
2016
.pdf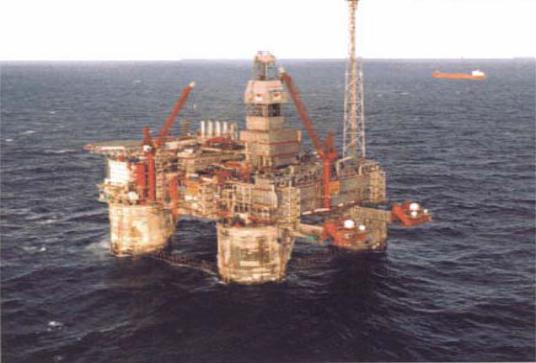
из летучей золы, производится уже длительное время в объёме более 550 тыс. м3 в год.
Лёгкий бетон на основе «LITAG» классов по прочности на сжатие В15–В60 и даже выше при плотности от 1600 до 2000 кг/м3 примеF няется высокоэффективно в обычных железобетонных и предвариF тельно напряжённых конструкциях различных видов. Результаты испытаний бетонов показывают существенно более высокую водоF и газонепроницаемость, стойкость к проникновению хлоридов в сравнеF нии с равнопрочным тяжёлым бетоном. В последнее время на основе LITAG получены и исследуются лёгкие бетоны прочностью на сжатие до 100 МПа.
На рис. 1.2F1.5 представлены фотографии нефтяной платформы, мостов и высотного здания, в которых основные несущие конструкции изготовлены из конструкционных легких бетонов классов В40FВ60.
Рис. 1.2. Нефтяная платформа Heidrun Tension (Norway, 1995 г.). (Конструкция платформы из высокопрочного легкого бетона на заполнителях из вспученной глины (Liapor) при плотности ρ0 = 1950 кг/м3 и прочности на сжатие в возрасте 28Fи суток R28 = 70 МПа)
21

Рис. 1.3. Мост “Stolmen”, Норвегия, построен в 1998 г. (L=94+301+72=467 м). (Конструкции главного пролета длиной 301 м выполнены из легкого бетона R28 = 70,4 MПa при ρо = 1940 кг/м3 на пористом заполнителе HF Leсa 800 из вспученных глинистых сланцев)
Рис. 1.4. Мост Coronado (California, USA, 1969 г.)
из конструкционного легкого бетона прочностью R28 = 42 МПа при ρ0 = 1840 кг/м3 на заполнителе из вспученных глинистых сланцев
22
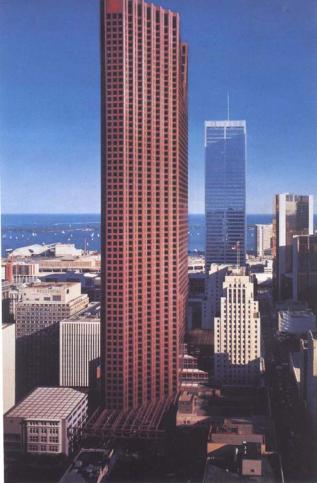
Рис. 1.5. Здание Scotia Plaza Tower (69 этажей, 276 м) в финансовом районе г. Торонто (Канада). Перекрытия высокой огнестойкости (класс К0 при τогн = 2 час) выполнены из монолитного лёгкого бетона класса по прочности В20 – В30 марки по плотности D1800 – D1900 на основе пористого шлакового гравия (pelletized slag), 1990 г.
На основании успешного опыта применения лёгких бетонов на LITAG в пролётных строениях мостов, в строительстве высотных зданий, различного рода инженерных сооружений специалисты делают выводы о перспективах существенного расширения производства заполнителя и бетонов.
Предприятия по переработке золыFуноса в заполнители типа LITAG действуют в настоящее время в Германии, Польше, Болгарии, Чешской Республике.
Последнее время в странах континентальной Европы расширяется производство пористого заполнителя из вспученного стекла. СчитаетF ся, что это самая рациональная утилизация стеклобоя. Так, в Германии
в2004 г. создана так называемая система стеновой кладки с высокими теплозащитными свойствами («Poraform wall system») с использованием
вблоках лёгкого бетона на основе гранулированного пористого стекла.
23
Плотность бетона в блоках – 0 500 кг/м3 при 0 = 0,11 Вт/м °С и очень
низком водопоглощении (всего 2 % по объёму). При таких характериF стиках стеновая кладка толщиной 37,5 см вполне удовлетворяет теплотехническим требованиям Германии и обеспечивает комфортF ность жилища.
Применение лёгких бетонов в Японии относится к началу 50Fх гг. прошлого века. Сначала использовали заполнители из вулканических пород. В 60Fх гг. начали применяться заполнители из вспученных глин
исланцев.
Внастоящее время действуют несколько заводов пористых заполF нителей, аналогичных тем, что имеются в Северной Америке. Общая производительность – около 1 млн м3 в год. Применяются они, главF ным образом, в конструкционных лёгких бетонах, которые успешно используются при строительстве:
– зданий, особенно высотных;
– пролётных строений мостов;
– морских платформ для добычи нефти;
– других морских гидротехнических сооружений.
1.3.2. Развитие отрасли в России
Первые опыты по вспучиванию глин в СССР выполнил Ф.Ф. СоF бесский в 1902F1906 гг. Основные усилия его были направлены на создание технологии пористого керамического кирпича. Первые поF ристые кирпичи Ф.Ф. Собесский продемонстрировал в 1906 г. в ТашF кенте на сельскохозяйственной выставке. Свои попытки создать техноF логию пористых блоков и кирпичей он продолжал до 1922 г.
Систематические исследования вопросов технологии получения пористых заполнителей из глин в СССР были начаты в 1925 году проф. Е.В. Костырко. Заполнитель получали дроблением вспученных обжигом крупных кусков глины. Заполнитель Е.В. Костырко предлоF жил называть керамзитом. Первая в стране опытноFпромышленная установка получения керамзитового щебня была построена в пос. ВоF ронцово (Московская область) в 1937 г. Обжиг глинистых комков производился в туннельной печи. Вспученный материал затем дробили на щебень. В последующем туннельная печь была заменена враF щающейся.
В 30Fх гг. в США, в ряде стран Западной Европы, а также в СССР
начинается освоение производства шлаковой пемзы из доменных шлаков. Первые установки предусматривали получение заполнителя простым «ямным» способом. ОгненноFжидкий шлак из шлаковозов
24
выливали в ямы, дно которых предварительно выкладывали кусками шлаковой пемзы и увлажняли водой. Вода, превращаясь в пар, остужает расплав и принимает участие в его поризации.
В конце 30Fх гг. появились первые сообщения о возможности вспуF чивания перлитовых горных пород (П.П. Будников, М.П. Воларович, А.А. Леонтьев). В США работа П.П. Будникова была прореферирована, и были начаты обширные исследования по технологии вспученного перлита. Первые установки для получения перлита были построены в США в середине 40Fх гг. Установки в основном строили рядом с месторождениями перлитовой породы.
Освоение производства пористых заполнителей в СССР было прервано войной. Лишь в конце 40Fх гг. оно было продолжено в МоскF ве, Киеве, Волгограде, Челябинске. В июне 1955 г. в Волгограде запуF стили в эксплуатацию опытноFпромышленную установку для полуF чения керамзита производительностью 1 м3/ч, а в 1956 г. в г. Волжском (Волгоградская область) был построен первый завод керамзита производительностью 110 тыс. м3/год. Видимо, 1956 г. можно считать началом массового освоения производства искусственных пористых заполнителей в СССР. В Москве и Московской области, в Куйбышеве (ныне Самара), Ленинграде, Ташкенте и РостовеFнаFДону строятся заF воды, которые в 1958 г. выпустили 175 тыс. кубических метров керамзита.
Помимо керамзита, шлаковой пемзы и вспученного перлита в разных регионах СССР строятся вначале опытноFпромышленные, а затем промышленные установки других разновидностей пористых заполнителей: аглопорита, глинозольного керамзита, зольного гравия, зольного аглопоритового гравия, гранулированного пеностекла, шлаF козита, термолита, шунгизита. Название заполнителей обусловлено названием исходного сырья и особенностью технологии их получения. Так, глинозольный керамзит – это пористый заполнитель, получаемый из сырьевой шихты, основу которой составляют глина и зола; зольный гравий – заполнитель, получаемый из золы ТЭС; зольный аглопоF ритовый гравий – это тоже заполнитель, получаемый из золы ТЭС, но по технологии аглопорита; шлакозит – заполнитель, получаемый из шлаков ТЭС. Название «термолит» определено технологией производF ства – тепловой обработкой кремнистых горных пород: опоки, диаF томита, трепела, после которой эти породы приобретают прочность и стойкость к агрессивным средам. При определенных условиях кремF нистые породы способны вспучиваться.
Наконец, «гранулированное пеностекло» – название, которое укаF зывает на близость данного пористого заполнителя к пеностеклу, но
25
технология и свойства материала отличаются от пеностекла. Сырьевая шихта гранулируется, гранулы обжигаются во вращающихся печах. В ряде литературных источников вместо термина «гранулированное пеностекло» для обозначения заполнителя применяют термин «стекF лозит» или «пеностеклогранулят».
В 1954 г. на территории ТЭЦF9 Мосэнерго строится опытная устаF новка аглопорита, на которой отрабатываются режимы обжига различF ных материалов, но главным образом, из отходов промышленности: зол
ишлаков тепловых электростанций, отходов угледобычи и углеобоF гащения и пр. Первая опытная установка по утилизации котельных зол
ишлаков была построена в 1957 году в г. Электросталь. Установка предусматривала получение аглопорита из золошлаковых отходов путем их спекания на ленточной агломерационной машине непрерывF ного действия. Совместное использование шлака и золы оказалось не совсем удачным решением. ВоFпервых, значительная часть неокомкоF ванной золы просыпалась через решетку палет непрерывной ленты, а, воFвторых, и это главное, неоднородность состава шихты порождала нестабильность качества материала, поступающего на агломерационF ную машину. Очень трудно следить за процессом, в который поступает сырье с постоянно изменяющимся качеством. Более совершенная агломерационная установка получения пористого заполнителя из зол тепловых электростанций была построена в 1972 г. в г. Люберцы. С вводом Люберецкой установки началось освоение производства зольного аглопоритового гравия. На этой установке зола перед подачей на спекание усреднялась и окомковывалась. Люберецкая установка имела невысокую производительность, порядка 50 тыс. м3 заполнителя в год, ее считали опытноFпромышленной. Поэтому в конце 70Fх гг. в Молдавии (Днестровск) строится промышленная установка зольного аглопоритового гравия мощностью 150 тыс. м3/год.
Параллельно с освоением технологии получения зольного аглопоF ритового гравия в Советском Союзе проводятся исследования по соF зданию технологии пористого заполнителя из зол тепловых электроF станций путем обжига сгранулированных зол во вращающейся печи. Первая установка зольного гравия построена в Кашире (Московская область). Мощность установки – 50 тыс. м3/год. Установка работает на золах Каширской ГРЭСF4, содержащих незначительное количество несгоревших угольных частиц – до 3 %. Попытка получить зольный гравий из зол с высоким, более 3 %, содержанием несгоревших частиц, оказалась неудачной. Так, не были пущены в эксплуатацию установки зольного гравия в Николаеве (Украина) и Дзержинске (Горьковская область), на которых в качестве сырья пытались использовать золы
26
местных тепловых станций, содержавших несгоревшие угольные частицы в количестве 8F10 %.
В80Fх гг. некоторые заводы Европейской части СССР вместо керамзитового гравия стали производить шунгизит – пористый заполF нитель, получаемый из глинистых сланцев Нигозерского месторожF дения (Карелия), называемых шунгитами. В шунгите содержится углеF род в виде тонкодисперсного графита в количестве от 0,5 до 10 %. РазF новидности шунгита, содержащие графит в количестве 0,5F1,5 %, преF красно вспучиваются, а получаемый заполнитель по своим свойствам аналогичен керамзитовому гравию. В начале 80Fх гг. в Карелии была поF строена дробильноFсортировочная фабрика мощностью 400 тыс. м3/год дробленого, фракционированного шунгита, который железнодорожF ным транспортом поставлялся на заводы шунгизита. Технология получения шунгизита чрезвычайно проста. Поступившая на завод крошка определенной фракции складируется в бункер и затем дозаторами подается на обжиг во вращающуюся печь. Отсутствуют переделы подготовки сырья и сушки сырцовых гранул. Благодаря простоте технологии и существенно меньшим затратам на единицу продукции производство шунгизита достаточно интенсивно развивалось в 80Fх гг.
Вконце 80Fх гг. начинают производить гранулированное пеностекF ло (п. Лузино Омской области), шлакозит (п. Залесье, Украина) и строится установка шлакозита в Тольятти (Россия). В табл. 1.3 привеF дены свойства наиболее легких пористых заполнителей, выпускавF шихся в Советском Союзе.
По мнению комиссии С8 fib Международной Федерации по бетону
ижелезобетону CEBFFIP (fib), наиболее важным и перспективным направлением развития легких бетонов на пористых заполнителях является применение их в конструкционных материалах. Проблемной группой ТG 8.1 fib в 2000 г. разработаны рекомендации по проекF тированию и применению несущих конструкций из легких бетонов классов по прочности до LС88 или марки М1000.
Легкие бетоны классов до В50 включительно, высокой морозостой кости (до F1500 вкл.) и особо низкой проницаемости (до W20 вкл.) разработаны НИИЖБом при использовании пористых шлаковых заполнителей различных видов. Из бетона на шлакопемзовом щебне на предприятиях стройиндустрии г. Липецка изготовлены и более 15 лет успешно эксплуатируются панели безрулонной кровли жилых зданий, бордюрные камни. В 2002F2003 гг. из легких бетонов классов по прочF ности В30FВ40 марок по плотности D1850FD1900 на пористом шлаF ковом гравии НовоFЛипецкого меткомбината при высокоподвижных смесях были возведены монолитные несущие каркасы жилых зданий
27
одного из микрорайонов г. Воронеж (застройщик – фирма ОАО «Воронежстроймонолит»).
Т а б л и ц а 1 . 3 Свойства особо легких пористых заполнителей,
выпускавшихся на предприятиях или полученных на опытноFпромышленных установках СССР
|
|
|
|
|
Свойства заполнителя |
|
||
МестонахожF |
|
|
|
|
|
КоэффиF |
||
|
|
|
|
|
циент |
|||
дение установки, |
Наименование |
Насыпная |
ПрочF |
СтруктурF |
|
|||
|
теплопроF |
|||||||
наименование |
сырья |
плотность, |
ность, |
ный фактор, |
|
|||
заполнителя |
|
кг/м3 |
МПа |
МПа см6/г2* |
|
водности |
||
|
|
засыпки, |
||||||
|
|
|
|
|
|
|
|
|
|
|
|
|
|
|
|
|
Вт/м К |
Омская |
область, |
Бой стекла + |
200F220 |
0,5F1,1 |
5,0F9,0 |
|
0,06F0,068 |
|
п.Лузино, |
грануF |
+жидкое стекло |
|
|
|
|
|
|
лированное |
|
|
|
|
|
|
||
пеностекло |
|
|
|
|
|
|
||
Ереван, НИИСМ, |
Перлит + |
200F250 |
1,3F2,0 |
10F12 |
|
0,06F0,07 |
||
пеностеклограF |
+ NaOH + HNO3 |
|
|
|
|
|
||
нулят |
|
|
|
|
|
|
|
|
ЗАО «Легкий кеF |
Бентонит |
200F250 |
0,6F1,3 |
5,4F7,5 |
|
0,07F0,09 |
||
рамзит», |
г. СаF |
Смышляевский; |
|
|
|
|
|
|
мара, |
керамзит |
данные за 2003 г. |
|
|
|
|
|
|
(10F20 мм) |
|
|
|
|
|
|
||
ТЭЦ г. Тольятти, |
Шлак + бентоF |
250F300 |
1,1F1,7 |
6,0F7,0 |
|
0,06F0,07 |
||
шлакозит |
|
нит+ЩСПК |
|
|
|
|
|
|
(10F20 мм) |
|
|
|
|
|
|
||
|
|
|
|
|
|
|
|
|
*П р и м е ч а н и е . Структурный фактор – константа уравнения R = Кρ2.
В Самарском ГАСУ и в МГСУ разработан керамзитобетон класса по прочности на сжатие В40 для применения в высоконапорных виброгидропрессованных трубах. В НИИЖБе совместно с НИИСФом в 2004F2005 гг. разработан легкий бетон классов по прочности до В60 вкл. при марке по плотности D1800FD1850 на высокопрочном (марок П300F П350) керамзитовом гравии Новочебоксарского ДСК. При использоF вании в качестве химикоFминеральной добавки модификатора МБF10 (микрокремнезем + пластификатор СF3) бетонные смеси изготовляютF ся для керамзитобетонов классов В40FВ60 вкл. высокоподвижными (ОК = 25F26 см) и не требующими при укладке виброуплотнения. ТаF кие бетонные смеси при классе бетона по прочности В45 (марки М650) и марке по плотности D1800 были применены практически во всех конструкциях возведенного в 2006г. в г. Москве 24Fэтажного здания фирмы GazFOilFTrade (дочернего предприятия ОАО «Газпром»).
28
1.3.3.Развитие отрасли в странах СНГ
Вцелом объёмы легкобетонного строительства в странах СНГ существенно сократились. Ведётся строительство практически только в столицах и нескольких крупных областных центрах. Особенно это относится к Казахстану.
Пересмотр норм строительной теплотехники в сторону существенF ного ужесточения вслед за Россией произошёл в 1995F1998 гг. и в этих странах. И это привело, поFсуществу, к развалу панельного домоF строения, и, как следствие, – к закрытию большинства предприятий по производству керамзитового гравия.
Так, в Украине, по информации НИИСМИ (Киев), панельное домостроение сохранилось только в некоторых регионах с крупными ДСК и соотношение панельного домостроения к каркасному сокраF тилось до 1:5. Из стеновых конструкций производятся, как правило, только трёхслойные наружные стеновые панелей с пенополистирольF ным утеплителем.
Объёмы производства керамзита сократились почти на порядок (с 4,47 млн м3 до 550 тыс. м3 /год). Керамзит применяется, в основном, только для изготовления стеновых блоков и в небольших объёмах – в конструкционном лёгком бетоне наружных слоёв трёхслойных стеноF вых панелей. Сохранилось производство блоков из мелкозернистого бетона на доменном гранулированном шлаке.
Вто же время строительный рынок Украины начинают завоёвыF вать изготовляемые вибропрессованием стеновые блоки из модифиF цированного перлитобетона. Страна имеет значительное собственное действующее месторождение перлита. Работают пять перлитоперерабаF тывающих предприятий. В НИИСМИ (г. Киев) разработана новая технология 2Fстадийной термообработки перлитового сырья, позволивF шая получить перлитовый песок, имеющий существенные достоинства по сравнению с уровнем мировых аналогов – практически в 2 раза меньшее водопоглощение за счёт оплавленной оболочки зерен заполF нителя. Плотность модифицированного перлитобетона в блоках (марка D500–D600) в среднем на 25 % меньше, чем приведенная плотность керамзитобетона в производимых вибропрессованием щелевых стеноF вых камнях. Отсюда значительные преимущества в снижении массы стены, уменьшенной её толщине за счёт лучших теплофизических свойств.
После преодоления трудностей переходного периода наблюдается подъём производства и применения легкобетонных стеновых изделий в Белоруссии и странах Балтии. Так, в 1996 г. в Эстонии построен завод по производству керамзита мощностью 400 тыс. м3/год и завод по
29
производству стеновых блоков из керамзитобетона. Заводы работают в настоящее время на полную мощность. В Литве построен завод– автомат по производству стеновых блоков из керамзитобетона мощF ностью 120 тыс. м3/год. Обслуживающий персонал – 18 человек. БлоF ки, получаемые методом полусухого вибропрессования при приведенF ной плотности 600–700 кг/м3, активно вытесняют пенобетонные блоки со строительного рынка этих стран.
Обусловлено это следующими преимуществами в сравнении с блоками из пенобетона: высокой степенью автоматизации, существенF но лучшими теплофизическими характеристиками керамзитобетона, большей однородностью и обеспеченностью строительноFтехнических свойств во время эксплуатации.
Керамзитобетонные блоки, производимые по вышеуказанным технологиям, широко используются в настоящее время в Белоруссии и странах Балтии при строительстве как жилых зданий каркасного типа (12–14 этажей), так и малоэтажных.
Впоследние 2F3 года серьёзную конкуренцию мелким керамзитобеF тонным блокам в применении для каркасных зданий начинают соF ставлять укрупнённые (почти в 2 раза) стеновые блоки из полистиролF бетона: их плотность и теплопроводность меньше практически в 2 раза, соответственно меньше масса стены, меньше (в среднем на 25 %) трудоёмкость возведения кладки.
ВКазахстане строительство ведётся, в основном, в северных регионах и притом в относительно небольших объёмах. Заводы по производству керамзитового гравия практически все закрыты. При производстве стеновых блоков применяется или неавтоклавный пеноF бетон, или мелкозернистый конструкционноFтеплоизоляционный лёгF кий бетон на основе доменного гранулированного шлака. В Казахстане имеются крупные резервы по использованию крупнотоннажных техноF генных отходов следующих видов: доменные шлаки, шлаки электротерF мофосфорного производства, бокситовые шламы, отходы глинозёмного производства, которые могут быть использованы для получения высокопрочных пористых заполнителей.
1.4.Перспективы развития пористых заполнителей
илегких бетонов
Перспективы развития легкобетонной промышленности в целом увязаны с действием следующих факторов.
1. Наличие мощной сырьевой базы. В табл. 1.4 приведены данные о химическом составе земной коры и некоторых строительных матеF
30