
16
.pdf1
МИНИСТЕРСТВО ОБРАЗОВАНИЯ РОССИЙСКОЙ ФЕДЕРАЦИИ
МОСКОВСКИЙ ГОСУДАРСТВЕННЫЙ ТЕХНИЧЕСКИЙ УНИВЕРСИТЕТ «МАМИ»
Кафедра «Детали машин и ПТУ»
Утверждено методической комиссией по общетехническим дисциплинам
А.С. ЛУКЬЯНОВ
С.А. СТАРОДУБЦЕВА
РАСЧЕТ КОНИЧЕСКИХ ЗУБЧАТЫХ ПЕРЕДАЧ
С ПРЯМЫМИ И КРУГОВЫМИ ЗУБЬЯМИ
Методические указания к разделу курса «Детали машин и основы конструирования»для студентов всех машиностроительных специальностей
МОСКВА-2001
2
Лукьянов Александр Сергеевич |
старший преподаватель |
Стародубцева Светлана Александровна |
доцент, кандидат технических наук |
Расчёт конических зубчатых передач с прямыми и круговыми зубьями. Методические указания к разделу курса «Детали машин и основы конструирования»для студентов всех машиностроительных специальностей
Настоящие методические указания составлены в помощь студентам, выполняющим домашнее задание №2 по курсу «Детали машин и основы конструирования», в котором предложено рассчитать по условиям работы и нагружения привод с редуктором, содержащий коническую зубчатую передачу с прямыми или круговыми зубьями.
Ниже приводятся методика расчёта конической зубчатой передачи с прямыми и круговыми зубьями, а также пример выполнения расчёта.
Содержание
1 Основные сведения о конических передачах |
Стр. |
|
3 |
||
2 Проектировочный расчет закрытой конической |
|
|
|
зубчатой передачи по контактным напряжениям |
5 |
2.1 |
Исходные данные |
5 |
2.2 |
Выбор материала зубчатых колес и их термообработки |
5 |
2.3 |
Выбор точности изготовления |
7 |
2.4 |
Выбор коэффициента относительной ширины Кbе |
7 |
2.5 |
Выбор среднего угла наклона зуба βm |
7 |
2.6 |
Определение углов делительных конусов δ1 и δ2 |
7 |
2.7 |
Определение коэффициентов нагрузки КH и КF |
7 |
2.8Определение коэффициентов υH и υF , учитывающих
вид конической передачи |
9 |
2.9Определение допускаемых контактных напряжений [σ]H
|
при проектировочном расчете |
|
2.10 |
Внешний делительный диаметр колеса |
10 |
2.11 |
Расчет геометрических параметров конической передачи |
10 |
3. |
Скорость и силы в зацеплении |
13 |
3.1Определение действительного значения средней
3.2 |
окружной скорости Vm |
13 |
Силы в зацеплении конических передач |
13 |
|
4. |
Проверочные расчеты |
|
4.1 |
Проверочный расчет на сопротивление контактной усталости |
14 |
4.2 |
Проверочный расчет на сопротивление усталости при изгибе |
15 |
4.3Проверочный расчет на прочность при действие
|
максимальной нагрузки |
17 |
5 |
Особенности расчета открытых конических зубчатых |
|
|
передач |
17 |
6 |
Пример расчета конической зубчатой передачи |
|
|
с круговыми зубьями |
18 |
|
Приложения |
26 |
|
Список литературы |
28 |
Московский государственный технический университет «МАМИ», 2001.
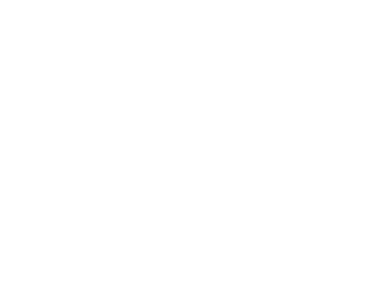
3
1Основные сведения о конических передачах
Конические зубчатые колеса используются в передачах, оси валов которых пересекаются под межосевым углом ∑ = 100...1700. Наиболее распространенными являются ортогональные передачи с ∑ =900 (рис.1).
Рис. 1 Коническая передача
Где : Re - внешнее конусное расстояние; b - ширина венца; δ - угол делительного конуса; de - диаметр внешней делительной окружности; dae - внешний диаметр вершин; he - наибольшая высота зубьев(у торца); hae - наибольшая высота головки зубьев(у торца); θf - угол ножки зубьев; δa - угол конуса вершин; δf -угол конуса впадин; A - расчетное базовое расстояние.( Индекс 1- для шестерни, 2- для колеса).
Конические передачи дороже цилиндрических в изготовлении и сложнее в
монтаже, |
используются при необходимости обеспечения заданной компоновки. |
Понижающие конические передачи рекомендуют выполнять с передаточным |
|
числом |
до 10. Предпочтительнее 6,3.Для повышающих передач передаточное число не |
рекомендуют принимать более 3,15.
Конические зубчатые колеса выполняют с прямыми, косыми(тангенсальными) и круговыми зубьями. Прямозубые колеса обладают наименьшей нагрузочной способностью. Их применяют в неответственных передачах с окружными скоростями до 3 м/с при не приработанных, и до 10 м/с при приработанных зубьях. При переменных нагрузках применяют прямозубые колеса с бочкообразными зубьями и локализованным пятном контакта. Длина образующей начального конуса 6...2500 мм, модуль 0,4...30 мм.
Косозубые колеса допускают окружные скорости до 12 м/с, имеют большую нагрузочную способность по сравнению с прямозубыми, но применяются редко из-за сложности изготовления. Их применяют, как правило, для крупных ответственных передач при мелкосерийном и индивидуальном производстве. Длина образующей начального конуса 400...800 мм, модуль свыше 15мм. Средний угол наклона βm рекомендуют принимать равным 200,250 или300.
Круговые зубья предпочтительней, т.к. они технологичнее и обладают более высокой несущей способностью и меньшей чувствительностью динамическим нагрузкам. Их применяют для ответственных тяжело нагруженных передач, работающих
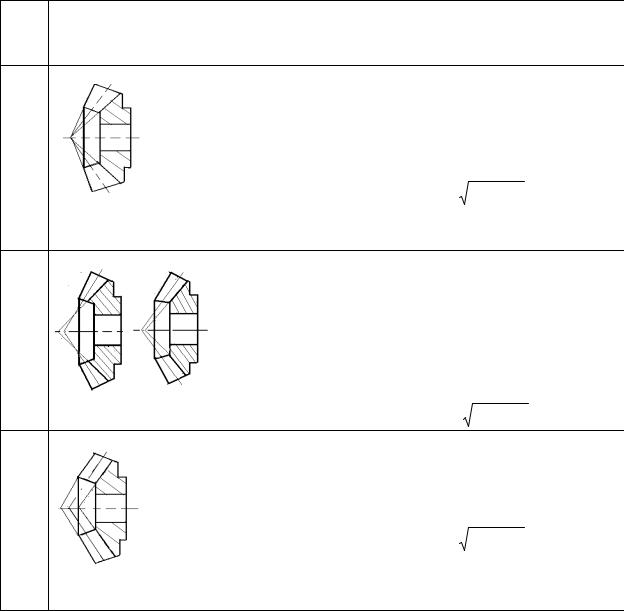
4
при постоянных и переменных нагрузках с окружными скоростями до 11 м/с при не приработанных , и до 35 м/с при приработанных зубьях. Допускаемые длины образующих начального конуса 6...420 мм. Средний угол наклона βm=350.
Для наилучшего обеспечения различных технологических требований, предусмотрено использование трех осевых форм зубьев конических колес. Характеристики и области применения зубьев различной формы с исходным контуром по СТ СЭВ 516-77 указаны в Табл.1
Форма зубьев
1
2
3
Характеристики и области применения осевых форм зубьев конических зубчатых колес (ГОСТ 19325-73)
|
|
|
|
Таблица 1 |
Эскиз |
Характеристика |
Область применения |
||
|
Пропорционально понижа- |
Зубчтые колеса с прямыми |
||
|
ющиеся зубья. Вершины |
зубьями. Зубчатые колеса с |
||
|
кону-сов делительного и |
круговыми зубьями при |
||
|
впадины совпадают. |
mn =2...2,5 мм; |
||
|
Высота ножки зубьев |
R =60...650 мм; βn =0...450; |
||
|
пропорциональна |
Zc = |
Z2 |
+ Z2 = 20...100 |
|
конусному расстоянию. |
|
1 |
2 |
|
Понижающиеся зубья. |
Зубчатые колеса с танген- |
||
|
Вершины конусов |
сальными зубьями. Зубчатые |
||
|
делитель-ного и впадин не |
колеса с круговы-ми зубьями |
||
|
совпадают. |
при |
|
|
|
|
mn =0,4...25 мм; |
||
|
|
R =6...700 мм; βn =0...150 ( |
||
|
|
допускается до 450); |
||
|
|
Zc = |
Z12 + Z22 =24...100 |
|
|
Равновысокие зубья. |
Зубчатые колеса с круго- |
||
|
Образующие конусов дели- |
выми зубьями при |
||
|
тельного, впадин и вершин |
mn =2...25 мм; |
||
|
параллельны. Высота |
R=75...750 мм; βn =25...450; |
||
|
зубьев постоянна по всей |
Zc = |
Z2 |
+ Z2 >40. |
|
длине. |
|
1 |
2 |
|
|
|
|
|
Измерение прямозубых конических колес осуществляется по внешнему дополнительному конусу. Исходный контур прямозубых колес регламентирован СТ СЭВ 515-77 со следующими параметрами: αn =200 (угол профиля) ;ha* =1 (коэффициент высоты головки) ; с*=0,2 (коэффициент радиального зазора).
5
Для колес с круговыми зубьями параметры исходного контура по СТ СЭВ 515-77
αn =200, ha*=1, с*=0,25.
Внешний окружной модуль (me и mte) стандартизирован.
Средний расчетный нормальный модуль (mnm) может быть любым, в том числе и дробным.
Точность определения линейных размеров не ниже 0,1 мм, угловых-1′, тригонометрических- 0,00001.
2 Проектировочный расчет закрытой конической зубчатой
передачи по контактным напряжениям
2.1 Исходные данные:
1.Тип передачи (открытая или закрытая).
2.Межосевой угол ∑.
3.Передаточное число u .
4.Частота вращения вала шестерни n1 (мин-1).
5.Вращающий момент на колесе T2 (Н м).
6.Режим работы.
7.Требуемый ресурс Lh (час).
2.2 Выбор материала зубчатых колес и их термообработки
Материал колес и их термообработку выбирают в зависимости от назначения передачи, требований к габаритам и технологии изготовления. В редукторах при отсутствии жестких требований к размерам и при небольшой мощности используют нормализованные улучшенные колеса до твердости ≤ 350 НВ. Твердость шестерни из-за большей частоты нагружения должна быть выше твердости колеса на 25-30 НВ. Более широко используются колеса с поверхностным упрочнением зубьев. Тогда твердость поверхностей зубьев шестерни и колеса делают одинаковой. Применяют также комбинацию шестерни с поверхностным упрочнением зубьев и с улучшенным колесом.
Наиболее распространены, пять комбинаций термообработок зубьев шестерни и колеса (Табл.2).
Таблица 2
Вариант комбинаций |
1 |
2 |
3 |
4 |
5 |
|||
термообработок |
||||||||
|
|
|
|
|
||||
|
|
Шестерня |
Улучшение |
Закалка ТВЧ |
Цементация |
Закалка ТВЧ |
Цементация |
|
Термо- |
|
Н1 |
(180...350)НВ |
>45 НRСэ |
>45 НRСэ |
>45 НRСэ |
>45 НRСэ |
|
|
Колесо |
|
|
|
Закалка ТВЧ |
Цементация |
||
обработка |
|
Улучшение |
Улучшение |
Улучшение |
||||
|
|
H2 |
(180...350)НВ |
(180...350)НВ |
(180...350)НВ |
>45 НRСэ |
>45 НRСэ |
|
C |
v |
|
925 |
930 |
1000 |
1100 |
1470 |
|
Круговые |
|
υH |
1,22+0,21u |
1,13+0,13u |
0,81+0,15u |
|||
зубья |
|
υF |
0,94+0,08u |
0,85+0,043u |
0,65+0,11u |
|||
Прямые |
|
υH=υF |
|
|
0,85 |
|
|
|
зубья |
|
|
|
|
|
|||
|
|
|
|
|
|
|
Выбор марки стали производиться по Табл.3.
6
Таблица 3
|
Термическая |
Твердость H |
Марка |
σH lim |
[σ]H max |
σ0F lim |
σFst |
|
|
|
|
|
|
|
|
обработка |
|
|
сталей |
SF |
SH |
Yd |
Yд |
γА |
Ygst |
||||
|
|
|
|
|
|
|
||||||||
|
|
Поверхности |
Сердцевины |
|
|
|
|
|
||||||
|
|
|
МПа |
МПа |
МПа |
МПа |
|
|
|
|
|
|
||
|
|
|
|
|
|
|
|
|
|
|
||||
|
Нормализация |
|
|
40,45,40Х,40ХН |
2.Н+ |
|
|
|
|
|
|
|
|
|
1 |
и улучшение |
H=180…350 НВ |
40ХФА, |
|
1,75Н |
6,5Н |
|
|
1,3 |
1,1 |
0,35 |
1 |
||
|
|
|
|
40ХН2МА |
+70 |
2,8 σТ |
|
|
|
|
|
|
|
|
|
Сквозная |
H=48…55 НRCЭ |
40Х,35ХМ |
|
480 |
2250 |
|
|
1,35 |
|
|
|
||
|
закалка при |
|
|
|
|
|
|
1,1 |
|
|
|
|||
2 |
нагреве ТВЧ |
|
|
40ХН,40ХН2МА |
|
|
580 |
2500 |
|
|
|
|
|
|
|
|
|
|
1,7 |
(1,25) |
|
|
|
|
|||||
|
ЗакалкаТВЧ |
|
|
40Х,35ХМ |
17.Н+ |
|
580 |
1800 |
|
1,0 |
|
1,1 |
||
|
по контуру |
H=48…58 |
H=25…35 |
|
|
|
|
|
|
|
|
|||
3 |
с охватом |
НRСЭ |
НRСЭ |
40ХН, |
+200 |
|
680 |
2200 |
|
|
1,1 |
|
|
|
впадин |
|
|
40ХН2МА |
|
|
|
|
|
|
|
|
|||
|
|
|
|
|
|
|
|
|
|
|
|
|
|
|
|
|
|
|
18ХГТ,30ХГТ, |
|
|
820 |
2000 |
|
|
1,1 |
|
0,25 |
|
|
Цементация с |
|
|
20Х |
|
|
|
|
|
|
|
|
|
|
|
|
|
|
|
|
|
|
|
|
|
|
|
||
|
автоматиче |
H=52…63 |
|
|
|
44 . Н |
|
|
1,55 |
|
|
0,75 |
|
|
4 |
ским регули- |
|
20ХН,20ХН2М |
|
|
|
|
|
|
|
|
|
||
НRСЭ |
|
|
|
|
|
|
|
|
|
|
|
|||
|
рованием |
|
20ХН3А, |
|
|
950 |
2800 |
|
1,2 |
1,05 |
|
|
1,05 |
|
|
|
|
|
|
|
|
|
|||||||
|
процесса |
|
H=30...45 |
12ХН3А |
23 . Н |
|
|
|
|
(1,35) |
|
|
|
|
|
Цементация |
H=56…63 |
HRCЭ |
|
|
|
|
|
|
|
|
|
|
|
5 |
|
НRСЭ |
|
Всех марок |
|
|
800 |
2000 |
1,65 |
|
1,2 |
0,8 |
|
|
|
Нитро- |
H=57…63 |
|
25ХГТ,30ХГТ |
|
|
750 |
2200 |
1,55 |
|
1,1 |
0,75 |
|
|
6 |
цементация |
НRСЭ |
|
25ХГМ |
|
|
1000 |
2500 |
|
|
1,0 |
0,7 |
|
0,95 |
Примечание: значение в скобках – для особо ответственных передач.

7
2.3 Выбор степени точности передачи
Точность изготовления зубчатых колес выбирают в зависимости от назначения передачи и возможностей технологии изготовления. В редукторах точность изготовления удобно назначать в зависимости от окружной скорости (Табл.4), среднее значение которой определяют по формуле:
Vm ≈ n1 |
3 T2 |
м/с, |
(1) |
cV |
u2 |
|
|
где СV- коэффициент, зависящий от термообработки шестерни и колеса (Табл.2).
Степень точности изготовления цилиндрических колес Таблица 4
Vm |
≤ 5 м/с |
5...12 |
м/с |
Прямозубые |
6 , 7 |
6 , 7 |
|
|
|
|
|
С круговыми зубьями |
7 , 8 |
6 , 7 |
|
|
|
|
|
2.4Выбор коэффициента относительной ширины Кbе
Для ограничения неравномерности распределения нагрузки по ширине венца конических колес коэффициент ширины Кbе=bw/Re принимают в пределах 0,25...0,3. Рекомендуется выбирать Кbе=0,285. Большие значения для более высокой степени точности.
2.5Выбор среднего угла наклона зуба βm
Для кругового зуба угол наклона в среднем сечении по ГОСТ 19326-73 рекомендуют брать в пределах от 00 до 450 кратным 50. Наиболее распространен βm=350 .
2.6Определение углов делительных конусов δ1 и δ2
Половины углов при вершине начальных конусов шестерни - δ1 и колеса - δ2 (Рис.1)
при Σ=900 определяют по формулам: |
|
|
δ2 = arctg u ; |
δ1= 900-δ2 . |
(2) |
2.7Определение коэффициентов нагрузки КH и КF
При расчете на сопротивление усталости КH и КF определяют:
При контактных напряжениях |
При изгибных напряжениях |
КН = КA КHV КHβ КHα (3а) |
КF = КA КFV КFβ КFα (3б) |
Коэффициент внешней динамической нагрузки КА
Если заданный блок нагружения, учитывает внешние динамические нагрузки, то КА = 1. В противном случае при расчетах на сопротивление усталости КА
принимают по Табл.1 (приложение).
Коэффициенты неравномерности распределения нагрузки по ширине колес
КHβ и КFβ
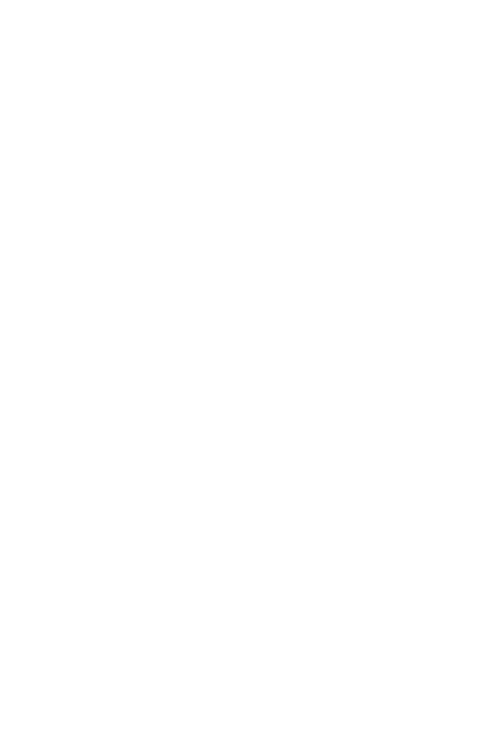
8
Коэффициенты КF β и КH β определяют в зависимости от расположения колес относительно опор валов (рис.2), вида этих опор (шариковые или роликовые), вида зубьев (прямые или круговые), параметра ψd= Кве u /(2- Кве) и твердости поверхности зубьев по графикам на рис.3.
Схемы расположения колес относительно опор
Рис. 2
Графики для определения КHβ и КFβ
1) Для вариантов термообработки 1, 2, 3 ( табл.2)
2) Для вариантов термообработки 4,5 (табл.2)
Рис.3 1- передача А по рис.2 (опоры на шариковых подшипниках), 2-передача А (опоры на
роликовых подшипниках), 3-передача Б. Сплошные линии для прямозубых колес, штрих пунктирные- с круговыми зубьями.

9
Коэффициенты динамической нагрузки КHV и КFV определяют по табл.5. Причем КHV, КFV ≥1.
Коэффициенты распределения нагрузки по парам одновременно работающих зубьев КHα и КFα для конической передачи с круговыми зубьями определяют по эмпирическим зависимостям ( табл.5). Причем КHα , КFα ≥1. Для конической передачи с прямыми зубьями
КHα = КFα =1.
|
|
|
|
Таблица 5 |
Степень точности |
6 |
|
7 |
8 |
КFV |
1+ 0,18 V |
|
1+ 0,11 Vm |
|
|
|
m |
|
|
КHV |
|
|
0,5(KFV+1) |
|
КHα |
1,003+2,7 10-3Vm |
|
1,02+5,3 10-3Vm |
(62,2-8,08Vm) 10-2Vm |
КFα |
1,025+8 10-3Vm |
|
1,096+1,33 10-2Vm |
1,172+2,13 10-2Vm |
2.8Определение коэффициентов υH и υF , учитывающих вид
конической передачи
Для конических зубчатых передач с прямыми и круговыми зубьями υH и υF определяются по Табл.2 в зависимости от термообработки колес и передаточного числа передачи.
2.9 Определение допускаемых контактных напряжений [σ]H при
проектировочном расчете
Суммарное число циклов за период службы:
шестерни |
колеса |
|
N∑1= 60 n1 Lh ( 4а) |
N∑2= N∑1 ⁄u |
(4б) |
n1 – частота вращения вала шестерни, мин-1, Lh – ресурс работы в часах,
u - передаточное число.
Коэффициент режима работы при n =const:
H = 3 |
|
t |
i |
|
T |
3 |
|
F= 6,9 = ∑ |
t |
i |
|
T |
qF |
|
= ∑ |
|
|
i |
|
(5а), |
|
|
i |
|
(5б), |
||||
|
|
|
|
|
|
|||||||||
t |
|
|
|
t |
|
|
|
|||||||
|
|
бл Tmax |
|
|
бл Tmax |
|
где ti, Ti – время работы и вращающий момент на каждой ступени нагружения; Tmax- наибольший длительно действующий момент; tбл - время работы за блок нагружения; qF- показатель степени при расчете на сопротивление усталости при изгибе: для колес с однородной структурой материала, включая закаленные при нагреве ТВЧ со сквозной закалкой, и зубчатых колес с приработанной переходной поверхностью qF = 6; для колес с поверхностным упрочнением и не приработанной переходной поверхностью qF =9.
Если частоты вращения колес различны по ступеням блока нагружения, то коэффициенты режима находятся по [3,4].
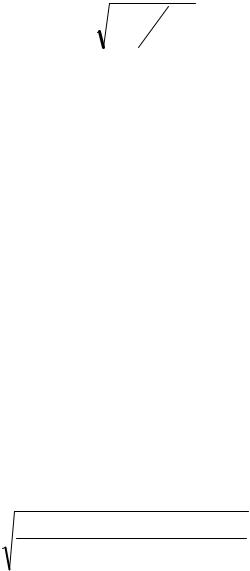
10
Эквивалентное число циклов за срок службы NHE: |
|
|
|||||||
для шестерни |
- |
|
|
NHE1 = N∑1 µ3 , |
|
|
|||
для колеса |
- |
|
|
NHE2 = NHE1 / u. |
|
(6) |
|||
Базовое число циклов NHG , соответствующее перелому кривой усталости |
|
||||||||
определяют по формулам (7а или 7б) |
|
|
|
|
|
|
|||
NHG=30 Н2,4 ≤ 120 106 |
|
|
при Н ≤ 350 НВ |
(7а) |
|||||
NHG ≈ 340 Н3,15 + 8 106 ≤ 120 106 |
|
при Н ≥ 45 НRСэ 2.7 |
(7б) |
||||||
Коэффициент долговечности ZN, по формуле: |
|
|
|
||||||
|
ZN = |
q |
H |
NHG |
NHE |
, |
|
|
(8) |
|
|
|
|
|
|||||
|
|
|
|
|
|
|
|
|
|
где qH -показатель степени кривой усталости: при NHE ≤ NHG - |
qH =6 |
|
|||||||
|
|
|
|
|
|
|
NHE > NHG - |
qH =20 |
|
Причём должно выполняться условие: ZNmin ≤ ZN < ZNmax , |
|
|
ZNmax= 2,6 - для материалов с однородной структурой ,ZNmax= 1,8 - для поверхностно-упрочненных материалов,ZNmin = 0,75.
Допускаемые напряжения [σ]H для передач с прямыми и круговыми зубьями определяют раздельно для шестерни и колеса по формуле:
[σ]H = [σ]H lim ZN / SH, МПа |
(9) |
где [σ]H lim- предел контактной выносливости по табл.3; SH- коэффициент запаса прочности (табл. 3).
Расчетное допускаемое контактное напряжение [σ]Н При расчете на сопротивление контактной усталости принимают меньшее из двух:
для передачи с прямыми зубьями |
[σ]Н1 или [σ]Н2, |
|
для передач с круговыми зубьями |
[σ]Н = 0,45([σ]Н1 + [σ]Н2) |
(10а) |
или |
[σ]Н =1,15[σ]Н2 |
(10б) |
2.10 Внешний делительный диаметр колеса |
|
de2 |
≥ 900 3 |
|
T2K Hu |
, (мм) |
(11) |
|
ϑH (1 |
− 0,5K be )2 K be [σ]H2 |
|||||
|
|
|
|
Здесь Т2- момент на колесе, Н м, КН- коэффициент нагрузки, ϑ- коэффициент, учитывающий вид передачи, Кbе - коэффициент ширины, [σ]H- допускаемое контактное напряжение, МПа.
Полученное значение рекомендуется округлить до стандартного по ГОСТ 13289-73
1 ряд 50 , 63 , 80 , 100 , 125 , 160 , 200 , 280 , 315 , 355 , 400 2 ряд 56 , 71 , 90 ,112 , 140 , 180 , 225.
2.11 Расчет геометрических параметров конической передачи