
Основы технологии приборостроения (лаб.практ
.).pdf
мощью винта. Несоблюдение этого правила может привести к свертыванию патрона со шпинделя при реверсе и нанести тяжелую травму.
3.Надежно закрепить деталь.
4.Не касаться вращающихся частей станка до полной его остановки.
5.Не приближаться к зоне резания во избежание травм от отлетающей стружки.
6.Запрещается пользоваться рукояткой реверса для торможения шпинделя. Это может привести к резким толчкам и ослабить крепление патрона.
7.Запрещается начинать работу с включения высоких чисел оборотов шпинделя (2000, 1340). Предварительно необходимо прогреть подшипники на средних оборотах.
П Р И Л О Ж Е Н И Е 1.2
Лаборатория №2 Отчет по лабораторной работе №1
«Исследование процесса обработки на токарном станке»
Работа принята_______________________________ Студент Руководитель ________________________________ Группа
«___»____________г.
1.Задание
2.Схема обработки
3.Исходные данные
№ |
Наименование |
|
Размерность |
Числовое значение |
п/п |
|
|||
|
|
|
|
|
1 |
Наименование |
марка |
|
Сталь 20 |
материала заготовки |
|
|||
|
|
|
||
|
Прочностные характери- |
|
|
|
|
стики материала заготовки: |
|
2.104 |
|
2 |
модуль упругости, Е |
МПа |
||
|
твердость, НВ |
|
МПа |
1630 |
|
предел прочности,σ |
МПа |
412 |
|
3 |
Вид резца |
|
|
Проходной отогнутый |
|
|
правый прямоугольно- |
||
|
|
|
|
го сечения державки |
4 |
Материалрежущейчастирезца |
|
|
|
5 |
Величина главного угла в |
град |
45 |
|
плане φ резца |
|
|||
|
|
|
|
|
6 |
Величина главного |
угла |
град |
90 |
|
при вершине резца ε |
|
|
|
7 |
Диаметр заготовки |
|
мм |
|
8 |
Диаметр детали |
|
мм |
|
9 |
Схема закрепления |
|
|
Консольное закрепле- |
заготовки |
|
|
ние в патроне |
|
|
|
|
20 |
|
4.Эскиз заготовки, операционный эскиз и эскиз токарного резца
5.Последовательность выполнения расчетов
1.Определение глубины резания.
2.Определение по нормативам расчетного S0 и паспортного Sст значений по-
дачи.
3.Выбор по нормативам скорости резания vp и определение числа оборотов шпинделя np.
4.Расчет оперативного времени То + Тв.
5.Расчет длины пути инструмента.
ЛАБОРАТОРНАЯ РАБОТА № 2
ВЛИЯНИЕ ЖЕСТКОСТИ ТЕХНОЛОГИЧЕСКОЙ СИСТЕМЫ НА ТОЧНОСТЬ ОБРАБОТКИ
Цель работы – изучить на практике процесс точения и возможности токарного станка, исследовать влияние на точность обработки таких технологических факторов, как жесткость обрабатываемой заготовки, способ ее закрепления, режимы резания.
Необходимые теоретические сведения
Под действием сил резания звенья технологической системы «станок–приспособление–инструмент–деталь» упруго деформируются, т.е. изменяется их начальное положение относительно друг друга. Вследствие этого режущие кромки, образующие обрабатываемую поверхность, отклоняются от заданного настройкой положения и фактический размер детали будет отличаться от настроечного.
Величина упругих перемещений отдельных элементов системы зависит от их жесткости и действующей силы резания:
j = Py /y.
Жесткость какого-либо элемента технологической системы определяется отношением составляющей силы резания Py, направленной по нормали к обрабатываемой поверхности, к смещению лезвия инструмента относительно заготовки, отсчитываемому в том же направлении.
При определении жесткости задается направление смещения, но рассматривается влияние не только одной составляющей силы резания Py, но и других.
21
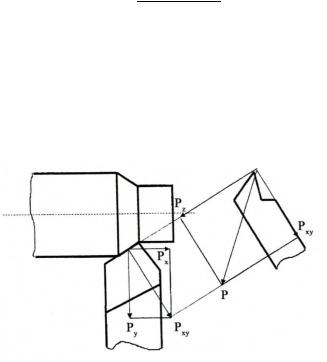
При точении сила резания, являющаяся результирующей сил деформирования металла и сил трения по передней и задней поверхностям резца, может быть представлена равнодействующей трех составляющих (рис. 2.1):
P = Px2 + Py2 + Pz2 ,
где Рх – осевая составляющая силы резания, параллельная оси главного вращательного движения резания; Рy – радиальная составляющая силы резания, направленная по радиусу главного вращательного движения резания в вершине резца; Рz – главная (касательная) составляющая силы резания, совпадающая по направлению со скоростью главного движения.
Рис. 2.1. Составляющие сил резания
Сила Рх противодействует продвижению резца вдоль оси заготовки и изгибает его в горизонтальной плоскости, а ее реакция сдвигает деталь вдоль оси.
Сила Рy стремится оттолкнуть резец от детали в направлении, перпендикулярном к ее оси, а реакция силы изгибает деталь в горизонтальной плоскости.
Сила Рz, действуя на резец, изгибает его в вертикальной плоскости, а ее реакция также в вертикальном направлении изгибает деталь.
22
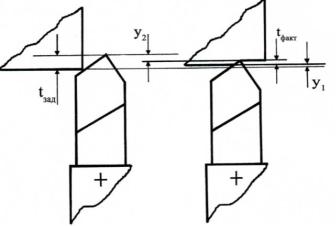
Смещение лезвия инструмента под действием составляющей силы резания Рy в направлении по нормали к обрабатываемой поверхности оказывает решающее влияние на формирование погрешности обработки. При этом смещение лезвия по касательной к обрабатываемой поверхности практически не влияет на точность обработки.
До начала обработки при настройке устанавливают заданную глубину резания tзад (рис. 2.2). В процессе обработки под действием радиальной составляющей силы резания Рy заготовка упруго отжимается на величину y1, а резец − на величину y2.
Рис. 2.2. Схема упругих перемещений элементов технологической системы при обработке
В результате этого заданная глубина резания уменьшается до значения tфакт :
tфакт = tзад – (у1 + у2).
Величины отжатий определяются по формулам
y |
= |
Py |
, |
y |
2 |
= |
Py |
, |
|
|
|||||||
1 |
jз |
|
|
jи |
|
|||
|
|
|
|
|
|
где jз – жесткость заготовки, кгс/мм, jи – жесткость системы инструмент−приспособление, кгс/мм.
23
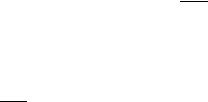
Таким образом, величина отклонения tфакт от tзад, означающая точность обработки, при данном значении Рy будет полностью определяться жесткостью отдельных элементов технологической системы. Чем выше жесткость, тем меньше величина отжатия и тем выше точность обработки.
Полагая, что жесткость системы «инструмент–приспособле- ние» (резец–суппорт) jи значительно выше жесткости заготовки jз, т.е. принимая y2 существенно меньше y1, tфакт можно записать в ви-
де tфакт = tзад – у1. Тогда размер детали после обтачивания заготовки равен:
d = dз – 2tфакт = dз – 2(tзад – y1),
где d – диаметр детали; dз – диаметр заготовки.
Жесткость отдельных элементов технологической системы при неизменном значении Рy зависит от условия нагружения. Например, при обтачивании валика его жесткость меняется при изменении положения резца по длине заготовки. Поэтому для оценки точности обработки определяют максимальное значение y1, что соответствует минимальной жесткости заготовки. Величину отжатая при изгибе детали в горизонтальной плоскости можно определить как прогиб балки, на которую действует сосредоточенная сила Рy:
y= Pyl з , kEJ
где l – длина участка заготовки, к которому приложена сила (расстояние от шпинделя до резца), мм; E – модуль упругости заготовки, ГПа; J – момент инерции поперечного сечения заготовки, мм4;
J = πd 4 0,05d 4 ; k – коэффициент, зависящий от способа закре-
64
пления детали (при консольном закреплении k = 3).
С целью увеличить жесткость детали, т.е. уменьшить погрешность формы как результат деформации, при обработке ее поджимают задним центром. В этом случае деталь можно представить в виде балки, закрепленной с двух сторон, на которую действует сосредоточенная сила. Деформация такой балки
24
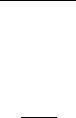
y = Py x2 (l − x)2 , 3ЕJl
где х – расстояние от шпинделя до точки приложения Рy, мм. Анализ последнего выражения показывает, что максимальный
прогиб (деформация) балки (детали) произойдет при х = l/2. При этом
y = Pyl3 . 48EJ
Тогда tфакт = tзад – y. При х = 0 и х = l деформация детали будет равна нулю, т.е. в этих сечениях tфакт = tзад. Таким образом, при данном способе закрепления деталь после обработки будет иметь боч-
кообразную погрешность формы.
При уменьшении фактической глубины резания относительно заданной уменьшается сила резания Рy, что, в свою очередь приводит к уменьшению деформации, поэтому при практических решениях принимают k = 110.
Величина Рy определяется по формуле
Py = C pyt xp S yr v np k p ,
где kp – обобщенный поправочный коэффициент, равный произведению поправочных коэффициентов, каждый из которых определяет влияние конкретных условий резания на величину Рy:
k p = km kφ k y kω kr kδ.
Поправочные коэффициенты учитывают: km – прочность или твердость обрабатываемого материала; kφ – величину главного угла в плане резца; ky – величину переднего угла; kω – применение СОЖ; kr – величину радиуса вершины резца; kδ – степень изношенности задней поверхности резца.
Постоянная Сру учитывает влияние на Рy некоторых постоянных условий резания в частности тех, для которых поправочные коэффициенты равны единице.
При наружном продольном точении конструкционных сталей твердосплавным резцом с главным углом в плане φ = 45°, оптимальным передним углом, с радиусом при вершине r = 0,5, нормальной степени износа, без применения СОЖ можно принять
25
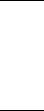
значения поправочных коэффициентов kφ, ky, kω, kr, kδ равными единице. Тогда kp = km,
|
σ |
в |
mр |
||
km = |
|
|
, |
||
750 |
|||||
|
|
|
где σв – предел прочности материала заготовки, МПа; mp – показатель, учитывающий материал режущей части резца и механические свойства материала заготовки (при обработке конструкционных сталей инструментом из твердого сплава mp = 1,35).
При перечисленных условиях обработки (условия лабораторной работы)
Сру = 243, xр = 0,9, yr = 0,6, nр = – 0,3.
Допустимая величина прогиба (отжатия) определяется заданной точностью. Чтобы погрешность обработки не превышала допуск на заданный размер, необходимо обеспечить выполнение следующего условия: ymax ≤ yдоп.
Принимая допустимую величину отжатия yдоп = 0,5Т, можно задать условие обеспечения заданной точности: y1max ≤ 0,5Т, где Т – допуск на диаметр детали, мкм.
Изменение жесткости заготовки в процессе обработки и, как следствие, непрерывное изменение y1 является причиной изменения фактической глубины резания, что ведет к появлению погрешности формы, вид которой определятся условиями обработки.
Определение режимов резания. Глубина резания t. Припуск на обработку (в мм) определяется по формуле
h = Dз2− D ,
где Dз – диаметр заготовки по обработанной поверхности, мм; D – диаметр детали по обработанной поверхности, мм.
Если припуск удаляется за один проход, то глубина резания равна:
t = h = Dз2− D мм.
Если обработка разделена на черновую и чистовую, то
tчист = (0,2 ÷0,25) / h, мм,
tчерн = h −tчист.
26
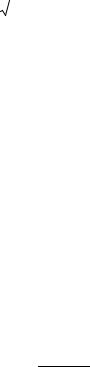
Подача S0. Подача S0 назначается в зависимости от глубины резания, геометрии резца, заданной шероховатости и точности, материала заготовки и режущей части резца. Рекомендуемые значения подач приведены в справочной литературе.
При выполнении работы для определения S0 (в мм/об) рекомендуется воспользоваться выражением
|
|
= |
(0,093 |
|
+ 0,002 D) y |
|
|
|
|
|
|
|
S |
0 |
D |
C |
м |
C |
ra |
rи k |
sm |
, |
|||
|
|
|
||||||||||
|
|
t x φ2 (180 − ϕ− ε)z |
|
|
в |
|
||||||
|
|
|
|
|
|
|
|
|
|
где φ – главный угол в плане; ε – угол при вершине резца; rви –
радиус вершины резца, мм; См – коэффициенты, характеризующие вид обрабатываемого материала; Сra – коэффициент, учитывающий стадию обработки (черновая, получистовая, чистовая отделочная); ksm – коэффициент, учитывающий твердость обрабатываемого материала.
При чистовом точении конструкционных сталей значения показателей степени и коэффициентов следующие: y = 1,4; x = 0,3; z = 0,35; u = 0,7; Cм = 0,008; Сra = 131 − для чистовой обработки;
Сra = 256 − для получистовой обработки; ksm = Сsm(HB)ym. Для конструкционной стали: Сsm = 349,9; ym = – 0,7737.
Расчетная величина подачи S0 корректируется по паспорту станка, принимается ближайшее значение подачи S0.
Скорость резания v. Допустимая скорость резания v (м/мин) рассчитывается с учетом назначенной глубины резания, подачи, стойкости инструмента Т, обрабатываемого материала режущей части резца, его геометрии и определяется по формуле
vp = t xvCvS yv kvт kvm ,
где Сv – коэффициент, учитывающий условия обработки (t и S) и вид материала; kvт – коэффициент, учитывающий стойкость ин-
струмента; kvm – коэффициент, учитывающий твердость обраба-
тываемого материала.
Для продольного точения конструкционных сталей при t ≤ 12 мм и S < 0,4 мм/об при работе твердосплавным инструментом значения показателей степени и коэффициентов следующие:
27

Cv = 141, xv = 0,15, yv = 0,25;
kvт = Сvm T mv , Cvm = 3,822, mv = −0,373; kvт = Сvm (HB)mv , Cvm =18107, mv = −1,288.
По величине vp (м/мин) определяется соответствующее значение оборотов шпинделя:
nр = |
1000 |
vр |
. |
|
|
π Dз |
|||
|
|
|
Расчетное число оборотов в минуту np следует корректировать по паспорту станка, приведя в соответствие с ближайшим меньшим значением.
Фактическую скорость резания vф можно рассчитать исходя из выбранного числа оборотов в минуту шпинделя по паспор-
ту (np):
vф = π Dз nр . 1000
Поскольку, как правило, фактическая скорость резания vф меньше расчетной vp, фактическая стойкость инструмента возрастает; если же расчетное число оборотов в минуту шпинделя лишь на 5…10% меньше ближайшей ступени числа оборотов в минуту по паспорту станка, можно воспользоваться этой ступенью, причем фактическая стойкость инструмента снизится незначительно.
Токарно-винторезный станок особо высокой точности
16Б05А. Станок 16Б05А (рис. 2.3) предназначен для выполнения различных токарных работ: обтачивания наружных и растачивания внутренних цилиндрических и конических поверхностей, подрезания торцевых поверхностей, отрезки, сверления, зенкерования и развертывания отверстий, нарезания резьбы.
Станина станка 1 представляет собой жесткую отливку с поперечными ребрами в средней части, разделенными окнами для осыпания стружки. Сверху на станине расположены две пары направляющих; крайние – для суппорта 8 и средние – для задней бабки 9. Слева на верхней плоскости станины установлена передняя бабка 5, справа – задняя бабка 9.
28
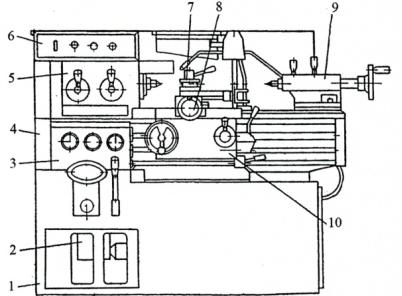
Рис. 2.3. Станок токарно-винторезный 16Б05А: 1 – станина, 2 – редуктор, 3 – коробка подач, 4 – гитара, 5 – бабка, 6 – электрооборудование, 7 – резцедержатель четырехпозиционный, 8 – суппорт, 9 – бабка задняя, 10 – фартук
Вкорпусе передней бабки собраны шпиндель, привод резьбы
иподач с механизмом управления, который позволяет изменить направление подачи или нарезаемой резьбы. Рукоятки управления механизмами передней бабки расположены на ее передней стенке. Спереди к корпусу бабки прикреплен литой кожух, в котором установлены кнопки управления главным электродвигателем.
Задняя бабка 9 состоит из основания и корпуса, в котором смонтированы механизмы бабки. Корпус может смещаться в поперечном направлении по выступу основания при помощи регулировочных винтов и гайки. Бабка закрепляется на направляющих станка рукояткой эксцентрикового зажима. В расточке корпуса расположена пиноль для установки упорного центра и других инструментов.
На передней стенке станины слева закреплена коробка подач 3, справа – колодка с опорами ходового винта и ходового меха-
29