
Методичка по строй мату 1
.pdf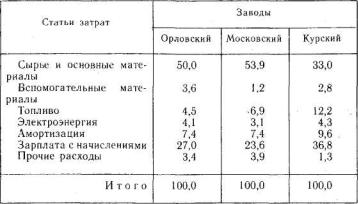
Таблица 5.3. Себестоимость, %, гипса по отдельным заводам
ном сырье; при этом затраты на сырье и материалы различаются в 3...3.5 раза.
Большие резервы заключены в снижении трудоемкости производства путем механизации и автоматизации производственных процессов.
Перспективы массового применения гипсовых изделий определяются в значительной степени наличием основного сырья— гипсовым камнем, а также пригодностью месторождений к промышленной эксплуатации.
Имеющиеся промышленные запасы сырья (около 6 млрд. т) достаточны как для обеспечения действующего производства гипсовых вяжущих и изделий, так и для его дальнейшего развития в целях полного удовлетворения потребностей строительства в этих эффективных видах продукции.
§ 5.5. Магнезиальные вяжущие вещества
Разновидностями магнезиальных вяжущих веществ являются каустический магнезит и каустический доломит.
Каустический магнезитполучают при обжигегорнойпороды магнезита MgCO3 вшахтных иливращающихся печах при650...
850°С. В результате MgCO3 разлагается по схеме MgCO3 = = MgO + CO2. Оставшееся твердое вещество (окись магния) из мельчают в тонкий порошок.
КаустическийдоломитMgO иСаСО3 получаютпутемобжига природного доломита СаСО3·MgCO3 с последующим измельче нием его в тонкий порошок. При обжиге доломита СаСО3 не раз лагается и остается инертным как балласт, что снижает вяжу щую активность каустического доломита по сравнению с каусти ческим магнезитом.
Магнезиальные вяжущие затворяют не водой, а водными рас-
5* |
— 131 — |
творами солей сернокислого или хлористого магния. Магнезиальные вяжущие, затворенные на растворе хлористого магния, дают большую прочность, чем на растворе сернокислого магния. Магнезиальные вяжущие, являясь воздушными, слабо сопротивляются действию воды. Их можно использовать только при затвердении на воздухе с относительной влажностью не более 60%. Каустический магнезит легко поглощает влагу и углекислоту из воздуха, в результате чего образуются гидрат оксида магния и углекислый магний. В связи с этим каустический магнезит хранят в плотной герметической таре. На основе магнезиальных вяжущих в прошлом времени изготовляли ксилолит (смесь вяжущего с опилками), используемый для устройства полов, а также фибролит и другие теплоизоляционные материалы. В настоящее время применение магнезиальных вяжущих резко сократилось.
§ 5.6. Кислотоупорные цементы
Кислотоупорные цементы состоят из смеси водного раствора силиката натрия (растворимого стекла), кислотоупорного напол-
нителя и добавки — ускорителя твердения. В качестве микрона-
полнителя используют кварц, кварциты, андезит, диабаз и другие кислотоупорные материалы; ускорителем твердения служит кремнефтористый натрий. Вяжущим материалом в кислотоупорном цементе является растворимое стекло — водный раствор силиката натрия Na2O·SiO2 или силиката калия K2O·nSiO2. Величина п указывает на отношение числа молекул кремнезема к числу молекул щелочного оксида и называется модулем стекла, он колеблется от 2,5 до 3,5.
Добавка кремнефтористого натрия также повышает водостойкость и кислотоупорность цемента. Отечественная промышленность выпускает кислотоупорный кварцевый кремнефтористый цемент, состоящий из смеси тонкомолотого чистого кварцевого песка 15...30% и кремнефтористого натрия Na2SiF6 — 4...6% от массы наполнителя.
Кислотоупорные цементы применяют для футеровки химической аппаратуры, возведения башен, резервуаров и других сооружений химической промышленности, а также для приготовления кислотоупорных замазок, растворов и бетонов.
Как указывалось ранее, для приготовления кислотоупорного цемента применяют растворимое стекло. Растворимое стекло получают при сплавлении в течение 7... 10 ч в стекловарочных печах при 1300...1400°С кварцевого песка, измельченного и тщательно смешанного с кальцинированной содой, сульфатом натрия или с поташом К2СО3. Полученная стекломасса поступает из печи в вагонетки, где быстро охлаждается и распадается на куски. Застывшие куски называют «силикат-глыба». Это стекло растворимо в воде при обычных условиях, но при действии пара высокого давления 0,5...0,6 МПа и температуре около 150°С сравнительно быстро переходит в жидкое состояние.
— 1 3 2 —
Твердеет растворимое стекло (довольно медленно) только на воздухе вследствие выделения и высыхания аморфного кремнезема под действием углекислоты воздуха по реакции
Na2SiO3 + СО2 + 2Н2О →Si (ОН) 4 + Na2CO3
Однако глубина проникания углекислоты воздуха сравнительно невелика и положительное ее действие наблюдается только на поверхности.
Ускоряет твердение растворимого стекла добавка катализатора — кремнефтористого натрия Na2SiF6. Последний вступает во взаимодействие с растворимым стеклом, в результате чего быстро образует гель кремнекислоты — клеящее вещество, что приводит к быстрому твердению системы:
Na2SiF6 + 2Na2SiO6 + 6H2O → 6NaF + 3Si (ОН) 4
Силикат-глыбу можно транспортировать в таре или навалом. Растворимое стекло, имеющее сиропообразную консистенцию, транспортируют в бочках, стеклянных баллонах. Растворимое стекло применяют для приготовления кислотостойких и жароупорных обмазок. Нельзя применять растворимое стекло для конструкций, подверженных длительному воздействию воды, щелочей и фосфорной, фтористо-водородной или кремнефтористоводородной кислоты.
Кислотоупорный цемент не водостоек; разрушается от воздействия воды и слабых кислот. Для повышения водостойкости в состав цемента вводят 0,5% льняного масла или 2% гидрофобизующей добавки. Полученный таким образом гидрофобизованный цемент называют кислотоупорным водостойким цементом (КВЦ).
Для повышения кислотостойкости кислотоупорных бетонов рекомендуется обрабатывать их поверхность разбавленной соляной или серной кислотой, раствором хлористого кальция или хлористого магния.
§ 5.7. Строительная известь
Строительную известь получают путем обжига (до удаления углекислоты) из кальциево-магниевых горных пород — мела, известняка, доломитизированных и мергелистых известняков, доло-
митов.
Для производства тонкодисперсной строительной извести гасят водой или размалывают негашеную известь, вводя при этом минеральные добавки в виде гранулированных доменных шлаков, активные минеральные добавки или кварцевые пески. Строительную известь применяют для приготовления строительных растворов и бетонов, вяжущих материалов и в производстве искусственных камней, блоков и строительных деталей.
В зависимости от условий твердения различают строительную известь воздушную, обеспечивающую твердение строительных
— 133 —
растворов и бетонов и сохранение ими прочности в воздушносухих условиях, и гидравлическую, обеспечивающую твердение растворов и бетонов и сохранение ими прочности как на воздухе, так и в воде. Воздушная известь по виду содержащегося в ней основного оксида бывает кальциевая, магнезиальная и доломитовая. Воздушную известь подразделяют на негашеную и гидратную (гашеную), получаемую гашением кальциевой, магнезиальной и доломитовой извести. Гидравлическую известь делят на слабогидравлическую и сильногидравлическую. Различают гидравлическую известь комовую и порошкообразную. Порошкообразная известь бывает двух видов: молотая и гидратная (гашенная вода). Комовую известь выпускают без добавок и с добавками.
Строительную негашеную известь по времени гашения делят на быстрогасящуюся — не более 8 мин, среднегасящуюся — не более 25 мин, медленногасящуюся — более 25 мин.
Строительную воздушную известь получают из кальциево-
магниевых карбонатных пород. Технологический процесс получения извести состоит из добычи известняка в карьерах, его подготовки (дробления и сортировки) и обжига. После обжига производят помол комовой извести, получая молотую негашеную известь, или гашение комовой извести водой, получая гашеную известь.
Основным процессом при производстве извести является обжиг, при котором известняк декарбонизуется и превращается в известь по реакции СаСО3↔ СаО + СО2. Диссоциация карбонатных пород сопровождается поглощением теплоты (1 г-моль СаСО3 требует для разложения примерно 190 кДж). Реакция разложения углекислого кальция обратима и зависит от температуры и парциального давления углекислого газа. Диссоциация углекислого кальция достигает заметной величины при температуре свыше 600°С. Теоретически нормальной температурой диссоциации считают 900°С. В заводских условиях температура обжига известняка зависит от плотности известняка, наличия примесей, типа печи и ряда других факторов и составляет обыч-
но1100...1200°С.
При обжиге из известняка удаляется углекислый газ, составляющий до 44% его массы, объем же продукта уменьшается примерно на 10%, поэтому куски комовой извести имеют пористую структуру. Обжиг известняка производят в различных печах: шахтных, вращающихся, в «кипящем слое», во взвешенном состоянии и т. д. Наибольшее распространение получили экономичные по расходу топлива шахтные пересыпные известеобжигательные печи, однако известь в них оказывается загрязненной золой топлива.
Шахтная печь (рис. 5.3) состоит из шахты, загрузочного и выгрузочного устройства, воздухоподводящей и газоотводящей аппаратуры. Известняк в шахтную печь загружают периодически или непрерывно сверху. Материал по мере выгрузки извести
— 134 —
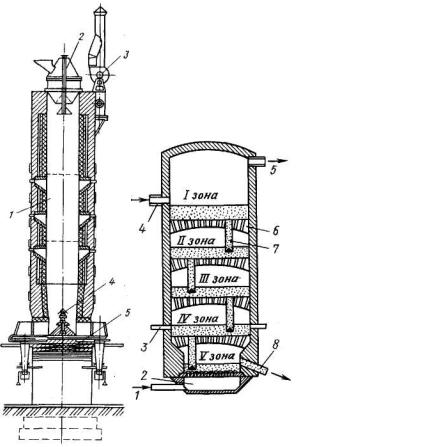
опускается вниз, и навстречу обжигаемому материалу просачиваются горячие дымовые газы. По характеру процессов, протекающих в шахтной печи, различают зоны подогрева, обжига и охлаждения. В зоне подогрева в верхней части печи с температурой печного пространства не выше 900°С известняк подсушивается, подогревается и в нем выгорают органические примеси. В средней части печи — в зоне обжига, где температура достигает 900...1200°С, — происходит разложение СаСО3 и выделение углекислого газа. В нижней части печи — зоне охлаждения — известь охлаждается поступающим снизу воздухом с 900 до
50...100°С.
Газовые печи позволяют получить «чистую» известь, они проще в эксплуатации, процесс обжига в них можно механизировать и автоматизировать.
Во вращающихся печах получают известь высокого качества, но при этом расходуется много топлива.
Имеют применение высокопроизводительные агрегаты с обжигом в «кипящем слое». Обжиг в «кипящем
|
Рис. 5.4. Схема установки для обжига из- |
|
вести в «кипящем слое»: |
|
1 — подача сжатого воздуха; 2 — воздушная ко- |
|
робка с непровальной решеткой; 3 — |
Рис. 5.3. Шахтная печь |
горелки; 4 — загрузка известняка; 5 — отвод |
для обжига извести: |
отходящих газов на очистку; 6 — решетчатый свод; |
7 — переливная труба; 8 — выгрузка |
|
1 — шахта; 2 — загрузоч- |
обожженной извести |
ный механизм; 3 — дымо- |
|
сос; 4 — гребень для подачи |
|
воздуха; 5 — разгрузочный |
|
механизм |
|
|
— 135 — |
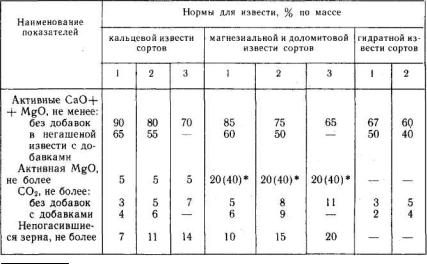
слое» (рис. 5.4) производят в реакторе, представляющем собой металлическую шахту, отфутерованную внутри и разделенную по высоте решетчатыми сводами на 3...5 зон. Передача материала из зоны в зону производится через трубки, имеющие ограничитель. Высота «кипящего слоя» определяется от обреза переливной трубки до решетки. По периферии реактора имеются горелки для газа или мазута. Многозонность реактора позволяет получать известь высокого качества при небольшом расходе топлива. Полученный при обжиге карбонатных пород полупродукт носит название комовой извести-кипелки. В дальнейшем она поступает на помол или гашение.
Молотая негашеная известь с добавками производится 1-
го и 2-го сортов и гидратная (гашеная) без добавок и с добавками двух сортов: 1-го и 2-го. Воздушная известь должна удовлетворять требованиям табл. 5.4.
В соответствии с требованиями ГОСТ 9179—77 негашеную известь следует измельчать до тонкости, при которой остаток при просеивании пробы через сита № 02 и № 008 должен быть соответственно не более 1,5 и 15%. Обычно заводы выпускают известь, характеризующуюся остатками на сите № 008 до 2...7%, что примерно соответствует удельной поверхности 3500...
5000 см2/г.
Таблица 5.4. Технические требования к воздушной извести
* В скобках указано содержание MgO для доломитовой извести.
Молотую негашеную известь транспортируют в герметически закрытых металлических контейнерах или в бумажных битуминизированных мешках. Хранить молотую известь до употребления можно не более 10...15 сут в сухих складах.
— 136 —
При работах с известью необходимо соблюдать требования по охране труда. Попадание частиц молотой извести в легкие, а также на слизистые оболочки, особенно глаз, опасно.
Молотую негашеную известь применяют без ее предварительного гашения, что имеет ряд преимуществ: исключаются отходы в виде непогасившихся зерен, используется тепло, которое выделяется при гидратации извести, что ускоряет процессы твердения извести. Изделия из этой извести имеют и большую плотность, прочность и водостойкость.
Для ускорения твердения растворных и бетонных смесей на молотой негашеной извести в их состав вводят хлористый кальций, а для замедления твердения в начальный период (схватывания) добавляют гипс, серную кислоту и сульфитно-спиртовую барду. Добавка гипса и хлористого кальция, кроме того, повышает прочность растворов и бетонов, а добавки замедлителей твердения предупреждают образование трещин, что возможно при отсутствии определенных условий твердения. Гидратная известь. Известь воздушная отличается от других вяжущих веществ тем, что может превращаться в порошок не только при помоле, но и путем гашения — действие воды на куски комовой извести с выделением значительного количества тепла по реакции
СаО + Н2О = Са(ОН)2 + 65,5 кДж.
1 г-моль СаО выделяет 65,5 кДж тепла, 1 кг извести-кипел-
ки— 1160 кДж.
Стехиометрически для гашения извести в пушонку необходимо 32% воды от массы СаО. Практически в зависимости от состава извести, степени ее обжига и способа гашения количество воды берут в 2, а иногда и в 3 раза больше, так как в результате выделения тепла при гашении происходит парообразование и часть воды удаляется с паром. На скорость гашения извести оказывают влияние температура и размеры кусков комовой извести. С повышением температуры ускоряется процесс гашения. Особенно быстро процесс гашения протекает при гашении паром при повышенном давлении в закрытых барабанах.
В зависимости от скорости гашения различают строительную негашеную известь: быстрогасящуюся со скоростью гашения не более 8 мин; среднегасящуюся со скоростью гашения до 25 мин и медленногасящуюся со скоростью гашения не менее 25 мин.
Содержание активных CaO + MgO для гидратной извести должно быть не менее 70%, а влажность — не более 4%.
Гашение извести в пушонку производят в специальных машинах — гидраторах. Для гашения извести-кипелки в известковое тесто применяют известегаситель ЮЗ, в котором комовая известь одновременно размалывается, перемешивается с водой до образования известкового молока и сливается в сепараторотстойник. После отстаивания известкового молока образуется известковое тесто. Нельзя применять известковое тесто с боль-
— 137 —
шим содержанием непогасившихся зерен извести, так как гашение этих зерен может произойти в кладке, что приведет к растрескиванию затвердевшего известкового раствора. Измельчение извести в гасителе ЮЗ способствует практически полному гашению извести, тогда как в других машинах количество непогасившихся зерен (отходов) может достигать 30%.
Твердение извести может происходить только в воздушносухих условиях. Испарение воды (что имеет место при этом) вызывает слипание мельчайших частиц Са(ОН)2 в более крупные и их кристаллизацию. Кристаллы Са(ОН)2 срастаются друг с другом, образуя каркас, окружающий частицы песка. Наряду с этим происходит карбонизация гидрата оксида кальция за счет поглощения углекислоты воздуха по реакции
Са (ОН) 2 + СО2 + пН2О = СаСО3 + (п + 1) Н2О
Таким образом, твердение известковых растворов есть следствие их высыхания и образования кристаллического сростка Са(ОН)2, а также процесса образования углекислого кальция на поверхности изделия. Твердеет гашеная известь медленно, и прочность известковых растворов невысокая. Это объясняется тем, что кристаллизация гидрата оксида кальция происходит не интенсивно и кристаллы слабо связаны друг с другом. Кроме того, образовавшаяся на поверхности корка СаСО3 препятствует прониканию воздуха внутрь известкового раствора и тормозит дальнейшее развитие процесса карбонизации. Гидрат оксида кальция кристаллизуется тем быстрее, чем интенсивнее испаряется вода, поэтому для твердения извести необходима положительная температура.
Воздушную известь широко применяют для приготовления строительных растворов в производстве известково-пуццолано- вых вяжущих, для изготовления искусственных каменных материалов — силикатного кирпича, силикатных и пеносиликатных изделий, шлакобетонных блоков, а также в качестве покрасочных составов.
Транспортируют комовую известь навалом, защищая от увлажнения и загрязнения, а молотую — в специальных бумажных мешках или металлических закрытых контейнерах. Известковое тесто перевозят в специально для этого приспособленных кузовах самосвалов. Известь негашеная должна храниться в закрытых складах, защищенных от попадания влаги. Гидратную известь можно хранить непродолжительное время в мешках и сухих складах. Молотую известь не следует хранить более 30 сут, так как она постепенно гасится влагой воздуха и теряет активность.
§ 5.8. Экономика производства извести
Себестоимость 1 т строительной комовой извести около 18,5 руб/т, т. е. существенно выше среднеотраслевых издержек производства цемента. Причиной такого положения являются не-
— 138 —
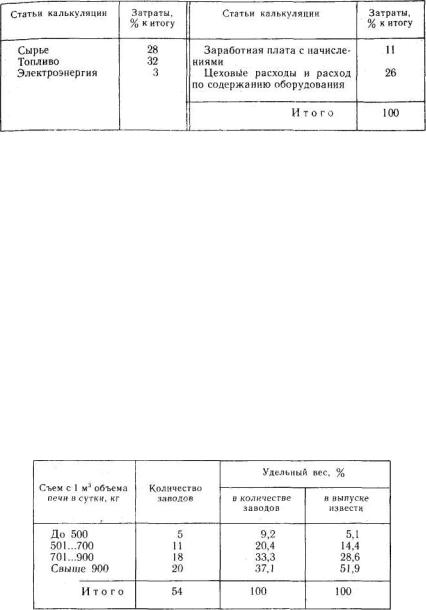
достаточно высокий технический уровень производства извести, слабая концентрация производства, повышенные издержки на сырье и топливо (табл. 5.5).
Таблица 5.5. Структура цеховой себестоимости комовой извести
Колебания в уровне себестоимости извести велики. Так, по Белгородскому заводу себестоимость извести в 2...2,5 раза ниже, чем по другим заводам.
Решающим образом на себестоимость извести влияет средняя мощность предприятия. На мелких, технически слабо оснащенных предприятиях выпускается более половины всей продукции. При этом себестоимость на мелких заводах со среднегодовой мощностью до 10 тыс. т почти в 2 раза выше, чем на крупных предприятиях. Следовательно, экономически целесообразно строительство цехов извести большей мощности по новым типовым проектам с применением более совершенных конструкций извест- ково-обжигательных печей.
Производство извести на предприятиях по изготовлению силикатных изделий осуществляется в основном в шахтных и вращающихся печах. Среднегодовое время работы шахтных печей в целом по СССР колеблется в очень широких пределах — от
187 до 346 сут.
Характеристика работы печей по величине съема продукции приведена в табл. 5.6.
Таблица 5.6. Группировка заводов по съему извести с
1 м3 объема шахтных печей
— 139 —
Улучшение работы шахтных печей по съемам и использованию их во времени даст возможность на 10...12% увеличить выпуск товарной извести и снизить ее себестоимость. Свыше 25% себестоимости извести составляют материальные затраты, среди которых особенно велики затраты на сырье. Исследования ВНИИСтрома показали, что эти затраты на предприятиях, работающих на собственном сырье, в 2,5 раза меньше, чем на предприятиях, получающих известняк со стороны. Привозной известняк в большинстве случаев является нефракционированным, что вынуждает организовать дробление и сортировку.
Осуществление концентрации карьерного хозяйства и комплексной механизации работ на карьерах позволяет снизить себестоимость камня на 30...40% и расходы на его транспортировку. Упорядочение карьерного хозяйства и снабжение известковообжигательных цехов силикатных заводов позволит снизить цеховую себестоимость извести на 7...8%.
Затраты на топлива также являются весьма значительными в себестоимости извести. Перевод предприятий на газообразное топливо не только удешевляет продукцию (1,5...2 руб/т), но и улучшает качество извести. Важное условие сокращения расхода топлива и улучшения качества извести — обеспечение оптимального режима сжигания топлива в печи.
Предприятия известковой промышленности характеризуются невысоким уровнем механизации труда (З0...60%), поэтому важнейшей задачей является механизация погрузочно-разгрузочных работ и транспортирование известняка и топлива к печам.
Осуществление мероприятий по снижению себестоимости обжига извести, организация снабжения заводов фракционированным известняком и углем, механизация трудоемких работ и улучшение организации труда позволяют снизить себестоимость извести на действующих предприятиях не менее чем на 20...25%.
В 1985 г. в СССР было произведено 9,4 млн. т строительной извести. В ближайшей перспективе будет увеличено производство извести, существенно повышена степень концентрации и техническая оснащенность производства на базе строительства специализированных известковых заводов годовой мощностью З00 тыс. т и более; постепенно осуществлена ликвидация мелких и нерентабельных предприятий и цехов, оснащенных устаревшими типами печей; созданы крупные специализированные карьеры, обеспечивающие известковые заводы фракционированным известняком; повышено качество и расширен ассортимент известковых вяжущих. Важнейшей задачей наращивания мощностей при этом является строительство новых высокомеханизированных предприятий с эффективными обжиговыми агрегатами.