
stroitelnye_materialy
.pdf
1.Генетическая классификация горных пород. Влияние условий образования на структуру и свойства горных пород.
Горные породы представляют собой скопления одного или нескольких минералов. Минералом называют тело, однородное по химическому составу и физическим свойствам, возникшее в результате физико-химических процессов, протекающих в земной коре. Группы минералов:1.Группа кремнезема (кварц, опал, халцедон). 2.Группа железомагнезиальных (пироксены, амфиболы, роговая обманка). 3.Группа карбонатов (кальцит, доломит, магнезит). 4.Группа сульфатов (гипс, ангидрит). 5.Группа глинистых минералов (каолинит, гидрослюды, монтмориллонит). 6.Группа алюмосиликатов ( слюда, полевые шпаты). Группы горных пород по происхождению Изверженные, или магматические1. Массивные: а) глубинные — гранит, сиенит, диорит,
габбро: б) излившиеся — порфиры, базальт, диабаз, трахит, андезит 2. Обломочные: а) рыхлые — вулканический пепел, вулканический песок, пемзы; б) цементированные —вулканические туфы, трассы. Осадочные (седиментарные) 1.Химические: известняк, доломит, магнезит, гипс, ангидрит 2. Обломочные: а) рыхлые — гравий, природный щебень, песок, глина; б) цементированные -песчаник, конгломерат, брекчия 3.Органогенные: плотный известняк, известняк-ракушечник, диатомит, трепел 3.Видоизмененные, или метаморфические1.Изверженные (гнейс) 2.Осадочные (сланцы, мрамор, кварцит). Свойства горных пород зависят от степени кристаллизации, размеров зерен, взаимного расположения составных частей породы, от плотности породы, которые определяются условиями образования. Магматические породы образовались в процессе кристаллизации сложного природного расплава-магмы. Осадочные возникли в поверхностных условиях из продуктов разрушения любых других горных пород. Метаморфические являются продуктом
перекристаллизации и приспособления пород к изменившимся в пределах земной коры физико-химическим условиям. По плотности: тяжелые — более 1800 кг/м3; легкие — менее 1800 кг/м3. По пределу прочности при сжатии (МПа) на марки: для тяжелых — от 10 до 100; для легких — от 0,4 до 20. По морозостойкости на марки: F15-500 (тяжелые) F10-25 (легкие). По степени обработки различают: грубообработанные (бутовый камень, щебень, гравий, песок); профилированные (пиленые штучные камни и блоки для стен; камни, плиты и профильные изделия для облицовки зданий и сооружений).
2.Магматические горные породы: механизмы образования, особенности строения, минеральный состав, свойства, применение в строительстве.
Главной составляющей изверженых пород является кремнезем (SiO2). Образование магматических пород связано
спроблемами происхождения земли и строения Земли. Магматические горные породы в зависимости от условий происхождения делятся на Массивные: 1.Глубинные – это породы, образовавшиеся при застывании магмы на разной глубине в земной коре (гранит, сиенит, габбро, диорит). 2.Излившиеся породы образовались при излиянии магмы из глубин и затвердении на поверхности (порфиры, трахит, андезит, диабаз, базальт). Обломочные породы образовались при быстром охлаждении лавы: 1.рыхлые (вулканический пепел, вулканический песок, пемза) 2.цементированные (вулканические туфы). Глубинные горные породы образуются при медленном
остывании магмы в глубинных породах, следствием является ряд общих свойств: малая пористость, большая плотность (2600-3000 кг/м3), высокая прочность (при сжатии 100-300 МПа), низкое водопоглощение (меньше 1% по объему), морозостойкость. Обработка таких пород из-за высокой прочности затруднительна, но благодаря высокой плотности хорошо полируются и шлифуются. Граниты обладают благоприятным для строительного камня минеральным составом, отличающимся высоким содержанием кварца( 25-30 %), натриевокалиевых шпатов(35-40%) и плагиоклоза (25-30%). Прочность при сжатии (120-250 МПа), малая пористость (меньше 1,5%). Благодаря высокой кислотостойкости, граниты применяют в качестве кислотоупорной облицовки. Из всех изверженных пород граниты наиболее широко используют в строительстве, так как они являются самыми распространенными. Излившиеся горные породы : Порфиры по своему минеральному составу близки к гранитам, а также сходны по прочности, пористости, водопоглощению. Трахиты по своему минеральному составу схожи с сиенитами, но более пористы, предел прочности при сжатии (60-70 МПа), легко обрабатываются,
но не полируются. Андезиты желтовато-серого цвета, содержит плагиоклазы, роговую обманку, пористая структура, плотность (2700-3100 кг/м3), предел прочности при сжатии (140-250 МПа). Диабазы – порода мелкозернистая, имеют черный цвет, отличаются высокой твердостью, прочностью(300-400 МПа) и вязкостью.
Обломочные горные породы: Пемза представляет собой пористое вулканическое стекло, цвет белый или серый, пористость до 60%, Твердость около 6, истинная плотность 300-900 кг/м3. Вулканический пепел – мелкие
частицы лавы размером до 2мм, является активной минеральной добавкой. Вулканические туфы – горные породы, образовавшиеся из твердых продуктов вулканических извержений, истинная плотность 2600 кг/м3, пористость 40-70%, малая теплопроводность, прочность от5 до 15 МПа.
3.Породообразующие минералы магматических горных пород: химический состав, свойства.
Основными породообразующими минералами магматических горных пород являются: кварц и его разновидности; полевые шпаты; железисто-магнезиальные силикаты. Кварц состоит из кремнезема(диоксида кремния SiO2) – обычно прозрачен, белого молочного цвета, блеск жирный, спайность отсутствует, излом
1
раковистый, твердость 7, плотность 2,6 г/см3. Выветривается слабо, прочность при сжатии 2000 МПа, химически устойчив, t пл. = 1723 град. Полевые шпаты- распространенные минералы в магматических породах. Главными разновидностями полевых шпатов являются ортоклаз и плагиоклаз. Ортоклазы K2O*Al2O3*6SiO2 – прямораскалывающийся, твердость: 6-6,5; плотность: 2,57 г/см3 плавится при 1170 0 С. Плагиоклазы: -косо- раскалывающиеся например: альбит Na2O*Al2O3*6SiO2. У полевых шпатов плотность 2,5 – 2,7, температура плавления = 1200-1600 град, предел прочности при сжатии = 120-170 МПа, при выветривании из полевых шпатов получается группа алюмосиликатов (глина). Группа алюмосиликатов (слюда, полевые шпаты): Слюды - минералы с совершенной спайностью в одном направлении, способны расщепляться на тончайшие упругие пластинки. По химическому составу они представляют собой водные алюмосиликаты сложного состава. Наиболее часто в составе горных пород присутствуют две разновидности слюды — мусковит (светлая алюминиевая слюда) и биотит (железисто-магнезиальная слюда темного цвета). Плотность слюд 2760-3200 кг/м3, твердость 2...3, стойкость биотита меньше, чем мусковита. Присутствие слюд в горных породах понижает прочность и стойкость породы, затрудняет ее шлифовку и полировку. Группа железомагнезиальных (пироксены, амфиболы, роговая обманка): Амфиболы группа минералов подкласса ленточных силикатов. Общая формула: R7[Si4O11]2(OH)2, где R= Ca, Mg, Fe. Амфиболы имеют вытянутый облик кристаллов, совершенную спайность. Роговая обманка - Ca2(Mg,Fe,Al)5(Al,Si)8O22(OH)2 сложный алюмосиликат кальция, цвет чёрный или тёмно-зелёный, имеет плотность 3000...3400 кг/м3, твердость 5-6. 3. Это темноокрашенные минералы силикаты магния, железа, кальция. Группы: пироксены, амфиболы, роговая обманка, прочность при сжатии 300-400, высокая стойкость к выветриванию.
4. Осадочные горные породы: условия образования, минеральный состав, свойства, применение в строительстве.
Осадочные ГП образуются в результате естественного процесса разрушения первичных (магматических) горных пород под влиянием различных факторов, действующих в природе: механическое, химическое влияние внешней среды; выветривание – деятельность воды, ветра, микроорганизмов, замораживания и оттаивания. Осадочные породы в зависимости от условий их образования делятся на: химические (известковые туфы, гипс, органогенные породы: мел, известняк, диатомит) , сцементированные (песчаники, конгломераты), обломочные (гравий, глины, пески). 1.Пески 0,14-0,5 мм. По мин. составу: кварцевые, полевошпатные, известковые, туфовые. По условиям залегания: морские, горные, речные, овражные. Применение: стекольная, фарфоровая промышленность, производство стекла, силикатного кирпича, заполнитель бетонов и растворов. 2.Гравий и щебень: 5-70 мм, природный и искусственный, получают из гранита, сиенита, применяют: заполнитель бетонов, посыпка дорожки. 3.Валуны – крупные обломки ледникового происхождения, размер100-1000мм прим: получение булыжного камня и щебня. 4.Доломит – плотный известняк. Применение: производство огнеупоров. Органогенные – в результате отложения и цементирования продуктов жизнедеятельности и останков животных и растений. Мел – раковины; побелки, приготовления шпаклевок, замазок, вяжущих в-в; производство стекла. 4.Ракушечник-раковины + природный цемент. Плотность=0,6-1,5 г/см3 . Повышенная пористость, водопоглощение, воздухопроницаемость. Прим: устройство стен, но требуется оштукатуривание, фундаменты, цоколи зданий. 5.Диатомит – из морских водорослей белого цвета, реже серый, желтоватый. ρ0=0,3-1 г/см3 П=70-80% λ=0,17-0,23 6.Трепел – изоляционный материал, активная минеральная добавка.
5.Породообразующие минералы осадочных горных пород: химический состав, свойства.
Группа кремнезема. Наиболее распространенные минералы этой группы - кварц, опал, халцедон. Кварц — диоксид кремния (SiO2) в кристаллической форме. Плотность - около 2650 кг/м3, Твердость - 7, Прочность при сжатии - до 2000 МПа. Кварц имеет различную окраску (бесцветную, желтую, молочную) и стеклянный блеск. При обычной температуре кварц не взаимодействует с кислотами и щелочами. Плавится кварц при 1710°С и при быстром охлаждении расплава дает кварцевое стекло. Опал (SiO2-nH2O) содержание воды от 2 до 14%, менее плотен (1900 –2500 кг/м3), чем кварц. Обладает повышенной внутренней микропористостью и высокодисперсной структурой, твердость 5-6, хрупкий, цвет зависит от наличия примесей. Халцедон (SiO2) является волокнистой разновидностью кварца. Цвет белый, серый, бурый, зеленый, плотность 2600кг/м3, твердость 6. Группа карбонатов (кальцит, доломит, магнезит): Кальцит (СаСО3) имеет плотность 2700 кг/м3, твердость 3. Кальцит растворяется в кислотах, в обычной воде - мало. Это распространенный минерал, слагающий различные виды известняков. Окраска белая, серая, иногда он прозрачен. Магнезит (MgCO3) имеет плотность 2900-3100 кг/м3, твердость 3,5-4,5. Он распространен меньше кальцита и образует породу того же названия, бесцветный, белый или серый, имеет высокую огнеупорность и вяжущие свойства. Доломит (CaCO3-MgCO3) по физическим свойствам близок к кальциту, но более тверд - 3,5...4, плотность 2900 кг/м3. Цвет доломита от белого до темносерого. Группа глинистых минералов (каолинит, гидрослюды, монтмориллонит). Глинистые минералы играют важную роль в составе осадочных пород. Они слагают глины, и могут находиться в качестве примеси, изменяя физико-химические свойства. Каолинит (Аl2О3*2SiO2*2H2О) — водный силикат алюминия, образуется при выветривании полевых шпатов и слюд. Цвет каолинита без примесей — белый, плотность – 2600 кг/м3, твердость -1. Каолинит и другие водные алюмосиликаты являются основными в глинах, они часто встречаются в
2
виде примесей в известняках, песчаниках, гипсовых и других осадочных породах. Наличие этих примесей понижает водо- и морозостойкость пород. Гидрослюды образуются при разложении слюд и других силикатов, используют в строительстве как пористые заполнители. Монтмориллонит образуется в условиях щелочной среды и выветривании, слагает различные виды глин, служит цементирующим материалом в песчаниках. Примеси глинистых минералов резко понижает водостойкость и морозостойкость. Группа сульфатов (гипс, ангидрит): Гипс (CaSO4-2H2O) — минерал кристаллического строения, его кристаллы имеют зернистое, пластинчатое, игольчатое, волокнистое строение. Он белого цвета. Плотность гипса 2300 кг/м3, твердость 2, сравнительно легко растворяется в воде, используют в производстве вяжущих веществ. Ангидрит (CaSO4) - безводная разновидность гипса. Плотность ангидрита 2900-3000 кг/м3, твердость З...3,5. Иногда применяют как облицовочный материал для внутренних отделок зданий.
6.Метаморфические горные породы: условия образования, особенности строения, минеральный состав, свойства, применение в строительстве.
Видоизмененные ГП – образовались превращением горных пород в земной коре под действием высоких температур, давления и подвижки земной коры. Главные породообразующие минералы: полевые шпаты, кварц, слюда, роговая обманка, кальцит, доломит. Основные разновидности метаморфических горных пород: 1.Гнейс – состав как у гранита (кварц 20%, ортоклаз 40-70%, слюда 5-15%) Структура – зернисто-кристаллическая. Сланцеватость понижает прочность и морозостойкость. Прим: бутовый камень, облицовочный материал, фундамент. 2.Кварцит – мелкозернистые кварцевые песчаники, песчинки не видны. Кварциты содержат 95-99%
SiO2. Сцепление кварца из-за температуры и давления. Прочность на сжатие = до 1000 Мпа. Высокая морозоустойчивость, малая истираемость, высокая огнеупорность, атмосферостойкость. Прим: подферменные камни в мостах, облицовка гидротехнич. сооруж., сырье д/производства огнеупоров. 3.Мрамор крупнозернистая плотная карбонатная порода, состоит из плотного известняка, в основе кальцит (карбонат кальция), отсутствует
цемент (спайка из-за температуры и давления) Горная порода – т.к. однороден. Прочность на сжатие = 100-300 МПа, но легко поддается обработке. Плотность до 2,9 г/см3 «+» хорошо обрабатывается, пилится, полируется. «-» истираемость, низкая атмосферостойкость и химическая устойчивость, не переносит резких перепадов
температур.4.Сланцы – имеют мелкозернистое строение. Полнокристаллическая структура. Хорошо колется. Прим: кровельный материал Состав: кварц, полевые шпаты, слюды, глина. Плотность 2700-2800 кг/м3, пористость до3%, прочность 50-240 МПа.
7.Состав, макро- и микроструктура древесины.
Растущее дерево состоит из корневой системы, ствола и кроны. Промышленное значение имеет ствол, так как из него получается от 60 до 90 % древесины. Макроструктурой называют строение ствола дерева, видимое невооруженным глазом или через лупу. Обычно изучают три основных разреза ствола: поперечный (торцовый), радиальный, проходящий через ось ствола, и тангенциальный, проходящий по хорде вдоль ствола. Макростроение древесины. На поперечном разрезе ствола древесного растения можно выделить следующие основные состовляющие древесины: 1) кора - защитный покров ствола дерева, состоящий из внешнего пробкового и внутреннего слоёв. Это своеобразная кожа дерева, предохраняющая его от воздействия внешней среды, а также участвующая в регуляции дыхания. 2) Камбий - тонкий слой, состоящий из живых клеток, размножающихся делением. Деление клеток камбиального слоя начинается весной и заканчивается осенью. Поэтому древесина ствола в поперечном разрезе состоит из ряда концентрических так называемых годичных колец, располагающихся вокруг сердцевины. Каждое годичное кольцо состоит из двух слоев: ранней (весенней) древесины, образовавшейся весной или в начале лета, и поздней (летней) древесины, которая образуется к концу лета. Ранняя древесина светлая и состоит из крупных, но тонкостенных клеток; поздняя древесина более темного цвета, менее пориста и обладает большей прочностью, так как состоит из мелкополостных клеток с толстыми стенками. 3) Луб− непосредственно примыкающий к камбию внутренний слой коры, состоящий в основном из живых клеток, выполняющий проводящую функцию между кроной дерева и его корнями. На поперечном разрезе древесины можно различить концентрические слои прироста, называемые годичными кольцами, которые светлее к поверхности дерева и темнее у центра. Светлая часть древесины называется 4) заболонью, а темная – 5)ядром. Заболонь более молодая часть ствола, менее устойчива к загниванию, чем ядро. Ядро образуется за счёт отмирания живых клеток древесины, закупорки водопроводящих путей, ядро обычно гораздо темнее заболони. В результате этого изменяются цвет древесины, её масса и показатели механических свойств. Ядро является самой прочной частью древесины. 7)Сердцевинные лучи. На поперечном разрезе некоторых пород хорошо видны светлые, направленные от сердцевины к коре линии − сердцевидные лучи. Сердцевидные лучи имеются у всех видов, но видны лишь у некоторых. Особенно хорошо сердцевинные лучи видны у дуба, бука. Сердцевинные лучи служат для прохода в поперечном направлении по стволу воды, воздуха и органических веществ, вырабатываемых деревом. У хвойных пород они обычно очень узки и видны только под микроскопом. 6)Сердцевина находится в центре ствола и проходит по всей его длине. Она представляет собой рыхлую ткань, которая легко разрушается живыми организмами, состоит в основном из живых клеток. Сердцевину не применяют в строительстве. Эта часть ствола дерева легко загнивает и имеет малую прочность.
3
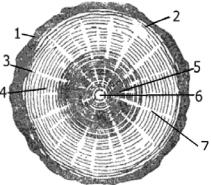
Древесные породы делят на: ядровые, имеющие ядро и заболонь (дуб, ясень, платан, сосна, лиственница, кедр и др.); спелодревесные, имеющие спелую древесину (она не отличается по цвету от заболони) и заболонь (ель, пихта, осина, бук и др.); заболонные, у которых отсутствует ядро и нельзя заметить существенного различия между центральной и наружной частями древесины ствола (береза, клен, ольха, липа). Микроструктура древесины— это строение древесины, видимое под микроскопом. Клетки древесины классифицируют в зависимости от выполняемых ими функций: Клетки механической, или опорной, ткани древесины — наиболее прочная и стойкая к загниванию. В древесине хвойных пород опорную ткань образуют трахеиды поздней древесины. Древесина хвойных пород на 90-95% состоит из трахеид. Опорная ткань в стволах лиственных пород состоит из толстостенных клеток, называемых «древесными волокнами». Проводящие клетки — сосуды у лиственных пород и трахеиды — у хвойных. Сосуды представляют собой тонкостенные трубочки, расположенные одна над другой диаметром 0,04-0,3 мм, длиной около 100 мм и более. У большинства хвойных пород сосудов нет, так как соответствующую функцию у них выполняют трахеиды. Сердцевинные лучи видны на поперечном разрезе ствола дуба, клена, бука и некоторых других лиственных пород в виде узких радиальных полосок. На тангенциальном разрезе ствола сердцевинные лучи представляются в виде темных штрихов. У хвойных пород они очень узки и видны только под микроскопом. В растущем дереве сердцевинные лучи служат для перемещения питательных веществ и сохранения запаса их на зиму. По отношению к объему всей древесины хвойные породы содержат 5-10%, а лиственные 10-35% сердцевинных лучей. Химический состав Абсолютно сухая древесина всех пород в среднем содержит (в %): углерода - 49,5; водорода - 6,3; кислорода - 44,1; азота - 0,1. В древесине на долю оболочек клеток приходится около 95% массы. Главные составные части оболочек целлюлоза (43-56%) и лигнин (19-30%), остальные : гемицеллюлозы, пектиновые вещества, минеральные вещества (главным образом соли кальция), небольшое количество жиров, эфирных масел, алкалоидов, гликозидов и т.п. Для всех клеток древесины характерно одревеснение — пропитывание оболочек лигнином. Древесина некоторых деревьев содержит дубильные вещества (квебрахо), красители (кампешевое дерево, сандал), бальзамы, смолы, камфору и т. д.
8.Физико-механические свойства древесины.
Физические свойства. Истинная плотность древесины изменяется незначительно, так как древесина всех деревьев состоит в основном из одного и того же вещества — целлюлозы (1,54 г/см3). Средняя плотность древесины разных пород и даже древесины одной и той же породы колеблется в весьма широких пределах, поскольку строение и пористость растущего дерева зависят от почвы, климата и других природных условий.
Пористость древесины хвойных пород колеблется от 46 до 81%, лиственных — от 32 до 80%. Влажность. В древесине различают гигроскопическую влагу, связанную в стенках клеток, и капиллярную влагу, которая свободно заполняет полости клеток и межклеточное пространство. Предел гигроскопичности (в среднем он составляет около 30%) соответствует полному насыщению стенок клеток древесины водой. У свежесрубленного дерева полная влажность может колебаться от 40 до 120%, а при выдерживании древесины в воде ее влажность может возрасти до 200%. При длительном нахождении влажной древесины на воздухе она постепенно высыхает и достигает равновесной влажности. Равновесная влажность комнатносухой древесины составляет 8-12%, поэтому до такой влажности высушивают паркетную клепку, древесину, идущую на изготовление столярных изделий, и т. п. Воздушно-сухая древесина после продолжительной сушки на открытом воздухе имеет влажность 15-18%. Теплопроводность древесины зависит от ее пористости, влажности и направления потока тепла. Электропроводность древесины зависит от ее влажности. Древесина, используемая при электрической проводке должна быть сухой. Электросопротивление сырой древесины в десятки раз меньше. Теплопроводность древесины зависит от ее пористости, влажности и направления потока тепла. Механические свойства древесины определяют путем испытания малых чистых (без видимых пороков) образцов древесины. Показатели свойств древесины должны быть пересчитаны на влажность 12%. Древесина по своей удельной прочности конкурирует с современными конструкционными материалами. Однако сучки, трещины и другие пороки сильно снижают механические свойства. Прочность при статическом изгибе древесины очень высокая: она примерно в 1,8 раза превышает прочность при сжатии вдоль волокон и составляет около 70% прочности при растяжении. Предел прочности при скалывании вдоль волокон для основных древесных пород составляет 6,0-13 МПа, а при
4
скалывании поперек волокон — в 3-4 раза выше. Статическая твердость численно равна нагрузке, которая необходима для вдавливания в образец древесины половины металлического шарика радиусом 5,64 мм. Твердость древесины по торцу на 15-50% выше чем в радиальном и тангенциальном направлениях. Особенностью древесины является высокая ползучесть, проявляющаяся особенно во влажных условиях.
9.Влажность древесины и ее влияние на свойства древесины.
Древесина, имея волокнистое строение и большую пористость, обладает огромной внутренней поверхностью, которая легко сорбирует водяные пары из воздуха (гигроскопичность). Влажность, которую приобретает древесина в результате длительного нахождения на воздухе с постоянной температурой и влажностью, называется равновесной. Она достигается в тот момент, когда упругость паров над поверхностью древесины оказывается равной упругости паров окружающего ее воздуха. По содержанию влаги различают мокрую древесину— с влажностью до 100%; свежесрубленную — 35 % и выше; воздушносухую —15...20 %; комнатносухую — 8...12 % и абсолютно сухую древесину. Стандартной принято считать влажность древесины 12 %. Влажность древесины, при которой стенки клеток насыщены водой (предельное содержание гигроскопической влаги), а полости и межклеточные пространства свободны от воды (отсутствие капиллярной воды), называют пределом гигроскопической влажности. Для древесины различных пород она колеблется от 23 до 35 % от массы сухой древесины. Гигроскопическая вода, покрывая поверхность мельчайших элементов в стенках клеток водными оболочками, увеличивает и раздвигает их. При этом объем и масса древесины увеличивается, а прочность снижается. Свободная вода в полостях клеток, существенно не изменяет расстояния между элементами древесины и поэтому не влияет на ее прочность и объем, увеличивая лишь массу, теплопроводность и теплоемкость. Усушка, разбухание и коробление. Как уже отмечалось, изменение влажности древесины от нуля до предела гигроскопической влажности вызывает изменение ее линейных размеров и объема — усушку или разбухание, величина которых зависит от количества испарившейся или поглощенной ею влаги и направления волокон. Вдоль волокон линейная усушка для большинства древесных пород не превышает 0,1 %, в радиальном направлении — 3...6 %, а в тангенциальном — 7...12 %. Разница в усушке древесины в тангенциальном и радиальном направлениях и неравномерность высыхания сопровождается возникновением внутренних напряжений в древесине, что может вызвать ее коробление и растрескивание. Боковые края досок стремятся выгнуться в сторону выпуклости годовых слоев, а наибольшему короблению подвержены доски, выполненные из древесины, расположенной ближе к поверхности бревна, и широкие доски.
10.Глины: условия образования, составы и основные свойства глин.
Основным сырьевым материалом для производства строительных керамических изделий является глинистое сырье, применяемое в чистом виде, или с добавками – отощающими, порообразующими, пластификаторами. Глинистое сырье (глины и каолины) – продукт выветривания изверженных полевошпатных ГП, содержащий примеси других ГП. Глинистые минеральные частицы диаметром 0,005 мм и менее обеспечивают способность при затворении водой образовывать пластичное тесто, сохраняющее при высыхании приданную форму, а после обжига приобретающее водостойкость и прочность камня. Помимо глинистых частиц в составе сырья имеется определенное содержание пылевидных частиц с размерами зерен 0,005-0,16 мм и песчаных частиц с размерами зерен 0,16-2 мм. При сушке глиняное тесто теряет воду и уменьшается по объему. Этот процесс называется воздушной усадкой. Чем больше в глинистом сырье глинистых частиц, тем выше пластичность и воздушная усадка. В зависимости от этого глины делятся на: высокопластичные (80-90% глинистых частиц, число пластичности более 25, водопотребность более 28%, воздушная усадка 10-15%); средне- и умеренно-пластичные (имеют в своем составе30-60% глинистых частиц, число пластичности 15-25, водопотребность 20-28%, воздушная усадка 7-10% ); малопластичные (5-30% глинистых частиц, число пластичности 7-15, водопотребность до 20%, воздушная усадка 5-7%). Глинистые частицы в большинстве своем состоят из вторичных минералов: каолинита Аl2О3*2SiO2*2H2О, монтмориллонита Аl2О3*4SiO2*4H2О , гидрослюдистых и их смесей. Глины с преобладающим содержанием каолинита имеют светлую окраску, слабо набухают при взаимодействии с водой, малопластичны, малочувствительны к сушке. Глины, содержащие монтмориллонит, весьма пластичны, сильно набухают, чувствительны к сушке и обжигу. Химический состав глин выражается содержанием различных оксидов. В керамическом сырье содержание оксидов колеблется в пределах: SiO2 – 4080%, Al2O3 – 8-50%, Fe2O3 – 0-15%, CaO – 0.5-25%, MgO – 0-4%. Качество глинистого сырья для производства керамики оценивается по ряду показателей: пластичности, связующей способности, усадке, спекаемости и огнеупорности. Под пластичностью понимается свойство глины во влажном состоянии принимать под влиянием внешнего воздействия желаемую форму без образования разрывов, трещин и сохраняющуюся при последующей сушке и обжиге. Спекаемостью глин называют их свойство уплотняться при обжиге и образовывать камнеподобный черепок.
11.Добавки, применяемые в производстве строительной керамики.
Для улучшения качества сырья и регулирования свойств керамических изделий в глину вводят отощающие, порообразующие (выгорающие), пластифицирующие и специальные добавки, плавни. Отощающие добавки –
5
вводят в пластичные глины для уменьшения усадки при сушке и обжиге и предотвращения деформаций и трещин в изделиях. К ним относятся: дегидратированная глина, шлаки, золы, кварцевый песок. Порообразующие добавки – вводят для повышения пористости черепка и улучшения теплоизоляционных свойств керамических изделий. К ним относятся: древесные опилки, угольный порошок, торфяная пыль. Плавни – вводят для снижения температуры обжига керамических изделий. К ним относятся: полевые шпаты, железная руда, доломит, магнезит, тальк, песчаник. Пластифицирующие добавки – для повышения пластичности сырьевых смесей при меньшем расходе воды. Это могут быть высокопластичные глины, поверхностноактивные вещества. Специальные добавки
– добавляют для повышения кислотостойкости: (песчаные смеси, затворенные жидким стеклом).
Глазурь – это стекловидное покрытие толщиной 0,1-0,2 мм, нанесенное на изделие и закрепленное обжигом. Глазури могут быть прозрачными и непрозрачными (глухими), различного цвета. Ангобом называется нанесенный на изделие тонкий слой белой или цветной глины, образующей цветное покрытие с матовой поверхностью. Ангоб по своим свойствам должен быть близок к основному черепку.
12.Основы технологии производства изделий строительной керамики.
1)карьерные работы; 2)механическая обработка глиняной массы; 3)формование изделий (пластическим, жестким, пулусухим, сухим и шликерным способом); 4)сушка и обжиг. Карьерная глина в естественном состоянии непригодна для получения керамических изделий. Поэтому проводится обработка с целью подготовки массы. Подготовку массы ведут в сочетании естественной и механической обработки. Естественная обработка – вылеживание предварительно добытой глины в течение 1-2 лет при периодическом увлажнении, замораживании
иоттаивании. Механическая обработка глин производится с целью дальнейшего разрушения их природной структуры, удаления или измельчения крупных включений, удаления вредных примесей. В зависимости от вида изготовляемой продукции, вида и свойств сырья массу приготовляют пластическим, жестким, полусухим, сухим
ишликерным способами. При пластическом способе подготовки массы и формования исходные материалы при естественной влажности или предварительно высушенные смешивают с добавками воды до получения теста с влажностью от 18 до 28%. Этот вид производства является наиболее простой и распространенный. Глиняная масса подвергается уплотнению под давлением 1,6-7МПа. Жесткий способ формования является разновидностью пластического способа. Влажность формуемой массы при этом способе колеблется от 13% до 18%. Формование осуществляется на мощных вакуумных шнековых или гидравлических прессах под давлением до 20 МПа. При этом способе требуются меньшие энергетические затраты чем при пластическом способе. Полусухой способ. Керамические изделия формуют из шихты с влажностью 8-12% при давлениях 15-40 МПа. Недостатком является металлоемкость, но длительность производственного цикла сокращается в два раза, до 30% уменьшается расход топлива. Сухой способ – это разновидность полусухого производства керамических изделий. Пресс-порошок готовится с влажностью 2-6%. При этом устраняется полностью необходимость сушки. Таким способом изготовляют плотные керамические изделия – плитки для полов, дорожный кирпич, материалы из фаянса и фарфора. Шликерный способ применяется, когда изделия изготавливаются из многокомпонентной массы, состоящей из неоднородных и трудноспекающихся глин и добавок. Отливка изделий производится из массы с содержанием воды до 40%. Сушка: Перед обжигом изделия должны быть высушены до содержания влаги 5-6%
во избежание неравномерной усадки, искривлений и растрескивания при обжиге. Сушка производится в туннельных или камерных сушилах до 72 часов при температуре 120-150оС. Затем идет обжиг.
13.Физико-химические процессы, протекающие в сырце при его обжиге.
Обжиг – важнейший и завершающий процесс в производстве керамических изделий. Процесс делится на три периода: прогрев сырца, собственно обжиг и регулируемое охлаждение. 1.При прогреве сырца до 120 град удаляется физически связанная вода и керамическая масса становится непластичной. Но если добавить воду, пластические свойства массы сохраняются. 2.В температурном интервале от 450 до 600 град происходит отделение химически связанной воды, разрушение глинистых минералов и глина переходит в аморфное состояние. При этом и при дальнейшем повышении температуры выгорают органические примеси и добавки, а керамическая масса теряет свои пластические свойства. При 800 град начинается повышение прочности изделий, благодаря протеканию реакций в твердой фазе на границах поверхностей частиц компонентов. В процессе нагрева до 1000 град возможно образование новых кристаллических силикатов. Одновременно с этим легкоплавкие соединения керамической массы и минералы плавни создают некоторое количество расплава, который обволакивает не расплавившиеся частицы, стягивает их, приводя к уплотнению и усадке массы в целом. Эта усадка называется огневой усадкой (2-8%). После остывания изделие приобретает камневидное состояние, водостойкость и прочность. Свойство глин уплотняться при обжиге и образовывать камнеподобный черепок называется спекаемостью глин. Интервал температур от температуры огнеупорности до начала спекания называется интервалом спекания. Интервал спекания для легкоплавких глин составляет 50-100 град, а огнеупорных до 400 град. Интервал температур обжига в зависимости от назначения и свойств керамического изделия от 900 для кирпича до 1800 для огнеупорной керамики градусов.
14.Структура и состав строительного стекла. Свойства строительного стекла.
6
Стекло - твердый аморфный материал, полученный в процессе переохлаждения расплава. Для придания стеклу нужных свойств ( цвета, прозрачности, химической и механической стойкости) используются химические соединения бора, алюминия, магния, кальция, бария, свинца, натрия, калия, железа, серы. Общая классификация стекла по назначению: строительное стекло; тарное стекло; техническое; сортовое. Строительным стеклом называют изделия из стекла, применяемые для остекления световых проёмов, устройства прозрачных и полупрозрачных перегородок, облицовки и отделки стен, лестниц и др. частей зданий. СОСТАВ. Стекло не является химическим веществом с определенным составом, который может быть выражен химической формулой; поэтому состав стекол условно выражают суммой оксидов (например, состав обычного оконного стекла SiO, — 70..72 %; Na2O — 14...15 %; CaO — 6,5...7 %; MgO - 4 %; Ai2O3 - 2 % ). Материалы, применяемые для стекловарения, делятся на главные и вспомогательные. Главные сырые материалы содержат кремнезём, борный и фосфорный гидриды, окись алюминия, оксиды щелочных и щёлочноземельных металлов, окись свинца, цинка и др. Кремнезём - главная часть стекла, вводимая в виде молотого кварца. Пригодность песка для стекловарения определяется содержанием в нём примесей и зерновым составом. Вредными примесями являются соединение железа и хрома, придающие желтовато-зелёный цвет. Размер зёрен песка для стекловарения должен находиться в пределах 0,2-0,5 мм. Окись алюминия Аl2О3вводится с глиной, каолином, гидратом окиси алюминия или в виде чистого глинозёма. Окись натрия Na2O вводится с одной кальцинированной содой либо (частично) с селитрой. Окись калия К2О вводится в виде солей —кислой или азотнокислой (селитра); применяется главным образом в производство посуды, цветных, оптических и некоторых технических стекол. Окись лития используется при выработке опаловых и некоторых специальных стекол и даётся в виде содержащих литий минералов. Окись кальция СаО вводится преимущественно в виде мела или известняка; окись магния MgO —в виде доломита, магнезита или жжёной магнезии. Окись бария применяется в виде углекислого, азотнокислого и сернокислого бария; используется при производстве оптических стекол и хрусталя. В тех же производствах находит применение окись свинца, которая вводится в виде сурика или глёта. Окись цинка применяется в производство оптических, химико-лабораторных и некоторых других стекол. К
вспомогательным сырым материалам относятся осветлители, обесцвечиватели, красители, глушители, а
также восстановители. СТРУКТУРА. Стекло — аморфное вещество. По агрегатному состоянию занимает промежуточное положение между жидким и кристаллическим веществами. Однако упорядоченность расположения атомов существует и в стеклах. Для плавленого кварца и силикатных стекол остаются в силе общие законы кристаллохимии силикатов; каждый атом кремния в них тетраэдрически окружен четырьмя атомами кислорода, но эти тетраэдры сочетаются друг с другом беспорядочно, образуя непрерывную пространственную сетку, в пустотах которой тоже беспорядочно располагаются ионы металлов. Благодаря этому один «микроучасток» стекольной массы отличен по атомному строению от другого, соседствующего с ним. Этим и объясняется отсутствие у стекла постоянной точки плавления, постепенность перехода его из твердого в жидкое состояние и обратно. СВОЙСТВА Строительное стекло чаще подвергается изгибу, растяжению и удару, поэтому главным показателем, прочность при растяжении и хрупкость. Расчетный теоретический предел прочности стекла при растяжении составляет 12 000 МПа, практически эта величина ниже в 200...300 раз, и колеблется от 30 до 60 МПа (при сжатии — 700... 1000 МПа и более). Это объясняется тем, что в стекле имеются ослабленные участки (трещины, внутренние напряжения). На прочность стекла оказывают влияние и технологические дефекты, инородные включения. Хрупкость — главный недостаток стекла, проявление хрупкости у материалов является следствием сочетания нескольких факторов: низкое значение отношения прочности материала на разрыв к его модулю упругости Rp/E и высокая скорость и отсутствие препятствий для распространения трещин. Оптические свойства стекла характеризуются светопропускаиием (прозрачностью), светопреломлением, отражением, рассеиванием и др. Обычные силикатные стекла пропускают всю видимую часть спектра и не пропускают ультрафиолетовые и инфракрасные лучи. Теплопроводность различных видов стекла составляет 0,5... 1 Вт/(м*°С). Коэффициент линейного температурного расширения стекла относительно невелик. Звукоизолирующая способность стекла относительно высока. По этому показателю стекло толщиной 1 см соответствует кирпичной стене в полкирпича — 12 см.
15. Разновидности строительного стекла и их применение в строительстве. Понятие о ситаллах.
Строительным стеклом называют изделия из стекла, применяемые для остекления световых проёмов, устройства прозрачных и полупрозрачных перегородок, облицовки и отделки стен, лестниц и др. К этой же категории относят тепло- и звукоизоляционные материалы (пеностекло и стекловата), а также стеклянные трубы. Строительное стекло подразделяют на: Листовое оконное стекло изготавливается в виде плоских листов, размер которых колеблется от 400х400 мм до 1600х2200 мм при толщине от 2 до 6 мм. Плотность от 2470 до 2500 кг/м3. Средняя прочность при изгибе составляет 400 кгс/см2. Качественные листы оконного стекла прозрачны и бесцветны. К-Стекло (низкоэмиссионное энергосберегающее стекло) Высококачественное флоат-стекло со стойким, прозрачным покрытием и с низкой эмиссией. Покрытие пропускает солнечную коротковолновую энергию в помещение, но не пропускает наружу длинноволновое тепловое излучение, например, от отопительного прибора. Применяется обычно в качестве внутреннего стекла в стеклопакетах, причем покрытие обращено в сторону межстекольного пространства. К-стекло может быть закалено и ламинировано.
7
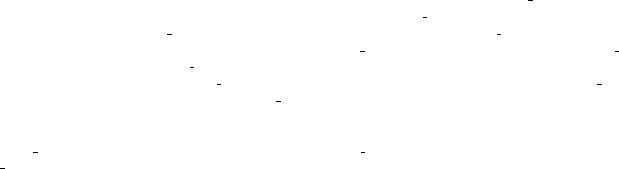
Полированное стекло. Прозрачное стекло, обе поверхности которого отшлифованы и отполированы для придания им плоскостности и параллельности, с целью обеспечения четкого неискаженного изображения, востребовано в производстве светопрозрачных конструкций (окон, витрин, в производстве зеркал). Из полированного закалённого стекла толщиной 10-20 мм изготовляют стеклянные полотна для дверей. Витринное стекло Полированное прозрачное листовое стекло толщиной 6-10 мм. Используется для оформления витрин и витражей. Армированное стекло Плоское стекло с вмонтированной металлической сеткой с квадратными или шестиугольными ячейками, оно может быть полированным (полированное армированное стекло) или полупрозрачным с шестиугольной сеткой (узорчатое прокатное армированное стекло). Армирование не увеличивает механическую прочность стекла и даже снижает его примерно в 1,5 раза. Зато наличие сетки не позволит в результате удара осколкам разлетаться и выпадать из переплетов. Узорчатое стекло Листовое стекло, которое имеет с одной стороны рифлёную поверхность, предназначается для рассеяния света. Рисунок рельефа может быть выполнен как в процессе изготовления, так и в момент доработки. Узорчатое строительное стекло используют для остекления лестничных клеток, внутренних перегородок. Выпускается размерами от 400х400 до 1200х1800 мм при толщине 3-6,5 мм. Цветное(тонированное) стекло. Это стекло получают путем внесения специальных добавок в процессе изготовления, в результате чего стекло окрашивается по всей толщине. Другой вариант цветного стекла состоит из 2 слоев – основного бесцветного и тонкого цветного. Такое стекло применяют для витражей, декорирования мебели, остекления зданий. Профилированное строительное стекло Прозрачные или цветные стеклянные пластины с профилем швеллерного или коробчатого типа. Толщина профилированного стекла 6 мм; На поверхности профилированного стекла, как правило, нанесен какой-либо рисунок, рассеивающий свет. Кроме того профилированное стекло может быть прозрачным или селективным (с нанесенным солнцезащитным покрытием). Профилированные стекла находят применение в стеновых конструкциях в виде одноили двухслойных конструкций. Стеклоблоки изделия с герметически закрытой полостью, образованной в результате соединения двух отпрессованных стеклянных пластин. Каждая половинка сделана из стекла толщиной 6-9 мм. Поверхность стеклоблока может быть рифленой, прозрачной, глянцевой и матовой, однотонной и разноцветной. Стеклопакеты Элементы, в которых два стекла или более соединены герметично друг с другом с помощью рамки средника, огибающей края стекол, или с помощью эластичных масс, при этом теплоизолирующая способность элемента улучшается. Многослойное стекло Состоит из двух и более стекол, которые склеены прочной промежуточной пленкой при высокой температуре и высоком давлении, образуя при этом монолитный лист. Многослойное стекло может быть изготовлено из обычного строительного стекла, а также закаленного или полузакаленного стекла. При разбивании кусочки стекла удерживаются на промежуточной пленке, что снижает возможность травм. Многослойное стекло можно сверлить и вырезать. Невидимая промежуточная пленка повышает звукоизоляцию и снижает воздействие ультрафиолетовых лучей. Марблит утолщенное плоское глушеное стекло от черного до зеленого цвета с блестящими переливающимися вкраплениями преимущественно с полированной поверхностью, выпускаемое в виде плиток различных размеров. Лицевая сторона марблита может быть гладкой, кованой, рифленой или мелкоузорчатой, тыльная - рифленая. Его применяют для облицовки наружных и внутренних стен лечебных помещений, магазинов, производственных помещений с повышенной влажностью, общественных зданий, мемориальных комплексов, витражей, взамен естественных каменных материалов. Стемалит - стекло закаленное эмалированное покрыто с одной стороны эмалевой краской и подвергнуто термообработке с целью упрочнения стекла и закрепления краски на его поверхности, применяется для наружной и внутренней отделки стен и перегородок зданий и сооружений. Имеет высокую термостойкость, устойчивость против атмосферных воздействий, сохраняет постоянный цвет. Увиолевое стекло, стекло, пропускающее ультрафиолетовое излучение с длиной волны менее 400 нм (в биологической области спектра). Используется для остекления школ, детсадов, лечебных учреждений, парников, для оболочек бактерицидных и люминесцентных ламп и т.д. Плитки облицовочные, часто используются в виде мозайки сложенное в ковер, они применяются для наружной и внутренней облицовки зданий, изготовления декоративно-художественных панно. Плитки могут быть непрозрачными, белого или другого цвета, с гладкой или рифленой, матовой или блестящей поверхностью. Ситаллы представляют собой стеклокристаллические материалы, получаемые из стекла в результате его полной или частичной кристаллизации. Сырьем для получения ситаллов служат те же природные материалы, что и для стекла. Особенность структуры ситаллов характеризуется тем, что между весьма мелкими кристаллами (несколько мкм) равномерно распределена стекловидная фаза (прослойкой около 1 мкм). Ситаллы получают методом вытягивания, выдувания, прокатки и прессования, добавляя к стеклянным расплавам специальные добавки (минерализующие катализаторы), улучшающие кристаллизацию. По сравнению с производством изделий из стекла получение ситаллов требует дополнительной термической обработки, в процессе которой происходит превращение стекла в стеклокристаллическое состояние. Ситаллы имеют большую прочность (до 500 МПа) и высокую стойкость к химическим и тепловым воздействиям. По внешнему виду ситаллы могут быть темного, коричневого, серого, кремового, светлого цветов, глухие и прозрачные . Они могут использоваться в виде конструктивного и отделочного материала. Шлакоситалл - это стеклокристаллический материал, на основе металлургического шлака, кварцевого песка и некоторых добавок и характеризуемый мелкозернистой кристаллической структурой. Листовой шлакоситалл производят белого и серого цветов с гладкой или рифленой поверхностью. При необходимости поверхность
8
шлакоситалла шлифуют, полируют и фрезеруют; обладает высокой химической стойкостью, износостоек, водонепроницаем, отличается повышенной механической прочностью и твердостью по сравнению со стеклом. Плотность — 600-2700 кг/м3; Прочность при изгибе — 65-110 МПа; Прочность на сжатии — 250-550 МПа.
16.Основы технологии производства изделий строительного стекла.
Технология получения стекла состоит из двух циклов. Цикл технологии стекломассы включает: а) подготовки сырых материалов; б) смешивания их в определённых соотношениях в шихту; в) варки шихты в стекловаренных печах для получения однородной жидкой стекломассы. Цикл технологии получения стеклянных изделий складывается из операций: а) доведения стекломассы до температуры, требуемой условиями формования; б) формования изделий; в) постепенного охлаждения изделий до комнатной температуры; г) термической, механической или химической обработки отформованных изделий для придания им заданных свойств. Массовое производство стекла стало возможным только в конце XIX века благодаря изобретению печи Сименса-Мартина и заводскому производству соды. В XX в. были разработаны различные способы вытягивания бесконечной ленты стекла, методы машинной вытяжки стекла Либби-Оуэнса, Фурко, Питтсбурга. По способу Эмиля Фурко стекло вытягивалось по вертикали из стекловаренной печи через прокатные вальцы в виде непрерывной ленты наружу, поступая в шахту охлаждения, в верхней части которой оно резалось на отдельные листы. Толщина стекла регулировалась изменением скорости вытягивания. Метод Фурко находит применение вплоть до настоящего времени. Стекло, получаемое этим методом, называется тянутым стеклом. Для изготовления витринных и зеркальных стекол тянутое и прокатное листовое стекло подвергают шлифовке и полировке. Наиболее передовым является флоат-метод, разработанный и запатентованный в 1959 году английским изобретателем Пилкингтоном. Стекло поступает из печи плавления в горизонтальной плоскости в виде плоской ленты через ванну с расплавленным оловом для дальнейшего охлаждения и отжига. Преимуществом флоат-метода является более высокая производительность, стабильная толщина и качество поверхности. По качеству поверхности такое стекло не уступает полированному—флоат-процесс вытесняет технику шлифовки и полировки стекла. Наибольший размер получаемого стекла, как правило, составляет 5100-6000 мм х 3210 мм, при этом толщина листа может быть даже меньше 2 мм и достигать 25 мм. Получаемое стекло может быть прозрачным, окрашенным или иметь специально нанесенное покрытие. Стекло, получаемое при помощи флоат-метода, называется флоат-стеклом и в настоящее время является наиболее распространенным типом стекла.
17.Особенности поведения металлов при их деформировании. Обработка металлов давлением.
Качество металлов и изделий из них оценивают по результатам механических, химических, технологических испытаний и наружного осмотра. Испытание на растяжение. Изготовливают стандартные образцы с установленной расчетной длиной, диаметром образца, площадью поперечного сечения. Испытания проводят на специальной машине путем осевого растяжения образца до разрыва, с автоматической записью диаграммы зависимости деформации от нагрузки. Испытание на изгиб. Испытание на изгиб в холодном или нагретом состоянии проводится для определения способности листового металла принимать заданный по размерам и форме изгиб. Образцы для испытания вырезают из листа без обработки поверхностного слоя и подвергают пробе на изгиб. Испытание на удар. Так определяют способность работы металла в условиях динамических нагрузок или хрупкость. Чем пластичнее металл, тем лучше он переносит ударные нагрузки. Испытание на удар производят на специальных маятниковых копрах с применением стандартных образцов с надрезом. Ковка— обработка металла давлением, при котором инструмент оказывает многократное прерывистое воздействие на заготовку, в результате чего она, деформируясь, приобретает заданную форму. По способу обработки ковка бывает горячей и холодной. Температура ковки зависит от химического состава и структуры обрабатываемого металла. Идеальный материал для ковки — мягкая сталь, которая в разогретом состоянии практически течет. Холодная ковка требует от металла высокой степени ковкости — определенной степени вязкости, пластичности
итекучести. В современных условиях холодная ковка применяется главным образом в ювелирном деле — для обработки золота, серебра, меди и платины. Неотъемлемая часть холодной ковки — гнутье. Прутья, декоративные элементы, вырезанные вручную или машинным способом, гнут, придавая им необходимую форму, после чего все детали спаивают между собой. В настоящее время таким образом собираются заборы, ворота, балконные и лестничные ограждения и т. д. Еще одна из разновидностей холодной ковки — штамповка, то есть обработка металлов давлением на прессах с помощью формообразующего приспособления.
18.Кристаллизация металлов, типы структур, дефекты кристаллов.
Металлы, простые вещества, обладающие в обычных условиях характерными свойствами: высокой электропроводностью и теплопроводностью, пластичностью. Металлы в твёрдом состоянии имеют кристаллическое строение. Сплавы – это макроскопические однородные системы, состоящие из двух или более элементов (металлов, реже - металлов и неметаллов) с характерными металлическими свойствами. Металлы обладают рядом ценных для строительства свойств: большая прочность, пластичность, свариваемость, способность упрочняться при термомеханических и химических воздействиях. Этим обуславливается их широкое применение в строительстве. В чистом виде металлы применяются редко, они используются в виде сплавов.
9

Железо и его сплавы (сталь С<=2,14%; чугун С>2,14%) называются черными металлами, остальные (Be, Mg, Al, Ti, Cr, Mn, Ni, Cu, Zn и др.) и их сплавы называются цветными. Наибольшее применение в строительстве имеют черные металлы, их стоимость ниже цветных, но цветные металлы более прочны, пластичны, стойки против коррозии. Сырьем для получения черных металлов служат руды железа: магнетит(FeFe2O4), гематит(Fe2O3), хромит(Fe Cr 2O4). Для производства цветных металлов используются бокситы, руды меди, цинка и др. Процесс восстановления руды выражается уравнением: Fe2O3 + 3CO = 2Fe + 3CO2 Сталь выплавляют в основном в трех агрегатах: 1)Конвекторах 2)Мартеновских печах 3)Электрических печах. В процессе продувки воздухом жидкого чугуна в конвекторе выгорают кремний, марганец, углерод и частично железо. В мартеновском процессе (в отличие от конвертерных) тепла, выделяющегося в результате химических реакций окисления примесей, недостаточно для плавки. Поэтому в печь дополнительно подаётся тепло, получаемое в результате сжигания топлива. Для выплавки стали используют электрические печи двух типов: дуговые и индукционные (высокочастотные). Металлы и сплавы в твердом состоянии – кристаллические тела. Атомы в них расположены закономерно в узлах кристаллической решетки и колеблются с частотой порядка 1013Гц. Связь электростатическая, обусловленная силами притяжения и отталкивания между положительно заряженными ионами и электронами проводимости. Большинство металлов имеет пространственные решетки в виде простых геометрических фигур. Взаимное расположение зерен отдельных элементов и сплавов определяет структуру металлов и их свойства. Кристаллическая решетка металлов и сплавов далека от идеального строения. В ней имеются дефекты – вакансии и дислокации. Процесс кристаллизации начинается с образования кристаллических зародышей и продолжается при их росте. В зависимости от условий кристаллизации образуются кристаллы разных размеров неправильной формы. Стали являются многокомпонентными сплавами. Кроме основы – железа
(от 97,0 до 99,5% Fe) и углерода (до 2,14%), имеются ряд примесей: Mn, Si, S, P, O, N, H и др. Наличие Mn, Si
обусловлено технологическими особенностями производства. Наличие P, S, O, N, H обусловлено невозможностью полного удаления их из металла при выплавке. Случайные примеси Ni, Cr, Cu и др. – попадают из легированного металлического лома. Влияние углерода на свойства стали Относительное удлинение, по мере увеличения углерода непрерывно снижаются. Твердость линейно повышается с увеличением углерода, предел прочности до 0,8-0,9% С растёт линейно, при дальнейшем увеличении углерода снижается предел прочности. Ударная вязкость по мере увеличения содержания углерода до 0,6% резко снижается Влияние кремния и марганца. Кремний и марганец раскисляют сталь, т.е. соединяясь с кислородом закиси железа FeO, в виде окислов переходят в шлак: 2FeO + Si = 2Fe + SiO; FeO + Mn = Fe + MnO. Удаляя О2 – Si и Mn повышают плотность металла. Si – сильно повышает предел текучести, снижает пластичность. Mn – заметно повышает прочность, не снижая пластичности. Влияние серы Сера (S) является вредной примесью. Попадает в сталь из чугуна (из золы и руды). Содержание серы: S – 0,035-0,06%. Выводят серу из стали с помощью марганца. Марганец образует соединение MnS: FeS + Mn → MnS + Fe. Сера и её соединения при комнатных и пониженных температурах способствует снижению ударной вязкости стали. Также сера снижает пластичность. Влияние фосфора (Р) является вредной примесью. Содержится в пределах 0,025–0,045% . Попадает в сталь в процессе производства из руды, топлива. Растворяясь в железе, фосфор сильно искажает решетку и увеличивает пределы прочности и текучести, но уменьшает пластичность и вязкость. Фосфор – усиливает ковалентную (хрупкую) связь и ослабляет металлическую. С понижением температуры хрупкость металла увеличивается, облегчает обрабатываемость стали режущим инструментом. Влияние азота, кислорода и водорода Кислород (О2): образует неметаллические включения оксиды – FeO, MnO, Al2O3, SiO2. Азот (N2): образует нитриды – Fe4N, Fe2N, AlN. Кислород и азот в свободном виде располагаются в трещинах и др. Эти включения значительно уменьшают ударную вязкость, повышают порог хладноломкости и уменьшают пластичность, при этом повышается прочность стали. Водород (Н2): при затвердевании часть водорода в атомарном состоянии остаётся в стали, способствуя сильному охрупчиванию стали. Примеси цветных металлов Примеси: Cu, Pb, Zn, Sb, Sn и др. попадают в сталь в процессе переплавки лома. Их содержание невелико и оказывают незначительное влияние на механические свойства.
19.Термическая и химико-термическая обработка металлов.
Вцелях получения более высоких или специально заданных свойств изделия из металлов и сплавов подвергают термической обработке. Такая обработка заключается в изменении структуры сплава путем его предварительного нагрева до заранее определенных температур, некоторой выдержке при этих температурах и последующего охлаждения по заданному режиму. Шире всего применяют отжиг, нормализацию, закалку и отпуск стали. Отжиг стали производят в тех случаях, когда необходимо уменьшить твердость, повысить пластичность и вязкость, улучшить обрабатываемость. Отжиг стали производят путем нагрева ее до температуры выше верхних критических точек на 20...50 СС выдержки при такой температуре до полного прогрева слитка с последующим очень медленным охлаждением. Нормализация заключается в нагреве стали на ЗО...5О°С выше критических точек, непродолжительной выдержке при этой температуре и последующем охлаждении на воздухе. Нормализацию стали применяют в тех случаях, когда необходимо получить мелкозернистую однородную структуру с более высоким твердостью и прочностью, но с несколько меньшей пластичностью, чем после отжига. Закалка стали заключается в нагреве ее до температуры образования аустенита, выдержке при этой температуре
10