
ИДЗ1_ТМИЭС
.pdfМИНОБРНАУКИ РОССИИ САНКТ-ПЕТЕРБУРГСКИЙ ГОСУДАРСТВЕННЫЙ ЭЛЕКТРОТЕХНИЧЕСКИЙ УНИВЕРСИТЕТ «ЛЭТИ» ИМ. В.И. УЛЬЯНОВА (ЛЕНИНА) Кафедра микро- и наноэлектроники
ОТЧЁТ по практическому заданию № 1
по дисциплине «Технология материалов и эпитаксиальных структур» Тема: Легирование кристаллов при выращивании методом Чохральского
Вариант №5
Студентка гр. 1283 |
____________________ |
Григорьева В.В. |
Преподаватель |
__________________________ |
Бобков А.А. |
Санкт-Петербург
2024
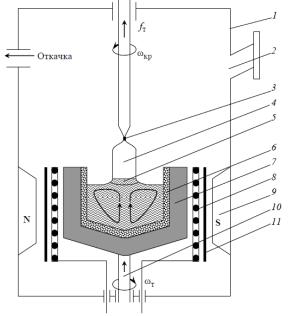
ТЕОРЕТИЧЕСКАЯ ЧАСТЬ
На рисунке 1 приведём схему установки для выращивания кристаллов
методом Чохральского.
Рисунок 1 – Схема установки для выращивания кристаллов методом Чохральского
|
Элементы установки: |
|
|
1. |
Камера роста |
2. |
Смотровое окно |
3. |
Затравка |
4. |
Монокристалл |
5. |
Переохлаждённый столбик расплава |
6. |
Тигель из кварцевого стекла |
7. |
Графитовый стакан |
8. |
Резистивный нагреватель |
9. |
Источник магнитного поля |
10. |
Устройство подъёма и вращения тигля |
11. |
Тепловые экраны |
|
|
Соотношения, используемые в расчётах.
Соотношение (1) – равновесный коэффициент распределения примеси – характеризует отношение концентрации примеси в твёрдой и жидкой фазах в условиях термодинамического равновесия.
где Ci тв
Ci ж
k0 |
= |
Ci тв |
, |
(1) |
|
||||
|
|
Ci ж |
|
–концентрация примеси в твёрдой фазе,
–концентрация примеси в жидкой фазе.
2
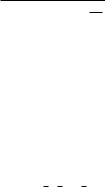
Если скорость кристаллизации имеет конечное значение, то перед фронтом кристаллизации по мере роста кристалла образуется слой расплава с эффективной толщиной δ, обогащённый или обеднённый примесью, если k0
меньше или больше единицы соответственно.
В этих условиях содержание примеси в закристаллизовавшейся части слитка Ств будет определяться концентрацией примеси в расплаве у фронта кристаллизации Ств = k0Сж0. Значение Сж0, как правило, неизвестно, поэтому в неравновесных условиях связь между концентрациями примеси в твёрдой Ств
и жидкой Сж фазах осуществляют с помощью эффективного коэффициента распределения k, который задаётся выражением (2) – уравнение Бартона-
Прима-Слихтера, связывающее равновесный и эффективный коэффициенты распределения.
k = |
|
k |
0 |
|
|
|
|
, |
|
|
|
|
|
|
|||
|
|
|
|
|
|
|
|
|
|
|
|
|
|
|
− |
f |
|
k |
|
+ (1− k |
|
)e |
D |
|
||
|
|
|
|
|||||
|
|
|
|
|
|
|
|
|
|
0 |
|
|
0 |
|
|
|
|
(2)
где f – скорость кристаллизации (0,5…5 мм/мин),
D – коэффициент диффузии примеси в жидкой фазе, см2/с,
δ – толщина диффузионного слоя, определяемая соотношением (3) (0,1…10-3 см).
1 |
1 |
− |
1 |
(3) |
|
= AD3 v 6 |
2 , |
||||
|
где А – численный коэффициент, принимающий значения 1…2 (для МЧ – 1,6), v – кинематическая вязкость жидкости, см2/с,
ω – скорость вращения кристалла относительно тигля, рад/с.
Закон распределения примеси вдоль слитка – соотношение (4) –
уравнение Галливера:
C |
тв |
0 |
( |
− g |
) |
k −1 |
, |
(4) |
|
||||||||
|
= kС |
1 |
|
|
|
где g – доля закристаллизовавшегося расплава, равная отношению текущего и начального объёмов.
Приведённый коэффициент испарения имеет смысл в случае легирования кристалла летучей примесью, он определяется соотношением (5).
3
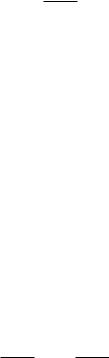
k |
|
= |
F |
, |
|
и |
fS |
||||
|
|
|
|||
|
|
|
|
(5)
где S – площадь поперечного сечения кристалла – соотношение (6),
α – линейный коэффициент испарения (коэффициент межфазного взаимодействия),
F – площадь поверхности испарения, рассчитываемая с использованием соотношения (7).
|
|
|
D |
|
S |
|
= |
2 |
, |
|
кр |
|||
|
|
|
|
|
|
кр |
|
4 |
|
|
|
|
|
(6)
где Dкр – диаметр кристалла.
F = |
|
(D |
2 |
− D |
2 |
), |
|
|
|
|
|
||
|
4 |
т |
кр |
|
||
|
|
|
|
|
|
(7)
где Dт – диаметр тигля.
Тогда имеет смысл ввести обобщённый коэффициент распределения,
учитывающий как эффективный коэффициент распределения, так и коэффициент испарения – соотношение (8).
k |
об |
= k + k |
. |
(8) |
|
и |
|
Концентрация носителей заряда может быть рассчитана с использованием соотношений (9).
n = |
1 |
|
, |
p = |
1 |
, |
e |
|
e |
||||
|
n |
|
|
p |
||
|
|
|
|
|
(9)
где е = 1,6 · 10-19 Кл, ρ – удельное сопротивление, которое может быть определено из марки
выращиваемого полупроводника,
μn и μp – подвижности электронов и дырок в полупроводнике при определённой температуре.
4

РАСЧЁТНАЯ ЧАСТЬ
Параметры, используемые в расчётах – таблица 1
Таблица 1 – Используемые значения параметров для Ge, легированного Ga, и для Ge,
легированного Sn
Материал |
ν 103, |
см2 |
|
k0 102 |
D 104, |
см2 |
|
α 104, |
см |
||
|
|
с |
|
||||||||
с |
с |
||||||||||
|
|
|
|
|
|
|
|||||
|
|
|
|
|
|
|
|
|
|
|
|
Ge − Ga |
1,35 |
|
8,7 |
0,7 |
|
|
- |
|
|
||
|
|
|
|
|
|
|
|
|
|||
Ge − Sn |
|
2 |
1,26 |
|
1,2 |
|
|
||||
|
|
|
|
|
|
||||||
|
|
|
|
|
|
|
|
|
|
|
1. Построить зависимость Ств(g) для различных скоростей кристаллизации Ge, легированного Ga. Скорость вращения кристалла относительно тигля 60 об/мин. Скорость кристаллизации 0,5; 5; 10 мм/мин.
Начальная концентрация примеси в расплаве 1015 см-3. Построить график зависимости kэфф как функции скорости кристаллизации при скорости вращения кристалла относительно тигля 60 об/мин. Для указанных скоростей кристаллизации записать в таблицу значения kэфф.
Таблица 2 – Расчётные значения kэфф для различных скоростей кристаллизации
Скорость кристаллизации |
0,5 |
5 |
10 |
|
f, мм/мин |
||||
|
|
|
||
|
|
|
|
|
kэфф · 103 |
95,63 |
212,54 |
433,26 |
1) Переведём заданные величины – скорости кристаллизации fi и
скорость вращения кристалла относительно тигля ω – в удобные для расчёта
единицы измерения:
|
|
|
|
|
об |
|
|
|
|
2π рад |
|
|
рад |
|
|
|
|
|
|
|||||||||||||||||
ω = 60 |
|
|
|
|
= 60 |
|
|
|
|
|
|
|
|
|
|
≈ 6,283 |
|
|
|
, |
|
|
|
|
|
|
||||||||||
мин |
60 |
|
|
|
|
с |
|
с |
|
|
|
|
|
|
|
|
||||||||||||||||||||
|
|
мм |
|
|
|
|
|
|
10−1 |
|
см |
≈ 8,33 10−4 |
|
см |
||||||||||||||||||||||
f = 0,5 |
|
|
|
|
|
= 0,5 |
|
|
|
|
|
|
|
|
|
|
|
|
|
|
|
|
, |
|||||||||||||
|
|
|
|
|
|
|
|
|
|
|
|
|
|
|
|
|
|
|
|
|
||||||||||||||||
1 |
|
мин |
|
|
|
|
|
|
60 |
|
|
|
с |
|
|
|
|
|
|
|
|
|
с |
|
||||||||||||
|
|
|
|
|
|
|
|
|
|
|
|
|
|
|
|
|
|
|
|
|
||||||||||||||||
|
|
|
мм |
|
|
|
|
|
10−1 см |
|
|
|
|
см |
|
|
|
|
||||||||||||||||||
f2 |
= 5 |
|
|
|
|
|
= 5 |
|
|
|
|
|
|
|
|
|
|
|
≈ 8,33 10−3 |
|
|
|
|
|
, |
|
|
|||||||||
мин |
60 |
|
|
с |
|
|
|
с |
|
|||||||||||||||||||||||||||
|
|
|
|
|
|
|
|
|
|
|
|
|
|
|
|
|
|
|
|
|
||||||||||||||||
|
|
|
|
мм |
|
|
|
|
|
|
|
10−1 см |
|
≈ 17 10−3 |
|
см |
|
|||||||||||||||||||
f3 |
= 10 |
|
|
|
|
|
|
= 10 |
|
|
|
|
|
|
|
|
|
|
|
|
|
|
|
|
|
|
, |
|
|
|||||||
|
мин |
60 |
|
|
|
|
с |
|
|
|
с |
|
|
|||||||||||||||||||||||
|
|
|
|
|
|
|
|
|
|
|
|
|
|
|
|
|
|
|
|
|
|
|||||||||||||||
ωkэфф(f) = 60 |
об |
|
= 60 |
|
2π |
|
рад |
≈ 6,283 |
|
рад |
. |
|
||||||||||||||||||||||||
мин |
|
60 |
|
|
|
|||||||||||||||||||||||||||||||
|
|
|
|
|
|
|
|
|
|
|
|
|
|
|
|
|
|
с |
|
|
|
с |
|
|
|
|
||||||||||
|
|
|
|
|
|
|
|
|
|
|
5 |
|
|
|
|
|
|
|
|
|
|
|
|
|
|
|
|
|
|
|
|
|
|
|
|
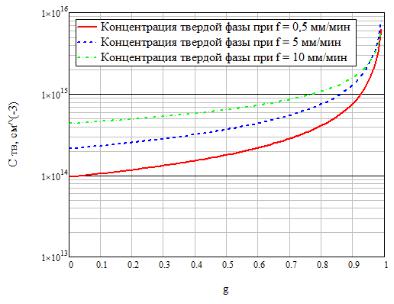
2) Рассчитаем значение толщины диффузионного слоя δ для первого случая – ω = 60 об/мин. Учтём, что для метода Чохральского – А = 1,6:
1 |
1 |
1 |
1 |
1 |
1 |
≈ 8,746 10−3см. |
δ = AD3ν6ω−2 |
= 1,6 (0,7 ∙ 10−4)3 |
(1,35 10−3)6 |
(6,283)−2 |
3) Проведём расчет значений эффективного коэффициента распределения kэфф для различных значений скорости кристаллизации:
k1 |
= |
|
|
|
|
|
k0 |
|
|
|
|
|
|
= |
|
8,7 10−2 |
|
|
|
|
|
|
|
|
|
||
|
|
|
|
|
|
|
|
|
f1δ |
|
|
|
|
|
−4 |
|
|
−3 |
|||||||||
эфф |
|
|
k |
|
|
+ (1 − k |
|
)e− |
|
|
8,7 10−2 + (1 − 8,7 10−2) exp (− |
8,33 10 |
8,746 10 |
||||||||||||||
|
|
|
0 |
0 |
D |
|
|
|
|
) |
|||||||||||||||||
|
|
|
|
|
|
|
|
|
|
|
|
|
|
|
|
|
0,7 ∙ 10−4 |
|
|
|
|||||||
|
|
|
|
|
|
|
|
≈ 0,09563, |
|
|
|
|
|
|
|
|
|
|
|
|
|
||||||
k2 |
= |
|
|
|
|
|
k0 |
|
|
|
|
|
|
= |
|
8,7 10−2 |
|
|
|
|
|
|
|
|
|
||
|
|
|
|
|
|
|
|
|
f2δ |
|
|
|
|
|
−3 |
|
|
−3 |
|||||||||
эфф |
|
|
k |
|
|
+ (1 − k |
|
)e− |
|
|
8,7 10−2 + (1 − 8,7 10−2) exp (− |
8,33 10 |
8,746 10 |
||||||||||||||
|
|
|
0 |
0 |
D |
|
|
|
|
) |
|||||||||||||||||
|
|
|
|
|
|
|
|
|
|
|
|
|
|
|
|
|
0,7 ∙ 10−4 |
|
|
|
|||||||
|
|
|
|
|
|
|
|
≈ 0,21254, |
|
|
|
|
|
|
|
|
|
|
|
|
|
||||||
k3 |
|
= |
|
|
|
|
k0 |
|
|
|
|
|
|
|
= |
8,7 10−2 |
|
|
|
|
|
|
|
|
|
||
|
|
|
|
|
|
|
|
|
|
f3δ |
|
|
|
−3 |
|
|
−3 |
||||||||||
эфф |
|
|
k |
|
|
+ (1 − k |
|
)e− |
|
|
8,7 10−2 + (1 − 8,7 10−2) exp (− |
17 10 |
8,746 10 |
||||||||||||||
|
|
|
|
0 |
0 |
D |
|
|
|
|
|
|
) |
||||||||||||||
|
|
|
|
|
|
|
|
|
|
|
|
|
|
|
|
|
0,7 ∙ 10−4 |
|
|
|
≈0,43326.
4)Полученным значениям эффективного коэффициента
распределения сопоставим зависимости концентрации твёрдой фазы Ств(g) = kC0(1–g)k–1. Полученные зависимости аналитически представим на рисунке 1:
Рисунок 1 – График зависимостей концентрации твёрдой фазы от соотношения объёма
твёрдой фазы и полного объёма при различных скоростях кристаллизации
6
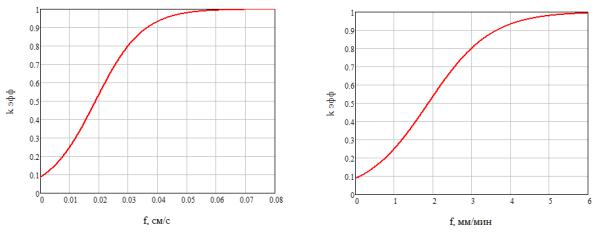
5) Построим график зависимости эффективного коэффициента распределения kэфф от скорости кристаллизации f при скорости вращения кристалла относительно тигля ω = 60 об/мин на рисунке 2:
а) б)
Рисунок 2 – Графики зависимостей эффективного коэффициента распределения от скорости кристаллизации при скорости вращения кристалла относительно тигля 60 об/мин
(а – скорость кристаллизации в см/с, б – скорость кристаллизации в мм/мин)
7

2. Построить зависимость Ств(g) для различных скоростей кристаллизации Ge, легированного Ga. Скорость кристаллизации 3 мм/мин.
Скорость вращения кристалла относительно тигля составляет 20; 50; 120
об/мин. Начальная концентрация примеси в расплаве 1015 см-3. Построить графики зависимости толщины диффузионного слоя δ и kэфф как функции скорости вращения кристалла относительно тигля при скорости кристаллизации 3 мм/мин. Для указанных скоростей кристаллизации записать в таблицу значения δ и kэфф.
Таблица 3 – Расчётные значения kэфф и δ для различных относительных скоростей вращения кристалла относительно тигля
ω, об/мин |
20 |
50 |
120 |
|
|
|
|
kэфф · 103 |
219,454 |
158,889 |
129,081 |
|
|
|
|
δ, см |
15,148 10−3 |
9,58 10−3 |
6,184 10−3 |
1) Переведём заданные величины – скорости кристаллизации fi и
скорость вращения кристалла относительно тигля ω – в удобные для расчёта единицы измерения:
|
|
мм |
|
|
|
10−1 см |
≈ 5 10−3 |
см |
||||||||||||||||||||
f = 3 |
|
|
|
|
= 3 |
|
|
|
|
|
|
|
|
|
|
|
|
|
, |
|
|
|
||||||
мин |
60 с |
|
|
с |
|
|||||||||||||||||||||||
|
|
|
|
|
|
|
|
|
|
|
|
|
|
|
||||||||||||||
ω1 |
= 20 |
об |
= 20 |
2π рад |
≈ 2,094 |
|
рад |
, |
|
|||||||||||||||||||
мин |
60 |
|
|
|
|
с |
|
|
|
|||||||||||||||||||
|
|
|
|
|
|
|
|
|
|
|
|
|
с |
|||||||||||||||
ω2 |
= 50 |
об |
= 50 |
2π рад |
≈ 5,236 |
|
|
рад |
, |
|
||||||||||||||||||
мин |
60 |
|
|
|
|
с |
|
|
|
|||||||||||||||||||
|
|
|
|
|
|
|
|
|
|
|
|
|
с |
|||||||||||||||
ω3 = 120 |
|
об |
|
= 120 |
2π |
|
рад |
≈ 12,566 |
рад |
. |
||||||||||||||||||
мин |
|
|
|
|||||||||||||||||||||||||
|
|
|
|
|
60 |
|
|
с |
|
|
|
|
|
с |
2) Рассчитаем значение толщин диффузионного слоя δ для всех случая. Учтём, что для метода Чохральского – А = 1,6:
δ |
|
1 1 |
−1 |
|
1 |
|
1 |
|
1 |
≈ 15,148 10−3см, |
|||
= AD3ν6ω |
2 |
= 1,6 (0,7 ∙ 10−4)3 |
(1,35 10−3)6 (2,094)−2 |
||||||||||
1 |
|
|
|
1 |
|
|
|
|
|
|
|
|
|
δ |
|
1 |
1 |
|
−1 |
|
1 |
|
1 |
|
1 |
≈ 9,58 10−3см, |
|
2 |
= AD3 |
ν6ω |
2 |
= 1,6 (0,7 ∙ 10−4)3 |
(1,35 10−3)6 |
(5,236)−2 |
|||||||
|
|
|
|
2 |
|
|
|
|
|
|
|
|
|
δ |
|
1 1 |
−1 |
|
1 |
|
1 |
|
|
1 |
≈ 6,184 10−3см. |
||
= AD3ν6ω |
2 |
= 1,6 (0,7 ∙ 10−4)3 |
(1,35 10−3)6 |
(12,566)−2 |
|||||||||
2 |
|
|
|
3 |
|
|
|
|
|
|
|
|
|
8
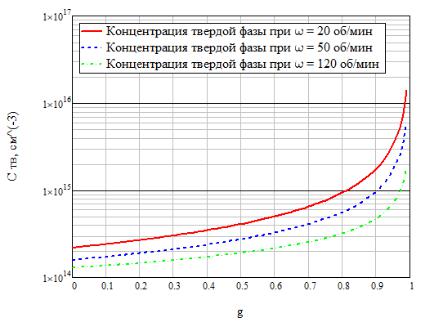
3) Проведём расчет значений эффективного коэффициента
распределения kэфф для различных значений скорости кристаллизации:
k1 |
= |
|
|
|
|
|
|
k0 |
|
|
|
|
|
|
|
= |
|
|
8,7 10−2 |
|
|
|
|
|
|
|
|
|
|
|
|
|||
|
|
|
|
|
|
|
|
|
|
|
|
|
|
|
|
|
|
−3 |
|
|
|
|
|
−3 |
||||||||||
эфф |
|
|
k |
|
|
+ (1 − k |
|
|
|
|
|
fδ1 |
|
8,7 10−2 + (1 − 8,7 10−2) exp (− 5 10 |
15,148 10 |
|||||||||||||||||||
|
|
|
0 |
0 |
)e− |
D |
|
|
|
|
) |
|||||||||||||||||||||||
|
|
|
|
|
|
|
|
|
|
|
|
|
|
|
|
|
|
|
|
|
0,7 ∙ 10−4 |
|
|
|
|
|
||||||||
|
|
|
|
|
|
|
|
|
≈ 0,21945, |
|
|
|
|
|
|
|
|
|
|
|
|
|
|
|
|
|||||||||
k2 |
|
= |
|
|
|
|
k0 |
|
|
|
|
|
|
|
|
= |
8,7 10−2 |
|
|
|
|
|
|
|
|
|
|
|
|
|||||
|
|
|
|
|
|
|
|
|
|
|
|
fδ1 |
|
|
|
|
−3 |
|
−3 |
|||||||||||||||
эфф |
|
|
|
k |
|
|
+ (1 − k |
|
|
|
|
|
|
8,7 10−2 + (1 − 8,7 10−2) exp (− |
5 10 |
9,58 10 |
||||||||||||||||||
|
|
|
|
|
0 |
0 |
)e− D |
|
|
|
|
|
|
|
|
) |
|
|||||||||||||||||
|
|
|
|
|
|
|
|
|
|
|
|
|
|
|
|
|
|
|
|
|
0,7 ∙ 10−4 |
|
|
|
|
|
||||||||
|
|
|
|
|
|
|
|
|
≈ 0,15889, |
|
|
|
|
|
|
|
|
|
|
|
|
|||||||||||||
k3 |
|
= |
|
|
|
|
|
|
k0 |
|
|
|
|
|
|
|
|
|
= |
|
|
8,7 10−2 |
|
|
|
|
|
|
|
|
|
|
|
|
|
|
|
|
|
|
|
|
|
|
|
|
|
|
fδ1 |
|
|
|
|
|
−3 |
|
|
|
−3 |
||||||||||
эфф |
|
|
|
k |
|
|
+ (1 − k |
|
|
|
)e− |
|
|
8,7 10−2 + (1 − 8,7 10−2) exp (− 5 10 |
6,184 10 |
|||||||||||||||||||
|
|
|
|
0 |
0 |
D |
|
|
|
|
|
|
) |
|||||||||||||||||||||
|
|
|
|
|
|
|
|
|
|
|
|
|
|
|
|
|
|
|
|
0,7 ∙ 10−4 |
|
|
|
|
|
≈0,12908.
4)Полученным значениям эффективного коэффициента
распределения сопоставим зависимости концентрации твёрдой фазы Ств(g) = kC0(1–g)k–1. Полученные зависимости аналитически представим на рисунке 1:
Рисунок 3 – График зависимостей концентрации твёрдой фазы от соотношения объёма
твёрдой фазы и полного объёма при различных скоростях кристаллизации
9
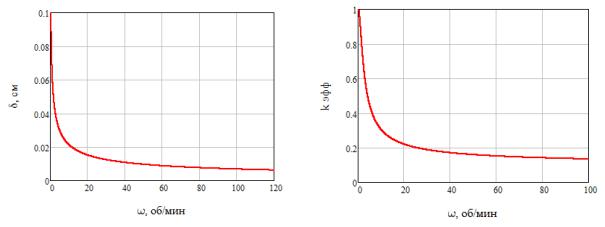
5) Построим график зависимости эффективного коэффициента распределения kэфф и диффузионного слоя δ от скорости вращения кристалла относительно тигля ω при скорости кристаллизации f = 3 мм/мин при на рисунке 2:
а) б)
Рисунок 4 – Графики зависимостей эффективного коэффициента распределения от скорости вращения кристалла относительно тигля при скорости кристаллизации 3 мм/мин
(а – толщина диффузионного слоя, б – эффективный коэффициент распределения)
10