
логистика балалаев
.PDF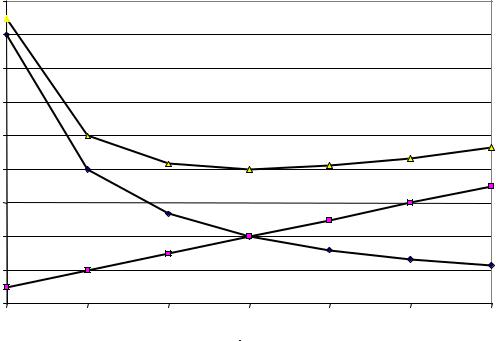
Решение задачи графическим способом заключается в построении гра-
фиков зависимости Стр (q), |
Схр (q) |
и C(q) , предварительно выполнив не- |
||||||||||
обходимые расчеты по определению Cтр , Схр и С . |
|
|
|
|
||||||||
Определим значения Стр , Схр |
и С при изменении q в пределах от 50 |
|||||||||||
до 350 с шагом 50. Результаты расчетов заносим в табл. 2.1. |
|
|
||||||||||
|
|
|
|
|
|
|
|
|
|
|
Таблица 2.1 |
|
|
Значения Стр , Схр |
и С |
|
|
|
|
||||||
|
|
|
|
|
|
|
|
|
|
|
||
Затраты, р. |
|
|
|
|
Размер партии q , т |
|
|
|||||
|
|
|
|
|
|
|
|
|
|
|
|
|
50 |
|
100 |
|
150 |
|
200 |
|
250 |
|
300 |
350 |
|
|
|
|
|
|
|
|||||||
Стр |
800 |
|
400 |
|
267 |
|
200 |
|
160 |
|
133 |
114 |
Схр |
50 |
|
100 |
|
150 |
|
200 |
|
250 |
|
300 |
350 |
С |
850 |
|
500 |
|
417 |
|
400 |
|
410 |
|
433 |
464 |
По данным табл. 2.1 построены графики зависимости затрат на транс- |
||||||
портировку, хранение и суммарных затрат от размера партии, представ- |
||||||
ленные на рис. 2.1. |
|
|
|
|
|
|
Стр , Схр и С , р. |
|
|
|
|
|
|
900 |
|
|
|
|
|
|
800 |
|
|
|
|
|
|
700 |
|
|
|
|
|
|
600 |
|
|
|
|
|
|
500 |
|
|
|
|
С |
|
400 |
|
|
|
|
|
|
300 |
|
|
|
|
Схр |
|
|
|
|
|
|
|
|
200 |
|
|
|
|
|
|
100 |
|
|
|
|
Стр |
|
|
|
|
|
|
|
|
0 |
|
|
|
|
|
|
50 |
100 |
150 |
200 |
250 |
300 |
350 q , тонн |
|
Рис. 2.1. Зависимость затрат от размера партии |
|
21

Анализ графика показывает, что затраты на транспортировку Стр
уменьшаются с увеличением размера партии, что связано с уменьшением количества рейсов. Затраты, связанные с хранением С хр , возрастают про-
порционально размеру партии.
Б. Оптимальный размер партии в условиях дефицита qдеф увеличивает-
ся за счет необходимости хранения бóльшей партии груза в связи с затруднениями, связанными со сложностями прогнозирования сбыта и, как следствие, дополнительными сопутствующими затратами сдеф . В условиях
дефицита qопт , рассчитанное по формуле (2.8), корректируется на коэффициент k , учитывающий расходы, связанные с дефицитом.
qдеф |
k |
|
2 Qг од |
cтр |
|
k qопт . |
(2.9) |
схр |
|
|
|||||
|
|
|
|
|
|
|
Коэффициент k рассчитываем по формуле
|
|
|
|
|
|
k |
|
схр сдеф |
|
. |
(2.10) |
|
|
|
|
|
|
||||||
|
|
|
|
|
|
|
|
сдеф |
|
||
Подставив значения, получаем |
|
|
|
|
|||||||
|
|
|
|
|
|
|
|
|
|
|
|
k |
2 |
|
3 |
1,29 |
|
qдеф 1,29 200 |
258 т. |
||||
|
|
|
|
||||||||
|
3 |
|
|
||||||||
|
|
|
|
|
|
|
|
|
|
|
2.3.Пример 3. Определение наилучшего поставщика на основе расчета рейтинга
Требуется: выбрать из нескольких потенциальных поставщиков наилучшего.
Исходные данные: в процессе поиска потенциальных поставщиков был сформирован список из 7 фирм (1–7).
Решение
1. Выбираются наиболее предпочтительные для предприятия критерии, по которым анализируются фирмы-поставщики. Количество критериев может составлять несколько десятков. Рассматриваемая фирма в качестве
22

критериев выбрала следующие: надежность поставки, цена, качество товара, условия платежа, возможность внеплановых поставок, финансовое состояние поставщика. Все поставщики оцениваются по каждому критерию по десятибалльной шкале. Поставщику, в лучшей степени удовлетворяющему данному критерию, выставляется более высокая оценка. В рассматриваемом примере сформулированы и оценены критерии, представленные в табл. 2.2.
Таблица 2.3.1
Оценка поставщиков по соответствию критериям выбора, балл
Критерии выбора поставщика |
|
Фирмы-поставщики |
|
|||||
1 |
2 |
3 |
4 |
5 |
6 |
7 |
||
|
||||||||
Надежность поставки |
1 |
2 |
4 |
5 |
7 |
3 |
6 |
|
Цена |
3 |
5 |
6 |
4 |
1 |
7 |
9 |
|
Качество товара |
5 |
6 |
2 |
3 |
8 |
4 |
1 |
|
Условия платежа |
7 |
8 |
3 |
9 |
2 |
6 |
4 |
|
Возможность внеплановых поставок |
9 |
10 |
8 |
6 |
5 |
2 |
3 |
|
Финансовое состояние поставщика |
4 |
1 |
9 |
7 |
3 |
5 |
2 |
2. Каждому критерию экспертным путем специалисты предприятия устанавливают коэффициент значимости i , величина которого зависит от
важности того или иного критерия. Необходимым условием при этом является следующее ограничение:
n |
1, |
|
i |
(2.11) |
i 1
где n – число критериев выбора.
Для рассматриваемого предприятия значения коэффициентов значимости на основе мнения менеджеров предприятия распределились следую-
щим образом: |
|
надежность поставки |
0,30 |
цена |
0,25 |
качество товара |
0,15 |
условия платежа |
0,15 |
возможность внеплановых поставок |
0,05 |
финансовое состояние поставщика |
0,10 |
Итого |
1,00 |
23

3. Расчет значений критериев осуществляется умножением коэффициента значимости на его оценку в соответствии с табл. 2.3. Например, по критерию «Надежность поставки» первый поставщик получает значение –
0,30 (0,30 ∙ 1 = 0,30); второй поставщик – 0,60 (0,30 ∙ 2 = 0,60); третий по-
ставщик – 1,20 (0,30 ∙ 4 = 1,20) и т.д. Результаты расчетов заносятся в табл. 2.3.
Таблица 2.3
Расчет рейтинга поставщиков
Критерии выбора |
|
|
Фирмы-поставщики |
|
|||||
поставщика |
i |
|
|
|
|
|
|
|
|
1 |
2 |
3 |
4 |
5 |
6 |
7 |
|||
|
|||||||||
|
|
|
|
|
|
|
|
|
|
Надежность поставки |
0,30 |
0,30 |
0,60 |
1,20 |
1,50 |
2,10 |
0,90 |
1,80 |
|
|
|
|
|
|
|
|
|
|
|
Цена |
0,25 |
0,75 |
1,25 |
1,50 |
1,00 |
0,25 |
1,75 |
2,25 |
|
|
|
|
|
|
|
|
|
|
|
Качество товара |
0,15 |
0,75 |
0,90 |
0,30 |
0,45 |
1,20 |
0,60 |
0,15 |
|
|
|
|
|
|
|
|
|
|
|
Условия платежа |
0,15 |
1,05 |
1,20 |
0,45 |
1,35 |
0,30 |
0,90 |
0,60 |
|
|
|
|
|
|
|
|
|
|
|
Возможность |
0,05 |
0,45 |
0,50 |
0,40 |
0,30 |
0,25 |
0,10 |
0,15 |
|
внеплановых поставок |
|||||||||
|
|
|
|
|
|
|
|
||
|
|
|
|
|
|
|
|
|
|
Финансовое состояние |
0,10 |
0,40 |
0,10 |
0,90 |
0,70 |
0,30 |
0,50 |
0,20 |
|
поставщика |
|||||||||
|
|
|
|
|
|
|
|
||
|
|
|
|
|
|
|
|
|
|
Сумма баллов |
1,00 |
3,70 |
4,55 |
4,75 |
5,30 |
4,40 |
4,75 |
5,15 |
|
|
|
|
|
|
|
|
|
|
Фирма, получившая максимальное число баллов, в наибольшей степени отвечает требованиям интегрального критерия выбора поставщика и может быть выбрана в качестве наилучшего партнера. По результатам табл. 2.3 это четвертый поставщик с суммой баллов 5,30.
2.4. Пример 4. Выбор региона закупок комплектующих [8]
Требуется: определить для фирмы, расположенной в европейской части России, где его компании выгоднее покупать комплектующие для производимого оборудования: в Европе или в Азиатско-Тихоокеанском регионе (АТР).
Исходные данные представлены в табл. 2.4.
24

Таблица 2.4
Варианты закупки комплектующих
|
|
Исходные данные |
|
Варианты закупок |
|
|||
|
|
1 |
2 |
3 |
4 |
5 |
||
|
|
|
|
|||||
У – удельная стоимость поставляемого |
3000 |
4000 |
5000 |
6000 |
4500 |
|||
груза, у.е./м3 |
|
|||||||
Та |
– транспортный тариф из АТР, у.е./м3 |
120 |
120 |
120 |
120 |
120 |
||
Те |
– |
транспортный тариф |
из Европы, |
8 |
8 |
8 |
8 |
8 |
у.е./м3 |
|
|
||||||
|
|
|
|
|
|
|
||
Пи |
– |
импортная пошлина |
на товар из |
12 |
12 |
12 |
12 |
12 |
АТР, % |
|
|||||||
|
|
|
|
|
|
|||
Зп |
– ставка на запасы в пути, % |
1,9 |
3,0 |
4,0 |
2,0 |
2,5 |
||
Зс |
– ставка на страховые запасы, % |
0,8 |
0,8 |
0,8 |
0,8 |
0,8 |
||
Се |
– стоимость товара в Европе, у.е. |
108 |
116 |
98 |
110 |
118 |
||
Са |
– стоимость товара в АТР, у.е. |
89 |
99 |
78 |
90 |
101 |
Решение
1. Расчет доли дополнительных затрат, возникающих при доставке товаров из АТР в удельной стоимости поставляемого груза осуществляется по формуле
Д = 100 ∙ Та /У + Пи + Зп + Зс , %. |
(2.12) |
Подставив в формулу 2.12 исходные данные первого варианта из табл. 2.4, получаем:
Д= 100 ∙ 120/3000 + 12 + 1,9 + 0,8 = 18,7 %.
2.Приняв за 100% наименьшую стоимость товара Са , определим
разницу Рс между стоимостью комплектующих товаров в Европе и АТР по формуле
Рс = ( Се ∙(1 + Те /У) – Са )∙100/Са , %. |
(2.13) |
Подставив в формулу (2.13) исходные данные первого варианта из табл. 2.4, получаем:
Рс = 108 (1 + 8/3000) – 89 ∙100/89 = 21,67 %.
25
Полученный результат показывает, что стоимость комплектующих в АТР на 21,3% меньше, чем в Европе.
3. Сравним полученные значения Д и Рс
Д = 18,7% < Рс = 21,67 %.
Поскольку доля дополнительных затрат, возникающих при доставке из АТР, в удельной стоимости поставляемого груза меньше, чем разница между стоимостью комплектующих в Европе и АТР, то именно в странах этого региона выгоднее покупать комплектующие.
Рассчитаем величины Д и Рс для остальных вариантов (2, 3, 4, 5) из табл. 2.12 и сведем в табл. 2.13.
Таблица 2.5
Расчет вариантов закупки комплектующих товаров в разных регионах мира
Расчетные данные |
|
Варианты закупок |
|
|||
1 |
2 |
3 |
4 |
5 |
||
|
||||||
Д – доля дополнительных |
|
|
|
|
|
|
затрат, возникающих при |
18,7 |
18,8 |
19,2 |
16,8 |
18,0 |
|
доставке товаров из АТР, % |
|
|
|
|
|
|
Рс – разница между стои- |
|
|
|
|
|
|
мостью комплектующих то- |
21,7 |
17,2 |
25,8 |
22,4 |
16,9 |
|
варов в Европе и в АТР, % |
|
|
|
|
|
|
Ответы |
АТР |
Европа |
АТР |
АТР |
Европа |
Контрольные вопросы
1.Дайте определение понятия «закупочная логистика».
2.Охарактеризуйте место и роль службы снабжения в логистических процессах.
3.Охарактеризуйте факторы, влияющие на принятие решений по зада-
че Make-or-Buy.
4.Перечислите методы поиска потенциальных поставщиков.
5.Приведите порядок расчета рейтинга поставщика.
6.По каким критериям может оцениваться потенциальный поставщик при принятии решения о заключении с ним договора поставки?
Используемая литература
26
3. ПРОИЗВОДСТВЕННАЯ ЛОГИСТИКА
3.1. Теоретические положения
Производственная логистика – процесс управления продвижением материальных ресурсов в пределах предприятия от склада снабжения до складов готовой продукции.
Специфика этого этапа заключается в том, что основной объем работ по проведению потока выполняется в пределах территории одного предприятия, поэтому характерной чертой таких объектов является их территориальная компактность. Участники логистического процесса при этом, как правило, не вступают в товароденежные отношения и движение продукции осуществляется не в результате заключения договора (контракта) купли-продажи, а в результате решений, принимаемых системой управления предприятием.
Целью производственной логистики является оптимизация материальных потоков внутри предприятий путем создания таких материальных услуг как перемещение в пределах предприятия, комплектование, сортировка и др. При этом может ставиться цель снижения величины запасов, сокращения количества перемещений на складе, общего увеличения прибыли предприятия.
Логистические системы, рассматриваемые производственной логистикой, носят название внутрипроизводственных логистических систем. К ним можно отнести: промышленное предприятие; оптовое предприятие, имеющее складские сооружения; железнодорожную станцию (сортировочную, грузовую); морской порт и др.
Внутрипроизводственные логистические системы рассматриваются на макро- и микроуровнях.
На макроуровне внутрипроизводственные логистические системы выступают в качестве элементов макрологистических систем. Они задают ритм работы этих систем, являются источниками материальных потоков. Возможность адаптации макрологистических систем к изменениям окружающей среды в существенной степени определяется способностью входящих в них внутрипроизводственных логистических систем быстро менять качественный и количественный состав выходного материального потока, т. е. ассортимент и количество выпускаемой продукции.
27
На микроуровне внутрипроизводственные логистические системы представляют собой ряд подсистем, находящихся в отношениях и связях друг с другом, образующих определенную целостность, единство. Эти подсистемы: закупка, склады, запасы, обслуживание производства, транспорт, информация, сбыт и кадры обеспечивают вхождение материального потока в систему, прохождение внутри нее и выход из системы. В соответствии с концепцией логистики построение внутрипроизводственных логистических систем должно обеспечивать возможность постоянного согласования и взаимной корректировки планов и действий снабженческих, производственных и сбытовых звеньев внутри предприятия.
Логистическая концепция организации производства включает в себя следующие основные положения:
–отказ от избыточных запасов;
–отказ от завышенного времени на выполнение основных и транс- портно-складских операций;
–отказ от изготовления серий деталей, на которые нет заказа покупателей;
–устранение простоев оборудования;
–обязательное устранение брака;
–устранение нерациональных внутризаводских перевозок;
–превращение поставщиков из противостоящей стороны в доброжелательных партнеров.
В отличие от логистической традиционная концепция организации производства предполагает:
–никогда не останавливать основное оборудование и поддерживать во что бы то ни стало высокий коэффициент его использования;
–изготавливать продукцию как можно более крупными партиями;
–иметь максимально большой запас материальных ресурсов «на всякий случай».
Содержание концептуальных положений свидетельствует о том, что традиционная концепция организации производства наиболее приемлема для условий «рынка продавца», в то время как логистическая концепция – для условий «рынка покупателя».
Производство в условиях рынка может выжить лишь в том случае, если оно способно быстро менять ассортимент и количество выпускаемой продукции. До 70-х годов весь мир решал эту задачу за счет наличия на скла-
28

дах запасов готовой продукции. Сегодня логистика предлагает адаптироваться к изменениям спроса за счет запаса производственной мощности.
Запас производственной мощности возникает при наличии качественной и количественной гибкости производственных систем (рис. 3.1).
Производственная
мощность
|
|
|
|
|
|
|
|
|
|
|
|
|
|
|
|
|
|
|
Качественная |
|
|
|
|
Количественная |
|
|
|
||||||||
|
гибкость |
|
|
|
|
|
гибкость |
|
|
|
|||||||
|
|
|
|
|
|
|
|
|
|
|
|
|
|
|
|
|
|
|
|
|
|
|
|
|
|
|
|
|
|
|
|
|
|
|
|
Универсальный |
|
|
|
Гибкая |
|
|
|
|
|
|
|
|
|
Резерв |
|||
|
|
автоматизация |
|
|
|
Резерв |
|
|
|
||||||||
обслуживающий |
|
|
|
|
|
|
|
рабочей |
|||||||||
|
|
системы |
|
оборудования |
|
|
|||||||||||
персонал |
|
|
|
|
|
|
силы |
||||||||||
|
станков с ЧПУ |
|
|
|
|
|
|
|
|
|
|||||||
|
|
|
|
|
|
|
|
|
|
|
|
|
|
||||
|
|
|
|
|
|
|
|
|
|
|
|
|
|
|
|
|
|
Рис. 3.1. Гибкость производственной мощности
Качественная гибкость обеспечивается за счет наличия универсального обслуживающего персонала и гибкого производства. Количественная гибкость может обеспечиваться различными способами. Например, на некоторых предприятиях Японии основной персонал составляет не более 20% от максимальной численности работающих. Остальные 80% – временные работники. Таким образом, при численности персонала в 200 человек предприятие в любой момент может поставить на выполнение заказа до 1000 человек. Резерв рабочей силы должен дополняться соответствующим резервом средств труда.
Управление материальными потоками в рамках внутрипроизводственных логистических систем может осуществляться различными способами, из которых выделяют два основных: толкающий и тянущий, принципиально отличающиеся друг от друга.
Первый вариант носит название «толкающая система» и представляет собой систему организации производства, в которой предметы труда, поступающие на производственный участок, непосредственно этим участком у предыдущего технологического звена не заказываются. Материаль-
29

ный поток «выталкивается» получателю по команде, поступающей на передающее звено из центральной системы управления производством
(рис. 3.2).
Система управления
Склад |
|
Цех |
|
Цех |
∙∙∙∙∙ |
Цех |
|
Цех |
сырья |
|
№ 1 |
|
№ 2 |
№ N |
|
сборки |
|
|
|
|
|
|||||
|
|
|
|
|
|
|
|
|
Рис. 3.2. Принципиальная схема толкающей системы управления материальным потоком в рамках внутрипроизводственной логистической системы: – материальный поток;
– информационный поток
Толкающие модели управления потоками характерны для традиционных методов организации производства. Возможность их применения для логистической организации производства появилась в связи с массовым распространением вычислительной техники. Эти системы, первые разработки которых относят к 60-м годам, позволили согласовывать и оперативно корректировать планы и действия всех подразделений предприятия – снабженческих, производственных и сбытовых с учетом постоянных изменений в реальном масштабе времени.
На практике реализованы различные варианты толкающих систем, известные под названием «системы МРП» (MRP). Возможность их создания обусловлена началом массового использования вычислительной техники. Системы МРП характеризуются высоким уровнем автоматизации управления, позволяющим реализовывать следующие основные функции:
–обеспечивать текущее регулирование и контроль производственных запасов;
–в реальном масштабе времени согласовывать и оперативно корректировать планы и действия различных служб предприятия – снабженческих, производственных, сбытовых.
В современных, развитых вариантах систем МРП решаются также различные задачи прогнозирования. В качестве метода решения задач широко применяется имитационное моделирование и другие методы исследования операций.
Второй вариант организации логистических процессов на производстве основан на принципиально ином способе управления материальным
30