
- •1. Основные понятия
- •1.1. Современное состояние микроэлектроники
- •1.1.1. Роль электроники в мировой сфере производства и потребления
- •1.1.2. Зачем России своя электроника
- •1.2.1. Классификация интегральных микросхем
- •1.2.2. Технологические операции
- •1.2.3. Элементы микросхем
- •1.2.4. Проблемы в производстве
- •Контрольные вопросы
- •2. Материалы электронной компонентной базы
- •2.1. Классификация материалов
- •2.2. Классификация полупроводниковых материалов
- •2.2.1. Собственные и примесные полупроводники
- •2.2.3. Полупроводниковые соединения
- •Контрольные вопросы
- •3. Конструкции и технологические последовательности изготовления полупроводниковых приборов и ИС
- •3.1. Развитие технологии производства изделий электронной техники
- •3.2. Методы изоляции элементов монолитных биполярных ИС
- •3.3. Методы изоляции МДП-транзисторов
- •Контрольные вопросы
- •4. Химическая обработка и травление кремниевых пластин
- •4.1. Жидкостная очистка поверхности пластин
- •4.2. Травление
- •4.3. Пористый кремний
- •Контрольные вопросы
- •5. Плазменная обработка и травление материалов электронной компонентной базы
- •5.1. Ионное травленне
- •5.2. Плазмохимическое травление
- •5.3. Реактивное ионное травление
- •Контрольные вопросы
- •6. Термическая диффузия
- •6.1. Процессы диффузионного легирования
- •6.2. Уравнение диффузии
- •6.2.1. Диффузия из одной полуограниченной области в другую
- •6.2.2. Факторы, влияющие на величину коэффициента диффузии
- •6.3. Моделирование процессов диффузии в твердом теле
- •6.3.1. Диффузия из одной полуограниченной области в другую
- •6.3.2. Количество примеси, введенной из источника неограниченной мощности
- •6.3.3. Диффузия из слоя конечной толщины
- •6.3.4. Диффузия из бесконечно тонкого слоя (точечный источник)
- •6.6. Формула Пуассона
- •6.7. Диффузия в прямоугольное окно
- •6.8. “Разгонка” примеси. Многостадийная диффузия
- •6.9. Диффузия примеси в гетерогенной системе
- •6.10. Диффузия в область ограниченных размеров
- •6.11. Определение зависимости D(N)
- •6.12. Результирующее примесное распределение
- •6.13. Методы диффузионного легирования
- •6.13.1 Диффузия из пленок, наносимых на поверхность полупроводника
- •6.13.2 Диффузия в ампуле
- •6.13.3 Диффузия в потоке газа-носителя
- •6.13.4 Метод параллельного источника
- •6.14. Источники диффузанта
- •6.14.2 Алюминий (Al), галлий (Ga) и индий (In)
- •6.14.3 Фосфор (P) мышьяк (As) и сурьма (Sb)
- •6.14.4 Эффект вытеснения коллекторного перехода
- •6.14.5 Другие диффузанты
- •6.15. Выбор легирующей примеси
- •Контрольные вопросы
- •7. Ионное легирование
- •7.1. Общие принципы процесса ионной имплантации
- •7.2. Пробеги и дисперсии пробегов ионов
- •7.2.1. Распределение пробегов ионов
- •7.2.2. Боковое рассеяние ионов
- •7.2.3. Ионное каналирование
- •7.3. Влияние радиационных дефектов
- •7.4. Отжиг дефектов ионно-имплантированных слоев
- •7.4.1. Примеры профилей распределения ионов
- •7.4.2. Лазерный и электронно-лучевой отжиг
- •7.5. Влияние технологических факторов
- •7.5.1. Диффузия имплантированных примесей
- •7.5.2. Технология маскирования при ионной имплантации
- •7.5.3. Гетерирование
- •7.6. Преимущества и недостатки ионного легирования
- •Контрольные вопросы
- •8. Методы создания диэлектрических слоев
- •8.1. Термическое окисление
- •8.2. Осаждение пленок диоксида кремния
- •8.3. Получение пленок нитрида кремния
- •8.4. Плазмохимическое осаждение
- •8.5. Особенности окисления некоторых материалов
- •8.6. Воспроизведение рельефа поверхности
- •Контрольные вопросы
- •9. Термическое окисление кремния
- •9.1. Методы получения пленок оксида кремния
- •9.2. Механизмы окисления кремния
- •9.3. Кислород в кремнии
- •9.4. Свойства и применения пленок оксида кремния
- •9.5. Модель процесса
- •9.6. Перераспределение примеси при окислении
- •9.7. Особенности технологии МДП структур
- •9.7.1. Влияние режимов окисления и термообработок на свойства МДП структур на основе кремния
- •9.7.2. Механизмы нестабильности МДП структур
- •9.7.3 Методы повышения стабильности МДП структур
- •Контрольные вопросы
- •10. Методы литографии
- •10.1. Электронно-лучевая литография
- •10.2. Рентгеновская литография
- •10.3. Ионно-лучевая литография
- •10.4. Сравнение и тенденция развития процессов литографии
- •Контрольные вопросы
- •11. Технология фотолитографии
- •11.1. Стандартная фотолитография
- •11.2. Процесс переноса изображения в фотолитографии
- •11.3. Фотолитография в глубоком ультрафиолете
- •11.4. Волновые эффекты при экспонировании
- •Контрольные вопросы
- •12. Физико-химические основы технологии эпитаксиальных слоев
- •12.1. Эпитаксия из газовой фазы
- •12.1.2. Реакторы установок эпитаксиального наращивания
- •12.1.3. Легирование и автолегирование эпитаксиальных слоев
- •12.1.4. Технология процесса эпитаксии кремния
- •12.2. Молекулярно-лучевая эпитаксия
- •12.3. Эпитаксия кремния на изолирующей подложке
- •12.4. Получение эпитаксиальных слоев полупроводниковых соединений
- •Контрольные вопросы
- •13. Технология многоуровневой металлизации
- •13.1. Термическое испарение в вакууме
- •13.1.1. Физические основы термического вакуумного напыления
- •13.1.2. Конденсация вещества на подложке
- •13.1.3. Оборудование процесса термического вакуумного напыления
- •13.1.4. Распределение толщины пленки по подложке
- •13.2. Методы ионно-плазменного распыления
- •13.2.1. Механизмы распыления вещества потоком ионов
- •13.2.2. Ионно-плазменное распыление на постоянном токе (катодное распыление)
- •Контрольные вопросы
- •14. Монтажно-сборочные операции
- •14.1. Разделение пластин на кристаллы
- •14.2. Присоединение кристаллов к корпусу
- •14.2.1. Присоединение кристалла к основанию корпуса
- •14.2.2. Присоединение выводов
- •14.2.3. Герметизация
- •14.3. Монтаж приборов в корпус
- •Контрольные вопросы
- •15. Контрольные операции
- •15. 1. Функциональный контроль приборов
- •15.2. Испытания и измерения
- •15.2.1. Контроль технологического процесса
- •15.2.2. Причины брака
- •15.2.3. Методы контроля толщины пленок
- •15. 3. Заключительные операции
- •15.3.1. Герметизация кристалла
- •15.3.2. Контроль герметичности
- •Контрольные вопросы
242
Измерение емкости конденсатора, диэлектриком которого служит напыляемая пленка. Точность измерения толщины 3 – 5 % при ширине проводника и зазора 0,2 мм.
15.3. Заключительные операции
15.3.1.Герметизация кристалла
Для герметичного соединения основания корпуса с крышкой широко используют пайку, электроконтактную и холодную сварку, а для герметизации кристалла на держателе – заливку, обволакивание и опрессовку пластмассой.
Пайка металла с металлом. Основными элементами паяного соединения при герметизации интегральных схем являются основание корпуса и крышка. Процесс соединения основания корпуса с крышкой может проводиться либо с использованием прослойки припоя, которая располагается между основанием корпуса и крышкой в виде кольца, либо без прослойки припоя. Во втором случае края основания корпуса и крышки предварительно облуживают припоем.
Процесс пайки проводят в вакууме, инертной или восстановительной среде. При использовании флюсов пайку можно проводить на воздухе. Флюсы в значительной степени улучшают смачивание и растекание припоя по соединяемым поверхностям деталей. По выполняемой роли флюсы подразделяют на две группы: защитные и активные. Защитные флюсы предохраняют детали от окисления в процессе пайки, а активные способствуют восстановлению оксидов, образовавшихся в процессе пайки. В качестве защитных флюсов наиболее часто используют растворы канифоли. Активными флюсами служат хлористый цинк и хлористый аммоний. Для пайки используют припои ПОС-40 и ПОС-60.
Пайка керамики с металлом обеспечивает более надежную герметизацию интегральных схем.
Для получения паяных соединений керамики с металлом ее предварительно металлизируют с помощью паст, которые наносят на керамическую деталь. Хорошее сцепление металлизационного слоя с поверхностью керамики достигается высокотемпературным вжиганием. При вжигании паст растворитель улетучивается, а металлические частицы прочно соединяются с поверхностью керамической детали. Полученную таким образом металлизированную керамику можно паять обычными припоями.
Пайка стекла с металлом. Стекло ни с одним из чистых металлов не спаивается, так как чистая поверхность металлов не смачивается или плохо смачивается жидким стеклом. Однако если поверхность металла покрыта слоем оксида, то смачивание улучшается, оксид частично растворяется в стекле и после охлаждения может произойти герметичное соединение. Основная трудность при изготовлении спаев металл стекло состоит в подборе компонентов стекла и металла с достаточно близкими значениями КТР. Для получения герметичных спаев стекла с металлом используют три
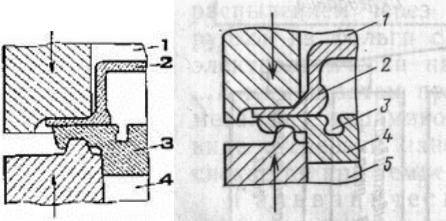
243
способа нагрева исходных деталей: в пламени газовой горелки, с помощью токов высокой частоты, в муфельных или силитовых печах. Во всех случаях процесс проводят на воздухе, так как наличие оксидной пленки способствует процессу пайки.
Электроконтактная сварка основана на расплавлении определенных частей соединяемых металлических деталей за счет прохождения через них электрического тока. К свариваемым деталям подводят два электрода, на которые подают напряжение. Большие плотности тока разогревают контактные участки до расплавления определенных зон исходных материалов. Большое значение имеет время прохождения сварочного тока через электроды и детали.
Холодная сварка обеспечивает прочное герметичное соединение наиболее часто используемых разнородных металлов (меди, никеля, ковара и стали).
Это сварка давлением без нагрева, осуществляется за счет совместной пластической деформации поверхностей соединяемых деталей. Усилие сжатия при холодной сварке зависит от пластичности материалов соединяемых деталей и контактной площади рабочего инструмента (пуансона).
Большое значение для проведения процесса холодной сварки имеет наличие на поверхности соединяемых деталей пленки оксида. Если эта пленка пластичная и более мягкая, чем основной металл, то под давлением она растекается во все стороны и утоньшается, разделяя тем самым чистые металлические поверхности, в результате чего сварка не происходит. Если оксидная пленка более хрупкая и твердая, чем покрываемый ею металл, то под давлением она трескается, причем растрескивание происходит одинаково на обеих соединяемых деталях.
В зависимости от свойств свариваемых материалов применяют двуили одностороннюю холодную сварку (рис. 15.1). Односторонняя сварка применяется для материалов с различной пластичностью.
Рис. 15.1. Схема односторонней сварки: 1 – верхний пуансон; 2 – крышка корпуса; 3 –
разгрузочная канавка; 4 – основание корпуса; 5 – нижний пуансон
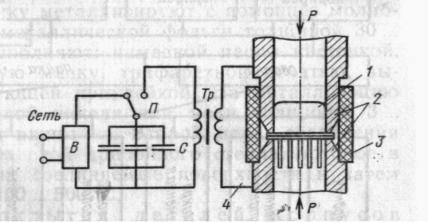
244
Достоинством холодной сварки являются: отсутствие нагрева, газовыделений и выплеска металла, а также простота сварочного оборудования.
Недостатки: увеличение периметра наружного контура корпуса и значительные деформации околошовной области, трудность надежного подсоединения тонкостенных деталей, неравномерность пластических деформаций по периметру прямоугольного корпуса, возможности нарушения вакуумной плотности шва из-за непровара или подреза со стороны более мягкого материала, ограниченный выбор материалов как по толщине, так и по свойствам.
Контактная электросварка. При герметизации микросхем наиболее часто применяется конденсаторная контурная сварка. Сварка происходит в момент разрядки конденсаторной батареи на первичную обмотку сварочного трансформатора. Вторичная обмотка трансформатора соединена с электродами, выполняющими роль сварочного инструмента (рис. 15.2).
Рис. 15.2. Схема контурной конденсаторной электросварки:
1 – корпус; 2 – электроды; 3 – стакан; 4 – электрическая цепь сварочной установки; Р – сжимающее усилие
Способ широко применяется для герметизации малогабаритных металлостеклянных корпусов квадратной и прямоугольной формы.
Роликовая сварка выполняется подвижными электродами. Электроды, подводящие ток и имеющие форму роликов, в процессе сварки прокатываются по периметру корпуса на небольшом расстоянии друг от друга по одной поверхности. Сварка выполняется в среде аргона. Метод обеспечивает получение плотного шва, применяется для герметизации металлостеклянных и металлокерамических прямоугольны корпусов периметром до 75 мм, корпуса круглой и прямоугольной формы со штыревыми выводами (рис. 15.3).
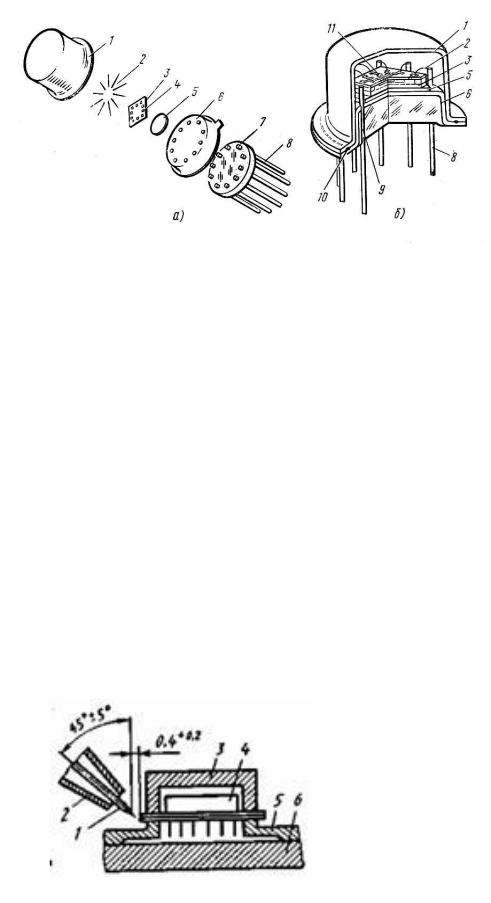
245
Рис. 15.3. Схема сборки (а) и разрез ИС (б) в круглом корпусе:
1 баллон; 2 соединительные проводники; 3 кристалл; 4 контактные площадки; 5 припой; 6 колпачёк ножки; 7 стекло; 8 выводы; 9 спай выводов со стеклом; 10 соединение электроконтактной сваркой баллона и ножки; 11 металлизационный слой (шина)
Достоинствами контактной электросварки являются: высока воспроизводимость результатов, так как энергия сварки постоянна; минимальная зона нагрева свариваемых деталей, так как процесс кратковременный, легкость автоматизации.
Недостатки: повышенные тебования к плоскостности и равномерности толщины соединяемых деталей, невозможность сваривания высокотеплопроводных металлов.
При аргонно-дуговой сварке, которая является одним из видов электродуговой, аргон, обтекающий электрод и зону соединения, предохраняет расплавленный металл от воздействия кислорода и азота воздуха. Вольфрамовый электрод служит для возбуждения и поддержания горения дуги. При герметизации этим способом (рис. 15.4) кромки крышки и основания корпуса микросхемы под воздействием теплоты электрической дуги оплавляются с образованием сварочной ванны. Охлаждаясь, металл в месте сварки кристаллизуется, и образуется сварочный шов.
Рис. 15.4. Взаимное расположение электрода и корпуса ИМС при аргонно-дуговой сварке:
1 – электрод; 2 – сопло; 3, 5 – теплоотводы крышки и основания, корпус микросхемы; 4 – крышка корпуса; 6 – плита
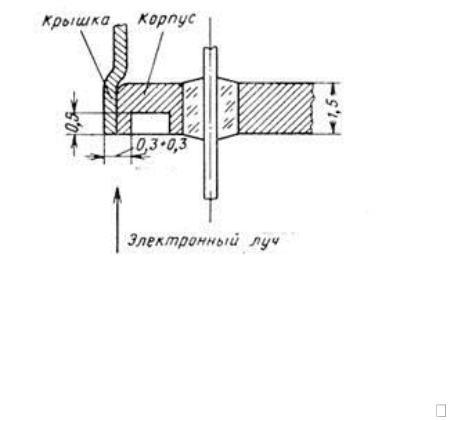
246
Основное преимущество аргонно-дуговой сварки возможность местного (локального) нагрева деталей, а недостаток повышенные требования к точности их совмещения и изготовления оснастки. Аргоннодуговой сваркой герметизируют металлостеклянные корпуса со штыревыми выводами.
Электроннолучевая сварка имеет ряд преимуществ перед другими способами герметизации.
Для уменьшения допусков на размеры зазора и воздействия сварки на металлостеклянные спаи необходимо разрабатывать специальную конструкцию корпусов и подготовку кромок. Наиболее рациональная форма кромок корпуса под сварку приведена на рис. 15.5. При такой форме соединение происходит за счет взаимного расплавления металла крышки и основания. Глубина проплавления может достигать 0,5 мм, что обеспечивает герметичность изделия.
Рис. 15.5. Форма кромок металлостеклянного корпуса под электроннолучевую сварку
Пайка. Герметизацию пайкой применяют в стеклянных и керамических корпусах с плоскими планарными выводами.
Золотое покрытие на коваровой рамке позволяет получать надежное паяное соединение с крышкой корпуса (никель, никелированная медь и др.).
Пайка припоями выполняется при температурах 170 350 °С. Перед пайкой изделие облуживают расплавленным припоем или помещают его между соединяемыми деталями в виде прокладок, таблеток, колец и др. Далее корпуса герметизируют, применяя различные способы нагрева, необходимые для оплавления припоя.
Недостаток метода значительный нагрев основания корпуса, на котором расположена ИМС, а также необходимость применения флюса, остатки которого трудно полностью удалить, и они могут попасть внутрь корпуса.
При обдуве струей горячего газа (азота или аргона) корпуса со стороны крышки применение флюса исключается, так как пайка проводится в инертной атмосфере.
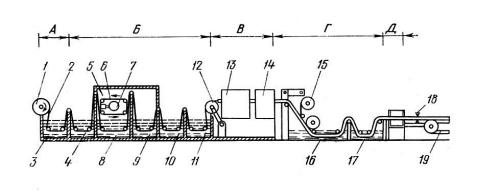
247
Пайку стеклом применяют не только для контакта кристаллов с корпусами и крепления внешних выводов к керамическим основаниям, но и для соединения керамических крышек с основаниями. При такой пайке в качестве припоев используют низкотемпературные стекла.
Герметизация пластмассой. Основными методами герметизации являются заливка, обволакивание и опрессовка под давлением. При герметизации заливкой используют полые формы, в которые помещают полупроводниковые кристаллы с припаянными внешними выводами. Внутрь форм заливают пластмассу.
При герметизации приборов обволакиванием берут два (или более) вывода, изготовленных из ленточного или проволочного материала, соединяют их между собой стеклянной или пластмассовой бусой и на один из выводов напаивают полупроводниковый кристалл, а к другому (другим) выводу присоединяют электрические контактные проводники. Полученную таким образом сборку герметизируют обволакиванием пластмассой.
Наиболее перспективным путем решения проблемы сборки и герметизации приборов является герметизация кристаллов с активными элементами на металлической ленте с последующей герметизацией пластмассой. Основным элементом конструкции пластмассового корпуса является металлическая лента.
Технологическая схема пластмассовой герметизации прибора включает в себя основные этапы планарной технологии. Присоединяют полупроводниковые кристаллы с активными элементами к металлической ленте, покрытой золотом, эвтектическим сплавлением золота с кремнием или обычной пайкой. Металлическую ленту изготовляют из ковара, меди, молибдена, стали, никеля.
Рис. 15.6. Схема линии сборки интегральных схем
На линии сборки используют трансферные ленты. Сборка и транспортировка осуществляются на коваровой ленте, которую на участках А и Б подвергают фотолитографии для получения выводов 2 (рис. 15.6). На участках В, Г и Д на базе ленты с выводными рамками изготавливают корпуса приборов с золочеными выводами. Отрезки ленты с корпусами поступают на сборку. Лента 2, сматываясь с катушки 1, подвергается промывке и обезжириванию в ванне 3 и нанесению фоторезиста в ванне 4, экспонированию в установке 5 с помощью ультрафиолетовой лампы 7. Роль маски в установке выполняет непрерывно движущаяся синхронно с лентой 2
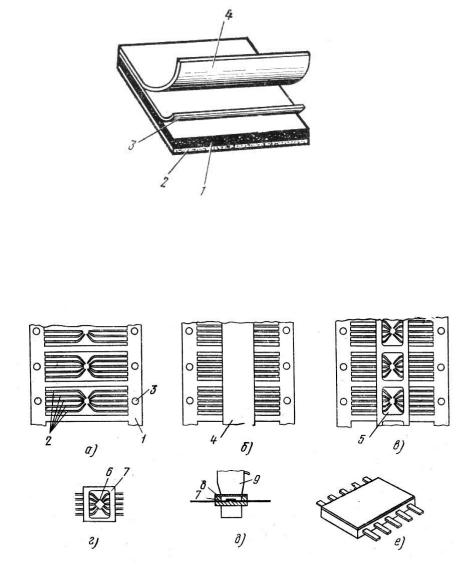
248
лента 6. Затем ленты промывают в ваннах 8 и 9. Выводы рамки 2 (рис. 15.8, а) и перфорационные отверстия вытравливают в ванне 10. Слой фоторезиста удаляют в ванне 11, и на выходе ленту сушат. Полученные перфорационные отверстия используют для натяжения и перемещения ленты с помощью звездочки 12. В установке 13 на коваровую ленту с выводами приклеивают с двух сторон трансферную ленту со слоем припоечного стекла. Полученная система обжигается, адгезивный слой выгорает, а стекло спаивается с металлом основной ленты (рис. 15.8, б). Охлаждение до комнатной температуры производят в камере 14. С помощью устройства 15 на стеклянные слои приклеивают маскирующие ленты с окнами, через которые в ванне 16 осуществляют вытравливание полостей до обнаружения внутренних выводов (рис. 15.8, е).
Рис. 15.7. Трансферная лента:
1 несущий слой; 2 трансферный слой; 3 адгезивный слой; 4 антиадгезивная бумага
Рис. 15.8. Схема автоматизированной сборки ИС на ленте:
1 лента-носитель; 2 выводы (после травления); 3 перфорация для перемещения ленты; 4 стеклянная лента-припой; 5 полость корпуса ИС; 6 кристалл с готовыми структурами; 7 корпус; 8 крышка;
9 нагревательный инструмент
Полученные таким образом из металлической и стеклянных лент корпусные блоки подают в ванну 17 для золочения выводов. На устройстве 18