
- •1. Основные понятия
- •1.1. Современное состояние микроэлектроники
- •1.1.1. Роль электроники в мировой сфере производства и потребления
- •1.1.2. Зачем России своя электроника
- •1.2.1. Классификация интегральных микросхем
- •1.2.2. Технологические операции
- •1.2.3. Элементы микросхем
- •1.2.4. Проблемы в производстве
- •Контрольные вопросы
- •2. Материалы электронной компонентной базы
- •2.1. Классификация материалов
- •2.2. Классификация полупроводниковых материалов
- •2.2.1. Собственные и примесные полупроводники
- •2.2.3. Полупроводниковые соединения
- •Контрольные вопросы
- •3. Конструкции и технологические последовательности изготовления полупроводниковых приборов и ИС
- •3.1. Развитие технологии производства изделий электронной техники
- •3.2. Методы изоляции элементов монолитных биполярных ИС
- •3.3. Методы изоляции МДП-транзисторов
- •Контрольные вопросы
- •4. Химическая обработка и травление кремниевых пластин
- •4.1. Жидкостная очистка поверхности пластин
- •4.2. Травление
- •4.3. Пористый кремний
- •Контрольные вопросы
- •5. Плазменная обработка и травление материалов электронной компонентной базы
- •5.1. Ионное травленне
- •5.2. Плазмохимическое травление
- •5.3. Реактивное ионное травление
- •Контрольные вопросы
- •6. Термическая диффузия
- •6.1. Процессы диффузионного легирования
- •6.2. Уравнение диффузии
- •6.2.1. Диффузия из одной полуограниченной области в другую
- •6.2.2. Факторы, влияющие на величину коэффициента диффузии
- •6.3. Моделирование процессов диффузии в твердом теле
- •6.3.1. Диффузия из одной полуограниченной области в другую
- •6.3.2. Количество примеси, введенной из источника неограниченной мощности
- •6.3.3. Диффузия из слоя конечной толщины
- •6.3.4. Диффузия из бесконечно тонкого слоя (точечный источник)
- •6.6. Формула Пуассона
- •6.7. Диффузия в прямоугольное окно
- •6.8. “Разгонка” примеси. Многостадийная диффузия
- •6.9. Диффузия примеси в гетерогенной системе
- •6.10. Диффузия в область ограниченных размеров
- •6.11. Определение зависимости D(N)
- •6.12. Результирующее примесное распределение
- •6.13. Методы диффузионного легирования
- •6.13.1 Диффузия из пленок, наносимых на поверхность полупроводника
- •6.13.2 Диффузия в ампуле
- •6.13.3 Диффузия в потоке газа-носителя
- •6.13.4 Метод параллельного источника
- •6.14. Источники диффузанта
- •6.14.2 Алюминий (Al), галлий (Ga) и индий (In)
- •6.14.3 Фосфор (P) мышьяк (As) и сурьма (Sb)
- •6.14.4 Эффект вытеснения коллекторного перехода
- •6.14.5 Другие диффузанты
- •6.15. Выбор легирующей примеси
- •Контрольные вопросы
- •7. Ионное легирование
- •7.1. Общие принципы процесса ионной имплантации
- •7.2. Пробеги и дисперсии пробегов ионов
- •7.2.1. Распределение пробегов ионов
- •7.2.2. Боковое рассеяние ионов
- •7.2.3. Ионное каналирование
- •7.3. Влияние радиационных дефектов
- •7.4. Отжиг дефектов ионно-имплантированных слоев
- •7.4.1. Примеры профилей распределения ионов
- •7.4.2. Лазерный и электронно-лучевой отжиг
- •7.5. Влияние технологических факторов
- •7.5.1. Диффузия имплантированных примесей
- •7.5.2. Технология маскирования при ионной имплантации
- •7.5.3. Гетерирование
- •7.6. Преимущества и недостатки ионного легирования
- •Контрольные вопросы
- •8. Методы создания диэлектрических слоев
- •8.1. Термическое окисление
- •8.2. Осаждение пленок диоксида кремния
- •8.3. Получение пленок нитрида кремния
- •8.4. Плазмохимическое осаждение
- •8.5. Особенности окисления некоторых материалов
- •8.6. Воспроизведение рельефа поверхности
- •Контрольные вопросы
- •9. Термическое окисление кремния
- •9.1. Методы получения пленок оксида кремния
- •9.2. Механизмы окисления кремния
- •9.3. Кислород в кремнии
- •9.4. Свойства и применения пленок оксида кремния
- •9.5. Модель процесса
- •9.6. Перераспределение примеси при окислении
- •9.7. Особенности технологии МДП структур
- •9.7.1. Влияние режимов окисления и термообработок на свойства МДП структур на основе кремния
- •9.7.2. Механизмы нестабильности МДП структур
- •9.7.3 Методы повышения стабильности МДП структур
- •Контрольные вопросы
- •10. Методы литографии
- •10.1. Электронно-лучевая литография
- •10.2. Рентгеновская литография
- •10.3. Ионно-лучевая литография
- •10.4. Сравнение и тенденция развития процессов литографии
- •Контрольные вопросы
- •11. Технология фотолитографии
- •11.1. Стандартная фотолитография
- •11.2. Процесс переноса изображения в фотолитографии
- •11.3. Фотолитография в глубоком ультрафиолете
- •11.4. Волновые эффекты при экспонировании
- •Контрольные вопросы
- •12. Физико-химические основы технологии эпитаксиальных слоев
- •12.1. Эпитаксия из газовой фазы
- •12.1.2. Реакторы установок эпитаксиального наращивания
- •12.1.3. Легирование и автолегирование эпитаксиальных слоев
- •12.1.4. Технология процесса эпитаксии кремния
- •12.2. Молекулярно-лучевая эпитаксия
- •12.3. Эпитаксия кремния на изолирующей подложке
- •12.4. Получение эпитаксиальных слоев полупроводниковых соединений
- •Контрольные вопросы
- •13. Технология многоуровневой металлизации
- •13.1. Термическое испарение в вакууме
- •13.1.1. Физические основы термического вакуумного напыления
- •13.1.2. Конденсация вещества на подложке
- •13.1.3. Оборудование процесса термического вакуумного напыления
- •13.1.4. Распределение толщины пленки по подложке
- •13.2. Методы ионно-плазменного распыления
- •13.2.1. Механизмы распыления вещества потоком ионов
- •13.2.2. Ионно-плазменное распыление на постоянном токе (катодное распыление)
- •Контрольные вопросы
- •14. Монтажно-сборочные операции
- •14.1. Разделение пластин на кристаллы
- •14.2. Присоединение кристаллов к корпусу
- •14.2.1. Присоединение кристалла к основанию корпуса
- •14.2.2. Присоединение выводов
- •14.2.3. Герметизация
- •14.3. Монтаж приборов в корпус
- •Контрольные вопросы
- •15. Контрольные операции
- •15. 1. Функциональный контроль приборов
- •15.2. Испытания и измерения
- •15.2.1. Контроль технологического процесса
- •15.2.2. Причины брака
- •15.2.3. Методы контроля толщины пленок
- •15. 3. Заключительные операции
- •15.3.1. Герметизация кристалла
- •15.3.2. Контроль герметичности
- •Контрольные вопросы
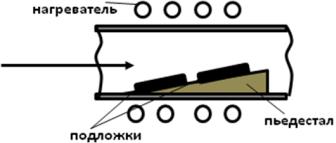
178
слоя линейно зависит от парциального давления кремнийсодержащего соединения в газе-носителе. Незначительное увеличение скорости роста с температурой в области В обусловлено увеличением коэффициента диффузии реагентов в газовой фазе с ростом температуры.
Промышленные процессы обычно проводятся при условиях, соответствующих области В для уменьшения влияния колебаний температуры на скорость роста эпитаксиального слоя.
12.1.2. Реакторы установок эпитаксиального наращивания
Реакторы установок эпитаксиального наращивания, как правило изготовляются из плавленого кварца. Конструктивно реакторы подразделяются на горизонтальные, вертикальные и цилиндрические. Горизонтальный реактор мы, по сути уже рассмотрели. Он представляет собой кварцевую трубу, внутри которой размещен подложкодержатель (пьедестал) (рисунок 12.5).
Рис. 12.5.
Нагрев подложкодержателя осуществляется либо индукционным методом (в этом случае нагреватель представляет собой высокочастотный индуктор), либо радиационным методом (нагреватель состоит из кварцевых галогенных ламп). При этом реакционная труба дополнительно охлаждается и остается относительно холодной (реакторы с «холодной стенкой). От нагретого подложкодержателя, благодаря теплопроводности, нагреваются подложки, на которых выращивается эпитаксиальный слой.
Подложкодержатель должен быть механически прочным, не загрязнять реакционный объем и не вступать в химические реакции с газами, присутствующими в реакторе. Наиболее полно этим требованиям удовлетворяют поликристаллический кремний и графит. Однако поликристаллический кремний взаимодействует с HCl, что ведет к эрозии подложкодержателя. Для предотвращения эрозии на поверхность подложкодержателя наносится нитрид кремния (SiN).
Графитовые подложкодержатели также нуждаются в защитном покрытии по двум причинам:
графит достаточно мягкий материал;
обычные марки графита содержат достаточно много примесей, которые могут загрязнять реакционный объем.
Вкачестве устойчивого покрытия графитовых подложкодержателей используют слои карбида кремния (SiC) толщиной порядка сотни микрон.
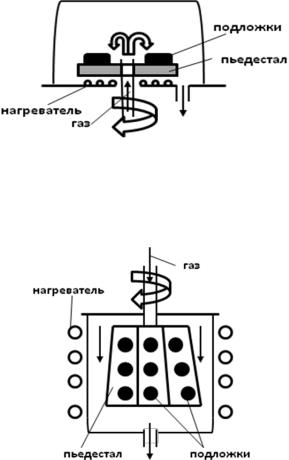
179
Горизонтальные реакторы дают возможность одновременно проводить процесс на большом количестве пластин (20 – 30), но поддержание однородности параметров эпитаксиального слоя по всей длине подложкодержателя весьма затруднено.
Конструкция вертикального реактора приведена на рисунке 12.6.
Рис. 12.6.
Вертикальные реакторы обеспечивают более высокую степень однородности эпитаксиальных слоев, но допускают наращивание эпитаксиального слоя на меньшее количество пластин.
Определенным компромиссом между двумя рассмотренными типами реакторов является цилиндрический реактор (рисунок 12.7).
Рис. 12.7.
12.1.3. Легирование и автолегирование эпитаксиальных слоев
Легирование эпитаксиальных пленок в процессе их роста осуществляется введением газообразных соединений легирующей примеси в рабочую парогазовую смесь. В случае использования в процессе эпитаксии реакций восстановления (например, тетрахлорида кремния) в качестве легирующих соединений используются BCl3, BBr3, PCl3:
BBr3 + H2 → B↓ + HBr
При пиролитическом разложении силана легирование осуществляют добавкой в газовую смесь диборана (B2H6), фосфина (PH3) или арсина (AsH3):
РН3 → Р↓ + Н2.
Следует отметить, что указанные газы весьма токсичны. Арсин, например, вызывает мгновенную смерть, если его концентрация во вдыхаемом воздухе превышает 0,025 %.
Существует тесная взаимосвязь между процессом эпитаксиального роста и процессом легирования эпитаксиального слоя. Зависимость концентрации легирующей примеси в эпитаксиальном слое от скорости его роста приведена на рисунке 12.8.
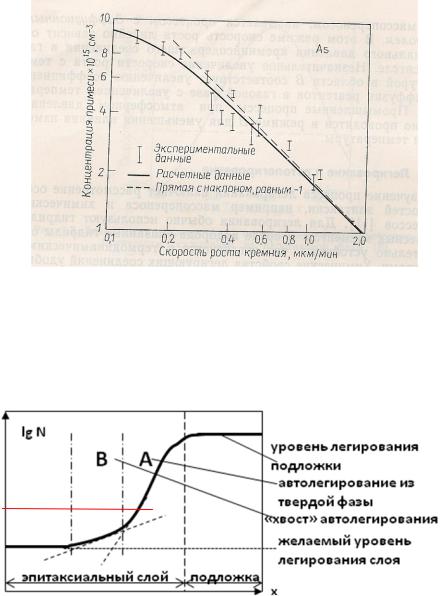
180
При низких скоростях роста между твердой и газообразной фазой устанавливается равновесие. При этом концентрация примеси в слое должна быть постоянна и максимальна. Чем больше скорость роста, тем сильнее процесс сдвинут относительно равновесия и тем меньшее количество примесных атомов встраивается в растущий слой.
Наряду с намеренно вводимыми примесями в растущий эпитаксиальный слой попадают и неконтролируемые примеси из подложки. Этот процесс называется автолегированием. Имеется два канала автолегирования:
диффузия примесей в твердой фазе через границу подложка – растущий эпитаксиальный слой;
десорбция примеси с обратной и боковой поверхностей подложки и перенос её в эпитаксиальный слой через газовую фазу.
Рис. 12.8.
Автолегирование проявляется как увеличение переходной области между эпитаксиальным слоем и подложкой. Форма профиля легирования вблизи границы раздела определяется, в основном, твердотельной диффузией из подложки (область А на рисунке 12.9).
Рис. 12.9.
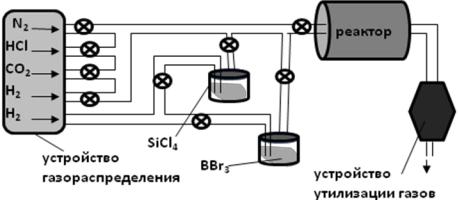
181
Так как скорость роста эпитаксиального слоя существенно превосходит скорость диффузии атомов примеси, то в области В профиль легирования определяется, в основном, переносом примеси через газовую фазу. Это так называемый «хвост» автолегирования. Если количество испаряемой с подложки примеси меньше количества примеси, вводимой в
реактор, то «хвост» автолегирования не наблюдается (красный пунктир на рисунке). Автолегирование ограничивает минимальную толщину эпитаксиальных слоев, которая может быть получена управляемым легированием при его минимальном уровне. Снижение эффекта автолегирования возможно либо понижением температуры процесса, либо использованием подложек, легированных элементами с невысоким коэффициентом диффузии (например, мышьяком вместо фосфора).
12.1.4. Технология процесса эпитаксии кремния
Схема установки для выращивания эпитаксиальных слоев кремния, легированных бором, с использованием реакции восстановления приведена на рисунке 12.10.
Рис. 12.10.
Источники кремния (SiCl4) и легирующего элемента – бора (BBr3) являются жидкостями и подаются в реактор барботажным методом. При барботировании газ-носитель (водород) пропускается чепез жидкость для насыщения её парами. Степень насыщения зависит от температуры источника. Поэтому источники размещены в термостатах, обеспечивающих поддержание температуры с точностью не хуже ± 1ºС. Поскольку расход водорода значителен, то, во избежание выброса испаряемой жидкости в сторону реактора, в источник подается лишь 2 – 5 % общего количества водорода, а в общей магистрали концентрированная смесь разбавляется основным потоком водорода.
Порядок проведения эпитаксиального процесса:
1.Продувка газом-носителем (водородом) для очистки системы от воздуха.
2.Прогрев пьедестала с подложками до рабочей температуры (1150 – 1250 ºС) и выдержка с целью восстановления окислов на поверхности пластин.