
ДиагнЦв
.pdf
61
Принцип "половинного разбиения" обычно используют в тех случаях, когда отсутствует информация о вероятностях появления дефектов Pi и трудоёмкостях (времени) проведения проверок Tj. или они имеют примерно одинаковые значения.
Систему каждый раз разбивают на два участка, содержащих примерно одинаковое число элементов, один из которых подвергают проверке.
Для определения числа разбиений (проверок), необходимых для выявления дефекта, систему, содержащую N - элементов, представляют в виде:
N = 2m + R,
где R - число элементов сверх полной степени числа 2; m - целое положительное число.
Вслучае R = 0 необходимое число проверок составит К = m
Вслучае R > 0 число проверок составит К = m + 1.
Принцип "равных вероятностей" обычно используют при различных значенияхPi и |
||||||
примерно одинаковых значениях Tj. |
|
|
|
|
|
|
На каждом шаге разбиения системы на участкистремятся к обеспечению равенства сумм |
||||||
|
|
|
||||
вероятностей отказов структурных элементо,в входящих в состав образующихся участков, т.е. к |
||||||
выполнению условия |
|
|
|
|
|
|
|
|
|
|
|
|
|
|
n |
N |
N |
|
|
|
|
åPi = å Pi, |
при этом å Pi = 1. |
|
|
|
|
|
i=1 |
n+1 |
i=1 |
|
|
|
|
|
|
|
|
|
|
Реализация данного принципа позволяет уменьшить число проверок, необходимых для выявления дефекта, в особенности при наличии существенных различий в значениях Pi.
Принцип "минимальной |
продолжительности" обычно |
используют |
при |
|
существенных различиях в значениях Pi и Tj. |
|
|
|
|
Сокращение времени поиска при этом достигается за счет дополнительного учета значений Tj. |
||||
При выборе очередного проверяемого |
участка рассчитывают значение |
показателяe |
= Pi / |
Tj. |
|
|
i |
|
|
Первоочередной проверке подвергают участок, для которого величинаei имеет
наибольшее значение.
Принцип "максимума информации" обычно используют при наличииинформации о значениях Pi и Tj. для объектов, содержащих большое число функционально взаимосвязанных элементов.
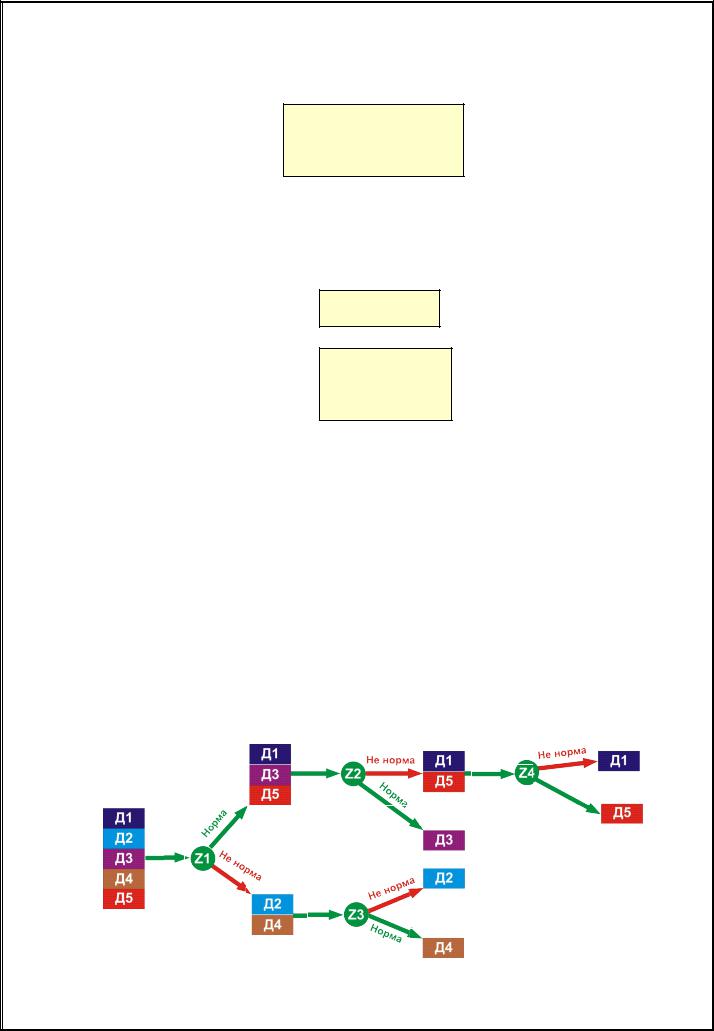
62
Вобщем случае неопределенность состояния (энтропию) объекта, состоящего из N
-элементов, определяют по формуле:
N
H (N) = - å Pi × log Pi. i=1
Каждая проверка Zj несет некоторое количество информации I (Zj) о состоянии объекта, в силу чего его энтропия уменьшается.
Критерием достаточности информации для определения технического состояния
объекта (выявления дефекта) служит условие:
I (K) = H (N),
K
где I (K) = å I (Zj); j=1
K - число проверок.
Если при проверке одновременно проверяется n - элементов, сумма вероятностей отказов которых составляет
n
P (Zj) = å Pi, i=1
то количество получаемой информации составит
I (Zj) = - [P (Zj) × log P (Zj) + (1 – P (Zj)) × log (1- P (Zj))].
Поиск отказавшего элементаDi начинают с проверкиZj, несущей максимум информации о состоянии системы.
При проверке функциональной системы разбивают её элементы на две подгруппы:
1)на изменение состояния которых подгруппа реагирует - «Норма»;
2)на изменение состояния которых подгруппа не реагирует - «Не норма».
Рис. 15.2.1. Алгоритм поиска неисправностей (дефектов) системы
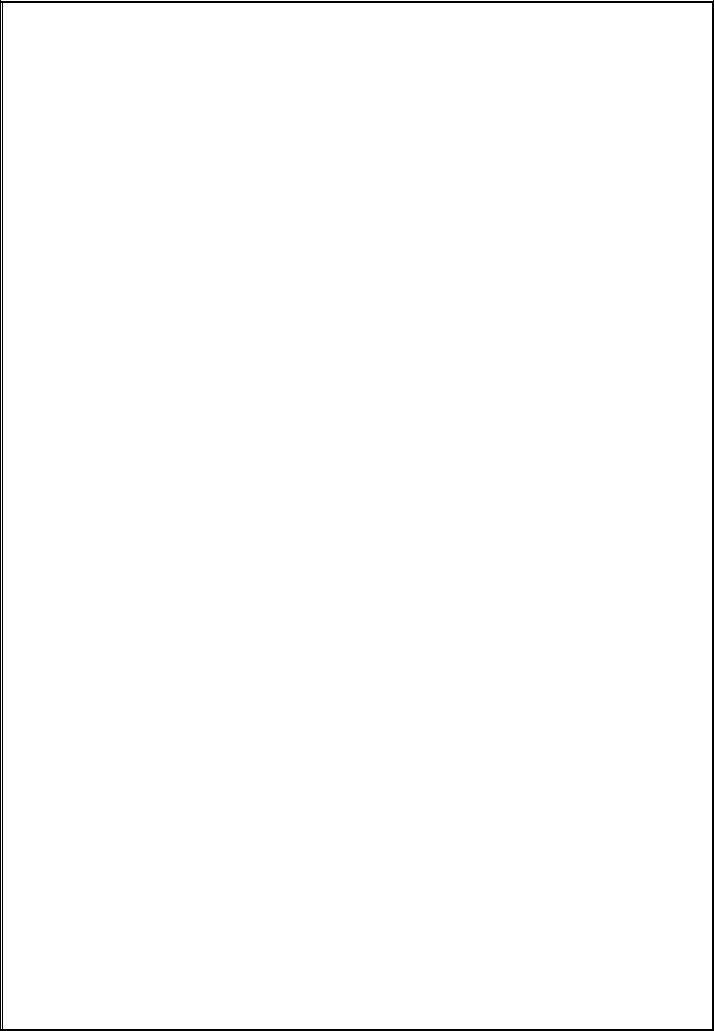
63
Вторую проверку выбирают по максимуму информации для образовавшихся подгрупп элементов и т.д.
Разбиение системы на подгруппы продолжают до момента отыскания отказавшего элемента.
Алгоритм поиска в этом случае представляют в виде ориентированного графа (рис.2.20).
Взаимосвязь между результатами проверок и состояниями системы обычно представляют в виде диагностической матрицы:
|
Di |
|
Z1 |
Z2 |
|
|
|
Pi |
|
|
D1 |
|
0 |
1 |
|
|
|
P1 |
|
|
D2 |
|
1 |
0 |
|
|
|
P2 |
|
|
|
|
|
|
|
|
|
|
|
|
I (Zi) |
I (Z1) |
I (Z2) |
|
|
|
å Pi |
|
|
|
|
|
|
|
|
|
|
=1 |
|
С использованием матрицы проводят минимизацию числа измеряемых параметров (проверок) и |
|||||||||
выбор очерёдности их проведения. |
|
|
|
|
|
|
|||
При этом проверки, |
реагирующие на все |
и не реагирующие ни на о |
|||||||
неисправность из алгоритма исключают. |
|
|
|
||||||
Из двух проверок, дающих одинаковые результаты, оставляют простейшую. |
Контрольные вопросы по разделу 15.0...15.2
1.Что считается ДЕФЕКТОМ при проведении технической диагностики?
2.Что является результатом технической диагностики при поиске дефектов?
3.Что служит основной характеристикой технической диагностики при поиске дефектов?
4.Чем характеризуется эффективность поиска дефектов?
5.Какие виды алгоритмов составляют в зависимости от задачи и условий технической диагностики?
6.Что такое алгоритмы поиска дефектов с жёсткой программой и с гибкой программой?
7.Что такое алгоритмы поиска дефектов с условной остановкой и с безусловной остановкой?
8.Что такое рабочие алгоритмы поиска дефектов и общие алгоритмы поиска дефектов?
9.Что предшествует составлению общего алгоритма поиска дефектов?
10.Что отражает граф причинно-следственных связей?
11.Какие алгоритмы поиска дефектов используют на практике при проведении ТОиР?
12.По каким принципам составляется очерёдность проверок при поиске дефектов?
13.Когда применяются принципы очерёдности поиска дефектов: от простого к сложному, возрастающая трудоёмкость, проверка слабых точек, минимальная трудоёмкость?
14.В чём особенность поиска дефектов функциональных систем?
15.По какому принципу составляется алгоритм поиска дефектов функциональных систем?
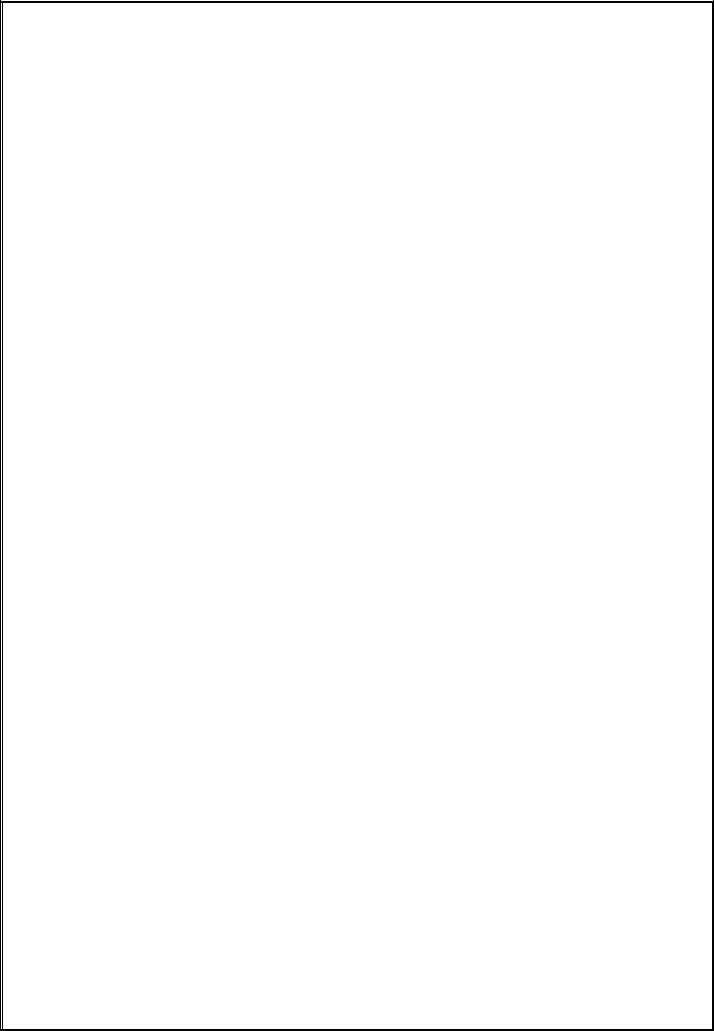
64
16.0.ОБЩАЯ ХАРАКТЕРИСТИКА СРЕДСТВ ТД
1.Бортовые средства контроля
Современные воздушные суда оснащены бортовыми средствами контроля, обеспечивающими проверку работоспособности (правильности функционирования) основных функциональных систем.
В их число входит большое число(до 150) разнообразных контрольно-измерительных и пилотажно-навигационных приборов, указателей и сигнализаторов, часть которых (до 10) может быть использована и для целей технической диагностики.
Эффективность |
технической |
диагностики |
при |
этом |
зависит |
не |
только |
от |
контролируемых параметров, диапазона и точности измерений, но и от уровня автоматизации |
||||||||
контрольно-диагностических операций. |
|
|
|
|
|
|
|
На начальных этапах развития АТдля получения и обработки диагностической информации в полете требовалось активное участие экипажа.
Качество технической диагностики при этом во многом зависело от квалификации пилотов, их умения быстро и точно регистрировать и обрабатывать показания приборов.
Следующим этапом явилось создание бортовых систем контроля, обеспечивающих:
1)автоматический сбор;
2)первичную обработку;
3)регистрацию диагностической информации с помощью бортовых самописцев(МСРП, БУР, САРПП и т.д.) для ее дальнейшего использования на земле.
Однако оперативность и точность постановки диагнозов в полете во многом зависели от квалификации экипажа.
На современном |
этапеуспешно решается задача |
полной автоматизации бортового |
|
|||||
контроля. |
|
|
|
|
|
|
|
|
Разработаны |
и |
внедрены |
бортовые |
системы |
встроенного |
контроля |
и |
ото |
диагностической информации, которые используются инженерно-техническим и лётным персоналом |
|
|||||||
для подготовки воздушного судна к полёту на ,землеа также обеспечивают диагностической |
||||||||
информацией экипаж в полёте. |
|
|
|
|
|
|
Диагностическая информация поступает к экипажу в "готовом" виде с указанием:
ðтекущих значений контролируемых параметров;
ðхарактера возникающих неисправностей;
ðрекомендаций по предупреждению возможных отказов.
Для этого в состав системы контроля введены специализированные ЭВМ, предназначенные для оперативной обработки всей полетной информации.
В настоящее времяв бортовых системах контроля ВСначали использоваться и новейшие типы контрольно-измерительных приборов(радиационные термометры,
оптические пирометры, анализаторы спектров вибраций и т.д), которые позволяют существенно увеличить объем получаемой в полёте диагностической информации, а, следовательно, повысить оперативность и точность технической диагностики.
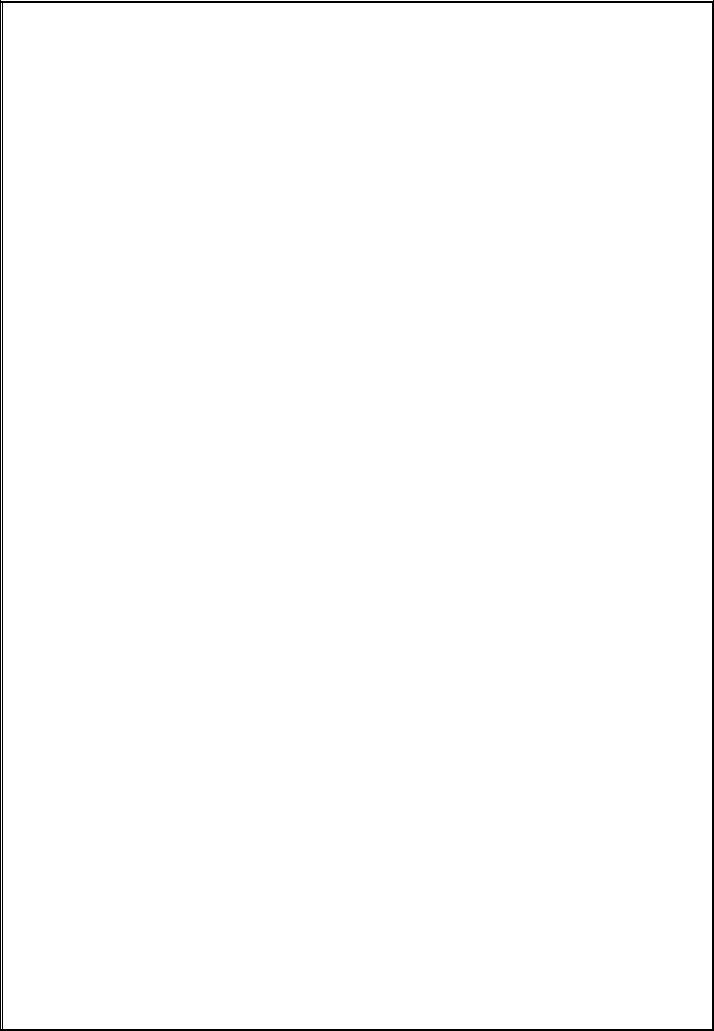
65
Успешно решается и проблема повышения достоверности технической диагностики, для чего в системах контроля предусматриваются логические устройства для комплексной обра диагностической информации.
При этом сигнал"отказ" поступает к экипажу только в тех случаях, когда |
|
информация получена по нескольким независимым каналам. |
|
С целью уменьшения числа контрольно-измерительных приборов, устанавливаемых |
на |
приборные доски ВС, широко используются многофункциональные дисплейные индикаторы, |
на |
которые выводится только та информация, которая необходима экипажу на текущий момент полёта, |
|
а также аварийная информация. |
|
Бортовые системы контроля большинства воздушных судов(Ту-154, Як-42, Ил-76, МИ-8 и др.), находящихся в эксплуатации не отвечают требованиям, предъявляемым к контролепригодности АТ.
Поэтому при технической диагностике приходится прибегать к записи и наземной обработке полетной информации, а также к использованию разнообразных средств локальной технической диагностики.
В состав бортовых средств контроля, используемых для целей технической диагностики, входят измерители:
ºчастот вращения роторов (оборотов);
ºтемпературы жидкостей и газов;
ºдавления жидкостей и газов;
ºвибрации и другие.
Все измерительные приборы работают по принципу электродистанционной передачи сигналов и содержат:
8 датчик-преобразователь неэлектрических величин в электрические сигналы; 9 согласующие устройства;
ºуказатель (индикатор).
1.Параметр "обороты" (частота вращения) обладает высокой информативностью.
Он |
позволяет |
судить |
о |
характере |
протекания |
рабочих |
процессов |
в , двиг |
|
турбохолодильниках и других агрегатах, а также о работе регуляторов, систем защиты и т.д. |
|
||||||||
Например |
|
|
|
|
|
|
|
|
|
|
º По величине оборотов |
роторов |
ГТДсудят о работе регуляторов |
и |
состоянии |
||||
|
проточной части. |
|
|
|
|
|
|
|
|
|
º По времени "выбега" (времени с момента выключения СТОП-КРАНА двигателя до |
||||||||
|
полной |
остановке |
роторов) судят |
о состоянии |
подшипников |
опор |
роторов |
приводных агрегатов.
ºПо величине "скольжения" роторов (разнице между оборотами КНД и КВД) - о
состоянии проточной части, подшипников опор, настройке регуляторов и т.д.
2.Параметр "температура" обладает высокой информативностью, так как служит основным показателем протекания тепловых процессов в двигателях, турбохолодильниках, теплообменниках и т.д.
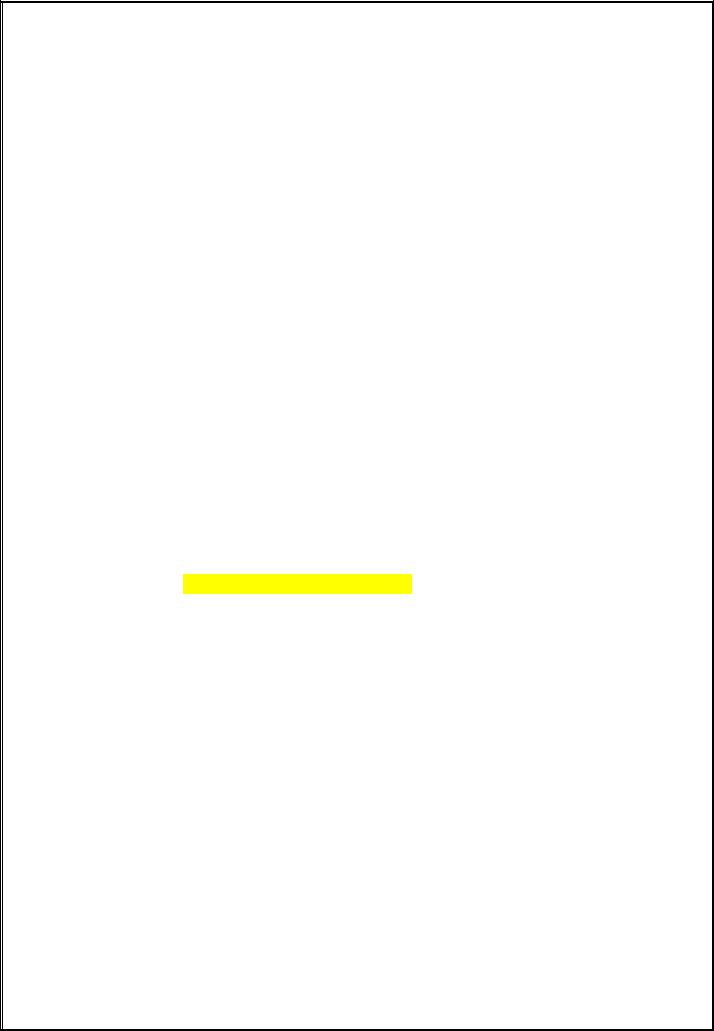
66
Например
ºПо температуре газов за (перед) турбиной ГТД судят о состоянии проточной части,
работе топливных насосов-регуляторов, камеры сгорания и форсунок;
ºпо температуре масла на входе (выходе) в двигатель судят о состоянии узлов трения,
работе масляной системы и ее агрегатов;
ºпо температуре воздуха, подаваемого в гермокабину, судят о состоянии и работе системы кондиционирования и её агрегатов и т.д.
3. При использовании |
радиационных термометров(оптических пирометров) |
имеется возможность |
измерять температуру различных элементов конструкции ГТД |
(лопаток и дисков турбин, кожухов и жаровых труб камеры сгорания и т.д.), что позволяет |
|
судить о работе систем охлаждения, регулирования, и т.д. |
4.Параметр "давление" достаточно информативен, так как позволяет судить о характере протекания рабочих процессов в гидрогазовых системах.
Например
ðпо величине давления в гидравлической системе судят о работе и состоянии насосов.
ðпо скорости изменения давления после отключения насосов- о внутренней герметичности агрегатов и зарядке азотом гидроаккумуляторов;
ðпо отношению давлений воздуха на входе и на выходе из ГТД - о величине развиваемой тяги и т.д.
5.Параметр "расход" обладает достаточно высокой информативностью, так как позволяет судить о протекании рабочих процессов ,в гидрогазовыхГТД системах, системе кондиционирования воздуха и т.д.
Например ½ по величине часового расхода топлива судят о состоянии проточной части и
работе регуляторов ГТД;
½по величине расхода воздуха в системе кондиционирования, необходимого для обеспечения заданного перепада давления судят о герметичности гермокабин и работе системы автоматического регулирования давления.
6.Параметр "вибрация" обладает высокой информативностью, так как позволяет судить о состоянии роторов и их опор, протекании рабочих процессов в компрессорах и турбинах ГТД, соосности валов трансмиссий вертолетов и т.д.
Например,
³по уровню вибрации ГТД судят о состоянии роторов компрессоров и турбин(лопаток, дисков, бандажных полок, подшипников и т.д.);
³ по |
уровню вибрации вертолета- о состоянии несущего и хвостового винта, |
|||||||||
|
трансмиссий и т.д. |
|
|
|
|
|
|
|
||
При |
использовании |
|
анализаторов |
спектра |
вибрации |
можно |
проводить |
локал |
||
неисправностей, |
т.е. определять причину повышения уровня вибрации объекта. |
|
|
|
||||||
Следует |
отметить, |
что |
большая |
часть измеряемых |
параметров, обладая |
высокой |
||||
диагностической ценностью, имеют относительно малый диагностический вес. |
|
|
|
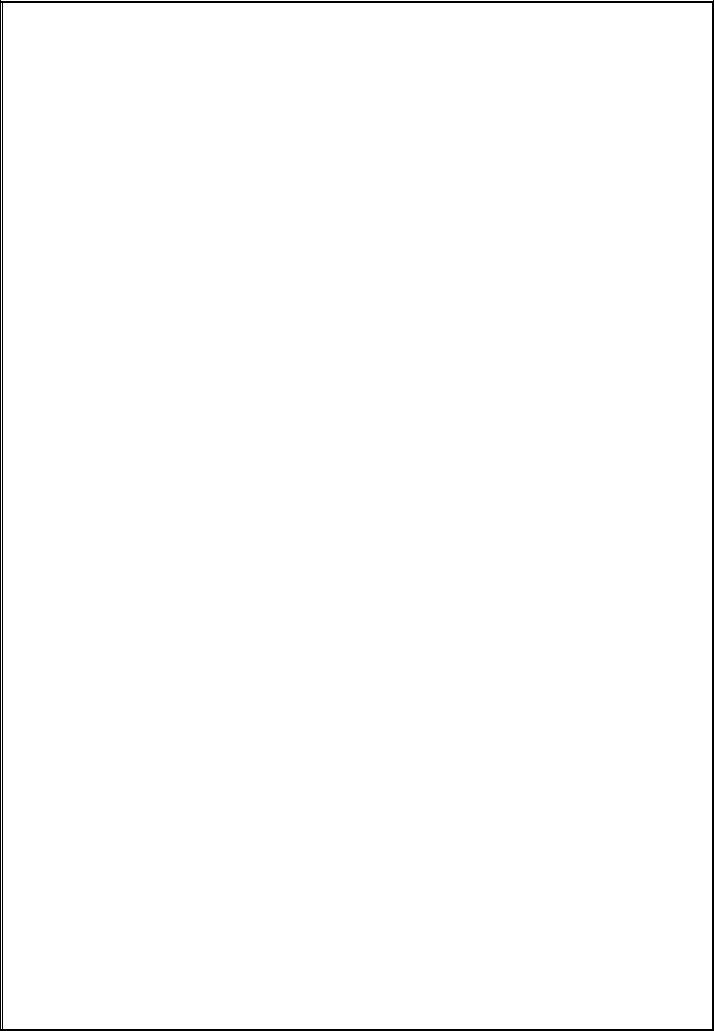
67
В силу этого они позволяют достаточно объективно судить о работоспособности объектов, но не приспособлены для распознавания причин неисправностей (дефектов).
С целью повышения глубины диагностирования прибегают к использованию специальных методов обработки диагностической информации, комплексных, обобщенных и интегральных ДП,
атакже средств локального ТД.
17.0.Средства локального технического диагностирования (ТД)
Ксредствам локального технического диагностирования относятся
1)мерительные и специальные инструменты:
Øнутромеры;
Øщупы;
Øиндикаторы;
Øтензометры;
Øдинамометрические ключи и т.д.
2)методы неразрушающего контроля:
aвизуально-оптический;
aмагнитопорошковый;
aвихретоковый;
aультразвуковой;
aкапиллярный;
aрентгенографический;
aтепловизионный
aвибрационный и другие;
3)методы, основанные на анализе рабочих жидкостей:
-дифференциально-магнитный;
-спектральный;
-рентгено-спектральный;
-колорометрический и др.
Мерительные и специальные инструменты используются при проверках |
размеров |
|
сопряженных деталей, зазоров в узлах |
трения, натяжения тросов, моментов затяжки |
резьбовых |
соединений и т.д. |
|
|
Технические характеристики и |
методики применения инструментальных средств |
|
общеизвестны. |
|
|
Методы неразрушающего контроля служат для проверки прочностных характеристик конструкций без разрушения.
При проведении проверок выявляют разнообразные дефекты конструкций:
ªв виде нарушений сплошности материала(трещины, забоины, очаги коррозии, непровары, шлаковые включения и т.д.);
ªотклонения толщины и химического состава защитных покрытий.
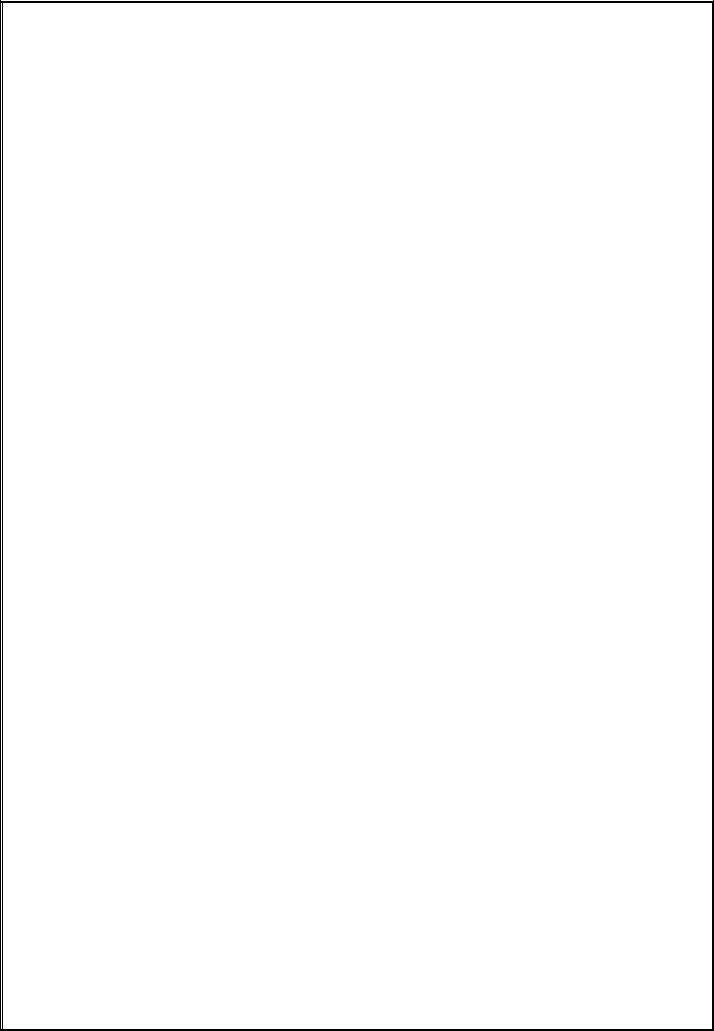
68
Выбор методов и средств неразрушающего контроля (НК) проводят с учетом:
Fхарактера и локализации ожидаемых дефектов;
Fсвойств материалов деталей и покрытий;
Fсостояния контролируемых поверхностей;
Fдоступности зон контроля;
Fтребований, предъявляемых к чувствительности, надежности и трудоемкости контроля.
Например:
для проверки барабанов колес на отсутствие усталостных трещин можно проводить использованием токовихревого и ультразвукового метода дефектоскопии.
При этом трудоемкость токовихревой проверки составляет около 3 человеко-часов и требует разборки колеса, а трудоемкость ультразвуковой проверкиоколо 0,5 человеко-часа без снятия колес с ЛА.
Всилу высокой надежности и чувствительности токовихревого контроля периодичность проверок, необходимая для обеспечения заданного уровня безотказности, составляет 150 посадок, а при проведении ультразвукового контроля - 25 посадок.
Врезультате токовихревой контроль колёс совмещают с периодическими формами ,ТОна которых проводятся плановые переборки колес, а ультразвуковой контроль проводят на оперативных формах ТО, имеющих ограниченный резерв времени.
Врезультате предпочтение обычно отдают более трудоемкому токовихревому контролю, не влияющему на величину простоя ЛА на ТО.
На сегодняшний день имеется большой арсенал методов и средств НК(дефектоскопов), отличающихся друг от друга, как по техническим возможностям, так и по источникам питания, габаритам, весу, универсальности и т.д.
Однако в практике технической диагностики АТ нашли применение только6 методов НК и около 20 типов дефектоскопов.
1.Визуально-оптический метод используется для проведения обследования проточной части ГТД на предмет выявления повреждений лопаток компрессоров и турбин, дефектов камеры сгорания, уплотнений и т.д.
При этом используют"жесткие" (линзовые) и "гибкие" (волоконные) оптические дефектоскопы (эндоскопы).
Первые (Н-200, Н-201, АС, ЭЛЖ и др.) обладают высокой чувствительностью (разрешение до 100 штр./мм), но требуют оснащения объектов специальными смотровыми лючками.
Вторые (ОД-20Э, ЭВГ, "Olympus" и др.) имеют меньшую чувствительность (разрешение до 20 штр./мм), но менее требовательны к контролепригодности объектов.
При контроле выявляют разнообразные поверхностные дефекты (забоины, трещины, очаги коррозии и т.д.) с раскрытием более 0,01 мм.
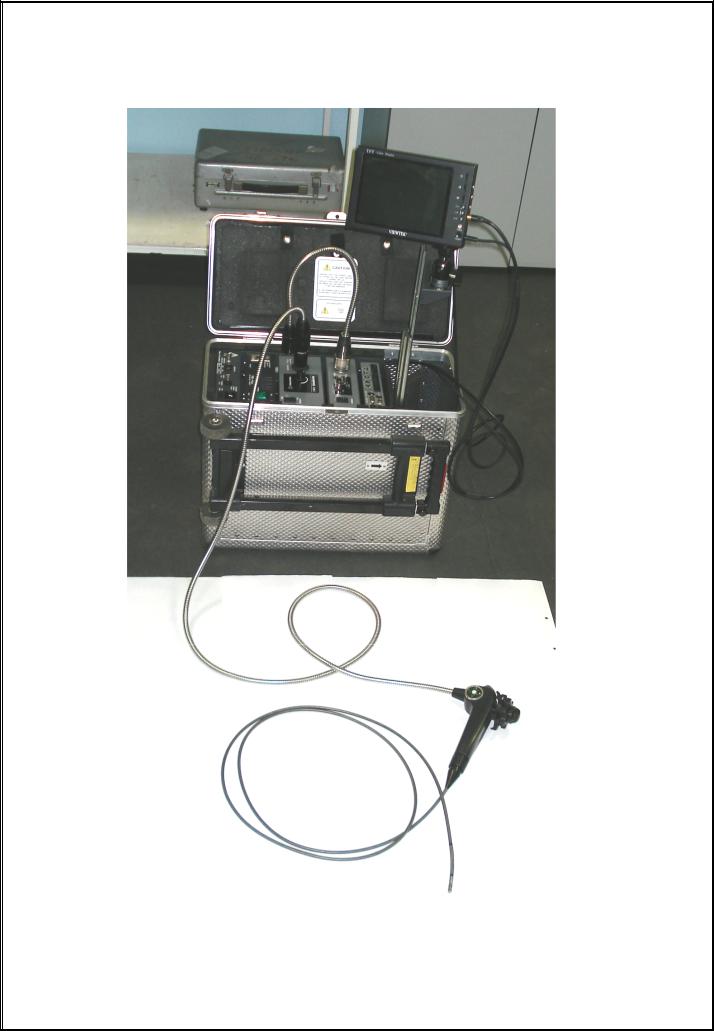
69
Рис. 17.1. Оптоволоконный эндоскоп «Олимпус»
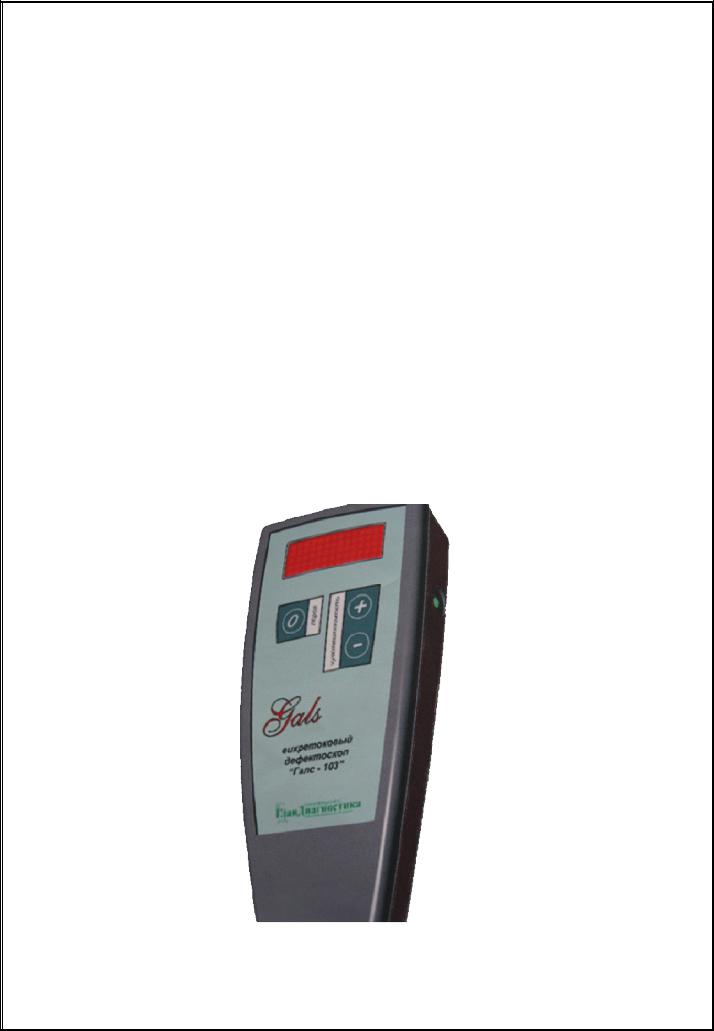
70
2.Магнитопорошковый метод используется для контроля конструкций, изготовленных из ферромагнитных материалов (силовые элементы шасси, крепежные детали планера, силовой установки и т.д.).
При этом обычно используют переносные дефектоскопы типа ПМД-70, ДМП-1 и др.
При магнитном контроле на деталях и узлах конструкций выявляют:
F усталостные |
трещины |
и |
разнообразные |
производственные |
деф |
(непровары, флокены, волосовины, шлифовочные и термические трещины и .)т.дс
раскрытием более 0,0025 мм.
3.Метод вихревых токов используется для контроля конструкций, изготовленных из токопроводящих материалов (барабаны колес, лопасти воздушных винтов, силовые элементы планера и т.д.).
При этом используют портативные дефектоскопы типа ТВД, ВД-1ГА, ВДЦ, ГАЛС-103
идр.
При токовихревом (или вихретоковом) контроле на деталях и узлах конструкцийвыявляют трещины с раскрытием более 0,01 и длиной более 1 мм, нарушения толщины покрытий
и т.д.
Рис. 17.2. Вихретоковый дефектоскоп «ГАЛС ВД-103»