
- •1 Экономическое обоснование эффективности применения эвм для решения задачи проектирования технологических процессов
- •2 Анализ автоматизированных систем для решения технологических задач подготовки производства в швейной промышленности
- •3 Методика разработки базы данных
- •4 Подготовка исходной информации
- •3.2 Кодирование информации о материалах
- •3. Общие требования к безопасности и экологичности к эвм (техническим системам)
2 Анализ автоматизированных систем для решения технологических задач подготовки производства в швейной промышленности
2.1 Основные этапы процесса изготовления швейных изделий
Предприятия швейной промышленности играют важную роль в удовлетворении потребностей людей в качественной и удобной одежде, соответствующей направлению моды, изготовленной из современных материалов и фурнитуры [5].
Весь процесс изготовления швейных изделий делится на три крупных этапа:
1. Предпроектные исследования;
2. Конструкторское проектирование;
3 .Технологическое проектирование.
На стадии предпроектного исследования (рисунок 1) проводятся маркетинговые исследования и подробное изучение имеющегося предприятия. Проанализировав парк основного и вспомогательного оборудования, а также принятые на предприятии технологии обработки, выбирается ассортимент, мощность, материалы и оборудование для изготовления швейных изделий.
Результатом конструкторского проектирования (рисунок 2) является эскизы проектируемого изделия, пакет материалов для него и рабочая документация. К рабочей документации относится техническое описание швейного изделия и комплект лекал.
На этапе технологического проектирования (рисунок 3) разрабатываются схемы обработки узлов изделий, осуществляется нормирование затрат времени, формирование технологической последовательности операций, проектирование разделения труда между исполнителями, выбор транспортных средств перемещения полуфабрикатов в потоке и расстановка оборудования [2].
Решение задач на каждом из этапов проектирования одежды характеризуется большой трудоемкостью, необходимостью сокращения сроков проектирования, зависимостью результатов их решения от опыта и интуиции специалистов. Получаемые при этом решения часто бывают несовершенны.
Для своевременного реагирования на спрос потребителей швейные предприятия должны создать условия для осуществления подготовки моделей к выпуску в наиболее короткие сроки и гибкой переналадки производственных процессов для изготовления новых швейных изделий [2]
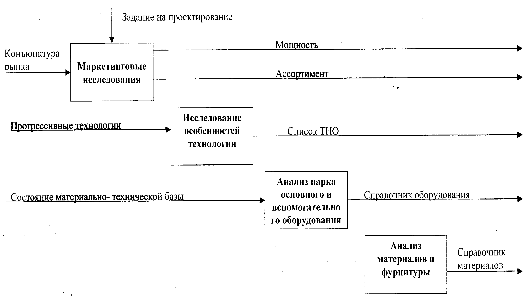
2.2
Автоматизированные
системы проектирования в швейной
промышленности
Развитие швейной промышленности неотделимо от высоких технологий. Сегодня швейные предприятия хотят шить качественно, быстро, сменяя свой ассортимент и выпуская новые коллекции. Серьезным помощником в решении этих задач являются швейные САПР (системы автоматизированного проектирования).
Система автоматизированного проектирования - это организационно-технологическая система, решающая задачу описания объекта проектирования средствами автоматизации вычислений, созданием систем информации и автоматизации ее обработки, человеко-машинного процесса проектирования /7/.
Швейная САПР - это компьютерная программа (или набор программ) для автоматизации работ по конструированию, моделированию, размножению по размерам и ростам, изготовления раскладки лекал и ее зарисовки, разработки документации для технологической подготовки производства. Зачастую под термином "САПР", помимо программного обеспечения, понимается также и набор оборудования: компьютеры, плоттеры (графопостроители), дигитайзеры и т.п., которое необходимо для полноценного функционирования системы [8].
На многих предприятиях легкой промышленности около девяти лет назад появились первые САПР лекал и раскладок лекал. Это были очень дорогостоящие системы ведущих в этой области зарубежных фирм. Затем на рынке появились САПР и отечественных производителей. На предприятиях, освоивших компьютерные технологии, быстро ощутили их преимущества, и возврат к традиционным методам работы там уже не возможен.
Некоторое время отечественные системы не могли конкурировать с зарубежными из-за отсутствия сопоставимой по возможностям и надежности вычислительной техники [9]. Ситуация поменялась в середине 80-х годов прошлого века, когда было решено приобрести лицензию испанской фирм
investronica на производство автоматизированных настилочно-раскройных комплексов. Это решение дало мощный импульс к разработке отечественных САПР одежды, в которых проектирование охватывает весь процесс создания образцов изделий от разработки лекал до их раскроя. Появление относительно дешевых персональных компьютеров и средств периферии, привело к тому, что в настоящее время САПР в производстве одежды широко используется не только на крупных предприятиях, но и в небольших фирмах и ателье.
На сегодняшний день можно насчитать более двадцати систем автоматизированного проектирования швейных изделий, успешно функционирующих на различных отечественных и зарубежных предприятиях. Присутствие такого количества САПР на рынке и постоянный спрос на них объясняется различными средствами реализации задач, которые ставит перед собой пользователь [7].
Наиболее развитые системы проектирования одежды включают дизайнерские программы, позволяющие разрабатывать внешний вид изделий, подбирать наиболее удачные сочетания расцветок ткани, конструкторские программы, реализующие творческий замысел дизайнера в лекалах, технологические программы оптимизации раскладки лекал на материале и проектирования процесса раскроя и пошива изделий, учитывающие особенности конкретных производств.
При анализе источников информации выяснилось, что за последние 20 лет из основного комплекса работ по автоматизации процесса проектирования в швейной промышленности наибольшее внимание уделялось конструктивной подготовке производства, и в настоящее время эта часть проектирования является наиболее исследованной и автоматизированной.
Количество существующих САПР для технологической подготовки производства (ТПП) исчисляется десятками. Все они обладают как преимуществами, так и недостатками по отношению друг к другу.
В настоящее время в швейной промышленности выделены две группы САПР:
- САПР швейных изделий,
- САПР швейных потоков.
САПР швейных изделий - это программный комплекс для организации рабочего места конструктора, позволяет в автоматизированном режиме выполнить создание рисунка модели, разработку базовых и модельных конструкций, градацию (размножение на различные размеры), раскладку лекал.
САПР швейных потоков представляет собой рабочее место технолога. Процесс проектирования потоков швейных цехов включает решение трех основных задач:
1) Разработку технологического процесса изготовления изделия.
2) Организацию трудового процесса в потоке (составление технологической схемы разделения труда).
3) Выбор транспортных средств перемещения полуфабрикатов в потоке и расстановку оборудования (планировочные решения).
Наряду с САПР швейных потоков и САПР швейных изделий существуют, так называемая, комплексная САПР, которая представлена как совокупность информационно-согласованных объектно-ориентированных подсистем или модулей: маркетинга, поиска моделей-аналогов, проектирования базовых основ и исходных модельных конструкций, конструктивного моделирования, проектирование основных и производных лекал, градации лекал, выполнения раскладок, документирования, организацию технологического процесса.
Проектирование комплексных систем автоматизации производства для швейной отрасли является достаточно новой задачей, малоисследованной. Авторы таких систем не публикуют методов, алгоритмов и технологии их создания. Примерами комплексных САПР одежды являются разработка центра компьютерных технологий МГУ С "Грация", разработка центра компьютерных технологий МФТИ "Ассоль", разработка научно-технического Центра дизайна и технологии МГУДТ "Eleandr САРР" и др. [9].
Большое внимание развитию САПР уделяется Центральным научно исследовательским институтом швейной промышленности (ЦНИИШП); полученные результаты, использовались в разработке отечественных систем проектирования.
С 1999 года ОАО «ЦНИИШП» и фирма «Комтенс» ведут совместные работы по развитию САПР и адаптации ее к производству специальной и форменной одежды.
В настоящее время отработаны методики проектирования и градации деталей изделий рассматриваемой ассортиментной группы; разработаны средства формального представления последовательности операций при конструировании деталей изделий в САПР, что позволяет упростить и ускорить процесс внедрения методических разработок ОАО «ЦНИИШП» и других организаций в отрасли. С учетом того, что для рассматриваемого класса изделий характерна высокая степень унификации и повторяемости деталей, предложен программный инструмент формирования изделий, существенно упрощающий и ускоряющий процесс создания новых моделей. Эффект достигается за счет использования базы данных унифицированных деталей, включающей собственно лекала, правила их размножения и технологию обработки.
Специальное внимание было уделено разработке программ технологической подготовки швейного и раскройного производств, управлению работой швейного цеха. В состав САПР входят модули АРМ «Технолог» и АРМ «Мастер». АРМ «Технолог» предназначен для автоматизации работы технологов экспериментального и швейного цехов швейного производства и позволяет решить следующие задачи:
1) составление технологической последовательности изготовления швейных изделий;
2) нормирование времени выполнения технологических операций;
3) расчет стоимости отдельных операций и технологической последовательности в целом;
4) компоновка организационных операций.
Программный модуль АРМ «Мастер» позволяет эффективно управлять работой швейного цеха. Он используется как для формирования планового задания работы цеха (задача руководителя швейного цеха), так и для составления индивидуальных заданий работникам (задача мастера цеха или бригадира). Индивидуальные задания составляются с учетом предрасположенности каждого работника к выполнению конкретных операций. АРМ «Мастер» наиболее эффективно применяется в мелкосерийном производстве и позволяет вести контроль выполнения работ при одновременном производстве до 20 изделий.
-
САПР "Ассоль" разработана в Московском Физико-техническом институте. При ее создании использованы самые современные информационные технологии и методы программирования в графической среде AutoCAD.
САПР "Ассоль" - модульный программный комплекс, который позволяет по эскизу, фотографии или образцу быстро и точно разрабатывать лекала моделей любой сложности. В системе можно конструировать изделия с "нуля", вводить с дигитайзера готовые лекала и редактировать их, выполнять градацию и раскладку, распечатывать чертежи конструкций, лекала, сетки градаций раскладки, создавать сопроводительную текстовую документацию, использовать подсистему «Технолог» для составления технологической последовательности и выполнения разделения труда (13).
-
Компания САПРЛЕГПРОМ, разработчик программ для конструирования одежды и управления швейным производством, занимает одну из лидирующих позиций на рынке информационных технологий с 1980-х годов[4]. Среди их клиентов предприятия швейной промышленности России, Украины, Беларусии, Болгарии, Кыргызстана, Молдовы, Казахстана, Монголии. Разработанный и поставляемый фирмой «САПРЛЕГПРОМ» программный комплекс JULIVI включает в себя:
a) Систему Автоматизированного Проектирования одежды (САПР одежды);
б) Автоматизированную Систему Управления Производством (АСУП), интегрированную с САПР одежды.
Программы АСУП:
"Технологическая последовательность" - программа для разработки технологии пошива одежды; "Расчет норм времени" - программа расчета норм времени на пошив; "Схема разделения труда" - программа, организующая работу швейного потока; "Расчет ниток и кромок" - программа для расчета ниток и кромок; "Техническое описание" - программа для составления всей необходимой технологической документации на модель одежды, описания швейной фурнитуры; "Учет труда сдельщиков" - программа для расчета заработной платы швей; "Материалы заказа" - программа расчета ткани и швейной фурнитуры на пошив одежды, составление конфекционных ведомостей; "Галерея моделей" - программа для представления информации о моделях одежды на швейном производстве; "Планирование заказа" - программа расчета расхода ткани для пошива одежды; "Расчет кусков" - модуль автоматического и полуавтоматического расчета расхода ткани с учетом отдельных кусков, формирование карты раскроя; "Предварительная проработка заказа (расчет себестоимости изделия)" - программа для проработки заказа на пошив одежды с оценкой экономических показателей; "Учет тканей", "Учет фурнитуры", "Учет кроя", "Учет готовой продукции" - это программы складского учета; "Артикулы швейных изделий" - программа формирования артикулов готовых изделий швейного производства и задания их цен; "Календарное планирование" - программа составления плана работы швейного производства; "Диспетчер" - программа сбора информации о незавершенном швейном производстве и корректировки графиков работы швейного производства; "График работы предприятия" - программа формирования графика работы швейной фабрики на год, расчета общего рабочего времени
Программы АСУП ускоряют работу планового отдела швейного производства и отдела технологов в 4 раза.
-
Для швейного предприятия средней мощности, выпускающего женские костюмы из всего многообразия программного и технического обеспечения возможно использование САПР «Грация», так как это первый полнофункциональный САПР, созданная конструкторами и технологами. В результате - простой и наглядный процесс проектирования, не требующий серьёзных затрат на освоение и эксплуатацию системы [5].
В подсистеме «Конструирование и Моделирование» САПР ГРАЦИЯ для построения Модельной конструкции специалист может выполнить все необходимые приемы технического моделирования на основе базовых конструкций, построенных по наиболее распространенным методикам конструирования и поставляемых вместе с САПР. Программа для моделирования одежды также представляет возможность самостоятельно построить Базовую конструкцию «с нуля».
Кроме вышеназванных подсистем в состав комплекса САПР"Грация" входят следующие подсистемы:
- "Индивидуальные и корпоративные заказы";
- "Технология изготовления";
- "Учет";
- "Планирование";
- "Управление предприятием".
Подсистема «Технология изготовления» предназначена для создания и ведения баз данных оборудования, специальностей, неделимых операций и блоков поузловой обработки, составления технологических последовательностей и схем разделения труда. Строятся графики синхронности работы потока, загрузки оборудования и использования рабочей силы.
Автоматизация процессов учета, планирования и управления позволяет своевременно обеспечить производство необходимыми материалами и комплектующими, рассчитать себестоимость и отпускную цену, оперативно получить информацию о динамике производства и реализации любого изделия за любой период времени и сформировать оптимальный план выпуска [5].
Вывод
На рынке представлено достаточно большое число САПР отечественного и импортного производства. На первый взгляд функционально все системы очень похожи и отличия вызваны лишь степенью проработки той или иной программы, но все они являются дорогостоящими и используются только на крупных швейных предприятиях.
На сегодняшний день многие предприятия легкой промышленности стоят на перепутье, решая вопрос экономичности и целесообразности внедрения систем автоматизированного проектирования. С одной стороны, применяя САПР, можно значительно повысить показатели своего производства, с другой - загнать предприятие в долги. Однако в такой ситуации есть и компромиссный вариант, который заключается в создании систем, способных автоматизировать процесс решения ряда задач, используя простые прикладные программы. Такой путь является наиболее правильным и выгодным, особенно для средних и мелких предприятий швейной промышленности.
Следует отметить что, не смотря на унификацию методов обработки, каждое предприятие использует собственные стандарты и технические условия (ТУ), которые подчас существенно отличаются от унифицированных, следовательно, приобретение такого САПР становится бессмысленным.
Справочники технологии швейного цеха в электронном виде имеются, как правило, только на крупных швейных предприятиях. Малые предприятия, при этом, не в состоянии создавать собственные базы данных (БД), т.к. это требует не только времени, но и немалых денежных средств. Необходимость же создания БД на малых предприятиях диктуется частой сменой ассортимента, к этому же вынуждает частая смена материалов.
Решением данной проблемы может разработка такой базы данных, которая могла бы быть адаптирована для любого технологического процесса изготовления одежды.
2.3 Характеристика технологического процесса как системы
Все работы по автоматизации производства производятся с точки зрения системного анализа.
Системный подход к решению задач технологической подготовки обеспечивают единство исходной переменной и условной информации, минимизацию и многократное использование нормативно-справочных данных, исключает повторение кодирования одних и тех же данных и т.п.
Системный подход требует формализации использованной информации необходимой при работе с ЭВМ. Чтобы создать способ проектирования оптимальных технологических процессов изготовления швейных изделий с использованием ЭВМ, необходимо рассмотреть ТП, как систему [2].
Объектом технологии швейных изделий является типовой технологический процесс изготовления изделия (ТПШИ) определенной ассортиментной группы. Технологические процессы относятся к числу сложных объектов. В понятие сложной системы вкладывается следующий смысл:
-
сложную систему можно расчленить на конечное число подсистем, а каждую подсистему, в свою очередь – на конечное число более простых подсистем и т.д., до тех пор, пока не будут получены элементы системы (под элементами системы понимаются объекты, которые в условиях данной задачи не подлежат расчленению на части);
-
элементы сложной системы функционируют во взаимодействии друг с другом;
-
свойства сложной системы определяются не только свойствами отдельных элементов, но и характером взаимодействия между элементами.
Таким образом, системный анализ сложной технологической системы включает в себя три основных этапа:
-
декомпозиция, т.е. расчленение системы на составляющие её структурные элементы;
-
анализ рассматриваемой технологической схемы;
-
синтез оптимальной технологической системы.
При традиционных методах изучения информации сложных объектов и процессов обращается внимание на количественное и качественное описание свойств объектов. Построенные такими методами модели отображают связи объектов с окружающей средой, их функцию и многоуровневую систему, в то время как эти факторы оказывают решающее влияние на вид и структуру алгоритмов процесса. В связи с этим все большее значение для развития теории и методов проектирования приобретает системный подход к объектам производства, технологическим процессам и процессам проектирования.
В отличие от традиционных методов формализации системный подход исходит из того, что специфика сложных объектов и процессов не исчерпывается свойствами составляющих их элементов, а обусловлена характером связей и отношений между ними.
Элементами системного подхода являются:
-
формулирование целей системы до начала деятельности, связанной с принятием решений;
-
формулирование иерархии целей;
-
разработка математических и логических моделей, отражающих целевое содержание;
-
определение требований и ограничений, накладываемых средой на создаваемую систему;
-
разработка разных способов достижения целей;
-
оценка вариантов разработанных решений на основе комплекса критериев;
-
выбор наилучшего (оптимального) решения1.
Сложные системы можно разбить на подсистемы и элементы с иерархической структурой связи. Каждая подсистема, решая конкретную задачу, обеспечивает тем самым достижение общей цели.
Таким образом, ТП как система определяется функцией, структурой, набором характеристик, связями с окружающей средой [3].
Функция любого ТП Ф определяется как преобразование объекта обработки из исходного состояния Со в конечное Ск :
Ф : Со Ск
Исходное состояние швейного изделия как объекта обработки характеризуется множеством деталей кроя {ДTi}, конечное определяет готовое изделие ИЗ. Таким образом, функция ТПШИ может быть описана как
Ф : {ДTi} [ИЗ]
Функцию технологического процесса более узко можно определить как последовательный многоуровневый синтез изделия из узлов или множества деталей (элементов). При этом функция i каждого элемента ТПШИ связана с функциями других его элементов 1, 2, … , n и направлен на выполнение общей функции Ф всего технологического процесса. Поэтому функции i элементов ТПШИ может быть как преобразование деталей ДT и сборочных единиц СБ из одного состояния в другое, так и их сборка в более крупные сборочные единицы, т.е.
i : {ДTi-1 ; СБi-1} {ДTi ; СБi}
или
i : {ДTj ; СБj}i-1 СБi
Для реализации одной и той же функции элементов технологического процесса могут быть использованы различные виды оборудования, приспособлений, вспомогательных материалов, определяющих различную последовательность воздействия на предмет труда. Разные методы обработки деталей и узлов швейного изделия, реализующие одну функцию, называются альтернативными методами обработки. Например, клапан бокового прорезного кармана может быть изготовлен с помощью, как стачивающей машины, так и полуавтомата. Рассматриваемые методы обработки, имея одинаковую функцию, отличаются друг от друга характеристиками и последовательностью воздействия на обрабатываемый предмет.
Структура S ТПШИ представляет собой конечное множество элементов технологического процесса с взаимосвязями, определяющими отношение между этими элементами. Элементами технологического процесса могут быть различные его части. Способ расчленения структуры технологического процесса зависит от цели решаемой задачи.
Структуру технологического процесса изготовления швейных изделий изображают в виде схем сборки, списков технологических операций (последовательности обработки), графа технологического процесса. Первые два варианта дают лишь общее представление о последовательности выполнения операций по обработке изделия и не описывают взаимосвязи между всеми элементами структуры ТПШИ.
Представление технологического процесса в виде графа позволит описать связи между элементами ТПШИ, оперативно скомплектовать технологические операции в организационные, произвести различные технологические расчёты и т.д.
Основными характеристиками Z технологического процесса изготовления швейных изделий являются: виды оборудования и приспособлений, с помощью которых выполняются отдельные технологические операции (ТО); время выполнения ТО, их разряд; режимы и параметры. Каждый вариант ТПШИ описывается набором характеристик.
Характеристики технологического процесса формируются на основе характеристик предметов и средств труда. К основным характеристикам предметов труда относятся число деталей в изделии, размеры срезов деталей и др. К основным характеристикам средств труда можно отнести производительность оборудования, тип привода (для оборудования влажно-тепловой обработки) и др.
Характеристики технологического процесса, которые формируются непосредственно на основе характеристик предметов и средств труда и определяют способ обработки изделия, принято называть внутренними характеристиками ТПШИ. К внутренним характеристикам технологического процесса относятся параметры и режимы выполнения технологических операций (время прессования, время пропаривания, частота стежка и др.).
Внешние характеристики технологического процесса определяются применяемыми способами обработки изделия. Внешние характеристики ТП оценивают его функционирование в рамках конкретного производства (например, трудоемкость, себестоимость, капитальные затраты). Внешние характеристики ТПШИ во многом зависят от организационных факторов производства и структуры самого технологического процесса.
Связи технологического процесса изготовления швейного изделия с внешней средой Н представляют собой связи с подразделениями производственного процесса и системами управления предприятием, работа которых зависит от ТПШИ или оказывает на него своё влияние.
2.4 Граф технологического процесса изготовления модели швейного изделия
Структуру ТП изготовления швейных изделий изображают в виде схем сборки, списков технологических операций, графа ТП. Первые два варианта дают общее представление о последовательности выполнения операций по обработке изделия и не описывают взаимосвязи между элементами структуры ТГППИ.
Технологический процесс изготовления швейного изделия представляет собой конечное множество элементов, взаимосвязанных определенным образом между собой. В качестве этих элементов могут выступать обработка отдельных узлов изделия, технологически неделимые операции, а также приемы их выполнения. Характер взаимосвязей элементов определяет структуру ТПШИ, которая при проектировании процессов должна строго соблюдаться [1].
Представления ТП в виде графа позволяет описать связи между элементами ТПШИ, оперативно скомплектовать технологические операции в организационные, произвести различные технологические расчеты.
В практике проектирования технологических процессов изготовления швейных изделий информация о процессе задается различными способами. Наиболее приемлемой формой представления взаимосвязей элементов технологического процесса, порядка их следования нужно считать ориентированный граф.
Математически граф G структуры ТПШИ можно определить как пару множеств N и Е:
G=(N,E)
Где N - множество вершин, каждой из которых соответствует технологическая операция;
Е - множество дуг, соответствующих связям между операциями технологического процесса.
При этом для каждого номера операции N; задаются параметры (Ci, Ri, Ti}, где Сi - специальность исполнителя операции;
Ri - разряд исполнителя операции;
Ti
- время
выполнения операции (рисунок 4).
Каждая технологическая операция в графе процесса обработки изделия расположена на определенном операционном уровне. Операционный уровень обуславливает очередность выполнения операций технологического процесса и исключает ошибки при его построении. Указание порядкового номера в вершине графа технологического процесса не является отражением порядка выполнения операций, а служит для нахождения места данной операции в справочнике.
Параллельная обработка деталей изделия на графе обозначаются параллельной цепочкой работ, последовательная обработка и сборка деталей изделия - последовательной цепочкой работ. Возможный одинаковый приоритет в обработке при сборке деталей или сборочных единиц изделия на графе указывается одинаковым уровнем начала их сборки.
Справочники технологических операций по обработке и сборке швейных изделий включают в себя все возможные при обработке изделия данного вида операции.
Большинство технологических процессов изготовления швейных изделий можно представить в виде частного случая ориентированного графа, называемого ориентированным деревом. Дерево на множестве р вершин всегда содержит q=p-l дуг, т.е. минимальное количество дуг, необходимое для того, чтобы граф был связным.
При отсутствии навыков построения графа ТПШИ целесообразно начинать с выделения условной сборочной единицы изделия, т.е. такой детали, которая имеет наибольшее количество конструктивно-технологических связей с другими деталями. Для этого составляют матрицу связей деталей в изделии, где под порядковым номером детали указывается единица при наличии конструктивно-технологической связи с другой деталью и ноль - при отсутствии связи (таблица 1).
Таблица 1 - Матрица конструктивно-технологических связей деталей швейного изделия
Код детали |
01 |
02 |
03 |
04 |
05 |
06 |
07 |
Rs |
01 |
х |
1 |
0 |
1 |
0 |
1 |
1 |
4 |
02 |
1 |
Х |
1 |
0 |
0 |
1 |
0 |
3 |
03 |
0 |
1 |
х |
1 |
0 |
0 |
0 |
2 |
04 |
1 |
0 |
1 |
х |
0 |
0 |
1 |
3 |
и т.д. |
|
|
|
|
|
|
|
|
Деталь с наибольшей суммой связей Rs условно принимается за основную. На графе процесса она будет являться стволом древовидного изображения процесса обработки (при построении графа располагается посередине листа). Выделение основной сборочной единицы изделия условно и применяется для облегчения построения и восприятия графа процесса. Реальное отображение связей операций ТПШИ не имеет ствола, так как детали в изделии равнозначны.
Параллельная обработка деталей изделия на графе обозначаются параллельной цепочкой работ, последовательная обработка и сборка деталей изделия - последовательной цепочкой работ. Возможный одинаковый приоритет в обработке при сборке деталей или сборочных единиц изделия на графе указывается одинаковым уровнем начала их сборки.
Ромбики в обработке изделия характеризуют ситуацию “или- или”: или первой будет участвовать в обработке эта цепочка операций , или другая.
Технологической особенностью обработки швейных изделий является наличие “плавающих” операций. “Плавающая” операция может быть выполнена в любой момент на протяжении определенного периода обработки изделия (например, приутюживание подкладки может выполняться как в середине процесса, так и при окончательной отделке изделия). На графе процесса такие операции условно выносятся за основной процесс с указанием интервала времени их возможного выполнения.
2.5 Методика построения графа ТП
Методика построения обобщенного графа ТП изготовления швейного изделия основана на схеме построения графа ТП конкретной модели.
Методика включает в себя следующие этапы:
- отбор моделей изделия с рисунком и описанием внешнего вида, деталями кроя, технологической последовательностью изготовления;
- построение схем сборки деталей моделей изделия и графов ТП изготовления на уровне операций, модулей, блоков;
- анализ и группировка деталей кроя данного вида изделия;
- построение обобщенного графа ТП изготовления изделия на уровне модулей, операций.
Методика построения графа ТП изготовления конкретной модели изделия включает в себя элементы его членения и синтеза из частей. Сначала необходимо составить укрупненную схему обработки и сборки деталей и узлов изделия. Для этого названия всех деталей изделия выписывают в горизонтальную строку, каждой детали присваивают порядковый номер. Номер детали, имеющий согласно последовательности начальную обработку до соединения с другой деталью, следует заключать в прямоугольник. Детали, не подвергающиеся начальной обработке, направляют непосредственно к элементу сборки ТП. Соединение деталей в какой-либо узел оформляют элементом ТП с присвоением очередного порядкового номера.
После построения схемы сборки частей изделия ее элементы заполняют группами операций согласно последовательности обработки изделия. Наполненная операциями схема сборки деталей и узлов изделия представляет собой граф ТПШИ.
Таким образом, построение графа процесса выполняется по схеме 1.
2.6 Структура технологического процесса изготовления швейного изделия
Для формирования обобщенного графа технологического процесса строят частные графы обработки конкретных моделей изделия или их частей. Один из графов принимают за базовый и сравнивают с графом другой модели: вершины графа, характеризующие аналогичные операции, заштриховывают, отличительные операции второй модели включают в граф первой. В обобщенном графе технологического процесса сохраняют последовательность выполнения операций индивидуальных процессов. Любой конкретный технологический процесс представляет собой подграф данного обобщенного графа. На рисунке 6а приведен пример обобщенного графа, на рисунке 6 б - его подграф.
Рисунок 6 -Граф процесса и его подграф
На рисунке 7а представлены фрагменты графов индивидуальных процессов обработки. Операции элемента Ml аналогичны для обеих моделей. В процессе обработки изделий могут быть предусмотрены различные методы обработки узлов, называемые альтернативными, объединяемые в одну элементарную часть процесса. Операции элемента М2 разные и объединены в одну элементарную часть технологического процесса по выполняемой функции. Операции элементов МЗ и М4 определяются модельными особенностями изделия, поэтому обе они включены в обобщенный граф. Операции элемента М5 аналогичны для обеих моделей. Элементы с одинаковой функцией для двух графов на рисунке заштрихованы. На рисунке 76 изображена обобщенная структура рассматриваемого процесса, где штриховой линией обозначен один из альтернативных методов. Полученные элементарные части технологического процесса по выполняемой функции выделены на графах прямоугольниками и названы конструктивно-технологическими модулями (КТМ). На рисунке 7в дана схема сборки процесса из этих элементарных частей.
Конструктивно-технологический модуль представляет собой завершенную в технологическом отношении часть ТИШИ, определяющую способ изготовления относительно самостоятельной части конструкции изделия. Самостоятельность таких элементов заключается в том, что они могут присутствовать в любой модели изделия независимо от других элементов, не связанных с ними функционально. Например, часть ТП по обработке вытачки, манжеты, воротника независимо от конструкции изделия всегда имеет одну и ту же функцию. Кроме того, между методами обработки различных модулей отсутствуют причинно-следственные связи. Например, метод обработки вытачки не влияет на метод обработки кармана.
Отдельные КТМ можно реализовать несколькими альтернативными методами. Примерами могут служить различные методы обработки нижнего среза отлетной кокетки.
Таким образом, основными признаками КТМ, служащими критериями для их выделения, являются:
- технологическая завершенность обработки относительно самостоятельной части изделия;
- функциональная целостность;
- отсутствие причинно-следственных связей между методами обработки в различных КТМ.
Для систематизации сведений о ТПШИ и создания рациональной системы кодирования и поиска исходной информации о технологическом процессе в его структуре выделены элементы более высоких уровней детализации, такие, как блоки и этапы.
Блоки технологического процесса представляют собой совокупности КТМ. Блок технологического процесса соответствует обработке отдельных частей основных сборочных единиц изделия. Совокупность блоков технологического процесса представляет собой этап.
Структуру конкретного технологического процесса с взаимосвязями между элементами различных уровней детализации представлена на рисунке 8 с помощью графа.
Структурный состав обобщённого технологического процесса изготовления определённого вида изделия в виде иерархической схемы приведён на рисунке 9.
Элементами I уровня являются этапы технологического процесса (Э);
Элементами II уровня - блоки (Б).
Элементами III уровня являются КТМ. Отдельные КТМ могут иметь несколько разновидностей технологического решения (R) в зависимости от вида материала, конструкции и длины шва, способа соединения и т.д. Разновидности технологического решения КТМ могут быть выполнены на различном оборудовании, поэтому в структуре предусмотрены варианты методов обработки (М).
Элементами IV уровня структуры ТПШИ являются технологические операции (О), а элементами уровня V - приемы выполнения технологической операции (П). Технологические операции, так же как и КТМ, могут иметь варианты (V) в зависимости от параметров шва. Технологическая операция представляет собой элемент структуры технологического процесса, при выполнении которой происходит качественное изменение предмета обработки. Каждая технологическая операция состоит из совокупности основньк и вспомогательных приемов ее выполнения. В производственном процессе в зависимости от способа организации труда в составе технологических операций могут применяться различные вспомогательные приемы. Для подсистемы проектирования технологического процесса изготовления швейных изделий элементами низшего уровня структуры ТПШИ приняты технологические операции.
Иерархическая схема членения технологического процесса швейного изделия приведена на рисунке 8.
Технологическая операция представляет собой элемент структуры технологического процесса, при выполнении которой происходит качественное изменение предмета обработки. Каждая технологическая операция состоит из совокупности основных и вспомогательных приемов ее выполнения. В производственном процессе в зависимости от способа организации труда в составе технологических операций могут применяться различные вспомогательные приемы. Для подсистемы проектирования технологического процесса изготовления швейных изделий элементами низшего уровня структуры ТПШИ приняты технологические операции.
36
Рисунок 8- Иерархическая схема членения технологического процесса изготовления швейного изделия
Таким образом, изображение технологического процесса изготовления различных моделей швейного изделия в виде обобщенного графа позволяет в сжатой форме дать полную информацию о технологии изготовления изделия с учетом возможных модельно-конструктивных решений деталей и узлов, систематизировать эту информацию, совершенствовать существующие способы представления сведений о технологии изготовления изделий и в дальнейшем подойти к автоматизации процесса проектирования технологических процессов.