
Методичка по строй мату 1
.pdf
ных печей и сливу его в отвал составляют в настоящее время в среднем 25...30 коп. на 1 т шлака, тогда как себестоимость 1 т гранулированного шлака — 50...60 коп.
Применение в строительстве шлаковой пемзы в качестве пористого заполнителя с малой плотностью, мелкопористой структурой и сравнительно высокой прочностью позволяет снизить стоимость наружных стеновых конструкций по сравнению с кирпичными на 20...25% и сократить в 2...3 раза удельные капитальные вложения на организацию производства искусственных легких заполнителей.
Производство минераловатных изделий из шлакового расплава намного выгоднее изготовления из карбонатного сырья. Удельные капитальные вложения на производство минераловатных теплоизоляционных материалов из металлургических шлаков составляют с привязкой 12... 14 руб/м3 изделий, а из горных пород — на 15...20% больше (при равной мощности цеха).
Производство строительных материалов на основе шлаковых расплавов увеличивается значительными темпами. При выпуске минераловатных изделий намечено значительно повысить качество изделий и расширить их номенклатуру. Главное направление реконструкции предприятий минеральной ваты — переход на выпуск более качественных изделий на синтетической связке.
В целом эффективность материалов на основе шлаковых расплавов характеризуется перспективными данными НИИЭС Госстроя СССР (табл. 4.1).
Таблица 4.1. Экономический эффект применения шлаковых материалов и изделий
Высокие эксплуатационные качества изделий из каменного литья обеспечивают им все более широкое применение в различных отраслях промышленности и строительства.
В стекольной промышленности СССР предусмотрено освоить производство новых высокоэффективных видов строительного
- 121 -
стекла, в частности намечено выпустить закаленное строительное стекло по непрерывной технологии. Возрастает производство высокоэффективного светотеплозащитного стекла самых различных цветовых оттенков, расширяется выпуск стеклокристаллических плиток и стекла «мороз» для отделки и др. Предусмотрено создание технологии по производству упрочненного листового стекла непосредственно при его формовании. Это исключает такие технологические операции, как резка стекла на заготовки и нагрев при закалке стекла. Начат выпуск герметичных стеклопакетов размером 2×3,3 м, в том числе стеклопакетов с солнцезащитными стеклами, защищающими помещение от шума, пыли и солнца.

ГЛАВА 5 МИНЕРАЛЬНЫЕВЯЖУЩИЕВЕЩЕСТВА
Минеральными вяжущими веществами называют тонкоизмельченные порошки, образующие при смешивании с водой пластичное тесто, под влиянием физико-химических процессов переходящее в камневидное состояние. Это свойство вяжущих веществ используют для приготовления на их основе растворов, бетонов, безобжиговых искусственных каменных материалов и изделий. Различают минеральные вяжущие вещества воздушные и гидравлические.
Воздушные вяжущие вещества твердеют, долго сохраняют и повышают свою прочность только на воздухе. К воздушным вяжущим веществам относятся гипсовые и магнезиальные вяжу щие, воздушная известь и кислотоупорный цемент.
Гидравлическиевяжущиевеществаспособнытвердетьидли тельно сохранять свою прочность не только на воздухе, но и в воде. В группу гидравлических вяжущих входят портландце мент и его разновидности, пуццолановые и шлаковые вяжущие, глиноземистый и расширяющиеся цементы, гидравлическая из весть. Их используют как в надземных, так и в подземных и под водных конструкциях.
Наряду с этим различают вяжущие вещества, эффективно твердеющие только при автоклавной обработке — давлении насыщенного пара 0,8...1,2 МПа и температуре 170...200°С. В группу вяжущих веществ автоклавного твердения входят известковокремнеземистые и известково-нефелиновые вяжущие.
5.А. ВОЗДУШНЫЕ ВЯЖУЩИЕ ВЕЩЕСТВА §
5.1.Гипсовые вяжущие вещества
Гипсовые вяжущие вещества делят на две группы: низкообжиговые и высокообжиговые.
Низкообжиговые гипсовые вяжущие вещества получают при нагревании двухводного гипса CaSO4·H2O до температуры 150...160°С с частичной дегидратацией двуводного гипса и пере водом его в полуводный гипс CaSO4·0,5H2O.
Высокообжиговые (ангидритовые) вяжущие получают обжи гом двуводного гипса при более высокой температуре до 700...
1000°С с полной потерей химически связанной воды и образова нием безводного сульфата кальция — ангидрита CaSO4. К низко обжиговым относится строительный, формовочный и высокопроч ный гипс, а к высокообжиговым — ангидритовый цемент и эстрих-гипс.
— 123 —
Сырьем для производства гипсовых вяжущих служат природный гипсовый камень и природный ангидрид CaSO4, а также отходы химической промышленности, содержащие двуводный или безводный сернокислый кальций, например фосфогипс. Возможно применение гипсосодержащего природного сырья в виде сажи и глиногипса.
Гипсовым вяжущим называют воздушное вяжущее вещество, состоящее преимущественно из полуводного гипса и получаемое
путем тепловой обработки гипсового камня при температуре
150...160°С. При этом двуводный гипс CaSO4·2H2O, содержащийся в гипсовом камне, дегидратирует по уравнению
CaSO4 · 2Н2О= CaSO4 · 0,5Н2О+ 1,5Н2О
В этих условиях образуются мелкие кристаллы полуводного сернокислого кальция β-модификации; такой гипс обладает повышенной водопотребностью (60...65% воды). Избыточная вода, т. е. сверхпотребная на гидратацию гипса (15%), испаряется, образуя поры, вследствие чего затвердевший гипс имеет высокую пористость (до 40%) и соответственно небольшую прочность.
Производство гипса складывается из дробления, помола и тепловой обработки (дегидратации) гипсового камня. Имеется несколько технологических схем производства гипсового вяжущего: в одних помол предшествует обжигу, в других помол производится после обжига, а в третьих помол и обжиг совмещаются в одном аппарате. Последний способ получил название обжига гипса во взвешенном состоянии. Тепловую обработку гипсового камня производят в варочных котлах, сушильных барабанах, шахтных или других мельницах.
Наиболее распространена схема производства гипсового вяжущего с применением варочных котлов (рис. 5.1). Гипсовый камень, поступающий на завод в крупных кусках, сначала дробят, затем измельчают в мельнице, одновременно подсушивая его. В порошкообразном виде камень направляют в варочный котел периодического или в установку непрерывного действия. Последняя имеет в 2...3 раза выше производительность, но еще находится в стадии практического освоения.
Варочный котел периодического действия (рис. 5.2) представляет собой обмурованный кирпичом стальной котел 4 со сферическим днищем 1, обращенным выпуклой стороной внутрь цилиндра. Для перемешивания гипса в котле имеется мешалка 2, приводимая в движение электродвигателем 3. Раскаленные топочные газы обогревают днище и стенки котла, а также проходят через жаровые трубы 5 внутри котла и в охлажденном состоянии удаляются по дымовой трубе. Продолжительность варки 90...
180 мин. При варке в котле гипс не соприкасается с топочными газами, что позволяет получать чистую продукцию, не загрязненную золой топлива.
Гипсовое вяжущее в сушильных барабанах получают путем обжига гипсового камня в виде щебня размером до 20 мм.
— 124 —

Рис. 5.1. Технологическая схема производства строительного гипса с. применением варочных котлов: 1— мостовой грейферный кран;
2 — бункер гипсового камня; 3 — лотковый питатель;
4 — щековая дробилка; 5 — ленточные транспортеры; 6 — бункер гипсового щебня; 7 — тарельчатый питатель; 8 — шахтная мельница; 9 — сдвоенный циклон; 10 — батарея
циклонов; 11 — вентилятор; 12 — рукавные фильтры; 13 — пылеосадительная камера; 14— шнеки; 15 — бункер сырого молотого гипса; 16 — камера томления; 17 — гипсо-
варочный котел; 18 — элеватор; 19 — бункер готового гипса; 20 — скребковый транспортер
Рис. 5.2. Варочный котел для изготовления строительного гипса: 1 —
днище; 2 — смеситель; 3 — электродвигатель; 4 — котел; 5 — жаровые трубы; б — выгрузочный желоб
Обжиговой частью сушильного барабана служит наклонный стальной цилиндр диаметром до 2,5 м и длиной до 20 м, установленный на роликовых опорах и непрерывно вращающийся. Гипсовый щебень подается в барабан с приподнятой стороны и в
— 125 —
результате вращения наклонного барабана перемещается в сторону наклона. Из топки в барабан поступают раскаленные дымовые газы, которые при движении вдоль барабана обжигают гипсовый камень, а с противоположной стороны удаляются вентилятором. Далее гипсовый камень измельчают в мельницах.
При обжиге гипса во взвешенном состоянии совмещают две операции: измельчение и обжиг. В мельницу (шахтную, шаровую или роликовую) подают гипсовый щебень и одновременно нагнетают горячие дымовые газы. Образующиеся при размоле мельчайшие зерна гипса товарной фракции увлекаются из мельницы потоком дымовых газов и в процессе транспортирования в раскаленном газовом потоке обжигаются. Пылевоздушная смесь поступает в циклоны и фильтры для осаждения гипса. Наибольшую производительность из рассмотренных схем имеет последняя, затем схема обжига в сушильных барабанах и, наконец, в варочных котлах. Однако первые две схемы существенно уступают по качеству продукции схеме с варкой гипса.
При затворении порошка гипса водой полуводный сернокислый кальций CaSO4·0,5H2O, содержащийся в нем, начинает растворяться до образования насыщенного раствора и одновременно гидратироваться, присоединяя 1,5 молекулы воды и переходя в двугидрат CaSO4-2H2O по уравнению
CaSO4 · 0,5Н2О+ 1,5Н2О= CaSO4 · 2Н2О
Растворимость двугидрата примерно в 5 раз меньше растворимости исходного порошка — полугидрата CaSO4·0,5H2O. В результате образовавшийся насыщенный раствор полугидрата оказывается пересыщенным по отношению к двугидрату. Пересыщенный раствор в обычных условиях не может существовать — из него выделяются мельчайшие частицы твердого вещества — двуводного сернокислого кальция. По мере накопления этих частиц они склеиваются между собой, вызывая загустевание (схватывание) теста. Затем мельчайшие частицы гидрата начинают кристаллизоваться, определяя этим образование прочного гипсового камня. Дальнейшее увеличение прочности гипса происходит вследствие высыхания твердеющей массы и более полной кристаллизации при этом. Твердение гипса можно ускорить сушкой, но при температуре не выше 65 °С во избежание обратной дегидратации двуводного гипса.
Быстрое схватывание гипса затрудняет в ряде случаев его использование и вызывает необходимость применения замедлителей схватывания (кератинового, известково-кератинового клея, сульфитно-дрожжевой бражки в количестве 0,1...0,3% от массы гипса). Замедлители схватывания уменьшают скорость растворения полуводного гипса и замедляют диффузионные процессы. При необходимости ускорить схватывание гипса к нему добавляют двуводный гипс, поваренную соль, серную кислоту. Одни из них повышают растворимость полуводного гипса, другие (дву-
— 126 —
водный гипс) образуют центры кристаллизации, вокруг которых быстро закристаллизовывается вся масса.
Применяется гипсовое вяжущее для производства гипсовых и гипсобетонных строительных изделий для внутренних частей зданий (перегородочных плит, панелей, сухой штукатурки, приготовления гипсовых и смешанных растворов, производства декоративных и отделочных материалов, например искусственного мрамора), а также для производства гипсоцементно-пуццолано- вых вяжущих.
Высокопрочный гипс является разновидностью полуводного гипса. Этот полуводный гипс α-модификации, который имеет бо лее крупные кристаллы, обусловливающие меньшую водопотребность гипса (40...45% воды), позволяет получать гипсовый ка мень с большей плотностью и прочностью. Получают его путем нагревания природного гипса паром под давлением 0,2...0,3 МПа с последующей сушкой при температуре 160...180°С. Прочность его за 7 сут достигает 15...40 МПа. Высокопрочный гипс выпус кают пока в небольшом количестве и применяют в основном в металлургической промышленности для изготовления форм. Од нако он успешно может заменить обыкновенное гипсовое вяжу щее, обеспечив изделиям высокую прочность.
Формовочный гипс состоит в основном из кристаллов β-мо-
дификации и незначительного количества примесей. Онобладает
повышенной водопотребностью, а будучи затвердевшим, имеет высокую пористость. Это свойство формовочного гипса успешно используется в керамической и фарфорофаянсовой промышлен ности для изготовления форм.
§ 5.2. Свойства и применение низкообжиговых гипсовых вяжущих веществ
Основнымихарактеристиками гипсовыхвяжущихявляются сроки схватывания, тонкость помола, прочность при сжатии и растяжении, водопотребность и др.
Гипсовое вяжущее является быстросхватывающим и быстротвердеющим вяжущим веществом. По срокам схватывания ГОСТ 125—79 предусматривает выпуск вяжущих: быстротвердеющего (индекс А) с началом схватывания не ранее 2 мин, концом — не позднее 15 мин; нормальнотвердеющего (индекс Б) с началом схватывания не ранее 6 мин, концом — не позднее 30 мин; медленнотвердеющего (индекс Б) с началом схватывания не ранее 20 мин, конец схватывания не нормируется.
В зависимости от степени помола различают вяжущие грубого, среднего и тонкого помола с максимальным остатком на сите с размером ячеек в свету 0,2 мм не более 23, 14 и 2% (обозначаемые соответственно индексами I, II и I I I ) .
Марку гипсовых вяжущих характеризуют по прочности при сжатии образцов-балочек 40×40×160 мм в возрасте 2 ч после затворения водой. Минимальный предел прочности каждой марки
— 127 —
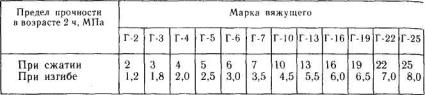
должен соответствовать значениям, приведенным в табл. 5.1. Четкое индексирование различных сортов гипсовых вяжущих позволяет давать большой объем информации в сокращенной форме. Например, гипсовое вяжущее с прочностью при сжатии 5,2 МПа, началом схватывания 5 мин, концом схватывания 9 мин и остатком на сите 0,2 мм 9%, т. е. вяжущее марки Г-5, быстротвердеющее, среднего помола, может быть записано в виде сокращенного обозначения Г-5АП.
Таблица 5.1. Применяемые значения предела прочности каждой марки гипсового вяжущего
Чтобы получить гипсовое удобоукладываемое тесто, необходимо взять 60...80% воды от массы вяжущего, а на химическую реакцию гидратации требуется лишь 18,6% воды. Избыток ее остается в порах, затем испаряется, поэтому получившийся в результате твердения полуводного гипса гипсовый камень обладает высокой пористостью, достигающей 40...60% и более. Чем больше воды затворения, тем выше пористость камня, а прочность его соответственно меньше. Прочность гипсовых образцов, высушенных при температуре до 60°С, в 2...2,5 раза выше прочности влажных образцов после 1,5 ч твердения. Лучшие сорта гипса после сушки имеют прочность при сжатии 18...20 МПа, а прочность при растяжении в 6...8 раз меньше.
При твердении гипс расширяется в объеме до 1%, благодаря чему гипсовые отливки хорошо заполняют форму и передают ее очертания. При его высыхании трещин не образуется, что позволяет применять гипсовое вяжущее без заполнителей.
Гипсовое вяжущее в воде снижает свою прочность вследствие растворения двугидрата и разрушения кристаллического сростка. Водостойкость его может быть повышена введением небольших количеств гидрофобных веществ (олеиновой кислоты и др.), добавкой молотого гранулированного шлака, извести, портландцемента.
Наряду с гипсовыми вяжущими общестроительного назначения выпускаются вяжущие для фарфорофаянсовой и керамической промышленности, к которым предъявляется ряд дополнительных требований: объемное расширение — не более 0,15%, примесей, нерастворимых в НСl, — не более 1%, водопоглощение — не менее 30%.
Гипсовые вяжущие применяют при производстве гипсовой штукатурки, перегородочных стеновых плит и панелей, вентиля-
— 128 —
ционных коробов и других деталей в зданиях и сооружениях, работающих при относительной влажности воздуха не выше 65%. Изделия из них обладают небольшой плотностью, несгораемостью и рядом других ценных свойств, но при увлажнении прочность их снижается.
Для гипсовых строительных изделий всех видов рекомендуются марки Г-2...Г-7 всех сроков твердения и степеней помола; для тонкостенных строительных изделий и декоративных деталей может использоваться гипс тех же марок, но только тонкого и среднего помола, быстрого и нормального твердения. При штукатурных работах и заделке швов применяют марки Г-2...Г-25 нормального и медленного твердения. Гипс марок Г-5...Г-25 нормального и медленного твердения. Гипс марок Г-5...Г-25 тонкого помола с нормальными сроками твердения служит для изготовления форм и моделей в керамической, машиностроительной промышленности, а также в медицине.
§ 5.3. Ангидритовые вяжущие вещества
Ангидритовое вяжущее получают обжигом природного двуводного гипса при температуре 600...700°С с последующим его измельчением с добавками — катализаторами твердения (изве стью, смесью сульфата натрия с медным или железным купоро сом, обожженным доломитом, основным доменным гранулиро ванным шлаком и др.). Ангидритовое вяжущее можно получить также путем помола природного ангидрита с указанными выше добавками.
Ангидритовое вяжущее было предложено П. П. Будниковым следующего состава: известь — 2...5%; смесь бисульфата или сульфата натрия с железным или медным купоросом — по 0,5...
1% каждого; доломит, обожженный при 800...900°С,— 3...8%, основной гранулированный доменный шлак — 10...15%. Железный и медный купоросы уплотняют поверхность затвердевшего ангидритового цемента, вследствие чего катализаторы не выделяются и не образуют выцветы на поверхности изделия. Действие катализаторов объясняется тем, что ангидрит обладает способностью образовывать комплексные соединения с различными солями в воде неустойчивого сложного гидрата, который затем распадается, образуя CaSO4·2H2O.
Ангидритовый цемент — это медленно схватывающееся вяжущее вещество с началом схватывания не ранее 30 мин, концом — не позднее 24 ч. Марки ангидритового цемента по прочности при сжатии М50, 100, 150 и 200. Применяют ангидритовые цементы для приготовления кладочных и отделочных растворов, бетонов, производства теплоизоляционных материалов, искусственного мрамора и других декоративных изделий.
Высокообжиговый гипс (эстрих-гипс) является разновидно стью ангидритовых цементов. Его получают обжигом природного гипса или ангидрита при температуре 800... 1000°С с последую-
5-707 |
— 129 — |

щим тонким измельчением. При этом происходит не только полное обезвоживание, но и частичная диссоциация (разложение) ангидрита с образованием СаО (в количестве 3...5%) по реакции CaSO4 — СаО + SO3. При затворении водой СаО действует как катализатор по схеме твердения ангидритового цемента, рассмотренной выше. Высокообжиговый гипс медленно схватывается и твердеет, но водостойкость и прочность при сжатии (10...
20 МПа) позволяют успешно использовать его при устройстве мозаичных полов, изготовлении искусственного мрамора и др. Изделия из высокообжигового гипса мало-, тепло- и звукопроводны, они обладают по сравнению с изделиями из гипсового вяжущего более высокой морозостойкостью, повышенной водостойкостью и меньшей склонностью к пластическим деформациям.
§ 5.4. Экономика производства гипсовых вяжущих веществ
Производство гипсовых вяжущих веществ с каждым годом увеличивается.
Себестоимость товарного гипса составляет в среднем около 12 руб. за 1 т и существенно колеблется на различных заводах. При этом решающим фактором является степень концентрации производства: на более крупных и технически оснащенных пред- приятиях со среднегодовой мощностью более 100 тыс. т себестоимость гипса почти в 2 раза ниже, чем на мелких (табл. 5.2).
Таблица 5.2. Группировка гипсовых предприятий по себестоимости
Как видно из табл. 5.2, около 40% гипса выпускают предприятия среднегодовой мощности до 100 тыс. т. Большие колебания себестоимости (в 2...4 раза) свидетельствуют о значительных резервах ее снижения.
В табл. 5.3 приведена структура себестоимости гипса по отдельным заводам.
Обращает на себя внимание высокий удельный вес затрат на сырье и вспомогательные материалы (33,0...53,9%) и на заработную плату с начислениями (23,6...36,8%).
Себестоимость гипса заводов, работающих на привозном сырье, по данным ВНИИСтрома, примерно в 1,5 раза превышает уровень себестоимости гипса заводов, работающих на собствен-
— 130 —