
- •МАТЕРИАЛОВЕДЕНИЕ
- •1.1. Металлы, их классификация и основные физические свойства
- •1.3. Реальное строение металлов и дефекты кристаллических решеток
- •1.4. Строение сплавов
- •2.1. Энергетические и температурные условия процесса кристаллизации
- •2.3. Превращения в твердом состоянии. Полиморфизм
- •3. МЕХАНИЧЕСКИЕ СВОЙСТВА МАТЕРИАЛОВ
- •3.2. Деформации и напряжения
- •4. ДИАГРАММЫ СОСТОЯНИЯ СПЛАВОВ
- •4.1. Правило фаз, построение диаграмм состояния
- •4.4. Диаграмма состояния для сплавов с ограниченной растворимостью в твердом состоянии, с эвтектикой
- •4.6. Диаграмма состояния для сплавов, образующих химические соединения
- •4.7. Диаграмма состояния для сплавов с полиморфным превращением одного из компонентов
- •4.8. Диаграмма состояния сплавов с полиморфными превращениями компонентов и эвтектоидным превращением
- •6. ЖЕЛЕЗОУГЛЕРОДИСТЫЕ СПЛАВЫ
- •7.1. Влияние нагрева и скорости охлаждения углеродистой стали на ее структуру
- •7.2. Отжиг углеродистых сталей
- •8.1. Закалка углеродистых сталей
- •Обработке холодом подвергают быстрорежущие стали, цементованные детали, измерительные инструменты, подшипники и другие особо точные изделия.
- •8.2. Отпуск закаленных углеродистых сплавов
- •9.1. Назначение легирования
- •9.2. Влияние легирующих элементов на структуру и механические свойства сталей
- •9.3. Влияние легирования на превращения при термообработке
- •10.1. Упрочнение легированием
- •10.2. Упрочнение пластическим деформированием
- •10.4. Цементация стали
- •10.5. Азотирование стали
- •10.6. Нитроцементация
- •11. КОНСТРУКЦИОННЫЕ СТАЛИ
- •12.3. Жаропрочные стали и сплавы
- •12.4. Жаростойкие стали и сплавы
- •13.1. Условия работы деформирующих и режущих инструментов, требования к инструментальным материалам
- •13.2. Инструментальные легированные (штамповые) стали
- •13.3. Классификация режущих инструментальных материалов
- •14. ТВЕРДЫЕ СПЛАВЫ
- •14.1. Классификация твердых сплавов и общая характеристика их свойств
- •14.2. Режущая керамика
- •14.3. Сверхтвердые инструментальные материалы
ется вследствие упрочнения твердых растворов и выделения карбидов по зерну и границам зерен.
Легирующими элементами являются: никель (10–30%), хром (в деформируемых сплавах – 18–20%, в литых – 23–28%), вольфрам (до 10%),
бор (до 1%), углерод (0,3–04 %), а также Nb, Ti, V.
Термическая обработка кобальтовых сплавов представляет собой рекристаллизационный отжиг, отжиг для снятия напряжений у деформируемых сплавов или отжиг у литых сплавов.
Сравнительные характеристики прочности жаропрочных сталей и сплавов на основе никеля и кобальта приведены на рисунке 12.4.
12.4. Жаростойкие стали и сплавы
Жаростойкость – способность металла сопротивляться окислению в газовой среде или в других окислительных средах при повышенных температурах. Жаропрочные сплавы в принципе должны быть и жаростойкими, иначе они быстро выходят из строя из-за быстрого окисления. Однако жаростойкие сплавы не всегда бывают жаропрочными.
К жаростойким относятся стали и сплавы, работающие в ненагруженном или слабонагруженном состоянии при температурах выше550 ºС и обладающие стойкостью против химического разрушения поверхности в газовых средах.
Повышение жаростойкости сплавов заключается в легировании - до бавками, которые, не снижая показателей жаропрочности и других свойств, снижают скорость окисления сплавов за счет образования на их поверхности плотной защитной пленки окислов, хорошо связанных с основой. Диффузия (особенно кислорода) через оксидные пленки затруднена, что приводит к торможению процесса дальнейшего окисления.
Жаростойкость стали достигается введением хрома, никеля, алюминия или кремния, образующих в процессе нагрева защитные пленки оксидов (Cr,Fe)2O3, (Al,Fe)2О3. Введение в сталь 5–8 % хрома повышает жаростой-
кость до 700–750 °С, до 17% – до 1000 °С, 25% – до 1100 °С. Дополнитель-
ное легирование к 25% хрома 5% алюминия повышает жаростойкость до
1300 °С.
Жаростойкие стали и сплавы разделены на следующие группы:
·хромистые и хромоалюминиевые стали ферритного класса;
·хромокремнистые мартенситного класса;
·хромоникелевые аустенитные стали;
·сплавы на хромоникелевой основе.
Кгруппе ферритных хромистых и хромоалюминиевых сталей отнесены высокохромистые стали на основе13–28% Сг, которые при достаточно низком содержании углерода или легирования их ферритообразующими -эле
150
ментами имеют однофазную ферритную структуру. Эти стали применяют для изготовления теплообменников, деталей аппаратуры химических производств, печного оборудования и других изделий, которые не испытывают значительных нагрузок и работают при высоких температурах длительное время (08Х17Т, 15Х25Т, 15Х28, 1Х13Ю4). Чем выше содержание хрома, алюминия и кремния в сталях, тем больше температуры, при которых они сохраняют требуемые эксплуатационные свойства.
Стали ферритного класса обладают невысокой прочностью и -жаро прочностью, высокой пластичностью и удовлетворительными технологическими свойствами.
Изделия из хромоалюминиевых сталей(содержание Аl от 3,5 до 5,8 %) устойчивы в атмосфере воздуха, в среде сернистых газов, но резко теряют работоспособность в восстановительных средах, содержащих окись углерода, пары воды, а также в хлорсодержащих средах. При длительной работе в азотсодержащих средах образуются нитриды алюминия, которые устойчивы до высоких температур и не оказывают вредного влияния на свойства сталей.
Хромистые и хромоалюминиевые стали имеют крупный недостаток: они могут охрупчиваться в процессах технологических нагревов и -дли тельных выдержек при повышенных температурах во время эксплуатации.
Жаростойкие стали, имеющие повышенное содержание углерода(до 0,5–0,8%) и легированные совместно хромом(6–14%) и кремнием (1–3%) (15Х6СЮ, 40Х10С2М), называются сильхромами. Они обладают хорошим сопротивлением газовой коррозии в продуктах сгорания различных видов топлива и высокой износостойкостью при трении и ударных нагрузках. Термическая обработка сильхромов состоит чаще всего из закалки на мартенсит и высокого отпуска или, реже, из нормализации.
Основное назначение сталей этой группы– клапаны автомобильных, тракторных и авиационных двигателей средней мощности. Кроме того, сильхромы используют в качестве жаростойких сплавов для изготовления регуляторов, теплообменников и колосниковых решеток в котельном и химическом машиностроении.
Жаропрочные свойства сильхромов до600 °С достаточно высоки, а при более высоких температурах резко снижаются.
В качестве жаростойких сталей аустенитного класса применяются, главным образом, стали на хромоникелевой основе. Эти стали не имеют больших преимуществ по жаростойкости перед высокохромистыми сталями ферритного класса, но выгодно отличаются от них по уровню механических свойств, в том числе жаропрочных, технологичности (способности к глубокой вытяжке, штамповке, свариваемости). Они также менее склонны к охрупчиванию после длительных выдержек при высоких температурах.
151
Недостатком сталей этого класса является их сравнительно высокая стоимость, использование в больших количествах дефицитного никеля, низкие теплопроводность и сопротивление газовой коррозии в средах.
Аустенитные стали (08X18Н9Т, 12Х18Н9, 12Х18Н9Т, 20Х25Н20С2) используют в качестве жаростойкого материала для выхлопных систем, труб, листовых и сортовых деталей при температурах600–800 °С и невысоких нагрузках. Повышение жаростойкости аустенитных сталей достигается увеличением содержания в стали хрома, никеля, а также дополнительным легированием кремнием. В качестве жаростойких материалов для работы в науглероживающих средах до1100 °С (например, печные контейнеры и арматура) используют стали с повышенным содержанием углерода (сталь 36Х18Н25С2).
Термическая обработка аустенитных жаростойких сталей заключается обычно в закалке от температур 1000–1050 °С.
Жаростойкие сплавы на никельхромовой основе(нихромы) получили значительное распространение в качестве материалов для работы при 800—1100 °С, а при кратковременной работе– до 1200 °С. Эти сплавы применяют для изготовления деталей газовых турбин, не испытывающих больших рабочих нагрузок и работающих при высоких температурах(камеры сгорания, жаровые трубы, нагревательные элементы электрических печей и другие детали).
Сплавы представляют собой в основном твердый раствор хрома (15–27%) в никеле с решеткой ГЦК, слабо упрочняются при термической обработке, имеют высокую пластичность, высокое электросопротивление и хорошие технологические свойства. В качестве элементов, дополнительно повышающих жаростойкость нихромов, применяется алюминий (до 3,5%), титан, молибден, ниобий в небольших количествах, а также вольфрам.
152
13. ИНСТРУМЕНТАЛЬНЫЕ МАТЕРИАЛЫ ДЛЯ ОБРАБОТКИ МЕТАЛЛОВ ДАВЛЕНИЕМ И РЕЗАНИЕМ
13.1. Условия работы деформирующих и режущих инструментов, требования к инструментальным материалам
Условия работы деформирующих инструментов(штампов) различаются, прежде всего, тем, нагреваются ли предварительно заготовки или они деформируются в холодном состоянии.
Штамповые инструменты для горячего деформирования по условиям работы можно разделить на три группы: инструменты для прессов, для штамповочных молотов и для высокоскоростного деформирования на скоростных молотах и гидровинтовых прессах. Время деформирования заготовок для всех способов горячей обработки давлением относительно невелико, но для различных способов может существенно отличаться.
Прессовые инструменты работают в условиях наиболее медленного деформирования. Время деформирования при работе на прессах находится в пределах от 0,1 до 0,4 с. Чем длительнее контакт с заготовкой, тем значительнее нагрев штампа.
Инструменты для молотовых штампов работают в условиях ударного нагружения. Время деформирования при штамповке на молотах на порядок меньше, чем при прессовании, и находится в пределах 0,012–0,014 с. При этом плотность теплового потока в инструмент возрастает, но за меньшее время в него поступает меньшее количество тепла. Следовательно, поверхностные слои молотовых штампов нагреваются менее прессовых.
При высокоскоростной штамповке на молотах и гидровинтовых прессах время деформирования еще меньше (0,001–0,006 с). Соответственно, в штамп в этом случае поступает еще меньше тепла, а плотность теплового потока еще выше.
В связи с высокой температурой нагрева деформируемых заготовок на поверхностях штампов возникают достаточно высокие температуры. Из-за кратковременности контакта штампа с заготовкой толщина прогреваемых до высокой температуры (500–550 °С) слоев штампа невелика (около 0,6– –1,0 мм), причем распределяется температура по этой толщине– неравномерно. При штамповке жаропрочных труднодеформируемых материалов температура поверхностных слоев штампа может достигать650–750 °С. Наиболее нагретыми оказываются поверхностные слои, основная масса штампа прогревается до меньших температур и более равномерно. После завершения кратковременного периода деформирования неравномерно распределенная температура поверхностных слоев штампа выравнивается и приближается к более низкой средней температуре штампа, обычно находящейся в пределах 300–400 °С.
153
Всвязи с характером работы кузнечно-прессового оборудования температура контактных поверхностей штампов циклически изменяется. Колебания температуры вызывают в материале штампа термические напряжения. С течением времени на рабочих поверхностях штампа могут возникать и развиваться термические трещины, являющиеся причиной искажения профиля или разрушения ручьев штампа.
Удельные давления на инструмент зависят от механических свойств материала деформируемой заготовки. При горячем деформировании они обычно находятся в пределах от 300 до 900 МПа. С увеличением температуры предварительного подогрева заготовки удельные давления снижаются, а с увеличением скорости деформирования – возрастают.
Таким образом, для операций горячего деформирования штамповые стали должны:
·обладать удовлетворительной пластической прочностью после термической обработки на твердость HRC 45–50;
·сохранять высокие значения предела текучести и твердости при повышенных температурах;
·обеспечивать длительную эксплуатацию инструментов при высоких контактных температурах 600–700 °С, устойчиво сопротивляться отпуску;
·сопротивляться износу и возникновению трещин вследствие термической усталости.
Условия работы штамповых инструментов для холодного деформирования существенно отличаются от условий, характерных для горячего деформирования. Эти отличия связаны с более высокими механическими характеристиками деформируемых заготовок, вызывающими и более высокие удельные давления, а также с низкой начальной температурой заготовки. Удельные давления при холодном прессовании достигают 2000–2500 МПа.
Температурные условия работы инструментов для холодного деформирования могут изменяться в широком диапазоне. В наибольшей степени разогреваются инструменты для холодной объемной штамповки(например, при прессовании, высадке), а также на некоторых операциях пробивки, вырубки.
Например, при холодном прессовании температура пуансона увеличивается с ростом скорости деформирования и в среднем возрастает с течением времени, постепенно приближаясь к некоторому стационарному значению (рис. 13.1).
Вкаждом цикле(т. е. при штамповке одной заготовки) в начальный момент соприкосновения с холодной заготовкой температура пуансона снижается, а затем под влиянием выделяющейся теплоты от деформации и трения снова возрастает. С ростом скорости деформирования и толщины
разрубаемого материала температура увеличивается, иногда до 450–550 °С.
154
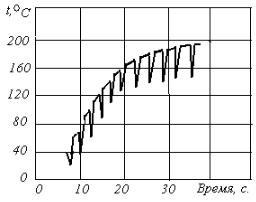
Рис. 13.1. Изменение температуры пуансона при холодном прессовании
Таким образом, штамповые стали для холодного деформирования должны обладать:
·теплостойкостью не ниже 400–450 °С;
·способностью противостоять воздействию удельных давлений до 2000–2200 МПа в течение длительного времени;
·высокой износостойкостью (в частности, для вырубных штампов). Штамповые стали для горячего и холодного деформирования должны
также обладать удовлетворительными технологическими свойствами: шлифуемостью, обрабатываемостью резанием, хорошей прокаливаемостью, малой деформируемостью при термической обработке.
Режущие инструменты работают при очень напряженных термомеханических нагрузках, их поверхности находятся в контакте с чистыми, только что образовавшимися поверхностями стружки и детали. Зачастую контакт инструмента со стружкой и обрабатываемой деталью осуществляется в течение достаточно длительного периода, поэтому режущее лезвие инструмента в окрестности режущей кромки и участков контакта инструмента со стружкой и обрабатываемой деталью прогревается достаточно равномерно до высоких температур.
Из-за очень больших скоростей деформации в процессе резания прочностные характеристики и твердость стружки существенно возрастают в сравнении с исходными свойствами обрабатываемого материала, измеренными в статических условиях нагружения. Прочность и твердость инструментального материала под влиянием температуры резко уменьшаются. При резании, например, чистое железо, мягкое в условиях статического нагружения, способно вызвать напряжения, достаточные для деформации и срезания быстрорежущей стали, имеющей в аналогичных условиях нагружения значительно более высокие механические характеристики. В связи с этим к режущим инструментальным материалам предъявляется целый ряд повышенных требований.
Для того, чтобы иметь возможность резать обрабатываемый материал и противостоять абразивному изнашиванию, режущий инструментальный
155