
- •1. Основные понятия
- •1.1. Современное состояние микроэлектроники
- •1.1.1. Роль электроники в мировой сфере производства и потребления
- •1.1.2. Зачем России своя электроника
- •1.2.1. Классификация интегральных микросхем
- •1.2.2. Технологические операции
- •1.2.3. Элементы микросхем
- •1.2.4. Проблемы в производстве
- •Контрольные вопросы
- •2. Материалы электронной компонентной базы
- •2.1. Классификация материалов
- •2.2. Классификация полупроводниковых материалов
- •2.2.1. Собственные и примесные полупроводники
- •2.2.3. Полупроводниковые соединения
- •Контрольные вопросы
- •3. Конструкции и технологические последовательности изготовления полупроводниковых приборов и ИС
- •3.1. Развитие технологии производства изделий электронной техники
- •3.2. Методы изоляции элементов монолитных биполярных ИС
- •3.3. Методы изоляции МДП-транзисторов
- •Контрольные вопросы
- •4. Химическая обработка и травление кремниевых пластин
- •4.1. Жидкостная очистка поверхности пластин
- •4.2. Травление
- •4.3. Пористый кремний
- •Контрольные вопросы
- •5. Плазменная обработка и травление материалов электронной компонентной базы
- •5.1. Ионное травленне
- •5.2. Плазмохимическое травление
- •5.3. Реактивное ионное травление
- •Контрольные вопросы
- •6. Термическая диффузия
- •6.1. Процессы диффузионного легирования
- •6.2. Уравнение диффузии
- •6.2.1. Диффузия из одной полуограниченной области в другую
- •6.2.2. Факторы, влияющие на величину коэффициента диффузии
- •6.3. Моделирование процессов диффузии в твердом теле
- •6.3.1. Диффузия из одной полуограниченной области в другую
- •6.3.2. Количество примеси, введенной из источника неограниченной мощности
- •6.3.3. Диффузия из слоя конечной толщины
- •6.3.4. Диффузия из бесконечно тонкого слоя (точечный источник)
- •6.6. Формула Пуассона
- •6.7. Диффузия в прямоугольное окно
- •6.8. “Разгонка” примеси. Многостадийная диффузия
- •6.9. Диффузия примеси в гетерогенной системе
- •6.10. Диффузия в область ограниченных размеров
- •6.11. Определение зависимости D(N)
- •6.12. Результирующее примесное распределение
- •6.13. Методы диффузионного легирования
- •6.13.1 Диффузия из пленок, наносимых на поверхность полупроводника
- •6.13.2 Диффузия в ампуле
- •6.13.3 Диффузия в потоке газа-носителя
- •6.13.4 Метод параллельного источника
- •6.14. Источники диффузанта
- •6.14.2 Алюминий (Al), галлий (Ga) и индий (In)
- •6.14.3 Фосфор (P) мышьяк (As) и сурьма (Sb)
- •6.14.4 Эффект вытеснения коллекторного перехода
- •6.14.5 Другие диффузанты
- •6.15. Выбор легирующей примеси
- •Контрольные вопросы
- •7. Ионное легирование
- •7.1. Общие принципы процесса ионной имплантации
- •7.2. Пробеги и дисперсии пробегов ионов
- •7.2.1. Распределение пробегов ионов
- •7.2.2. Боковое рассеяние ионов
- •7.2.3. Ионное каналирование
- •7.3. Влияние радиационных дефектов
- •7.4. Отжиг дефектов ионно-имплантированных слоев
- •7.4.1. Примеры профилей распределения ионов
- •7.4.2. Лазерный и электронно-лучевой отжиг
- •7.5. Влияние технологических факторов
- •7.5.1. Диффузия имплантированных примесей
- •7.5.2. Технология маскирования при ионной имплантации
- •7.5.3. Гетерирование
- •7.6. Преимущества и недостатки ионного легирования
- •Контрольные вопросы
- •8. Методы создания диэлектрических слоев
- •8.1. Термическое окисление
- •8.2. Осаждение пленок диоксида кремния
- •8.3. Получение пленок нитрида кремния
- •8.4. Плазмохимическое осаждение
- •8.5. Особенности окисления некоторых материалов
- •8.6. Воспроизведение рельефа поверхности
- •Контрольные вопросы
- •9. Термическое окисление кремния
- •9.1. Методы получения пленок оксида кремния
- •9.2. Механизмы окисления кремния
- •9.3. Кислород в кремнии
- •9.4. Свойства и применения пленок оксида кремния
- •9.5. Модель процесса
- •9.6. Перераспределение примеси при окислении
- •9.7. Особенности технологии МДП структур
- •9.7.1. Влияние режимов окисления и термообработок на свойства МДП структур на основе кремния
- •9.7.2. Механизмы нестабильности МДП структур
- •9.7.3 Методы повышения стабильности МДП структур
- •Контрольные вопросы
- •10. Методы литографии
- •10.1. Электронно-лучевая литография
- •10.2. Рентгеновская литография
- •10.3. Ионно-лучевая литография
- •10.4. Сравнение и тенденция развития процессов литографии
- •Контрольные вопросы
- •11. Технология фотолитографии
- •11.1. Стандартная фотолитография
- •11.2. Процесс переноса изображения в фотолитографии
- •11.3. Фотолитография в глубоком ультрафиолете
- •11.4. Волновые эффекты при экспонировании
- •Контрольные вопросы
- •12. Физико-химические основы технологии эпитаксиальных слоев
- •12.1. Эпитаксия из газовой фазы
- •12.1.2. Реакторы установок эпитаксиального наращивания
- •12.1.3. Легирование и автолегирование эпитаксиальных слоев
- •12.1.4. Технология процесса эпитаксии кремния
- •12.2. Молекулярно-лучевая эпитаксия
- •12.3. Эпитаксия кремния на изолирующей подложке
- •12.4. Получение эпитаксиальных слоев полупроводниковых соединений
- •Контрольные вопросы
- •13. Технология многоуровневой металлизации
- •13.1. Термическое испарение в вакууме
- •13.1.1. Физические основы термического вакуумного напыления
- •13.1.2. Конденсация вещества на подложке
- •13.1.3. Оборудование процесса термического вакуумного напыления
- •13.1.4. Распределение толщины пленки по подложке
- •13.2. Методы ионно-плазменного распыления
- •13.2.1. Механизмы распыления вещества потоком ионов
- •13.2.2. Ионно-плазменное распыление на постоянном токе (катодное распыление)
- •Контрольные вопросы
- •14. Монтажно-сборочные операции
- •14.1. Разделение пластин на кристаллы
- •14.2. Присоединение кристаллов к корпусу
- •14.2.1. Присоединение кристалла к основанию корпуса
- •14.2.2. Присоединение выводов
- •14.2.3. Герметизация
- •14.3. Монтаж приборов в корпус
- •Контрольные вопросы
- •15. Контрольные операции
- •15. 1. Функциональный контроль приборов
- •15.2. Испытания и измерения
- •15.2.1. Контроль технологического процесса
- •15.2.2. Причины брака
- •15.2.3. Методы контроля толщины пленок
- •15. 3. Заключительные операции
- •15.3.1. Герметизация кристалла
- •15.3.2. Контроль герметичности
- •Контрольные вопросы
128
7. Какие факторы влияют на качество воспроизведения пленкой рельефа поверхности подложки?
9. ТЕРМИЧЕСКОЕ ОКИСЛЕНИЕ КРЕМНИЯ
Окисление кремния – одни из самых характерных процессов в технологии современных ИС. Получаемая при этом пленка двуокиси кремния (Si02) выполняет несколько функций в том числе:
защиты, в частности, пассивации участков рп–переходов, выходящих на поверхность;
маски, через окна которой вводятся необходимые примеси при локальном легировании (диффузионном или ионном);
тонкого диэлектрика вод затвором МОП-транзистора;
в качестве диэлектрика межуровневой изоляции систем металлизации.
Втехнологии ИС различают «толстые» и «тонкие» окислы Si02. Толстые окислы (d= 0,7–0,8 мкм) выполняют функции защиты и маскировки, а тонкие (d = 0,1–0,2 мкм) – функции подзатворного диэлектрика в МОПтранзисторах.
Одной из важных проблем при выращивании пленки Si02 является обеспечение ее однородности. В зависимости от качества поверхности пластины, от чистоты реагентов и режима выращивания в пленке возникают те или иные дефекты. Распространенным типом дефектов являются микро-
имакропоры, вплоть до сквозных отверстий (особенно в тонком окисле). Поверхность кремния всегда покрыта «собственной» окисной пленкой,
получающейся в результате «естественного» окисления при комнатной температуре. Эта пленка имеет малую толщину (около 5 нм), чтобы выполнять какую-либо из перечисленных функций. Поэтому в технологии ИС пленки Si02 получают искусственным путем.
9.1. Методы получения пленок оксида кремния
Искусственное окисление кремния осуществляется обычно в окислительных печах, подобных тем, которые используются для диффузии в потоке газа-носителя при высокой температуре (1000–1200 °С). Основу таких печей составляет, как и при диффузии, кварцевая труба с пластинами кремния, нагреваемая либо токами высокой частоты, либо иным путем. Через трубу пропускается поток кислорода (сухого или увлажненного) или пары воды, которые реагируют с кремнием в высокотемпературной зоне. Окисляющим агентом обычно является кислород или пары воды при давлении, равном атмосферному:
Si + О2 → Si02
Si + H2О → Si02+ 2 H2
129
Энергия активации химической реакции Ea близка к 2.2 эВ, величине
соответствующей энергии разрыва связи Si – Si.
Используются также их смеси, или различного состава смеси кислорода с азотом.
Термическое окисление можно проводить в атмосфере кислорода (сухое окисление), в смеси кислорода с парами воды (влажное окисление) или в парах воды. Получающийся оксид по свойствам близок к плавленому кварцу, имеет аморфную структуру и практически однороден по толщине.
Коэффициент диффузии О2 несколько выше, чем коэффициент диффузии паров воды, однако, по крайней мере, при атмосферном давлении растворимость паров воды в SiO2приблизительно на три порядка величины больше, чем растворимость О2. Поэтому окисление в парах воды идет в десятки раз быстрее, чем в кислороде. Например, для выращивания пленки Si02 толщиной 0,5 мкм в сухом кислороде при 1000° С требуется около 5 ч, а во влажном – всего 20 мин. С уменьшением температуры на каждые 100° С время окисления возрастает в 2–3 раза.
Энергия активации Ea диффузионных процессов этих окислителей также различна, EaO2 1.25 эВ и приблизительно Ea 0.8 эВ для паров воды.
Пары воды скорее всего диффундируют в виде молекул.
Качество окисной пленки повышается с уменьшением температуры при выращивании, а также при использовании сухого кислорода. Поэтому тонкий подзатворяый окисел, от качества которого зависит стабильность параметров МОП-транзистора, получают сухим окислением. При выращивании толстого окисла чередуют сухое и влажное окисление: первое обеспечивает отсутствие дефектов, а второе позволяет сократить время процесса.
В последние годы начали все шире использоваться методы термического окисления при умеренно повышенных давлениях (приблизительно до 6–10 атм) и температурах, типичных для обычного термического окисления. Этот метод позволяет в несколько раз увеличить скорость окисления при сохранении других качеств пленок, которые получаются при атмосферном давлении.
Ограниченное распространение получил и метод анодирования. Этот метод позволяет получать пленки оксида кремния толщиной до 200–300 нм при комнатной температуре и прецизионно воспроизводить их толщину. Очень высокие значения поверхностного заряда на границе раздела SiO2 – Si (см. ниже) ограничивают применение этого метода. Практически он используется лишь для послойного стравливания кремния при исследованиях профилей распределения примесей и в других аналогичных случаях.
Необходимо отметить и некоторые особенности окисления кремния при пониженных давлениях окислителя. В этом случае могут формироваться пленки моноокиси (SiO). Этот оксид при температурах выше 1200–1250оС испаряется заметно легче, чем кремний или его диоксид. В результате может наблюдаться не окисление, а травление кремния.
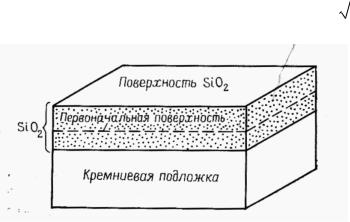
130
9.2. Механизмы окисления кремния
Установлено, что чистая поверхность Si в O2 начинает окисляться очень быстро, и пленка SiO2 толщиной порядка нескольких нм успевает образоваться за единицы секунд.
Механизм окисления имеет два варианта. Первый состоит из следующих этапов: 1) диффузия атомов кремния через уже имеющуюся пленку окисла к поверхности, 2) адсорбция молекул кислорода поверхностью из газовой фазы, 3) собственно окисление, т. е. химическая реакция. В этом случае пленка нарастает над исходной поверхностью кремния. Второй вариант состоит из следующих этапов: 1) адсорбция кислорода поверхностью уже имеющегося окисла,2) диффузия кислорода через окисел к еще не окисленному кремнию, 3) собственно окисление. В этом случае пленка нарастает вглубь от исходной поверхности кремния. На практике оба механизма сочетаются, но главную роль обычно играет второй.
Экспериментально установлено, что окислитель диффундирует в оксиде гораздо быстрее, чем Si, и поэтому рост оксида идет преимущественно на границе раздела Si–SiO2.
При протекании процесса окисления граница раздела Si–SiO2 двигается в глубь кремниевой подложки однако происходящее при этом расширение объема приводит к тому, что внешняя поверхность пленки SiO2 не совпадет с первоначальной поверхностью кремния. Если обратиться к значениям плотности и молекулярному весу Si и SiO2 можно показать, что рост окисной пленки толщиной d происходит за счет слоя кремния толщиной 0,44 d (рис.
9.1).
Очевидно, что скорость роста окисла со временем должна убывать, так как новым атомам кислорода приходится диффундировать через все более толстый слой окисла. Полуэмпирическая формула, связывающая толщину окисной пленки со временем термического окисления, имеет вид;
|
|
|
d k t |
(9.1) |
где k – параметр, зависящий от температуры и влажности кислорода.
Рис. 9.1. Рост Si02
Естественно, что абсолютная величина константы равновесия химической реакции, зависит от ориентации пластин кремния, медленнее других окисляется плоскость (100), а наиболее быстро – плоскость (111).
Легированный кремний также окисляется несколько быстрее нелегированного.

131
9.3. Кислород в кремнии
Кислород относится к числу примесей, быстро диффундирующих в кремнии. Его предельная растворимость несколько превышает 1017 см–3 при температуре, близкой к температуре плавления кремния и быстро уменьшается при понижении температуры. Например, при 900оС (температуре “загонки”) растворимость кислорода падает приблизительно до 1015 см–3. В растворенном состоянии кислород электрически не активен.
Связь O2–Si представляет собой ковалентную связь.
В оксиде кремния кислород занимает положение мостика между двумя атомами кремния, которые приблизительно сохраняют свою тетраэдрическую координацию по отношению друг к другу. Эти тетраэдры относительно легко деформируются, благодаря чему у SiO2 при разных температурах стабильными являются несколько кристаллографических форм. Фазовые переходы между этими формами идут достаточно медленно, так что вполне устойчивой является и аморфная модификация – плавленый кварц, структуре которого и соответствуют получаемые на кремнии пленки термически выращенного оксида.
При температуре 500…600оС кислород химически связывается с кремнием, причем вначале образуется комплекс, обладающий донорными свойствами. При дальнейшем повышении температуры каждый атом кислорода как бы встраивается между двумя атомами кремния, образуется Si–O–Si связь. В таком состоянии О2 также электрически не активен.
9.4. Свойства и применения пленок оксида кремния
Оксид кремния относится к числу наиболее высококачественных диэлектриков. Он имеет диэлектрическую проницаемость 3.9, n 1.46,
ïð 2 .107 В/см (в слоях d 200 нм). У более толстых слоев ïð уменьшается пропрорционально d 0.25 .
Роль, которую выполняет пленка SiO2 определяет возможность использования того или иного метода ее получения.
Для использования в качестве межуровневой изоляции или защитного слоя, наносимого поверх металлизации можно использовать химическое осаждение из газовой фазы. Защитные слои часто наносятся также пиролизом ТЭОС.
Слои, используемые в качестве масок при локальном легировании, обычно получают термическим окислением. На практике нередко используется комбинированный режим окисления, когда начальный этап окисления ведется в атмосфере сухого O2, затем в атмосфере паров воды, после чего опять следует окисление в сухом O2. Длительности этих трех процессов выбираются приблизительно равными. Первый этап окисления задает структуру границы раздела Si–SiO2. Во время второго этапа формируется основная толща пленки. Третий этап является термообработкой, в процессе которой понижается концентрация растворенной в пленке воды, толщина пленки при этом увеличивается