
Синтез зубчатого зацепления
.pdfпередаче максимальный коэффициент перекрытия и отсутствие подреза зубьев
колес.
6.5. Передача с заданным межосевым расстоянием
Если, кроме чисел зубьев и модуля, задано межосевое расстояние aw, то вначале определяется угол зацепления по формуле
W |
arccos |
m(z1 |
z2 )cos |
. |
|
2aW |
|||
|
|
|
|
Зная αw, можно определить коэффициент суммы смещений
х |
|
(inv W inv ) (z1 z2 ) |
, |
||
|
|
2 |
tg |
|
|
|
|
|
где значения invαw и invα определяются по таблице инволютной функции (см.
приложение).
Далее на блокирующем контуре (рис. 6.2) проводится под углом 45 к осям ко-
ординат прямая 1-1, в любой точке которой
x1 x2 x const .
Используя дополнительное условие (например, получение максимальной из-
гибной прочности зубьев), можно найти на проведенной прямой точку, отве-
чающую этому условию (см. раздел 6.2).
7.Расчет геометрии и качественных показателей передачи на ЭВМ
7.1.Исходные данные для расчета
7.1.1.По зубчатой передаче:
- число зубьев меньшего колеса (шестерни) z1;
30
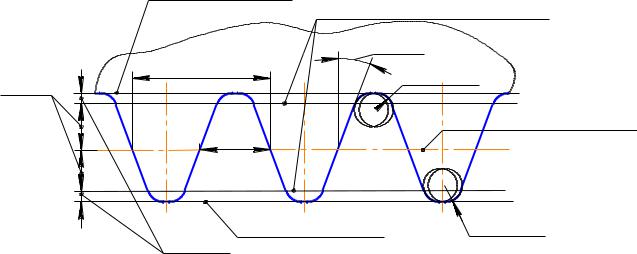
- число зубьев большего колеса z2;
значения z1 и z2 даны в правом верхнем углу каждого блокирующего контура
(приложение), номер блокирующего контура задает преподаватель.
7.1.2. По инструменту реечного типа, которым нарезаются зубья колес Зубья колес быстроходной ступени нарезаются стандартным инструментом ре-
ечного типа, исходный производящий контур (ИПК) которого показан на рис. 7.1.
Значения параметров ИПК: |
|
- угол профиля 20 ; |
|
- коэффициент высоты головки h* |
1,0 ; |
|
|
- коэффициент радиального зазора |
C * 0,25 ; |
- модуль m (числовые значения модуля студент берет согласно номеру и вари-
анту задания на курсовое проектирование или рассчитывает предварительно).
|
|
прямая впадин |
прямая граничных точек |
|
|
|
|
||
|
|
|
=20 |
|
* |
|
p= m |
|
|
|
|
f |
=0,384m |
|
ha m |
|
|
|
|
|
|
0,5p |
|
делительная прямая |
|
H |
|
H |
|
|
|
|
||
|
|
прямая вершин |
f =0,384m |
|
|
|
c*m |
|
|
|
|
Рис. 7.1. Исходный производящий контур (ИПК) |
Коэффициент радиального зазора может быть увеличен до 0,35 для ци-
линдрических передач с модулем m=1 мм и менее и уменьшен до 0,20 – для ко-
нических передач с прямыми зубьями с модулем m=1 мм и более.
31
Допускается также увеличение коэффициента радиального зазора цилин-
дрической зубчатой передачи до С*=0,35 при обработке колес долбяками и ше-
верами и до С*=0,40 при обработке под зубошлифование [5, с. 227].
7.2. Порядок выбора оптимальных коэффициентов
смещений с помощью блокирующего контура
Исходными данными для расчета передачи на ЭВМ являются также ко-
эффициенты смещений шестерни – x1 и большего колеса x2, значения которых надо выбрать.
Для этого вначале по характеристике передачи из таблицы (вариант таб-
лицы задает преподаватель) устанавливается наиболее вероятностный вид раз-
рушения зубьев (см. раздел 3). Далее, используя указания раздела 4, определя-
ются оптимальные коэффициенты смещения, которые должны устранить воз-
можность наиболее вероятного вида разрушения зубьев. Выбор численных зна-
чений таких коэффициентов для каждого из колес следует провести по блоки-
рующему контуру (см. прил.), руководствуясь положениями разделов 5 и 6.
При этом выбранные коэффициенты смещений должны также обеспечить вы-
полнение следующих требований, общих для всех:
-отсутствие подрезов ножек зубьев каждого из колес;
-отсутствие заострения зубьев, при этом толщина зуба по окружности вершин
Sa 0,25m ;
-отсутствие интерференции зубьев;
-непрерывность зацепления, при этом коэффициент перекрытия 1,2 .
32

7.3. Алгоритм расчета геометрии и качественных показателей передачи
7.3.1. Вычисление параметров колес:
а) делительного радиуса r 0,5mz , мм;
б) основного радиуса rb r cos mzcos , мм;
в) радиуса впадин rf r m(ha* c* x) , мм.
7.3.2. Определение окружного делительного шага, равного шагу зубьев исход-
ного контура:
|
|
|
p m , мм. |
|||
7.3.3. Расчет параметров передачи по формулам: |
||||||
а) угла зацепления αw: inv W |
|
|
2tg ( x1 x2 ) |
inv ; |
||
|
|
|
|
|||
|
|
|
|
z1 z2 |
||
б) межосевого расстояния: a |
|
a |
cos |
, мм, |
||
W |
|
|||||
|
|
|
cos W |
|||
|
|
|
|
где a 0,5m(z1 z2 ) - делительное межосевое расстояние.
в) начальных радиусов: r 0,5mz cos , мм;
W cos W
г) коэффициента воспринимаемого смещения: y aW a ; m
д) коэффициента уравнительного смещения: y x1 x2 y .
7.3.4.Вычисление радиуса вершин по формуле ra r m(ha* x y) , мм.
7.3.5.Определяют толщину зуба колеса по окружностям:
а) основной (Sb); |
|
б) делительной (S); |
|
в) начальной (SW); |
|
г) радиуса ry 0,5(rW |
ra ) (Sy); |
д) вершин (Sa). |
|
33
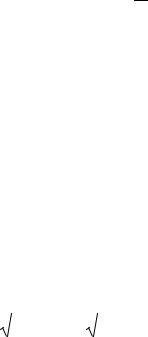
Для вычисления используют общую формулу
|
|
0,5 2xtg |
|
|
|
S |
|
2r |
|
inv inv |
, |
|
|
||||
|
a |
y |
z |
|
y |
где y arccos(rb ry ). Полученные значения толщин зубьев используют в дальнейшем для построения эвольвенты профиля зуба каждого колеса.
7.3.6. Проверка качественных показателей передачи а) Толщина зубьев на окружности вершин
|
|
0,5 2xtg |
|
|
|
S |
|
2r |
|
inv inv |
, мм, |
|
|
||||
|
a |
y |
z |
|
|
где αα - угол профиля колеса в точке, лежащей на окружности вершин, при этом
cos rb . ra
В передаче должно выполняться условие Sa 0,25m . Значения Sa при различ-
ных видах химико-термической обработки (ХТО) поверхности зубьев:
улучшение Sa (0,25...0,30)m ;
цементация, азотирование Sa (0,30...0,40)m ;
закалка Sa (0,40...0,45)m .
Для передач с малыми нагрузками (кинематических) предельное значение Sa
может быть уменьшено до (0,10…0,25)m.
б) Коэффициент перекрытия
|
|
|
r 2 |
r 2 |
|
r 2 r 2 |
a |
sin |
W ; |
||||
|
a1 |
b1 |
|
a 2 |
|
b 2 |
W |
|
|||||
|
|
|
|
|
m cos |
|
|
|
|||||
|
|
|
|
|
|
|
|
|
|||||
в передаче должно выполняться условие |
|
1,2 . |
|
|
|
||||||||
|
|
|
|
|
|
|
|
|
|
|
|
|
7.3.7. Вычисление удельных скольжений в контактных точках профиля зуба шестерни λ1 и колеса λ2:
1 |
1 |
|
|
z1 2 |
|
|
; |
|
z2 |
(aW |
sin W |
|
2 ) |
||||
|
|
|
34
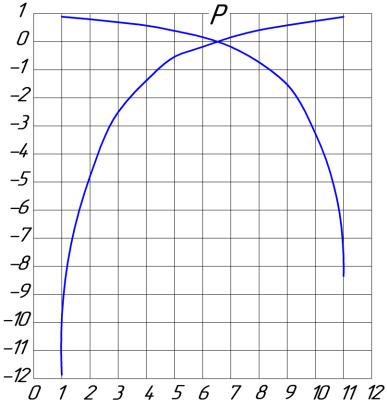
|
|
1 |
z2 (aW sin W 2 ) |
, |
|
|
|
||||
|
2 |
|
z1 |
2 |
|
|
|
|
|
|
где ρ2 – радиус кривизны большего колеса, определяющий положение контакт-
ной точки на линии зацепления AB.
Программа составлена так, что вся линия зацепления (отрезок AB) разби-
вается на 12 равных частей (0, 1, 2,…, 12). Вычисление удельных скольжений ЭВМ начинает в точке 1 линии и заканчивает в точке 11. В точках 0, 12, а также в полюсе зацепления Р студент должен определить удельные скольжения само-
стоятельно.
Рис. 7.2. График скольжения зубьев
Полученные результаты вычислений используются для графического по-
строения станочного зацепления и самой передачи, а также при оформлении расчета геометрии и качественных показателей в РПЗ.
35
8. Построение станочного зацепления
Построение станочного зацепления выполняется для меньшего колеса
(шестерни) после полного расчета геометрии. Для зубонарезания принят инст-
румент реечного типа, соответствующий стандартному исходному производя-
щему контуру (рис.7.1). Масштабный коэффициент длины μl следует выбрать таким, чтобы высота зуба на чертеже была не менее 50 мм. При выполнении графической части в CAD системах сначала лучше выполнить все построения в масштабе 1:1, а потом перенести на формат А1 и отмасштабировать до нужного размера. Построение станочного зацепления удобно производить в следующем порядке.
1) Провести делительную прямую рейки Н-Н (рис. 7.1), по которой тол-
щина зуба и ширина впадины равны между собой и, следовательно, каждая со-
ставляет половину шага р. Используя значения параметров исходного контура
(см. раздел 7.1.2 и рис. 7.1), построить несколько зубьев инструментальной рейки.
2) Провести ось симметрии впадины рейки. Она же будет являться осью симметрии зуба шестерни. При нарезании колес со смещением делительная ок-
ружность шестерни радиуса r1 отстоит от делительной прямой Н-Н рейки на расстоянии, равном x1m . Отложив от прямой Н-Н на построенной оси симмет-
рии зуба отрезок, равный r1 + x1m, получим точку O1 – центр шестерни.
3) Из точки О1 как из центра вычертить основную, делительную, началь-
ную окружности, окружность вершин и окружность радиуса ry/1 0,5(rW 1 ra1 ) .
На этих окружностях отложить по обе стороны от оси симметрии зуба шестер-
ни дуги, равные половине толщины зуба по соответствующей окружности
(см. рис. 8.1.1 и рис. 8.1.2). Соединив по лекалу найденные точки, лежащие по каждую сторону от оси симметрии зуба, получают эвольвенту, которая ограни-
чена окружностью вершин и основной окружностью.
36
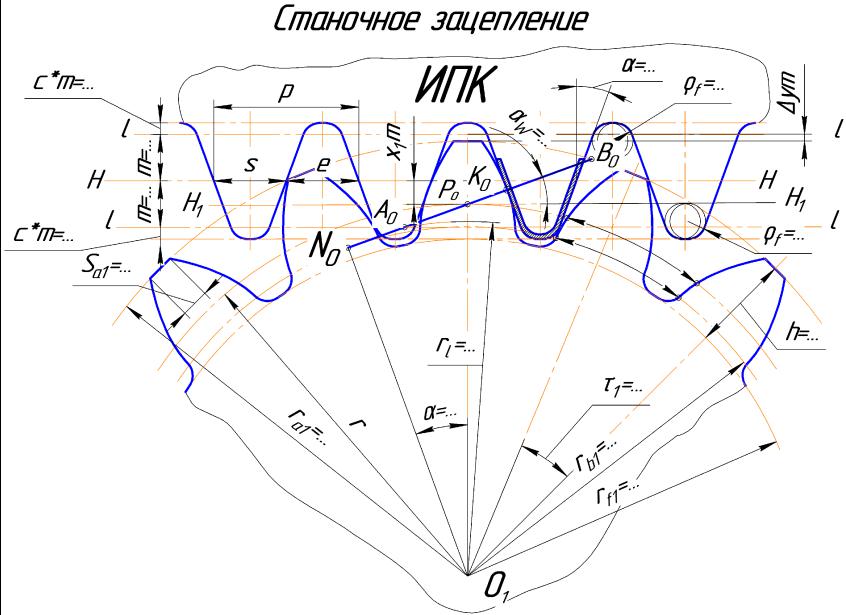
37
Рис. 8.1.1. Фрагмент № 1 построения станочного зацепления
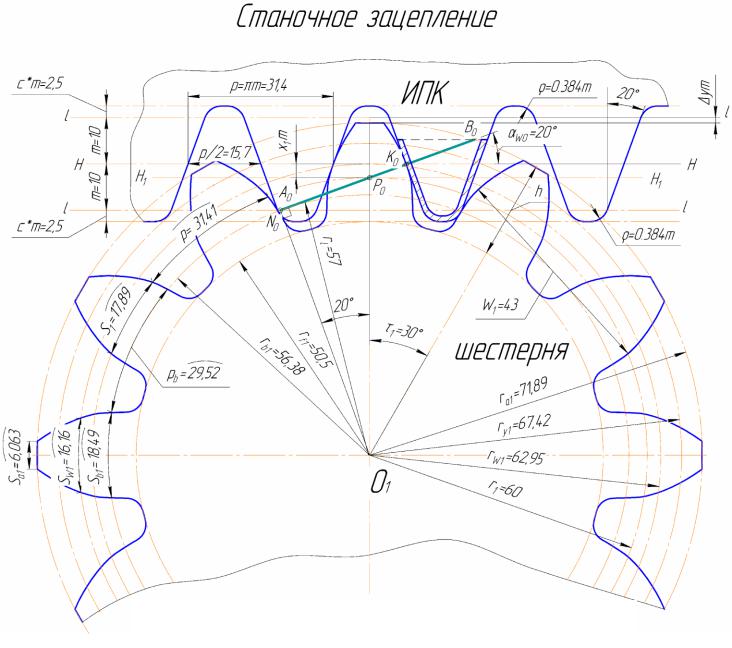
38
Рис. 8.1.2. Фрагмент № 2 построения станочного зацепления
4) Провести окружность впадин шестерни и выполнить сопряжение этой ок-
ружности с эвольвентой по дуге радиуса 0,384m . Следует заметить, что та-
кое сопряжение упрощено. В действительности эвольвента и окружность впадин сопрягаются по переходной кривой, автоматически получающейся при зубонарезании. При правильно построенном станочном зацеплении линия вер-
шин зубьев рейки пройдет касательно к окружности впадин, а наименьшее рас-
стояние между граничной прямой l-l рейки и окружностью вершин шестерни должно быть равно уравнительному смещению ym (см. рис. 8.1.1 и рис. 8.1.2).
Кроме того, эвольвенты зуба должны касаться прямолинейных участков исход-
ного контура рейки.
5) Найти положение осей симметрии остальных зубьев и вычертить их профили. Угол между осями симметрии зубьев равен угловому шагу, величину которого можно определить по формуле
|
|
|
3600 |
. |
1 |
|
|||
|
|
z1 |
||
|
|
|
Так как угловой шаг опирается на дугу, равную окружному шагу, то для опре-
деления положения осей симметрии зубьев можно воспользоваться, например,
шагом р по делительной окружности. После построения зубьев правильность взаимного расположения профилей контролируется длиной общей нормали,
определяемой по формуле
W1 pb (n 1) Sb ,
где n - число охватываемых при замере зубьев, зависящее от общего чис-
ла зубьев шестерни, так n=2 при z 17 .
Вычисленной величине W1 должна соответствовать на чертеже длина от-
резка, заключенного между разноименными эвольвентными участками профи-
лей n охватываемых зубьев; отрезок при этом надо проводить касательно к ос-
новной окружности.
39