
- •1. Основные понятия
- •1.1. Современное состояние микроэлектроники
- •1.1.1. Роль электроники в мировой сфере производства и потребления
- •1.1.2. Зачем России своя электроника
- •1.2.1. Классификация интегральных микросхем
- •1.2.2. Технологические операции
- •1.2.3. Элементы микросхем
- •1.2.4. Проблемы в производстве
- •Контрольные вопросы
- •2. Материалы электронной компонентной базы
- •2.1. Классификация материалов
- •2.2. Классификация полупроводниковых материалов
- •2.2.1. Собственные и примесные полупроводники
- •2.2.3. Полупроводниковые соединения
- •Контрольные вопросы
- •3. Конструкции и технологические последовательности изготовления полупроводниковых приборов и ИС
- •3.1. Развитие технологии производства изделий электронной техники
- •3.2. Методы изоляции элементов монолитных биполярных ИС
- •3.3. Методы изоляции МДП-транзисторов
- •Контрольные вопросы
- •4. Химическая обработка и травление кремниевых пластин
- •4.1. Жидкостная очистка поверхности пластин
- •4.2. Травление
- •4.3. Пористый кремний
- •Контрольные вопросы
- •5. Плазменная обработка и травление материалов электронной компонентной базы
- •5.1. Ионное травленне
- •5.2. Плазмохимическое травление
- •5.3. Реактивное ионное травление
- •Контрольные вопросы
- •6. Термическая диффузия
- •6.1. Процессы диффузионного легирования
- •6.2. Уравнение диффузии
- •6.2.1. Диффузия из одной полуограниченной области в другую
- •6.2.2. Факторы, влияющие на величину коэффициента диффузии
- •6.3. Моделирование процессов диффузии в твердом теле
- •6.3.1. Диффузия из одной полуограниченной области в другую
- •6.3.2. Количество примеси, введенной из источника неограниченной мощности
- •6.3.3. Диффузия из слоя конечной толщины
- •6.3.4. Диффузия из бесконечно тонкого слоя (точечный источник)
- •6.6. Формула Пуассона
- •6.7. Диффузия в прямоугольное окно
- •6.8. “Разгонка” примеси. Многостадийная диффузия
- •6.9. Диффузия примеси в гетерогенной системе
- •6.10. Диффузия в область ограниченных размеров
- •6.11. Определение зависимости D(N)
- •6.12. Результирующее примесное распределение
- •6.13. Методы диффузионного легирования
- •6.13.1 Диффузия из пленок, наносимых на поверхность полупроводника
- •6.13.2 Диффузия в ампуле
- •6.13.3 Диффузия в потоке газа-носителя
- •6.13.4 Метод параллельного источника
- •6.14. Источники диффузанта
- •6.14.2 Алюминий (Al), галлий (Ga) и индий (In)
- •6.14.3 Фосфор (P) мышьяк (As) и сурьма (Sb)
- •6.14.4 Эффект вытеснения коллекторного перехода
- •6.14.5 Другие диффузанты
- •6.15. Выбор легирующей примеси
- •Контрольные вопросы
- •7. Ионное легирование
- •7.1. Общие принципы процесса ионной имплантации
- •7.2. Пробеги и дисперсии пробегов ионов
- •7.2.1. Распределение пробегов ионов
- •7.2.2. Боковое рассеяние ионов
- •7.2.3. Ионное каналирование
- •7.3. Влияние радиационных дефектов
- •7.4. Отжиг дефектов ионно-имплантированных слоев
- •7.4.1. Примеры профилей распределения ионов
- •7.4.2. Лазерный и электронно-лучевой отжиг
- •7.5. Влияние технологических факторов
- •7.5.1. Диффузия имплантированных примесей
- •7.5.2. Технология маскирования при ионной имплантации
- •7.5.3. Гетерирование
- •7.6. Преимущества и недостатки ионного легирования
- •Контрольные вопросы
- •8. Методы создания диэлектрических слоев
- •8.1. Термическое окисление
- •8.2. Осаждение пленок диоксида кремния
- •8.3. Получение пленок нитрида кремния
- •8.4. Плазмохимическое осаждение
- •8.5. Особенности окисления некоторых материалов
- •8.6. Воспроизведение рельефа поверхности
- •Контрольные вопросы
- •9. Термическое окисление кремния
- •9.1. Методы получения пленок оксида кремния
- •9.2. Механизмы окисления кремния
- •9.3. Кислород в кремнии
- •9.4. Свойства и применения пленок оксида кремния
- •9.5. Модель процесса
- •9.6. Перераспределение примеси при окислении
- •9.7. Особенности технологии МДП структур
- •9.7.1. Влияние режимов окисления и термообработок на свойства МДП структур на основе кремния
- •9.7.2. Механизмы нестабильности МДП структур
- •9.7.3 Методы повышения стабильности МДП структур
- •Контрольные вопросы
- •10. Методы литографии
- •10.1. Электронно-лучевая литография
- •10.2. Рентгеновская литография
- •10.3. Ионно-лучевая литография
- •10.4. Сравнение и тенденция развития процессов литографии
- •Контрольные вопросы
- •11. Технология фотолитографии
- •11.1. Стандартная фотолитография
- •11.2. Процесс переноса изображения в фотолитографии
- •11.3. Фотолитография в глубоком ультрафиолете
- •11.4. Волновые эффекты при экспонировании
- •Контрольные вопросы
- •12. Физико-химические основы технологии эпитаксиальных слоев
- •12.1. Эпитаксия из газовой фазы
- •12.1.2. Реакторы установок эпитаксиального наращивания
- •12.1.3. Легирование и автолегирование эпитаксиальных слоев
- •12.1.4. Технология процесса эпитаксии кремния
- •12.2. Молекулярно-лучевая эпитаксия
- •12.3. Эпитаксия кремния на изолирующей подложке
- •12.4. Получение эпитаксиальных слоев полупроводниковых соединений
- •Контрольные вопросы
- •13. Технология многоуровневой металлизации
- •13.1. Термическое испарение в вакууме
- •13.1.1. Физические основы термического вакуумного напыления
- •13.1.2. Конденсация вещества на подложке
- •13.1.3. Оборудование процесса термического вакуумного напыления
- •13.1.4. Распределение толщины пленки по подложке
- •13.2. Методы ионно-плазменного распыления
- •13.2.1. Механизмы распыления вещества потоком ионов
- •13.2.2. Ионно-плазменное распыление на постоянном токе (катодное распыление)
- •Контрольные вопросы
- •14. Монтажно-сборочные операции
- •14.1. Разделение пластин на кристаллы
- •14.2. Присоединение кристаллов к корпусу
- •14.2.1. Присоединение кристалла к основанию корпуса
- •14.2.2. Присоединение выводов
- •14.2.3. Герметизация
- •14.3. Монтаж приборов в корпус
- •Контрольные вопросы
- •15. Контрольные операции
- •15. 1. Функциональный контроль приборов
- •15.2. Испытания и измерения
- •15.2.1. Контроль технологического процесса
- •15.2.2. Причины брака
- •15.2.3. Методы контроля толщины пленок
- •15. 3. Заключительные операции
- •15.3.1. Герметизация кристалла
- •15.3.2. Контроль герметичности
- •Контрольные вопросы
187
системы требуется длительный отжиг в вакууме. Поэтому подложки загружают в шлюзовое устройство, отделенное от рабочей камеры высоковакуумным затвором. После откачки шлюзового устройства подложки перемещаются в рабочую камеру).
10 – трубопровод к системе безмасленной откачки шлюзового устройства;
11– загрузочное шлюзовое устройство;
12– устройство для магнитного перемещения загрузочной штанги;
13, 14, 15, 16 и 17 – элементы устройства формирования ионного пучка для ионного легирования; 18 – источник для ионного легирования в целом с системой безмаслянной
откачки (криогенный насос); 19 – подложкодержатель с подложкой и резистивным нагревателем; 20 – натекатель.
12.3. Эпитаксия кремния на изолирующей подложке
Переход от дискретных полупроводниковых приборов к интегральным схемам явился революционным событием не только в технологии твердотельной электроники, но и в развитии нашей цивилизации
вцелом. История развития:
штучное изготовление дискретных приборов и сборка их на
плате в электронную схему;
групповое изготовление дискретных приборов (много приборов на одной пластине), резка пластины на отдельные приборы, их корпусирование и сборка в электронную схему;
зачем резать? может быть их сразу и соединять? →
изготовление интегральных схем, а затем групповое изготовление интегральных схем.
Однако при переходе к интегральным схемам сразу возникла проблема электрической изоляции отдельных элементов друг от друга, так как они находятся в одной полупроводниковой пластине.
Наиболее распространенным методом изоляции элементов интегральных схем является изоляция обратносмещенным р – n переходом:
В пластине р-типа проводимости создается p-n-p транзистор и разделительные области р+- типа. Таким образом, транзистор оказывается отделенным от остальной пластины p-n переходом. Если подать на этот переход отрицательное смещение, то, благодаря малым обратным токам p-n перехода, транзистор будет электрически изолирован от остальной части схемы.
Однако метод изоляции обратносмещенным p-n переходом обладает рядом существенных недостатков. Основным из которых является низкая эффективность изоляции на высоких частотах (из-за паразитной емкости обратносмещенного перехода). Кроме того, такие интегральные схемы обладают низкой радиационной стойкостью (из-за возрастания обратных токов переходов под воздействием ионизирующего излучения).
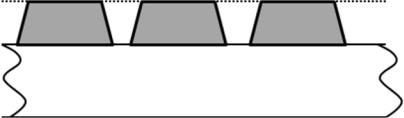
188
Одним из путей решения этих проблем является формирование элементов схемы в монокристаллической пленке, выращенной на изолирующей подложке. Точнее, в отдельных островках монокристаллического кремния, находящихся на изолирующей подложке:
Рис. 12.14.
Это возможно при использовании гетероэпитаксии кремния на изолирующей монокристаллической подложке. При этом подложка должна иметь близкие к кремнию параметры кристаллической решетки, значения температурного коэффициента расширения и минимальное химическое взаимодействие. В настоящее время наибольшее распространение получила гетероэпитаксия кремния на сапфире (Al2O3), так называемая технология КНС.
Получение гетероэпитаксиальных слоев кремния на сапфире проводится методом пиролитического разложения силана: SiH4→Si+H2. Выбор метода обусловлен двумя причинами:
возможностью снижения температуры процесса (как правило, 1000 – 1050 °С), что уменьшает автолегирование растущего слоя алюминием из сапфировой подложки;
химическим взаимодействием хлоридов, используемых в методе
восстановления, с сапфировой подложкой.
Технологический процесс и оборудование для КНС процесса по существу идентичны используемым для автоэпитаксии кремния.
Итак, первой проблемой гетероэпитаксиальных слоев кремния на сапфире является автолегирование алюминием. Атомарный алюминий образуется в результате взаимодействия подложки с осаждаемым кремнием:
Si + Al2O3 → SiO + Al2O
и последующим взаимодействием окисла алюминия с водородом газовой смеси (восстановление алюминия из окисла):
Al2O + H2 → Al + H2O.
Перечисленные реакции протекают на начальной стадии процесса, до образования сплошного слоя кремния. Однако при дальнейших температурных обработках при производстве интегральных схем атомы алюминия могут диффундировать вглубь эпитаксиального слоя. Для предотвращения участия в автолегировании обратной стороны сапфировой подложки её покрывают тугоплавким металлом, например вольфрамом.
Вторая проблема эпитаксиальных слоев КНС заключается в неполном соответствии кристаллических решеток кремния и сапфира и в различии
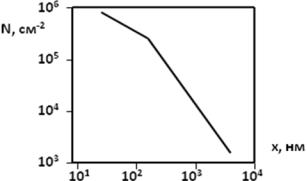
189
термических коэффициентов термического расширения. Это приводит к высокой плотности дефектов в пограничной области эпитаксиального слоя, примыкающего к подложке. Зависимость плотности дефектов упаковки кристаллической решетки от расстояния от поверхности подложки приведена на рисунке 12.15.
Рис. 12.15.
Если учесть, что толщины эпитаксиальных слоев, как правило, не превышают 1 мкм, то видно, что плотность дефектов в них оказывается достаточно высокой. Высокая плотность дефектов уменьшает время жизни неосновных носителей заряда. Поэтому КНС целесообразно применять для изготовления интегральных схем на приборах, работающих на основных носителях заряда – на полевых транзисторах.
Преодоление указанных проблем во многом возможно при использовании метода молекулярно-лучевой эпитаксии. Снижение температуры процесса ведет к уменьшению автолегирования и к снижению механических напряжений между пленкой и подложкой, со всеми вытекающими отсюда последствиями.
Получение монокристаллической пленки кремния на аморфной подложке
Известны работы, в которых монокристаллическую пленку кремния получали на аморфных подложках. Суть метода заключается в нанесении на подложку пленки аморфного или поликристаллического кремния и в её последующей кристаллизации (перекристаллизации) с целью получения монокристаллической пленки. Строго говоря, данный метод нельзя назвать эпитаксией, так как в процессе наращивания пленка не является монокристаллической. Для изготовления монокристаллических пленок кремния на аморфных подложках предложен ряд методов. Рассмотрим один из них.
На монокристаллической кремневой подложке создаётся профиль со ступенькой, как показано на рисунке 12.16. Затем подложка покрывается оксидом (кроме выступающей части).

190
Рис. 12.16.
После этого наносится пленка поликристаллического или аморфного кремния (~ 0,5 мкм). Сверху структура покрывается слоем диоксида или нитрида кремния. Полосковый подвижной нагреватель первоначально устанавливается над открытой частью кремниевой подложки и обеспечивает расплавление поликристаллической пленки по всей толщине. При движении нагревателя расплав за ним остывает, подложка играет роль затравочного кристалла и монокристаллическая пленка растет в боковом направлении вслед за перемещающимся нагревателем между двумя слоями окисла. Верхний слой окисла (нитрида) улучшает термостабильность расплавленной зоны и уменьшает вероятность загрязнения монокристаллического слоя. В качестве нагревателя может быть использован сканирующий луч лазера. Метод принципиально позволяет создавать монокристаллические слои на большой площади, например на всей поверхности подложки. Это в свою очередь открывает возможность создания трехразмерных (3D) монолитных интегральных схем. Однако до уровне промышленного производства этот метод в настоящее время не доведен.
12.4. Получение эпитаксиальных слоев полупроводниковых соединений
Получение эпитаксиальных слоев различных полупроводниковых соединений типа AIIIBV и AIIBVI не имеет между собой принципиальных отличий. Поэтому мы будем рассматривать эпитаксию наиболее распространенного полупроводникового материала – арсенида галлия (GaAs), отмечая при необходимости особенности получения других материалов.
Для получения монокристаллических слоев полупроводниковых соединений используются
эпитаксия из жидкой фазы (жидкостная эпитаксия);
эпитаксия из газовой фазы (газофазная эпитаксия);
молекулярно-лучевая эпитаксия.
Жидкостная эпитаксия заключается в выращивании монокристаллической пленки из раствора-расплава, контактирующего с
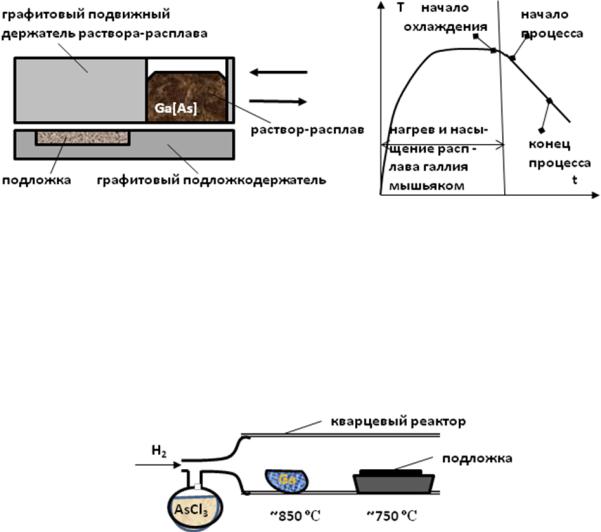
191
монокристаллической подложкой. При эпитаксии арсенида галлия в качестве раствора-расплава используется расплав галлия (Тпл= 29,8 ºС), насыщенный мышьяком. Процедура выращивания пленки заключается в следующем. Галлий помещают в специальную кассету (рисунок 12.17). Для насыщения галлия мышьяком в расплав добавляют поликристаллический GaAs и проводят термообработку при температурах на 15 – 20 ºС выше температуры роста (750 – 800 ºС). После этого начинают медленно (доли градуса Цельсия в минуту) охлаждать систему и сдвигают кассету с расплавом так, чтобы расплав контактировал с подложкой. При снижении температуры происходит осаждение арсенида галлия на подложке. Качественная зависимость температуры от времени процесса приведена на рисунке 12.18.
Рис. 12.17. |
Рис. 12.18. |
Для легирования эпитаксиального слоя в раствор-расплав вводятся донорные (теллур, селен, олово) или акцепторные (цинк, кадмий, германий) примеси. Методом жидкофазной эпитаксии получают слои арсенида галлия толщиной от 0,1 мкм до нескольких сотен мкм.
Газофазная эпитаксия. При газофазной эпитаксии арсенида галлия используется реакция восстановления. Источником мышьяка является AsCl3, источником галлия – жидкий галлий, а газом носителем водород.
Рис. 12.19.
Водород захватывает пары AsCl3 и переносит их в реактор. При нагревании в присутствии водорода AsCl3 восстанавливается:
AsCl3 + Н2 → HCl
Образовавшийся хлористый водород взаимодействует с галлием:
Ga + HCl → GaCl + H2