
ХИМИЧЕСКАЯ технология керамики и огнеупоров
.pdf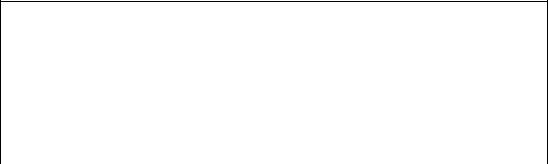
Включают нагреватель кнопкой 4 («Нагрев»), рукояткой 6 устанавливают на вольтметре 5 начальное напряжение 40 В, а переключатель 8 переводят в положение, соответствующее заданной температуре (25, 50, ..., 200°С). Прибор Ф 136 включают на измерение, отжав кнопку «АРР».
При приближении к заданному значению температуры световой указатель прибора Ф 136 подходит к нулевой отметке. При ее достижении переключатель 7 быстро переводят в положение «Пт». Световой указатель при этом отклоняется на несколько делений от нулевой отметки. Фиксируют количество делений, быстро переводят переключатель 7 в положение «По», также отметив число делений отклонения от нуля, возвращают переключатель в положение «tс». Число зафиксированных делений заносят в соответствующие графы табл. 39.
Переключатель 8 переводят на следующее значение температуры и для нее осуществляют аналогичные определения. По достижении верхнего значения температуры снимают напряжение на вольтметре, отключают нагрев, заарретировав прибор Ф 136 нажатием кнопки «АРР», отключают приборы от сети.
По полученным данным производят необходимые расчеты для каждой температуры в следующей последовательности:
1)рассчитывают поправку на теплоемкость образца σс;
2)находят тепловое сопротивление образца Рс;
3)вычисляют теплопроводность испытуемого образца λ. Полученные значения также записывают по форме табл. 39. Строят графическую зависимость теплопроводности от темпера-
туры, производят оценку полученной зависимости.
Таблица 39
Результаты измерений и расчета теплопроводности образцов
h = ___, d = ___, S = ___, m = ___, Co(t) = ___
t, °С |
По, дел. |
Пт, дел. |
sс |
Ро, м2 × К/Вт |
l, Вт/(м × К) |
|
|
|
|
|
|
25 |
|
|
|
|
|
50 |
|
|
|
|
|
... |
|
|
|
|
|
200 |
|
|
|
|
|
190
4.5. Определение термостойкости
Общие сведения
Термическая стойкость керамических изделий и материалов характеризует их способность выдерживать без разрушения резкие смены температуры. Это один из важнейших качественных показателей керамики, во многих случаях определяющих возможность ее применения в условиях резкого термоциклирования.
При резком нагревании или охлаждении в изделии возникают температурные перепады и разные слои претерпевают объемные неодинаковые изменения, вызывающие в свою очередь термические напряжения, которые могут быть разрывающими, сжимающими, сдвигающими в зависимости от размера и формы изделий и условий их нагрева или охлаждения. Влияние термических напряжений на различного рода материалы зависит от величины этих напряжений, их распределения по объему изделий и продолжительности действия, а также от таких свойств материала, как пластичность или мера хрупкости, которое оказывает значительное воздействие на термостойкость при высоких температурах. Величина термических напряжений в основном определяется перепадом температуры:
σт.н = Еα (Тсер – Тпов),
где Е – модуль Юнга; α – температурный коэффициент линейного расширения; Тсер, Тпов – соответственно температуры середины и поверхности изделия, °С.
Если возникшие термические напряжения превышают предел прочности материала, то происходит нарушение сплошности изделия, т. е. возникновение термических трещин или разрушение.
Термическая прочность – это комплексная характеристика изделия или материала, зависящая от многих факторов и единого критерия оценки термической стойкости изделия нет. Исследователями предложены 22 критерия для теоретической характеристики термостойкости.
Наиболее значимыми из них являются:
– критерий термического сопротивления
R = σ(1 − μ) ,
Еα
где σ – предел прочности при разрыве, МПа; μ – коэффициент Пуассона; Е – модуль Юнга, МПа; α – температурный коэффициент линейного расширения, К–1 ;
191

– критерий, учитывающий условия передачи тепла в изделии (температуропроводность)
K = f(λ, а), а = λ ,
сρ
где λ – коэффициент теплопроводности, Вт/(м × К); а – температуропроводность, м2/с; с – теплоемкость, Вт/(кг × К); ρ – плотность материала, кг/м3;
– критерий (фактор) формы и размеров изделий S.
В некотором приближении без учета размерных и структурных особенностей изделия термостойкость можно оценить общим коэффициентом:
R′ = σ(1 − μ)λ S .
Еλсρ
Некоторыми исследователями предложены для оценки критерии, характеризующие скорость образования и распространения термической трещины, зависящие от меры хрупкости материала.
Физические свойства керамических материалов, а также фактор формы и размера и условия теплоотдачи определяют предпосылки возникновения трещин в изделии. Скорость распространения образующейся трещины может быть различной в зависимости от структуры материала. В керамике, характеризующейся плотной, мелкозернистой структурой, а также при большом содержании стекловидной фазы термическая магистральная трещина возникает и распространяется мгновенно, нарушая целостность изделия.
Изменяя структуру керамики, можно влиять на скорость распространения термических трещин. Так, в материалах зернистого строения, а также состоящих из нескольких фаз с разными ТКЛР, образуется микротрещиноватая структура, которая в известной степени снижает скорость распространения трещин при термоударах, что приводит к повышению термостойкости изделий. Термическая стойкость в этих случаях растет за счет увеличения соотношения σ/Е, представляющего собой максимальную относительную упругую деформацию. Кроме этого, особенности структуры допускают некоторые перемещения зерен относительно друг друга при термоударах, что дает возможность существенно релаксировать возникающие термические напряжения.
Таким образом, для теоретической оценки термостойкости керамических изделий необходимо определить показатели механической прочности, модуля упругости, температурного коэффициента
192
линейного расширения, теплофизических и других характеристик. Кроме того, следует знать о структурных особенностях материала.
На практике термическую стойкость керамических огнеупоров и технических материалов оценивают:
–числом теплосмен до полного или частичного разрушения изделия при нагреве его до определенной температуры и резком
охлаждении. Например, для контроля огнеупоров предусмотрен нагрев до 1300 или 850°С и охлаждение в проточной воде;
–потерей механической прочности соответствующих образцов после ряда теплосмен. Термическая прочность выражается в виде потери механической прочности в процентах к первоначальной после установленного числа теплосмен;
–предельным температурным перепадом, при котором изделие разрушается или значительно теряет необходимые технические свойства (например, вакуум-плотность).
Проведение анализа
Определение термической стойкости методом последова- тельных теплосмен до образования трещин и разрушения
Посуда и приборы: сосуд с водой, огнеупорные подставки, щипцы, печь электрическая с карбидкремниевыми нагревателями, сушильный шкаф, технические весы с разновесом.
Методы теплосмен заключаются в том, что исследуемые образцы определенных размеров нагревают до заданной температуры, вынимают из печи и охлаждают в проточной воде, струей холодного воздуха или при нормальных условиях на какой-либо подставке. Обычно образцы нагревают до 800...850 или 1300°С и выше.
За одну теплосмену принимают нагрев образца до заданной температуры и последующее охлаждение.
Критерием термической стойкости в этих случаях служит количество теплосмен, приводящее к образованию трещин на образцах или их разрушению.
Метод теплосмен применяют для определения термической стойкости огнеупоров зернистого строения и, в частности, для промышленных огнеупорных материалов.
Стандартный метод испытания огнеупорных изделий на термическую стойкость заключается в установлении количества теплосмен (нагревов и резких охлаждений), которое может выдержать изделие до определенной степени разрушения.
193
Образцами служат кирпичи нормального размера (230×114×65 мм) с допусками по всем измерениям ±4 мм, клин ребровый и клин торцевой нормальных размеров. Изделия, которые по своей конфигурации не пригодны для изготовления из них образцов размером 230×114×65 мм, например изделия типа трубок или с толщиной стенки менее 50 мм, по этому методу не испытываются.
Перед определением образцы высушивают при 110°С и взвешивают с погрешностью до 5 г. Нагревают образцы в специальной электрической печи с нагревателями из карбида кремния, рассчитанной на одновременное испытание пяти кирпичей нормального размера. Образцы на 50 мм вводят в рабочее пространство печи, предварительно разогретое до 1300°С, торцом к задней стенке. Все зазоры между образцами, а также между ними и стенками загрузочного отверстия печи необходимо закладывать легковесными шамотными вкладышами или асбестом. Снизившуюся при введении образцов температуру в течение 10–20 мин снова поднимают до 1300°С и выдерживают образцы при этой температуре на протяжении 10 мин. Колебания температуры в процессе выдержки образцов допускаются в пределах ±10°С. Термопару устанавливают в печи между образцами и карборундовыми нагревателями на высоте середины образцов и на расстоянии 10 мм от их концов, введенных в печь.
После нагревания образцы вынимают из печи и опускают нагретым концом в специальный бак с проточной водой (температура воды 5...25°С) на глубину 50 мм, охлаждают в течение 5 мин, затем вынимают из воды и выдерживают 5–10 мин на воздухе. Во время охлаждения образцов загрузочное отверстие печи должно быть закрыто. Нагрев и охлаждение повторяют до потери 20% массы образца. Для обеспечения одинаковых условий испытания после каждой теплосмены меняют месторасположение образцов в печи, кроме того, каждый кирпич поворачивают на 180° вокруг продольной оси.
Нельзя помещать на повторный нагрев в печь влажные изделия. После охлаждения в воде их надо высушить в сушильном шкафу.
По окончании каждой теплосмены остывшие образцы осматривают и отмечают появление трещин, потерю массы и характер разрушения (выкрошивание или отколы материала). Результаты испытаний выражают в целых теплосменах, которые выдержал образец до потери 20% первоначальной массы. Теплосмена, в которой поте-
194
ря массы превысила 20%, в счет выдержанных теплосмен не включается. Показателем термостойкости считается среднее арифметическое результатов испытаний всех пяти образцов.
Условное обозначение термостойкости нормального или близкого к нему образца, испытанного при 1300°С и выдержавшего, например, 10 теплосмен: ТС1300 – 10.
Возможно проведение испытаний на термостойкость при нагревании образцов изделий до 850°С и охлаждении в проточной воде.
Для ориентировочной сравнительной оценки термостойкости керамических материалов в лабораторных условиях могут использоваться образцы (выпиленные из изделий или сформованные и обожженные при оптимальных условиях) в виде кубиков (50×50×50 мм; 30×30×30 мм), плиточек (50×50×10 мм) или других размеров. Лабораторные образцы в количестве не менее пяти штук одного состава на огнеупорной подставке устанавливаются в печь, нагретую до заданной температуры (850 или 1300°С). Дальнейшие испытания проводят аналогично вышеописанной методике.
Данные по определению термостойкости записывают по форме табл. 40.
Таблица 40
Определение термостойкости
|
|
|
Число теплосмен |
|
|
|
||
|
|
|
|
до |
|
Общая |
Характер |
При- |
Мате- |
Размеры |
№ |
до появ- |
до 20% |
потеря |
|||
риал |
образца |
образца |
ления |
начала |
потери |
массы, |
разру- |
меча- |
|
|
|
трещин |
потерь |
массы |
% |
шения |
ние |
|
|
|
|
массы |
|
|
|
|
|
|
|
|
|
|
|
|
|
Определение термической стойкости по потере прочности
Посуда и приборы: сосуд с водой или шамотная плита с песком, щипцы, печь электрическая муфельная или с силитовыми нагревателями, термопара ХА или ПП, штангенциркуль, установка для испытаний образцов на изгиб.
Термическую стойкость спекшейся керамики, а также некоторых огнеупорных изделий можно характеризовать косвенно величиной потери прочности после одной или нескольких теплосмен. Этим методом можно пользоваться, если при воздействии теплового удара полного разрушения образца не происходит, а только уменьшается прочность вследствие образования на поверхности
195
и внутри материала микротрещин за счет возникающих термических напряжений. Чаще термостойкость таким методом находится после одной теплосмены, так как именно после первой теплосмены наблюдается наибольшая потеря прочности.
Наиболее часто при этом методе оценки термостойкости применяется определение показателей предела прочности при изгибе.
Для испытаний используют образцы в виде удлиненных плиточек или балочек (круглого или квадратного сечения) различного размера в зависимости от вида материала и технических возможностей изготовления образцов. Для испытаний отбирают образцы без видимых дефектов с достаточно правильной формой и точными размерами. Для получения сравнительных данных необходимо брать образцы, одинаковые по форме и размерам, и проводить испытания в одинаковых условиях.
На 3–5 образцах определяют прочность при изгибе до испытаний и рассчитывают ее среднее арифметическое значение. В начале испытаний 10–15 образцов из испытуемого материала помещают в электрическую муфельную печь или с силитовыми нагревателями и медленно нагревают до требуемой температуры, при достижении которой дается выдержка в течение 20–30 мин, после чего образцы быстро вынимают и охлаждают по определенному режиму.
Температура испытаний для каждого вида материала точно не установлена и подбирается опытным путем. Как правило, для образцов из фарфоровых масс и тонкокерамических материалов, содержащих стеклофазу, а также для керамики с низкой теплопроводностью и высоким ТКЛР (например, ZrO2) температура испытания невысока, обычно до 600...700°С. Для плотной оксидной керамики (Al2O3, MgO, BeO и др.) температура нагрева может составлять
800...1500°С.
Охлаждают образцы в проточной воде, струей холодного воздуха или при естественном охлаждении на шамотной или металлической плитке.
По окончании теплосмены определяют величину прочности при изгибе испытуемых образцов. Показателем термической стойкости данного материала является значение потери прочности или значение остаточной прочности, выраженное в процентах. Ошибка определения составляет около 10%. Полученные данные заносят в табл. 41.
196
Таблица 41
Определение термической стойкости по изменению показателей прочности при изгибе
№ |
Прочность |
Средняя прочность |
Потеря |
|
при изгибе после |
при изгибе до теплосмены, |
прочности, |
||
образца |
||||
теплосмены, МПа |
МПа |
% |
||
|
||||
|
|
|
|
Определение термической стойкости тонкокерамических материалов и глазурных покрытий методом разрушающего температурного перепада
Материалы, посуда и приборы: чернила или эозин (фуксин), со-
суд с водой, печь электрическая, термопара ХА, гальванометр. Термическая стойкость тонкокерамических, в том числе глазу-
рованных, изделий (фарфор, фаянс, стеатит и некоторых других), а также стекла определяется по появлению цека на глазурном слое или трещин на теле изделия под влиянием резкой смены температур. В данном случае критерием термической стойкости является максимальная разность между температурой нагретого образца и температурой охлаждающей среды, приводящая к разрушению глазури или керамического тела.
Испытуемые изделия или опытные образцы в виде пластин или балочек небольшого размера (5×5×50 мм) помещают в электрическую печь, нагретую до 100°С, и выдерживают при этой температуре в течение 20 мин. Затем образцы быстро вынимают из печи и погружают в холодную проточную воду с температурой 12...20°С. (Время переноса образцов из печи в воду должно быть не более 5 с.)
Для лучшего визуального определения трещин охлаждение образцов желательно проводить в воде, подкрашенной чернилами или фуксином (эозином). Охлажденные образцы тщательно осматривают и при отсутствии цека глазури или видимых вооруженным глазом повреждений снова помещают в печь и выдерживают в течение 20 мин при 125°С, затем снова охлаждают в воде. Испытание с последующим увеличением температуры нагрева продолжают до тех пор, пока не появятся трещины на образцах или цек на глазури. Температуру каждого последующего нагрева повышают на 25°С.
В некоторых случаях при проведении таких испытаний каждый раз при увеличении температуры нагрева используют образцы, не подвергавшиеся термоудару. Это позволяет получить более
197
правильную оценку поведения материала, но требует большего количества образцов.
Разрушение глазурованных образцов начинается обычно с глазурованного покрытия, трещины на котором образуются при разности температур испытания 150...300°С. На неглазурованных фарфоровых изделиях трещины обычно появляются при температуре около 400°С. Глазури для фаянса, имеющие меньшее сродство с керамическим черепком, чем фарфоровые, разрушаются обычно при меньшей разности температур.
Испытание проводят параллельно на пяти образцах, результаты записывают по форме табл. 42.
Таблица 42
Определение термической стойкости тонкокерамических изделий
№ |
№ |
Температура |
Результаты внешнего осмотра |
образца |
теплосмены |
нагрева, °С |
испытуемых образцов |
|
|
|
|
Термическую стойкость керамических электротехнических материалов определяют по ГОСТ 24409 путем осуществления последовательных циклов – нагрева образцов в электропечи с выдержкой 30 мин при заданной температуре и резкого охлаждения их в воде в течение 15 мин.
Испытания проводят на образцах в виде цилиндров диаметром и высотой 25 мм, неглазурованных или глазурованных по цилиндрической поверхности. Количество образцов должно быть не менее шести.
При первом цикле в печи устанавливают температуру на 100°С выше температуры охлаждающей воды.
После охлаждения образцы вынимают из воды, подсушивают и проверяют наличие в них трещин. Для большей достоверности образцы после подсушки окрашивают в спиртовом растворе фуксина.
Образцы без трещин подвергают повторному циклу нагрева и охлаждения. При каждом новом цикле разность температур между нагревом и охлаждением увеличивают на 10°С. Циклы продолжают до появления трещин на всех испытуемых образцах.
За величину термической стойкости принимают среднее арифметическое значение разрушающих перепадов температур для отдельных образцов с округлением до 5°С в сторону меньшего значения.
198
Допускается выражать термическую стойкость в виде самой низкой разницы температур, при которой появились первые трещины на двух или более образцах. Ошибка в определении разрушающего перепада на должна превышать 5%. Результаты записывают по форме табл. 42.
4.6. Определение химической стойкости
Общие сведения
Керамические материалы в процессе эксплуатации подвергаются агрессивному действию различных веществ: твердых (пыли, сырья, огнеупоров и т. д.), жидких (растворов кислот, щелочей, расплавов солей, стекол, шлаков и т. д.), газообразных (продуктов химических реакций, горения топлива и т. д.). Способность керамики противостоять действию агрессивных сред называется химической стойкостью.
В результате воздействия агрессивной среды на керамику происходит ее коррозионное разрушение, что приводит к частичной или полной потере прочности, значительным изменениям других свойств материала.
Химическая стойкость керамики определяется главным образом природой взаимодействующих фаз, их химическим и минералогическим составом и подчиняется общехимическим законам кинетики гетерогенных процессов.
Скорость химического взаимодействия зависит от таких внешних факторов, как температура, давление, концентрация и вязкость агрессивной среды, скорость перемещения среды относительно керамического материала. На химическую стойкость керамики оказывают большое влияние ее структурные особенности: пористость, вид и характер распределения пор, состояние поверхности, количественное соотношение и объемное распределение кристаллических и стекловидных фаз.
Плотная малопористая керамика обладает более высокой коррозионной стойкостью. С повышением пористости, особенно проникающей, химическое разъедание керамики интенсифицируется, так как увеличивается контактная поверхность взаимодействия с агрессивной средой, поэтому в пористой керамике коррозия распространяется на весь объем. В многофазной керамике возможна избирательная коррозия по одной из фаз, менее устойчивой, преимущественно стекловидной. Если распределение фаз в керамике неравномерное, то вероятно разъедание ее в отдельных участках, точках.
199