
ТСП конспект
.pdfфакторов на достижение состояния, близкого к предельному теплонасыщению (ψ = 0,95), кроме расстояния большое влияние оказывает и скорость перемещения источника тепла. Так, при скорости v = 0,3 см/с период теплонасыщения на расстоянии R = 3 см от оси дуги практически заканчивается в течение 10 с. При
меньших скоростях сварки влияние периода теплонасыщения проявляется в большей степени и должно учитываться при выполнении сварки.
После окончания действия источника тепла введенное тепло продолжает распространяться в теле вследствие теплопроводности. Период процесса распространения тепла, начиная от момента прекращения действия источника,
называется периодом выравнивания температуры.
Пусть после прохождения отрезка ОК источник мощностью q, прекративший ввод тепла в тело в момент его нахождения в точке К, продолжает действовать и дальше (вплоть до достаточно отдаленной точки М) как фиктивный источник той же мощности. Одновременно в момент К введен и фиктивный сток тепла мощностью –q, приложенный к тем же участкам тела, что и фиктивный источник +q, т.е. на участке КМ тело тепла не получает.
Температуру Тв в момент М в периоде выравнивания можно представить как алгебраическую сумму температуры Т от продолжающего действовать источника q и температуры –Т от начавшего действовать стока тепла -q:
TB(t) = T(t) – T(t-tk) t > tk.
Обе температуры можно выразить через температуру предельного состояния Тпр и соответствующие коэффициенты теплонасыщения
TB(t) = Tnp(ψ(t) – ψ(t-tk)).
Пример На поверхность массивного тела наплавляют валик ОК длиной 10
см. Режим наплавки: q = 1000 кал/с; v = 0,1 см/с; теплофизические свойства металла:
λ = 0,1 кал/ ( см*с*0С), a = 0,1 см2 /с.
Рассчитать температуру точки К через 10 с после окончания наплавки. Решение. При наплавке действительный точечный источник на длине валика
10 см перемещался со скоростью v = 0.1 cм /с. Длительность его действия t к = =10 / 0,1 =100 с. После окончания наплавки фиктивные источник и сток, двигаясь той же скоростью, через 10 с находятся в точке М. Координаты точки К, температура которой нас интересует, относительно фиктивного источника и стока x k =- 0,1*10 = - 1 см; yk = 0; z k =0. Температура предельного состояния точки ( -1; 0; 0), лежащей на отрицательной полуоси х < 0, вычисляется по уравнению
T |
пр(−1) |
= |
1000 |
= 15900 C. |
|
2*0.1*1,0 |
|||||
|
|
|
|||
|
|
|
|
61
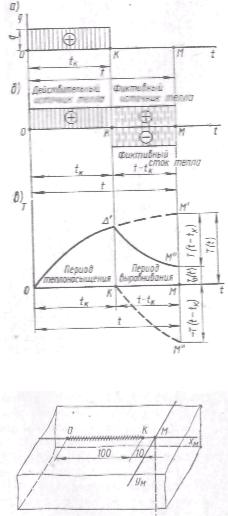
Рис. 3.11. Расчетная схема периода выравнивания температуры.
Рис. 3.12. Пример расчета температур после окончания наплавки.
Длительность действия источника (действительного и фиктивных) t = 100 + 10 = 110 с. Длительность действия стока t – tk = 10 c. Безразмерные критерии для нахождения коэффициентов теплонасыщения:
расстояния:
ρ = vR/2a =0,1*1,0/(2*0,1) = 0,5;
времени действительного и фиктивного источников
τ = v2t/4a = 0,12*110/(4*0,1) = 1,75;
времени стока
τ! = 0,12*10/(4*0,1) = 0,25.
Соответствующие коэффициенты теплонасыщения ψ = 1,0 ψ! = 0,7.
Температура точки К через 10 с после окончания наплавки Т(-1,110) = 1590(1,0 – 0,7) = 477 0С.
3.7 Температурные поля распределенных источников тепла
До сих пор мы рассматривали сосредоточенные источники тепла. Фактически
источники сварочного тепла являются распределенными в объеме или по поверхности. Расчетные схемы, учитывающие распределенность источников, значительно сложнее и для практических случаев используются редко.
62

Известно, что удельный тепловой поток q(r) как газового пламени, так и дуги распределен нормально по радиусу r пятну нагрева, подчиняясь уравнению q = qmaxe- kr2. Для конкретных случаев значения qmax, qr и к определяются из опытных измерений и расчетов по полученным величинам. Пятно нагрева в виде окружности с удельным потоком, нормально распределенным по площади, получается, когда ось газового пламени или дуги направлена перпендикулярно к нагреваемой поверхности. Такой источник называют нормально-круговым. Связь между общей мощностью q такого источника и переменным удельным тепловым потоком q(r), распределенным по окружности площадью F, представляется в интегральной форме
q = òq(x, y)dF.
F
Примем распределение теплового потока по пятну нагрева в соответствии с рис. 3.13. Рассмотрим кольцевой элемент радиусом r и шириной dr. Удельный поток q(r) остается по всей площади такого кольца постоянным. Через это кольцо вводится тепло q(r) = 2πrdr. Тогда
∞
q = òq(r ) 2πrdr.
0
Подставив вместо q(r) общее его выражение через коэффициент сосредоточенности и применив подстановку kr2 = U и соответственно
2krdr = dU, получим
|
1 |
∞ |
1 |
∞ |
|
π qmax . |
|
q = |
qmaxπ òe−U dU = − |
qmaxπ òeU dU , |
q = |
||||
k |
k |
||||||
|
0 |
0 |
|
k |
|||
|
|
|
|
|
Рис.3.13. Нормально-круговой источник тепла.
Если заменить нормально-круговой фиктивным с равной мощностью q, но с
равномерно распределенным удельным тепловым потоком по окружности радиусом r0, то r0 можно найти из простейших геометрических расчетов (рис.). Объем цилиндра с площадью основания πr20, равновеликий объему, ограниченному поверхностью
удельного теплового потока q(r), q = πr20qmax. Отсюда r20 = q/(πqmax). Заменив q/qmax = π/k, получим
r 2 |
= |
1 |
; |
r = |
1 |
. |
|
|
|
||||||
0 |
|
k |
0 |
|
k |
||
|
|
|
|
63
Чем больше коэффициент сосредоточенности к, тем меньше радиус эквивалентного цилиндра.
Приняв наиболее вероятные значения коэффициентов сосредоточенности для сварочной дуги от 1,5 до 6,0 и для газосварочного пламени от 0,16 до 0,4, получим предельные значения радиусов эквивалентных цилиндров: для сварочной дуги в пределах 0,4 – 0,8 см; для пламени в пределах 1,6 – 2,5 см.
Таким образом, если расчеты температурных полей при нагреве сварочной
дугой могут в ряде случаев заменяться нагревом сосредоточенными источниками тепла и это дает погрешность в областях нагрева (т.е. в поле на расстоянии около 1 см от места действия источника), то для газосварочного пламени эта погрешность
значительно больше и здесь следует учитывать распределенность ввода тепла в изделие.
3.8 Расчет нагрева и плавления электродной проволоки
В огромном большинстве случаев сварки плавлением формирование сварочной ванны обеспечивается расплавленным основным и добавочным (присадочным) металлами. При сварке плавящимся электродом интенсивность
плавления присадочного металла непосредственно связана с конкретными сварочными режимами. Производительность сварочной операции в основном определяется количеством наплавленного металла в г/с или кг/час. Применительно к
процессу механизированной сварки плавящийся электрод нагревается и расплавляется с торца, на который непосредственно действует дуговой разряд, теплом этого дугового разряда и теплом, выделяющимся при протекании по электроду сварочного тока. Для установившегося процесса средняя скорость подачи электродной проволоки равна скорости ее плавления vпод = vпл. Уравнение теплового баланса:
Vплhk = qэ + qп.п. – qпот,
где
vпл – средняя скорость плавления, г/с;
hк – удельная энтальпия расплавленного на торце электрода металла перед отрывом капель электрода, кал/г;
qэ – эффективная мощность дуги, вводящая тепло в электрод, кал/с;
qп.п. – тепло, выделяющиеся в электроде вследствие протекания в нем тока,
кал/с;
qпот – потери тепла в окружающую среду, в основном через боковые поверхности электродной проволоки, кал/с.
По опытным данным Б.Е.Патона, В.П.Демянцевича и др. авторов потери в окружающую среду составляют небольшую величину (от 1 до 5%) и ими можно пренебречь.
Количество тепла, вводимого в электродную проволоку дугой за единицу времени, может быть выражено как часть полной электрической мощности дуги
qэ = 0,24IUη,
где η – эффективный к.п.д. процесса нагрева плавящегося электрода дугой.
64
Нагрев электрода проходящим в нем током зависит от силы (плотности) тока, теплофизических свойств материала электрода, удельного электрического сопротивления ρ, поперечного сечения электрода и длины проводника, определяющего и время нагрева. В связи с тем, что для многих сталей, применяемых в качестве электродных проволок, удельное электрическое сопротивление в зависимости от температуры изменяется в 5 – 7 раз, использование усредненных значений ρ дает очень большие погрешности. Поэтому следует использовать температурную зависимость ρТ = ρ0(1 + αТ), которая в пределах до 500 – 8000С (более
высокая температура электродной проволоки и стержня штучных электродов приводит к ухудшению сварочных характеристик) приближенно может быть принята со значениями α = const.
Температуру предварительного нагрева электродной проволоки при подходе ее к дуге можно оценить интенсивностью тепловыделения элемента длины вылета у торца электрода (кал/с):
qп.п. = FcρvподТп.п.
Пренебрегая потерями в окружающую среду, можно считать, что qп.п. = qвыд, где qвыд – тепло, выделенное проходящим током. Тогда для элемента длины проволоки dl:
dqп.п. = Fcρvпод dT, |
|
|
|
||||||||||||||
dqвыд = 0,24ρ |
dl |
I 2 = 0,24ρFjdl, |
|||||||||||||||
F |
|||||||||||||||||
|
|
|
|
|
|
|
|
|
|
|
|
|
|
||||
где j – плотность тока в электродной проволоке, А/см2. |
|||||||||||||||||
Подставляя температурную зависимость: |
1 |
|
|
|
|||||||||||||
0,24ρ* j2 dl = cρv |
|
|
|
dT. |
|||||||||||||
под 1 |
+ αT |
||||||||||||||||
0 |
|
|
|
|
|
|
|
|
|
|
|
|
|||||
Отсюда |
|
|
|
|
|
|
vпод Тпò.п. |
|
|
|
|
||||||
0,24ρ0* òl |
dl = |
cρ |
1 |
|
вТ. |
||||||||||||
2 |
1+ αТ |
||||||||||||||||
0 |
|
|
|
j |
|
|
|
|
0 |
|
|
||||||
Решение этого равенства |
|
|
|
|
|
|
|
|
|
|
|
|
|
|
|
|
|
0,24ρ*l = |
cρ |
v |
|
|
|
1 |
ln(1+ αT |
|
), |
||||||||
|
|
|
|
|
|||||||||||||
0 |
|
j2 |
под α |
|
п.п. |
|
|||||||||||
а решение относительно температуры |
1 |
(eD −1), |
|
|
|
||||||||||||
|
Tп.п. = |
|
|
|
|||||||||||||
|
|
|
|
|
|
||||||||||||
|
|
|
|
|
α |
|
|
|
|
|
|
|
|
|
где |
D = |
0,24ρ |
0*αj2l |
- величина, зависящая и от режима сварки и от |
|
cρvпод |
|||||
|
|
|
теплофизических характеристик электродной проволоки.
Так как gпл = vплFρ = αpI/3600, получаем vпл = vпод = αpI/(3600Fρ) = αpj/(3600ρ).
Подставляя значения vпод в величину D, получаем
D = |
864ρ |
0*αjl |
. |
|
cα p |
||||
|
|
Для низкоуглеродистой проволоки марки Св-0,8А (ρ0* = 14*10-6 Ом*см; α = 72*10-4 1/0С и с = 0,148 кал/(г*0С)) значение D = 58,8(jl/αp)10-5.
65

800 |
L |
Н2=40мм |
|
600 |
H1 |
||
|
|||
400 |
|
|
|
200 |
|
|
10 20 30 40 50 60 70 80 90
Расчетный вылет, мм
Рис. 3.13. Распределение температуры по длине электродной проволоки.
На рис. 3.13 показано распределение температуры по длине электродной проволоки диаметром 4 мм при I = 840 A, vпод = 3,45 см/с, при автоматической сварке под флюсом и свободном вылете проволоки Н1 = 6,0 см. При расчете расчетный участок нагреваемой части электродной проволоки условно принят l = H1 + 0,75H2,
хотя при прохождении по каналу токоподводящего мундштука контактная поверхность каким-то образом распределена по длине мундштука. Сплошная линия – экспериментальная (А.Г.Мазель).
3.9 Использование тепловых расчетов применительно к условиям сварки
Рассмотренные вопросы распространения тепла позволяют получить расчетным путем температурные поля в свариваемых изделиях и находить рациональные технологические решения изготовления различных сварных конструкций. Температурные поля, связанные со сварочными режимами размерами и свойствами свариваемых металлов, позволяют определить области металла нагревающиеся при сварке до различных максимальных температур, и термические циклы T = f(t) для различных объемов свариваемого металла. При этом следует иметь в виду, что целый ряд допущений, принятый при выводе расчетных формул (сосредоточенность ввода тепла источником; независимость теплофизических свойств от температуры; исключение учета теплот фазовых превращений, включая скрытую теплоту плавления), довольно сильно искажают размеры температурных областей металла, нагревающихся до высоких температур. Так, например, если при дуговой сварке сталей рассчитанные изотермы температуры ниже 700 – 8000С удовлетворительно совпадают с определенными экспериментально, то изотермы более высоких температур (1200 – 15000С) уже значительно отличаются от фактических. Поэтому, например, контур сварочной ванны, рассчитанный по приведенным схемам расчета, может довольно значительно отличаться от реального.
Для правильной оценки температурных полей, областей нагрева и
охлаждения необходим выбор правильной расчетной схемы для решения конкретных задач. Некоторые рекомендации по выбору расчетных схем приведены в табл. 3.5
66
Таблица 3.5 Расчетные схемы процессов распространения тепла при сварке
Характеристи |
Процесс |
Форма |
Характеристика |
Рассчитываемая |
|
ка источника |
изделия |
расчетной схемы |
стадия процесса |
||
|
|||||
|
1.Наплавка |
|
Точечный подвижной |
|
|
|
Массивное тело |
источник тепла на |
Нагрев и охлаждение |
||
|
валика на |
||||
|
поверхности |
||||
|
поверхность |
|
|
||
|
|
полубесконечного тела |
|
||
|
дуговой |
|
|
||
|
|
|
|
||
|
сваркой |
Толстый лист |
То же, на поверхности |
То же |
|
Длительное |
|
плоского слоя |
|||
|
|
|
|||
воздействие; |
|
|
|
|
|
2. Дуговая |
|
Линейный подвижный |
|
||
источник |
сварка |
|
|
||
Тонкий лист |
источник тепла в |
То же |
|||
перемещается |
стыковых швов |
||||
|
пластине с теплоотдачей |
|
|||
прямолинейно и |
за один проход |
|
|
||
|
|
|
|||
равномерно |
|
|
|
|
|
|
|
Комбинация линейных |
|
||
|
3.Электрошлако |
|
подвижных источников |
|
|
|
|
тепла в пластине без |
|
||
|
вая сварка |
Толстый лист |
теплоотдачи (большая |
То же |
|
|
стыковых швов |
|
толщина) или с |
|
|
|
|
|
теплоотдачей (средняя |
|
|
|
|
|
толщина. |
|
|
|
|
|
Точечный мгновенный |
|
|
|
4.Заварка |
Массивное тело |
источник на |
|
|
|
небольших |
поверхности |
Охлаждение |
||
|
|
||||
|
поверхностных |
|
полубесконечного тела |
||
|
|
|
|||
Кратковременное |
дефектов |
Толстый лист |
То же, на поверхности |
|
|
воздействие; |
|
плоского слоя |
|
||
|
|
|
|||
источник |
|
|
Линейный мгновенный |
|
|
практически |
|
Тонкий лист |
источник в пластине с |
То же |
|
неподвижен |
5.Прихватка |
|
теплоотдачей |
|
|
|
|
|
|
||
|
Стержни |
|
|
||
|
стыков |
Плоский мгновенный |
|
||
|
|
малого |
источник тепла в |
То же |
|
|
|
поперечного |
|||
|
|
стержне с теплоотдачей |
|
||
|
|
сечения |
|
||
|
|
|
|
3.10 Контрольные вопросы к разделу «Сварочные источники тепла»
1.Что такое массовая и объемная теплоемкости? Единицы их измерения и характер зависимости от температуры.
2.Что такое температурное поле?
3.В чем заключается передача тепла теплопроводностью, конвекцией и радиацией?
4.Что такое краевые условия и как необходимо их учитывать?
5.Какая схематизация формы и размеров теплопроводящих тел применяется для тепловых расчетов?
6.Как схематизируют источники тепла применительно к тепловым расчетам при сварке?
7.Какие основные закономерности температурного поля в полубесконечном теле от действия точечного источника, перемещающегося по его поверхности с произвольной скоростью.
67
8.Рассчитайте длину сварочной ванны сзади точечного источника тепла при дуговой автоматической наплавке на поверхности массивного тела
при режиме: I = 500 A, Ud = 32 B, v = 12 м/ч. Материал тела: низкоуглеродистая сталь, нержавеющая сталь.
9.Какие основные особенности и закономерности нагрева полубесконечного тела быстродвижущимся источником тепла?
10.Рассмотрите основные положения и расчетные формулы распространения тепла в пластине без теплоотдачи и с теплоотдачей при различной скорости перемещения линейного источника тепла.
11.Какая стадия нагрева относится к периоду теплонасыщения?
Рассмотрите общие закономерности расчета температур в период теплонасыщения.
12.Какие особенности расчета температурных полей в период выравнивания температур?
13.Как влияет распределенность источника тепла на температуру объемов нагреваемого металла, расположенных близко к источнику и далеко от него?
14.Что такое коэффициент сосредоточенности источника тепла? Рассмотрите его влияние на нагрев металла.
15.Рассмотрите области применения расчетных методов тепловых основ сварки и дайте примеры использования различных расчетных схем.
68
РАЗДЕЛ 4. МЕТАЛЛУРГИЧЕСКИЕ ПРОЦЕССЫ ПРИ СВАРКЕ ПЛАВЛЕНИЕМ
4.1 Общая характеристика металлургических процессов при сварке плавлением
При сварке плавлением происходит интенсивное расплавление основного и присадочного материалов, зачастую и значительный перегрев выше температуры плавления. Наличие жидкого и парообразного металлов при большой относительной
поверхности создает возможность их значительного взаимодействия с окружающей средой. Это взаимодействие может быть вредным, снижая механические (эксплуатационные) свойства сварных соединений. Так кислород и азот, содержащиеся в атмосфере, сильно снижают механические свойства. Науглероживание расплавленного металла, происходящее, например, при неправильно выбранном соотношении ацетилен – кислород или сварке угольным электродом приводит к хрупкости металла. При попадании в сварочную ванну
водорода происходит значительное ухудшение свойств металла шва и появлению пористости в сварных швах.
Защита сварочной ванны достигается применением специальных электродных покрытий, сварочных флюсов и защитных газов. Однако вводимые в
покрытие газообразующие и шлакообразующие вещества, как правило, при сварке не нейтральны по отношению к металлу.
Обычно в качестве газообразующих веществ в покрытиях применяют органические добавки (крахмал, декстрин, целлюлозу и пр.) или углекислые соли – карбонаты (мрамор, магнезит и пр.). Первые, разлагаясь, образуют водород и различные газы СО, СО2, Н2О при наличии некоторого количества свободного кислорода. Вторые дают СО, СО2, а также кислород и пары воды, наличие которых определяется технологией изготовления покрытий. Шлакообразующие вещества представляют собой системы окислов различных элементов (чаще всего фторидов). Некоторые из них при сварочных условиях также взаимодействуют с металлом, в частности, окисляя его.
Флюсы – шлаки, применяемые при автоматической дуговой и электрошлаковой сварках, также содержат окислы и газообразующие добавки. Почти всегда как технологическая примесь в них содержится то или иное количество воды.
Для газовой защиты сварочного пространства применяют либо активные (реагирующие с металлом при сварке) газы, либо инертные. Из активных защитных газов наибольшее применение имеет углекислый газ. Менее распространены водород, пары воды и другие газы. В сварочных условиях углекислый газ может взаимодействовать с металлом в виде СО2, СО, а также углерода и кислорода. При наличии в нем примеси воды в процессе участвуют водород и пары воды. При других активных защитных газах основная часть газовой атмосферы, контактирующая с металлом в сварочной ванне, состоит из паров воды, водорода и кислорода. В технически применяемых инертных газах имеются примеси паров воды, кислорода и азота. Они даже при небольшой концентрации могут также взаимодействовать с металлом при сварке.
69
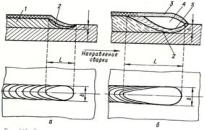
Таким образом, практически при всех способах сварки плавлением (кроме сварки в глубоком вакууме) приходится учитывать взаимодействие металла, его примесей или легирующих добавок с окружающей газовой, шлаковой или газошлаковой средой. Основными газами при этом являются О2, N2, Н2, СО, СО2, Н2О и некоторые их производные. Шлаки представляют собой системы окислов и галоидных соединений.
Протекание реакций взаимодействия как между простыми веществами, таки сложными соединениями определяется внешними факторами, в частности температурой, давлением, характером поверхности раздела, скоростью поступления веществ в реакционную зону, временем взаимодействия и др.
Рассмотрим температурную обстановку в сварочном реакционном пространстве при различных способах сварки. Необходимо отметить, что температурное состояние присадочного материала и сварочной ванны, находящейся на свариваемом изделии принципиально различно.
Различают сварочные ванны двух типов:
1)образующиеся при естественном охлаждении и формировании шва;
2)образующиеся при использовании искусственного охлаждения и принудительного формирования шва.
На рис. 4.1 показана ванна первого типа для ручной и автоматической дуговой сварки под флюсом. При ручной дуговой сварке шов 1 формируется из расплавленного металла 2. И шов, и металл находятся под слоем шлака. При автоматической сварке дуга и ванна закрыты слоем флюса. Расплавленный слой флюса 3 образует полость – пузырь, охватывающую зону 4 сварки.
Рис. 4.1. Сварочная ванна.
Для сварочной ванны этого типа характерны эллипсовидные очертания с различной степенью вытянутости вдоль продольной оси. Стенки ванны образует твердый оплавленный основной металл. Расплавленный металл 2, находящийся в начальный период ее существования, частично оттеснен от передней ее стенки к задней, вследствие чего образуется углубление, называемое кратером 5.
Основными размерами ванны являются: длина – L, ширина – b, величина заглубления в основной металл – h. Для различных участков ванны время пребывания металла в жидком состоянии различно. Наиболее долго в расплавленном виде находятся объемы металла, расположенные на продольной оси ванны, тогда как у ее краев металл кристаллизуется сразу же после расплавления. Распределение температуры по объему сварочной ванны также неравномерно. Средняя температура ванны при автоматической дуговой сварке примерно 18000С. Передний участок ванны, который находится под непосредственным воздействием дуги, нагрет
70