
2016
.pdf
МИНИСТЕРСТВО ОБРАЗОВАНИЯ И НАУКИ РОССИЙСКОЙ ФЕДЕРАЦИИ
Федеральное государственное бюджетное образовательное учреждение высшего профессионального образования «Пензенский государственный университет
архитектуры и строительства»
Н.И. Макридин, И.Н. Максимова
ИСКУССТВЕННЫЕ ПОРИСТЫЕ ЗАПОЛНИТЕЛИ И ЛЕГКИЕ БЕТОНЫ
Рекомендовано Редсоветом университета в качестве учебного пособия для студентов,
обучающихся по направлению подготовки 270800.62 «Строительство», профиль «Производство строительных материалов,
изделий и конструкций»
Пенза 2013
1
УДК 66.041.9.666.972.12 ББК 30.36+38.626.1я73
М17
Рецензенты: доктор технических наук, профессор, зав. кафедрой «Кадастр недвижимости и право»О.В. Тараканов (ПГУАС); кандидат технических наук, заместитель директора по качеству ООО «СтроиF тельные материалы» В.Ю. Нестеров
Макридин Н.И.
М17 Искусственные пористые заполнители и легкие бетоны: учеб. пособие / Н.И. Макридин, И.Н. Максимова. – Пенза: ПГУАС, 2013. – 324 с.
Рассмотрены основы материаловедения пористых заполнителей и легких бетонов – состав, структура, свойства материалов. На основе обобщения инфорF мации и результатов собственных исследований изложены технологии получения этих материалов с заданными свойствами.
Учебное пособие предназначено для бакалавров и магистрантов, обучающихся по направлению 270800.62 «Строительство», а также может быть полезно научным сотрудникам, аспирантам, преподавателям учебных заведений и инженерноF техническим работникам предприятий строительной индустрии.
Пензенский государственный университет архитектуры и строительства, 2013
© Макридин Н.И., Максимова И.Н., 2013
2
ВВЕДЕНИЕ
Развитие мирового строительства неразрывно связано с нарастающей тенденцией применения строительных материалов и конструкций, обеспечивающих значительное снижение массы зданий и сооружений. Одно из ведущих мест здесь принадлежит легким бетонам, которые, в свою очередь, могут успешно развиваться только при наличии достаточно развитой и совершенной сырьевой базы, включая пористые заполнители.
Традиционным пористым заполнителем для России является ке# рамзитовый гравий. Несмотря на существенное уменьшение выпуска, он продолжает занимать в России ведущее место среди пористых заполнителей. Между тем в ведущих зарубежных странах уже с середины 70#х годов прошлого века строительство керамзитовых пред# приятий прекращено. Но продолжают строить предприятия пористых заполнителей, в качестве исходного сырья использующих различные отходы промышленности, в том числе доменные шлаки, золошлаковые отходы тепловых электростанций, отходы угледобычи и углеобога# щения. Это позволяет не только улучшить экологическую обстановку путем утилизации отходов производства и сокращения земельных угодий на разработку карьеров и складирование отходов, но в ряде случаев существенно повысить эффективность производства пористого заполнителя за счет сокращения расхода топлива.
В табл. 1 приведен объем выпуска пористых заполнителей в послед# ние годы существования Советского Союза по данным Госкомстата
СССР и в России.
Т а б л и ц а 1 Выпуск пористых заполнителей в СССР и России
Заполнитель |
Всего в СССР, тыс. м3 |
Всего в России, тыс. м3 |
|
||||
|
1985 г. |
1989 г. |
1990 г. |
1985 г. |
1989 г. |
1990 г. |
2007 г. |
Все пористые заполнители, |
44103 |
52248 |
49610 |
22636 |
27768 |
26164 |
9020 |
в том числе: |
|
|
|
|
|
|
|
природные |
7008 |
7145 |
7512 |
600 |
600 |
550 |
260 |
искусственные |
|
|
|
|
|
|
|
в том числе: |
37006 |
45001 |
42000 |
22636 |
27768 |
26164 |
8760 |
керамзит |
30945 |
394124 |
36763 |
19138 |
24019 |
22892 |
7700 |
шунгизит |
791 |
951 |
867 |
791 |
951 |
867 |
– |
аглопорит |
801 |
883 |
870 |
227 |
240 |
233 |
– |
перлит |
2215 |
2414 |
2089 |
1509 |
1558 |
1303 |
450 |
шлаковая пемза |
1987 |
1073 |
963 |
830 |
850 |
728 |
460 |
зольный гравий |
43 |
24 |
24 |
43 |
24 |
24 |
30 |
зольный аглопоритовый |
|
|
|
|
|
|
|
гравий |
102 |
173 |
193 |
– |
– |
– |
– |
термолит |
36 |
24 |
17 |
36 |
24 |
17 |
20 |
Прочие |
88 |
102 |
98 |
88 |
102 |
98 |
100 |
3
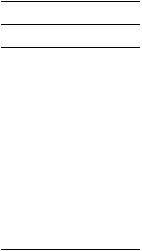
Максимальный выпуск пористых заполнителей достигнут в 1989 г. Всего в СССР в том году было произведено 52,25 млн м3 заполнителей, в России – 27,7 млн м3, в том числе – 24 млн м3 керамзита. С 1990 г. происходит снижение выпуска пористых заполнителей, вначале медленными темпами, начиная с 1996 г. – ускоренными. Примерная структура применения пористых заполнителей в различных сферах народного хозяйства в 80#х гг. и в настоящее время приведена в табл. 2.
Т а б л и ц а 2 Структура выпуска и применения пористых заполнителей в России
Область применения |
Объем применения, % |
|
|
|
80#е гг. |
|
2000#е гг. |
Теплоизоляционные засыпки |
18#22 |
|
35#45 |
Легкие бетоны, в том числе: |
78#80 |
|
40#60 |
стеновые панели |
36#38 |
|
5#10 |
стеновые блоки |
23#25 |
|
10#15 |
перегородочные плиты |
8#10 |
|
10#15 |
монолитные конструкции |
0,2#0,4 |
|
5#10 |
легкобетонные армированные |
11#13 |
|
10#15 |
изделия |
|
|
|
Прочие сферы народного |
0,4#0,6 |
|
5#10 |
хозяйства |
|
|
|
Почти 65#70 % выпуска заполнителей в 80#е годы уходило на из# готовление однослойных ограждающих конструкций: панелей, блоков толщиной 40#60 см с термическим сопротивлением 0,9#1,5 (м2 оС)/Вт. После выхода Постановления Совета Министров России №18#81 от 11.08.1995 г. «Об изменении № 3 СНиП II#3#79 «Строительная теплотехника», направленного на повышение уровня тепловой защиты зданий, положение дел с использованием пористых заполнителей и легких бетонов в строительстве резко изменилось. С 1996 г. жилые и общественные здания строят с использованием в качестве ограждаю# щих конструкций трехслойных стеновых панелей с так называемыми «эффективными» утеплителями и наружными слоями из армирован# ного тяжелого или конструкционного легкого бетонов. Широко приме# няют сложные стеновые конструкции с применением кирпича и эф# фективных утеплителей. Потребность в легких бетонах и пористых заполнителях, как стеновых материалах, резко падает. В настоящее время их производят не более 30 % от выпуска 1989 г.
Авторы настоящего пособия полагают, что современный уровень развития легкобетонного строительства и связанный с ним уровень производства пористых заполнителей не отражают «строительные» и
4
прочие возможности этих материалов. Пористым заполнителям и лег# ким бетонам на их основе уготована более весомая роль в строительном деле будущего.
Последние учебные пособия по легким бетонам и пористым запол# нителям, которые могли использовать учащиеся и инженерно#техниче# ские работники, интересующиеся проблемами производства и приме# нения этих материалов, были изданы в 70#80#х годах прошлого столе# тия. За последние 25#30 лет наука и техника пополнились новыми данными о легких бетонах и пористых заполнителях. Авторы настоя# щего пособия считают себя учениками и продолжателями основателей отечественной школы легкобетонного строительства, к которым, в пер# вую очередь, нужно отнести Н.А. Попова, М.З. Симонова, И.А. Ива# нова, Г.А. Бужевича, В.Г. Довжика, С.П. Онацкого, М.И. Рогового и многих других, на монографиях, учебниках и учебных пособиях кото# рых воспитывалось не одно поколение инженерно#технических работ# ников. В настоящем учебном пособии авторы старались сохранить накопленный фундамент знаний о легких бетонах и пористых запол# нителях, а также попытались дополнить его результатами собственных исследований и обобщениями исследований других авторов, выпол# ненных в указанный период.
Учебное пособие состоит из введения и пяти глав.
Во введении обоснована актуальность применения строительных материалов и конструкций, обеспечивающих значительное снижение массы конструкций зданий и сооружений.
В первой главе представлены общие сведения о пористых заполни# телях и легких бетонах; дана краткая история и перспективы развития пористых заполнителей и легких бетонов.
Во второй главе описана сырьевая база для пористых заполнителей и легких бетонов как из природного, так и техногенного сырья.
Третья глава посвящена технологии пористых заполнителей, в которой дана подробная технология переработки твердых сырьевых материалов, формования сырцовых гранул с рассмотрением элементов теории, сушка, обжиг и охлаждение гранул.
В четвертой главе рассматриваются структура кристаллической и аморфной фаз искусственных пористых заполнителей, дается пред# ставление о формировании пористой структуры и свойств пористых заполнителей как отдельных зерен, так и их совокупности.
Пятая глава посвящена формированию структуры цементного камня и легких бетонов как двух пористых взаимодействующих сис# тем; приводятся физические, деформативные, теплотехнические и экс# плуатационные свойства легкого бетона. Достаточно подробно рас#
5
сматривается структура легкого бетона конструкционного назначения с изучением напряженно#деформированного состояния структуры бетона и исследованием прочностных, деформативных и структурных изменений конструкционного легкого бетона на диаграмме его нагружения.
По мнению авторов, несмотря на спад объемов выпуска легкобе# тонных изделий, в перспективе отрасль будет развиваться. В пособии названы основные причины неизбежности данного процесса.
Материал пособия написан преимущественно по результатам исследований, выполненных авторами, с привлечением результатов исследований других авторов, монографии которых приведены в библиографическом списке.
6
1.ОБЩИЕ СВЕДЕНИЯ О ПОРИСТЫХ ЗАПОЛНИТЕЛЯХ
ИЛЕГКИХ БЕТОНАХ
1.1. Классификация пористых заполнителей
Согласно действующим стандартам, наименование которых привеF дено в конце настоящего раздела, пористыми заполнителями называют сыпучие зернистые материалы с насыпной плотностью не более 1200 кг/м3 при крупности зерен до 5 мм и не более 1000 кг/м3 при крупности зерен 5F40 мм. Основное назначение пористых заполниF телей – быть компонентами легких бетонов, в которых они занимают до 80 % объема. По происхождению заполнители подразделяют на приF родные (вулканические и осадочные) и искусственные (специально изготовляемые и отходы промышленности).
Кприродным пористым заполнителям вулканического происхожF дения относятся: пемза – пористая сыпучая порода губчатого или волокнистого строения от сероватоFбелого до коричневого цвета, предF ставленная в основном кислым вулканическим стеклом; вулканичеF ский шлак – сыпучая порода ноздреватого или губчатого строения от красного до черного цвета, состоящая из вулканического стекла основного состава; вулканический туф – мелкопористая порода, соF стоящая из сцементированного вулканического стекла и пепла.
Кзаполнителям из отходов промышленности относятся: пористые металлургические шлаки, образующиеся в результате естественного охлаждения в отвалах; топливные шлаки, получаемые при кусковом (слоевом) или пылевидном сжигании углей или при их газификации; грубодисперсные золыFуносы или золошлаковые смеси ТЭС; керамиF ческий бой – пористые кусковые материалы, получаемые дроблением боя кирпича и других пористых керамических изделий.
Кискусственным, специально изготовляемым, пористым заполниF телям относятся:
керамзит (в виде гравия, щебня и песка) и его разновидности (шунгизит, зольный гравий, глинозольный керамзит, стеклозит, шлаF козит, термолит), получаемые обжигом со вспучиванием во враF щающейся печи гранул (зерен) из глин, глинистых сланцев, в том числе шунгитсодержащих, кремнеземистых опаловых пород, золыF уноса или золошлаковой смеси ТЭС, боя стекла и др.;
аглопорит – сыпучий пористый материал щебнеF или гравиеF подобной формы, продукт контактного спекания на решетках агломеF рационных машин подготовленных гранул (зерен) песчаноFглинистых пород, трепелов и других алюмосиликатных материалов, а также
7
глинистых углесодержащих пород (отходы от обогащения углей) или золыFуноса ТЭС от пылевидного сжигания углей;
шлаковая пемза – пористый кусковой материал щебнеподобной или округлой формы, получаемая поризацией расплава шлака металлурF гического и химического производств;
гранулированный шлак – пористый мелкозернистый материал, производимый путем быстрого охлаждения расплава шлаков металF лургического и химического производств;
вспученный перлитовый щебень и песок – пористый материал, получаемый обжигом со вспучиванием подготовленных зерен из вулканических водосодержащих пород (перлита, обсидиана и других водосодержащих вулканических стекол) во вращающейся печи или в печи кипящего слоя;
вспученный вермикулит, получаемый обжигом зерен, подготоF вленных из природных гидратированных слюд.
Пористые щебень и песок из горных пород, отходов промышF ленности и специально изготовленных заполнителей получают рассевом после предварительного дробления.
Пористые заполнители классифицируют по следующим физикоF техническим свойствам. По форме и характеру зерен различают гравиеF подобные (гравий) и щебнеподобные (щебень) крупные заполнители. Гравиеподобные характеризуются округлой формой и не подвергаются дроблению после термической обработки. Щебнеподобные получают главным образом дроблением исходного природного сырья или термиF чески обработанного материала; они имеют угловатую (неправильную) форму и шероховатую (ноздреватую) поверхность.
По крупности зерен заполнители делят на фракции, мм: Песок:
мелкий .....................................………………. до 1,2 крупный ..................................……………… от 1,2 до 5 нефракционированный .....……………… до 5 Щебень или гравий .............……………… от 5 до 10 мм
» 10 » 20 » » 20 » 40 »
По насыпной плотности (кг/м3) щебень, гравий и песок, высуF шенные до постоянной массы, делят на марки – 50, 100, 150, 200, 250, 300, 400, 500, 600, 700, 800, 1000, 1200, 1400.
По прочности крупные пористые заполнители делят на марки – П15, П25, П35, П50, П75, П100, П125, П150, П200, П250, П300, П350, П400. Под маркой по прочности понимается прочность при сжатии кубика, выпиленного из гранулы заполнителя (если это возможно). На
8
практике прочность при сжатии пористого заполнителя определяют испытанием его в бетонах, сущность которого состоит в сравнении прочности бетонов на испытуемом заполнителе с прочностью растворF ной составляющей бетонов. Существует несколько методов испытания заполнителя в бетоне. Опишем один из них, применяемый при определении марки пористого заполнителя по прочности фракции 5F10 или 10F20 мм.
По стандартным методикам определяют среднюю плотность зерен испытуемого заполнителя в цементном тесте, кз , его водопоглощение за один час, Wпогл , и прочность заполнителя при сдавливании в металF лическом стакане (цилиндре), Rц . Готовят бетонную смесь следующего
состава: расход цемента Ц = 4 кг; расход кварцевого песка П = 6 кг; расход крупного пористого заполнителя К = 3,5 кз кг; расход воды
В 0,35Ц WпоглК 100.
Высыпают высушенные до постоянной массы материалы на предварительно протертый влажной тканью противень и тщательно перемешивают вручную мастерком, приливают воду порциями и вновь тщательно перемешивают в течение 5 минут. Проверяют подвижность бетонной смеси, которая должна быть не меньше 2F4 см, в противном случае добавляют воду. Через 20 минут после приготовления бетонной смеси из части смеси формуют образцы – три образца размером 10 10 10 мм. Из оставшейся части отсеивают раствор на сите с ячейкаF ми 5 мм. Отсев производят на вибростоле, сетку предварительно протиF рают влажной тканью. Из отсеянного раствора также формуют три куба с ребром 10 мм. Формы, в которых формуют образцы, предварительF но взвешивают. После вибрирования смеси формы с бетоном и расF твором вновь взвешивают, вычисляют плотность бетонной и растворной смесей и уточняют фактические расходы материалов, в том числе фактическую концентрацию крупного заполнителя в бетоне, к , которая
не должна сильно отличаться от величины 0,35 – более чем на ±0,02. Формы с образцами закрывают влажной тканью, выдерживают не
менее 6 часов, затем пропаривают в лабораторной пропарочной камере при t = (85 ± 2) оC по режиму 4 + 4 + 16 (подъем температуры, выF держка при t = (85 ± 2) оC, остывание). После извлечения из камеры образцы выдерживают в течение 4 часов на воздухе и испытывают с определением прочности бетона и раствора. По результатам испытаний с помощью номограммы (рис. 1.1) определяют марку по прочности пористого заполнителя.
9
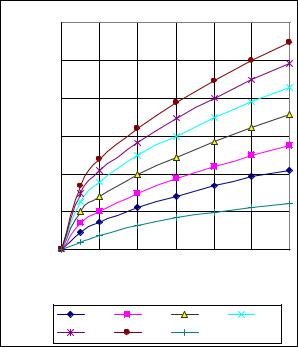
|
60 |
|
|
|
|
|
|
|
50 |
|
|
|
|
|
|
, МПа |
40 |
|
|
|
|
|
|
бетона |
|
|
|
|
|
|
|
30 |
|
|
|
|
|
|
|
Прочность |
|
|
|
|
|
|
|
20 |
|
|
|
|
|
|
|
|
|
|
|
|
|
|
|
|
10 |
|
|
|
|
|
|
|
0 |
|
|
|
|
|
|
|
0 |
10 |
20 |
30 |
40 |
50 |
60 |
|
|
Прочность раствора, МПа |
|
||||
|
|
П5 |
П10 |
|
П20 |
|
П30 |
|
|
П40 |
П50 |
|
П2,5 |
|
|
Рис. 1.1. Номограмма для определения марочной прочности заполнителя по прочности
В табл. 1.1 приведено соотношение между маркой заполнителя по прочности и прочностью заполнителя при сдавливании в цилиндре.
Т а б л и ц а 1 . 1 Соотношение между маркой пористого заполнителя по прочности
и прочностью при сдавливании в цилиндре (ГОСТ 9757F90)
Марка |
Прочность при сдавливании в цилиндре, МПа |
|
||||
по |
|
|
|
|
|
|
керамзитового |
керамзитового |
аглопоритового и |
шлакоF |
|||
прочF |
||||||
гравия и его |
щебня и его |
шлакового |
пемзового |
|||
ности |
||||||
аналогов |
аналогов |
гравия |
щебня |
щебня |
||
|
||||||
П15 |
До 0,5 |
F |
F |
До 0,3 |
До 0,2 |
|
П25 |
Св.0,5 до 0,7 |
– |
– |
Св.0,3 до 0,4 |
Св.0,2 до 0,3 |
|
П35 |
Св.0,7 до 1,0 |
Св.0,5 до 0,6 |
– |
Св.0,5 до 0,5 |
Св.0,3 до 0,4 |
|
П50 |
Св.1,0 до 1,5 |
Св.0,6 до 0,8 |
Св.0,7 до 1,0 |
Св.0,5 до 0,6 |
Св.0,4 до 0,5 |
|
П75 |
Св.1,5 до 2,0 |
Св.0,8 до 1,2 |
Св.1,0 до 1,2 |
Св.0,6 до 0,7 |
Св.0,5 до 0,6 |
|
П100 |
Св.2,0 до 2,5 |
Св.1,2 до 2,0 |
Св.1,2 до 1,2 |
Св.0,7 до 0,8 |
Св.0,6 до 0,8 |
|
П125 |
Св.2,5 до 3,3 |
Св.1,6 до 2,5 |
Св.1,5 до 1,7 |
Св.0,8 до 0,9 |
Св.0,8 до 1,1 |
|
П150 |
Св.3,3 до 4,5 |
Св.2,0 до 3,3 |
Св.1,7 до 2,0 |
Св.0,9 до 1,0 |
Св.1,1 до 1,4 |
|
П200 |
Св.4,5 до 5,5 |
Св.3,0 до 4,5 |
Св.2,0 до 2,5 |
Св.1,0 до 1,2 |
Св.1,4 до 1,8 |
|
П250 |
Св.5,5 до 6,5 |
Св.4,0 до 5,5 |
Св.2,5 до 3,0 |
Св.1,2 до 1,4 |
Св.1,8 до 2,2 |
|
ПЗ00 |
Св.6,5 до 8,0 |
Св.5,0 до 6,5 |
Св.3,0 до 3,5 |
Св.1,4 до 1,6 |
Св.2,2 до 2,7 |
|
П350 |
Св.8,0 до 10,0 |
Св.6,0 до 7,0 |
Св.3,5 |
Св.1,6 |
Св.2,7 |
|
П400 |
Св. 10,00 |
Св.6,0 |
– |
– |
– |
10