
- •Введение
- •1 Содержание курсового проекта
- •2 Анализ конструкции детали и требований к ее изготовлению
- •3 Определение типа производства
- •4 Отработка конструкции детали на технологичность
- •6 Выбор технологических баз
- •7 Выбор методов и количества необходимых переходов обработки
- •9 Выбор средств технологического оснащения операций
- •10 Расчет припусков и операционных размеров
- •11 Определение режимов резания
- •12 Нормирование технологического процесса
- •13 Проектирование схем технологических наладок
- •14 Оформление технологической документации
- •Список использованных источников
Результаты определения промежуточных размеров удобно представить в виде таблицы 10.3. В таблице приведены размеры, соответствующие маршруту обработки поверхностей по рисунку 10.12. Для обработки применено черновое и чистовое фрезерование. Заготовка – отливка 9 класса точности по ГОСТ 26645-85. Номинальные припуски приняты по приложению Е. Допуск исходной заготовки по приложению А. Допуски, соответствующие методам обработки, по приложению Б.
Таблица 10.3 - Припуски и промежуточные размеры
|
|
Номи- |
|
Размер с |
|
|
|
|
предель- |
||
Технологический |
Припуск, |
нальный |
Допуск, |
||
ными от- |
|||||
переход |
мм |
размер, |
мм |
||
клоне- |
|||||
|
|
мм |
|
||
|
|
|
ниями |
||
|
|
|
|
||
|
|
|
|
|
|
Исходная заготов- |
- |
66,2 |
2,0 |
66,2 ±1,0 |
|
ка |
|||||
|
|
|
|
||
|
|
|
|
|
|
Черновое фрезеро- |
2,30 |
63,9 |
h12 |
63,9−0,3 |
|
вание плоскости 1 |
(0,300) |
||||
|
|
|
|||
|
|
|
|
|
|
Черновое фрезеро- |
2,30 |
61,6 |
h12 |
61,6−0,3 |
|
вание плоскости 2 |
(0,300) |
||||
|
|
|
|||
|
|
|
|
|
|
Чистовое фрезеро- |
0,80 |
60,8 |
h9 (0,074) |
60,8−0,074 |
|
вание плоскости 1 |
|||||
|
|
|
|
||
|
|
|
|
|
|
Чистовое фрезеро- |
0,80 |
60 |
h9 (0,074) |
60,0−0,074 |
|
вание плоскости 2 |
|||||
|
|
|
|
||
|
|
|
|
|
11 Определение режимов резания
Режимы резания, с одной стороны, определяются техническими факторами: требуемой шероховатостью обрабатываемой поверхности, возможностями технологического оборудования, требуемой точностью и др. С другой стороны, от режимов резания зависит производительность и технологическая себестоимость. Таким образом, назначение режимов резания является важной технико-экономической задачей.
Режимы резания назначают по нормативам режимов резания [10] или используют аналитический метод расчета [7]. В настоящее время наибольшее распростра-
103
нение получило определение режимов резания по нормативам. Режимы резания определяются для каждого технологического перехода. При этом следует руководствоваться следующей общей последовательностью назначения режимов.
Сначала устанавливают глубину резания t. Глубина резания должна равняться припуску, снимаемому на данном переходе. При этом необходимо учитывать, что при работе на станках средней мощности максимальная глубина резания не должна превышать при точении – от 8 до 10 мм, при фрезеровании цилиндрическими фрезами – от 10 до 12 мм, при фрезеровании торцовыми фрезами – от 12 до 15 мм; При больших значениях припуска или при необходимости снять напуск с поверхности заготовки обработку следует производить за несколько рабочих ходов.
Следующим этапом определения режимов резания является назначение подачи S. Для большинства методов обработки, таких как - точение, сверление, растачи-
вание, определяется подача в миллиметрах на оборот заготовки или инструмента, Sо
мм/об. Для фрезерования исходным расчетным значением подачи является подача в миллиметрах на зуб фрезы, Sz, мм/зуб. Для строгания, некоторых видов шлифования принимается подача в миллиметрах на двойной ход, S мм/дв.ход. Для черновых переходов значение подачи определяется прочностными характеристиками элементов технологической системы. Для чистовых технологических переходов подача ограничивается требуемой точностью и шероховатостью обработанной поверхности. Значения подач приведены в [7, 10], для наиболее распространенных методов обработки можно использовать таблицы приложения Ж. Выбранная подача корректируется по паспортным данным станка.
Затем следует определить период стойкости инструмента Т. Период стойкости, обеспечивающий наиболее экономичные режимы обработки, определяется в соответствии со следующей зависимостью
|
|
1 |
|
|
|
Э |
|
|
Tэк |
= |
|
−1 t |
|
+ |
и |
, |
(11.1) |
|
з |
|
||||||
|
m |
|
|
|
Е |
|
где m – показатель относительной стойкости;
104
tз - время простоя станка, связанное с заменой инструмента, мин;
Эи - затраты на эксплуатацию инструмента за его к период стойкости, руб.;
Е – стоимость минуты работы оборудования, руб./мин.
Определение экономичного периода стойкости в соответствии с зависимостью (11.1) требует большого числа исходных данных. Поэтому чаще используют табличные значения периода стойкости [7]. При определении режимов резания по нормативам предполагается использование нормативного периода стойкости.
Скорость резания V определяется в зависимости от периода стойкости Т, от глубины резания t, подачи S, от механических характеристик обрабатываемого материала, от марки инструментального материала, от состояния поверхности заготовки и от ряда других факторов. Значения скорости резания приведены в [7, 10], для наиболее распространенных методов обработки - в приложении Ж.
Частота вращения n определяется по формуле
n = |
1000 V |
, |
(11.2) |
|
|
π D |
|||
|
|
|
|
где D – диаметр обрабатываемой поверхности или диаметр инструмента, мм. Частота вращения корректируется по паспортным данным станка. В качестве утонченного значения nут принимается наиболее близкое значение. При бесступен-
чатом регулировании привода главного движения станка желательно округлить расчетную частоту вращения до значения кратного 10. После этого уточняется скорость резания. Уточненная скорость резания Vут определяется по формуле
Vут = |
π D n |
ут |
, |
(11.3) |
|
|
|||
1000 |
|
|||
|
|
|
|
При черновой обработке производят проверку выбранного режима резания по мощности привода главного движения станка.
105
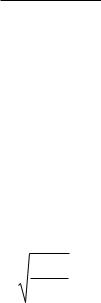
N рез ≤ Nст η , |
(11.4) |
где N рез - мощность, потребная на резание, кВт;
Nст - мощность главного привода станка, кВт;
η - коэффициент полезного действия привода главного движения (0,9 - 0,8).
При невыполнении условия (11.4) необходимо уменьшить глубину резания, подачу или применить на данной технологической операции станок большей мощности.
Для современных станков с ЧПУ ограничением является значение максимального крутящего момента на шпинделе. Крутящий момент от сил резания, (Н·м)
Mрез =1000N рез 30 . (11.5)
πn
Впаспортных данных металлорежущих станков часто приводятся в только максимальные и минимальные значения частот вращения и подач, а также число ступеней К. Промежуточные значения в таких случаях принимают по нормали станкостроения H11-1. Для чего предварительно определяют знаменатель геометрической прогрессии ряда частот вращения или подач
ϕ = K −1 nmax , |
(11.6) |
nmin |
|
где ϕ - знаменатель геометрической прогрессии;
nmax и nmin - наибольшая и наименьшая частоты вращения привода главного движе-
ния; К - число ступеней частот вращения привода главного движения.
106
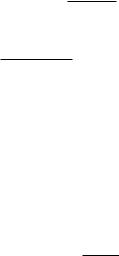
СтандартныезначениячастотвращенияиподачприведенывприложенииГ.
В качестве примера рассмотрим назначение режимов резания на черновую обработку шейки вала.
Исходные данные:
а) обрабатываемый материал - сталь 45; б) заготовка - штампованная поковка, полученная в закрытом штампе на прес-
сах;
в) оборудование - токарный станок с ЧПУ 16Б16Т1; г) режущий инструмент – контурный резец с пластинкой твердого сплава
Т15К6 (Резец 2103-0695 Т15К6 ГОСТ 20872-80);
д) заготовка установлена в центрах; е) диаметр обработки D = 20 мм;
Глубина резания t соответствует припуску z = 1,5 мм. Подача S = 0,4 мм/об (таблица Ж.1)
Период стойкости соответствует нормативному. Скорость резания V = 170 м/мин (таблица Ж.4). Частота вращения n
n =1000πDV ,
n=1000 170 = 2707 об/мин.
π20
По паспортным данным станка принимаем nут = 2000 об/мин.
Уточненная скорость резания Vут
= πDn Vут 1000 ,
107