
надежность машин и оборудования
.pdf31
|
|
|
|
|
|
|
|
|
|
Таблица 6.10 |
||
|
|
|
|
|
|
РАСЧЕТ ВЕРОЯТНОСТИ КАПИТАЛЬНОГО РЕМОНТА |
|
|
||||
¹¹ |
Номер узла |
Сумма |
|
|
|
|
|
|
||||
|
|
|
|
 å ð î ÿ ò í î ñ ò ü |
|
|
|
|
|
|||
1 |
2 |
3 |
4 |
|
-M{C1k} |
|
-M{C3k} |
|
||||
состо- |
рангов |
+M{C0n} |
+M{C2k} |
+M{C4k} |
||||||||
|
Ð à í ã |
|
ñ î á û ò è ÿ |
|||||||||
ÿíèÿ |
|
|
åRi |
|
|
|
|
|
||||
1,0 |
0,8 |
0,5 |
0,2 |
|
|
|
|
|
|
|||
|
|
|
|
|
|
|
|
|||||
|
|
|
|
|
|
|
|
|
|
|
|
|
1 |
+ |
0 |
0 |
0 |
1,0 |
(1–p1)p2p3p4 |
p2p3p4 |
–p1p2p3p4 |
|
|
|
|
2 |
+ |
+ |
0 |
0 |
1,8 |
(1–p1)(1–p2)p3p4 |
p3p4 |
–p1p3p4–p2p3p4 |
p1p2p3p4 |
|
|
|
3 |
+ |
0 |
+ |
0 |
1,5 |
(1–p1)p2(1–p3)p4 |
p2p4 |
–p1p2p4–p2p3p4 |
p1p2p3p4 |
|
|
|
4 |
+ |
0 |
0 |
+ |
1,2 |
(1–p1)p2p3(1–p4) |
p2p3 |
–p1p2p3–p2p3p4 |
p1p2p3p4 |
|
|
|
5 |
+ |
+ |
+ |
0 |
2,3 |
(1–p1)(1–p2)´ |
p4 |
–p1p4–p2p4–p2p4 |
p1p2p4+p1p3p4+ |
-p1p2p3p4 |
|
|
|
|
|
|
|
|
´(1–p3)p4 |
|
|
+p2p3p4 |
|
|
|
6 |
+ |
+ |
0 |
+ |
2,0 |
(1–p1)(1–p2)´ |
p3 |
–p1p3–p2p3–p3p4 |
p1p2p3+p1p3p4+ |
-p1p2p3p4 |
|
|
|
|
|
|
|
|
´p3(1–p4) |
|
|
+p2p3p4 |
|
|
|
7 |
+ |
0 |
+ |
+ |
1,7 |
(1–p1)p2´ |
p2 |
–p1p2–p2p3–p2p4 |
p1p2p3+p1p2p4+ |
-p1p2p3p4 |
|
|
|
|
|
|
|
|
´(1–p3)(1–p4) |
|
|
+p2p3p4 |
|
|
|
8 |
+ |
+ |
+ |
+ |
2,5 |
(1–p1)(1–p2)´ |
1 |
–p1–p2–p3–p4 |
p1p2+p1p3+p1p4+ |
−p1p2p3-p1p2p4- |
p1p2p3p4 |
|
|
|
|
|
|
|
´(1–p3)(1–p4) |
|
|
+p2p3+p2p4+p3p4 |
-p1p3p4-p2p3p4 |
|
|
9 |
0 |
+ |
+ |
0 |
1,3 |
p1(1–p2)(1–p3)p4 |
p1p4 |
–p1p2p4–p1p3p4 |
p1p2p3p4 |
|
|
|
10 |
0 |
+ |
0 |
+ |
1,0 |
p1(1–p2)p3(1–p4) |
p1p3 |
–p1p2p3–p1p3p4 |
p1p2p3p4 |
|
|
|
11 |
0 |
+ |
+ |
+ |
1,5 |
p1(1–p2)´ |
p1 |
–p1p2–p1p3–p1p4 |
p1p2p3+p1p4p4+ |
-p1p2p3p4 |
|
|
|
|
|
|
|
|
´(1–p3)(1–p4) |
|
|
+p1p3p4 |
|
|
|
|
|
|
|
|
|
åP(Ai) = |
1 |
-p1p2 |
|
-p1p3p4 |
+p1p2p3p4 |
|
|
|
|
|
|
|
|
|
|
|
|
|
П р и м е ч а н и е : В таблице указаны только состояния с суммой рангов еRi ³ 1.

32
1 |
2 |
|
|
3 |
4 |
Рис.6.7. Структурная схема надежности машины
при рангах ремонтных затрат: R1=1,0; R2=0,8; R3=0,2; R4=0,6
1 |
2 |
3 |
4 |
Рис.6.8. Структурная схема надежности машины
при рангах ремонтных затрат: R1=1,0; R2=1,5; R3=0,5; R4=0,2
Для сравнения в табл.6.11 представлены состояния
машины без капитального ремонта (события типа Â). В соответствии с данными табл.6.11
P(Tγ) = p1p2+p1p3p4-p1p2p3p4 = p1[1-(1-p2)(1-p3p4)]. Таким образом, получено то же выражение, что и
по табл.6.10, но с меньшим объемом вычислений. Пример 6.15 [11]. Изделие состоит из четырех уз-
лов, ранги которых R1=1,0, R2=1,5, R3=0,5, R4=0,2. Расчет вероятности работы без капитального ремонта приведен в табл.6.12.
Следовательно, Ð(Tγ)=p1p2, что означает преимущественное влияние на уровень ремонтопригодности машины узлов 1 и 2. Влияние узлов 3 и 4 незначи- тельно даже в случае, когда они оба будут находиться
в капитальном ремонте (R3+R4=0,5+0,2=0,7<1). На рис.6.8 в структурной схеме на связи элементов 3 и 4 опущена стрелка. Это условное обозначение указывает, что суммарный ранг ремонтных затрат узлов 3 и 4 не влияет на предельное состояние машины. Логиче- ская запись такой структурной схемы будет иметь вид
N{Ai} ' {R1ÚR2-(R3ÚR4) = {R1ÚR2}.
Выражения типа (6.35) и (6.36) не всегда приводятся к виду, удобному для образования структурной формулы и построения структурной схемы. В таких случаях в расчет вводится норматив текущего ремонта Zòð, который составляет некоторую долю α от затрат капитального ремонта машины: Zòð=αZêð (0<α<1). Тогда ремонтные затраты на отдельные узлы, ран-
Таблица 6.11
РАСЧЕТ ВЕРОЯТНОСТИ РАБОТЫ МАШИНЫ БЕЗ КАПИТАЛЬНОГО РЕМОНТА
¹¹ |
Номер узла |
Сумма |
|
|
|
|
|
|
|
|||
состо- |
1 |
2 |
3 |
4 |
рангов |
 å ð î ÿ ò í î ñ ò ü |
+M{C0n} |
-M{C1k} |
|
|
+M{C2k} |
|
ÿíèÿ |
|
Ð à í ã |
|
åRi |
ñ î á û ò è ÿ |
|
|
|
|
|
||
|
1,0 |
0,8 |
0,5 |
0,2 |
|
|
|
|
|
|
|
|
1 |
0 |
0 |
0 |
0 |
0,0 |
p1p2p3p4 |
p1p2p3p4 |
|
|
|
|
|
2 |
0 |
+ |
0 |
0 |
0,8 |
p1(1–p2)p3p4 |
p1p3p4 |
–p1p2p3p4 |
|
|
|
|
3 |
0 |
0 |
+ |
0 |
0,5 |
p1p2(1–p3)p4 |
p1p2p4 |
–p1p2p3p4 |
|
|
|
|
4 |
0 |
0 |
0 |
+ |
0,2 |
p1p2p3(1–p4) |
p1p2p3 |
–p1p2p3p4 |
|
|
|
|
5 |
0 |
0 |
+ |
+ |
0,7 |
p1p2(1–p3)(1-p4) |
p1p2 |
–p1p2p3–p1p2p4 |
p1p2p3p4 |
|||
|
|
|
|
|
|
åP(Bi) = |
p1p2+ |
–p1p2p3p4 |
|
|
|
|
|
|
|
|
|
|
|
|
+p1p3p4 |
|
|
|
|
П р и м е ч а н и е : В таблице указаны только состояния с суммой рангов еRi |
< 1. |
|||||||||||
|
|
|
|
|
|
|
|
|
Таблица 6.12 |
|||
|
РАСЧЕТ ВЕРОЯТНОСТИ РАБОТЫ МАШИНЫ БЕЗ КАПИТАЛЬНОГО РЕМОНТА |
|||||||||||
¹¹ |
Номер узла |
Сумма |
|
|
|
|
|
|
|
|||
состо- |
1 |
2 |
3 |
4 |
рангов |
 å ð î ÿ ò í î ñ ò ü |
|
+M{C0n} |
-M{C1k} |
|
|
+M{C2k} |
ÿíèÿ |
|
Ð à í ã |
|
åRi |
ñ î á û ò è ÿ |
|
|
|
|
|
|
|
|
1,0 |
1,5 |
0,5 |
0,2 |
|
|
|
|
|
|
|
|
1 |
0 |
0 |
0 |
0 |
0,0 |
p1p2p3p4 |
|
p1p2p3p4 |
|
|
|
|
2 |
0 |
0 |
+ |
0 |
0,5 |
p1p2(1–p3)p4 |
|
p1p2p4 |
–p1p2p3p4 |
|
|
|
3 |
0 |
0 |
0 |
+ |
0,2 |
p1p2p3(1–p4) |
|
p1p2p3 |
–p1p2p3p4 |
|
|
|
4 |
0 |
0 |
+ |
+ |
0,7 |
p1p2(1–p3)(1-p4) |
|
p1p2 |
–p1p2p3–p1p2p4 |
p1p2p3p4 |
||
|
|
|
|
|
|
åP(Bi) = |
|
p1p2 |
–p1p2p3p4 |
|
|
|
П р и м е ч а н и е : В таблице указаны только состояния с суммой рангов еRi < 1.

33
ги которых находятся в интервале α≤Ri<1, условно приравнивают к капитальному ремонту машины.
Пример 6.16 [11]. Затраты на капитальные ремонты четырех узлов, из которых состоит машина, соответствуют рангам R1 = 0,8, R2 = 0,2, R3 = 0,6, R4 = 0,4. Вероятность состояний типа Â (òàáë.6.13):
P(Tγ) = p1p3 + p1p4 + p2p3p4 - p1p3p4 - p1p2p3p4.
Тогда состояние 7 (см.табл.6.13) можно отнести к типу À и исключить из таблицы,
òàê êàê R1=0,8>a. Вероятность работы машины без капитального ремонта теперь будет подсчитана по шести состояниям, что дает возможность построить структурную схему.
|
|
|
|
|
|
|
|
|
|
|
|
|
Таблица 6.13 |
|||
|
РАСЧЕТ ВЕРОЯТНОСТИ РАБОТЫ МАШИНЫ БЕЗ КАПИТАЛЬНОГО РЕМОНТА |
|||||||||||||||
¹¹ |
Номер узла |
Сумма |
|
|
|
|
|
|
|
|
|
|
|
|||
состо- |
|
|
|
|
рангов |
 å ð î ÿ ò í î ñ ò ü |
|
|
-M{C1k} |
|
|
|
|
|||
1 |
2 |
3 |
4 |
+M{C0n} |
|
|
|
|
+M{C2k} |
|||||||
ÿíèÿ |
|
Ð à í ã |
|
åRi |
ñ î á û ò è ÿ |
|
|
|
|
|
|
|
|
|
|
|
|
0,8 |
0,2 |
0,6 |
0,4 |
|
|
|
|
|
|
|
|
|
|
|
|
1 |
0 |
0 |
0 |
0 |
0,0 |
p1p2p3p4 |
p1p2p3p4 |
−p1p2p4-p1p3p4 |
|
|
||||||
2 |
0 |
+ |
+ |
0 |
0,8 |
p1(1–p2)(1–p3)p4 |
p1p4 |
|
p1p2p3p4 |
|||||||
3 |
0 |
+ |
0 |
+ |
0,6 |
p1(1–p2)p3(1–p4) |
p1p3 |
−p1p2p3-p1p3p4 |
|
p1p2p3p4 |
||||||
4 |
0 |
0 |
0 |
+ |
0,4 |
p1p2p3(1–p4) |
p1p2p3 |
|
–p1p2p3p4 |
|
|
|
p1p2p3p4 |
|||
5 |
0 |
0 |
+ |
0 |
0,6 |
p1p2(1–p3)p4 |
p1p2p4 |
|
–p1p2p3p4 |
|
|
|
|
|||
6 |
0 |
+ |
0 |
0 |
0,2 |
p1(1–p2)p3p4 |
p1p3p4 |
|
–p1p2p3p4 |
|
|
|
|
|||
7 |
+ |
0 |
0 |
0 |
|
(1–p4)p2p3p4 |
p2p3p4 |
|
–p1p2p3p4 |
|
|
|
|
|||
|
|
|
|
|
|
åP(B ) = |
p1p3+p1p4 |
–p |
p |
p |
–p |
p p |
p |
4 |
|
|
|
|
|
|
|
|
i |
++p2p3p4 |
1 |
3 |
4 |
1 |
2 |
3 |
|
|
|
|
|
|
|
|
|
|
|
|
|
|
|
|
|
|
|
П р и м е ч а н и е : В таблице указаны только состояния с суммой рангов еRi < 1. |
|||
Данное выражение не приводится к виду, удобному |
1 |
3 |
|
для построения структурной схемы. Поэтому вводим |
|||
дополнительное условие, по которому ремонтные за- |
|
|
|
траты на отдельные узлы могут быть условно приров- |
2 |
4 |
|
нены к затратам на капитальный ремонт машин, если |
|||
их ранг превышает норматив текущего ремонта маши- |
Рис.6.9. Структурная схема |
||
ны. Пусть норматив текущего ремонта машины a=0,7. |
|||
Выражение для структурной формулы имеет вид |
надежности машины |
||
при рангах ремонтных затрат: |
|||
P(Tγ) = p1p3+p1p4-p1p3p4 = p1[1-(1-p3)(1-p4)]. |
|||
R1=0,8; R2=0,2; R3=0,6; R4=0,4; |
|||
Структурная схема показана на рис.6.9, логическое |
|||
выражение |
|
a = 0,7 |
|
|
|
N{Ai} ' {R1Ú(R3ÙR4)-R2} = {R1Ú(R3ÙR4)}.
В данном случае самый младший (по величине ранга) элемент 2 не учитывается в расчетной формуле вероятности и на схеме он находится под знаком стрелки.
Приведенные примеры расчета структурных схем надежности раскрывают все основные закономерности их формирования.
6.3.2. Расчет структурных схем надежности
Исходными данными для расчета структурных схем являются:
- минимальные оперативные затраты на капитальный ремонт машины при агрегатно-узловом методе его выполнения (Zêð) в единицах времени, трудоемкости или стоимости;
-минимальные оперативные затраты на текущий ремонт машины (Zòð) в сопоставимых единицах измерения;
-оперативные затраты на капитальные ремонты узлов (zi), входящих в машину, в сопоставимых единицах.
34
Порядок расчета структурных схем надежности машин:
1. Определяется отношение нормируемых затрат на текущий и капитальный ремонты
a = Zòð/Zêð. |
(6.42) |
2.Определяются ранги ремонтных затрат узлов Ri = Zòp/Zêp.
3.Составляется упорядоченный ряд рангов ремонтных затрат узлов в порядке убывания их значений:
R1 ³ R2 ³ ... ³ 1 > Ri ³ Ri+1 ³ ... ³ a > Rj ³ Rj+1 ³ ... ³ Rn. |
(6.43) |
Общее число членов ряда равно числу узлов n в машине.
4. По рангам ремонтных затрат с учетом отношения a определяются ремонтные комплекты.
Очевидно, что все узлы, ранг которых Ri³1, составляют сами ремонтные комплекты (последовательно соединенная группа элементов в структурной схеме). Остальные узлы разделяются на три группы. К первой
группе относят узлы, ранги которых 1>Ri³a. Эта группа узлов образует самостоятельные ремонтные комплекты (элементы структурной схемы этой группы соединяются последовательно). Вторая группа узлов образует ремонтные комплекты так, чтобы минимальное число рангов давало
суммарный ранг, равный или превышающий единицу (еRi³1). Все эти элементы одного комплекта образуют параллельное соединение. Исключе- ние составляют элементы, ранги которых с остальными элементами комплекта дают логический вариант “или-или”, такие элементы образуют последовательную цепочку в одном из параллельных звеньев ремонтного комплекта. Оставшаяся группа узлов может образовать самостоятельный
ремонтный комплект, если 1>еRi³a. Если в оставшейся группе суммар-
ный ранг меньше a, то члены этой группы добавляются в ремонтные комплекты, у которых суммарный ранг ремонтных затрат меньше единицы. В структурной схеме эти элементы располагаются под стрелкой.
5.Все ремонтные комплекты соединяются последовательно в структурной схеме. Каждый из узлов должен быть представлен в схеме только одним элементов.
6.По графическому изображению схемы или по логической формуле составляется структурная формула для определения вероятности работы машины без капитального ремонта
P(Tγ) = p1p2...papα1pα2...pαm ³ g, |
(6.44) |
ãäå p1p2...pa - вероятность работы без капитального ремонта узлов 1,2,...,à (для узлов этой группы Ri³1); pαpα1pα2...pαm - вероятность работы комплектов узлов без одновременного капитального ремонта (для узлов, входящих в каждый комплект 1>Ri³a); g - вероятность того, что машина за наработку Tγ не достигнет предельного состояния по избранному критерию Zêð.
7. Выбираются такие значения p1,..., чтобы вероятности работы узлов без капитального ремонта соответствовали требованию, предъявленному к
нормируемой вероятности g для машины в целом (в правой части структурной формулы).
Пример 6.17 [11]. Изделие состоит из n = 10 узлов, ранги ремонтных затрат которых R1=1,2, R2=1,0, R3=0,8, R4=0,75, R5=0,60, R6=0,35, R7=0,2, R8=0,15, R9=0,10, R10=0,05. Норматив текущего ремонта машины определен величиной a = 0,7.

|
|
|
|
35 |
|
|
|
Составим упорядоченный ряд рангов (1,2; 1,0; 0,8; 0,75; a=0,7; 0,60; 0,35; 0,2; 0,15; |
|||||||
0,10; 0,05) и определим ремонтные комплекты. |
|
|
|
||||
Первые четыре ремонтных комплекта образуют узлы с рангами Ri³a, ò.å. óçëû ñ |
|||||||
рангами R1=1,2, R2=1,0, R3=0,8, è R4=0,75. Пятый ремонтный комплект образуется из |
|||||||
узлов 5 и 6: R5+R6 |
= 0,6+0,35 = 0,95. Оставшаяся часть ряда имеет суммарный ранг |
||||||
R7+R8+R9+R10 = 0,2+0,15+0,1+0,05 = 0,5<a, поэтому элементами этой части ряда до- |
|||||||
полним третий, четвертый и пятый комплекты: |
|
|
|
||||
|
|
R3-(R7) = 0,8 + 0,2 = 1,0; |
|
|
|
||
|
|
R4-(R8ÚR9) = 0,75 + 0,15 + 0,1 =1,0; |
|
|
|||
|
|
R5-(R10)+R5 |
= 0,60 + 0,05 + 0,35 = 1,0. |
|
|
||
Теперь можно составить логическую формулу структурной схемы |
|
||||||
|
N{Ai} ' {R1ÚR2Ú[R3-(R7)]Ú[R4-(R8ÚR9)]Ú[R5-(R10)ÙR6]}, |
|
|||||
которая дает возможность построить структурную схему (рис.6.10) и написать уравне- |
|||||||
ние для определения вероятности работы машины без капитального ремонта |
|
||||||
|
|
P(Tγ)=p1p2p3p4p5−6 ³ g/100, |
|
|
|
||
ãäå p5−6 = 1 - (1 - p5)(1 - p6). |
|
|
|
|
|
||
Пусть g = 80%, тогда, чтобы выполнить требование по уровню g для машины в це- |
|||||||
лом, необходимо задаться значениями вероятности капитального ремонта по каждому |
|||||||
узлу. Пусть |
|
|
|
|
|
|
|
Тогда |
p1 = p2 = p3 = p4 = 0,95; p5 = p6 = 0,9; p7 = p8 = p9 = p10 = 0,8; |
|
|||||
|
p5−6 = 1 - (1 - 0,9)2 = 1 - 0,12 = 0,99; |
|
|
||||
|
|
|
|
||||
Таким |
образом, |
P(Tγ) = 0,954×0,99 = 0,815×0,99 = 0,807 > 0,8. |
|
||||
выдвинутые |
|
3 |
|
4 |
5 |
||
требования по величине gi äëÿ óç- |
|
|
|||||
лов удовлетворяют условию по- |
|
|
|
|
|
||
ставленной задачи по обеспече- |
1 |
2 |
|
|
10 |
||
нию требования по уровню g для |
|
|
|||||
машины в целом. |
|
|
|
|
|
|
|
Если ставится задача, чтобы за |
|
7 |
8 |
9 |
6 |
||
весь ресурс машины с вероятно- |
|
||||||
стью 0,8 не производилось ни од- |
Рис.6.10. Структурная схема надежности машины |
||||||
ного капитального ремонта любого |
|||||||
узла, то все 10 узлов становятся |
|
из десяти узлов (к примеру 6.17) |
|
||||
базовыми. И в этом случае для |
|
|
|
|
|
||
обеспечения выдвинутых требований необходимо, чтобы каждый из них обладал ресур- |
|||||||
сом с вероятностью не менее 0,98. Тогда |
|
|
|
|
|||
|
|
P(Tγ) = 0,9810 = 0,817 >0,8. |
|
|
|
Рассмотренные примеры показывают универсальность структурных схем, отражающих разнообразие требований к надежности машин различ- ного класса и назначения, и преобразующих исходную информацию в новую информацию в соответствии со своей внутренней организацией. Являясь информационно-логической системой, структурная схема способна отражать и преобразовывать как требования к ремонтопригодности и долговечности (если выдвигается критерий предельного состояния машины в любом его проявлении), так и требования в безотказности (если критерий предельного состояния отсутствует, а важен лишь факт наличия отказа исследуемой машины). Структурные схемы объективно отражают различ- ную постановку задач исследования долговечности, ремонтопригодности и безотказности и поэтому являются основным средством решения проблемы управления надежностью при проектировании.
Прогнозирование надежности машин при проектировании с целью определения единичных показателей надежности проектируемого варианта и сопоставления прогнозируемых показателей надежности проектируемого варианта с требуемыми значениями выполняется по ГОСТ 27.301-83 [21].
36
При прогнозировании надежности машины рассматриваются как сложные системы, общая структурная схема которых должна быть представлена в виде двух групп подсистем: основная группа (минимальная структура) и обеспечивающие подсистемы (избыточная структура).
Машину можно разбить на подсистемы, у которых основными критериями, определяющими их надежность, является прочность, герметич- ность, износостойкость и т.д. Соответственно, вероятность безотказной работы машины в целом
P(t) = PÏ(t)×PÃ(t)×PÌ(t) ..., |
(6.45) |
ãäå Pn(t) - вероятность безотказной работы подсистем, у которых основным критерием,
определяющим надежность, является прочность; PÃ(t) - вероятность безотказной работы подсистем, у которых основным критерием, определяющим надежность, является
герметичность; PÌ(t) - вероятность безотказной работы подсистем, у которых основным критерием, определяющим надежность, является точность изготовления деталей.
6.3.3. Требования к ресурсам сборочных единиц
На стадии разработки технического задания нормируемыми показателями надежности являются, как правило, средний и гамма-процентный ресурсы. Изделий, имеющих наработку, равную или большую гаммапроцентному ресурсу, должно быть не менее 80% (для большинства изделий машиностроения) [11].
Наиболее часто встречающиеся законы распределения ресурсов для изделий машиностроения нормальный, логарифмически нормальный и Вейбулла.
Соотношение между средним и гамма-процентным ресурсами можно представить в виде соотношения
Kγ = T/Tγ, |
(6.46) |
ãäå Kγ - коэффициент, зависящий от вида распределения (прил.V).
При нормальном законе распределения значения гамма-процентного и среднего ресурсов находятся также по выражению
Tγ/T = 1 - uγv, |
(6.47) |
ãäå uγ - квантиль нормального распределения, соответствующая величине γ (ñì.ïðèë.I); σ - среднее квадратическое отклонение ресурса; v - коэффициент вариации.
При проектировании новых машин одной из существенных трудностей является определение характера распределения ресурса будущей машины. Основным методом оценки распределения ресурса является анализ статистических данных о ресурсах изделий аналогичного класса и назначения.
Точность в оценке вида и параметров распределения ресурса зависит от правильности учета факторов, влияющих на разброс значений ресурса. При выборе закона распределения ресурса проектируемого изделия целесообразно пользоваться коэффициентом вариации. Установлено, что основными факторами, оказывающими основное влияние на величину разброса статистических данных о ресурсах изделий, являются характер разрушения базового элемента, стабильность условий эксплуатации, степень нагруженности изделия и уровень технологии его изготовления (табл.6.2 и 6.3). При стабильных условиях и режимах работы при изнашивании проявляется нормальный закон распределения ресурса, при усталостном разрушении - закон Вейбулла. Условия работы изделия, оцениваемые интен-
37
сивностью использования во времени, влиянием климатических воздействий и уровнем технического обслуживания и хранения техники, являются важным фактором, определяющим разброс ресурсных характеристик. При режимах нагружения, близких к максимальным, коэффициент вариации меньше, чем при режимах, характеризующих средние нагрузки. На разброс ресурса оказывает существенное влияние уровень технологии изготовления изделия, характеризуемый множеством факторов. Среди них важное место занимают уровень серийности, степень унификации и стандартизации применяемых сборочных единиц, степень специализации производства, наличие средств объективного контроля качества изготовления, стабильность применяемых материалов, степень использования прогрессивных технологических процессов. Чем выше уровень технологии, тем меньше причин для увеличения разброса ресурса изделия.
Анализ предполагаемых условий эксплуатации и режимов нагружения будущей машины, а также учет технологических факторов ее изготовления позволяет установить в первом приближении вид закона распределения ресурса машины до первого капитального ремонта и численное значе- ние коэффициента вариации этого распределения (табл.6.3). По заданному значению гамма-процентного ресурса по формулам вида (6.47) или номограммам (см.прил.V) можно определить средний ресурс машины, т.е. определить ремонтный цикл, в пределах которого устанавливается периодич- ность текущих ремонтов машины.
Наработка машины до замены основных (базовых) узлов должна быть не менее ее среднего ресурса до капитального ремонта. Затраты на капитальный ремонт или замену любого узла или группы узлов машины в периоды ее текущих ремонтов не должны превышать установленного норматива, а периодичность таких ремонтов должна быть кратной ремонтному циклу машины, т.е. должно выполняться условие
Ti = T1ê/Ni ïðè Ri << a, åRi £ a; Ti = NiT1ê ïðè Ri ³ a, (6.48)
ãäå Ti- наработка машины до замены (или капитального ремонта) i-ãî óçëà; T1ê- средний ресурс машины до первого капитального ремонта; Ni - кратность замены узла.
Условие (6.48) определяет требования к назначению ресурсных показателей узлов машины. Значение среднего ресурса должно быть вычислено по назначенной наработке с учетом коэффициента использования узла в рабочем цикле машины, а также в других операциях (транспортировании, монтаже, демонтаже и т.д.)
Ti = TiKi, |
(6.49) |
ãäå Ti - средний ресурс узла в собственных единицах наработки; Ki = KâiKãði - коэффициент использования узла в рабочих и вспомогательных операциях машины; Kâi - êî-
эффициент использования по времени; Kãði - коэффициент использования по нагрузке узла в рабочих и вспомогательных операциях машины.
Условие (6.48) является необходимым, но еще не достаточным для окончательного назначения требуемых ресурсов узлов, обеспечивающих заданный ресурс машины до первого капитального ремонта или другого предельного состояния. Это условие определяет минимальные значения ресурсов узлов, но не обеспечивает требования, определяемые структурной схемой машины. Для решения этой задачи необходимо проанализировать условия эксплуатации и режимы нагружения каждого узла, а также
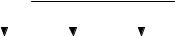
38
оценить уровень технологии их изготовления. На основе такого анализа можно определить вид распределения ресурса каждого узла с соответствующим коэффициентом вариации. Тогда по формуле (6.47) можно полу- чить значения гамма-процентных ресурсов для каждого узла:
Tγi = Ti(1 - uγivi) (6.50)
Гамма-процентная наработка машины до замены или капитального ре-
монта i-ãî óçëà |
|
Tγi = Tγi/Ki = Ti(1 - uγivi). |
(6.51) |
Эта наработка для узлов, для которых Ri ³ a, должна быть приблизительно равна гамма-процентному ресурсу машины до предельного состоя-
ния, т.е. должно выполняться условие Tγi/Tγ » 1. Если для какого-либо
óçëà ïðè Ri ³ a это отношение существенно меньше единицы (менее 0,6), то средняя наработка машины до замены или капитального ремонта данного узла должна превышать не менее чем вдвое средний ресурс машины до ее первого капитального ремонта. К такой категории узлов машин можно отнести узлы металлоконструкций несущих систем, опорно-поворотные устройства, системы гидро- и электроприводов, характер разрушений в которых связан с явлениями усталости и внезапными отказами, вследствие которых ресурс изделий распределяется с положительной косостью. Обычно такие распределения подчиняются закону Вейбулла с коэффици-
ентами вариации 0,35¸0,70. Поэтому такие узлы должны иметь либо высокий уровень среднего ресурса (основные узлы металлоконструкций машин обычно работают весь срок службы машины до ее списания), либо обладать высокими уровнями показателей ремонтопригодности (гидросистемы, электропривод и др.).
6.3.4. Прогнозирование ресурса и затрат на капитальный ремонт
Поскольку в структурной формуле надежности машины заключена информация о вероятности появления предельного состояния по заданному критерию минимума оперативных ремонтных затрат, то с помощью структурной формулы можно прогнозировать распределение ресурса машины и функцию распределения затрат на капитальный ремонт (или затрат на восстановление работоспособности машины, если она может работать без капитального ремонта весь срок службы).
Пример 6.18 [11]. Машина, состоящая из 10 узлов, ранги которых R1 = 1,0, R2 =
0,85, R3 = 0,80, R4 = 0,70, R5 = 0,50, R6 = 0,45, R7 = 0,30, R8 = 0,20, R9 = 0,10, R10 = 0,05, должна обладать 80%-ным ресурсом до первого капитального ремонта не менее
10000 ÷, а относительные затраты на текущие ремонты не должны быть более a=0,7. За весь срок службы до списания требуется проводить один капитальный ремонт. Исходя из условий эксплуатации машины, режимов ее нагружения и технологии изготов-
|
|
|
|
|
|
|
|
|
|
|
|
|
|
|
|
|
|
|
ления можно считать, что распределение ре- |
|
|
|
|
|
|
3 |
|
|
|
4 |
|
|
|
5 |
|
||||
|
|
|
|
|
|
|
|
|
|
|
|
|
сурса подчиняется нормальному закону с ко- |
||||||
|
|
|
|
|
|
|
|
|
|
|
|||||||||
|
|
|
|
|
|
|
|
|
|
|
|
|
|
|
|
|
|
|
эффициентом вариации 0,2 (см.табл.6.3). |
|
|
|
|
|
|
|
|
|
|
|
|
|
|
|
|
|
|
|
|
|
|
|
|
|
|
|
|
|
|
|
|
|
|
|
|
|
|
|
Средний ресурс машины до первого капи- |
|
1 |
|
2 |
|
|
|
|
|
|
|
7 |
|
|
|
6 |
|
тального ремонта по формуле (6.47) |
||
|
|
|
|||||||||||||||||
|
|
|
|
|
|
|
|
|
|
|
|
|
|
|
|
|
|
|
T1ê=Tγ/(1-uγv)=10000/(1-0,8416×0,2)»12000, |
|
|
|
|
|
|
|
|
|
|
|
|
|
|
|
|
|
|
|
|
|
|
|
|
|
|
|
|
|
|
|
|
|
|
|
|
|
|
|
ãäå uγ = 0,8416 - квантиль нормального рас- |
|
|
|
|
|
|
|
|
|
|
|
|
|
|
|
|
|
|
|
|
|
|
|
|
|
|
8 |
|
|
|
9 |
|
|
|
10 |
|
пределения при g=0,8 (см.прил.I). |
|||
|
|
|
|
|
|
|
|
|
|
|
|||||||||
|
|
|
|
|
|
|
|
|
|
|
|
|
|
|
|
|
|
|
Схема надежности в соответствии с рангами |
|
|
Рис.6.11. Структурная схема |
|||||||||||||||||
|
|
узлов представлена на рис.6.11. |
|||||||||||||||||
|
надежности землеройной машины |
||||||||||||||||||
|
|
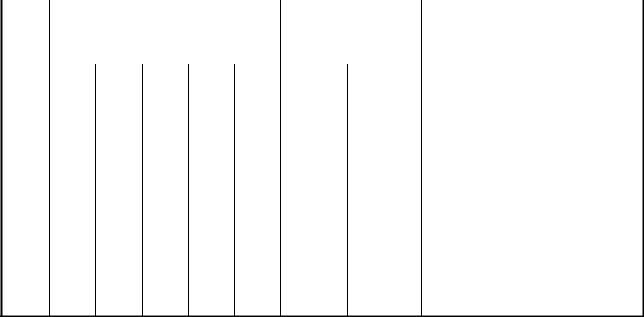
39
По структурной схеме формула вероятности работы без капитального ремонта
P(Tγ)=p1p2p3[1-(1-p4)(1-p7)][1-(1-p5)(1-p6)]³0,8. Примем следующие значения вероятностей узлов:
|
¹ óçëà |
1 |
|
2 |
|
3 |
4 |
5 |
|
6 |
7 |
8 |
9 |
10 |
|||
|
|
pi |
0,95 |
|
0,95 |
|
0,95 |
0,9 |
0,9 |
0,8 |
0,8 |
0,8 |
0,8 |
0,8 |
|||
Тогда |
|
|
|
|
|
|
|
|
|
|
|
|
|
|
|
||
|
p4−7 = 1 - (1 - 0,9)(1 - 0,8) = 0,98; |
p5−6 = 1 - (1 - 0,9)(1 - 0,8) = 0,98; |
|||||||||||||||
|
|
|
|
|
|
|
P(Tγ) = 0,953 × 0,982 = 0,823 > 0,8. |
|
|
|
|||||||
Предположим, что после анализа условий и режимов работы каждого узла удалось |
|||||||||||||||||
установить вид распределения ресурса и его коэффициент вариации (табл.6.14). |
|||||||||||||||||
|
|
|
|
|
|
|
|
|
|
|
|
|
|
|
|
Таблица 6.14 |
|
|
|
|
|
|
|
|
ТРЕБОВАНИЯ К НАРАБОТКЕ УЗЛОВ |
|
|
|
|||||||
|
|
|
|
|
|
|
|
|
|
|
|
|
|
|
|
||
¹ |
|
|
|
Исходные данные |
|
Наработка |
|
Условия замены узлов |
|||||||||
|
|
|
|
мащины |
|
||||||||||||
óçëà |
|
|
|
|
|
|
|
|
до замены узлов, |
|
по средней наработке |
||||||
|
|
|
|
|
|
|
|
|
|
|
òûñ.÷. |
|
|
|
|
|
|
|
|
p |
i |
распр. |
v |
i |
Kγ |
i |
R |
T |
|
Tγ |
i |
|
|
|
|
|
|
|
|
|
|
i |
i |
|
|
|
|
|
|
||||
1 |
0,95 |
 |
0,45 |
3,33 |
1,00 |
36 |
|
10,8 |
Работа до списания |
|
|||||||
2 |
0,95 |
 |
0,50 |
3,70 |
0,85 |
36 |
|
9,75 |
Работа до списания |
|
|||||||
3 |
0,95 |
Í |
0,20 |
1,47 |
0,80 |
24 |
|
16,3 |
Работа до списания |
|
|||||||
4 |
0,90 |
Í |
0,25 |
1,43 |
0,60 |
12 |
|
8,4 |
При капитальном ремонте |
||||||||
5 |
0,90 |
 |
0,35 |
2,00 |
0,50 |
24 |
|
12,0 |
Работа до списания |
|
|||||||
6 |
0,80 |
Í |
0,15 |
1,17 |
0,45 |
12 |
|
10,25 |
При капитальном ремонте |
||||||||
7 |
0,80 |
Í |
0,20 |
1,20 |
0,30 |
4 |
|
3,3 |
При капитальном ремонте |
||||||||
|
|
|
|
|
|
|
|
|
|
|
|
|
|
или текущих ремонтах T2 и Т |
|||
8 |
0,80 |
Í |
0,25 |
1,25 |
0,20 |
2 |
|
1,6 |
При ремонтах всех видов |
||||||||
9 |
0,80 |
Í |
0,25 |
1,25 |
0,10 |
6 |
|
4,8 |
При капитальном ремонте |
||||||||
|
|
|
|
|
|
|
|
|
|
|
|
|
|
или текущем ремонте Т3 |
|||
10 |
0,80 |
Í |
0,20 |
1,20 |
0,05 |
12 |
|
10,0 |
При капитальном ремонте |
Предположим, что "слабым" звеном является узел 8 с рангом R8=0,2. Продолжи-
тельность работы машины до замены узла 8 равна 2000 ÷. Следовательно, кратность замены узла определит число текущих ремонтов (Т1, Т2 и т. д.), которые будут выполняться в первом ремонтом цикле (до капитального ремонта К) с периодичностью:
Вид ремонта |
Ò1 |
Ò2 |
Ò3 |
Ò4 |
Ò5 |
Ê |
Наработка, ÷ |
2000 |
4000 |
6000 |
8000 |
10000 |
12000 |
Из табл.6.14 следует, что для обеспечения гамма-процентного ресурса машины необходимо задавать высокие требования к ресурсам некоторых узлов, поскольку распределения этих ресурсов существенно отличаются своими коэффициентами вариации от распределения ресурса машины. Кажущаяся избыточность средних ресурсов таких узлов обусловлена необходимостью обеспечения гамма-процентного ресурса машины. Вы-
полнение условия (6.48) легко контролируется суммарными затратами |
в каждом теку- |
|||||||||||
щем ремонте (табл.6.15). |
|
|
|
|
|
|
|
|||||
Таким |
образом, ни в од- |
|
|
|
|
|
|
|||||
ном из текущих ремонтов не |
|
|
|
|
Таблица 6.15 |
|||||||
превышен |
|
установленный |
ПЛАНИРУЕМЫЕ ЗАТРАТЫ В ТЕКУЩИХ РЕМОНТАХ |
|||||||||
норматив a=0,7. |
|
|
|
|||||||||
|
|
|
Номер |
Наработка |
|
Ðàíã |
|
Суммарный |
||||
Рассмотрим |
изменение |
Номер |
|
|||||||||
функции |
распределения |
âå- |
текущего |
машины, |
óçëà |
ремонтных |
ðàíã |
|||||
роятностей |
ïî |
|
данным |
ремонта |
÷ |
|
затрат |
|
ремонтных |
|||
òàáë.6.15. |
|
После |
анализа |
|
|
|
|
|
затрат |
|||
|
Ò1 |
2000 |
8 |
0,2 |
|
0,2 |
||||||
ремонтопригодности |
âñåõ |
|
||||||||||
Ò2 |
4000 |
7 |
0,3 |
|
|
|||||||
узлов установлено, что узлы |
|
0,5 |
||||||||||
8, 9 и 10 по рангам ремонт- |
|
|
8 |
0,2 |
|
|
||||||
íûõ |
затрат |
íå |
влияют |
íà |
Ò3 |
6000 |
8 |
0,2 |
|
0,3 |
||
предельное |
состояние |
ìà- |
|
|
9 |
0,1 |
|
|||||
|
|
|
|
|||||||||
шины. Поэтому эти узлы не |
Ò4 |
8000 |
7 |
0,3 |
|
0,5 |
||||||
вошли в структурную фор- |
|
|
8 |
0,2 |
|
|||||||
|
|
|
|
|||||||||
ìóëó |
надежности. |
Èç |
âî- |
Ò5 |
10000 |
8 |
0,2 |
|
0,2 |

|
|
|
|
|
|
40 |
|
|
|
|
|
|
|
|
|
|
|
|
|
|
шедших в структурную формулу узлов только один узел 7 трижды меняется в доре- |
||||||||||||||||||||
монтном цикле. Остальные узлы либо работают до списания машины, либо заменяются |
||||||||||||||||||||
при ее капитальном ремонте (см.табл.6.14). Введем в структурную формулу надежно- |
||||||||||||||||||||
сти машины вместо частных значений вероятностей обеспечения ресурсов узлов сами |
||||||||||||||||||||
функции распределения обеспечения этих ресурсов: |
|
|
|
|
|
|
|
|
|
|
||||||||||
|
P(Tγ) = p1(t)p2(t)p3(t){1−[1−p4(t)][1−p7(3)(t)]}{1−[1−p5(t)][1−p6(t)]}, |
|
|
|||||||||||||||||
ãäå p7(3)(t) - функция распределения обеспечения ресурса узла 7 для третьей замены. |
|
|||||||||||||||||||
Параметры распределения вероятностей обеспечения ресурса i-ãî óçëà ïðè k-îé çà- |
||||||||||||||||||||
мене определяем из соотношений: |
|
|
|
|
|
|
vi( |
|
|
|
|
|
|
|
|
|
||||
|
Mi( |
k |
)(T) |
1 |
σi( |
k |
|
|
1 |
|
k |
|
1 |
|
k , |
|
|
|
|
|
|
|
= Mi( )(T)k; |
|
) = σi( ) |
k; |
|
) = vi( ) |
|
|
|
(6.52) |
|||||||||
ãäå M |
(1)(T) - математическое ожидание ресурса i-го узла до первой замены; σ (1), v (1) |
- |
||||||||||||||||||
|
i |
|
|
|
|
|
|
|
|
|
|
|
|
|
|
|
|
i |
i |
i- |
среднее квадратическое отклонение и коэффициент вариации распределения ресурса |
||||||||||||||||||||
го узла до первой замены. |
|
|
|
|
|
|
|
|
|
|
|
|
|
|
|
|
||||
Узел 7 заменяется в среднем через каждые 4000 ÷ наработки машины. Коэффициент |
||||||||||||||||||||
вариации до первой замены был принят 0,2. Расчет параметров распределений при ка- |
||||||||||||||||||||
ждой из трех замен дает следующие результаты: |
|
1 |
|
|
|
2 |
|
3 |
|
|
||||||||||
|
¹ замены узла 7, k |
|
|
|
|
|
|
|
|
|
|
|
|
|||||||
|
Средняя наработка до замены M(k)(T7) |
|
4000 |
|
8000 |
12000 |
|
|
||||||||||||
|
Коэффициент вариации v7(k) |
|
|
|
|
|
0,200 |
|
0,141 |
0,115 |
|
|
||||||||
|
Среднее квадратическое отклонение σ7 |
(k) |
800 |
|
1130 |
1380 |
|
|
||||||||||||
|
Расчет |
распределения |
вероятностей |
|||||||||||||||||
P(Tγ) |
|
|
|
|
|
|
обеспечения ресурса машины выполняет- |
|||||||||||||
1 |
|
|
|
|
|
|
|
|||||||||||||
|
|
|
2 |
|
|
|
ñÿ |
с помощью |
ÝÂÌ. Íà |
ðèñ.6.12 |
ïðåä- |
|||||||||
|
|
|
|
|
|
|
ставлены графики двух кривых распреде- |
|||||||||||||
|
|
|
|
|
|
|
|
|||||||||||||
0,75 |
|
|
|
|
|
|
|
ления. Кривая 1 является предваритель- |
||||||||||||
|
|
|
|
|
|
|
ной функцией распределения вероятно- |
|||||||||||||
|
|
|
|
|
|
|
|
сти обеспечения ресурса с математиче- |
||||||||||||
|
|
|
1 |
|
|
|
ским ожиданием 12000 ÷ и коэффициен- |
|||||||||||||
0,5 |
|
|
|
|
|
том вариации 0,2 для нормального зако- |
||||||||||||||
|
|
|
|
|
|
|
на. Кривая 2 представляет собой восста- |
|||||||||||||
|
|
|
|
|
|
|
|
новленную функцию распределения с ма- |
||||||||||||
|
|
|
|
|
|
|
|
тематическим ожиданием 12433 ÷ è êî- |
||||||||||||
0,25 |
|
|
|
|
|
|
|
эффициентом |
|
вариации |
0,20232. |
Ýòà |
||||||||
|
|
|
|
|
|
|
кривая имеет незначительную отрица- |
|||||||||||||
|
|
|
|
|
|
|
|
|||||||||||||
|
|
|
|
|
|
|
|
тельную косость. |
|
|
|
|
|
|
||||||
0 |
|
|
|
|
|
|
|
|
|
Рассмотренный |
метод |
прогнози- |
||||||||
7,5 |
|
10 |
12,5 |
|
|
|
рования |
ресурса |
äàåò |
возможность |
||||||||||
5 |
|
t, òûñ.÷ |
контролировать |
правильность |
ðàç- |
|||||||||||||||
|
|
|
|
|
||||||||||||||||
Рис.6.12. Функция обеспечения ресурса [11] |
работки |
требований |
ê |
ресурсным |
||||||||||||||||
показателям сборочных единиц и уровням их ремонтопригодности. Он мо- |
||||||||||||||||||||
жет использоваться также для оценки ресурса машины по эксплуатацион- |
||||||||||||||||||||
ной информации о распределениях ресурсов сборочных единиц. С помощью |
||||||||||||||||||||
ЭВМ этот метод контроля позволяет активным образом управлять показа- |
||||||||||||||||||||
телями долговечности и ремонтопригодности сборочных единиц путем про- |
||||||||||||||||||||
верки различных вариантов и выбора наилучшего их них для заданных по- |
||||||||||||||||||||
казателей надежности машины. При этом погрешность вычисления значе- |
||||||||||||||||||||
ния вероятности обеспечения ресурса машины не превышает ±5%. |
|
|
||||||||||||||||||
При проведении структурного анализа надежности машины в качестве |
||||||||||||||||||||
критерия оценки предельного состояния была избрана средняя продолжи- |
||||||||||||||||||||
тельность (трудоемкость) капитального ремонта машины Zêð при продол- |
||||||||||||||||||||
жительности (трудоемкости) капитального ремонта каждой сборочной еди- |
||||||||||||||||||||
íèöû zi. Однако реализация этих затрат зависит от вероятности их появ- |
||||||||||||||||||||
ления, поэтому при определении общих трудовых затрат |
необходимо ус- |
|||||||||||||||||||
тановить вероятность этой реализации по структурной схеме машины. |
|
|