
2336
.pdfров, поэтому допуски остаются прежними. Требования к макрогеометрии, шероховатости, твердости и износостойкости поверхности не меняются.
Какую деталь надо заменить и какую восстановить, решают в основном исходя из экономических соображений. Более дорогую деталь почти во всех случаях целесообразно оставить и обработать, а дешевую – заменить. Следует заметить, что деталь с несколькими соединяемыми поверхностями может выступать в роли заменяемой или восстанавливаемой. Например, поршень по отношению к гильзе – заменяемая деталь, а по отношению к поршневым кольцам увеличенной толщины – восстанавливаемая. Канавки в поршне протачивают под кольца ремонтного размера по толщине. Отверстие в бобышках также может быть развернуто под палец большей размерной группы.
Стандартные ремонтные размеры широко используют для соединений коленчатыйвал– вкладыш, гильза– поршень, поршень– поршневойпалецидр.
Число стандартных ремонтных размеров для соединений одного и того же вида, но для машин разных марок неодинаково и зависит от многих факторов: износа деталей, при котором должна быть прекращена эксплуатация соединения; однородности материала детали по глубине от поверхности; точности оборудования и инструмента, применяемого при обработке детали под ремонтный размер и изготовлении заменяемых деталей; конструктивной прочности деталей; ограничений, накладываемых рабочими процессами самих машин, и пр.
К недостаткам метода ремонтных размеров относят: осложнения в организации ремонта, вызванные ограниченной взаимозаменяемостью; понижение ресурса соединений из-за возрастания удельных нагрузок (например, из-за уменьшения диаметра шейки коленчатого вала при одновременном увеличении массы поршня ремонтного размера); необходимость переналадки оборудования; затраты на маркировку.
Обработкой под ремонтный размер восстанавливают кинематические пары типа вал – втулка, поршень – цилиндр и т.п. Под ремонтный размер обычно обрабатывают наиболее сложную и дорогостоящую деталь пары, а вторую заменяют новой или восстановленной также до ремонтного размера. Данный способ позволяет восстановить геометрическую форму, требуемую шероховатость и параметры точности изношенных поверхностей деталей.
Различают регламентированные и нерегламентированные ремонтные размеры. Регламентированные ремонтные размеры и допуски на них устанавливает предприятие-изготовитель. Детали с регламентированными размерами выпускает промышленность. К ним относятся поршни, поршневые кольца, поршневые пальцы, тонкостенные вкладыши подшипников шеек коленчатого вала. Применительно к этим размерам ремонтные предприятия ремонтируют под соответствующие регламентированные (заранее установленные) ремонтные размеры соединенные детали: цилиндры блока
211
двигателя, отверстия в верхней головке шатуна, шейки коленчатых валов. В соединенных деталях с такими размерами сохраняется класс точности и посадка, предусмотренные в рабочих чертежах.
Примером регламентированных ремонтных размеров являются размеры шеек коленчатых валов автомобильных двигателей.
Нерегламентированными называют ремонтные размеры детали, установленные для подгонки детали «по месту». В этом случае ремонтируемую деталь обрабатывают лишь до получения правильной геометрической формы и требуемой шероховатости поверхности.
Примером может служить обработка рабочей фаски седла в головке цилиндров лишь до выведения следов износа, к которой затем «по месту» притирается клапан двигателя. Обработка деталей под ремонтные размеры имеет следующие преимущества: увеличивается срок службы сложных и дорогих деталей, повышается качество ремонта.
Наряду с преимуществами этот способ имеет и недостатки. К ним относятся: ограничение взаимозаменяемости отремонтированных деталей, которое усложняет ремонт машин и особенно снабжение запасными частями из-за увеличения номенклатуры деталей; снижение износостойкости некоторых деталей после снятия поверхностного слоя металла.
Значение и число регламентированных ремонтных размеров зависят от износа деталей за межремонтный период, от припуска на механическую обработку и от запаса прочности детали или глубины термической обработки ее поверхностного слоя.
Износ устанавливают замером детали соответствующим инструментом. Припуск на обработку назначают с учетом характера обработки, типа оборудования, размера и материала детали. Задавая припуск на обработку, следует иметь в виду искажения геометрической формы детали, ее овальность и конусность. Припуск должен способствовать получению правильной геометрической формы изношенной поверхности детали после механической обработки, без наличия следов износа на ее рабочей поверхности.
Метод определения значения и количества ремонтных размеров для вала и отверстия был впервые разработан проф. В. В. Ефремовым. Если обозначить (рис. 9.1) через dH и DH соответственно размеры вала и отверстия по рабочему чертежу, dp1 и Dp1 – первые ремонтные размеры вала и отверстия, Иmin и Иmах – минимальный и максимальный износ поверхности детали на сторону, а через Z – припуск на механическую обработку на сторону, то первый ремонтный размер может быть определен по формулам:
для наружных цилиндрических поверхностей (валов)
dp1=dH–2(Иmax+Z); |
(9.1) |
для внутренних цилиндрических поверхностей (отверстий) |
|
Dр1=DН+2(Иmax+Z). |
(9.2) |
212
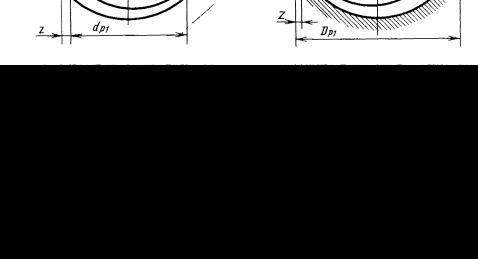
Припуск на механическую обработку зависит от вида обработки: при чистовой обточке и расточке он составляет 0,05–0,1 мм, при шлифовании – 0,03 - 0,05 мм на сторону.
Определить неравномерный односторонний износ можно только одноконтактным измерительным прибором (индикатор и т.п.). В связи с тем что на производстве валы и втулки обычно измеряют двухконтактным инструментом (микрометром, индикатором-нутромером), для упрощения пользования формулами (9.1) и (9.2) в них вводят коэффициент неравномерности износа ß, который равен отношению максимального одностороннего износа к износу на диаметр:
ß=Иmax/И. |
(9.3) |
При симметричном износе детали, когда Иmax=Иmin/2, коэффициент неравномерности износа ß=Иmax/И=0,5. При одностороннем износе, когда Иmin=0, a Иmах=И, коэффициент неравномерности износа ß=Иmax=1.
Таким образом, значения коэффициента неравномерности износа могут изменяться в пределах от 0,5 до 1.
Рис. 9.1. Определение ремонтных размеров: а – для вала; б – для отверстия
Для конкретных деталей значения этого коэффициента устанавливают опытным путем.
Найдя из уравнения (9.3) значение Иmах и подставив его в выражения
(9.1) и (9.2), получим:
dp1=dH–2(ßИ+Z); Dp1=DH+2(ßИ+Z). (9.4)
Вэтих формулах член 2(ßИ+Z) называется межремонтным интервалом
иобознычается – γ (гамма).
Следовательно, расчетные формулы для определения ремонтных размеров можно представить окончательно в следующем виде:
213

для наружных цилиндрических поверхностей (валов)
|
d p1 dH ; |
|
|
|
|
d p2 dH 2 ; |
|
|
|
|
......................; |
|
|
(9.5) |
|
......................; |
|
|
|
|
d pn dH n ; |
|
|
|
для внутренних цилиндрических поверхностей (отверстий) |
|
|||
|
Dp1 DH ; |
|
|
|
|
Dp2 DH 2 ; |
|
|
|
|
......................; |
|
|
(9.6) |
|
......................; |
|
|
|
|
d pn dH n ; |
|
|
|
где n – число ремонтных размеров. |
|
|
|
|
Число ремонтных размеров может быть найдено по формулам: |
|
|||
для валов |
nВ (dН dmin ) |
; |
|
(9.7) |
для отверстий |
nОТВ (Dmax DH ) |
, |
(9.8) |
где dmin – минимально допустимый диаметр вала, мм;
Dmax – максимально допустимый диаметр отверстия, мм.
Предельные значения диаметров dmin и Dmax определяют по условиям прочности детали, из конструктивных соображений или исходя из минимально допустимой толщины слоя химико-термической обработки поверхности детали.
Обработка под ремонтный размер широко практикуется при восстановлении изношенных поверхностей цилиндров или гильз цилиндров автомобильных двигателей. Технологический процесс включает в себя расточную и хонинговальную операции. Расточка проводится на вертикальных алмазно-расточных станках моделей 278, 278Н, 2А78Н и многошпиндельных полуавтоматах.
9.2. Восстановление способом дополнительной ремонтной детали
Этот способ – разновидность способа ремонтных размеров. Его применяют при постановке втулок в гнезда под наружные кольца подшипников коренных опор коленчатого вала двигателя; установке полуколец под
214
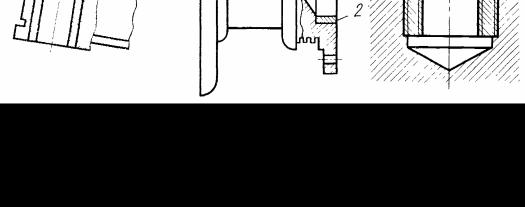
вкладыши коренных опор коленчатого вала двигателей и закреплении их штифтами; запрессовке сухих гильз или втулок в гильзы, исчерпавшие ресурс последнего стандартного ремонтного размера; установке всевозможных дополнительных колец, накладок и т.п. Способ получает все большее распространение в ремонтной практике, поскольку позволяет «вернуться» при ремонте к номинальным размерам заменяемых деталей (поршней, вкладышей, толкателей и пр.) со всеми вытекающими отсюда положительными последствиями, касающимися условий работы соединений, предусмотренных при конструировании. В связи с этим можно также говорить об улучшении условий взаимозаменяемости.
Недостаток этого способа – определенное ухудшение условий теплопередачи, например, от запрессованной сухой гильзы или свернутой втулки к материалу гильзы или блоку цилиндров двигателя, что при прочих равных условиях может приводить к форсированному изнашиванию зеркала или даже задирам.
Дополнительные ремонтные детали (ДРД) применяют для компенсации износа рабочих поверхностей деталей, а также при замене изношенной или поврежденной части детали. В первом случае ДРД устанавливают непосредственно на изношенную поверхность детали. Этим способом восстанавливают посадочные отверстия под подшипники качения в картерах коробок передач, задних мостов, ступицах колес, отверстия с изношенной резьбой и другие детали.
В зависимости от вида восстанавливаемой поверхности ДРД могут иметь форму гильзы, кольца, шайбы, пластины, резьбовой втулки или спирали (рис. 9.2).
Рис. 9.2. Дополнительные ремонтные детали (ДРД): 1 и 2 – втулки; 3 – ввертыш
Разновидностью способа ДРД является пластинирование – способ облицовки рабочих поверхностей деталей машин тонкими износостойкими легкосменяемыми пластинами. Областью его применения является производство и ремонт машин, имеющих детали с интенсивно изнашивающимися поверхностями в виде гладких замкнутых и разомкнутых цилиндрических и конических отверстий, а также плоских поверхностей.
215

Виды пластинирования деталей машин показаны на рис. 9.3.
Рис. 9.3. Формы пластин при различных видах пластинирования деталей машин: 1, 2 и 3 – разновидности поясов, изготовленных из пластин; 4 – пластины, подготовленные для продольного пластинирования внутренних цилиндрических поверхностей; 5 и 6 – спирали, предназначенные для облицовки соответственно внутренних и наружных цилиндрических поверхностей; 7 и 8 – пластины для пластинирования разомкнутых цилиндрических поверхностей;
9 и 10 – соответственно плоская пластина и деталь, подлежащая облицовке; 11 и 12 – облицовочная пластина и деталь, предназначенная для передачи крутящего момента
Базой для объединения различных технологий пластинирования в виды по эксплуатационно-ремонтным признакам является цель, достигаемая при помощи пластинирования в процессе эксплуатации и ремонта машины.
По этим признакам различают износостойкое (ресурсоувеличивающее), восстановительное (ресурсовосстанавливающее) и регулировочное пластинирование.
Износостойкое пластинирование применяют для увеличения ресурса деталей, повышения их ремонтопригодности, для компенсации износов соединенных деталей. Восстановительное пластинирование позволяет неоднократно восстанавливать ресурс деталей, как не подвергавшихся ранее пластинированию, так и уже пластинированных. Регулировочное пластинирование применяется для получения требуемых зазоров и натягов в соединяемых деталях в результате подбора при сборке толщины регулировочных прокладок. Регулировочным пластинированием можно также компенсировать износ деталей.
Технологические признаки учитывают сходство формы и процессов обработки пластин, а также способы установки их на рабочую поверхность. По способам установки пластин на рабочую поверхность пластинирование бывает напряженным, свободным и связанным.
216
Напряженным пластинированием называется способ, при котором пластину перед установкой на поверхность детали обжимают и устанавливают на деталь в напряженном состоянии. Фиксация пластины производится в результате действия сил трения. Напряженное пластинирование делится на поясное, продольное (осевое) и спиральное.
Поясное пластинирование предусматривает установку на внутренние цилиндрические и конические поверхности отверстий одной или нескольких пластин – поясов, расположенных перпендикулярно к образующей отверстия. В случае применения нескольких поясов стыки их концов располагаются вдоль образующей под углом: при двухпоясном пластинировании – 180 °С, при трехпоясном – 120 °С, при четырехпоясном – 90°.
Формы пластин, применяемых для поясного пластинирования, показаны на рис. 9.3 а. Поясным пластинированием можно восстанавливать гильзы цилиндров и цилиндры автомобильных двигателей, цилиндры автомобильных компрессоров, тормозные цилиндры гидравлической тормозной системы автомобилей.
Продольное или осевое пластинирование применяется для восстановления внутренних поверхностей длинных отверстий, в которых затруднительно использовать поясное пластинирование из-за большого числа поясов. При продольном пластинировании стыки пластин располагаются только вдоль оси отверстия. Комплект пластин для сохранения продольной устойчивости вводят в отверстие вместе с поддерживающей оправкой. Наружный диаметр свернутого комплекта пластин должен быть больше внутреннего диаметра отверстия детали на размер натяга. Формы пластин, применяемых для продольного пластинирования, показаны на рис. 9.3 б.
Спиральное пластинирование заключается в том, что на внутреннюю или наружную поверхность детали устанавливают по винтовой линии тонкую стальную пластину, имеющую форму удлиненного параллелограмма. При этом витки спирали располагаются под углом к плоскости, перпендикулярной к оси цилиндра. Для удержания пластины требуется дополнительное крепление. Пластины для спирального пластинирования показаны на рис. 9.3 в. Этот способ целесообразно использовать для восстановления цилиндрических деталей, длина которых более чем в 4 раза превышает их диаметр, например, для восстановления гидросиловых цилиндров, а также валов с неограниченными размерами.
Свободным пластинированием называется способ, при котором пластина устанавливается на деталь свободно и удерживается на ней в силу специфики их формы. Формы пластин для свободного пластинирования показаны на рис. 9.3 г.
Связанное пластинирование предусматривает применение дополнительных средств крепления пластин – приварки, приклеивания или установки механических стопоров. Пластины при этом можно устанавливать поясами, продольно или спирально.
217
Дополнительные ремонтные детали обычно крепятся посадкой и натягом. В отдельных случаях могут быть использованы дополнительные крепления приваркой по торцу, приклеиванием или постановкой стопорных винтов или штифтов.
9.3.Способы закрепления ДРД
Механический способ закрепления ДРД осуществляется с целью обеспечения достаточной прочности соединения деталей при работе.
1.Исходные данные: номинальный диаметр соединения dн; длина соединения l; продольная (осевая) сила, стремящаяся сдвинуть одну деталь относительно другой Рос; допустимый предел текучести металла [σт]d.
2.Определяют необходимое давление р на контактных поверхностях соединения:
p |
Pос |
, |
d l f |
где Рос – продольная осевая сила, Н;
dн – номинальный диаметр соединения, м; l – длина соединения, м;
f – коэффициент трения.
3. Определение наименьшего предельного натяга:
|
|
|
|
|
, |
Nmin p d CD |
Cd |
||||
|
E |
D |
|
E |
|
|
|
d |
|
где ED и Ed – модули упругости материалов;
CD и Cd – коэффициенты определяемые по формулам:
|
|
|
d |
|
2 |
|
|
|
|
|
D |
2 |
|
|
|
1 |
|
|
|
|
|
1 |
|
1 |
|
|
|||
|
|
|
|
|
||||||||||
CD |
d2 |
|
|
D ; Cd |
|
|
|
|
d |
|
|
d , |
||
|
|
d |
|
2 |
|
|
|
|
D |
2 |
||||
|
|
|
|
|
|
|
|
|||||||
|
1 |
|
|
|
|
1 |
|
1 |
|
|
||||
|
D2 |
|
|
d |
|
|||||||||
|
|
|
|
|
|
|
|
|
|
|
где μD и μd – коэффициенты Пуассона материалов;
D2 – габаритный размер, охватывающей детали, мм; D1 – внутренний диаметр втулки, мм.
4. Определяют значения расчетного натяга:
Nрасч Nmin 1,2 RZD RZd ,
где RZD и RZd – высота микронеровностей поверхностей.
(9.9)
(9.10)
(9.11)
(9.12)
218

5. Выбирают стандартную посадку из посадок группы «с натягом», удовлетворяющую условию:
Nminст Nрасч, |
(9.13) |
где Nminст – наименьший предельный натяг, обеспечиваемый выбранной
стандартной посадкой.
6. Проверка выбора посадки по условию прочности. Расчет наибольшего давления, возникающего при реализации выбранной посадки:
P |
Nmaxст |
1,2 |
RZD |
RZd 10 6 |
МПа. |
(9.14) |
|
|
|
|
|||
max |
|
|
|
|
|
|
|
|
d CD |
Cd |
|
|
|
|
|
|
ED |
Ed |
|
|
7. Расчет наибольшего напряжения, возникающего в материале втулки: 1 d1 2
d d 2 Pmax ; МПа. (9.15) 1 d1
d
8. Анализ выполнения условия прочности ремонтной втулки. Условие прочности выполняется, если:
d T d . |
(9.16) |
9. Необходимое усилие при запрессовке собираемых деталей: |
|
Pn fn Pmax d l ,. |
(9.17) |
где fn – коэффициент трения при запрессовке: |
|
fn 1,15...1,20 f . |
(9.18) |
Также ДРД можно закреплять при помощи полимерных композиций (см. разд. 6), сварки (см. разд. 3).
219
10. ПАЙКА И ЕЕ ПРИМЕНЕНИЕ ПРИ ВОССТАНОВЛЕНИИ ДЕТАЛЕЙ АВТОМОБИЛЕЙ
10.1. Общие сведения
Пайкой называют процесс получения неразъемных соединений деталей в твердом состоянии при помощи расплавленного сплава, называемого припоем. Кромки соединяемых деталей при пайке нагревают до такой температуры, при которой припой полностью расплавляется, смачивает поверхности и заполняет зазор между ними. При охлаждении припой кристаллизуется и образует достаточно прочное соединение деталей.
Пайка (ГОСТ 17325–79) как способ восстановления деталей имеет следующие преимущества:
небольшой нагрев деталей (особенно при низкотемпературной пайке);
возможность соединения деталей, изготовленных из разнородных металлов;
достаточно высокая прочность соединения деталей;
простота технологического процесса и применяемого оборудования. Пайку применяют для устранения трещин и пробоин в радиаторах, то-
пливных и масляных баках, трубопроводах, приборах электрооборудования и др. Пайку используют также при восстановлении размеров изношенных деталей путем постановки ленты или навивки проволоки с последующей их припайкой к поверхности детали.
К числу недостатков пайки следует отнести некоторое снижение прочности соединения деталей по сравнению со сваркой.
10.2. Припои и их свойства
Наиболее часто при восстановлении деталей автомобилей применяют оловянно-свинцовые, медно-цинковые и алюминиевые припои. По температуре плавления все припои подразделяются на низкотемпературные – ниже 450 °С и высокотемпературные – выше 450 °С.
Оловянно-свинцовые припои. Температура плавления не более 280 °С. Обладают достаточно высокой противокоррозионной стойкостью и высокими технологическими свойствами. Прочность пайки этими припоями по пределу прочности на разрыв составляет 80...100 МПа. Состав и температура плавления этих припоев приведены в табл. 10.1. Оловянносвинцовые припои применяют при восстановлении радиаторов, трубопроводов низкого давления, деталей и узлов электрооборудования и др.
220