
ХИМИЧЕСКАЯ технология керамики и огнеупоров
.pdf
|
Таблица 34 |
Величины ТКЛР различных видов керамики |
|
|
|
Материал |
α · 106, К–1 (20...500°С) |
|
|
Техническая керамика: |
|
корундовая |
7,4–8,0 |
кордиеритовая |
1–2 |
периплазовая |
11–13 |
муллитовая |
4,6–5,3 |
тиалитовая |
–0,5–1,7 |
сподуменовая |
8,4–8,6 |
броммелитовая |
8,4–8,6 |
карбидкремниевая |
3,9 |
Огнеупорные материалы: |
|
шамотный |
–5–6 |
динасовый |
–11,5–13 |
хромито-периплазовый |
9–10 |
Фарфор |
5–7 |
Кварцевое стекло |
0,54 |
Следует отметить, что изучение термического расширения керамических материалов является достаточно чувствительным методом, который фиксирует структурные изменения, происходящие при нагревании, и может дополнять классические методы изучения структуры.
Проведение анализа
Приборы: трубчатая печь с температурой нагрева до 1000°С, горизонтальный дилатометр кварцевый с устройством для крепления (или ДКВ-2), индикатор многооборотный часового типа с ценой деления 0,001 мм, термопара типа ХА, потенциометр, автотрансформатор типа ЛАТР, секундомер.
В настоящее время для определения ТКЛР керамических материалов используют несколько методов: рентгеновский, интерферометрический, дилатометрический, – а также применение прецизионного микроскопа. Наиболее простой и распространенный метод – дилатометрический. Широко используют горизонтальные и вертикальные кварцевые дилатометры.
На рис. 63 представлена схема горизонтального дилатометра.
180
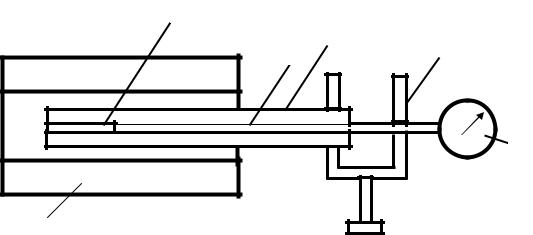
4 |
|
|
5 |
2 |
6 |
|
|
|
|
|
3 |
1 |
|
|
Рис. 63. Схема кварцевого горизонтального дилатометра:
1 – трубчатая печь; 2 – кварцевая трубка; 3 – индикаторная головка; 4 – образец; 5 – кварцевый стержень; 6 – металлическая стойка
Прибор состоит из горизонтальной трубчатой печи 1, кварцевой трубки 2 и индикаторной головки 3. Температура в печи регулируется автотрансформатором типа ЛАТР и измеряется проградуированной хромель-алюмелевой термопарой. Для испытаний используют образец размером 5×5×50 мм (или Ø5 мм) со строго плоскопараллельными торцами. Начальную длину образца l0 измеряют с точностью до 0,01 мм.
Образец 4 помещают в кварцевую трубку. Запаянный конец трубки должен плотно соприкасаться с торцом образца. К образцу подводят термопару. Другую сторону трубки (открытую) закрепляют в металлической стойке 6. С открытого конца в трубку вставляют тонкий кварцевый стержень 5 такого же диаметра, что и образец. Другой конец стержня соединяют со стержнем индикаторной головки. Индикаторная головка укреплена на металлической стойке. Плотный контакт стержня с образцом осуществляется при помощи давления пружины индикатора. При расширении образец давит через кварцевый стержень на индикатор.
Перед началом испытаний показания индикатора устанавливают на нуль. Подъем температуры в печи с образцом производится со скоростью 4...5°С/мин. Регулируют скорость подъема температуры с помощью автотрансформатора. Через определенные интервалы температуры (например, 50°С) снимают показания индикатора (количество делений). Устанавливают и контролируют
181
температуру в печи с помощью потенциометра, соединенного с термопарой, пользуясь градуировочной таблицей для данного вида термопары (см. прил. 4).
На расширение образца и перемещение кварцевого стержня указывает стрелка индикатора. К величине расширения образца, измеренной индикатором по перемещению стрелки, прибавляется поправка на расширение кварца, которая приведена в табл. 35.
|
|
Таблица 35 |
|
Средние значения ТКЛР кварцевого стекла |
|
|
|
|
№ |
Температурный интервал, |
ТКЛР кварцевого стекла, |
°С |
10–6 град–1 |
|
|
|
|
1 |
0...20 |
0,383 |
2 |
20...100 |
0,502 |
3 |
20...200 |
0,572 |
4 |
20...300 |
0,576 |
5 |
20...400 |
0,579 |
Введение поправки на расширение кварца необходимо в связи с тем, что держатель образца – трубка изготовляется из кварцевого стекла и закрепляется жестко с одной стороны. Образец начальной длины при нагревании расширяется не только в сторону стержня, передающего расширение на индикатор, но и в противоположном направлении, в сторону свободного конца кварцевой трубки, на некоторую величину за счет расширения самой трубки, поэтому в результате измерения следует внести поправку на расширение кварцевого стекла.
Опытные данные вносят в табл. 36.
Таблица 36
Экспериментальные данные измерения ТКЛР
|
|
Температура, |
|
|
Абсо- |
|
|
|
||
|
|
°С |
|
Показания |
|
Относи- |
|
|
||
|
|
|
Поправка |
лютное |
|
|
||||
|
|
|
|
|
индикато- |
тельное |
ТКЛР |
|||
№ |
Время, |
задан- |
|
фак- |
ра, число |
на расши- |
удлине- |
удлинение |
a × 106, |
|
|
мин |
|
тиче- |
делений |
рение |
ние об- |
образца, |
К |
–1 |
|
|
|
ная |
|
–1 |
разца l, |
|
||||
|
|
|
ская |
(мм) |
кварца, К |
l/L × 100% |
|
|
||
|
|
|
|
|
мм |
|
|
|||
|
|
|
|
|
|
|
|
|
|
|
|
|
|
|
|
|
|
|
|
|
|
182
Температурный коэффициент линейного расширения образца рассчитывается для всех температурных интервалов по следующей формуле:
|
|
α = |
|
nК |
+ αкв, |
|
|
(Tк |
− Tн)l0 |
||
|
|
|
|
||
где |
n – |
показания индикатора; К |
– цена деления индикатора; |
||
(Тк – |
Тн) – |
разность температур (конечной и начальной) для выбран- |
ного интервала, °С; l0 – начальная длина образца, мм; αкв – поправка на расширение кварца, град–1 .
Кроме вышеуказанных горизонтальных дилатометров, для определения ТКЛР довольно часто используют вертикальные кварцевые дилатометры ДКВ. Прибор состоит из трубчатой электрической печи с нагревателем (до 1000°С), в которой находится кварцевая трубка дилатометра с прижимным кварцевым стержнем. Для нахождения ТКЛР используется такой же образец, как и в горизонтальном дилатометре. Расширение образца при нагревании передается многооборотному индикатору, укрепленному сверху на стойке. Порядок испытаний и расчет ТКЛР идентичны работе на горизонтальном дилатометре.
Применяются также приборы с автоматической записью расширения образца. Вместо индикатора в этом случае используется специальная электронная лампа – механотрон, а запись осуществляется на двухкоординатном потенциометре.
Температурный коэффициент линейного расширения при температурах выше 1000°С можно определить дилатометром из кордиерита, карбида кремния, корунда или монокристалла сапфира. В этих случаях для нагрева служат печи с нагревателями из карбида кремния, сплава платины и родия или дисилицида молибдена.
Применение для дилатометров графита, вольфрама или молибдена позволяет проводить испытания при температурах до 2000...2500°С, однако нагрев при этом следует осуществлять в вакуумных печах или печах с инертной атмосферой.
Во всех вариантах измерений для снятия кривой ТКЛР материалов необходимо соблюдение следующих условий: торцы образца, трубки и стержня должны быть тщательно обработаны для обеспечения нормального контакта; во время испытаний нужно нагревать образец с определенной скоростью, зависящей от теплопроводности материала; для лучшего прогрева образца в трубке дилатометра должны быть сделаны окна.
183

Испытание проводится до температуры, определяемой возможностями дилатометра или образца.
По полученным экспериментальным данным на любом из применяемых дилатометров строят графические зависимости αср от температуры. По этим кривым делают заключение о поведении керамического материала при нагревании и предполагаемых фазовых переходах. Чем равномернее происходит расширение материала, тем, как правило, будет выше термостойкость изделий.
4.4.Определение теплопроводности
итемпературопроводности
Общие сведения
Теплопроводность является важнейшим свойством керамики, характеризующим эффективность ее использования в качестве теплоизоляции и теплозащиты. Теплопроводность – это способность материала переносить теплоту, обусловленную наличием в материале градиента температуры.
Одним из наиболее известных и применяемых на практике показателей материалов, количественно характеризующих их способность проводить тепло, является коэффициент теплопроводности λ, Вт/(м · К), который определяется из следующего соотношения:
q = ∂Q = −λ ∂T , S∂τ ∂x
где q – плотность теплового потока в веществе в направлении х; ∂Q – количество тепла, переносимого за время ∂τ через площадь образца S, перпендикулярную к направлению теплового потока; ∂T / ∂x – градиент температуры в направлении х.
Вышеприведенная формула является математическим выражением закона Фурье, согласно которому плотность теплового потока (количество тепла, передаваемого через единичную площадку в единицу времени) пропорциональна градиенту температуры. При этом знак «–» указывает на то, что тепло течет в направлении, противоположном градиенту температур, т. е. от горячей области к холодной.
Согласно теории теплопроводности, развитой Фурье, скорость изменения температуры материала в нестационарном тепловом потоке,
184
который распространяется в веществе в направлении х, выражается уравнением
|
|
|
∂T |
|
|
|
|
|
∂T |
= ∂ |
α ∂x |
. |
|
|
|
|
∂τ |
|
|
|
|
||
|
|
∂x |
|
|
|
||
Если считать коэффициент теплопроводности λ независящим |
|||||||
от температуры, то из этого уравнения следует, что |
∂T |
= α |
∂2T . |
||||
|
|
|
|
|
∂τ |
|
∂x2 |
Величина α, м2/с, в уравнении, называемая коэффициентом температуропроводности материала, характеризует скорость изменения температуры тела в нестационарных условиях и равна отношению теплопроводности λ к объемной теплоемкости Сv материала.
Как следует из вышесказанного, величина α определяет скорость выравнивания температуры тела по его толщине в нестационарном тепловом потоке, например при помещении изделия, имеющего температуру Т1, в среду с температурой Т2 (например, нагрев либо охлаждение стенок промышленных печей в режимах подъема или снижения температуры в них).
Чем большие значения коэффициента температуропроводности имеет материал, тем быстрее происходит установление заданного температурного режима в отдельных областях внутри образца при прочих равных условиях (объем и форма образцов, условия нагрева либо охлаждения). При нагреве (охлаждении) керамических материалов температура достаточно медленно выравнивается по их объему, что вызывает большие перепады температуры и, как следствие, приводит к появлению термомеханических напряжений. Небольшие значения α (2,4–6,10 –7 м2/с) соответствуют большим температурным градиентам внутри материала в период его нагрева (охлаждения) и, следовательно, увеличивают опасность разрушения вследствие внезапного изменения его температуры (термического удара).
Коэффициент теплопроводности λ и величина α зависят от множества факторов, так как перенос тепла в керамических материалах, большинство из которых являются пористыми, – сложный процесс, связанный с четырьмя основными механизмами теплопередачи: проводимостью твердой фазы, проводимостью газа в порах, излучением через поры и конвекцией газа в порах.
185

На теплопроводность керамики оказывают влияние состав твердой фазы, пористость, однородность материала и температура. Наиболее радикально на теплопроводность воздействует пористость, поскольку воздушные прослойки благодаря низкой проводимости воздуха являются эффективным барьером на пути теплового потока. Так, при пористости около 80% теплопроводность обычно в 8–10 раз ниже, чем у плотного материала такого же химического состава. Влияние пористости на теплопроводность зависит от формы, размеров пор и их распределения в объеме материала. В общем виде зависимость теплопроводности от пористости для изотропных материалов можно выразить следующим соотношением:
λ= λ0 (1− П) ,
п1+ аП
где λ0, λп – теплопроводность материала соответственно без пор и с порами, Вт/(м · К); П – пористость, %; а – корреляционная константа, изменяющаяся от 0,5 до 20.
Зависимость теплопроводности от температуры для некоторых видов керамических материалов представлена в табл. 37.
|
|
|
|
|
|
|
Таблица 37 |
Значения коэффициента теплопроводности |
|
||||||
|
некоторых керамических материалов |
|
|||||
|
|
|
|
|
|
|
|
|
|
|
Коэффициент теплопроводности, Вт/(м × К), |
||||
Материал |
|
|
|
при температуре, °С |
|
||
|
|
|
|
|
|
|
|
|
|
–50 |
20 |
100 |
500 |
1000 |
1500 |
|
|
|
|
|
|
|
|
Корунд |
|
50 |
33 |
29 |
12 |
9 |
7 |
Периклаз |
|
– |
40–60 |
36–38 |
13–16 |
6–8 |
6-8 |
Шпинель |
|
– |
15 |
13 |
8 |
5 |
– |
Бадделеит |
|
– |
1,7–2,0 |
1,7–2,0 |
1,7–2,0 |
1,7–2,2 |
1,8–3,3 |
Нитрид кремния |
|
– |
37–43 |
30 |
28 |
18 |
15 |
Нитрид алюминия |
|
– |
До 250 |
117 |
76 |
40 |
– |
Карбид бора |
|
– |
27 |
21 |
15 |
14 |
13 |
Карбид кремния |
|
– |
110 |
90 |
65 |
45 |
40 |
Стеатит |
|
– |
6 |
– |
3,7 |
– |
– |
Фарфор |
|
– |
– |
– |
0,65–0,8 |
0,7–0,8 |
– |
Кордиерит |
|
– |
– |
0,8 |
0,7 |
0,65 |
– |
186

Проведение анализа
Материалы и приборы: смазка теплоустойчивая ПФСМ-4 или графит, опытные образцы, измеритель теплопроводности ИТ-l-400, штангенциркуль, весы аналитические.
Для нахождения теплопроводности в измерителе теплопроводности ИТ-l-400 использован метод динамического калориметра, который позволяет получить температурную зависимость изучаемого
параметра (ГОСТ 7076). |
|
||||
Тепловая схема метода по- |
|
||||
казана на рис. 64. Как следует |
|
||||
из рисунка, испытуемый обра- |
4 |
||||
зец 3, пластина контактная 1 и |
1 |
||||
тепломер 2 разогреваются теп- |
2 |
||||
ловым |
потоком Q(t), посту- |
3 |
|||
2 |
|||||
пающим от нагревателей 4. Бо- |
|||||
1 |
|||||
ковые |
поверхности |
пластин, |
|||
4 |
|||||
тепломеров и образца адиабати- |
|
||||
чески изолированы. |
|
|
|||
Тепломер и контактная пла- |
Рис. 64. Тепловая схема определения |
||||
стина изготовлены из меди, об- |
теплопроводности: |
||||
ладающей |
высокой |
теплопро- |
1 – контактная пластина; 2 – тепломер; |
||
водностью, |
поэтому |
перепады |
3 – образец; 4 – нагреватель |
||
|
температур на них незначительны.
Тепловой поток Q(t), проходящий через поперечное сечение пластины, частично поглощается ею и далее идет на разогрев тепломера и образца.
Регистрируя величины температурных перепадов на образце и тепломере, фиксируют потери тепла при прохождении его (тепла) через образец.
По величине этих потерь можно оценить тепловое сопротивление материала, его теплопроводность.
Размеры системы выбраны таким образом, чтобы потоки, аккумулируемые образцом и пластиной, были в 5–10 раз меньше поглощаемых стержнем. В этом случае образец и пластина оказываются в тепловом потоке, близком к стационарному, и для них справедливы нижеприведенные формулы.
Теплопроводность образца l, Вт/(м × К), находится по формуле
187
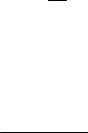
l = h ,
Po
где h – высота образца, м; Р0 – тепловое сопротивление образца (между стержнем и контактной пластиной), м2 × К/Вт.
Величина Ро определяется следующим выражением:
Po = ПоS (1 + σc ) - Pк ,
ПтKт
где По – перепад температуры на образце, дел. (число делений на приборе Ф 136); S – площадь поперечного сечения образца, м2; sс – поправка на теплоемкость образца; Пт – перепад температуры на пластине, дел. (число делений на приборе Ф 136); Kт – тепловая проводимость пластины, Вт/К; Рк – поправка, учитывающая тепловое сопротивление контакта, неидентичность и тепловое сопротивление заделки термопар, м2 × К / Вт.
Поправка sс рассчитывается по формуле
sc |
= |
Cо |
, |
|
2(Cо + Cc ) |
||||
|
|
|
||
где Со – теплоемкость образца, Дж/К; |
Сс – теплоемкость стерж- |
|||
ня, Дж/К. |
|
|
|
В свою очередь полная теплоемкость образца Со определяется из следующего выражения:
Со = Со(t)mо,
где Со(t) – ориентировочное значение удельной теплоемкости образца, Дж/(кг × К); mо – масса образца, кг.
Величины Kт, Рк и Сс являются «постоянными» для данного прибора, не зависят от свойств образца и определены предварительно в градуировочных экспериментах. Их значения приведены в табл. 38.
Измерение теплопроводности осуществляют на образцах диаметром (15 ± 0,3) мм и высотой (5 ± 0,1) мм. Отклонение от размеров и формы, шероховатости поверхностей приводят к увеличению погрешности измерений. Для улучшения теплового контакта образцов используют теплостойкую смазку ПФСМ-4, а для образцов, впитывающих смазку, – графитовый порошок или алюминиевую пудру. Охлаждение измерительной ячейки допускается проводить с помощью бытового электровентилятора.
188
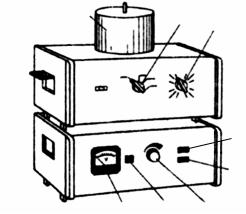
Таблица 38
Значения «постоянных» для используемого прибора
t, °C |
Рк × 104, м2 × К/Вт |
Сс, Дж/К |
Kт × 102, Вт/К |
|
|
|
|
25 |
7,6 |
15,86 |
6,15 |
50 |
6,1 |
16,54 |
7,02 |
75 |
6,1 |
16,54 |
7,02 |
100 |
5,6 |
16,87 |
8,26 |
125 |
5,6 |
16,87 |
8,26 |
150 |
5,0 |
17,08 |
8,85 |
175 |
5,0 |
17,08 |
8,85 |
200 |
4,9 |
17,21 |
9,22 |
Перед проведением испытания замеряют высоту и диаметр образца с погрешностью ±0,01 мм и взвешивают образец на аналитических весах.
Целесообразно предварительно определить теплоемкость образца. При отсутствии данных о величине истинной теплоемкости образца допускается при расчетах пользоваться ориентировочными значениями удельной теплоемкости Со(t). Полученные об образцах данные записывают по форме табл. 39.
На рис. 65 приведен внешний вид установки для определения
теплопроводности. |
|
|
|
|
|
|
|
|
|||
Перед началом испытаний под- |
|
1 |
7 |
8 |
|
||||||
нимают верхнюю половину корпуса 1 |
|
|
|
|
|||||||
|
|
|
|
|
|||||||
измерительной |
ячейки, |
протирают |
|
|
|
|
|
||||
смазкой |
контактные |
поверхности |
|
|
|
|
|
||||
стержня, пластины тепломера и ус- |
|
|
|
|
|
||||||
танавливают образец на контакт- |
|
|
|
|
|
||||||
ную пластину, а стержень – |
на кон- |
|
|
|
|
||||||
|
|
|
|
3 |
|||||||
тактные иглы термопары. |
Опуска- |
|
|
|
|
|
|||||
|
|
|
2 |
||||||||
ют верхнюю половину корпуса из- |
|
|
|
||||||||
|
|
|
|
|
|||||||
мерительной |
ячейки. |
|
Включают |
|
5 |
4 |
6 |
|
|||
измеритель и прибор Ф 136 нажа- |
|
|
|||||||||
Рис. 65. Установка для определения |
|||||||||||
тием кнопки 2 («Сеть»), устанавли- |
|||||||||||
вают переключатель |
7 |
(«Измере- |
|
теплопроводности: |
|
|
|||||
1 – корпус измерительной ячейки; |
|||||||||||
ние») в положение «tс», а пере- |
|||||||||||
2 – |
кнопка «Сеть»; 3 – сигнальная лампа; |
||||||||||
ключатель 8 («Температура») – в по- |
4 – |
кнопка «Нагрев»; 5 – |
вольтметр; |
||||||||
ложение |
«0». |
Прогревают |
прибор |
6 – |
рукоятка; 7 – кнопка «Измерение»; |
||||||
в течение 20–30 |
мин. |
|
|
|
|
8 – кнопка «Температура» |
189