
- •Предисловие
- •1.1. Структура наполненных полимерных покрытий
- •1.2. Взаимодействие поверхности пигментов с компонентами пленкообразующих систем
- •1.3. Влияние пигментов на структуру и свойства лакокрасочных покрытий
- •2. Основы технологии производства пигментированных лакокрасочных материалов
- •2.1. Принципы выбора пигментов
- •2.3. Основы процесса диспергирования пигментов
- •2.4. Стабилизация пигментных дисперсий
- •3. Способы производства пигментированных лакокрасочных материалов
- •3.1. Пигментирование однофазных органорастворимых пленкообразующих систем
- •3.2. Пигментирование однофазных водоразбавляемых пленкообразующих систем
- •3.3. Пигментирование однофазных нелетучих пленкообразующих систем
- •3.4. Пигментирование двухфазных систем
- •3.5. Порошковые краски
- •3.6. Фляшинг-процесс
- •4. Основное оборудование для получения пигментированных лакокрасочных материалов
- •4.1. Диссольверы
- •4.2. Трехвалковые мельницы
- •4.3. Бисерные мельницы
- •4.6. Ультразвуковые диспергаторы и магнитная обработка при диспергировании пигментов
- •Заключение
- •Литература
- •Содержание
такие высокие скорости, средний размер частиц, который может быть получен, составляет все же 10 мкм и выше, что недостаточно, например, для многих ЛКМ, используемых для верхних покрытий.
При обработке пигментной пасты в диссольвере очень важна правильная установка характера потока. Диспергируемый материал должен перемещаться по спирали от стенок к диску с небольшим вздутием и ровным (ламинарным) потоком, оставляя собственно вал чистым.
Предварительными условиями для установления такого характера течения (известного как «эффект теста») являются необходимость задания вязкости на оптимальном уровне и соответствующая корректировка состава диспергируемого материала. Слишком низкая вязкость ведет к распылению и вспениванию, тогда как, если вязкость слишком высока или материал комковатый, диск вращается в «дисперсионной дыре», так как течение материала к диску прерывается.
4.2. ТРЕХВАЛКОВЫЕ МЕЛЬНИЦЫ
Трехвалковый тип мельниц сейчас редко встречается в производстве ЛКМ, хотя они все еще иногда используются в производстве типографских красок и в специальных областях промышленности ЛКМ. Одновалковые мельницы практически исчезли.
Принцип работы устройства следующий (рис. 4.4). Валки вращаются в следующем диапазоне скоростей: 40 < n1 < 100 об/мин, 140 < п2 < 200 об/мин, 300 < n3 < 600 об/мин (грубо в соотноше-
нии 1 : 3 : 9).
Валки сделаны из закаленной стали; они гладко притерты, но могут быть прижаты друг к другу. Чтобы скомпенсировать деформацию при нагрузке (примерно до 100 бар поверхностного давления), диаметр валков слегка больше в центре, чем по концам; это называется «бочковатостью».
Для того чтобы варьировать или устанавливать верхний предел температуры пасты в зазоре, валки могут охлаждаться или нагреваться водой изнутри. Валки располагаются горизонтально в небольших мельницах и наклонно в больших моделях. Параметры работы современных трехвалковых мельниц (скорости, контактное давление, ширина зазора, температура валков) могут быть, ко-
98
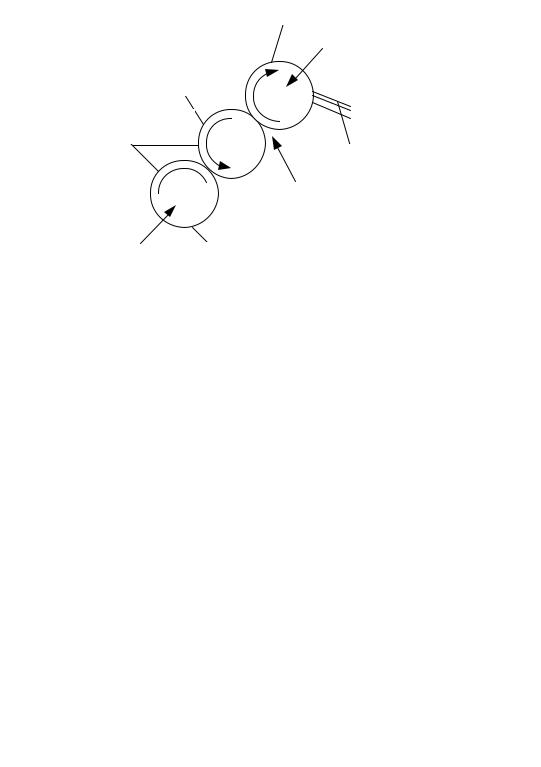
нечно, измерены, изменены и согласованы с помощью электроники. В больших трехвалковых мельницах валки могут быть до 0,5 м в диаметре и длиной примерно до 2 м.
Выпускающий валок
Центральный
валок
n3
Бункер
питателя n2
Срезающее лезвие
n1 Зазор
n1 < n2 < n3
Питающий валок
Рис. 4.4. Трехвалковая мельница:
F – контактное давление; n – скорость вращения
Диспергирующее действие трехвалковой краскотерки возникает из-за того, что три валка вращаются с разной скоростью и, таким образом, сдвигают пасту, содержащую агломераты в двух зазорах. Поскольку частицы пигмента постоянно покрыты жидкостью в этом процессе, диспергирование очень «мягкое»; между частицами пигментаи поверхностью валка практически нет сухого трения.
Теория, на которой основано диспергирование на трехвалковой краскотерке, дает следующие общие правила наиболее эффективного ее использования:
–зазор не слишком узкий (иначе количество перерабатываемого материала будет слишком малым);
–скорость не выше необходимой (для экономичности переработки);
–вязкость максимально возможная (для получения больших сдиговых сил).
В заключение рассмотрим характерные достоинства и недостатки трехвалковых краскотерок.
К числу достоинств относятся:
1) «мягкое» диспергирование, как механическое (важно для пигментов, которые чувствительны к абразивному воздействию,
99
например пигментов с обработанной поверхностью частиц), так
ипо температуре;
2)можно диспергировать пастообразные материалы;
3)аппарат простой и легко регулируемый. Недостатками являются:
– значительная неконтролируемая потеря растворителя при
использовании летучих растворителей (необходима вытяжка; содержание растворителя в пасте неизвестно);
–требуются относительно сложные системы постоянного контроля;
–сравнительно низкая производительность.
4.3.БИСЕРНЫЕ МЕЛЬНИЦЫ
Степень диспергирования частиц пигмента в диссольвере достаточна для некоторых пигментированных ЛКМ – ряда грунтовок, эмалей для разметки дорог, окраски фасадов, т. е. там, где требуется размер частиц пигмента более 50–60 мкм. Для изготовления многих пигментированных лакокрасочных материалов необходимо применять пигментные пасты с более высокой степенью дисперсности. В этом случае для диспергирования используется двухступенчатый каскад, состоящий из диссольвера и бисерной мельницы. Применение одной мельницы без диссольвера невозможно, так как на бисерную мельницу подается уже смоченный и частично дезагрегированный пигмент (пигментная паста). Бисерная мельница используется с целью окончательного измельчения агломератов пигмента – как для сокращения среднего эквивалентного диаметра частиц, так и для получения более узкого распределения их по размеру. Поскольку в ходе диспергирования при разрушении агломератов частиц выделяется значительное количество тепла, емкость с измельчаемым продуктом требуется принудительно охлаждать.
Выбор типа бисерной мельницы определяется параметрами, касающимися ее способности измельчать частицы пигмента, т. е. конструктивными особенностями аппарата, установленной мощностью, непосредственно влияющей на плотность диссипации энергии, а также параметрами производительности, характеризующими ее способность разделять продукт и мелющие тела, и возможностями системы охлаждения мельницы.
100
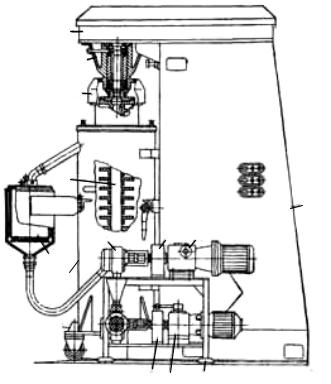
В данный момент в лакокрасочных производствах наиболее часто встречаются следующие типы бисерных мельниц: вертикальные, горизонтальные, циклические, конусные и погружные.
Вертикальные бисерные мельницы. В настоящее время на участках диспергирования пигментов ряда лакокрасочных предприятий достаточно часто встречаются вертикальные бисерные мельницы (рис. 4.5).
1
2
3
4
12
6 |
8 |
9 |
|
|
5
7
11
8 9 10
Рис. 4.5. Вертикальная бисерная мельница: 1 – привод; 2 – упорный подшипник; 3 – муфта; 4 – вал с дисками; 5 – приемник пасты; 6 – насос; 7 – размольная камера; 8 – ограждения;
9 – вариатор; 10 – станина; 11 – электродвигатель; 12 – корпус мельницы
Такая мельница состоит из цилиндрической размольной камеры 7 со сменным «стаканом», внутри которого вращается вал с дисками 4. Размольная камера установлена на колесах, закрепляется в корпусе 12, и вал ротора соединен с приводным валом эластичной передачей. Пигментная суспензия непрерывно подается насосом в нижнюю часть корпуса вертикального «стакана», заполненного на 50–60% объема бисером. Меняя производительность насоса, можно регулировать среднее время пребывания
101
пигментной пасты в рабочей камере мельницы и, тем самым, степень пасты. В верхней части корпуса паста отделяется от бисера при помощи сепаратора сетчатого типа. Корпус снабжен рубашкой охлаждения, с помощью которой поддерживается температура пигментной пасты. Охлаждение бисерной мельницы производится водой, подаваемой в рубашку охлаждения.
Основные достоинства вертикальных бисерных мельниц:
1)сравнительно простая конструкция;
2)простота обслуживания;
3)относительно малая занимаемая производственная площадь. Существенными недостатками являются:
– низкая производительность при дезагрегации паст трудно-
диспергируемых пигментов;
–невозможность использования «тяжелого» циркониевого бисера для повышения производительности мельницы;
–сильная загазованность рабочей зоны при применении сепаратора сетчатого типа;
–необходимость замывки сетки сепаратора от насыхающей пигментной пасты при работе в периодическом режиме;
–невозможность использования более эффективного противоточного режима охлаждения.
Горизонтальные бисерные мельницы. Рабочая система го-
ризонтальной бисерной мельницы состоит из герметичной цилиндрической камеры, заполненной измельчающими рабочими телами, которые приводятся в движение при помощи дисков или пальцев, расположенных на вращающемся в оси камеры валу (рис. 4.6). Рабочие тела – бисер из стекла, керамики, окиси циркония или титана различного диаметра.
Пигментная суспензия, содержащая агломераты, проходит через рабочую камеру мельницы, при этом предварительно смоченные жидкой фазой агломераты продавливаются между бисером и подвергаются измельчению. Измельченный продукт выходит из камеры через сепарирующую систему (разделительное устройство щелевого, реже – сетчатого, типа), где бисер отделяется от пигментной пасты.
В отличие от диссольвера в бисерной мельнице измельчение происходит по всему объему рабочей камеры. Зоны возникновения деструктивных срезывающих напряжений образуются между перемещающимися рабочими телами. Из-за этого величины плотности диссипации энергии значительно выше, нежели в
102
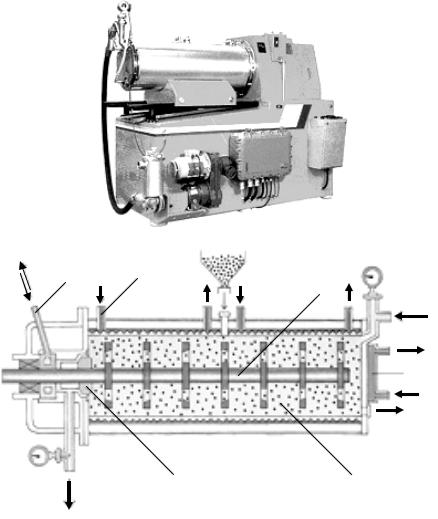
диссольвере и достигают нескольких сотен, а иногда и нескольких тысяч ватт на килограмм (Вт/кг).
|
|
|
|
а |
|
|
3 |
|
|
2 |
|
|
|
|
|
|
|
|
||
|
|
|
|
|
|
|
|
|
3 |
|
|
|
|
|
|
|
|
44 |
||
|
|
|
|
|
||
|
|
|
|
2
5 |
1 |
|
б |
Рис. 4.6. Горизонтальная бисерная мельница (а) и ее рабочая камера (б): 1 – пигментная паста и мелющие тела; 2 – охлаждение; 3 – водяной замок охлаждения; 4 – ротор с дисками; 5 – щелевой сепаратор
Горизонтальные бисерные мельницы целесообразно применять в стационарных технологических схемах для непрерывного диспергирования паст низкой и средней вязкости одного пигмента или для периодического диспергирования по дежной технологии различных пигментов общей цветовой группы, например синезеленых, красно-коричневых и т. д. Частые переходы с цвета на цвет нежелательны, так как сопряжены с длительным простоем оборудования и большим расходом растворителя на замывку.
Бисерные мельницы с зазором и циркулирующим бисе-
ром. В последние годы, наряду с бисерными мельницами горизон-
103
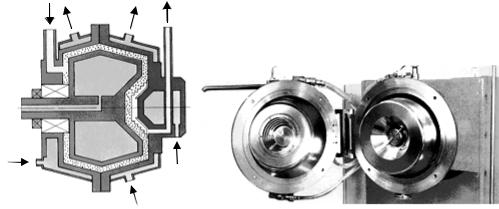
тального типа, лакокрасочная промышленность начала активно использовать и бисерные мельницы с зазором и циркулирующим бисером, называемыетакжеконуснымибисернымимельницами(рис. 4.7).
В отличие от горизонтальной бисерной мельницы рабочая камера конусного диспергатора сравнительно невелика. Она состоит из неподвижного статора и вращающегося ротора, имеющего вид усеченного конуса, отсюда и название мельницы. В узком зазоре между статором и ротором находится измельчаемый продукт и мелющие тела. В качестве мелющих тел используется только циркониевый бисер диаметром 0,8–1,2 мм. Этот узкий зазор между статором и ротором, собственно, и есть рабочий объем камеры. Применение стеклянного бисера в мельницах этого типа нецелесообразно, так как генерируемые сдвиговые усилия приводят к очень быстрому его разрушению.
а |
б |
Рис. 4.7. Конусная бисерная мельница:
а– принцип работы конусной бисерной мельницы;
б– общий вид рабочей камеры
Измельчение пигментных частиц происходит за счет мощных сдвиговых усилий, образующихся в узком пространстве рабочей камеры при вращении ротора. Во избежание перегрева пигментной пасты мельница снабжена системой охлаждения. Для разделения продукта и мелющих тел она оснащена статическим щелевым сепаратором.
Преимущества конусных бисерных мельниц:
1)быстрота и легкость замывки рабочей камеры малым количеством растворителя и перехода с цвета на цвет;
2)возможность дезагрегации труднодиспергируемых пигментов, как правило органических;
104
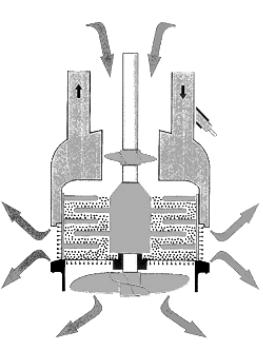
3) получение пигментных паст с узким распределением частиц по размеру.
Основная область применения бисерных мельниц с зазором и циркулирующим бисером – диспергирование вязких пигментных паст конвейерных и авторемонтных ЛКМ. Особенно эффективны эти бисерные мельницы при дезагрегации труднодиспергируемых цветных органических пигментов.
Погружные бисерные мельницы (турбо-милы). Наряду с горизонтальными и конусными мельницами в последние годы широкую популярность получили погружные бисерные диспергаторы (рис. 4.8).
Рис. 4.8. Размольная корзина погружной бисерной мельницы
Независимо от конструктивных особенностей погружных бисерных мельниц, все они работают по идентичному принципу. Рабочим органом мельниц данного типа является размольная корзина, погруженная в передвижную дежу с пигментной суспензией. В качестве мелющих тел применяется циркониевый или керамический бисер. Диспергирование пигментной пасты осуществляется непосредственно в деже, куда опускается размольная корзина.
В зависимости от конструкции погружной бисерной мельницы размольная корзина имеет два принципиально различных варианта исполнения. В одном случае она представляет собой
105
неподвижный закрытый кожух, внутри которого вращается вал, оснащенный системой пальцев. Через верхнее отверстие под действием центробежной силы, возникающей при вращении вала, суспензия пигмента поступает внутрь корзины и дезагрегируется при взаимодействии с бисером. Для усиления эффекта диспергирования на внутренней поверхности размольной корзины расположены неподвижно закрепленные контрпальцы.
В другом варианте исполнения корзина жестко закреплена на валу и вращается вместе с ним. Расположенная внутри корзины мешалка приводит в движение бисер, при этом в узком пространстве размольной корзины возникают мощные сдвиговые усилия, интенсифицирующие процесс измельчения.
На вертикальных боковых стенках размольных корзин обоих типов присутствуют узкие щели (сетка) для отделения продукта от бисера.
Если конструкцией погружного диспергатора предусмотрено охлаждение размольной корзины, то охлаждать дежу, как правило, не требуется.
Диспергирование пигментной пасты осуществляется в деже, использовавшейся ранее для приготовления суспензии пигмента на диссольвере, что дает возможность сократить число деж. Такая технология позволяет избавиться от большого числа насосов трубопроводов для перекачки пигментных паст, а размер замеса будет зависеть от объема дежи. К тому же погружные бисерные мельницы позволяют работать с пастами труднодиспергируемых пигментов. Стоит упомянуть и возможность быстрой и легкой замывки размольной корзины машины путем погружения ее в емкость с растворителем и, следовательно, простоту перехода с цвета на цвет.
Однако эксплуатация данного типа диспергирующего оборудования сопряжена с рядом ограничений, например невозможностью получения пигментных паст с узким распределением частиц по размеру, сложностью диспергирования тиксотропных пигментных паст.
Рекомендуемая область применения погружных бисерных мельниц – изготовление низко- и средневязких нетиксотропных пигментных паст широкого цветового ассортимента, зачастую на различных пленкообразователях, для авторемонтных, индустриальных и декоративно-строительных ЛКМ.
Кроме рассмотренных выше видов диспергирующего оборудования, существуют также варианты, оснащенные фрезой и раз-
106
мольной корзиной, т. е. совмещающие в себе возможности диссольвера и погружной бисерной мельницы.
Весьма важно, чтобы бисер не скапливался в сепараторе, забивая его и подвергая недопустимо высоким механическим нагрузкам; это явление известно как бисерная (гидравлическая) пробка (не относится к погружным мельницам). Чем мельче бисер, тем выше риск этого. Эмпирическое правило гласит, что бисерная пробка возникает, когда увеличение производительности вызывает рост температуры выходящей пасты. При признаках пробки следует:
–снизить количество перерабатываемой пасты;
–и/или уменьшить вязкость пасты (добавляя растворитель);
–и/или увеличить скорость ротора.
4.4.СПОСОБЫ ПОВЫШЕНИЯ ПРОИЗВОДИТЕЛЬНОСТИ ДИСПЕРГИРУЮЩЕГО ОБОРУДОВАНИЯ
Наряду с оптимальным подбором нового диспергирующего оборудования всегда следует учитывать возможность повышения производительности существующих диспергаторов без изменения конструкции аппаратов и переобвязки технологических схем. Существуют различные способы повышения производительности диспергирующего оборудования.
Для стационарных и дежных диссольверов:
1)диспергирование при оптимальной окружной скорости вращения фрезы;
2)подбор оптимальной для каждой пигментной пасты вязкости и объемного содержания пигмента;
3)применение оптимальных геометрических размеров системы фреза – дежа диссольвера.
Для бисерных мельниц всех типов:
– снижение размера мелющих тел при одновременном увеличении их плотности – переход со стеклянного бисера на стеклокерамический или циркониевый (там, где это возможно);
– оптимальное заполнение объема рабочей камеры бисерной мельницы рабочими телами;
– обеспечение оптимальной частоты вращения перемешивающего устройства (вала с пальцами или дисками, ротора) бисерных мельниц;
107
–последовательная, вместо параллельной, установка бисерных мельниц;
–оптимальная температура охлаждающей воды, что обеспечивает бесперебойную работу бисерных мельниц, которая не допускает остановки оборудования из-за превышения допустимых пределов температуры пигментной пасты;
–тщательная отработка пигментной суспензии на диссольвере перед запуском на бисерную мельницу.
4.5.ОСНОВНОЕ ОБОРУДОВАНИЕ
ДЛЯ ПРОИЗВОДСТВА ПОРОШКОВЫХ КРАСОК
Диспергирование пигментов при производстве порошковых ЛКМ происходит практически только в экструдерах (червячных смесителях). Попытки использования других видов оборудования не оправдали себя.
Основной составляющей частью экструдера является шнек, который вращается в цилиндрическом корпусе; червяк захватывает смесь смола – пигмент – наполнитель из питающего бункера и пропускает ее через цилиндрический корпус, расплавляя и смешивая (перетирая) ее по мере движения. В промышленности порошковых ЛКМ приняты два конкурирующих типа экструдеров: первый является двухшнековым экструдером с двумя совмещенными шнеками, вращающимися в одном направлении, а второй – одношнековый экструдер, в котором шнек периодически двигается назад-вперед (известный как смеситель cocompounder).
Червяки в двухшнековом экструдере снабжены в дополнение к переносящим элементам перемешивающими дисками. В одношнековом экструдере смешение возникает из-за сложной формы и характера движения шнека в сочетании со специальными выступами, закрепленными на внутренней стенке цилиндра. В отличие от экструзии пластмасс расплав порошкового ЛКМ выходит из экструдера практически без давления и затем проходит через охлаждающее устройство.
На рис. 4.9 показана диаграмма профиля температур для одношнекового экструдера, используемого для порошковых ЛКМ. Перемешивание или плавление смеси происходит исключительно
108
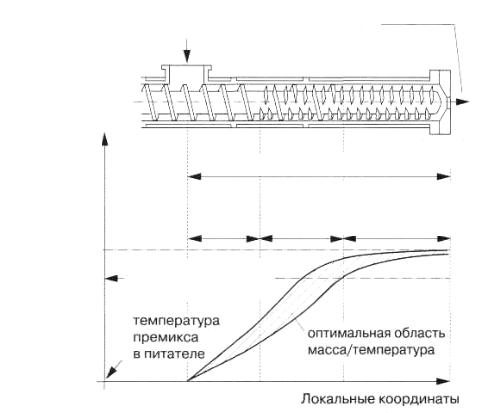
(кроме начального этапа) за счет механического сдвига и пластосмешения. Температурный профиль по длине червяка регулируется с помощью системы охлаждения цилиндра, которая может контролироваться по зонам, и системы внутреннего охлаждения шнека.
Температура
Например, 110°С
30°С
0
Горячий расплав
Премикс (из сухого смесителя)
Сопло
Рабочая зона
Зона Зона Зона пластосмешения питания пластикации и гомогенизации
Температура
пластикации
Температура |
|
|
|
|
|
|
|
|
|
|
|
премикса |
|
|
|
|
|
|
|
|
Оптимальная область |
|
|
|
|
|
|||
в питателе |
|
|
|
масса – температура |
|
|
|
|
|
|
|
|
|
|
|
|
|
|
|
|
Локальные координаты |
|
Рис. 4.9. Диаграмма профиля температур для диспергирования порошкового ЛКМ в одношнековом экструдере
За счет высоких сдвиговых сил в экструдере агломераты пигмента разрушаются вследствие отслаивающего действия снаружи вовнутрь. Силы сдвига и, соответственно, плотность диссипации энергии возрастают при увеличении скорости шнека (примерно до 400 об/мин). В то же время при 100%-ной производительности выработка (скорость потока массы) также растет, а среднее время пребывания падает. Там, где технически возможно, среднее время пребывания может быть увеличено удлинением зоны экструдирования.
Наиболее важным параметром при экструзии порошковых ЛКМ является температура расплава. Поскольку экструдируемый материал уже содержит все компоненты порошкового ЛКМ, он
109