
ХИМИЧЕСКАЯ технология керамики и огнеупоров
.pdfвискозиметр Энглера, секундомер, технические весы с разновесом, набор ареометров.
Навески исследуемого глинистого материала или смеси по 150 г, предварительно высушенные в сушильном шкафу при температуре 100...110° С и измельченные до прохождения через сито № 1, помещают в пронумерованные мерные цилиндры или другие сосуды вместимостью 300 мл. В первый цилиндр приливают дистиллированную воду в таком количестве, чтобы после размешивания и взбалтывания образовалась густая, но текучая суспензия. Количество воды в такой суспензии зависит от физико-химических свойств глин: для глин средней пластичности оно составляет 50–80%, а для высокопластичных – до 100–120% от массы сухой глины.
После определения количества воды для исходной суспензии готовят суспензии во всех остальных (пяти) сосудах, добавляя в каждый раствор электролита в таком количестве, чтобы концентрация электролита постепенно возрастала, например увеличивалась в каждом последующем сосуде на 0,05% таким образом, что в первом сосуде электролита будет 0%, во втором – 0,05%, в третьем – 0,1%, в шестом – 0,25% от массы сухой глины. Диапазон концентраций для различных электролитов может меняться. Дистиллированную воду вносят во все сосуды в таком количестве, чтобы общее ее содержание с учетом воды, введенной с электролитом, было таким же, как в исходной, т. е. без электролита, суспензии. Сосуды с пробами взбалтывают вручную в течение одного и того же времени, например 5 мин, так как на вязкости суспензий сказывается длительность перемешивания. Причем время от момента вливания воды в сосуд до определения вязкости должно быть во всех случаях одинаковым. Для удаления комков и равномерного истечения из вискозиметра шликер рекомендуется процедить через сито № 05.
Для установления вязкости приготовленную суспензию наливают во внутренний сосуд вискозиметра Энглера до метки, перемешивают в течение 3 мин и оставляют на 30 с в покое. Поместив под выпускное отверстие вискозиметра мерную колбу вместимостью 150 мл, поднимают деревянный или металлический штырь, освобождая выпускное отверстие вискозиметра, и одновременно фиксируют время по секундомеру, определяя продолжительность заполнения мерной колбы до метки 100 мл.
При установлении вязкости следует сделать не менее трех параллельных измерений и из них вычислить среднее значение. Затем
150
суспензию наливают в мерный цилиндр, выдерживают в покое 1 мин и измеряют ее плотность с помощью ареометра. Аналогично поступают с суспензиями всех сосудов. Вязкость обычно выражают в градусах вязкости Энглера (°Е), получаемых от деления времени истечения суспензии на время истечения того же объема воды. Поэтому в начале работы определяют время наполнения мерной колбы водой, вытекающей через выпускное отверстие вискозиметра.
После нахождения вязкости суспензии с электролитом-разжи- жителем проделывают аналогичную работу с электролитом-коагуля- тором, который вводится в тех же концентрациях, что и разжижитель. В качестве коагуляторов используют известь, СаCl2 и др. В этом случае исходная суспензия подбирается значительно более подвижная, чем при исследовании влияния разжижителя.
Результаты исследований записывают в табл. 27.
|
|
|
|
|
Таблица 27 |
Результаты определения процесса разжижения глин |
|
||||
|
|
|
|
|
|
|
Концентрация |
|
Вязкость |
|
Плотность |
Название |
электролита, |
Время истечения |
|
||
условная, |
|
шликера, |
|||
электролита |
мас. % или |
суспензии, с |
оЕ |
|
кг/м3 |
|
мг-экв |
|
|
|
|
|
|
|
|
|
|
По полученным данным строят графики разжижения или коагуляции, откладывая по оси абсцисс концентрацию электролита, а по оси ординат – вязкость суспензии. По результатам испытаний оценивают эффективность использования того или иного электролита и устанавливают его оптимальные количества.
3.9. Определение скорости набора черепка при литье водных шликеров в пористые формы
Общие сведения
Шликерное литье основано на способности компонентов керамических масс давать устойчивые суспензии в водной среде, заполнять пористую форму вследствие текучести, а также воспроизводить ее конфигурацию с образованием уплотненного пристеночного слоя.
151
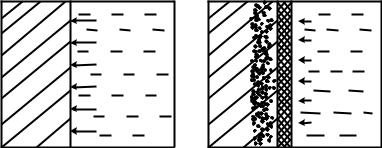
При заливке шликера в пористую форму под ее отсасывающим действием в дисперсной системе возникают микропотоки частиц, в результате чего начинается осаждение твердой фазы на внутренней поверхности формы при одновременном поглощении жидкой фазы ее порами. При этом частицы принимают уплотненное ориентированное расположение в пристеночном слое (большими плоскостями параллельно стенке). В дальнейшем фильтрация идет через набравшийся слой, процесс удаления влаги замедляется, а частицы внутренних слоев располагаются неориентированно (анизотропно), что приводит к снижению плотности внутренних слоев отливки.
Процесс образования частично обезвоженного уплотненного слоя материала на внутренней стенке пористой формы в керамической технологии называется набором черепка.
Литье изделий в пористые формы является, по существу, процессом фильтрования, происходящим в трехслойной системе: шликер – уплотненный слой – гипсовая форма. При этом пористость последней имеет исключительное значение, поскольку процесс образования черепка обеспечивает капиллярное давление, создающее мениски воды в порах гипсовой формы.
Как видно из рис. 55, с момента образования некоторого уплотненного слоя массы на поверхности формы общее сопротивление фильтрации влаги складывается из суммы:
R = Rш + Rч + Rф,
где Rш, Rч, Rф – соответственно сопротивление влагопереносу слоя шликера, черепка и формы.
а |
б |
Рис. 55. Схема процесса образования черепка на пористой форме: а – начало процесса; б – конечная стадия образования пристеночного обезвоженного слоя
152

Экспериментально установлено, что скорость удаления влаги из шликеров определяется прежде всего проницаемостью слоя черепка. Два других слагаемых играют значительно меньшую роль.
Образование слоя массы протекает тем медленнее, чем мельче частицы массы и чем выше содержание пластичных компонентов. Тонкодисперсные глинистые частицы забивают поры формы, уменьшая ее фильтрационную способность. Отливки из высокопластичных масс долго подсыхают и плохо отделяются от формы. Напротив, с повышением содержания непластичных составляющих, которые менее гидрофильны и обладают большим размером частиц, можно ускорить образование пристеночного слоя массы, что обусловлено значительным увеличением влагопроводности системы и скорости процесса фильтрации.
Температура также влияет на скорость образования массы. При повышении температуры шликера от 20 до 50°С скорость образования массы в зависимости от степени ее охлаждения в процессе литья возрастает от 50 до 100%. Это объясняется тем, что при увеличении температуры понижается вязкость воды и она быстрее отсасывается через набранный слой массы в гипсовую форму.
На практике формы часто подогревают до 60°С, что более чем в 2 раза ускоряет набор стенки изделия.
Кинетика процесса набора черепка характеризуется скоростью изменения толщины слоя во времени:
ds |
= kd |
c , |
|
||
dt |
S |
где k – коэффициент, зависящий от плотности дисперсной системы; d – коэффициент диффузии влаги через слой; c – перепад влажности от внутреннего к наружному слоям отливки, %; S – толщина набранного слоям, м.
Интегрированием уравнения получают зависимость:
S = K′τ ,
где K′ – константа процесса.
Скорость водоотдачи шликера в пористую форму и, соответственно, скорость увеличения толщины набираемого слоя определяют время отливки и являются важными характеристиками шликера. Они играют существенную роль при сравнении различных шликеров, а также при выборе оптимальных условий разжижения, кроме того, позволяют оценить работоспособность литейных форм.
153
Проведение анализа
Материалы, посуда и приборы: набор гипсовых стерженьков или тигельков, сосуд для шликера, стекло часовое – 3–5 шт., штатив, штангенциркуль, весы технические с разновесом, шкаф сушильный с терморегулятором, секундомер.
Зависимость скорости образования пристеночного слоя на пористой форме имеет сложный характер. В начальный момент соприкосновения литейного шликера с высушенной поверхностью гипсовой формы отсос воды происходит наиболее интенсивно, и скорость набора массы в это время максимальна. Затем форма постепенно насыщается водой, и ее поглотительная способность уменьшается. Кроме того, образующийся слой массы оказывает основное сопротивление процессу водоотдачи шликера. Вследствие этого скорость фильтрации и набора массы постепенно снижается во времени.
Скорость набора массы из шликера можно определять методами с использованием гипсовых тигельков и стержней. Их изготовляют из формовочного гипса, просеянного через сито № 02. Водную суспензию гипса (60 ч. по массе гипса и 40 ч. по массе воды) заливают в соответствующую форму из металла, дерева и др. После схватывания гипса стержни (тигли) вынимают из формы и высушивают при 65...70°С. Каждый стержень (тигель) можно применять для 10–15 испытаний.
При определении набора массы методом тигельков используют гипсовые тигельки в форме усеченного конуса высотой 20 мм, верхним и нижним диаметрами (внутренними) соответственно 40 и 30 мм и толщиной стенок 30 мм. Гипсовые тигли высушивают при температуре не выше 70°С, тщательно очищают от пыли, замеряют их внутренние размеры и взвешивают на технических весах с погрешностью до 0,1 г. Затем наливают в тигельки доверху шликер и оставляют их спокойно стоять.
Продолжительность выдержки для набора массы составляет 3, 5, 7 и 10 мин. Для каждой временной экспозиции должно быть использовано 3–5 тигельков. По прошествии указанного времени излишек шликера выливают, а тигельки на 2–3 мин оставляют опрокинутыми на узких деревянных рейках для окончательного стекания шликера. После этого тигельки взвешивают, определяют массу набранного керамического слоя и рассчитывают скорость его образования.
154
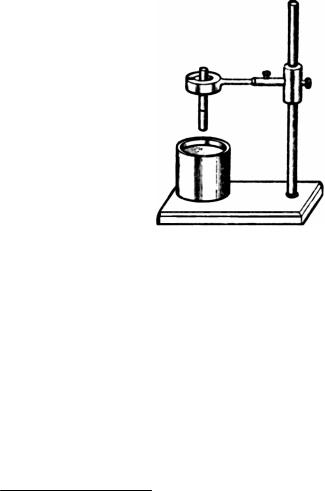
По методу |
стержней |
используют |
|
|
гипсовые стерженьки обычно диаметром |
|
|||
12–15 мм и длиной 100–120 |
мм. На рас- |
|
||
стоянии 30–35 мм от края на стержни по |
|
|||
окружности наносят карандашом метку. |
|
|||
Стержни высушивают при 70°С, измеряют |
|
|||
штангенциркулем |
размеры |
погружаемой |
|
|
части и взвешивают на технических весах |
|
|||
с погрешностью до 0,1 г. Затем стержень |
|
|||
закрепляют на штативе (рис. 56), подводят |
|
|||
под него стаканчик со шликером и точно |
|
|||
до метки погружают стержень в шликер, |
Рис. 56. Устройство |
|||
одновременно включая секундомер. Реко- |
||||
для определения скорости |
||||
мендуется набирать массу, как и при ме- |
||||
набора черепка методом |
||||
тоде тигельков, в течение 3, 5, 7 и 10 мин. |
гипсовых стержней |
|||
По истечении указанного времени стер- |
|
жень вместе с наросшим слоем керамической массы извлекают и на протяжении 2–3 мин дают стечь избытку шликера. После этого стержень с массой незамедлительно помещают на предварительно взвешенное часовое стекло и определяют массу на технических весах.
Массу набранного на гипсовый стержень (или на стенки гипсового тигля) слоя G, г, находят по формуле
G = (m − m0 )(100 − wшл ) , 100
где m0 – масса высушенного гипсового стержня (тигля), г; m – масса стержня (тигля) с набранным слоем, г; wшл – относительная влажность шликера, %.
Настоящая формула справедлива при условии, что вода, впитанная порами гипсового тела, а также находящаяся в отложившемся слое массы, в сумме соответствует относительной влажности шликера. Для каждой продолжительности набора устанавливают отношение массы набранного слоя к поверхности гипсового тела (G/S). Поверхность гипсового стержня Sc, см2, погруженную в шликер, подсчитывают с точностью до 0,1 см2:
Sc = πdh + πd 2 , 4
где d – диаметр стержня, см; h – глубина погружения стержня в шликер, см.
155
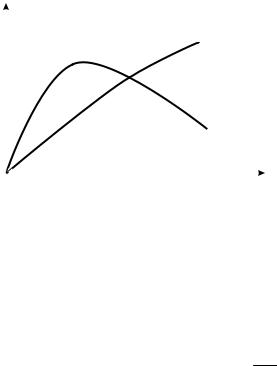
G/S |
|
υн |
|
|
|
|
|
|
|
|
Для |
гипсового |
тигля |
|||
|
|
|
|
|
|
|
G/S |
|
|
|
поверхность соприкоснове- |
|||||
|
|
|
|
|
|
|
||||||||||
|
|
|
|
|
|
|
||||||||||
|
|
|
|
|
|
|
|
|
|
|
|
|
ния со шликером Fт, см2, |
|||
|
|
|
|
|
|
|
|
|
|
|
|
|
определяют по формуле |
|||
|
|
|
|
|
|
|
|
|
|
|
|
|
Sт = |
p(d + d1 )l |
+ pd 2 , |
|
|
|
|
|
|
|
|
|
|
|
|
|
|
||||
|
|
|
|
|
|
|
|
|
|
|
|
|
|
|||
|
|
|
|
|
|
|
|
|
υн |
|
|
|
||||
|
|
|
|
|
|
|
|
|
|
|
2 |
|
4 |
|||
|
|
|
|
|
|
|
|
|
||||||||
|
|
|
|
|
|
|
|
|
|
|
|
|
где d – внутренний диаметр |
|||
|
|
|
|
|
|
|
|
|
|
|
|
|
||||
|
|
|
|
|
|
|
|
|
|
|
|
|
||||
|
|
|
|
|
|
|
|
8 τ, мин |
||||||||
2 |
4 |
6 |
|
дна тигля, см; d1 – внутрен- |
||||||||||||
Рис. 57. Зависимость набора массы |
ний диаметр верхнего осно- |
|||||||||||||||
вания, см; l – длина обра- |
||||||||||||||||
и скорости набора черепка от времени |
зующей |
внутренней |
части |
тигля, см.
Скорость набора массы Vн, г/(см2 × мин), находят по следующей формуле
V= G ,
нS1t
где S1 – поверхность гипса, соприкасающаяся со шликером, см2; τ – продолжительность набора массы, мин.
Для получения среднего значения скорости образования слоя на гипсовой форме необходимо провести не менее трех параллельных испытаний. Результаты определения заносят в табл. 28 и изображают графически (рис. 57), откладывая по оси абсцисс время набора (мин), а по оси ординат – массу слоя, приходящуюся на единицу поверхности гипса (г/см2), и скорость набора черепка (г/(см2 × мин)).
Таблица 28
Определение скорости набора массы
|
|
погружаемойВысота частиh, см |
3 |
|
|
Масса |
|
|
|
|
мин) |
|
стержня№ (тигля) |
Диаметр стержняd, см |
Времянабора массыτ, мин |
высушенногоm |
|
набраннымс |
слоемm |
Массасухого слояG, г |
Набормассы ,S/Gг/см |
Скоростьнабора |
|||
Поверхность гипсовоготеласмS, |
|
Vмассы |
||||||||||
|
|
|
|
|
стержня, г |
|
|
|
|
|||
|
|
|
|
|
0 |
|
|
|
|
2 |
|
× 2 |
|
|
|
|
|
|
|
|
|
|
|
|
/(см,г |
|
|
|
|
|
|
|
|
|
|
|
|
н |
|
|
|
|
|
|
|
|
|
|
|
|
|
156
Раздел 4. ОПРЕДЕЛЕНИЕ СВОЙСТВ КЕРАМИЧЕСКИХ МАТЕРИАЛОВ И ИЗДЕЛИЙ
4.1.Определение плотности, пористости
иводопоглощения
Общие сведения
Любой керамический материал – это, как правило, сочетание твердого вещества (кристаллического и стекловидного) с пустотами – порами. Объем пор, их размеры и характер распределения оказывают значительное влияние на ряд свойств керамических изделий и материалов. Так, например, механическая прочность керамики зависит не только от общей пористости, но и от размера пор, равномерности их распределения. Бесспорно, что с повышением пористости механическая прочность керамики уменьшается за счет увеличения дефектности структуры и снижения прочности связей. Установлено, что объем пор, заполненных водой, определяет морозостойкость строительной керамики; количество, размер и характер распределения пор во многом обусловливают шлакоустойчивость огнеупорной футеровки печей; пористость влияет на теплопроводность и звукопроводность керамических материалов.
Поры в керамике имеют разнообразную форму, очертания, неравномерно распределены по объему, поэтому полную характеристику пористости получить чрезвычайно трудно, даже при использовании современных поромеров. Несмотря на разнообразие форм, поры можно подразделить на закрытые (недоступные для проникновения в них жидкости и газа) и открытые поры, которые в свою очередь делятся на тупиковые (заполняемые жидкостью и газом, но не влияющие на проницаемость керамики) и каналообразующие (открытые с обоих концов поры, создающие поровые каналы).
Проницаемость керамики обусловливается прежде всего каналообразующими порами при наличии на их открытых концах перепадов давления. Пористость и проницаемость – важные характеристики текстуры для всех типов керамики, включающих как традиционную строительную, так и важнейшие виды технической керамики.
Поскольку прямые методы измерения пористости материалов чрезвычайно сложны, то в технологии керамики этот показатель
157
часто оценивают путем определения других свойств, непосредственно зависящих от пористости. К таким показателям относятся плотность материала (истинная, кажущаяся, относительная) и водопоглощение.
Истинная плотность ρи, кг/м3 (г/см3), является физической константой для индивидуального вещества и зависит от его строения. Для керамики эта величина находится в зависимости от плотности упаковки атомов в кристаллах и химического состава стекловидной фазы. Истинная плотность ρи определяется как отношение массы материала к его объему без учета пор.
Кажущаяся плотность ρк, кг/м3 (г/см3) – это отношение массы тела ко всему занятому им объему, включая поры.
Относительную плотность ρотн находят как отношение ка-
жущейся плотности к истинной (выражают в долях единицы или в процентах). Она представляет объемную долю твердого вещества в материале.
В технологии керамики, в справочной литературе часто встречается такой термин, как «насыпная плотность». Данный показатель характеризует укладку частиц сыпучих материалов, зерен отощителя, гранул наполнителя. Различают насыпную плотность в свободно насыпанном состоянии и с утряской. Ее определяют как отношение массы насыпанного материала к занимаемому им объему, включая поры между зернами, и выражают в тех же единицах, что и кажущуюся плотность.
Водопоглощение В, % – это отношение массы воды, поглощенной керамическим телом при полном насыщении, к массе сухого образца. Этот показатель часто используют в производственных условиях для характеристики степени спекания, качества изделий и соответствия требованиям стандарта.
Измерив вышеуказанные характеристики, можно оценить общую, открытую и закрытую пористость керамики.
Истинная, или общая, пористость Пи, % – отношение сум-
марного объема всех открытых и закрытых пор, выраженного в процентах, к общему объему материала. Эта величина численно равна сумме закрытой и открытой пористости.
Кажущаяся, или открытая, пористость Пк (По), % –
это отношение объема всех открытых пор тела (заполняемых водой при кипячении) ко всему объему материала, включая объем всех пор.
158
Закрытая пористость Пз, % – это отношение объема всех замкнутых пор тела к его объему, включая объем всех пор.
Между названными параметрами керамических изделий и материалов, исходя из указанных определений, существует взаимосвязь, которая может быть выражена следующими формулами:
ρ = |
m |
, |
ρ = |
m |
, ρ |
|
= |
ρк 100%, |
|
ν |
|
||||||
и |
νм |
к |
|
отн |
|
ρи |
||
|
|
|
|
|
|
где ρи, ρк – плотность материала соответственно истинная и кажущаяся, кг/м3; ρотн – относительная плотность, %; νм – объем материала (твердого вещества без пор), м3; ν – объем материала, включая поры, м3; m – масса материала, кг.
П = |
νп 100, |
П = |
νо 100, |
П = |
νз 100, |
|||
и |
|
ν |
к |
ν |
|
з |
|
ν |
|
|
|
|
|
|
|||
|
Пи = Пз + Пк , |
Пи = ν − νм |
100, |
|||||
|
|
|
|
|
ν |
|
|
|
где Пи, Пк, Пз – пористость материала соответственно истинная, кажущаяся, закрытая, %; νп – объем всех пор, м3; νо, νз – объем открытых и закрытых пор соответственно, м3.
|
|
П |
и |
|
|
|
ρ |
|
ρк = ρи 1 |
− |
|
|
, откуда Пи = 1 |
− |
|
к 100, |
|
|
|
|
||||||
|
|
100 |
|
|
ρи |
или
Пи = (1 – ρотн)100,
Пк = Вρк.
Зная истинную и открытую пористость, можно найти закрытую пористость из выражения: Пз = Пи – Пк.
В случае, если закрытые поры практически отсутствуют, величиины ρи, ρк и В связаны следующей приблизительной зависимостью:
|
|
|
П |
к |
|
|
1 |
|
1 |
|
ρк = ρи 1 |
− |
|
|
, |
В = 100 |
|
− |
|
. |
|
|
|
|
ρк |
|
||||||
|
|
100 |
|
|
|
ρи |
Таким образом, измерив плотность и водопоглощение керамики, можно косвенно оценить все виды ее пористости.
159