Работоспособность трубчатого реактора определяется условиями обеспечения заданной производительности аппарата, неосаждения твердой фазы амина в вертикальных трубах и турбулентности гидродинамического режима течения в трубе. Основными параметрами, определяющими эти условия, являются диаметр трубы реактора и концентрация амина в питании реактора.
Допустимый диаметр трубы реактора по условию неосаждения агрегатов твердой фазы амина определяется как
d ≤ dкрI ,
где dкрI – первый критический диаметр трубы реактора рассчитывается по формуле
I |
Re µc |
|
|
||
dкр = |
|
|
|
, |
(3.63) |
Kv |
oc |
ρ |
|||
|
|
c |
|
|
где µc – средний динамический коэффициент вязкости суспензии, voc .– скорость осаждения агрегатов амина, ρc – средняя плотность суспензии, K = vп / voc , vп – скорость потока.
Средняя плотность суспензии при заданной плотности твердой фазы ρт и массовая доля кислоты в водном растворе X CK рассчитываются по формулам:

ρc = |
|
|
|
|
|
|
|
1 |
|
|
|
|
|
; |
ρ = |
|
|
|
|
|
|
1 |
|
|
|
|
; |
|
|
(3.6 |
||||
|
|
|
|
|
|
|
|
|
|
|
|
|
|
|
|
|
|
|
|
|
|
|
|
|
|
|
|
|
4) |
|||||
|
|
|
|
|
|
|
|
|
|
|
|
|
|
|
|
|
|
|
|
|
|
|
|
|
|
|
|
|
||||||
X т |
|
|
1− X т |
|
|
|
|
|
|
|
|
|
|
|
|
|
|
|||||||||||||||||
|
|
+ |
|
|
|
|
|
|
XCK |
+ |
|
1− XCK |
|
|
|
|
|
|||||||||||||||||
|
|
ρ |
т |
|
|
ρ |
|
|
|
|
|
ρ |
CK |
|
|
|
ρ |
|
|
|
|
|
|
|||||||||||
|
|
|
|
|
|
|
|
|
|
|
|
|
|
|
|
|
|
|
|
|
|
в |
|
|
|
|
|
|
||||||
X CK |
= |
|
CCK MCK |
; |
ϕ = |
CA(0) M A |
. |
|
|
|
|
|
|
|||||||||||||||||||||
|
(1 − ϕ)ρ |
|
|
|
|
|
|
|
||||||||||||||||||||||||||
|
|
|
|
|
|
|
|
|
|
|
|
|
ρт |
|
|
|
|
|
|
|
|
|
|
|
|
|||||||||
где |
|
|
CK , |
|
|
|
т – массовые доли концентрированной соляной кислоты в растворе и твердой фазы |
|||||||||||||||||||||||||||
X |
|
X |
||||||||||||||||||||||||||||||||
амина в суспензии, |
|
|
ρт, |
ρCK , ρв |
– плотности твердой фазы амина, концентрированной соляной ки- |
|||||||||||||||||||||||||||||
слоты и воды соответственно, |
c(0) |
, c |
= 2,5c(0) |
– концентрация амина и соляной кислоты в суспен- |
||||||||||||||||||||||||||||||
|
|
|
|
|
|
|
|
|
|
|
|
|
|
|
|
|
|
|
|
|
|
|
|
|
|
|
|
|
|
|
A |
CK |
A |
|
зии на входе в реактор.
Из условий надежной работы клапанов и насосов, питающих реактор, концентрация амина в суспензии на входе в реактор не должна превышать 800 моль/м3 . Отсюда максимальная объемная
доля твердой фазы амина в суспензии будет равна ϕ = 8,4 % , и этому значению ϕ соответствует сле-
дующая формула для расчета вязкости суспензии:
µc =µ(1+2,5ϕ), |
|
|
|
|
|
(3.6 |
|||
|
|
|
|
|
5) |
||||
|
|
|
|
|
|
|
|
|
|
где µc = |
|
|
|
1 |
|
|
|
, µ, µCK , µв – средние динамические коэффициенты вязкости жидкой фазы, соля- |
|
X |
CK |
+ |
1 |
− X |
CK |
||||
|
µCK |
|
|
|
µв |
|
|
|
|
ной кислоты и воды соответственно. |
|||||||||
Среднюю скорость свободного осаждения твердой фазы можно рассчитать по формуле |
|||||||||
|
dтmax (ρт − ρ) |
|
(3.66) |
||||||
voc = 5,46 |
. |
|
|||||||
|
|
|
ρ |
|
|
|
|||
|
|
|
|
|
|
|
|
После подстановки формул (3.64) – (3.66) в выражение (3.63) получим, что dкрI зависит от кон-
центрации амина в суспензии на входе в реактор, т.е.
dкрI = f (c(A0) ). |
(3.67) |
Вторым условием работоспособности реактора диазотирования является обеспечение турбулентного режима течения суспензии амина – Re =104 . Определяемый с учетом этого условия диа-
метр будем находить из следующего выражения:
dкрII = |
4G(0) |
ρ |
|
l |
c |
, |
|
|
|
||
|
πRe µc |
где dкрII – второй критический диаметр труб реактора; Gl(0) – расход жидкой фазы на входе в реак-
тор.
Общий расход солянокислой суспензии амина в питании реактора определяется из уравнений материального баланса по стадиям технологического процесса получения азокрасителей
G(0) |
= |
|
Q 106 |
, |
l |
|
c(0)A |
TэфKD K Az Мп |
|
|
|
|
где KD , K Az , Tэф – выходы по стадиям диазотирования, азосочетания и эффективный фонд рабочего
времени реакторной установки синтеза азопигментов, соответственно.
Диаметр dкрII зависит от концентрации амина в питании реактора и производительности
dкрII = f (c(A0) , Q), |
(3.68) |
где Q – производительность реактора по пигменту.
На рис. 3.26 представлены графики, соответствующие уравнениям (3.67) и (3.68), из которых видно, что при производительности меньше 1000 т/год (для примера был взят пигмент алый лакокрасочный) диаметр трубы реактора определяется условием турбулентности.
Задаваясь максимально возможным диаметром трубы реактора ( ~ 40 мм ), можно определить максимальную концентрацию амина с(A0) в питании реактора. Минимальную концентрацию ами-
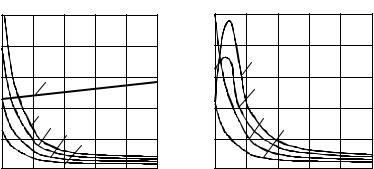
на можно определить по точке перегиба кривой для каждой производительности Q (рис. 3.26). |
||||||||||||||
Соответственно такими концентрациями будут: |
|
|
||||||||||||
|
– для производительности 500 |
т/год c(A0) [130, 210] |
моль/м3; |
|
||||||||||
|
– для производительности 1000 т/год c(0)A [280, 410] |
моль/м3. |
|
|||||||||||
|
На рис. 3.27 представлены графики зависимости среднего времени пребывания реакционной |
|||||||||||||
смеси t от концентрации амина c(A0) . Их анализ показывает, что при производительности больше |
||||||||||||||
1000 т/год и концентрации амина не более 100 моль/м3 |
время пребывания будет расти, так как опре- |
|||||||||||||
деляющим условием при этом является неосаждение твердой фазы амина (рис. 3.26). При концен- |
||||||||||||||
трациях больше 100 моль/м3 |
и Q >1000 т/год диаметр реактора определяется только из условий тур- |
|||||||||||||
булентности реакционного потока и существенно зависит от изменения концентрации амина, что |
||||||||||||||
вызывает большее изменение объема реактора, нежели расхода суспензии на входе в реактор. При |
||||||||||||||
Q <1000 т/год среднее время пребывания при всех концентрациях падает. Только при очень больших |
||||||||||||||
концентрациях (700 ... 800) моль/м3 |
влияние на время пребывания расхода суспензии и объема реак- |
|||||||||||||
тора становится равнозначным. |
|
|
|
|
|
|
|
|||||||
d |
, |
|
|
|
|
|
t /10, c |
|
|
|
|
|
||
0,71 |
крKP, м |
|
|
|
|
399 |
|
|
|
|
|
|
|
|
0,57 |
|
|
|
|
|
|
321 |
|
|
|
|
|
|
|
0,43 |
|
|
|
|
|
|
242 |
|
1 |
|
|
|
|
|
|
1 |
|
|
|
|
|
2 |
|
|
|
|
|
||
|
|
|
|
|
|
|
|
|
|
|
|
|
||
|
|
|
|
|
|
|
|
|
|
|
|
|
|
|
0,29 |
|
2 |
|
|
|
|
164 |
|
3 |
|
|
|
|
|
|
|
|
|
|
|
|
|
|
|
|
|
|||
|
|
3 |
|
|
|
|
|
|
4 |
|
|
|
|
|
0,15 |
|
|
4 |
5 |
|
|
85 |
|
|
|
|
|
|
|
|
|
|
|
|
|
|
|
|
|
|
|
|||
|
|
|
|
|
|
|
|
|
|
|
|
|
|
|
0,0150 |
200 |
350 |
500 |
650 |
800 |
7 |
50 |
200 |
350 |
500 |
650 |
800 |
|
|
|
|
|
|
|
cA(0) , моль/мм33 |
|
|
|
|
|
cA(0) , моль/ м3 3 |
|
||
|
|
|
|
|
|
|
|
|
|
|
|
моль/м |
|
|
Рис. 3.26 Зависимость крити- |
Рис. 3.27 Влияние |
концен- |
|
|||||||||||
ческих диаметров трубы ре- |
трации амина на входе в |
|
||||||||||||
актора, |
|
определяе- |
реактор на |
|
|
|
пре- |
|
||||||
мых |
из |
условий |
его |
бывания |
|
реакционной |
|
|||||||
работоспособности, от кон- |
смеси t − c(A0) : |
|
|
|
|
|||||||||
центрации амина на входе в |
1 – Q = 2000 |
т/год; |
|
|
|
|||||||||
реактор: |
|
|
|
|
2 – Q = 1500 |
т/год; |
|
|
|
|||||
1 – dкрI |
= f (c(0)A ); |
|
|
|
|
|
|
|||||||
|
|
|
3 – Q =1000 |
т/год; |
|
|
|
|||||||
2, 3, 4, 5 – dкрI = f (c(A0) , Q); |
|
|
|
|||||||||||
4 – Q = 500 т/год |
|
|
|
|
||||||||||
2 – Q = 2000 |
т/год; |
|
|
|
|
|
|
|
|
|
|
|||
3 – Q = 1500 |
т/год; |
|
|
|
|
|
|
|
|
|
|
|||
4 – Q = 1000 |
т/год; |
|
|
|
|
|
|
|
|
|
|
|||
5 – Q = 500 т/год |
|
|
|
|
|
|
|
|
|
|
|
|||
|
В производственных условиях диаметр трубы реактора постоянен и при необходимости уве- |
|||||||||||||
личения производительности Q можно наращивать его длину. Этого результата можно добиться |
||||||||||||||
и технологическим приемом, повышая концентрацию твердой фазы амина с целью снижения |
||||||||||||||
расхода солянокислой суспензии амина в питании реактора. Для увеличения концентрации ами- |
||||||||||||||
на без нарушения условий работоспособности реактора необходимо выбрать такой диаметр трубы |
||||||||||||||
(рис. 3.26), которому будет соответствовать максимально возможный интервал допустимых кон- |
||||||||||||||
центраций амина для выбранной производительности. Такому условию соответствует диаметр |
||||||||||||||
трубы, равный |
|
40 мм. |
|
|
|
|
|
|
|
|||||
|
Вторым важным достоинством применения реактора с максимальным диаметром (40 мм) яв- |
|||||||||||||
ляется возможность его использования в малотоннажных производствах, так как при больших |
||||||||||||||
диаметрах не будет выполняться условие турбулентности реакционной смеси. |
||||||||||||||
|
На рис. 3.28 представлен интервал допустимых значений концентраций амина на входе в ре- |
|||||||||||||
актор. По данной области определяются минимально и максимально возможные значения кон- |
||||||||||||||
центраций амина при различных производительностях |
установки по пигменту. На практике |
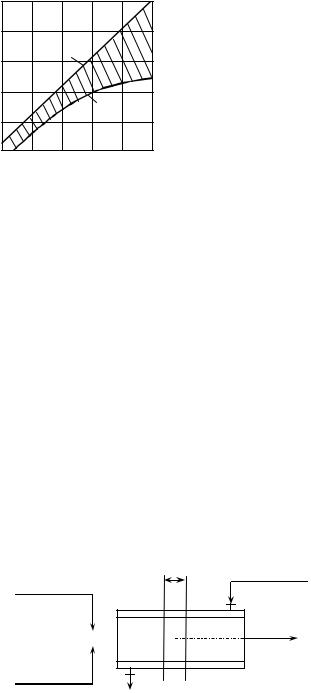
концентрация амина будет изменяться около номинального значения, ориентировочно, в пределах ±2,5 % . В связи с этим на рис. 3.28 изображена допустимая область значений концентраций
амина, ограниченная кривыми c(A0max) = f (Q) / 0,975 и c(A0max) = f (Q) /1,025 (допустимая область заштрихо-
вана).
cA(0) , моль/ м3 |
|
|
моль/м3 |
|
|||
750 |
|
|
|
|
|
|
|
610 |
|
|
|
|
|
|
|
470 |
|
|
cA(0max) |
|
|
|
|
|
|
|
|
|
|
|
|
330 |
|
|
|
cA(0min) |
|
|
|
|
|
|
|
|
|
||
190 |
|
|
|
|
|
|
|
50 |
115 |
492 |
869 |
1246 |
1623 |
2000 |
|
|
|
|
|
|
Q, т/ год |
т/год |
|
|
|
|
|
|
|
|
Рис. 3.28 Допустимая область концентрации амина на входе в реактор
Минимально возможная производительность трубчатого реактора по пигменту, при которой выполняются условия неосаждения твердой фазы амина и турбулентности реакционной среды, равна 115 т/год . При меньших производительностях необходимо использовать реактор периодиче-
ского действия или реактор смешения типа "царга-тарелка".
Прейдем к построению математической модели непрерывного процесса диазотирования, осуществляемого в трубчатом реакторе. Схема материальных потоков в одной секции трубчатого реактора приведена на рис. 3.29.
При составлении уравнений математической модели примем следующие допущения: 1) гидродинамические режимы течения реакционной смеси и хладагента близки к режиму идеального вытеснения; 2) реактор является объектом с распределенными только по длине l координатами, скорость потока vп(l) = const; 3) потери тепла в окружающую среду пренебрежимо малы; 4)
теплофизические характеристики принимаются постоянными в рабочем диапазоне температур; 5) кристаллы амина будем считать сферическими частицами; 6) реакция диазотирования происходит в растворе.
∆l
cA(0) , cCK(0) , Gl(0) , GS(0) , ψ(0, r), T (0)
солянокислая суспензия амина
cN(0) , GN(0) , TN(0)
Gx , Tx(0) l1 l2
Gx , Tx( L)
хладагент
c(L), ψ(L, r)
раствор
диазосоединения
водный раствор нитрита натрия
Рис. 3.29 Схема материальных потоков
втрубчатом реакторе диазотирования:
ψ(r) – гранулометрический состав; х – хладагент; l –
жидкая фаза; s – твердая фаза; σ, χ –
нитрозные газы и диазосмолы, соответственно
С учетом принятых обозначений и допущений составим уравнения материального покомпонентного баланса на участке трубы ( l1, l2 ) за промежуток времени ( t1, t2 ) например, по растворен-
ному амину:
t2 |
[c |
|
|
|
|
|
(l )]dt +S |
t2 l2 |
|
|
|
|
|
|
1 |
∞ |
|
|
|
G |
|
(l |
|
) −c |
|
∫∫ |
W (c |
|
, c |
|
, T) − |
∫ |
ψˆ (ξ, r)W (c |
|
, T)dr dξdt = |
||||
|
|
|
|
|
M A |
|
|||||||||||||
l ∫ |
|
A |
|
2 |
|
A |
1 |
|
2 |
A |
|
AK |
|
1 |
A |
|
|||
t1 |
|
|
|
|
|
|
|
t1 l1 |
|
|
|
|
|
|
|
0 |
|
|
|
l2
= S∫[CA(ξ, t2 ) −CA(ξ, t1)]dξ.
l1
Пользуясь теоремой о среднем, получим равенство:
|
[c |
|
|
|
(l )] |
|
|
|
|
|
|
|
|
|
|
|
|
|
|
|
|
1 |
|
∞ |
|
|
|
|
|
|
|
|
|
|
|||||
G |
(l ) −c |
|
|
∆t +S W (c |
, c |
|
|
|
, T) − |
|
|
∫ |
ψˆ (ξ, r)W (c |
|
|
, T)dr |
∆l∆t = |
||||||||||||||||||||||
|
|
|
|
|
|
|
|
|
|
|
|
|
|||||||||||||||||||||||||||
t A |
2 |
|
A |
1 |
|
|
t=t3 |
|
2 A |
|
|
AK |
|
|
|
M |
|
|
|
|
|
1 |
|
A |
|
|
ξ=l4 |
||||||||||||
|
|
|
|
|
|
|
|
|
|
|
|
|
|
|
|||||||||||||||||||||||||
|
|
|
|
|
|
|
|
|
|
|
|
|
|
|
|
|
|
|
|
|
|
|
|
|
|
|
A 0 |
|
|
|
|
|
|
|
|
|
|||
|
|
|
|
|
|
|
|
|
|
|
|
|
|
|
|
|
|
|
|
|
|
|
|
|
|
|
|
|
|
|
|
|
|
|
|
|
|
|
t=t |
|
|
|
|
|
|
|
|
|
|
=S[cA (ξ, t2) −cA (ξ, t1)] |
|
|
|
|
|
|
|
|
|
|
|
|
|
|
4 |
||||||||||||||
|
|
|
|
|
|
|
|
|
|
|
|
ξ=l |
∆l, |
|
|
|
|
|
|
|
|||||||||||||||||||
|
|
|
|
|
|
|
|
|
|
|
|
|
|
|
|
|
|
||||||||||||||||||||||
|
|
|
|
|
|
|
|
|
|
|
|
|
|
|
|
|
|
|
|
|
|
|
|
|
|
|
|
|
3 |
|
|
|
|
|
|
|
|
|
|
которое при помощи теоремы о конечных приращениях можно преобразовать к виду: |
|||||||||||||||||||||||||||||||||||||||
|
|
|
|
|
|
|
|
|
|
|
|
|
|
|
|
|
|
|
|
|
|
|
|
|
|
|
|
|
|
|
|
|
|
|
|
|
|
|
|
|
|
∂cA (l, t) |
|
|
|
|
|
|
|
|
|
|
|
|
|
|
|
|
|
|
|
1 |
|
|
|
∞ |
|
|
|
|
|
|
|
|
|
|
|
||
|
|
|
|
|
|
|
|
|
|
|
|
|
|
|
|
|
|
|
|
|
|
|
|
|
|
|
|
|
|
|
|
||||||||
G |
|
|
|
∆t∆l +S W (c |
|
, c |
|
|
|
, T) − |
|
|
|
|
∫ |
ψˆ (ξ, r)W |
(c |
|
|
, T)dr |
∆l∆t = |
||||||||||||||||||
|
|
|
|
|
|
|
M |
|
|
|
|
|
|||||||||||||||||||||||||||
l |
|
|
∂l |
l=l5 |
|
|
|
|
2 |
A |
|
|
AK |
|
|
|
|
|
|
|
|
|
|
1 |
|
A |
|
|
|
|
|||||||||
|
|
|
|
|
t=t3 |
|
|
|
|
|
|
|
|
|
|
|
|
|
|
|
|
|
A 0 |
|
|
|
|
|
|
|
|
|
|
ξ=l4 |
|||||
|
|
|
|
|
|
|
|
|
|
|
|
|
|
|
|
|
|
|
|
|
|
|
|
|
|
|
|
|
|
|
|
|
|
|
|
|
|
|
t=t4 |
|
|
|
|
|
|
|
|
|
|
|
S |
∂cA (l, t) |
|
|
∆l∆t. |
|
|
|
|
|
|
|
|
|
|
|
|||||||||||||
|
|
|
|
|
|
|
|
|
|
|
|
|
|
|
|
|
|
|
|
|
|
|
|
||||||||||||||||
|
|
|
|
|
|
|
|
|
|
|
|
|
∂t |
|
|
|
|
|
l=l3 |
|
|
|
|
|
|
|
|
|
|
|
|||||||||
|
|
|
|
|
|
|
|
|
|
|
|
|
|
|
|
|
|
|
|
|
t=t5 |
|
|
и t1, t2 → t , получим уравнение |
|||||||||||||||
Переходя к пределу при l1, l2 → l |
|||||||||||||||||||||||||||||||||||||||
|
|
|
v ∂cA |
+W (c |
, c |
, T ) |
− |
|
1 |
|
|
|
∞ ψˆ (l, r)W (c , T ) dr = |
|
∂c |
; |
(3.6 |
||||||||||||||||||||||
|
|
|
M |
|
|
|
|
∂t |
|||||||||||||||||||||||||||||||
|
|
|
∂l |
|
2 |
|
|
Ф |
AK |
|
|
|
|
|
|
∫ |
|
|
|
|
1 |
|
A |
|
|
|
|
|
9) |
||||||||||
|
|
|
|
|
|
|
|
|
|
|
|
|
A 0 |
|
|
|
|
|
|
|
|
|
|
|
|
|
|||||||||||||
|
|
|
|
|
|
|
|
|
|
|
|
|
|
|
|
|
|
|
|
|
|
|
|
|
|
|
|
|
|
|
|
|
|
||||||
cа (l, 0) = cаl |
(l); |
cа (0, t) = cа0 (t). |
|
|
|
|
|
|
|
|
|
|
|
|
|
|
|
|
|
|
|
|
|
|
|
|
|
Аналогичным образом можно получить уравнения динамики трубчатого реактора и для других компонентов реакционной смеси:
по азотистой кислоте (АК):
v |
∂cак +W |
(c |
|
, c |
ак |
, T ) +W (c |
ак |
, T ) +W |
(c |
ак |
, c |
д |
, T ) = ∂cак ; |
|
||||||||||||||||||||||||||
|
∂l |
|
|
2 |
|
а |
|
|
|
|
|
|
|
|
3 |
|
|
|
|
|
|
|
4 |
|
|
|
|
∂t |
|
|||||||||||
|
cAK (l, 0) = clAK (l); |
|
cAK (0, t) = cN GN(0) (t) / Gl(0) (t); |
|
||||||||||||||||||||||||||||||||||||
|
по диазосоединению (D): |
|
|
|
|
|
|
|
|
|
|
|
|
|||||||||||||||||||||||||||
ϑ |
∂cD |
−W |
2 |
(c |
A |
, c |
AK |
, T ) |
+W |
4 |
(c |
AK |
, c |
D |
, T ) |
+W |
(c |
D |
, T ) = |
∂cD |
; |
|||||||||||||||||||
|
|
|
||||||||||||||||||||||||||||||||||||||
|
∂l |
|
|
|
|
|
|
|
|
|
|
|
|
|
|
|
|
|
|
|
|
|
|
5 |
|
|
∂t |
|
||||||||||||
cD (l, 0) = cD0 (l); |
|
cD (0, t) = cD0 (t); |
|
|
|
|
|
|
|
|
|
|
|
|
|
|
||||||||||||||||||||||||
|
по продуктам разложения (σ, χ) : |
|
|
|
|
|||||||||||||||||||||||||||||||||||
|
∂cσ |
−W3 |
(cAK , |
T ) = |
∂cσ |
|
|
|
|
|
|
|
|
|
|
|
|
0 |
|
|
|
|
|
|
0 |
|
||||||||||||||
ϑ |
|
|
|
|
|
|
; |
|
cσ |
(l, 0) = cσ (l); |
cσ (0, t) = cσ (t); |
|
||||||||||||||||||||||||||||
∂l |
∂t |
|
|
|
|
|||||||||||||||||||||||||||||||||||
ϑ |
∂cχ |
−W |
4 |
(c |
AK |
, |
c |
D |
, T ) |
−W |
|
(c |
D |
, T ) |
= |
|
∂cχ |
; |
|
|
|
|
|
|
||||||||||||||||
|
|
|
|
|
|
|
|
|
|
|
|
|
||||||||||||||||||||||||||||
|
∂l |
|
|
|
|
|
|
|
|
|
5 |
|
|
|
|
|
|
|
∂t |
|
|
|
|
|
|
|
|
|
||||||||||||
|
|
|
|
|
|
|
|
|
|
|
|
|
|
|
|
|
|
|
|
|
|
|
|
|
|
|
|
|
|
|
|
|
|
|
|
|
|
|||
cχ (l, 0) = cχ0 (l); |
|
cχ (0, t) = cχ0 (t). |
|
|
|
|
|
|
|
|
|
|
|
|
|
|
|
(3.70)
(3.71)
(3.72)
(3.73)
Составим теперь уравнение динамики для фракции частиц амина, характеризующихся размером от r до r + dr на участке трубы (l1, l2 ) за время (t1 , t2 ) :

t∫2 [N(l2 , t)ψ(l2 , t, r)dr − N(l1 , t)ψ(l1 , t, r)dr]dt +
t1
+ 1v t∫2 l∫2 N(ξ, t)[ψ(ξ, t, r)W1(r) (ξ, t, r) −ψ(ξ, t, r + dr)W1(r) (ξ, t, r + dr)]=
t1 l1
= 1v l∫2 [N (ξ, t2 )ψ(ξ, t2 , r)dr − N(ξ, t1 )ψ(ξ, t1 , r)dr]dξ,
l1
которое с использованием приведенной выше техники можно преобразовать к уравнению вида:
|
∂ψ(l, t, r) |
|
∂ |
ˆ |
(r) |
(l, t, r)]= |
∂ψ(l, t, r) |
|
|
v |
∂l |
− |
∂r |
[ψ(l, t, r)W1 |
∂t |
; |
(3.74) |
||
ψˆ (0, t, r) = ψˆ (0) (t, r); |
ψˆ (l, 0, r) = ψˆ (0) (l, r). |
|
|
Получим теперь уравнения динамики теплообмена в трубчатом реакторе по реакционной сме-
си:
t2 |
t2 l2 |
|
c p ρ∫ |
[T (l2 , t) −T (l1 , t)]dτ+ ∫∫ |
[− hSW2 (ξ, t) + K1πD[T (ξ, t) −Tx (ξ, t)]]dξdt = |
t1 |
t1 l1 |
|
l2
= c p ρS ∫[T (ξ, t2 ) −T (ξ, t1 )]dξ;
по хладагенту (х): l1
t2 |
t2 l2 |
|
c pxρxGx ∫ |
[Tx (l2 , t) −Tx (l1, t)]dt − ∫∫[K1πD[T (ξ, t) −Tx (ξ, t)]]dξdt = |
|
t1 |
t1 l1 |
|
|
l2 |
[T (ξ, t2 ) −Tx (ξ, t1 )]dξ. |
|
= c px ρx S p ∫ |
|
|
l1 |
|
Проводя рассуждения аналогичные предыдущим, получим уравнения:
cp |
ρGl |
∂T (l, t) |
− hSW2 (l, t) + K1πD[T (l, t) −Tx (l, t)]= cpρS |
∂T (l, t) |
; |
||||||
|
|
||||||||||
|
|
|
∂l |
|
|
|
|
|
∂t |
|
|
T (l, 0) = T 0 (l); T (0, t) = T 0 (t); |
|
|
|
|
|||||||
c px ρxGx ∂Tx (l, t) |
− K1πD[T (l, t) −Tx (l, t)]= c pxρx S p |
∂Tx (l, t) |
; |
|
|||||||
|
|
|
∂l |
|
|
|
∂t |
|
|
||
T |
x |
(l, 0) = T 0 (l); |
T |
x |
(0, t) = T L (t); |
|
|
|
|
||
|
|
χ |
|
x |
|
|
|
|
(3.75)
(3.76)
Таким образом, уравнения динамики непрерывного процесса диазотирования в трубчатом реакторе представляют собой нелинейные дифференциальные уравнения в частных производных первого порядка, для решения которых можно использовать метод характеристик или конечноразностные методы [33].
Уравнения статики легко получить из выведенной системы уравнений динамики приравниванием нулю производной по времени, т.е.
∂∂ct = 0; ∂∂Tt = 0; ∂∂ψt = 0.
Математическая модель статики процесса диазотирования, осуществляемого в трубчатом реакторе, представляет собой систему нелинейных обыкновенных дифференциальных уравнений
(3.69) – (3.76).
Наибольшую сложность при решении системы дифференциальных уравнений, описывающих статические режимы диазотирования, представляет уравнение, описывающее гранулометрический состав твердой фазы амина в l -ом сечении трубчатого реактора
ϑ |
∂ψˆ (l, r) |
= |
∂ |
ψˆ |
(r) |
(l, r)], |
|
||
|
|
∂l |
∂r |
[ |
(l, r)W1 |
(3.77) |
|||
ψˆ (0, r) = ψˆ (0) (r). |
|
|
|
||||||
|
|
В случае линейного уравнения кинетики растворения частицы амина [138] |
|||||||
dr |
= −A r −α exp (− E1 / RT )(c*A −cA )/ ρA , |
(3.78) |
|||||||
dt |
|||||||||
|
|
|
|
|
|
|
где A, α - кинетические константы; c*A , cA - равновесная и текущая концентрации амина; ρA - плотность амина.
Решение уравнения (3.15) может быть получено методом характеристик в аналитическом виде [33]. Решение уравнения (3.78) запишем в виде
|
|
|
|
|
|
|
1 |
|
||
|
|
|
|
|
l |
|
|
1+α |
|
|
|
|
|
|
|
∫A exp (−E1 / RT )(c*A −cA ) |
|
|
|
||
|
|
|
r α+1 |
|
0 |
~ |
, |
|||
r(l) = |
f (r , l) = |
|
−(1+ α) |
dl |
|
|||||
|
||||||||||
|
0 |
0 |
|
ρA ϑ |
|
|
||||
|
|
|
|
|
|
|
|
|||
|
|
|
|
|
|
|
|
|
||
|
|
|
|
|
|
|
|
|
откуда можно рассчитать начальный радиус r0 частицы по формуле
r0 = f1 (r, l) = r
|
|
1 |
|
||
|
l |
|
1+α |
|
|
|
∫A exp (−E1 / RT )(c*A −cA ) |
|
|||
|
0 |
~ |
|||
α+1 + (1+ α) |
dl . |
||||
ρA v |
|||||
|
|
||||
|
|
|
|||
|
|
|
В этом случае решение уравнения (3.77) с начальным условием может быть записано в следующем виде [33]:
|
ˆ |
ˆ |
(0) |
|
l |
∂W (r ) |
~ |
~ ~ |
|
||
|
|
|
∫ |
1 |
[r(l , f1 |
(r, l ))]dl , |
(3.79) |
||||
ψ(r |
, l) = ψ |
|
( f1 |
(r, l)) exp |
|
||||||
|
∂r |
||||||||||
|
|
|
|
|
|
|
|
|
|
||
|
|
|
|
|
|
|
0 |
|
|
|
|
|
|
|
В случае нелинейного уравнения кинетики растворения частицы, например, в виде |
||||||||
|
dm |
|
= −β* (c*A −c A ) S , |
|
|
|
|
|
|||
|
dt |
|
|
|
|
|
|||||
|
|
|
|
|
|
|
|
|
|
||
где β - эффективный коэффициент массоотдачи; |
S - поверхность частицы, необходимо использо- |
вать численный алгоритм решения уравнения (3.77). Аппроксимируя дифференциальные уравнения в частных производных (3.77) конечной системой дифференциальных уравнений в обычных производных с использованием конечно-разностной схемы первого порядка, получим
dψˆ |
i |
r |
+ r |
|
|
|
|
|
ψˆ |
i |
− ψˆ |
i−1 |
|
|
∂W (r) |
|
|
|
|
|
|
||
|
= W (r) |
i |
i−1 |
, c |
|
, c |
|
|
|
|
|
|
− |
1 |
(r , c |
|
, c |
|
)ψ |
, |
|||
dl |
|
|
2 |
|
|
|
|
∆r |
|
∂r |
|
|
|||||||||||
|
1 |
|
A |
|
AK |
|
|
|
|
|
i |
A |
|
AK |
i |
|
|||||||
|
|
|
|
|
|
|
|
|
|
|
|
|
i |
|
|
|
|
|
|
|
|
|
|
|
|
ψˆ 1 (0) = ψˆ (0) (ri , l), ∆ri |
- шаг сетки. |
|
|
|
|
|
|
(3.80) |
Полученная система обыкновенных дифференциальных уравнений (3.80) одновременно с другими уравнениями модели может быть решена каким-либо численным методом. При этом могут возникнуть сложности, поскольку в начальной фазе процесса диазотирования скорость растворения твердой фазы и скорость реакции диазотирования различаются на несколько порядков, т.е. система дифференциальных уравнений математической модели процесса диазотирования является жесткой. В этом случае явные методы Рунге-Кутта исключаются из рассмотрения.
Для решения системы дифференциальных уравнений модели статики процесса диазотирования мы применяли два метода: неявный метод трапеций [34] и метод Дормана-Принса 5-го порядка
точности с автоматическим выбором шага [35], которые дают вполне сопоставимые результаты и обеспечивают получение решения с заданной точностью.
Математическая модель динамики процесса диазотирования, осуществляемого в турбулентном трубчатом аппарате, включает нелинейные дифференциальные уравнения с частными производными (3.69) – (3.76), для решения которых использовали конечно-разностный метод [11].
Для математического описания процесса диазотирования, осуществляемого в турбулентном трубчатом реакторе комбинированного типа, необходимо к уравнениям (3.69) – (3.76) добавить уравнения, описывающие протекание процесса диазотирования в камере смешения [23].
Математическое описание процесса азосочетания
При моделировании процесса азосочетания примем следующие допущения: 1) собственно реакция азосочетания протекает в растворе; 2) влияние изменения температуры вследствие экзотермической реакции на протекание химических процессов внутри модулей считается несущественным; 3) расчет гранулометрического распределения кристаллов азопигментов состоит в вычислении дискретных значений числа кристаллов, принадлежащих тому или иному диапазону размеров из всего возможного интервала изменения размеров кристаллов, определяемого по экспертным оценкам; 4) кислотность среды сочетания, обеспечивается на практике подачей в аппарат раствора углекислого натрия (соды); 5) учет расходов нейтрализующего агента и воды в питании модуля осуществляется путем пересчета общего расхода потока реакционной среды в реакторной системе.
Как показали экспериментальные исследования, одинаковое время пребывания частиц в трубчатом реакторе обеспечивается при развитом турбулентном режиме течения потока, который достигается при значениях Рейнольдса Re >10 000 . При этом длина трубчатой части реактора оп-
ределяется необходимым временем пребывания в нем реакционной массы и роста кристаллов пигмента.
Процесс азосочетания, осуществляемый в турбулентном трубчатом реакторе, описывается вектором концентраций взаимодействующих компонентов c(l, t) и гранулометрическим составом
f (r, l, t) кристаллов пигмента. Проводя рассуждения аналогичные рассуждениям при выводе мо-
дели диазотирования и учитывая, что в результате реакции протекает процесс кристаллизации пигмента уравнения покомпонентного материального баланса при допущении идеального вытеснения вдоль оси реактора можно записать в следующем виде:
по азосоставляющей (Az):
V |
∂cAz |
+WAz (cAz , cD , pH ) = |
∂cAz |
; |
|
|
∂l |
|
|
(3.81) |
|||
|
|
∂t |
|
|||
cAz (0, t) = c(Az0) ; |
|
|
|
|
||
|
по диазосоставляющей (D): |
|
|
|||
|
ϑ |
∂cD +WAz (cAz , cD , pH ) +Wp (cD , pH ) = |
∂cD ; |
(3.82) |
||
|
|
∂l |
|
|
∂t |
cD (0, t) = cD(0) ;
по продуктам разложения ( χ ) диазосоединения:
|
∂cχ |
|
(3.83) |
|
ϑ |
−Wp (cD , pH ) = |
∂cχ |
; |
|
|
|
|||
|
∂l |
∂t |
cχ (0, t) = cχ(0) ;
по пигменту в жидкой фазе:
ϑ |
∂cП |
−WAz (cAz , cD , pH ) +Wкp (cП ) = |
∂cП |
; |
(3.84) |
|
|||||
∂l |
∂t |
|
|||
|
|
|
|
cП (0, t) = 0;
где l – текущая длина; ϑ – линейная скорость движения потока реакционной массы; cAz , cD , cχ , cП
– концентрации азосоставляющей, диазосоставляющей, продуктов разложения диазосоединения (диазосмол) и пигмента в жидкой фазе, соответственно; Wкр – скорость перехода пигмента из жид-
кой фазы в твердую в результате кристаллизации.
По твердой фазе пигмента:
ϑ |
∂fˆ(l, t, r) |
− |
|
∂ |
|
[fˆ(l, t, r)η(l, t, r)]= |
∂fˆ(l, t, |
r) |
(3.85) |
|||
|
|
; |
||||||||||
∂l |
|
∂r |
|
∂t |
|
|||||||
|
|
|
|
|
|
|
|
|
||||
ˆ |
|
ˆ |
(0) |
(t, r); |
ˆ |
ˆ (0) |
(l, r). |
|
|
|||
f (0, t, r) = |
f |
|
|
f (l, 0, r) = |
f |
|
|
|
Уравнения статики процесса азосочетания можно получить из записанной выше системы дифференциальных уравнений приравнивая нулю производные по времени. Математическая модель статики процесса азосочетания, осуществляемого в турбулентном трубчатом реакторе, представляет собой систему нелинейных дифференциальных уравнений в обыкновенных производных (за исключением дифференциального уравнения в частных производных (3.85)). Уравнение (3.85) является нелинейным, так как скорость роста кристаллов пигмента алого описывается нелинейным уравнением вида [24]:
dr |
=η(cП ) = |
1 |
, |
|
dt |
(ηK−1 +ηD−1 ) |
|||
|
|
ηK = kK (cП − c*П )NK =1,91 10−5 (cП − c*П )1,82 ,
ηД = D(cП − c*П ) /(ρП r) = 5,81 10−14 (cП − c*П ) / r,
где cП , c*П – текущая и равновесная концентрация пигмента в растворе; D – коэффициент диффузии; ρП – плотность пигмента; ηK , ηD –скорости роста кристаллов в диффузионной и кинетиче-
ской областях.
В связи с этим аппроксимируем дифференциальное уравнение в частных производных конечной системой дифференциальных уравнений в обыкновенных производных с использованием конечно-разностной схемы первого порядка (аналогичной 3.80).
Полученная таким образом система нелинейных обыкновенных дифференциальных уравнений, описывающая статические режимы азосочетания в турбулентном трубчатом реакторе, может быть решена стандартными численными методами. Однако и в этом случае могут возникнуть трудности, связанные с явлением "жесткости", что предопределяет использование неявных методов интегрирования: метода трапеций [341] и метода Дормана-Принса 5 порядка точности.
Математическая модель динамики процесса азосочетания, осуществляемого в турбулентном трубчатом реакторе, включает нелинейные дифференциальные уравнения с частными производными (3.81) – (3.85), длярешения которых применяли конечно-разностный метод [11].
Экспериментальные исследования процесса азосочетания показали, что осуществление процесса азосочетания при синтезе пигментов с высокой точностью обеспечивается в турбулентных реакторах цилиндрического типа, горизонтального типа. Это обстоятельство позволило нам отказаться от исследования процесса азосочетания в более сложном трубчатом аппарате комбинированного типа.
Алгоритм компьютерного моделирования процессов диазотирования и азосочетания
Рассмотрим алгоритм математического моделирования процессов диазотирования и азосочетания при синтезе азопигмента алого (см. блок-схему на рис. 3.23).
Вблоке 1 осуществляется задание облика реактора, указывается конструктивное оформление
ичисло унифицированных модулей реакторов, задаются конструктивные размеры модулей и всего аппарата.
Вблоках 3а, б, в и 4 в зависимости от выбранного типа модулей формируются управляющие параметры программы расчета статических и динамических режимов процессов диазотирования
иазосочетания, в соответствии с которыми определяется последовательность расчета модулей аппарата и подбираются требуемые алгоритмы.
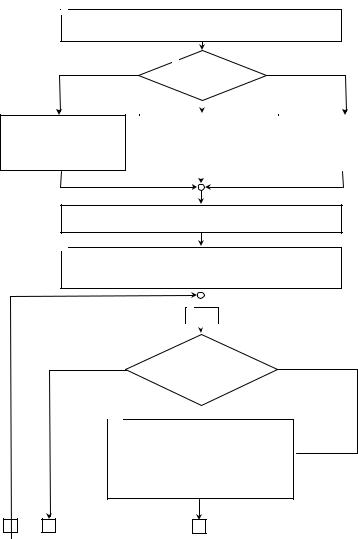
1
Формирование облика турбулентного трубчатого реактора, задание конструктивных параметров и числа модулейN
I |
2 |
Какие |
III |
|
модули включает |
||||
|
|
реактор?
3а
Модуль-реактор цилиндрического типа (в горизонтальном или вертикальном исполнении)
4
|
|
II |
|
|
|
3б |
|
|
3в |
|
|
|
|
|
|
||
|
|
|
|
|
|
Модуль-реактор диффу- |
|
Модуль-реактор комби- |
|||
|
нированного типа “труба- |
||||
|
зор-кофузорного типа |
|
|||
|
|
|
камера смешения” |
||
|
|
|
|
|
|
|
|
|
|
|
|
|
|
|
|
|
|
Формирование управляющих параметров программы
1'→< i >
5
Ввод исходных данных: кинетических параметров, физикохимических свойств веществ, переменных, определяющих условия осуществления процесса и др.
6
|
|
|
|
l := ∆l |
|
|
|
|
|
|
|
|
|
||
|
|
|
Проводится |
|
|||
|
|
7 |
|
||||
|
|
Динамика |
|||||
|
|
|
|||||
Статика |
исследование статиче- |
||||||
|
|
|
|
|
|
|
|
ских или динамических режимов?
16
Формирование начальных условий и решение диф. уравнений с частными производными (3.69)-(3.76), (3.81)-
(3.85) методом конечных разностей или после преобразований с использованием метода Дормана-Принса
С |
A |
B |
Рис. 3.23 Блок-схема алгоритма расчета статических и динамических режимов процессов диазотирования и азосочетания, осуществляемых в турбулентных реак-
торах трубчатого типа: (3.69) – (3.76), (3.81) – (3.85)