
108 Carbon, Graphite, Diamond, and Fullerenes
5.0
" 4.0 cl
+-
z 3.0
P
0 2.0
I I I I I I I I I
1.0
L |
I |
I |
I |
I |
I |
I |
I I |
I |
OO |
|
400 |
|
800 |
|
1200 |
1600 |
2000 |
Temperature, “C
Figure 5.9. Average coefficient of thermal expansion (CTE) of graphite as a function of temperature.
Table 5.8. Thermal Expansion of Typical Molded Graphite and Other
Materials
|
|
|
CTE |
|
|
m/m*% x 10e6 |
|
Material |
(100 |
- 600°C) |
|
Extruded |
Graphite |
|
|
with grain |
1.8 - 2.9 |
||
across grain |
3.2 - 5.0 |
||
lsostatic |
Graphite |
3.2-5.7 |
|
Aluminum |
|
23.5 |
(@ 25%) |
Copper |
|
16.6 |
(@ 25°C) |
Tungsten |
|
4.5 |
(@ 25°C) |
|
|
|
|
|
|
|
|
|
|
|
|
|
|
|
Molded Graphite |
107 |
|||||||
|
The |
thermal |
expansion |
|
of molded |
graphite |
is an |
important |
|
property |
|||||||||||||
since |
many |
applications |
involve |
high |
temperature, |
and |
expansion |
values |
|||||||||||||||
must |
be known |
accurately. |
|
|
|
|
|
|
|
|
|
|
|
|
|
|
|
||||||
|
Thermal Shock. The low modulus, |
high thermal |
conductivity, |
|
and |
low |
|||||||||||||||||
thermal |
expansion |
combine |
to give molded graphite |
excellent |
thermal-shock |
||||||||||||||||||
resistance. |
|
It is difficult to |
rupture |
the |
material by thermal |
shock alone. |
|
||||||||||||||||
3.7 |
Electrical |
Resistivity |
|
|
|
|
|
|
|
|
|
|
|
|
|
|
|
||||||
|
The |
electrical |
resistivity |
of the graphite |
crystal |
was |
reviewed |
|
in Ch. 3, |
||||||||||||||
Sec. |
5. |
The |
crystal |
has a high |
degree |
of electrical |
anisotropy |
with |
resistivity |
||||||||||||||
that is low |
in the |
ab directions |
and |
high in the |
c direction. |
Molded |
graphites |
||||||||||||||||
(even |
the |
isostatically |
molded |
material |
where |
the |
crystallites |
|
are essentially |
||||||||||||||
random) |
have higher |
resistivity |
than the single-crystal |
in the |
ab directions, |
||||||||||||||||||
but can |
still |
be considered |
|
electrical |
conductors. |
|
|
|
|
|
|
|
|
|
|||||||||
|
Table |
5.9 |
lists typical |
electrical-resistivity |
values |
of |
several |
|
molded |
||||||||||||||
carbons |
and graphites |
and |
selected |
low-resistivity |
metals. |
|
|
|
|
|
|||||||||||||
Table 5.9. |
Electrical |
Resistivity |
of Molded |
Graphite |
and |
Selected |
Metals |
||||||||||||||||
|
|
|
|
|
|
|
|
|
|
|
|
|
Electrical |
Resistivity |
|
|
|
||||||
|
|
|
|
Material |
|
|
|
|
|
|
|
at 25°C j&J-m |
|
|
|
||||||||
|
|
Molded |
carbon |
|
|
|
|
|
|
|
- |
50 |
|
|
|
|
|
|
|||||
|
|
Electrographite |
(from |
petroleum |
coke) |
|
|
7.6 |
|
|
|
|
|
|
|||||||||
|
|
Electrographite |
(from |
lampblack) |
|
|
|
30.5 |
|
|
|
|
|
|
|||||||||
|
|
Pyrolytic |
graphite |
(ab |
direction) |
|
|
2.5 |
- 5.0 |
|
|
|
|
|
|||||||||
|
|
Aluminum |
|
|
|
|
|
|
|
|
|
|
|
0.026 |
|
|
|
|
|
||||
|
|
Copper |
|
|
|
|
|
|
|
|
|
|
|
|
0.017 |
|
|
|
|
|
|||
|
|
Tungsten |
|
|
|
|
|
|
|
|
|
|
|
0.056 |
|
|
|
|
|
||||
|
|
Silver |
|
|
|
|
|
|
|
|
|
|
|
|
0.016 |
|
|
|
|
|
The values listed above for the molded carbons and graphites are averages and may vary depending on the raw materials, the process, and the degree of graphitization.
108 Carbon, Graphite, Diamond, and Fullerenes
The electrical resistivity of |
molded |
graphite, like that |
of the graphite |
||
crystal and metals, |
increases |
with temperature, |
above |
approximately |
|
4OO”C, and the material has the |
positive |
temperature coefficient of resis- |
|||
tance which is typical |
of metals. |
Below |
4OO”C, the |
coefficient is usually |
slightly |
negative. At high temperature, graphite becomes a better conduc- |
torthan |
the most-conductive refractory metal. The effect of temperature on |
the relative resistivity of molded graphite is shown graphically in Fig. 5.1 0.t3]
5 |
I |
|
|
|
|
|
= 0.5 - |
1 |
|
|
|
|
|
|
I |
|
|
|
|
|
|
I |
|
|
|
|
|
|
1 |
i |
I |
I |
I |
I |
-273 |
0 |
500 |
1000 |
1500 |
2000 |
2500 |
|
|
|
Temperature, |
“C |
|
Figure 5.10. Relative variation of electrical resistivity of molded graphite as a function of remperature.[121
3.8Emissivity
Emissivity is the ratio of the energy radiated by a body to that radiated
by an equal areaof a perfect black body. According to the Stefan-Boltzmann law, a perfect black body is an ideal material which radiates the maximum
amount of energy. The emissivity of a material depends |
on its structure and |
|
on its surface |
conditions. |
|
Molded |
graphite, being black, has high emissivity, |
which is an impor- |
tant advantage in high-temperature applications. Table |
5.10 lists the total |
emissivity of several carbon and graphite materials and selected metals for comparison.t131
Molded Graphite 109
Table 5.10. Emissivity of Carbon and Graphite Materials and Selected
Metals
Material |
Total Emissivity |
||
Graphite |
(petroleum-coke base) |
0.70 |
- 0.90 |
Graphite |
(lampblack base) |
0.85 |
- 0.95 |
Molded |
Carbon |
0.60 |
- 0.80 |
Lampblack |
0.90 |
- 0.99 |
Silver |
0.04 |
Nickel, oxidized |
0.87 |
Tungsten, polished |
0.15 |
4.0 |
APPLICATIONS |
|
AND |
MARKET |
OF MOLDED |
GRAPHITE |
|
|
|||||||||||||||||||
4.1 |
General Considerations |
|
|
|
|
|
|
|
|
|
|
|
|
|
|
|
|
|
|||||||||
|
The |
technology |
|
of molded |
graphite is versatile, |
|
improvements |
in the |
|||||||||||||||||||
manufacturing |
techniques |
are continuously |
made |
and the scope |
of applica- |
||||||||||||||||||||||
tions |
is gradually |
expanding. |
This |
expansion |
is the |
direct |
result |
of asizeable |
|||||||||||||||||||
research |
effort |
carried out by |
many |
|
workers |
|
in universities, |
government |
|||||||||||||||||||
laboratories, |
and |
industry. |
|
|
|
|
|
|
|
|
|
|
|
|
|
|
|
|
|
|
|||||||
|
In the |
last |
twenty |
years |
or |
so, |
several |
major applications |
|
of molded |
|||||||||||||||||
graphite |
|
have developed |
into an important, |
complex, |
and diverse |
industrial |
|||||||||||||||||||||
market. |
|
Because |
of this |
diversity, |
|
the |
classification |
|
of these |
applications is |
|||||||||||||||||
a critical |
factor |
if a proper perspective |
of the |
industry |
is to |
be |
obtained. |
||||||||||||||||||||
|
The |
classification |
by product |
function |
is the |
primary |
one |
used |
in this |
||||||||||||||||||
book. |
It is |
used |
in this |
chapter |
|
for |
molded |
graphite |
and |
|
in the |
following |
|||||||||||||||
chapters |
for the |
other |
main |
types |
of |
carbon |
|
and |
graphite |
|
materials, |
i.e., |
|||||||||||||||
polymeric, |
pyrolytic, |
fibers, carbon-carbon |
and |
powders. |
it is based on the |
||||||||||||||||||||||
following |
major |
functions: |
electrical, |
|
structural |
and |
mechanical, |
chemical |
|||||||||||||||||||
and |
refractory, |
and |
nuclear. |
These |
functions |
|
corresponds |
|
roughly |
to the |
|||||||||||||||||
various |
segments |
of industry |
and |
end-use |
market, |
such |
as electronic |
and |
|||||||||||||||||||
semiconductor, |
metal |
processing, |
|
chemicals, |
|
automobile, |
and |
aerospace. |
|||||||||||||||||||
|
The |
world |
|
market |
for |
molded |
graphite |
|
is large |
as |
shown |
in |
Table |
||||||||||||||
5.11 ?I |
|
|
|
|
|
|
|
|
|
|
|
|
|
|
|
|
|
|
|
|
|
|
|
|
|
|
110 Carbon, Graphite, Diamond, and Fuiierenes
Table 5.11. Estimated World Market for Molded Graphite in 1991
|
($ |
millions) |
Steel Production |
|
|
Electrodes |
2250 |
|
Aluminum |
Production |
|
Anodes |
940 |
|
Cathodes |
250 |
|
Specialty |
Graphites |
300 |
Total |
|
3740 |
The specialty graphites listed in the table include the molded graphites produced for semiconductor, electrical, chemical, nuclear, biomedical, mechanical, and aerospace industries.
4.2Applications in the Metal Processing industry
|
|
Electrodes for the Production |
of Electric-Arc Steel. As shown |
in |
|||||||||||||||||||
Table |
5.11, the production |
of electrodesfor |
steel |
and aluminum |
processing |
||||||||||||||||||
is the |
largest |
application |
of molded graphite, |
in terms of both tonnage |
and |
||||||||||||||||||
dollars. |
|
As |
mentioned |
in |
Sec. |
1.1, |
electrodes |
are one of the original |
|||||||||||||||
applications |
and |
|
have |
been |
manufactured |
with |
essentially |
the |
|
same |
|||||||||||||
process |
for almost |
a century. |
|
|
|
|
|
|
|
|
|
|
|
|
|
||||||||
|
|
The |
|
largest |
use |
of these |
electrodes |
is |
in |
the |
production |
of |
steel |
in |
|||||||||
electric-arc furnaces, mostly |
for the reclamation |
of ferrous |
scrap.t’) |
These |
|||||||||||||||||||
electrodes |
must |
have |
good |
electrical |
conductivity, good refractory |
|
proper- |
||||||||||||||||
ties, |
and low cost. They gradually |
erode in use and at times break |
altogether |
||||||||||||||||||||
and |
must |
be replaced |
at regular |
intervals. |
|
|
|
|
|
|
|
|
|
||||||||||
|
|
The |
|
worldwide |
production |
of steel is slowly |
increasing, |
but the |
produc- |
||||||||||||||
tion |
of electric-arc |
|
furnace |
steel |
is increasing |
at a more rapid |
rate. |
This rate |
|||||||||||||||
reached |
28% |
of total |
production |
|
in 1990 |
as shown |
in Fig. 5.11. |
The |
major |
||||||||||||||
producers |
by area |
are Europe, |
North |
America, |
and |
Japan. |
|
|
|
|
|
|
Molded Graphite |
111 |
. |
. |
. |
. |
1 |
I |
I |
I |
1 |
8 |
|
|
|
7Total |
|
|
||
7 |
|
|
|
|
|
|||
6 |
|
|
|
|
|
|||
|
|
|
|
Steel |
Production |
|
||
5 |
|
|
|
|
|
|
|
|
4 |
|
|
|
Electrical |
Steel |
|
||
3 |
|
|
|
|
||||
|
|
|
|
|
|
|
|
|
2 |
|
|
|
|
|
|
|
|
|
1981 |
|
1982 |
|
1984 |
|
|
|
1986 |
|
|
1988 |
|
1990 |
|
|||||
|
|
|
|
|
|
|
|
|
|
|
Year |
|
|
|
|
|
|
|
||
Figure 5.11. World |
production |
of steel.[‘] |
|
|
|
|
|
|
|
|
|
|||||||||
The |
gradual |
increase |
in electric-arc |
steel |
production |
does |
not |
neces- |
||||||||||||
sarily translate |
into a gradual increase |
in the tonnage |
of graphite |
electrodes. |
||||||||||||||||
In fact the |
opposite |
is |
happening |
and |
the |
total |
consumption |
of graphite |
||||||||||||
electrodes |
is decreasing |
(Fig. 5.12) |
|
due to a pronounced |
decrease |
in the |
||||||||||||||
consumption of |
graphite |
per |
ton |
of |
|
electric |
steel |
produced. |
In 1975, |
an |
||||||||||
average |
of 7.5 |
kg of molded |
graphite |
was |
required |
to produce |
one |
ton |
of |
|||||||||||
electric-arc |
steel. |
In 1990, this |
amount had dropped |
to 5 kg. The downward |
||||||||||||||||
trend is continuing. |
|
|
|
|
|
|
|
|
|
|
|
|
|
|
|
|
||||
This |
|
reduction |
is the result |
of |
two |
factors: |
(a) improvements |
of the |
||||||||||||
properties |
|
of the |
graphite |
materials, |
particularly |
a considerable |
reduction |
of |
||||||||||||
the thermal |
expansion |
and resulting |
|
increase in thermal-shock |
resistance, |
|||||||||||||||
and (b) improvements |
in arc-furnace |
|
operating |
|
techniques. |
|
|
|
|
112 Carbon, Graphite, Diamond, and Fullerenes
|
I. |
I ..I.. |
. |
* I |
1975 |
1980 |
|
1985 |
1990 |
|
|
Year |
|
|
Figure 5.12. Consumption of graphite in the production of steel.t’t
|
Electrodes |
for |
Aluminum |
Production. |
Aluminum |
is |
processed |
|||||||||||||||||
electrolytically |
|
and |
the |
production |
|
of |
the |
|
necessary |
|
electrodes |
is |
the |
|||||||||||
second-largest |
|
application |
of molded |
graphite |
(see Table |
5.11 |
above)!‘] |
|||||||||||||||||
The anodes |
are similar |
to those |
used |
in electric-arc |
steel production |
and are |
||||||||||||||||||
also |
manufactured |
from |
petroleum-coke |
|
filler |
and |
coal-tar |
pitch. |
The |
|||||||||||||||
aluminum |
collects |
at |
the |
cathodes |
|
which |
are |
large |
blocks |
lining |
the |
|||||||||||||
electrolytic |
cell. |
These |
cathodes |
were |
originally |
made |
of baked |
carbon |
||||||||||||||||
based on anthracite |
coal |
but, in recent |
years, |
have |
been |
upgraded |
and |
are |
||||||||||||||||
now |
made |
of molded |
graphite |
from |
petroleum |
coke. |
|
|
|
|
|
|
|
|||||||||||
|
The world |
production |
|
of aluminum |
was |
|
estimated |
at 14.2 x 1O6metric |
||||||||||||||||
tons |
in 1990. |
The consumption |
of molded-graphite |
anode |
is approximately |
|||||||||||||||||||
400 kg per metric ton of aluminum |
|
and |
the |
total |
estimated |
consumption |
||||||||||||||||||
worldwide |
is 5.68 x 1O6 metric |
tons. |
|
|
|
|
|
|
|
|
|
|
|
|
|
|
||||||||
|
Melting, |
Smelting, |
and |
Casting |
|
of |
Metals. |
Molded |
graphite |
has |
||||||||||||||
numerous applications |
in the processing |
of ferrous and non-ferrous |
metals |
|||||||||||||||||||||
and alloys such |
as |
copper, |
copper-nickel, |
brass, |
bronze, |
zinc, |
aluminum |
|||||||||||||||||
alloys, nickel |
and its alloys, precious |
metals, |
and grey and ductile |
irons.t31t151 |
||||||||||||||||||||
The |
wide variety |
of these |
applications |
|
is shown |
in the |
following |
partial |
list: |
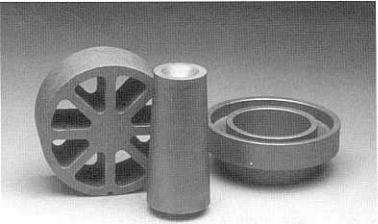
|
|
|
|
|
|
|
|
|
|
|
|
Molded |
Graphite |
113 |
|||
|
|
.Moldsfor |
centrifugal |
casting of brass and bronze bushings |
|
||||||||||||
|
|
|
and sleeves |
|
|
|
|
|
|
|
|
|
|
|
|
||
|
|
.Molds |
for pressure casting |
of steel slab and railroad-car |
|
||||||||||||
|
|
|
wheels |
|
|
|
|
|
|
|
|
|
|
|
|
|
|
|
|
.Dies for continuous |
casting |
and |
extrusion |
of aluminum |
|
||||||||||
|
|
|
and other non-ferrous |
metals |
|
|
|
|
|
|
|
||||||
|
|
.Extrusion |
guides and run-out |
tables |
|
|
|
|
|
||||||||
|
|
.Hot-pressing |
molds |
and plungers |
|
|
|
|
|
|
|||||||
|
|
.Pumps |
for molten aluminum |
and zinc |
|
|
|
|
|
||||||||
|
|
.Brazing |
fixtures |
|
|
|
|
|
|
|
|
|
|
|
|||
|
|
.Furnace |
linings |
|
|
|
|
|
|
|
|
|
|
|
|||
|
|
.Sintering |
boats and trays |
|
|
|
|
|
|
|
|
||||||
|
The factors |
to consider in selecting |
a suitable |
grade |
of molded |
grahite |
|||||||||||
for |
metal |
processing |
are: high thermal |
conductivity |
to reduce |
the thermal |
|||||||||||
stresses; |
high hardness to reduce |
abrasive |
wear and improve |
the |
lifetime |
||||||||||||
of |
the |
die; and |
high |
density, |
fine |
grain, |
and low |
porosity |
to minimize |
||||||||
chemical |
attack |
by molten metals |
and |
by dissolved |
atomic |
oxygen (the |
|||||||||||
latter |
especially |
found |
in nickel |
and |
its alloys) .Fig. |
5.13 shows |
typical |
||||||||||
molded-graphite |
casting dies. |
|
|
|
|
|
|
|
|
|
|
|
Figure 5.13. Examples of graphite casting dies. (Photograph courtesy of Sigri
Great Lakes Carbon Corp., Niagara Falls, NY.)
114 |
Carbon, |
|
Graphite, |
Diamond, |
and Fullerenes |
|
|
|
|
|
|
|
|
||||||||||||||||
4.3 |
Semiconductor |
and |
Related |
|
Applications |
|
|
|
|
|
|
|
|
|
|
||||||||||||||
|
In 1947, |
Bardeen, |
Brattain, and Shockley |
of Bell |
Telephone |
Labora- |
|||||||||||||||||||||||
tories |
demonstrated |
the transistor |
function with |
alloyed |
germanium |
and this |
|||||||||||||||||||||||
date |
is generally |
recognized |
|
as the |
start |
of the solid-state |
semiconductor |
||||||||||||||||||||||
industry. |
The |
era |
of |
integrated |
circuits |
(IC’s) |
was |
inaugurated |
|
in |
1959, |
||||||||||||||||||
when, |
for the |
first |
time, several |
components |
were |
placed |
|
on a single |
chip |
||||||||||||||||||||
at Texas |
Instruments. |
|
|
|
|
|
|
|
|
|
|
|
|
|
|
|
|
|
|
|
|
|
|||||||
|
These |
developments |
resulted |
in a drastic |
price |
reduction |
in all aspects |
||||||||||||||||||||||
of solid-state |
|
circuitry |
and the cost |
per unit of information |
(bit) |
has |
dropped |
||||||||||||||||||||||
by an estimated |
three |
orders |
of magnitude |
in the last twenty years. This |
cost |
||||||||||||||||||||||||
reduction |
been |
accompanied |
|
by a similar |
decrease |
in size, |
|
and today |
circuit |
||||||||||||||||||||
integration |
|
has |
reached |
the |
|
point where |
more |
than |
a million |
components |
|||||||||||||||||||
can be |
put |
on a single |
chip. |
|
|
|
|
|
|
|
|
|
|
|
|
|
|
|
|
|
|
|
|||||||
|
This |
progress |
is largely |
|
due to the development |
of glass |
and ceramic |
||||||||||||||||||||||
fabrication |
techniques, single-crystal production |
processes, |
and |
thin-film |
|||||||||||||||||||||||||
technologies |
|
such |
as evaporation, |
sputtering |
and |
chemical vapor |
deposi- |
||||||||||||||||||||||
tion (CVD). These advances |
were |
made |
possible |
in part |
by the |
availability |
|||||||||||||||||||||||
of high-purity |
|
molded graphite |
and itsextensive |
|
use as molds, |
crucibles |
and |
||||||||||||||||||||||
other |
components |
|
as shown |
by the following |
examples. |
|
|
|
|
|
|
|
|||||||||||||||||
|
Molded |
Graphite |
for |
|
Crystal |
Pulling. |
Single |
crystals |
of silicon, |
||||||||||||||||||||
germanium |
and |
WVand |
//-V/semiconductors |
|
are usually |
|
produced |
by the |
|||||||||||||||||||||
ribbon |
or the |
Czochralski |
crystal-pulling |
techniques. |
|
The |
latter |
is shown |
|||||||||||||||||||||
schematically |
in Fig. 5.14. |
The |
process |
makes extensive |
use |
of molded |
|||||||||||||||||||||||
graphite, |
as shown |
on the figure. |
The crucible |
holding |
the |
molten |
material |
||||||||||||||||||||||
is made of high-purii |
|
graphite |
|
lined |
|
with quartz, |
and so are the support |
and |
|||||||||||||||||||||
the heater. |
In some |
cases, the |
crucible is coated with |
pyrolytic |
boron |
nitride |
|||||||||||||||||||||||
deposited |
by chemical |
vapor |
deposition |
(CVD). |
|
|
|
|
|
|
|
|
|
|
|||||||||||||||
|
Other |
Molded |
Graphite |
Applications |
in Semiconductor |
Process- |
|||||||||||||||||||||||
ing. |
The |
following |
|
is a partial |
list |
of current applications |
of molded |
graphite |
|||||||||||||||||||||
in semiconductor |
|
processing:t16) |
|
|
|
|
|
|
|
|
|
|
|
|
|
|
|
|
|||||||||||
|
|
n |
Boats |
and assemblies |
for |
liquid-phase |
epitaxy |
|
|
|
|
|
|
|
|||||||||||||||
|
|
n |
Crucibles |
for molecular-beam |
epitaxy |
|
|
|
|
|
|
|
|
|
|
||||||||||||||
|
|
. |
Susceptors |
for metallo-organic |
CVD |
|
|
|
|
|
|
|
|
|
|
|
|||||||||||||
|
|
. |
Wafer trays for plasma-enhanced |
CVD |
|
|
|
|
|
|
|
|
|
|
|||||||||||||||
|
|
n |
Shields, |
|
electrodes, |
|
and |
ion sources |
for ion |
implantation |
|
|
|||||||||||||||||
|
|
. |
Electrodes |
for |
plasma |
etching |
|
|
|
|
|
|
|
|
|
|
|
|
|
|
|
|
|
|
|
Molded Graphite |
115 |
|
. |
Barrel-type |
wafer |
holders |
for epitaxiai |
deposition (Fig. |
|
||
|
5.15) |
|
|
|
|
|
|
|
. |
Liners for |
electron-beam |
evaporation |
|
|
|
||
. |
Resistance-heated |
jigs |
for |
brazing |
and glass-to-metal |
|
||
|
sealing |
|
|
|
|
|
|
|
9 |
Electrodes |
for pofycrystalline-silicon |
deposition |
|
||||
n |
Boats for |
reduction |
heating |
of germanium |
oxide |
|
|
• Anodes |
for |
power |
tubes |
and high-voltage rectifiers |
|
|
|
||||
in some |
of these |
applications, |
it is necessary |
to coat the |
surface |
of the |
||||||
molded |
graphite |
with |
a more |
inert coating such |
as pyrolytic graphite, |
boron |
||||||
nitride |
(BN) or silicon |
carbide |
(Sic), |
to prevent |
contamination |
and |
reaction |
|||||
with the graphite |
at high temperature. The coating |
is usually |
done |
by CVD |
||||||||
as reviewed |
in Ch. |
7. |
|
|
|
|
|
|
|
|
GraDhite
He’ater
/
Quartz-lined
Graphite
Crucible
Graphite
support
Clip
Figure 5.14. Czochralski apparatus for crystal growth of silicon.[3]